级进模冲孔弯曲Word文档下载推荐.docx
《级进模冲孔弯曲Word文档下载推荐.docx》由会员分享,可在线阅读,更多相关《级进模冲孔弯曲Word文档下载推荐.docx(13页珍藏版)》请在冰点文库上搜索。
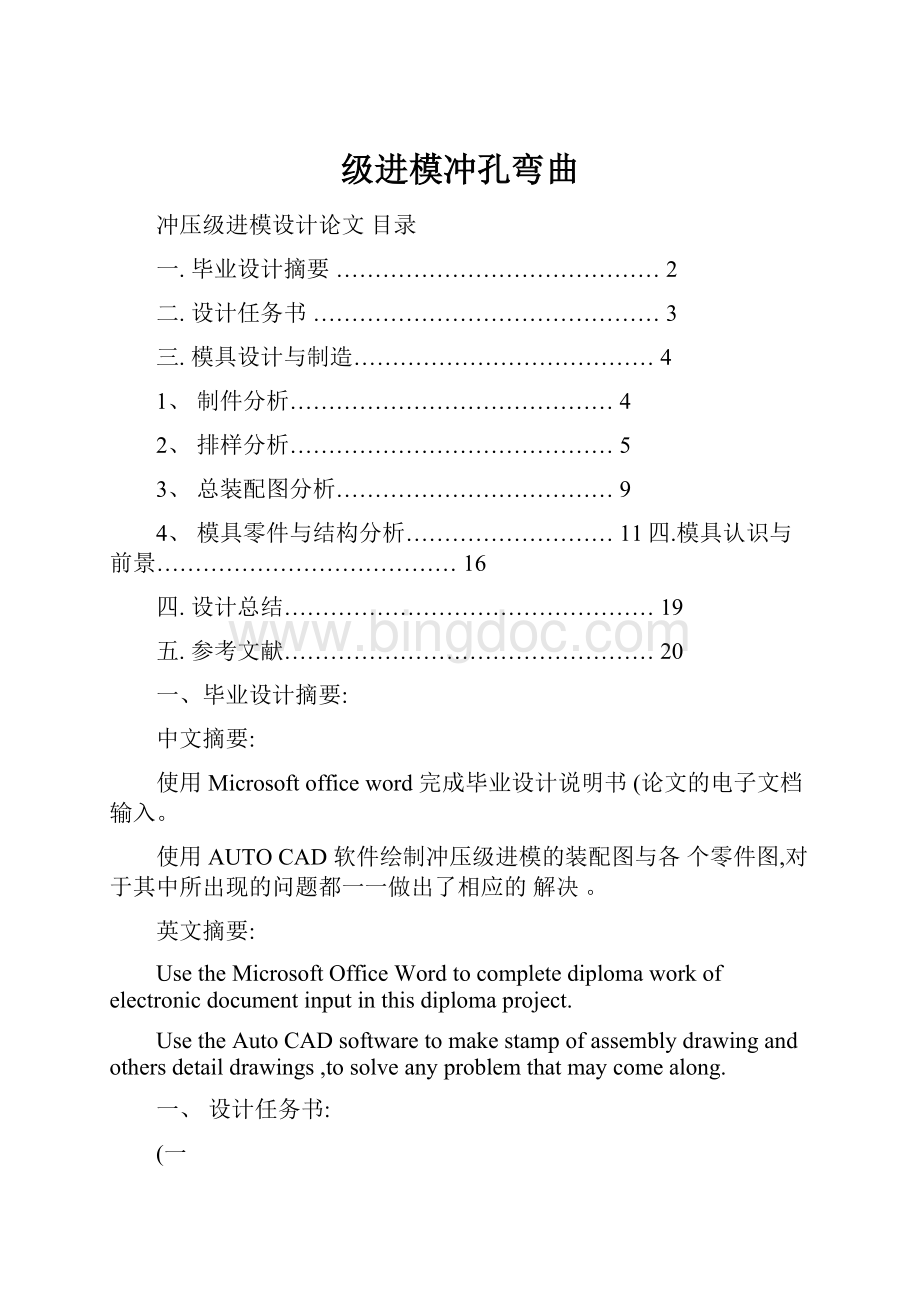
2、厚度0.3mm
3、生产批量大批量
4、未注公差均按IT14级制造
二、模具设计与制造
(一、制件的分析
(1制件的结构工艺特点
该制件主要用于连接方面,所要求的精度高,零件的主要成型是冲裁.弯曲.切断等多道工序,两侧采用向内弯曲形式,所以采用本制件采用多工位级进模设计比较合理,简单化。
(2对冲切断面质量要求
为保证制件的质量,要求表面规整、光亮、无毛刺,冲切断面粗糙度比较高,且制件表面不得有伤痕,要求制件进行滚磨、光饰和清洗处理。
(3
制件的展开图
(二、排样分析
零件工序排样图如图所示:
排样设计原则
2制作制件展开胚料样板,在图画上反复试排,待初步确定方位后,安排侧刃定位,在一端安排冲孔,切废料等工位,再向一边依次安排成型工位3第一工位,一般采用侧刃定位,在第二工位冲孔,在以后的工位中,视其工位数不多,加上侧刃定位,在第五工位与第七工位采用导正孔定位。
4对相对精度高的的孔同步冲出
5成型方向要有利于送料的顺畅
6对弯曲和拉深,每一工位不宜变形过大,这样有利于质量保证也有利于调试修整
7对要求高的要设整形工位
8尽量使冲压负荷平衡
9合理安排废料和制件的顺利排除
10保证带料搭边有足够的强度
11合理分布托料钉的位置,设计六颗托料钉12为提高各凹模的强度应设置空工位
13一般拉深半径应等于大于料厚4倍,否则应采用整形工序
因此带料选择可延伸连接的双中载体形式,主要是制件采用这样的载体,是因为这种可以保证成形件的质量,这样的载体平衡性能好。
宽度为30mm,步距为7.4mm。
材料利用率计算:
%
1000⨯=η式中:
η为材料利用率
F为工件的实际面积
0F为所用材料面积,包括工件面积与废料
面积
η=1550/(30x7.4x100%
=70%
所以本排样的材料利用率符合要求
排样的步距精度直接影响制件的尺寸精度,步距公差小制件精度高,但步距太小,模具制造困难,按精密级进模具步距公差的经验公式'
δkβ=查表β=0.13,k=0.85n=19
'
δ=0.015mm提高精度达到0.015mm
综合上述可知,该排样的缺点是材料利用率不高,但对制件精度有很好的保证,因此采用该方案。
工序说明如下:
1、侧刃定位在这排样当中,首先考虑到定位的问题,在第一部采用的是侧刃定位。
同以后工序的导正孔同时定位,不让材料抖动。
2、冲孔在侧刃定位之后,然后冲出制件的孔,为了对以后的工位中不产生影响,先冲出小孔。
3、导正因为制件的工位数不是很多,考虑到先前采用侧刃定位,所以在第五工位和第七工位采用导正孔导正,两者同时定位导正。
可以顺利的保证制件的精度。
4、去边料在第四工位设置去边料。
5、第一次弯曲先保证弧形弯曲的长度,先弯曲出制件弧度的8.5长度,保证了制件的精度。
6、第二次弯曲二次弯曲出成型制件。
7、空工位为使制件不产生变形,在弯曲的后头加上一空工位。
8、落料获得制件,自然落料。
9、切断条料切断废料,避免影响送料。
(三总装配图分析
一模具主要特点如下:
1、采用气动送料装置、浮动导料装置和精确的导正销导正,废料切刀切断保证安全。
2、模具精度高,其易损件具有互换性,可以方便迅速地更换备件。
3、模架刚性、导向性好,保证了模具的动态精度主模架采用加厚钢板,上模座上平面与下模座下平面的平行度0.04mm
4、模具材料分别采用硬质合金、高速钢、高合金钢等,模具的刃磨寿命和总寿命高。
5、重要零件也尽量用可换式零件
6、固定件采用高强度螺钉和销钉,部分弹性件采用高强度弹簧
二互换性模具设计与工艺措施分析
1消除或减小压力机动态精度误差
1选用高精度,刚性好的压力机和降低压力机速度
2冲压载荷的偏心量,将难于计算,压力机中心靠近模板中心。
3模架刚性,加厚模座和选用刚性好的材料,加粗或增加导套的有效长度
2提高凸模和凹模步距的一致性
将固定板,卸料板和凹模有关孔一次装夹加工,但必须保证步距精度
3提高凸模与凹模形状的一致性
1在数控机床上,用同一指令加工各板
2磨加工各镶件
4提高制件的加工精度
提高导正孔的精度和导正销的步距精度,一般与步距精度一样
四模具的装配
模具的装配过程视模具的类型结构的不同有所差别,为了保证装配精度和技术要求采用修配和调节的装配方法,在级进模中先装下模再装上模1子模加工过程中为保证精度往往将凸模固定板,凹模板,弹压卸料板,一起装夹加工,使得装配时各板位置精度准确2调整凸凹模间隙,反复试冲,保证最后间隙均匀3子模装配完之后,将凹模取下与下模架板进行装夹,把型孔位置定出后按凹模孔钻出4上模安装精度由导柱保证
各子模加工完之后,用销钉将其定位在下模架上,再用螺钉紧固,上模由导柱精度保证定位
模架采用可换式导柱导套形式以便快换,而且安装方便上下模板采用加厚钢板。
总
压机FF3.1≥根据各个子模形状中心对称,根据空间力系和合力作用线的求解方法121/abnnn
lxlxlxllX=++∙∙∙++∙∙∙+121/abnnn
Ylylylyll=++∙∙∙++∙∙∙+各个分力对某轴力矩之和等于其合力对同轴之矩的力学原理知力机中心与压力中心基本重合,但存在偏差,但在误差范围内可以忽略。
由于公称压力小,所以选取压力机为J23-3.15
(六、模具零件与结构分析:
模具的每个零件的粗糙度都应在Ra0.8及其以上,所以每个面都需用磨床加工,以保证模具的安装精度及配合精度
1、上下模座
因此模具为级进模,负荷大,受高速冲击,为防止冲压时产生弹性变形,材料以45钢为好,调质处理43~
48HRC。
上模座上平面与下模座下平面平行度为100:
0.012。
上模座上下平面与下模座上下平面平行度约为100:
0.008。
2、导向装置
导向装置采用导柱、导套,导柱采用台阶固定在凸模固定板上,导套采用过盈配合固定在卸料板上及凹模固定板上。
因是大量生产,所以材料选用T8A,渗碳淬硬56~60HRC。
导柱、导套采用过盈配合。
过盈量为0.01~0.15mm,垂直度200:
0.005。
导柱垂直度由导柱台阶保证。
导套的是B型导套(GB4678.7-84,材料选用T10A渗碳淬火58-62HRC,技术条件按GB4678-84的有关规定进行加工。
导柱也选用B型导柱,要求规定同导套。
3、垫块
该模具的受力不大,因此可按情况而定,如果要的话,则应淬火到HRC56-60,用T8A
4、卸料板
卸料板是多工位级进模结构中的关键零件,尤其是在高速冲裁下,凸模会受到冲击负荷作用,对于脆性的硬质合金材料,稍受侧向力,凸模很容易崩刃和断裂,所以卸料板不但起到压料和卸料的作用,还对凸模起到导向保护作用。
卸料板和凸模间的双面间隙为0.005mm,因此卸料板的精度、刚性、耐磨性和它的稳定性就非常重要。
故选用材料CrWMn,淬硬56-60HRC。
由于卸料板有保护凸模的作用,要求卸料板有很高的运动精度,
为此要在卸料板与上模座之间增设辅助导向零件─小导柱和小导套。
制造基准与凸凹模固定板一致,便于三板同时加工。
厚度根据冲压设计材料方面的资料,选取厚度为22.7mm。
5、凹模
凹模材料选用GrWMn,淬火到HRC58-62,在落料凹模镶件上采用焊接的形式,制件生产量较大,所以采用YG15,便于快换用螺钉紧固在下模座上,镶块采用过渡配合H7/m6凹模厚度可按下式进行估算:
(mmHp
=α式中:
αH为凹模厚度(mm
P为冲裁力(N
选取最大工序的冲压力,计算得出:
Ha为22mm
6凹模垫板
凹模垫板是由销钉定位于下模座上,由4个螺钉紧固。
4个销钉再将凹模固定板和凹模板一起固定在下模架上凸模固定板
凸模固定板在冲压时折断,就不必把整副模具拆离压力机,而仅需把损坏部分取下,换上备用凸模即可继续冲压。
固定板与凸模不是过盈配合,是间隙配合,避免由于加工误差使凸模在卸料板中卡死,也可使凸模与凹模孔自动对中,保证间隙均匀,而且是在凸模与卸料板,凸模与
凹模间隙中最大
可根据下式进行计算:
α
HH8.06.0(~=式中:
H为凸模固板厚(mm;
αH为凹模高度(mm。
则凸模高度在12~16mm范围内,
故选取H=16mm。
凸模固定板的上、下表面应磨平,并且应与形孔中心线相垂直。
因是级进模,所以选用材料CrWMn,并淬硬到56-60HRC
7、凸模
凸模采用台阶式固定,因冲缺凸模形状复杂,故采用快换装置,用一固定块将其压紧在垫板上,当凸模磨损或折断等不能再继续加工时,只需拆下紧固螺钉,取出凸模,将准备的备用凸模安装上即可继续加工。
因不锈钢材料力学性能好,所冲形状复杂,故采用焊件结构,在凸模工作部分焊上厚度为4mm的YG15(钨钴类合
金,热处理HRC66~68HRC,其余部分选用CrWMn材料,热处理使其硬度达58~60HRC。
弯曲、整形凸模选用材料Cr12MoV,热处理达61~63HRC。
8、托料钉
托料钉是具有托料和导向双重作用的模具零件,在级进模中应用广泛。
托料钉在设计中最重要的是导向的设计和卸料板凹坑深度的确定。
当送料结束、上模板下行时,卸料板凹坑地面首先压缩导向钉,使条料与凹模面平齐并开始冲压。
当上模板回升时,弹簧将托料钉推至最高位置,进行下一步的送料导向。
当凹坑过深时,会造成带料被压入凹坑内;
当凹坑过浅时,会使带料被向下挤入与托料钉的配合的孔内。
因此设计时必须注意各尺寸的协调,其协调尺寸推荐值为:
槽宽:
th~0.25.1(2=(槽宽即托料钉颈部与凹模板的距离
头高:
mm
h~(35.11=坑深:
hT~(5.03.01+=槽深:
t
~(53=-浮动高度:
h~(度材料向下成形的最大高25.1+=尺寸D和d可根据条料宽度、厚度和模具的结构尺寸确定。
托料钉常选用合金工具钢,淬硬到58~62HRC,并与凹模孔成H7/h6配合。
托料钉的下端台阶可做成装拆式结构,在装拆面上加垫片可即可调整材料托起的位置高度,以保证送料平面与凹模平面平行。
根据公式求得:
h2=(1.5~2×
0.33
取槽宽为0.5mm
头高取2mm
为了保证不让带料被挤入与托料钉的配合的孔内,同时还保证带料不被压入凹坑内,需对托料钉进行改进,改进按图纸所示。
10、导正销
用导正销对带料定位导正,在模具中,第一工位采用侧刃定位,工位数不多,本次采用第五工位跟第七工位导正就可以,在弯曲前加导正与前面侧刃定位结合起来,使带料不产生其他影响。
导正销选用合金材料,淬硬55-60HRC。
11、其它零件
螺钉、螺塞、弹簧等,都根据选取标准,在市场进行采购。
四、模具认识与前景:
我国模具工业从起步到飞速发展,历经了半个多世
纪。
近几年来,我国模具技术有了很大发展,模具设计与
制造水平有了较大提高。
大型、精密、复杂、高效和长寿命模具技术又上了新台阶。
大型复杂冲模以汽车覆盖件模具为代表。
我国主要汽车模具企业,已能生产部分轿车覆盖件模具。
体现高水平制造技术的多工位级进模具覆盖面大增,已从电机、电器铁芯片模具扩大到接插件、电子元器件、汽车零件、空调器散热片等家用电器零件模具上。
塑料模方面已能生产86厘米、122厘米大屏幕彩电塑壳模具、大容量洗衣机全套塑料模具及汽车保险杠和整体仪表板等塑料模具。
塑料模热流道技术更臻成熟,气体辅助注射技术已开始采用。
压
铸模方面已能生产自动扶梯整体梯级压铸模及汽车后桥齿轮箱压铸模等。
模具质量、模具寿命明显提高,模具交货期较前缩短。
模具CAD/CAM技术相当广泛地得到应用,并开发出了自主版权的模具CAD/CAM软件。
电加工、数控加工在模具制造技术发展中发挥了重要作用。
模具加工机床品种增多,水平明显提高。
快速经济制模技术得到了进一步发展,尤其是这一领域的高新技术快速原型制造技术(RPM进展很快,国内有多家企业已自行开发出达到国际水平的相关设备。
模具标准应用更加广泛,品种有所扩展。
模具
材料方面,由于对模具寿命的重视,优质模具钢的应用有较大进展。
在“八五”、“九五”期间,我国已有一大批模具企业推广普及了计算机绘图技术,数控加工的使用率越来越高,特别是以生产家用电器的企业为代表,陆续引进了相当数量的CAD/CAM系统。
如美国EDS的UGⅡ;
美国ParametricTechnology公司的Pro/Engineer等大型软件。
我国自主开发的CAD/CAM系统也有很大发展,主要有北航海尔公司的CAXA,华中理工大学开发的注塑模HS3.0系统及CAE软件,上海交大模具CAD国家工程中心开发的冷冲模CAD系统,还有如橡胶模具计算机辅助工程国家工程研究中心开发的橡胶模具CAE技术应用软件Z–MOLD等。
从我国整个模具工业的发展趋势来看,虽然经过改革开放20年来的努力,在飞速缩小与先进国家的差距,但这个差距还是明显的。
不论是设计水平还是制造工艺水平方面,都还需急起直追,例如我国目前模具产品的自给率仅为70%,产品的专业化、标准化程度低,先进制造技术NC、CNC加工设备层次低、数量少,开发利用率低,CAD/CAM技术采用不普遍,其他如大型化、精密化模具、多功能复合模具、
热流道塑料模具、气体辅助注射模具、高压注射成型模具以及快速经济模具产品开发亟待发展。
另外,模具设计与制造先进工艺的引进和普及也势在必行,如模具优质材料的应用及先进的表面处理和智能化、自动化抛光技术、快速原型制造技术(RPM、模具高速扫描及数字化系统、模具加工柔性同步系统等。
才能尽快地缩小我国模具工业与发达国家间的差距。
五、设计总结
通过这次毕业设计,让我收获颇多,首先是进一步明确了模具设计与制造的工作步骤:
(1收集资料,确定模具设计任务书;
(2作初步的草图,并作简单的分析;
(3批准设计思想,确定设计方案及步骤;
(4完成设计,包括零件图,并定尺寸;
(5核对图纸完成说明书。
在设计过程中,采用AutoCAD制图软件绘图,现在AutoCAD绘图能力也显著提高,画图能达到快而准,还学会使用CAXA电子图版2005软件。
在说明书的录入过程中,学会
了如何利用Word文档编辑公式、插入图形等操作。
由于资料有限很多资料都是从网上收寻。
在三年的模具学习中,我们学习了一定的理论基础,在这次设计上都有运用,在这副模具上,模具的定位要求十分精确,制件的尺寸小。
在设计中还得考虑实际加工问题,否则就是模具设计理论上完全合理,在生产部门上,达不到你的要求,那设计出来的模具就是一个幻想。
要设计出一副完整的能投入生产使用的模具,还得在今后的生活中不断努力学习,积累经验和教训。
此次毕业设计网上查阅了许多相关的资料,在设计过程中通过E-mail向胡志华老师请教与指导,在此表示诚挚的感谢!
参考文献:
冲压工艺与模具设计/成虹主编。
北京:
高等教育出版社,2002.7
模具设计与制造实训教程/李学锋主编。
化学工业出版社,2004.7
多工位级进模设计/王俊彪西安:
西北工业大学出版社,1999-O1.
《AUTOCAD软件教程》
网上搜寻课程《中国模具设计大典:
第3卷冲压模具设计》
成都电子机械高等专科学校毕业设计论文互换性与技术测量(第四版)。
中国计量出版社2000.1第四版21