汽机专业事故分析.docx
《汽机专业事故分析.docx》由会员分享,可在线阅读,更多相关《汽机专业事故分析.docx(40页珍藏版)》请在冰点文库上搜索。
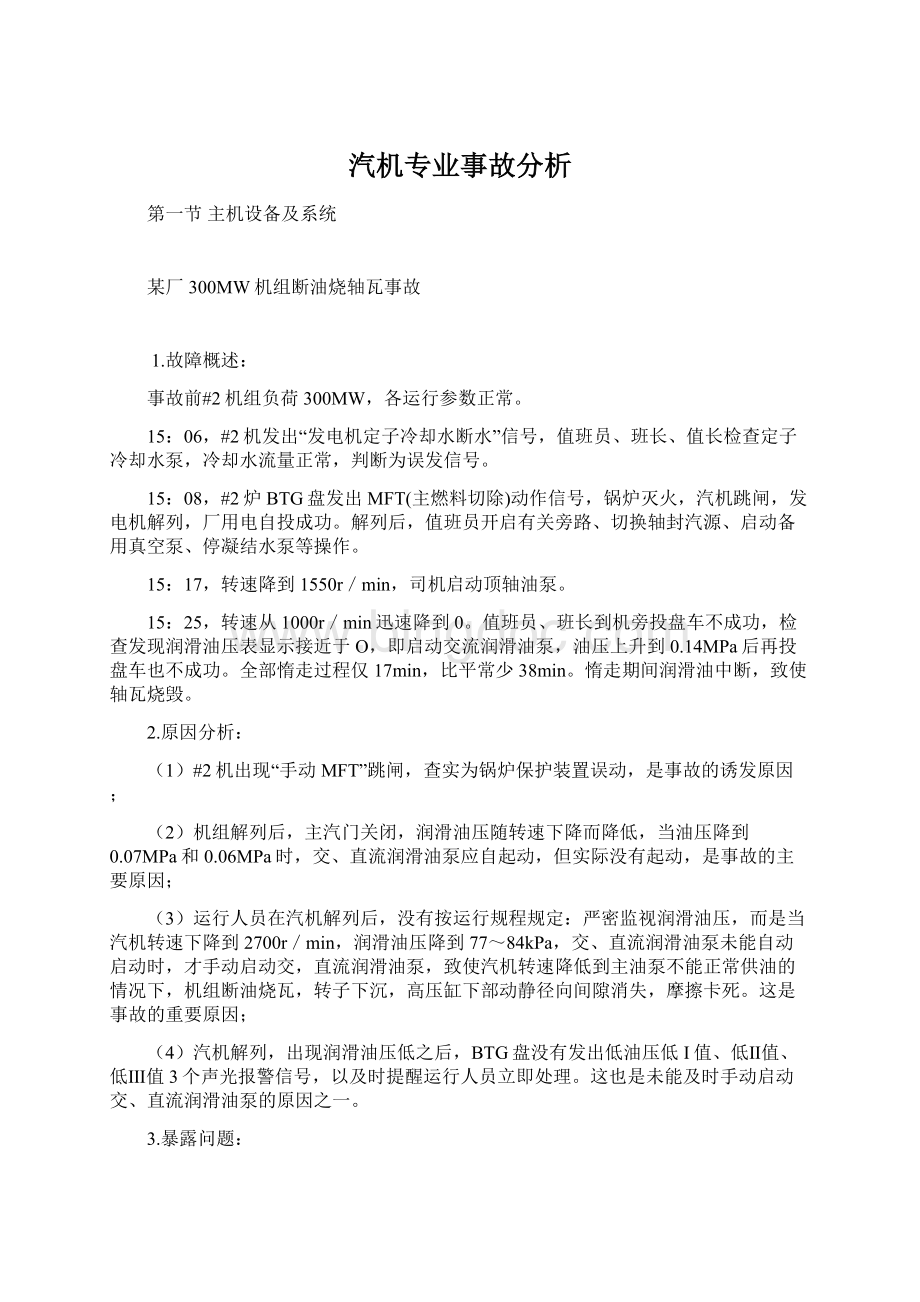
汽机专业事故分析
第一节主机设备及系统
某厂300MW机组断油烧轴瓦事故
1.故障概述:
事故前#2机组负荷300MW,各运行参数正常。
15:
06,#2机发出“发电机定子冷却水断水”信号,值班员、班长、值长检查定子冷却水泵,冷却水流量正常,判断为误发信号。
15:
08,#2炉BTG盘发出MFT(主燃料切除)动作信号,锅炉灭火,汽机跳闸,发电机解列,厂用电自投成功。
解列后,值班员开启有关旁路、切换轴封汽源、启动备用真空泵、停凝结水泵等操作。
15:
17,转速降到1550r/min,司机启动顶轴油泵。
15:
25,转速从1000r/min迅速降到0。
值班员、班长到机旁投盘车不成功,检查发现润滑油压表显示接近于O,即启动交流润滑油泵,油压上升到0.14MPa后再投盘车也不成功。
全部惰走过程仅17min,比平常少38min。
惰走期间润滑油中断,致使轴瓦烧毁。
2.原因分析:
(1)#2机出现“手动MFT”跳闸,查实为锅炉保护装置误动,是事故的诱发原因;
(2)机组解列后,主汽门关闭,润滑油压随转速下降而降低,当油压降到0.07MPa和0.06MPa时,交、直流润滑油泵应自起动,但实际没有起动,是事故的主要原因;
(3)运行人员在汽机解列后,没有按运行规程规定:
严密监视润滑油压,而是当汽机转速下降到2700r/min,润滑油压降到77~84kPa,交、直流润滑油泵未能自动启动时,才手动启动交,直流润滑油泵,致使汽机转速降低到主油泵不能正常供油的情况下,机组断油烧瓦,转子下沉,高压缸下部动静径向间隙消失,摩擦卡死。
这是事故的重要原因;
(4)汽机解列,出现润滑油压低之后,BTG盘没有发出低油压低I值、低Ⅱ值、低Ⅲ值3个声光报警信号,以及时提醒运行人员立即处理。
这也是未能及时手动启动交、直流润滑油泵的原因之一。
3.暴露问题:
(1)机组在基建调试阶段,对汽机润滑油系统这样重要的设计变更,未经会签和审批就予实施,暴露了管理不严;
(2)调试工作不完善,如润滑油系统在静态、动态低油压试验中,均没有发现机组解列、主汽门关闭后,交、直流润滑油泵低油压不能自起动的重大隐患;
(3)机组移交生产后,未能及时组织人员复核图纸和设计变更单,以致润滑油系统设计变更错误一直没有发现,酿成重大设备事故;
(4)运行岗位新人员多,缺乏实际经验,事故处理能力较差。
4.防范措施:
(1)设计部门必须切实加强设计工地代表的管理,对工地代表在现场变更重要设计、主要的自动装置和保护,必须严格审批,加强管理;
(2)新设备投产前的调试、试运行和验收工作,必须按《电力工业技术管理法规》有关规定,对设备的主保护、自动装置、重要保护及自动装置尚未投入或不完整的,不准起动,不予验收;
(3)运行中的汽轮机交、直流润滑油泵及其低油压自起动装置,必须经常处在良好状态。
没有自起动装置或自起动装置不完善的机组,不允许起动,运行中的机组必须立即安排处理;
(4)运行中汽轮机的交、直流润滑油泵,其低油压联锁起动开关必须在投入位置,不得随意退出;
(5)运行中交、直流润滑油泵及其低油压自起动装置应每周试验一次。
每次正常停机前要进行试验;停机后,在主汽门关闭工况下也要进行试验,以检查自启动功能是否正常;
(6)停机时,应设专人监测润滑油压和轴瓦温度,随转速的下降及时投入交、直流润滑油泵。
运行人员必须熟悉交、直流润滑油泵失常情况下的紧急处理方法;
(7)新投产及大修后的机组,专业技术人员要全面审核图纸和设备变更情况,查核各种保护完备,各自动装置可靠,各定值准确,一旦发现隐患,立即消除,防患未然。
某厂机组跳闸润滑油中断化瓦事故
1.故障概述:
某厂#1号机系上海汽轮机厂生产的N300—17/538/538型亚临界压力凝汽式机组,1996年5月14日10:
05热工车间程控班在循环水泵房(海水冷却)就地解除B循环水泵“润滑水压力低”保护时,因措施不当,导致B循环水泵跳闸,A循环水泵未联动投入,#1号机因失去冷却水低真空保护动作跳机。
当汽轮机惰走到1247r/min时,直流润滑油泵跳闸(交流润滑油泵正在检修、不能投用),跳闸后无任何信号发出,运行人员通过油压指示和开关指示灯发现直流润滑油泵跳闸,采取了以下处理措施:
(1)立即强开直流润滑油泵,但未成功;
(2)立即开A、B、C顶轴油泵,因油压低,于10:
19跳闸;(3)10:
21电气运行人员收回交流润滑油泵工作票,此时汽轮机转速为320r/min。
汽机运行人员开启A、B、C顶轴油泵;(4)电气运行人员打开直流润滑油泵就地控制箱,复归一下热偶保护。
10:
24启直流润滑油泵;(5)10:
22汽轮机惰走静止,投盘车跳闸,立即手动盘车约100度。
事故造成汽轮机主轴承报废、动叶片磨损严重。
少发电量18000万kW·h。
到6月20日12:
O0恢复。
2.原因分析:
(1)热工人员解除B循环水泵橡胶瓦“润滑水压力低”保护时,由于措施不当,造成保护动作,B循环水泵跳闸,A循环水泵因润滑水压力低不自投,引起主机低真空保护动作是跳机事故的直接原因,也是主机化瓦事故的起因;
(2)热工人员在联系解除循环水泵保护时,当值值长安排运行方式不当,措施不力,为事件的扩大埋下了潜在的隐患;
(3)直流润滑油泵热偶保护误动,系热偶保护离散性大、不可靠造成的;热偶保护动作应接发信号而施工错接跳闸,引起直流润滑油泵跳闸、润滑油中断化瓦。
因此,直流润滑油泵跳闸是#1号机化瓦的直接原因;
(4)从技术管理上看,厂及职能部门在生产管理上,在执行各种制度上不严、不细、有漏洞;主辅机主要保护停、服役管理制度不完善;工作票执行不严格,投、停保护使用工作票范围不明确。
3.防范措施:
(1)立即修订“重要辅机设备停复役制度”,对影响主机安全运行或重要辅机消缺,必须填写“设备停复役”申请单,办理工作票后执行;
(2)按#1号机设计图纸将主机直流润滑油泵控制接线核对改为正确接线。
某厂#6机组冲转造成#3、#4瓦化瓦
1.故障概述:
#6机在首次冲转过程中,当转速提升至600转/分钟做摩擦试验后,再次升速至300转/分钟左右时,#3瓦金属温度突然瞬间升至130℃,强行打闸停机,经揭瓦处理后再次冲转至2937转/分时,#4瓦金属温度升至118℃,打闸停机揭瓦检查并处理。
2.原因分析:
#3、#4瓦瓦温升高的主要原因为:
安装时工艺较差,下轴瓦顶轴油孔和顶轴油管冲洗不干净,导致杂物进入瓦内,#3、4瓦轴系标高偏高。
3.防范措施:
经过对#3瓦下瓦修刮处理,降低#3、4瓦轴系标高,更换#4瓦两块下瓦后,机组启动正常。
某厂#2汽轮机高压缸叶片断裂
1.故障概述:
#2汽轮发电机组于2003年6月6日5:
16冲至3000rpm后,各轴瓦振动均很小,其中最大轴振为#2瓦,轴振为63.3μm,在机组稳定了20分钟后,#2瓦轴振瞬间升至490μm,同时造成#1、#3瓦轴振超过跳机值造成跳机,此时就地测量瓦振很小,最大不超过10μm,跳机后汽轮机转子的偏心达到188μm。
指挥部根据以上现象初步认为造成振动的原因为动静摩擦,一般造成这种动静摩擦的原因为汽封间隙偏小,这可以通过汽轮机长时间的运转消除掉,所以决定转子偏心降至合格后再进行一次冲转。
同时为了预防由于振动探头松动而传送虚假信号的现象,在第二次冲转前对探头进行了检查。
在经过9小时盘车后,转子偏心将到了54μm,15:
06大机开始第二次冲转至1268rpm因#2瓦振动超标未能成功,停机后转子偏心达到了290μm。
6月7日进行第三次试冲转至1100rpm,#2轴承振动达160μm,继续升速振动增长较快,对振动原因进行了认真仔细的分析讨论,认为可能造成振动的原因有两个:
一是由于疏水不畅造成汽轮机积水;二是转子上有大质量的东西脱落。
由于第二个原因需揭开高压缸检查,工作量太大,因此一致同意先对高压缸有关的疏水系统进行全面检查,必要时进行割管检查。
在其后的8日至10日,电建公司对与高压缸相连的所有疏水系统主要包括高压缸第一级疏水管道、高压外缸疏水管道、左右侧高压导汽管疏水集块节流孔、高压缸前后轴封底部疏水管道、一抽电动门前疏水管道进行了检查,同时对汽轮机前、中轴承座进行了解体检查,未发现有影响振动的问题。
检查结束后于6月11日上午9:
36开始冲转,冲转时在汽轮机前、中轴承座及各疏水阀门处均设专人监护,在9:
48转速升至1256rpm时,#2瓦振动超过了254μm跳机值,10:
52投上盘车,此时转子偏心为50μm。
由于未解决#2瓦轴振的原因,指挥部决定将高压缸进行解体检查。
待缸温冷却后,6月13日晚11:
00将高压外上缸揭开,发现高压缸排汽侧端部汽封上有大量的金属粉末,在6月14日7:
00揭开上半高压隔板套,发现高压转子第5级动叶有一组叶片的围带已经脱落,同时该组叶片脱落了一只,叶片根部已经损坏,脱落的叶片及围带没有找到,只发现了有几个小的金属碎片,第5级隔板叶顶汽封已经全部磨化。
2.原因分析:
此次事故由高压转子第5级动叶末叶片及相应的一组围带脱落所致,为厂家制造原因。
3.防范措施:
(1)正常运行中和汽机冲转时就地严格检查、监视,仔细观察汽机内部声音及振动情况,发现振动、声音不正常时应立即汇报、分析查找原因;
(2)当振动随转速的增长而增长、随转速的降低而下降明显,且稳定转速增加暖机时间无效时,应对汽缸内部检查和分析;
(3)检修专业提高检修工艺,提高安装水平。
某厂通风阀未开高压缸闷缸运行造成转子损坏
1.故障概述:
某电厂600MW机组汽轮机为日本日立机组,为亚临界,一次中间再热,单轴,三缸四排汽,冲动凝汽式。
设计额定功率为600MW,汽轮机总级数为42级,高压转子有9级,其中第一级为调速级,中压转子有5级,低压转子有2×2×7级。
汽轮机采用高中压缸合缸结构。
2003年3月15日,9:
15汽机第一次冲转,采用中压缸方式,经过200RPM最小摩擦检查和中速暖机,14:
26汽机定速3000rPM,机组最大轴振36μm,最高瓦温87.1℃。
机组定速后进行了润滑油压力调整,事故润滑油泵联启试验,就地和主控打闸试验,闭锁阀闭锁试验,主跳闸电磁阀试验,DEH在线试验及推力瓦磨损试验,然后开始电气试验。
20:
06“高压缸排汽金属温度高”动作,汽机跳闸。
停机后,对引起高排温度高跳机的原因进行了检查,发现是因CV1关闭行程开关未正确闭合,引起通风阀关闭,造成高压转子闷缸运行所致。
闷缸发生后,甲方、调试方、建设单位、日立方对闷缸情况进行了分析,对日立提供的通风阀逻辑作了进一步确认,确认是由于机组远方打闸试验时,CV1阀门已关闭(该阀门在电调操作画面上的反馈指示已到0),但关闭节点没有回来,导致高压缸通风(也称VV)阀非正常关闭,引起的高压缸闷缸。
经分析,未发现闷缸运行对机组造成根本性损坏,遂决定机组继续试运。
3月16日16:
47汽机第二次冲转,为中压缸方式的温态启动,1700r/min过最小临界时#2瓦轴振曾达14丝,当时认为汽封可能有碰磨,渐渐振动又恢复正常。
定速后#2瓦振动由7.4丝慢慢降到4.4丝,随即进行发电机短路试验、发电机空载试验、发/变组短路试验(缺高厂变)、励磁系统闭环试验等电气试验,进行了润滑油压调整,完成变油温试验、变真空试验、旁路扰动试验,3月17日16:
12正常停机,锅炉进行蒸汽严密性试验,安全阀整定等工作。
其后根据调试工作安排,又进行了两次冲转,完成了升压站电气试验、超速试验等试验工作,但负荷根据需要一直未超过450MW。
4月16日进行机组大负荷试运。
试着将负荷由450MW升至600MW,此时调节级压力13.858MPa,一抽压力6.888MPa,GOVSET98%,CV1,CV2,CV3都全开,CV4开度至56%,发现机组出力受阻。
由于空预器非金属膨胀节漏热风直吹电机动力电缆导致温度升高,4月16日14:
44正常计划停机处理缺陷。
发现机组出力受阻后,在现场进行了多次查找和分析工作,基本排除了由于系统问题引起高压缸效率严重下降,出力不足且阻力增大的可能。
结合第一次开机曾发生高压缸闷缸运行的现象,决定对高压缸开缸检查,5月2日高压缸揭开后发现,高压缸转子的4、5、6、7、8级损坏严重,远远超出了预期的想象。
经与日立公司协商,决定更换机组高中压转子和高压隔板。
5月19日#1机组高压缸抢修工作结束。
影响调试工期30天。
2.原因分析:
(1)汽机第一次冲转做机组远方打闸试验时,CV1阀门已关闭(该阀门在电调操作画面上的反馈指示已到0),但关闭节点信号没有回来,导致高压缸通风(也称VV)阀非正常关闭,引起高压缸闷缸,鼓风摩擦产生热量造成高压转子过热损坏;
(2)调试人员及运行监视人员没有及时发现高压缸通风阀不正常状态,使汽机在故障状态下长时间运行。
造成设备损坏。
3.防范措施:
(1)机组调试期间,调试措施应针对具体工作所涉及的操作,列出相应的危险点监控措施,有关技术管理人员与操作人员应认真学习;
(2)业主、监理与建设单位应加强协调,从采购、保管、安装环节把好关,确保设备动作可靠性,尤其是重要的,涉及机组安全运行的热工保护接线和位置开关、流量计、压力开关等环节,必须保证可靠性;
(3)做好生产准备期间运行人员技术培训工作,提高操作人员业务素质;运行人员应熟练掌握机组热工联锁、保护逻辑与定值,能够及时发现故障苗头并采取正确及时的措施。
某厂汽轮机低压缸严重变形事故
1.故障概述:
某厂#3机组于1997年8月5日首次冷态启动,汽机共启动40次,于1997年10月16日17时完成“168”试运,于10月17日补做了50%、100%甩负荷试验(因汽机转速不能控制在3300r/min以内,试验不成功)。
于10月18日一10月19日进行了500kV系统单相接地短路试验。
后于10月19日13时31分重新并网。
10月20日20:
00因500kV线路对端保北站500kV侧做投切电容器试验,造成发电机进相运行,#3号发电机失磁保护动作解列,跳开500kV侧主开关,高低旁路快开,发电机带厂用变运行。
因汽轮机转速不能维持3000r/min,先升到3250r/min,后降到2800r/min,14秒钟后发电机低频保护动作停机、停炉,厂用电快速切换装置启动,但因启动变差动保护误动跳闸,强送启动变开关不成功,造成厂用电失电,柴油机自启动成功,直流润滑油泵和直流密封油泵自启动成功。
因高低旁路保护快关失灵,手动强关无效,锅炉主汽门失去电源无法操作,使高温蒸汽进入排汽缸,造成低压缸及小汽机排汽安全门动作。
直至仪表空气压力降至高低旁阀门自关设定值,20:
14高压旁路关闭,20:
24低压旁路关闭。
20:
16汽机转速到零,多次启动盘车,因盘车马达热偶动作不成功,强行人工手动盘车使转子转动45度。
其间多次强投电动盘车并于21:
17就地强投盘车成功,当时大轴偏心率为74μm,后稳定为52.6μm(规程规定为不大于66μm)。
22:
10恢复启动变运行,厂用电带电。
事故停机后,厂部于21日、22日连续两次召集生产、基建部门、施工单位、制造厂家代表、调试队专业人员开会,会议讨论了#3机停机消缺项目。
并针对“10.20”事故情况增加了检查项目,仅考虑到事故中,#3号机组凝汽器进入带压蒸汽后转子惰走了16分钟,认为高温蒸汽可能损坏凝汽器管子及胀口,大轴偏心率已达到规程要求,盘车亦正常,未认识到高温蒸汽可能引起低压缸体变形,决定除按原订168小时后消缺计划进行外,增加检查项目:
(1)#2号瓦、#5号瓦揭盖翻下瓦检查;
(2)凝汽器不锈钢管检查,胀口检查;(3)低压缸内主要焊缝外观检查;(4)联通管内不锈钢伸缩节外观检查;(5)低压末级叶片外观检查;(6)凝汽器压水试验。
10月28日,在2号瓦揭盖检查时发现瓦口两侧间隙不对称,左侧偏小,右侧偏大,按照制造厂家代表的建议,由施工单位将2号瓦左移了0.12mm,其它检查项目未见异常。
11月14日,厂部组织会议重点布置#3号机启动准备工作,会议确认#3机预订消缺项目全部完成,增加的检查项目未发现异常,决定即日开始启动准备。
1)11月16日机组启动。
本次启动共冲车四次,第一次冲至1200r/min,因胀差大打闸;第二次冲至950r/min,因高中压后轴封处碰磨,#1瓦轴振达250μm跳机,处理变形阻汽片并盘车至偏心率合格后;第三次冲至3000r/min;除1瓦轴振163μm外,其他各瓦均小于50μm,后因励磁系统故障,励磁开关跳闸停机;第四次冲至3000r/min,因#1瓦轴振大,达183μm,且有上升趋势,决定打闸停机检修。
惰走时间57分钟(未破坏真空),就地偏心指示O.035mm。
本次启动后,根据现场听音和#1号瓦振动数据分析,依据振幅不是常数,在同一转速下振幅发生变化,过临界时振幅无明显变化且只有#1号瓦振动较大,其余各轴振正常的现象,认为振动的主要原因为高压缸1号汽封碰磨,未认识到低压缸变形引起对轮中心变化,导致振动增大的问题。
经电厂、施工单位、制造厂共同研究,决定撤去上次消缺中对#2瓦加上的120μm垫片,恢复到原试运状态,再用低参数启动一次,并测量振动数据(相位、频谱、波形)。
2)11月26日机组再次启动,启动前请电研所协助加装了振动监测仪表。
升速至950r/min时,#1瓦轴振明显增大,达185μm,立即降速至500r/min,#1瓦轴振下降至110μm,再次升速至600r/min时,#1瓦轴振又升至150μm,其余各轴振正常,鉴于#1瓦轴振振动仍较大,决定打闸停机。
经与厂家代表研究并报公司领导批准,决定解体检查。
重点解体检查高中压缸和复查A、B对轮中心,在复查对轮中心时才发现低压缸变形下沉问题,进而扩大为解体检查低压缸。
2.原因分析:
(1)事故发生的起因为500kV系统在投电容器组(400Mvar)时引起发电机进相,系统低频振荡(约1Hz)造成发电机失磁保护动作解列,对线路投电容器造成的影响,事先认识不足。
对500kV系统振荡可能引起跳机缺乏思想准备和措施落实。
(2)事故扩大的直接原因是高、低旁路在事故全停后保护快关及手操均失灵,加之因失去厂用电,减温水及循环水同时中断,造成汽轮机低压缸超压、超温。
高、低旁路没能按指令及时关闭,经检查为气源管路含水(设计只有一级冷冻式干燥器,空气系统未设计放水点,疏水器堵塞不好用),造成内壁锈蚀,引起旁路气动阀堵塞所致。
仪表空气管道设计为普通碳钢管,受潮腐蚀后影响空气品质。
按“火力发电厂热工自动化设计技术规定CNOGJl6—89”规定,应采用不锈钢管。
(3)厂用电保护不完善,启动变差动误动,电气和热工设计匹配错误,造成厂用电系统全停,也是事故扩大的原因。
电气设计失磁保护动作解列,发电机带厂用变运行,不启动厂用电切换,而热工设计机炉控制又无甩负荷后带厂用电的功能。
加之汽机调速汽门调节参数尚未经甩大负荷验证。
在本次发电机甩负荷带厂用电后,机组转速波动很大,先超速至3250r/min,又降速到2820r/min,致使47Hz低频保护动作联跳机、炉。
发电机低频保护动作灭磁并停机停炉后,启动中压切换。
因主机已解列14秒,同期不满足,不能快速切换,只能慢速切换,6kV所有厂用电动机自启动(因为6kV母线低电压保护设计不完善,设计变更落实不及时,当时还没有投入使用),复杂的自启动电流造成启动变差动保护误动,致使厂用电失电。
在检查、恢复启动变时,又因合闸回路电缆端子接触不良,延误了恢复时间。
(4)经初步分析,引起汽轮机损坏和振动的原因为:
a、由于高温蒸汽进入低压缸,由钢板焊接而成的低压缸超温,引起不规则变形,连在低压缸上的#3、4瓦座发生变形,致使轴系中心偏差超标,造成动静碰磨;
b、由于制造质量原因,加之运行工况的变化,焊接结构的静叶在运行中开裂脱落,并与转子碰磨。
另外,低压转子A侧封头脱出并与高压转子发生轴向碰磨,也可能引发轴系振动。
3.暴露问题:
(1)对该厂双机单线500kV长线路(约200km)的运行方式缺乏经验,对系统运行稳定性估计不足,对500kV系统低频振荡缺乏事故预想和措施落实;
(2)对排汽缸超温的严重后果认识不足和缺乏经验。
认为在事故当时低压缸有蒸汽的工况下,惰走了16分钟,盘车启动后偏心率不大,而且逐渐回到了厂家允许值,轴系和转子就不会有问题。
因此只对排汽缸、凝汽器和轴瓦作了外观检查,未及时核查轴系中心和进一步揭缸检查,延误了检修时间,造成了重大损失;
(3)在基建调试转入试生产的过程中管理不力。
对基建调试工作中发现的问题,要求不严,处理不及时。
对热工、电气保护逻辑设计上的一些问题,未能及时发现;对调试中的电气保护投入率重视不够,以致6kV厂用低电压保护因设计不合理,二次订货不及时,直至“168”后还未投入;对仪用空气带水,汽轮机调速系统不稳,厂用保安电源薄弱等威胁安全生产的设备、设计问题,虽然从思想上意识到了,但处理力度不够,落实不果断,以致造成严重后患。
完成“168”后立即转入试生产,从熟悉设备、组织消缺、图纸资料和专用工具移交等方面,基建向生产的过渡不力;
(4)事故后的两次启动缺乏经验,暴露了我们的安全思想不牢固,考虑问题不全面。
在第一次启动中,由于思想上重视不够,没有加装振动相位频谱等监测仪表,在几次冲车振动较大时,只是根据听音和振幅分析就认为是汽封碰磨。
尤其是在第一次启动失败后,未经严密的科学分析,就作出了撤下120μm垫片再试的决定。
4.防范措施:
(1)进一步加强对单长线路双机运行方式的研究,联系省中调所、电研所委托电科院对500kV线路在不同运行工况下的稳定和可能产生的低频振荡进行分析试验。
并投入PSS(电力系统稳定器),在未取得正式结论前,采取投入电抗器,调变压器分接头,停投电容器等临时性措施;
(2)对#3机的热工、电气保护逻辑进行整理,对只解列不灭磁和旁路动作等不合理的设计进行改进,并在下次启动前逐项进行传动核实;
(3)为改善汽机转速调节特性,下次启动前将由省中调所、东汽、电厂共同配合,进行进一步调整试验;
(4)对厂用电系统进行完善化工作;
(5)改善仪用空气质量。
确保冷冻式、再生式干燥器运行正常,并对汽机侧仪表空气加装再生式干燥器,在仪表空气系统的低点、死点加装排水阀,制订定期排放制度。
确保冷冻式干燥器运行正常。
机侧加装再生式干燥器,炉侧加装放水点8处,机侧将8个损坏的疏水器改为放水门,制定排放制度。
某厂#1机#6轴振大原因分析
1.故障概述:
10月23日11:
05,#1机组第一次冲转3000r/min定速后,#6瓦振0.026mm,#7轴振0.061mm;10月23日17:
10,第二次冲转3000r/min定速后,#6瓦振0.0439(MAX0.0792)mm,#7轴振0.0515mm;
10月25日23:
40,第五次冲转3000r/min定速后,#6瓦振0.044mm,#7轴振0.056mm;
10月26日00:
22,机组第一次并网后,#6瓦振0.0626mm,#7轴振0.0566mm;9:
00机组超速试验前,#6瓦振0.0652mm,#7轴振0.0545mm;
10月29日机组3000r/min定速后,#6瓦振0.061mm,#7轴振0.054mm;并网后230MW负荷,#6瓦振0.0747mm,#7轴振0.0638mm;
10月30日310MW负荷,#6瓦振0.075mm,#7轴振0.0643mm;
上述记录表明机组从第一次冲转到现在#6瓦振、#7轴振,分别增大0.01~0.02mm。
2.原因分析:
机组从第一次冲转冷态到现在的带负荷50%,整个汽缸温度水平已提高很多,汽缸膨胀由冷态的4.1mmm/3.8mm到现在的32mm/30.2mm。
造成振动大的原因可能有:
(1)#6瓦及低压转子与发电机对轮联轴器冷却效果差,鼓风摩擦损失大