注塑机的基本参数Word文件下载.docx
《注塑机的基本参数Word文件下载.docx》由会员分享,可在线阅读,更多相关《注塑机的基本参数Word文件下载.docx(12页珍藏版)》请在冰点文库上搜索。
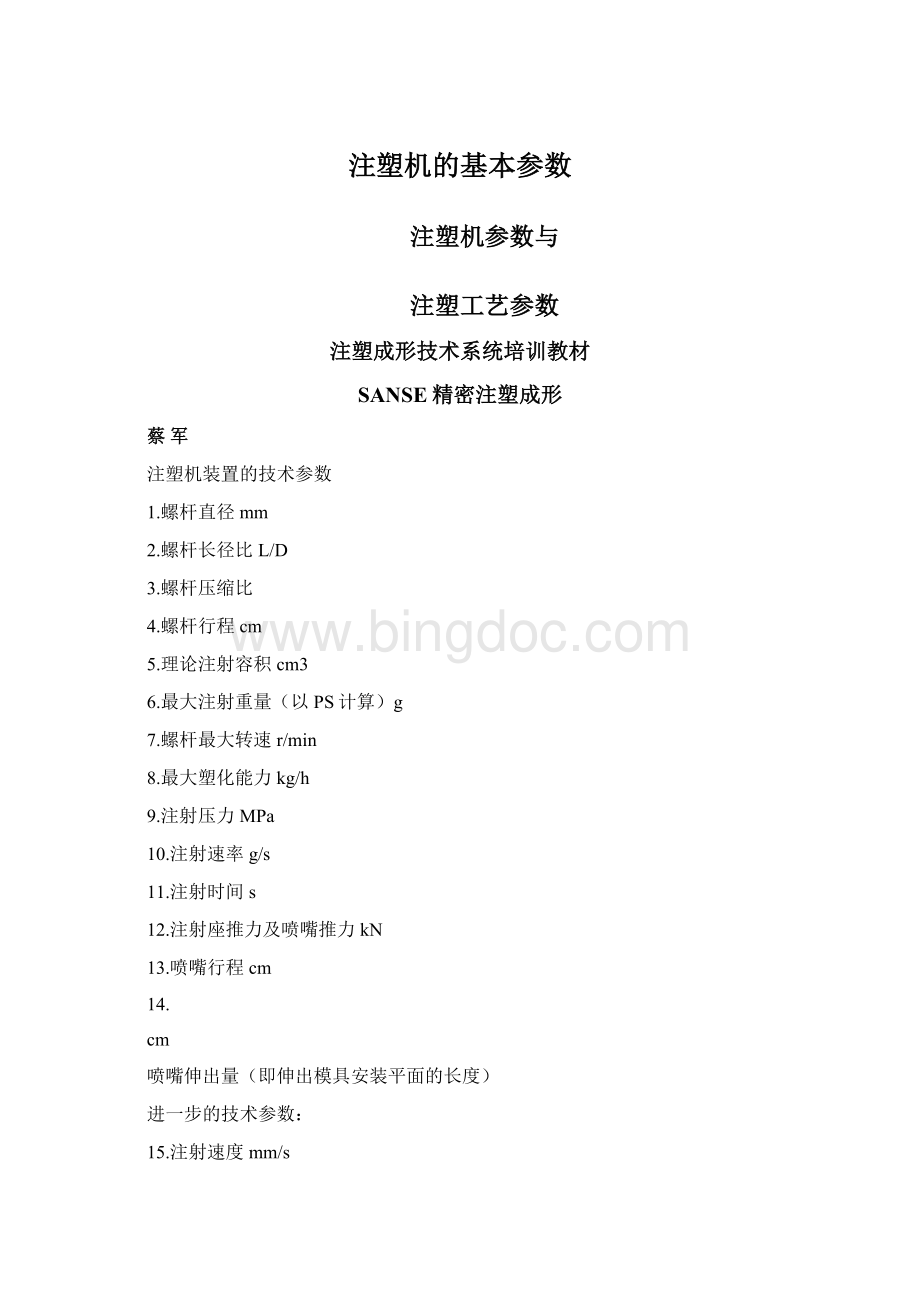
11.模板尺寸(H*V)mm
12.模具安装尺寸
可进一步提供的参数:
13.拉杆直径mm
14.调模驱动功率kN
15.调模方式:
如手动、电动、液压、马达等。
16.合模方式:
如机械式、液压式、机械-液压式等。
17.顶出方式:
机械、液压、气动等。
18.顶针数量
19.顶出次数
20.顶针速度
其它整机性能参数
1.油泵马达功率kN
2.
电热量kW
3.
油箱容量L
4.
料斗容量kg
5.
外形尺寸(长*宽*高)
6.
机器重量kg
7.
空循环时间s
8.
单耗Kw/kg
9.
最大油泵压力MPa
10.
总用电量kW
与成形工艺有关的参数
1.最大的注射量(通常要求制品及浇注系统所需塑料量为注射重量75%-80%)
2.合模力(足够的合模力才能保证成形模具的锁紧,精密制品需要的合模力为模具所需合模力的1.5倍)
与模具有关的参数
1.嘴头部球面半径
2.模板上的定位孔
3.拉杆间的有效间距
4.模具的厚度
5.模板上模具安装螺孔(或T形槽)的尺寸
与取出制品有关的参数
1.合模距离必须小于注塑机的最大开模距离,确认最大开模距离
2.顶出装置及顶出行程距离的确认和顶杆位置及顶杆数量的确认
与机器安装有关的参数
1.总用电量的确认
2•贮油箱容量的确认
3.注塑机外形尺寸的确认
4.整机重量的确认
5.冷却介质的确认
螺杆结构形式的选用
渐变形螺杆是一种有较长压缩段的螺杆,塑化时能量转换较为缓和,主要用于非结晶型材料,如:
PVC、PSHIPS等。
突变形螺杆是一种压缩段较短的螺杆,塑化时能量转换较为剧烈,主
要用于结晶型的材料,如PA、PET、PP、PE、POM等。
通用型螺杆是一种介于渐变形和突变形之间的螺杆,对于经常更换塑
料的机器,可以避免更换螺杆的麻烦,同时降低机器成本,通常选用通用型螺杆,适当调节成形工艺参数,基本上可以满足多种塑料的成形加工。
注塑工艺及主要工艺参数
注射操作过程
注射过程大致可分为:
预塑化、合模、注射座前移、注射、保压、注射座复位、制品冷却、开模、制品顶出等动作组成的周期动作过程
注射部分的工艺参数
(1)注射量:
(通常指一次注射的体积重量),在保压阶段中,料筒存料区要有一般为1.5-2.5mm的射出残量,以保持压力及补缩•防止制品出现各种各样的品质缺陷。
(2)注射压力:
是指注射时作用在螺杆头部熔体上的压力。
给予熔体一定的速度,并对熔体压实。
注射压力受下列因素影响:
A.影响熔体流动性能的因素如熔体指数Ml、塑料温度、
模具温度、注射速率等。
B.影响流动阻力因素如制品和浇口的形状和尺寸、模具流道等。
C.对制品尺寸精度的要求。
根据目前注射压力合使用的实际情况,注射压力选取可按下列原则:
i.加工流动性好的,形状简单的厚壁制品注射压力可v70Mpa
ii.加工粘度较低、形状一般、精度有一般要求的制品可取
70-100Mpa的注射压力。
iii.加工中等粘度如PS、PC、PP、等塑料,制品形状一般,对精度有一定要求的,注射压力可取100-140Mpa.。
iv.加工高粘度如PMMA、PPO、PF、等塑料,薄壁流动长,制品壁厚不均匀且精度要求高的制品,注射压力可取140-180MPa,
对加工优质精密微型制品注射压力可高达230-250MPa以上。
⑶注射速度:
为了把熔体充满模腔,制得密实,精度高的制品,必须在短时间内把熔体快速充模。
用来表征熔体充模快慢的参数除速度外,还可用注射速率、注射时间表示。
注射速度慢,熔体充模时间长,这样就容易产生接缝线、密度不均,内应力大等不良现象。
注射速度高,可以减少充模时间,从而减少熔体温差并改善了力的传导效果,能制得密度均匀、内应力小的制品。
同时还可缩短成形周期。
但是,充模速度过高,熔体流经喷咀和模具浇口时可能会出现剪切速度过大,使物料烧焦并伴随吸入气体的现象,从而直接影响制品的表面质量。
故一般采用多级充填速率进行充模。
注射速度是指注射时螺杆的移动速度。
单位为mm/s。
注射速率是表示单位时间内熔体从喷咀注入模腔的理论容积。
单位为
cm/s,是由注射速度和机器控制。
也是注塑机设计的重要指标。
注射压力设定值小于实际要克服的阻力,注射速率(或注射速度)就无法达到原设定值。
(4)保压压力:
保压压力的选择及保压时间的确定会直接影响产品的质量密度分布的均匀性以及内应力的大小。
提咼保压压力,延长保压时间,有助于减少制品的收缩率,实际操作中,一般选取保压压力小于或等于注射压力。
保压时间的选择必须考虑模温、料温、主流道及浇口的大小。
(5)螺杆转速:
螺杆转速对塑料在螺杆中输送和塑化能力及物料的受热历程与剪切效果有直接的影响,它是影响塑化能力、塑化质量、成型周期等方面的重要参数。
提高螺杆转速,塑化能力提高,塑化质量下降,熔融温度的均匀性有所改善,剪切作用加强,剪切热量会增大,外部加热能量可减少。
对于热敏感塑料,要防止剪切过热分解,故要正确选用螺杆转速。
(6)背压:
背压也称塑化压力,是指螺杆头部前端存料区内熔体在螺杆转动后退时所受到的压力。
背压大小除与螺杆和机筒中心阻力有关外,其压力大小还可通过调节注射油缸的回油阻力(回油路上的溢流阀)来控制。
实际生产中,背压压力大小的调节与螺杆结构,制品质量要求、以及塑料的种类有关。
如果这些条件不变,则增加背压压力会使熔体的温度上升,而塑化速率则减少。
适当地提高背压,能使熔体温度均匀、混合效果提高,并有利于熔体中气体的排出。
背压的增加会使熔体温度增加,塑化的质量得以改善,但过高的背压会使螺杆计量段螺槽中熔体反流和漏流现象增加,从而降低塑料的输送能力,导致塑化量的减少。
一般认为:
背压大小在保证制品质量的前提下越低越好。
合模部份的工艺参数
(1)合模力:
为了克服注射时模腔压力引起使模具分开的胀模力就必须要有对模具施以足够的夹紧力,就是合模力。
合模力的调整直接影响制品的表观质量,尺寸精度,合模力不足,会使模具分型面分开而发生溢料,产生飞边。
合模力太大,会使模具引起变形,并使机器能耗增加。
足够的合模力与模腔压力成正比。
计算合模力的方式:
合模力二模腔投影面积*材料注射压力*压力损失系数1/3*安全系数
(1.1-1.6)
(2)顶出力:
塑料制品在模腔中冷却而将型芯或凸模包紧,因此出模时必须要有克服这一粘附力的顶出力。
制品的顶出力,顶出速度、顶出行程应根据制品的结构、形状和尺寸、制品材料及工艺条件进行进行调整。
顶出力太小,制品难脱模,顶出力太高速度太快,制品可能会发生变形,损坏,影响制品尺寸精度和表面质量,甚至使之断裂。
塑料的弹性模量越大顶出力越大,塑料与模芯的摩擦系数越大,所需的顶出力越大。
(3)开关模速度:
是动模板在移动时的速度。
若开关模速度慢,相应周期就长,生产效率就低,调节开关模速度要考虑极限位时的冲击、碰撞和对制品的破坏作用。
故开关模具时要做到两头慢,中间快。
温度控制参数
(1)烘料温度:
原料干燥是塑料加工的必需工序。
有些塑料如:
PC、PA、
PMMA、ABS、等等,其大分子上含有亲水基团,容易吸湿,若含水量超过允许限度,轻则制品表面出现斑纹、银丝、汽泡等缺陷,重则引起高分子物质在注塑时降解,严重影响外观和内在质量。
使制品机械性能下降。
干燥的方法有很多,小批量时以热风循环干燥和红外线加热烘箱进行干燥,对在高温下受热时容易氧化变色的塑料如PA料宜采用真空干燥。
大批
量时宜用沸腾干燥和气流干燥,其效率高又能连续化。
一般来说,延长干燥时间有利于充分干燥,但过多延长干燥时间效果则不大。
干燥了的原料必须要注意防潮。
(2)机筒温度:
是指机筒表面的加热温度,它的选择与成型材料的特性的关。
通常,进料段(固体输送段)温度相对要低一些。
螺杆压缩段的温度要比进料段高出约20-25C,计量段又要高出些。
以保证物料能保持在熔融状态。
但此温度必须低于塑料的分解温度。
机筒温度直接影响充模过程及充模质量。
提高机筒温度有利于注射压力向模内传递,且充模后物料温度保持在熔点以上的时间越会长,有利于大分子的解取向。
同时熔体温度上升,粘度下降,流动阻力减少,从而可改变制品性能,所以机筒温度是控制熔体温度和制品质量的主要工艺手段之一。
机筒温度的选取还应结合制品和模具特点,对于薄壁制品由于模腔窄小,充模阻力大,机筒温度应高些。
对于厚壁制品可相对低一些,对于型腔复杂或带嵌件的模具或者充模流程较长且曲折的模具,机筒温度应高一些。
(3)喷嘴温度:
喷嘴温度的确定与塑料性能喷嘴结构模具流道等因素有关,常由工艺试验来确定。
对于直通式喷嘴,通常取低于第三段的最高温度,这是为了防止流涎现象。
但是喷嘴温度不能过低,否则会造成熔料早凝将喷嘴堵塞,或把早凝的塑料注入模腔影响制品的性能。
对于锁闭式喷嘴,由于结构复杂,流动阻力大,则要提高喷嘴温度。
(4)模具温度:
是指与制品接触的模腔表面的温度。
它直接影响制品的冷却速度,因而对制品内在性能和表观质量有很大的影响,选择合适的模具温度可以缩短周期,提高机器生产效率。
模具温度通常由冷却介质来控制;
或者对模具加热来保持定温。
由于塑料性能及加工艺条件的不同,所要求的模温也不同,选择模温的基本原则是:
对流动性好的塑料,通常用水冷却,以流动性差的塑料通常用温水或对模具加热来恒定模温。
模具温度主要影响熔体的粘度和流动性,即影响充模速度,若能顺利充模,可采用低的模温,缩短冷却时间。
对于粘度高的塑料提高模温可调整冷却速率,防止制品出现冷流痕、银丝、内应力和裂纹等缺陷。
结晶型塑料注射时,模具温度影响制品的结晶度和结晶构型,当模温高时,冷却速率小,结晶速率大,因为一般塑料的最大结晶速率出现在熔点以下的高
温区,种模温仅适合于结晶率很小的塑料;
当模温中等时冷却速率适宜,塑料分子的取向和结晶适中,这是常用的模温;
模温很低时,则冷却速率大,不利于晶体和球晶的生长,所以结晶度低,从而引起制品的后收缩及性能方面的变化。
部分塑料的模具温度与注塑温度
塑料
注塑温度
模腔温度
ABS
200-270
50-90
GRPA66
280-310
70-120
AS/SAN
220-280
40-80
PA66/矿
280-305
90-120
ASA
230-260
40-90
PA11/12
210-250
GPPS
180-280
10-70
PA610
230-290
30-60
HIPS
170-260
5-75
POM
180-220
60-120
LDPE
190-240
20-60
PPO
220-300
80-110
HDPE
210-270
30-70
GRPPO
250-345
PP
250-270
PC
280-320
80-100
GRPP
260-280
50-80
GRPC
300-330
100-120
TPX
PSF
340-400
95-160
CA
170-250
40-70
GRPBT
245-270
65-110
PMMA
170-270
20-90
GRPET
260-310
95-140
聚芳酯
300-360
80-130
PBT
330-360
约200
软PVC
170-190
15-50
PET
340-425
65-175
硬PVC
190-215
PES
330-370
110-150
PA6
40-60
PEEK
360-400
160-180
GRPA6
270-290
PPS
120-150精
PA66
260-290
35-80普通
(5)液压系统的油温:
注塑机的油温应控制在55C以下,油温保持在55C以下是靠冷却水的流量来控制的,油温过高,使油的粘度下降,增加泄漏量,导致液压系统压力油的压力和流量发生变化,从而引起注射压力和注射速度产生波动,造成注射过程的不稳定,影响产品的质量。
油温过高,还会加速油液氧化变质,加快密封圈的老化。
成形周期参数
(1)注射时间:
是指把塑料熔体全部注入模腔所用的全部时间。
注射时间与充模速度有关。
注射速度低时,注射时间会增加,这不利于快速充模,且对制品的质量有决定性的影响,同时也增加周期时间。
现代注塑机(通有型)注射量与注射时间的关系
注射量
注射时间
50
0.8
500
1.5
4000
3.0
100
1.0
1000
1.75
6000
3.75
250
1.25
2000
2.25
1000(
)5.0
(2)保压时间:
是指保压压力持续作用的时间。
保压时间的长短对制品尺寸的精确度有很能大的影响,若保压时间不足,熔体会从模腔中往外倒流,使模腔中压力下降,以致制品出现缩孔、凹陷等缺陷。
若在浇口封闭之后则不会影响,保压时间的确定依赖于熔体温度、模温、浇口的尺寸大小。
(3)冷却时间:
冷却时间取决于制品的厚度,塑料的热性能和结晶性能、模
具温度等。
在实际生产中,一般以顶出制品不变形为依据来确定冷却时间。
过
长的冷却时间会降低了生产效率。
冷却时间随熔体温度的增加而增加,随模具温度的减少而降低,制品厚度越大,冷却时间也越长。
在正常的生产中,塑化的时间应比制品的冷却时间要短,所以,通常情况下,成型周期中的冷却时间已包括了塑化时间(熔胶时间)。
(4)其它时间:
成型周期中的其它时间是指开模、关模、顶出、喷涂脱模剂、安放嵌件等辅助时间,尽量减少辅助时间是提高效率的关键手段。
要提高效率就必须缩短周期时间。
注塑主要工艺参数对制品质量的影响
塑化过程参数的影响
存料区熔料的温度分布直接决定了注塑制品尺寸的精度、机械性能、外观质量,实践证明:
加工PP料时,熔体温度增加12C其制品尺寸变化0.07%加工PC料时,当熔体温度变化10C,其制品尺寸相应变化0.052%。
存料区的熔体温度分布:
由于塑料在螺杆的计量段、压缩段、加料段内处于不同的物态(分别为熔体、固-熔两相、固体),其温度分布是沿轴向方向出现一定的温差。
影响存料区熔体温度的因素有:
螺杆转速、注射量、螺杆的静止时间、加工的物料。
对现有的注塑机来讲,存料区熔体温度分布性均匀得以改善的关键,
是正确选择对存料区熔体温度变化有影响的相关加工工艺参数,并对这些
参数进行严格的控制,以保证塑化时能提供能量数量一定、温度均匀的熔体,为制备高性能的制品创造良好的条件。
注射过程参数的影响
注射过程中塑料大分子的取向和结晶程度对制品的结构性能有明显的影响,而熔接线强度直接影响制品力学性能,所有影响制品结构性能的因素都与注塑过程的参数有关。
一、塑料在模腔中流动取向的特点:
1.熔体温度提咼,制品的取向程度降低,由于熔体温度咼,制品的冷却时间长,塑料大分子的松驰时间就长,熔易解取向,使取向程度减少。
冷却速度慢,同样可以解取向。
2.注射压力的增加,提高了充模过程熔体的剪切速率和剪切应力,有利于提高分子的取向程度。
同时制品的密度也随压力的增加而提咼。
3.注射速度的增加,使制品表层产生高度的取向,内心中层取向却小,在相同温度下慢速充模会延长流动时间,有利熔体实际温度的降低,同时中心部分的解取向作用减弱,而取向增强。
故快速充模时取向程度小,慢速充模时取向程度增加。
4.模具温度低,冷却速度高,解取高作用减小,冻结取高效果提
高,相反,模温高时,冷却缓慢,起解取向作用。
二、塑料在注塑过程中的结晶特点
结晶型塑料制品的性能受到结晶形态和结晶度的影响,,在注塑制品中,会不会出现结晶结构,出现结晶结构后结晶度有多大,制品各部分的结晶情况是否一样,这些都与注塑中工艺参数的选择有关。
1.温度及冷却速度与结晶的影响:
结晶型塑料在结晶过程中存
在着四个重要的温度特征,即结晶型塑料的熔化温度、出现最大结晶速率的结晶温度、出现最大成核速率的晶核生成温度及玻璃化温度。
当模具温度接近最大结晶速率温度时,这时冷却速度缓慢,晶核不易生成,结晶也缓慢,冷却时间加长,形成了较大晶球,制品往往较脆。
当把模具温度控制在最大结晶速率温度与玻璃化温度之间,这时结晶
比较完整,故利用这种温度来确定模具温度对成形制品是有利的,如
PP注塑时模温为30-80C、PA为70-120C之间。
2.压力和注射速度与结晶的关系:
注射压力和注射速度的提高使用使剪切作用加强,加速了结晶作用。
低压力下易生成大而完整的球晶,咼压力下易生成小而不规则的球晶。
在咼剪切速率下,冷却后的制品有咼的结晶度,所以在实际操作中,提咼注射压力和速度,能为结晶创造良好的条件。
三、接线及其力学性能
当制品存在孔或嵌件、米用多浇口、设计的部品壁厚薄不均时,熔体充模往往出现两个以上的方向流动状态,在两股料流汇流时就会形成熔接线。
当注射速度过高而形成喷射流时,也会出现熔接线。
在注塑制品中,熔接线大大影响了制品的表面质量,力学性能也严重降低。
一般认为,熔接线的结构特点是:
垂直取向、弱粘接和表面V型槽。
形成的原因有:
1.由于熔体流经一段距离,其温度有所降低,两股熔料汇流时表面不容易互相熔合。
2.对于结晶型塑料,在接缝界面上不能形成完全结晶,使力学性能下降。
3.流动前端夹带气体、杂质,使接触面减少,导致强度下降。
影响熔接线的因素:
1.温度:
熔接线的强度随温度的增加而增加。
2.模具温度:
提高模具温度是改善熔接线甚至消除表面V型槽的有效办法。
3.注射压力:
注射压力的提高有助于克服流动阻力,改善压力传递,使接合处在高压力下熔合,有助于增加接缝处的密度,也有利于排出气体,使强度提高。
4.充模速度:
充模速度的影响具有两面性,一方面,提高充模速度,使汇合时间减少,又能增加剪切热,使熔体温度升高,从而提高熔接强度;
另一方面,高充模速度使接缝处的垂直取向更加严重,使其塑性变形能力减弱。
一般认为,充模速度在接合线处存在一个最佳值。
退火处理可使熔接强度提高,因为退火处理后,释放了成形中
的内应力,改善了制品的机械性能。
多级注射工艺:
由于浇注系统的设计及各部分几何形状的不同,不同的部位对充模熔体的流动要求也不同,各部分所产生的取向效果也不同,故采用多级注射工艺,可以制备性能好,表面质量高的产品。
多级注射工艺的选择应根据制品的几何形状、尺寸大小、精确度要求、制品厚薄、浇口的形状与大小和使用塑料的种类来确定。
实现注射过程中多级工艺参数控制称为多级注射。
是在不同位置上有不同的注射压力和注射速度来控制注射过程。