品质管理资料1916抽样方案精品版Word文档下载推荐.docx
《品质管理资料1916抽样方案精品版Word文档下载推荐.docx》由会员分享,可在线阅读,更多相关《品质管理资料1916抽样方案精品版Word文档下载推荐.docx(16页珍藏版)》请在冰点文库上搜索。
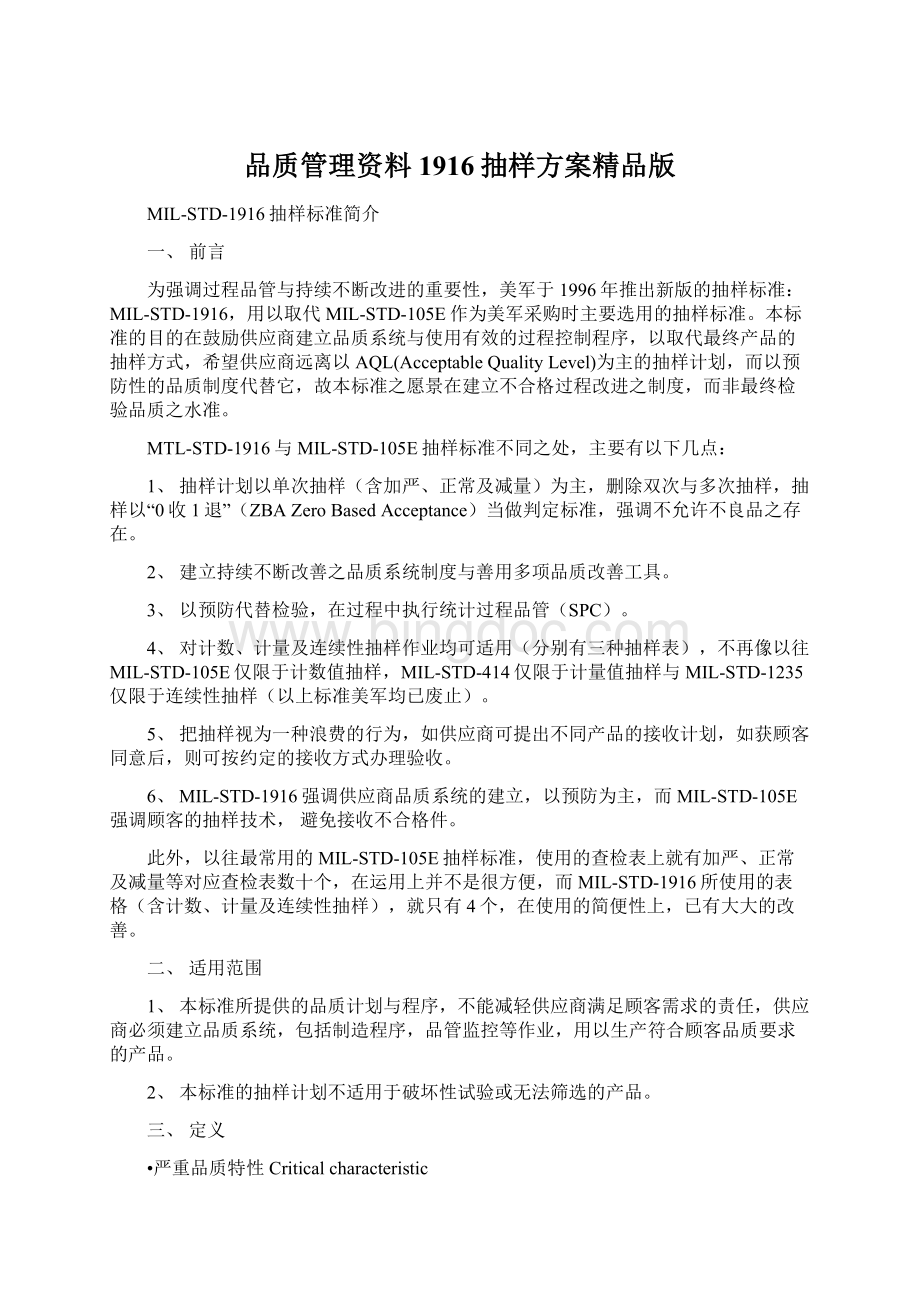
采取随机抽样或按比例抽样,并应尽可能避免采取固定模式的抽样方式。
6、被判定拒收,供应商必须进行下列行动:
1对不合格件进行隔离,并进行必要的返修或重加工,经纠正的产品供应商必须先行筛选后,再重新抽样检验。
2确定不合格原因,执行适当的过程变更。
3执行正常、加严与减量检验的转换法则。
4各项纠正措施必须告知政府机构或顾客,并再次将重新筛选批送政府或顾客执行评估。
7、对严重品质特性,除非另有规定,供应商必须执行自动化筛选作业,并且使用VL-VⅡ层级的抽样计划,若检验发现一项以上的不合格件,则需进行下列行动:
1不得运交且通知政府机构或顾客。
2确认原因,执行纠正措施,并执行100%筛选。
3维持纠正措施的记录,以备政府机构或顾客的查验。
五、品质管理系统的需求
1、供应商应建立以预防为主的品质系统,除了当作另一个可接受的方法外,亦展示供应商持续不断品质改进的决心。
2、品质系统必须文件化,其内容至少要包括组织机构、权责、作业程序、工作道次与生产资源,供应商并且要持续改善此项品质系统,以确保运作的有效性与正确性。
3、品质系统的独立,可依据ISO9000、MIL-Q-9858等标准加以规划,无论选择哪一种标准,品质系统必须以预防为主题,且需符合下列的目标:
a)影响品质的工作者必须了解品质系统的运作程序。
b)产品必须符合或超越顾客需求。
c)强调预防性的过程差异分析与不良率分析。
d)当疵病发生时,必须立即寻找失效的产生原因与疵病来源,并且采取有效的纠正措施。
e)使用统计分析方法与问题解析手法,用以降低过程变异量,改善过程能力与产品品质。
f)保存记录,用以证实品质计划与过程控制的有效性。
4、供应商必须对产品生产的相关过程加以研究与了解,通过文件化的程序证实供应商可以达成:
a)品质具有一致性,且执行完善的过程控制。
b)降低设备变异,原料及其它输入源所产生的变异。
c)只有标准化的操作程序以减少过程变异。
d)进行过程设计,在目标值下提高精密度。
e)具有不断过程改善的制度,通过过程变更与统计分析手法,达到过程预防与改善。
5、程改善可使用的手法
a)利用制造程序图规划重要控制点,用以阻止或侦测疵病之产生。
b)过程不良原因的分析工具,如PDCA循环(Plan-Do-Check-Action)、FMEA(FailureModesandEffectsAnalysis)、柏拉图分析(ParotoAnalysis)及要因分析(CauseandEffectAnalysis)等。
c)过程改善过程的评估工具,如趋势分析、品质成本、生产效率、不良品率及6个标准差(6-sigma)的能力。
d)利用实验计划,降低变异源产生之机率,改善生产力。
6、过程控制可使用的手法
a)确认过程控制技术的使用范围,如统计过程品管(SPC)、自动化、量具、预防保养、目视检验等。
b)过程控制计划(Processcontrolplan)必须包括SPC。
c)通过资料分析,显示供应商过程控制措施是有效性的。
d)根据工作的需要,执行适宜的教育训练。
e)确认各单位在SPC相互作用上的权责与工作内容。
f)使用控制图之前,必须先行确定每次抽样数与抽样频率,并建立修正控制界线的作业程序与律定超出控制范围的准则。
g)确认所指定品质特性的关键参数,并找出影响关键参数的生产程序。
h)律定过程改进的权责,对纠正措施进行追踪,直至失效原因被消除为止。
i)执行量测系统分析(MSAMeasurementSystemAnalysis),了解量仪具的变异量。
7、产品符合性可使用的手法
包括使用控制图,利用记录与纠正及预防措施,执行过程能力分析(如CPK、CP),或通过过去统计资料进行趋势分析,最后则100%检验。
六、如何进行抽样计划
1、抽样计划的步骤:
1根据品质要求指定不同等级之VL(共有7个等级),
2选定抽样的形式(计量、计数、连续抽样)
3根据批量大小或生产期间生产量与VL决定样本代字CL(CodeLetter)。
4执行转换程序(正常、加严、减量)。
表1样本代字(CL)对照表
批量
验证水平(VL)
Ⅶ
Ⅵ
Ⅴ
Ⅳ
Ⅲ
Ⅱ
Ⅰ
2-170
A
171-288
B
289-544
C
545-960
D
961-1632
E
1633-3072
3073-5440
5441-9216
教学诊断E
文成公主进藏教学实录9217-17408
教师读书摘抄及心得E
数学方案问题E
数学教师读书笔记E
提出全面改革总目标的会议是E
17409-30720
政治经济学04任务答案E
任务标题E
≥30721
教学过程中的建议E
教学科研E
表2计数值抽样计划
样本代字(CL)
验证水准(VL)
T
R
样本大小
3072
1280
512
192
80
32
12
5
3
4096
1536
640
256
96
40
16
6
5120
2048
768
320
128
48
20
8
6144
2560
1024
384
160
64
24
10
4
8192
1、当批量比样本量小则100%检验
2、加严检验在正常检验VL左边之隔栏,减量检验则为右边之隔栏。
表3计量值抽样计划
加严
减量
113
87
44
29
18
9
2
122
92
69
49
11
129
100
74
54
37
23
13
7
136
107
81
58
41
26
15
145
K法(适用单边规格或双边规格者)
3.51
3.27
3.00
2.69
2.40
2.05
1.64
1.21
1.20
3.58
3.32
3.07
2.79
2.46
2.14
1.77
1.33
3.64
3.40
3.12
2.86
2.56
2.21
1.86
1.45
3.69
3.46
3.21
2.91
2.63
2.32
1.93
1.56
3.76
F法(适用双边规格者)
0.136
0.145
0.157
0.174
0.193
0.222
0.271
0.370
0.707
0.134
0.143
0.154
0.168
0.188
0.214
0.253
0.333
0.132
0.140
0.152
0.165
0.182
0.208
0.242
0.301
0.130
0.138
0.148
0.162
0.177
0.199
0.233
0.283
0.435
0.128
1、如批量比样本数小时,100%检验
2、加严检验在正常检验VL的左边,减量检验则右边
表4连续性抽样计划
筛选阶段:
筛选数量
3867
2207
1134
527
264
125
55
27
NA
7061
3402
1754
842
372
180
83
36
11337
5609
2524
1237
572
246
116
53
16827
8411
3957
1714
815
368
155
73
26912
11868
5709
2605
1101
513
228
抽样阶段:
频率
1/3
4/17
1/6
2/17
1/12
1/17
1/24
1/34
1/48
1/68
1/96
1/136
1/192
3、一般注意事项:
1在合约或产品规格中指定VL,一项VL可使用在不同的品质特性。
表1的批量与VL决定样本代字CL,表2计数值抽样、表3计量值抽样与表4连续性抽样的VL和CL决定产品的抽样计划,用以评估产品符合合约和规格需求的程度,抽样合格的产品可通过转换法则在下次抽样时执行减量检验。
2抽样水准分成正常检验、加严检验与减量检验等三阶段,除非另有其它规定,VL值以正常检验为启始,加严检验的VL在表2与表3的左边,减量检验则在右边,而表4的执行方式则较复杂,请参照表4附注说明。
每一项品质特性的抽样水准不能改变。
除非执行转换法则。
3正常检验、加严检验及减量检验的转换法则系根据不同的VL在表2、3与4中执行抽样检验,转换法则的运作与纠正的结果(复验)无关,仅与初检的结果有关。
4、各项抽样标准执行说明:
1计数值抽样:
正常检验、加严检验与减量检验的抽样计划如表2所示,表中样本大小需随从批中随机抽出,经检验若无不合格件产生(零不良),则该批允收。
②计量值抽样:
A、正常、加严检验与减量检验的抽样计划如表3所示,计量值抽样不能任意使用,它必须假设数据的来源(量测结果)是独立性的且符合常态分布,在相同条件下(CL及VL)计数值的检验结果,并不保证与计量值的检验结果具有一致性。
B、计量值抽样结果若属允收,除必须所有样本的测量结果均在规格之内,且符合表3的K法(不良率的估计)或F法(过程变异量占公差的百分比)的判定准则,若上述两者无法同时满足则拒收。
K法:
适合单边规格与双边规格的产品
·
单边规格:
若(U-Xbar)/δ≥K或(Xbar-L)/δ≥K,则产品允收。
双边规格:
若(U-Xbar)/δ≥K且(Xbar-L)/δ≥K,则产品允收。
F法:
适合双边规格之产品者
若δ/(U-L)≤F,则产品允收。
Xbar=样本平均值,δ=样本标准差,U=规格上限,L=规格下限。
③连续性抽样:
1.执行连续性抽样的前提:
a)移动性的产品。
b)在检验站或检验站附近,有足够的空间、设备、人力可执行100%检验。
c)此过程可生产出品质稳定的产品。
2.连续性抽样计划步骤:
执行时首先应依照表4筛选阶段执行100%检验,当符合下列条件时,可依表4进入抽样阶段。
a)全数筛选的同型态产品处在稳定的状态。
b)达到表4所规定的筛选数量。
当下列条件发生后,应停止抽样阶段,而改为100%检验的筛选阶段。
a.此生产过程被中断三个工作天以上。
b.当此同型态产品处在稳定的状态。
c.在抽样时有任何的不符合项目被发现。
3.对严重品质特性的额外要求
如在抽样阶段发现严重品质特性的不合格件,自上次合格件后的所有产品,均应执行100%检验。
4、转换法则:
1正常检验转换加严检验:
当发生下列任一条件,则必须由正常检验转换加严检验:
A、计数值及计量值抽样:
最近2-5批中有2批被拒收。
B、连续性抽样:
在目前的抽样计划(不论是抽样或筛选阶段)期间,于执行5倍的样本大小过程中(此处的样本大小,应依照表2方式赋予)发现2个以上的不合格件。
2加严检验转换正常检验:
当下列两条件均符合时,则由加严检验转换正常检验:
A、不合格件的疵病原因已完成纠正。
B、计数值及计量值抽样:
且连续5批被允收。
C、连续性抽样:
在目前的抽样计划(不论是抽样或筛选阶段)期间,于执行5倍的样本大小过程中,无任何的不合格件。
3正常检验转换减量检验:
当下列四条件均符合时,则由正常检验转换减量检验:
连续10批被允收;
连续性抽样:
在目前的抽样计划(不论是抽样或筛选阶段)期间,于执行10倍的样本大小过程中,无任何的不合格件。
B、生产是在稳定的阶段。
C、品质系统正常运作,且表现被政府机构或顾客认为满意。
D、政府机构或顾客同意减量检验,始可进行。
4减量检验转换正常检验:
当发生下列任一条件,则必须由减量检验转换正常检验
有1批被拒收。
有任何不合格被发现;
B、生产情况不规则与延迟。
C、品质系统运作表现被政府机构或顾客认为不满意。
D、政府机构或顾客因其它生产条件之故,认为应回复正常检验。
七、范例说明
1、计数值抽样:
合约对品质的要求指定为VL-Ⅳ,供应商的交运批量可依需要弹性调整,表5为最近10批依计数值抽样的检验结果。
2、计量值抽样:
合约对品质的要求指定为VL-Ⅰ,检验项目为操作温度,规定下限为180º
F,规格上限为209º
F,该批产品的批量为N=40,从表Ⅰ之VL及批量查到CL为A,从表3之VL及CL查到样本大小为n=4。
假设此4件样本的量测数据为197、188、184及205,计算结果如下所示:
Xbar=193.5,δ=9.399
(U-Xbar)/δ=1.649(Xbar-L)/δ=1.436,δ/(U-L)=0.324
•K法:
从表3之VL-I及CL(A)查出K=1.21,计算结果1.649与1.436均≥K.
•F法
从表3之VL-I及CL(A)查出F=0.370,计算结果0.324<
F。
结论:
K法及F法均符合,故该产品允收。
3、连续性抽样:
合约对品质的要求指定为VL-Ⅱ,生产期间为八小时,生产批量约700到800个工件,依表Ⅰ及批量,可查出CL为C,筛选阶段的数量为116。
抽样阶段的频率为1/48,表6为制程抽样状况的检验结果。
表5计数值抽样检验范例
批号
样本代字
不合格件数
品质判定
抽样等级
备注
1
5000
拒收
正常
开始为正常检验
900
允收
3000
最近2-5批中有2批不合格,下一批将加严检验
1000
采用Ⅳ左边V之样本大小
2000
2500
过程已得到纠正,连续5批均允收,下一批转正常检验
回到Ⅳ之样本大小
表6连续性抽样检验范例
产品序号
频率或
100%
抽样
等级
事件/行动
开始生产,进行116件之筛选
发现1件不合格件,重新计数
124
连续116件合格,转为抽样阶段,频率为1/48
170
第一批选取的随机样本:
结果合格
9697
1.连续200件(10倍的样本大小)抽样:
样本合格
2.转减量检验,频率为1/68
(注:
据表2,在CL=C及VL-Ⅱ时,样本大小为20)
9769
随机样本抽取,频率1/68,结果合格。
13982
1.生产批量增加三倍(2100至2400件)
2.结束CL=C而以CL=E(重依批量查表1)阶段进行抽样阶段
3.另因现在VL-Ⅱ及减量阶段,查表4,频率为1/136。
14121
在新频率1/136下,第一件随机样本抽取,结果合格,继续随机抽取样本。
16290
1.发现一件不合格品,
2.转回正常抽样
3.开始筛选阶段,进行数量228件之筛选,因目前处在CL=E及VL-Ⅱ阶段
16518
100%
连续228件均合格,开始抽样阶段,频率1/96
八、VL值的指定及选用
在MIL-STD-1916中,并没有特别指出VL如何指定,其实可以利用OC曲线分析,对表2进行转换,计算其不良率的估计值(在N≥10n状况下),如表7所