焊接钢管检验方案.docx
《焊接钢管检验方案.docx》由会员分享,可在线阅读,更多相关《焊接钢管检验方案.docx(40页珍藏版)》请在冰点文库上搜索。
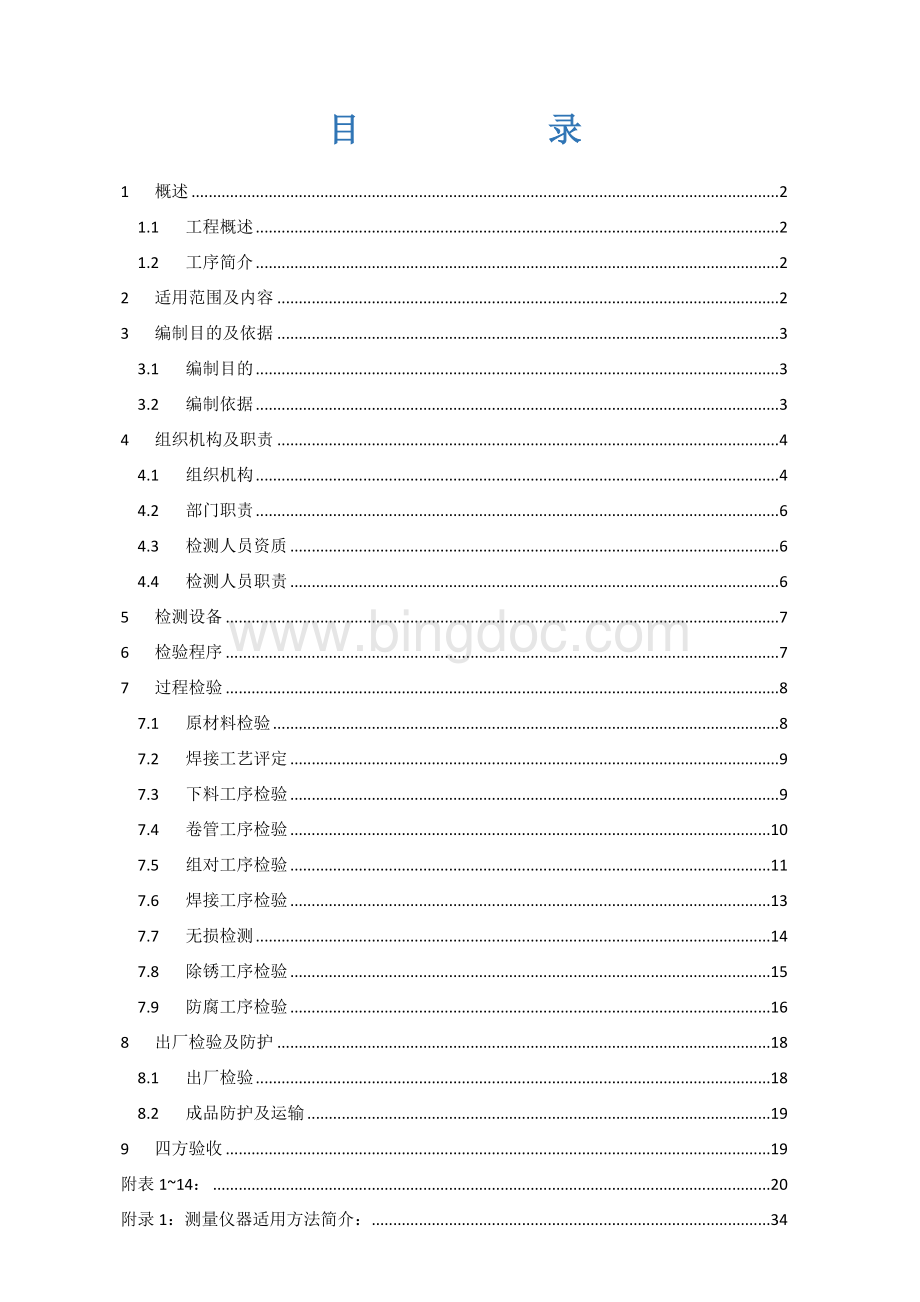
目录
1 概述 2
1.1 工程概述 2
1.2 工序简介 2
2 适用范围及内容 2
3 编制目的及依据 3
3.1 编制目的 3
3.2 编制依据 3
4 组织机构及职责 4
4.1 组织机构 4
4.2 部门职责 6
4.3 检测人员资质 6
4.4 检测人员职责 6
5 检测设备 7
6 检验程序 7
7 过程检验 8
7.1 原材料检验 8
7.2 焊接工艺评定 9
7.3 下料工序检验 9
7.4 卷管工序检验 10
7.5 组对工序检验 11
7.6 焊接工序检验 13
7.7 无损检测 14
7.8 除锈工序检验 15
7.9 防腐工序检验 16
8 出厂检验及防护 18
8.1 出厂检验 18
8.2 成品防护及运输 19
9 四方验收 19
附表1~14:
20
附录1:
测量仪器适用方法简介:
34
1概述
1.1工程概述
天津市南水北调中线室内配套工程宁汉供水工程管线工程(A0+000~A43+850)输水管线途径天津市宝坻区及宁河县两个行政区,管线工程出自宁汉供水泵站,主干管至芦台经济技术开发区东边界宁汉分水口,干线长43.85km。
管外径皆为1820mm,按不同使用条件,管壁厚为22~36mm。
钢管材质均为Q235B镇定钢,管道工作压力0.5MPa。
1.2工序简介
本次工程所用钢管均为直缝焊接钢管,利用钢管进行卷制、接长并焊接;在无损检测合格后进行除锈及涂装,工艺流程图如下:
滚圆
纵焊
对管
环焊
无损检测
成品检验
下料
防
腐
出
厂
2适用范围及内容
本检测方案适用于宁汉供水工程用钢管的加工及施工检测,本检测方案规定了钢管检测的适用依据、质保体系、检验程序、检验部门的职责、检验人员资质、过程检验的内容及方法、出厂验收的内容及四方验收等相关内容。
3编制目的及依据
3.1编制目的
为保证钢管的加工质量及施工质量,满足工程图纸,规范及相关标准要求,特编制本检测方案,用于钢管的加工及施工质量检验。
3.2编制依据
本方案编制主要依据下述设计要求、规范、规程及标准
(1)合同及设计文件
(2)GB50268-2008《给水排水管道工程施工及验收规范》
(3)SL432-2008《水利工程压力钢管制造安装及验收规范》
(4)NB/T47013.1-13-2015《承压设备无损检测》
(5)GB/T9445-2015《无损检测人员资格鉴定与认证》
(6)SY/T0414-2007《钢制管道聚乙烯胶粘带防腐层技术标准》
(7)GB50726-2011《工业设备及管道防腐工程施工规范》
(8)GB50727-2011《工业设备及管道防腐工程施工质量验收规范》
(9)GB50212-2014《建筑防腐工程施工规范》
(10)GB/T18370-2014《玻璃纤维无捻纱布》
(11)GB/T13657-2011《双酚A基环氧树脂》
(12)GB/T1447-2005《纤维增强塑料拉伸性能试验方法》
(13)GB/T1449-2005《纤维增强塑料拉伸性能试验方法》
(14)SL205-2007《水工金属结构防腐蚀规范》
(15)SL582-2012《水工金属结构制造安装质量检验通则》
(16)SL734-2016《水利工程质量检测技术规程》
(17)GB/T709-2006《热轧钢板和钢带的尺寸、外形、重量及允许偏差》
(18)GB/T700—2006《碳素结构钢》
(19)GB/T14977-2008《热轧钢板表面质量的一般要求》
(20)GB/T8923.1-2011《涂覆涂料前钢材表面处理表面清洁度的目视评定第1部》
(21)SL105-2007《水工金属结构防腐蚀规范》
4组织机构及职责
4.1组织机构
为保证钢管及管件的加工进度与质量,特组织了以下组织机构。
安全管理
制管
车间
防腐
车间
下
料
班
组
卷板
班
组
焊
前
组
对
班
组
焊
接
班
组
除锈
班
组
喷
涂
班
组
厂长
生产质量副厂长
经营副厂长
技术质量
设备管理
生产调度
生产管理部
物资科
总工程师
4.2部门职责
厂长责成生产副厂长主管制管厂全面质量工作,各科室、各车间、各班组配合生产副厂长的质量管理工作,具体分工如下:
a:
主管副厂长岗位职责
生产主管厂长主管制管厂质量工作,全面负责产品生产过程的质量及产品出厂质量,制定质量检验的程序,规定各检测岗位人员的职责,处理生产过程中出现的质量问题,批准质量提升的管理办法及方法。
b:
质量管理机构职责
设立生产管理部为制管厂质量管理机构。
《生产管理部岗位职责》,生产管理部部长负责生产管理部管理工作,《生产生产管理部部长岗位职责》。
4.3检测人员资质
检测人员应符合SL734-2016《水利工程质量检测技术规程》的相关要求,并经过专业培训,熟练掌握检测的方法及标准,取得相应资格证书。
4.4检测人员职责
生产管理部设质检员、焊接质检员、无损检测员负责产品检验工作,各岗位质检人员按照岗位要求、产品质量要求及检验批次要求,完成质量检验工程,并及时将质量检验结果上报主管领导及生产部门,并在相应的质检记录上签字存档。
5检测设备
检测设备应符合工程质量验收规范所规定的精度要求,并委托第三方对检测设备进行检验,并取得相应的检定证书。
本次工程用到的主要检测仪器如下:
生产检验工序
检验器具
下料
钢卷尺,钢板尺,焊接检验尺,游标卡尺
卷管
钢卷尺、弧度样板,钢板尺
组对
钢卷尺,钢板尺,焊接检验尺,游标卡尺
焊接
焊接检验尺,放大镜,钢直尺
无损检测
超声波检测仪,射线检测仪
除锈
粗糙度对比试块,除锈等级对比图片
防腐
涂层测厚仪,针孔探测仪
出厂检验
经纬仪,钢卷尺,涂层测厚仪,针孔探测仪
6检验程序
钢管及管件制作检验程序为三检制检验程序,分别为自检,互检和专检。
各检验工序的检验人员及职责如下:
自检:
由生产工段检验人员检验,并填写相关记录,检验合格后方可进入下一工序继续生产加工。
互检:
半成品构件在进入下道工序时,由该工序的检验人员对上道工序流转下来的产品进行检验,确认合格方可继续生产加工,检验合格后填写相关检验记录。
专检:
由质检部门委托的专职质检人员进行成品构件的最终检验,确定产品是否符合出厂要求,并填写相关记录,专职质检人员还需按批次对过程工序进行检验,填写相关抽检记录。
钢管检验记录表格样式见过程检验条款中规定的相关表格。
7过程检验
7.1原材料检验
7.1.1检验标准:
《碳素结构钢》GB/T700
7.1.2检测项目:
屈服强度,抗拉强度,断后伸长率,弯曲试验,冲击试验
7.1.3取样基数:
同炉号同批次,每60吨一组,不足60吨时按60吨处理
7.1.4取样方式:
可连续取样
7.1.5取样数量:
每10组中,7组自检,3组见证,再抽取1组抽检
7.1.6检验依据:
GB/T700—2006《碳素结构钢》
7.1.7检验记录表格见附表1
7.2焊接工艺评定
钢管加工前应依据NB/T47014《承压设备焊接工艺评定》进行焊接工艺评定,合格后方可钢管加工及施工。
详见《焊接工艺评定报告》。
7.3下料工序检验
7.3.1下料尺寸检验
(1)检验标准:
《水利工程压力钢管制造安装及验收规范》SL432-2008第4.1.1款
序号
项目
允许偏差(mm)
1
宽度和长度
±1
2
对角线相对差
2
3
对应边相对差
1
4
失高(曲线部分)
0.5
(2)检测项目:
下料长度,下料宽度,对角线相对差,失高(曲线部分)
(3)检测数量:
每张钢板
(4)检测方式:
使用钢卷尺量取相应尺寸
(5)检验依据:
《水工金属结构制造安装质量检验通则》SL582-2012
7.3.2下料端口检验
(1)检验标准:
《水利工程压力钢管制造安装及验收规范》SL432-2008第4.1.10及第4.1.11款,《承压设备无损检测》NB/T47013.3-2015
(2)检测项目:
端口质量
(3)检验数量:
逐张检验
(4)检验方式:
超声波检测
(5)检验依据:
《水工金属结构制造安装质量检验通则》SL582-2012,《承压设备无损检测》NB/T47013.3-2015
7.3.3检验记录表格见附表2
7.4卷管工序检验
7.4.1检验标准:
《水利工程压力钢管制造安装及验收规范》SL432-2008第4.1.12款
序号
检验项目
技术要求
检验方法
1
瓦片的弧度
不大于1.5mm
使用弦长900mm的样板检查弧度,使用塞尺测量样板与钢管之间的间隙
2
实测周长与设计周长差
不大于5.4mm
在每个管口距边沿50mm处用钢卷尺测量。
相邻关节周长差
极限偏差10mm
3
纵缝对口错边量
不大于2mm
用弧度样板紧靠管壁,用塞尺或钢直尺测坡口量测的间隙差
4
环缝对口错边量
30mm及以下板厚的钢管环缝错边量应不大于3mm;30mm以上板厚的钢管环缝错边量应不大于板厚的10%。
用焊检尺测量
5
焊缝处的弧度
极限间隙4mm
采用弦长500mm的样板检测
6
圆度检测
不大于5.4mm
测量分为两次,每次选取两个相互垂直的直径进行测量,其差量应不大于5.4mm,两次之间的测量位置应错开45°,即四个测量数据成米字型分布
7.4.2检测项目:
瓦片的弧度,实测周长与设计周长差,相邻关节周长差,纵缝对口错边量,环缝对口错边量,焊缝处的弧度,圆度
7.4.3检测数量:
逐根钢管检验
7.4.4检测方式:
使用钢卷尺、样板、钢直尺、焊接检验尺量取相应尺寸
7.4.5检验依据:
《水工金属结构制造安装质量检验通则》SL582-2012
7.4.6检验记录表格见附表3
7.5组对工序检验
7.5.1检验标准:
《水利工程压力钢管制造安装及验收规范》SL432-2008第4.1.12款
序号
检验项目
技术要求
检验方法
1
管长
不大于±10mm
钢卷尺
2
主管、支管的管口圆度
不大于5.4mm
每个管口用钢卷尺测2对相互垂直的直径,两次测量错开45°,取差值较大的两相互垂直直径之差为被测管口的圆度
3
主管、支管的管口实测周长与设计周长差
不大于±5.4mm
在每个管口距边沿50mm处用钢卷尺测量,将实测值与设计值进行比较
4
支管中心距离S1
不大于±S1(mm)÷1000
钢卷尺
5
主管、支管的中心高程相对差
不大于4mm
用水准仪和标尺测量
6
主管、支管的管口垂直度
不大于2mm
由管口顶部中心挂垂线,用钢直尺测管口顶部中心和底部中心至垂线的距离差
7
主管、支管管口平面度
不大于2mm
用电子经纬仪测量
8
纵缝对口错边量
不大于2mm
用弧度样板紧靠管壁,用塞尺或钢直尺测坡口两侧的间隙差
9
环缝对口错边量
30mm及以下板厚的钢管环缝错边量应不大于3mm;30mm以上板厚的钢管环缝错边量应不大于板厚的10%。
用焊接检验尺测量
7.5.2检测项目:
管长,主管、支管的管口圆度,主管、支管的管口实测周长与设计周长差,支管中心距离S1,主管、支管的中心高程相对差,主管、支管的管口垂直度,主管、支管管口平面度,纵缝对口错边量,环缝对口错边量
7.5.3检测数量:
逐根钢管检验
7.5.4检测方式:
使用钢卷尺、样板、钢直尺、焊接检验尺量取相应尺寸
7.5.5检验依据:
《水工金属结构制造安装质量检验通则》SL582-20127.5焊接工序。
7.5.6检验记录表格见附表4
7.6焊接工序检验
7.6.1焊接外观检验
(1)检验标准:
《水利工程压力钢管制造安装及验收规范》SL432-2008第4.1.12款
序号
项目
检测标准
检测手段
1
裂纹
不允许
目测
2
表面夹渣
不允许
目测
3
咬边
深度不大于0.5
焊接检验尺
4
未焊满
不允许
目测
5
表面气孔
不允许
目测
6
焊瘤
不允许
目测
7
飞溅
不允许
目测
8
焊缝余高
Δh
手工焊
δ≤25,Δh=0~2.5
25<δ≤50,Δh=0~3
焊接检验尺
自动焊
0~4
焊接检验尺
9
对接接头
焊缝宽度
手工焊
盖过每边坡口宽度1~2.5,且平缓过渡
焊接检验尺
自动焊
盖过每边坡口宽度2~7,且平缓过渡
焊接检验尺
7.6.2检测项目:
焊缝外观
7.6.3检测数量:
逐根钢管,逐条焊缝检验
7.6.4检测方式:
使用焊接检验尺量取相应尺寸
7.6.5检验依据:
《水工金属结构制造安装质量检验通则》SL582-2012
7.6.6检验记录表格见附表5~8
7.7无损检测
7.7.1焊接煤油渗透检验
(1)检验标准:
《钢制焊接常压容器》JB/T4735-1997中15.2.5.7的规定
(2)检测项目:
焊缝质量
(3)检测数量:
逐根钢管,逐条焊缝检验
(4)检测方式:
将焊接接头能够检查的一面清理干净,涂以白粉浆,晾干后,在焊接接头的另一面涂以煤油,使表面得到足够的浸润,经半小时后以白粉浆上没有油渍为合格。
(5)检验依据:
《钢制焊接常压容器》JB/T4735-1997
7.7.2焊缝内部检验
(1)检验标准:
《水利工程压力钢管制造安装及验收规范》SL432-2008
(2)检测项目:
焊缝质量
(3)检测数量:
钢种
板厚
一类焊缝的检测
方法和比例(%)
二类焊缝的检测
方法和比例(%)
碳素钢
-
UT
RT
UT
RT
100
2
50
1
(4)检测方式:
超声波检测与射线检测
(5)检验依据:
《承压设备无损检测》NB/T47013-2015
(6)根据设计要求,射线检测Ⅱ级合格,其中顶管部分射线检测Ⅰ级片比例80%,直埋管部分射线检测Ⅰ级片比例50%比例。
7.8除锈工序检验
7.8.1检验标准:
《水工金属结构防腐蚀规范》SL105-2007,喷砂除锈等级为Sa2.5级
7.8.2检测项目:
除锈等级是否达到Sa2.5
7.8.3检测数量:
逐根钢管检验
7.8.4检测方式:
参照粗糙度相对样块目测检查除锈级别
7.8.5检验依据:
《水工金属结构防腐蚀规范》SL105-2007
7.8.6检验记录表格见附表9
7.9防腐工序检验
7.9.1聚丙烯胶带检验
(1)检验标准:
《水工金属结构防腐蚀规范》SL105-2007,电火花检测电压不小于7kv
(2)检测项目:
电火花检测
(3)检测数量:
逐根钢管检验
(4)检测方式:
使用针孔检测仪对钢管表面外防腐进行涂刷式检测。
探头移动速度不大于0.3m/s
(5)检验依据:
《水工金属结构防腐蚀规范》SL105-2007
7.9.2特加强级环氧树脂玻璃钢检验
(1)检验标准:
《水工金属结构防腐蚀规范》SL105-2007,电火花检测电压不小于3.5kv,防腐层厚度不小于3.5mm
(2)检测项目:
电火花检测,涂层测厚仪检测
(3)检测数量:
电火花逐根钢管检验,厚度检测每节钢管四个点。
(4)检测方式:
电火花检测:
使用针孔检测仪对钢管表面外防腐进行涂刷式检测。
探头移动速度不大于0.3m/s。
涂层厚度检测:
在1dm²的基准面上做3次测量,其中每次测量的位置应相距25~75mm,应取这3次测量值的算术平均值为该基准面的局部厚度。
每10㎡至少应测量3个局部厚度。
且85%以上的局部厚度应达到设计厚度,没有达到设计厚度的部位,其最小局部厚度应不低于设计厚度的85%。
(5)检验依据:
《水工金属结构防腐蚀规范》SL105-2007
7.9.3饮水容器无毒环氧涂料检验
(1)检验标准:
《水工金属结构防腐蚀规范》SL105-2007,电火花检测电压不小于1.5kv,防腐层厚度不小于0.3mm
(2)检测项目:
电火花检测,涂层测厚仪检测
(3)检测数量:
电火花逐根钢管检验,厚度检测每节钢管四个点。
(4)检测方式:
电火花检测:
使用针孔检测仪对钢管表面外防腐进行涂刷式检测。
探头移动速度不大于0.3m/s
涂层厚度检测:
在1dm²的基准面上做3次测量,其中每次测量的位置应相距25~75mm,应取这3次测量值的算术平均值为该基准面的局部厚度。
每10㎡至少应测量3个局部厚度。
且85%以上的局部厚度应达到设计厚度,没有达到设计厚度的部位,其最小局部厚度应不低于设计厚度的85%。
(5)检验依据:
《水工金属结构防腐蚀规范》SL105-2007
7.9.4检验记录表格见附表9
8出厂检验及防护
8.1出厂检验
钢管出厂需经专职检验人员按照相关技术要求及标准进行100%检测,合格后填写《检验报告》,并对钢管喷涂标识及编号,整理第三方无损检测报告,母材复试报告及相关材料合格证,汇总后报送监理。
《检验报告》格式见附表10
8.2成品防护及运输
成品管堆放需在管底部端口处放置垫块,单层码放。
运输过程车辆地板上放置软垫,防止破坏外防腐,禁止使用钢丝绳对运输的管道进行固定及吊装。
9四方验收
钢管到达施工场地,需经过制造方、施工方、监理方及业主方同时到场检验,检验合格后方可施工。
附表1:
附表2:
附表3:
附表4:
附表5:
附表6:
附表7:
附表8:
附表9:
附表10:
附表11:
附表12
附表13:
附表14:
附录1:
测量仪器适用方法简介:
1.钢卷尺的使用
1.1使用方法
测量时钢卷尺零刻度对准测量起始点,施以适当拉力,直接读取测量终止点所对应的尺上刻度。
需测量直径但又无法直接测量时,可通过测量圆周长来求得直径。
1.2.注意事项
使用时不要前倾后仰、左右歪斜。
拉力不宜过大。
尺的长度是以在20℃、50N拉力标准状况下的测得值为依据。
1.3温度误差补正计算方法
不同温度环境下使用钢卷尺时,应通过线膨胀公式将测量值换算成20℃的值。
温度误差=实际测定值×尺带膨胀系数×(使用温度-20℃)。
尺带膨胀系数为0.0000115
2.焊接检验尺的使用
3.游标卡尺的使用
游标卡尺作为一种被广泛使用的高精度测量工具,它是由主尺和附在主尺上能滑动的游标两部分构成。
如果按游标的刻度值来分,游标卡尺又分0.1、0.05、0.02mm三种。
3.1游标卡尺的读数方法
以刻度值0.02mm的精密游标卡尺为例,读数方法,可分三步;
1)根据副尺零线以左的主尺上的最近刻度读出整毫米数;
2)根据副尺零线以右与主尺上的刻度对准的刻线数乘上0.02读出小数;
3)将上面整数和小数两部分加起来,即为总尺寸。
如上图所示,副尺0线所对主尺前面的刻度64mm,副尺0线后的第9条线与主尺的一条刻线对齐。
副尺0线后的第9条线表示:
0.02x9=0.18mm
所以被测工件的尺寸为:
64+0.18=64.18mm
3.2游标卡尺的使用方法
将量爪并拢,查看游标和主尺身的零刻度线是否对齐。
如果对齐就可以进行测量:
如没有对齐则要记取零误差:
游标的零刻度线在尺身零刻度线右侧的叫正零误差,在尺身零刻度线左侧的叫负零误差(这种规定方法与数轴的规定一致,原点以右为正,原点以左为负)。
测量时,右手拿住尺身,大拇指移动游标,左手拿待测外径(或内径)的物体,使待测物位于外测量爪之间,当与量爪紧紧相贴时,即可读数,如下图所示:
3.3使用注意事项
游标卡尺是比较精密的量具,使用时应注意如下事项:
1)使用前,应先擦干净两卡脚测量面,合拢两卡脚,检查副尺0线与主尺0线是否对齐,若未对齐,应根据原始误差修正测量读数。
2)测量工件时,卡脚测量面必须与工件的表面平行或垂直,不得歪斜。
且用力不能过大,以免卡脚变形或磨损,影响测量精度。
3)读数时,视线要垂直于尺面,否则测量值不准确。
4)测量内径尺寸时,应轻轻摆动,以便找出最大值。
5)游标卡尺用完后,仔细擦净,抹上防护油,平放在合内。
以防生锈或弯曲。
4.钢直尺的使用
4.1由于钢直尺的刻线间距为1mm,而刻线本身宽度就有0.1~0.2mm,所以用钢直尺测量物件的长度尺寸,测量结果是不太准确的,测量时读数误差比较大,只能读出毫米数,也就是说使用钢直尺的最小读数值为1mm,小于1mm数值,只能估读。
4.2钢直尺的读数分为两部分,一部分为测量值,另一部分为估计值。
通常钢直尺的前10cm精确值为0.5mm,10cm之后的为1mm,所以直尺的测量读数估计值是分度值的下一位小数。
4.3注意使用钢直尺的测量长度时尽量不使用“0”刻度作为零点,这样很容易对准非断面位置,从而造成读数的人
页40