学士学位论文塑料圆形罩模具制作Word文档下载推荐.docx
《学士学位论文塑料圆形罩模具制作Word文档下载推荐.docx》由会员分享,可在线阅读,更多相关《学士学位论文塑料圆形罩模具制作Word文档下载推荐.docx(24页珍藏版)》请在冰点文库上搜索。
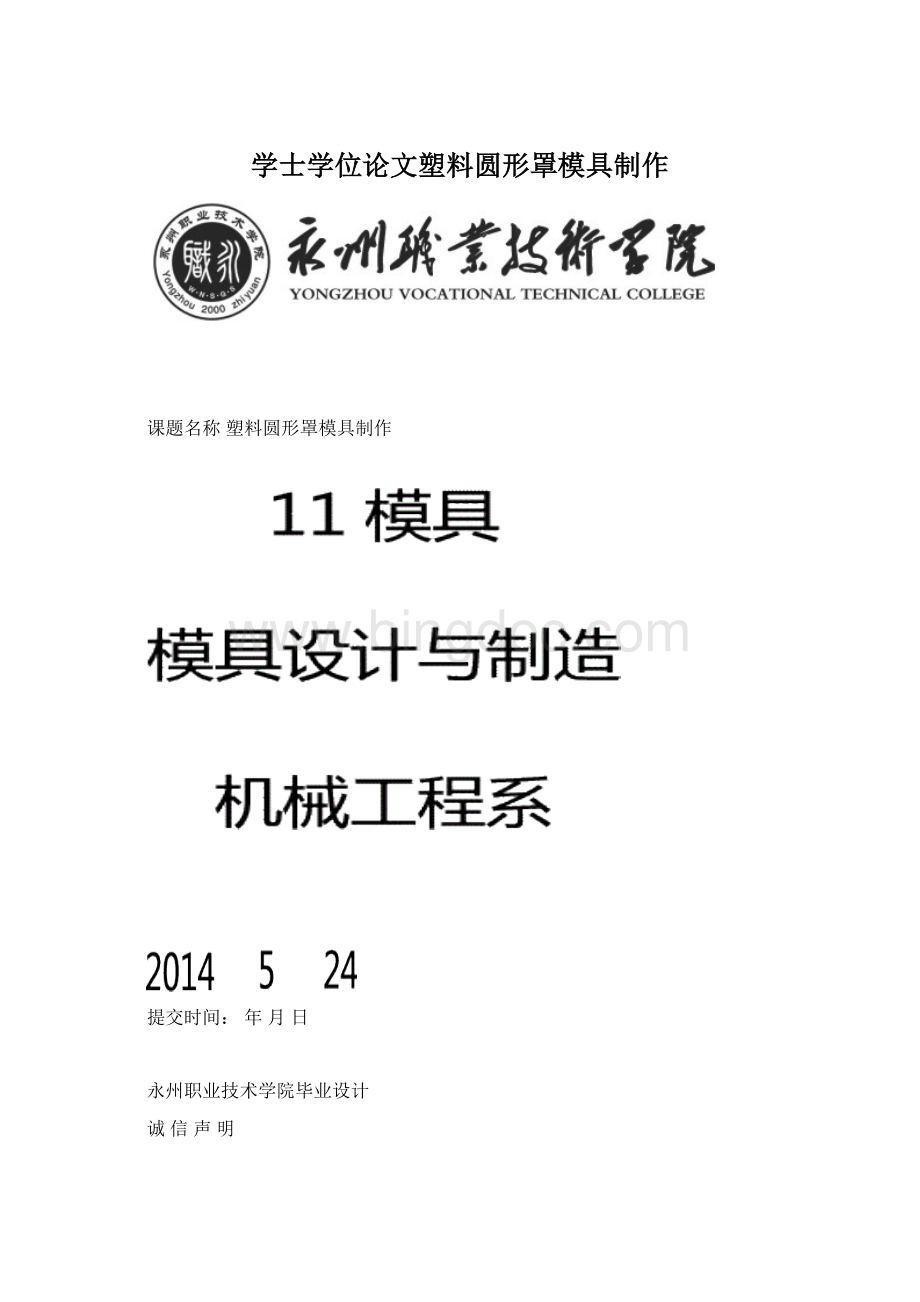
7.2脱模力的计算…………………………………………………………19
7.3校核推出机构零件的尺寸………………………………………………19
第八章冷却系统的设计……………………………………………………20
8.1冷却介质…………………………………………………………………20
8.2冷却系统的计算……………………………………………………………20
第九章导向与定位结构的设计………………………………………………20
第十章零件图和装配图的绘制………………………………………………21
参考文献…………………………………………………………………………21
附录…………………………………………………………………………21
致谢……………………………………………………………………………23
答辩成绩登记表………………………………………………………………24
永州职业技术学院毕业设计任务书
学号
201113001610
专业
模具
班级
11模具
毕业设计主题
塑料圆形罩模具制造
主题类型[1]
塑料模
主题来源[2]
全国高等职院抽考试题
毕业设计时间
2013年11月5日至2014年5月24日
1.毕业设计内容要求[立题背景及意义、目标、内容、成果;
字数>
500字]
立题背景及意义:
CA6140车床后托架的加工工艺及夹具设计为本课题的研究内容,对此研究查阅的大量的资料,首先明白机械加工工艺过程就是用切削的方法改变毛坯的形状、尺寸和材料的物理机械性质成为具有所需要的一定精度、粗糙度等的零件。
毕业设计目标:
为了能具体确切的说明过程,使工件能按照零件图的技术要求加工出来,就得制定复杂的机械加工工艺规程来作为生产的指导性技术文件,学习研究制定机械加工工艺规程的意义与作用就是本课题研究目标。
本设计拟解决的问题:
在这个设计过程中,我们还必须考虑工件的安装和夹紧.安装的正确与否直接影响工件加工精度,安装是否方便和迅速,又会影响辅助时间的长短,从而影响生产率,夹具是加工工件时,为完成某道工序,用来正确迅速安装工件的装置.它对保证加工精度、提高生产率和减轻工人劳动量有很大作用。
这是整个设计的重点,也是一个难点
本设计的主要内容:
我在实习中接触的大多数模具是塑料模具,所以我就选择了在实习时我们公司接到的一模具的设计——塑料圆形罩模具制作的设计我结合公司的设计图纸设计了这套模具的分型面、主流道、浇口、分流道、推杆、导柱、推板等部分。
毕业设计成果:
通过本次设计塑料圆形罩模具制作设计,它系统的介绍了塑料圆形罩模具中的各个零部件的加工工艺过程及整套模具的装配和使用。
本设计在保证加工质量,做到在提高生产率的同时把生产成本降到最低。
[1]主题类型:
与专业课程相关
[2]主题来源:
①工作任务题,②实践实训题,③模拟或仿真题,④学生自选题。
2.主要参考资源(参考文献、图书文献、相关网站)[3]
[1]陆志刚主编.《塑料模具设计》机械工业出版社,第二版
[2]冯炳尧主编.模具设计与制造简明手册.北京:
机械工业出版社,2004
[3]阎亚林主编.塑料模具图册.高等教育出版社
[4]刘航主编.模具制造技术西安电子科技大学出版社
[5]钱可强编著.机械制图(第四版).北京:
高等教育出版社,2002.
[6]范建蓓编著压铸模与其他模具机械工业出版社
3.毕业设计进度安排:
起止时间
阶段内容
2013年11月25日至2013年12月6日
任务下达,材料准备,课题选择
2013年12月7日至2013年12月25日
毕业设计
2013年12月26日至2014年5月15日
设计反馈,修改
2014年5月16日至2014年5月23日
答辩
4.指导老师审核意见:
指导老师(签字):
年月日
主要参考资源[3]:
参考文献:
作者,论文篇名,刊物名,出版年,卷(期),论文在刊物中的页码。
图书文献:
作者,书名,出版地,出版社,出版日期,引用内容所在页。
本任务书经指导教师审阅通过后,必须上传至世界大学城“职教新干线”学生个人空间“毕业设计”栏目内。
塑料圆形罩模具制造
摘要
我在实习中接触的大多数模具是塑料模具,所以我就选择了在实习时我们公司接到的一模具的设计——塑料圆形罩模具制作的设计。
我结合公司的设计图纸设计了这套模具的分型面、主流道、浇口、分流道、推杆、导柱、推板等部分。
由于在公司没有相应的设计手册、许多计算的部分我都是借鉴的公司的设计图纸。
本套模具是一套一腔四模的注射模,比之单型腔模具而言提高了生产效率,缩短了生产周期。
本设计为塑料圆形罩模具制作设计,它系统的介绍了塑料圆形罩模具中的各个零部件的加工工艺过程及整套模具的装配和使用。
其中,涉及到注射机各种参数的选取、零部件的加工方法、注射模的结构及相关的计算问题及特种加工工艺。
在该模具设计中,利用计算机绘图软件绘制了零件图和装配图,以及制定了机械加工工艺过程卡。
本设计在保证加工质量的前提下,尽量做到在提高生产率的同时把生产成本降到最低。
[关键字]圆形罩,分型面,参数化,模具设计,浇注系统
第一章.塑件成型工艺性分析
1.1塑件的分析
(1)外形尺寸
该塑件壁厚为2.4mm塑件外形尺寸不大,塑料熔体流程不太长,适合于注射成型,如图1-1所示。
图1-1
(2)精度等级
塑件的尺寸精度为MT5,属于低精度,根据精度等级和尺寸大小查表,得到各尺寸的实际公差并按此公差进行计算。
(3)脱模斜度
ABS属无定型塑料,成型收缩率较小,参考相关资料选择该塑件上型芯和凹模的统一模斜度为1°
。
1.2ABS的性能分析(材料性能分析)
(1)使用性能
综合性能好,冲击强度、力学强度较高,尺寸稳定,耐化学稳定性,电气性能良好;
易于成型和机械加工,其表面可镀铬,适合制作一般机械零件、减摩零件、传动零件和结构零件。
(2)成型性能
①无定型塑料。
其品种很多,各品种的机电性能及成型特性也各有差异,应按品种来确定成型方法及成型条件。
②吸湿性强。
水的质量分数应小于0.3%,必须充分干燥,要求表面光泽的塑件应要求长时间预热干燥。
③流动性中等。
溢边料0.04mm左右。
④模具设计时要注意浇注系统,选择好进料口的位置、进料形式。
当推出力过大或机械加工时塑件表面易呈现白色痕迹。
(3)ABS的主要性能指标
其性能指标见下表
ABS的性能指标
1.3ABS的注射成型过程及工艺参数
(1)注射成型过程
①成型前的准备。
对ABS的色泽、粒度和均匀度等进行检验,由于ABS吸水性较大,成型前应进行充分的干燥。
②注射过程。
塑件在注射机料筒内经过加热、塑化达到流动状态后,由模具的浇注系统进入模具型腔成型。
其过程可分为充模、压实、保压、倒流和冷却5个阶段。
③塑件的后处理。
处理的介质为空气和水,处理温度为60~75℃,处理时间为16~20s.
(2)注射工艺参数
①注射机:
螺杆式,螺杆转数为30r/min.
②料筒温度(℃):
后段15~170;
中段165~180;
前段180~200.
③喷嘴温度(℃):
170~180。
④模具温度(℃):
50~80。
⑤注射压力(MPa):
60~100。
⑥成型时间(s):
30(注射时间取1.6,冷却时间20.4,辅助时间8).
第二章.拟定模具的结构形式
2.1分型面位置的确定
通过对塑件结构形式的分析,分型面应选在端盖截面积最大且利于开模取出塑件的底平面上,其位置如图2-1所示。
图2-1
2.2型腔数量和排列方式的确定
(1)型腔数量的确定
该塑件的精度要求一般在2~3级之间,且为大批量生产,可采取一模多腔的结构形式。
同时,考虑到塑件尺寸、模具结构尺寸的大小关系,以及制造费用和各种成本费等因素,初步定为一模两腔结构形式。
(2)型腔排列形式的确定
多型腔模具尽可能采用平衡式排列布置,且力求紧凑,并与浇口开设的部位对称。
由于该设计选择的是一模两腔,故采用直线对称排列,如图2-2所示。
图2-2
(3)模具结构形式的确定
从上面的分析可知,本模具设计为一模两腔,呈直线对称排列,根据塑件结构形状,推出机构拟采用脱模板推出的推出形式。
浇注系统设计时,流道采用对称平衡式,浇口采用侧浇口,且开设在分型面上。
因此,定模部分不需要单独开设分型面取出凝料,动模部分需要添加型芯固定板、支撑板和脱模板。
由以上综合分析可确定选用带脱模板的单分型面注射模。
2.3注射机型号的确定与校核
(1)注射量的计算
通过三维软件建模设计分析计算得塑件体积:
塑件质量:
式中,ρ为塑料密度,查阅有关资料可取1.02g/cm3。
(2)浇注系统凝料体积的初步估算
浇注系统的凝料在设计之前不能确定准确的数值,但是可以根据经验按照塑件体积的0.2~1倍来估算。
由于本次采用的流道简单并且较短,因此浇注系统的凝料按塑件体积。
的0.2倍来估算,故一次注入模具型腔塑料熔体的总体积(即浇注系统的凝料和两个塑件体积之和)为
(3)选择注射机
根据第二步计算得出一次注入模具型腔的塑料总体积V总=6.5186cm3,依公式(V公=V总/0.8)则有:
V总/0.8=6.5186/0.8cm3=8.148cm3。
根据以上的计算,初步选定公称注射量为9cm3,注射机型号为XS-Z-30卧式注射机,其主要技术参数见下表.
理论注射容量/cm3
30
移动形程/mm
160
螺杆柱塞直径/mm
28
最大模具厚度/mm
180
注射压力/MPa
119
最小模具厚度/mm
60
锁模力/kN
2.5X105
锁模形式
液压-机械
拉杆内间距/mm
235
(4)注射机的相关参数的校核
①注射压力校核。
根据ABS的成型工艺要求可知,ABS所需注射压力为80~110MPa,这里取p0=90MPa,该注射机的公称注射压力p公=119MPa,注射压力安全系数k1=1.25~1.4,这里取k1=1.3,则
所以,注射机注射压力合格。
②锁模力校核。
a.塑件在分型面上的投影面积A塑,,则
b.浇注系统在分型面上的投影面积A浇,即流道凝料(包括浇口)在分型面上的投影面积,可以按照多型腔模的统计分析来确定。
A浇是每个塑件在分型面上的投影面积A塑的0.2~0.5倍。
由于本例流道设计简单,分流道相对较短,因此流道凝料投影面积可以适当取小一些。
这里取A浇=0.2A塑。
c.塑件和浇注系统在分型面上总的投影面积A总,则
d.模具型腔内的胀型力F胀,则
式中,p模是型腔的平均计算压力值,通常取注射压力的20%~40%,大致范围为25~40MPa。
对于勃度较大且精度较高的塑料制品应取较大值。
ABS属中等勃度塑料及有精度要求的塑件,故p模取35Mpa。
查上表可得该注射机的公称锁模力F锁=25000kN,锁模力安全系数为k2=l.l~1.2,这里取k2=1.2,则
所以,注射机锁模力合格。
对于其他安装尺寸的校核要等到模架选定,结构尺寸确定后方可行。
第三章浇注系统的设计模具的设计
3.1主流道的设计
主流道通常位于模具中心塑料熔体的入口处,它将注射机喷嘴注射出的熔体导入分流道或型腔中。
主流道的形状为圆锥形,以便熔体的流动和开模时主流道凝料的顺利拔出。
主流道的尺寸直接影响到熔体的流动速度和充模时间。
另外,由于其与高温塑料熔体及注射机喷嘴反复接触,因此设计中常设计成可拆卸更换的浇口套。
(1)主流道尺寸
①主流道的长度:
小型模具L主应尽量小于57mm,本次设计中初取50nn进行设计。
②主流道小端直径:
d=注射机喷嘴尺寸+(0.5~1)mm=(4+0.5)mm=4.5mm
③主流道大端直径:
d'=d+2L主tanα≈7.22,式中α=2°
④主流道球面半径:
SR0=注射机喷嘴球头半径+(1~2)mm=(16+2)mm=18mm
⑤球面的配合高度:
h=5mm
(2)主流道浇口套形式
主流道衬套为标准件可选购。
主流道小端入口处与注射机喷嘴反复接触,易磨损。
对材料的要求较严格,因而尽管小型注射模可以将主流道浇口套与定位圈设计成一个整体,但考虑上述因素通常仍然将其分开来设计,以便于拆卸更换。
同时也便于选用优质钢材进行单独加工和热处理。
设计中常采用碳素工具钢(T8A或T10A),热处理淬火表面硬度为50~55HRC,如图3-1所示。
图3-1
3.2分流道的设计
(1)分流道的布置形式
在设计时应考虑尽量减少在流道内的压力损失并尽可能避免熔体温度降低,同时还要考虑减小分流道的容积和压力平衡,因此采用平衡式分流道。
(2)分流道的长度
由于流道设计简单,根据两个型腔的结构设计,分流道较短,故设计时可适当选小一些。
单边分流道长度L分取15mm.
(3)分流道截面形状、尺寸
常用的分流道截面形状有圆形、梯形、U形、六角形等,为了便于加工和凝料的脱模,分流道大多设计在分型面上。
本设计采用圆形截面,其加工工艺性好,且塑料熔体的热量散失、流动阻力均不大。
3.3浇口的设计
该塑件要求不允许有裂纹和变形缺陷,表面质量要求较高,采用一模两腔注射,为便于调整充模时的剪切速率和封闭时间,因此采用侧浇口。
其截面形状简单,易于加工,便于试模后修正,且开设在分型面上,从型腔的边缘进料。
①侧浇口的截面形状:
3.4冷料穴的设计及计算
冷料穴位于主流道正对面的动模板上,其作用主要是收集熔体前锋的冷料,防止冷料进入模具型腔而影响制品的表面质量。
本设计仅有主流道冷料穴。
由于该塑件表面要求没有印痕,采用脱模板推出塑件,故采用与球头形拉料杆匹配的冷料穴。
开模时,利用凝料对球头的包紧力使凝料从主流道衬套中脱出。
第四章.成型零件的结构设计及计算
4.1成型零件的结构设计
(1)凹模的结构设计
凹模是成型制品外表面的成型零件。
按凹模结构的不同可将其分为整体式、整体嵌入式、组合式和镶拼式4种。
根据对塑件的结构分析,本设计中采用整体式凹模,如图4-1所示。
图4-1
(2)凸模的结构设计(型芯)
凸模是成型塑件内表面的成型零件,通常可以分为整体式和组合式两种类型。
通过对塑件的结构分析可知,该塑件的型芯有三个:
第一个是成型零件的内表面的大型芯,第二个是成型零件的内表面的圆形孔型芯,第三个是成型的内表面“十字形”型芯。
因塑件包紧力较大,所以成型零件的内表面的大型芯设在定模部分;
另一个是成型零件的成型的内表面“十字形”型芯,还有一个是成型零件底面的圆形孔设在动模,如图所示,设计时将其放在定模部分,同时有利于分散脱模力并简化了模具结构。
将这几个部分装配起来,如图4-2所示。
图4-2
4.2成型零件钢材的选用
根据对成型塑件的综合分析,该塑件的成型零件要有足够的刚度、强度、耐磨性及良好的抗疲劳性能,同时要考虑它的机械加工性能和抛光性能。
又因为该塑件为大批量生产,所以构成型腔的嵌入式凹模钢材选用P20(美国牌号)。
对于成型塑件外圆筒的大型芯来说,由于脱模时与塑件的磨损严重,因此钢材选用高合金工具钢Cr12MoV。
而对于成型内部圆筒的型芯而言,型芯较小,但塑件中心轮毅包住型芯,型芯需散发的热量比较多,磨损也比较严重,因此也采Cr12MoV。
4.3成型零件工作尺寸的计算
采用平均尺寸法计算成型零件尺寸,塑件尺寸公差按照查表查出的零件公差计算。
(1)凹模径向尺寸的计算
塑件外部径向的转换:
相应的塑件制造公差△1=1.14mm;
相应的塑件制造公差△1=1.34mm.
(2)凹模深度尺寸的计算:
塑件高度方向尺寸的转换:
塑件高度的最大尺寸
相应的
塑件轮毅外凸台高度的最大尺寸
(3)型芯径向尺寸的计算
①动模型芯径向尺寸的计算。
塑件内部径向尺寸的转换
②动模型芯内孔尺寸:
③定模型芯尺寸的计算。
塑件内孔径向尺寸的转换:
(4)型芯高度的计算
①型芯塑件内腔大型芯高度的计算塑件尺寸转换:
②成型塑件中心圆筒的型芯高度,塑件中心圆筒高度尺寸转换:
(5)成型孔间距的计算
第五章.模架及标准件的选用
(1)注射模架的结构
模架也称模体,是注射模的骨架和基体,模具的每一部分都寄生其中,通过它将模具的各个部分有机地联系在一起。
标准模架一般由定模座板(或叫定模底板T)、定模固定板(或叫定模板A)、动模固定板(或叫型芯固定板B)、动模垫板U、垫块(或叫垫脚、模脚C)、动模座板(或叫动模底板L)、推板(或叫推出底板F)、推杆固定板E、推件板D、导柱、导套、复位杆等组成。
(2)标准模架的确定
模具的大小主要取决于塑件的大小和结构。
对于模具而言,在保证足够强度和刚度的条件下,结构越紧凑越好,可以以塑件布置在推杆推出的范围之内及复位杆与型腔保持一定距离为原则来确定模架大小,可以大致按下列经验公式来计算。
塑件在分型面上的投影宽度W’须满足:
W’<
=W2-10mm
塑件在分型面上的投影长度L’须满足:
L’<
=lt-d-30mm
式中w2—推板宽度(mm);
lt—复位杆在长度方向的间距(mm);
d—复位杆直径(mm);
10—推杆与垫块之间的双边距离;
30—复位杆与型腔之间的双边距离。
根据上式可求得W2和lt这两个参数,再对照中小型标准模架尺寸系列中相应的参数就可以确定模架大小和型号。
本设计中:
塑件在分型面上的投影宽度W’﹦100mm,
因此,推板的宽度w2≥W’﹢10mm即w2≥110mm
对照中小型标准模架尺寸系列中相应的参数就可确定:
复位杆直径d为8mm,A板宽度为100mm。
塑件在分型面上的投影长度L’﹦230mm,
因此,复位杆在长度方向的间距lt≥L’﹢d﹢30mm即lt≥128mm
A板长度为315mm。
模架相关零件的尺寸如下表:
第六章排气系统的设计
该塑件由于采用侧浇口进料,熔体经塑件下方的台阶及中间的肋板充满型腔,顶部有一个Φ12mm小型芯,其配合间隙可作为气体排出的方式,不会在顶部产生憋气的现象。
同时,底面的气体会沿着推杆的配合间隙、分型面和型芯与脱模板之间的间隙向外排出。
第七章脱模推出机构的设计
7.1推出方式的确定
本塑件采用圆周为脱模板、中心为推杆的综合推出方式。
脱模板推出时为了减小脱模板与型芯的摩擦,设计中在脱模板与型芯之间留出0.2mm的间隙,并采用锥面配合,可以防脱模板因偏心而产生溢料,同时避免了脱模板与型芯产生摩擦。
7.2脱模力的计算
F脱=pA(f·
cosα-sinα)
其中:
f—摩擦系数(0.15~0.3)取f=0.2
P—因塑件收缩对型芯产生的单位包紧力(12~20MPa)取p=20MP
A—塑件包紧型芯的侧面积(mm2)
α—型芯的脱模斜度
F脱=20x5.263x(0.2x0.99-0.017)=19.052
7.3校核推出机构零件的尺寸
(1)推件板D厚度尺寸的校核
式中L—推件板长度上两推杆的最大距离(mm);
B—推件板宽度(mm)
E—钢材的弹性模量(2.1x105MPa)
F—脱模力(N);
—推件板中心所允许的最大变形量(mm),一般取制品在被推出方向上的尺寸公差的1/5~1/10。
取制品在被推出方向上的尺寸公差的平均值为3/20.
(2)推杆直径的校核
①推杆直径的确定
=27.3
d
式中d—推杆的最小直径(mm);
k—安全系数,一般取1.5;
L—推杆的长度(mm);
n—推杆的数目。
②推杆的强度校核
=140.4≤[160]
式中—推杆所受的应力(MPa);
—推杆材料的许用应力(MPa)。
其他符号与前相同
n—推杆的数目。
d—推杆的最小直径(mm);
第八章.冷却系统的设计
8.1冷却介质
ABS属中等勃度材料,其成型温度及模具温度分别为200℃和50~80℃。
所以,模具平均温度初步选定为60℃,用常温水对模具进行冷却。
即进口温度取20℃,出口温度取27℃