端盖零件的数控加工工艺设计与数控程序的编制Word格式文档下载.doc
《端盖零件的数控加工工艺设计与数控程序的编制Word格式文档下载.doc》由会员分享,可在线阅读,更多相关《端盖零件的数控加工工艺设计与数控程序的编制Word格式文档下载.doc(23页珍藏版)》请在冰点文库上搜索。
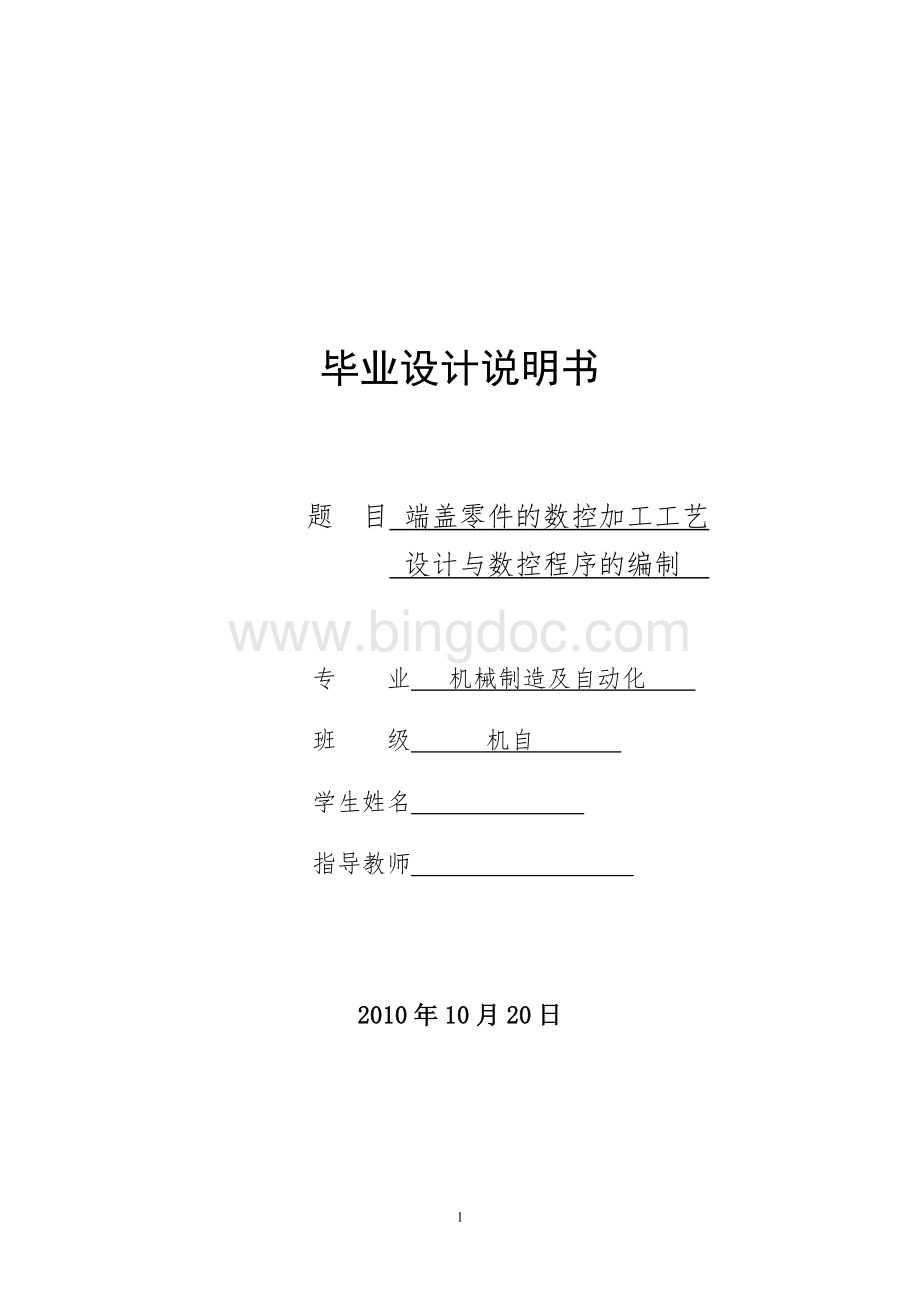
1.1课题的提出 -6-
1.2课题的主要内容 -7-
1.3课题的构思 -7-
1.4本人要完成的工作量 -7-
第二章端盖零件的数控加工工艺 -8-
2.1数控加工零件的工艺性分析 -8-
2.1.1.零件外形和特点分析 -8-
2.1.2.精度分析 -9-
2.1.3.零件的结构工艺性分析 -9-
2.2数控加工工艺路线设计 -9-
2.2.1.选择定位基准 -9-
2.2.2.确定数控加工方法 -9-
2.2.3.划分加工阶段 -10-
2.2.4.划分加工工序 -10-
2.2.5.确定加工顺序 -10-
2.3.确定毛坯类型及工序尺寸及公差 -11-
2.4.确定总加工余量与毛坯尺寸 -13-
2.5.确定工件装夹与定位方案 -13-
2.6.确定各工序的切削用量 -14-
2.7.制定数控加工工艺卡 -16-
2.8.刀具的选择和刀具卡的制定 -16-
2.8.1.数控铣刀 -16-
2.8.2.钻头 -17-
2.8.3.中心钻 -17-
2.8.4.铰刀 -18-
2.9.数控加工程序说明 -18-
2.10.数控加工仿真图(见附表三) -18-
第三章总结 -19-
参考文献 -20-
致谢 -21-
第一章绪论
毕业设计是大学教学的最后一个环节,旨在考查学生对理论知识的综合运用的能力,加深学生对专业理论知识的理解,启发学生设计创造思维,提高学生分析、解决问题的能力,增强学生在机械制造方面的实践能力,加强学生对语言的逻辑组织能力。
1.1课题的提出
随着电子元件、计算机、传感与检测、自动控制及机械制造等技术的不断发展,数控制造技术也得到了迅速的发展和广泛的应用。
它能很好的解决复杂、精密、小批多变的零件加工问题,在近几十年来数控加工技术得到了迅速的发展和广泛的应用。
数控加工自动化程度高,具有加工复杂形状零件的能力,生产周期短加工精度高且稳定,生产率高有益于实现计算机通信网络。
如今的数控机床已经在机械加工部门占有非常重要的地位,是柔性制造系统、计算机集成制造系统、自动化工厂的基本构成单位。
努力发展数控加工技术,并向更高层次的自动化、柔性化、敏捷化、网络化和数字化制造方向推进,是当前机械制造业发展的方向。
提高数控化率是当前机械制造技术革新的必由之路。
我国是制造大国,要加快经济的发展,必须掌握制造技术的核心,而先进的数控制造技术就是其中之一。
但是目前国内数控技术的发展相对于国外还比较落后,数控化率还不够,有待进一步的发展,这样本课题就顺应提出了。
1.2课题的主要内容
1、针对毕业设计任务1图对端盖零件进行数控加工工艺设计与数控程序编制,并用仿真软件进行模拟加工来验证所编数控程序的可行性。
2、能够运用所学的机械设计、机械加工基础、机械制图、机械制造工艺、数控加工工艺与编程及数控自动编程等基础知识进行综合设计,完成对所设计的平面类零件数控加工程序的编写;
3、进行数控模拟加工过程,以检验加工参数或加工路径的合理性,并分析和研究加工好的成品是否达到设计要求
1.3课题的构思
端盖零件时机械支撑连接的重要构建之一,零件品种繁多有针对性,生产成本高,效率低。
它为典型的端盖类零件,其加工属于典型的铣削加工,需仔细研究加工路线时期简单化,降低成本,提高效率适应小批量生产要求。
考虑到多把刀具加工选用数控铣床自动换刀,提高刀具旋转速度慢速走刀尽量一次性加工完成。
1.4本人要完成的工作量
1.毕业设计开题报告;
2.对零件进行数控工艺分析并确定加工工艺方案,制定数控加工工艺卡片;
3.根据所加工零件的技术要求选择合适的刀具制定数控刀具;
4.确定数控加工走刀路线后编制数控加工程序,再进行数控仿真加工验证;
5.编写毕业设计说明书。
第二章端盖零件的数控加工工艺
2.1数控加工零件的工艺性分析
2.1.1.零件外形和特点分析
本零件属于典型端盖类零件,有外表面、圆柱台阶、通孔沉孔的组成,以铣、钻、加工为主,可用加工中心、数控铣数或控钻对零件进行加工。
2.1.2.精度分析
尺寸精度:
精度要求较高的尺寸主要有Φ40H6。
对于尺寸精度要求,主要通过在加工过程中的精确对刀;
正确选用刀具的磨损量和正确选用合适的加工工艺等措施来保证。
表面粗糙度:
主要的表面粗糙度有中间孔内粗糙度最低为1.6ūm,两侧孔壁最低粗糙度为3.2ūm,其余为12.5ūm。
对于表面粗糙度要求,主要通过选用正确的粗、精加工路线,选用合适的切削用量等措施来保证。
2.1.3.零件的结构工艺性分析
端盖主要加工面是孔、曲面和平面。
零件上φ40的孔尺寸公差为H7可选用立铣通孔—镗孔的方案;
阶梯孔φ13和φ22的表面粗糙度要求不高,直接用立铣通孔可达到;
平面与外轮廓表面粗糙度值为3.2可采用粗铣—精铣方案。
2.2数控加工工艺路线设计
2.2.1.选择定位基准
从保证工件加工精度要求出发,定位基准应先选精基准,再选粗基准。
精基准的选择主要应考虑保证加工精度和工件安装方便可靠。
选择原则包括基准重合原则、基准统一原则、自为基准原则、互为基准原则、便于装夹原则。
粗基准的选择主要保证各加工表面有足够的加工余量,使加工面与不加工面间的位置符合图样要求,并特别注意尽快获得精基面。
选择原则包括选择重要表面、不加工表面、加工余量最小的表面作为粗基准。
因此端盖零件以自为基准原则选择上顶面为粗基准,下底面为精基准。
2.2.2.确定数控加工方法
获得同一级精度及表面粗糙度的加工方法有多种,在实际选择时要根据零件的加工精度、表面粗糙度、结构形状、尺寸、批量、毛坯材料及毛坯热处理等情况合理选用加工方法。
内孔表面加工方法根据被加工孔的加工要求、尺寸、具体生产条件、批量及毛坯上有无预制孔等情况合理选用。
孔常用选择方法通过查阅《机械加工工艺手册》表4.1-12[14],选择钻孔IT12级,扩孔IT10级,铰孔IT9,精铰IT7级。
平面加工方法通过查阅《机械加工工艺手册》表4.1-20[14],选择面铣IT12级,立铣IT12级
2.2.3.划分加工阶段
粗加工的主要任务:
去除各加工表面的余量并加工出精基准;
半精加工的主要任务:
减小粗加工中留下的误差,使加工表面达到一定的精度,为精加工做好准备;
精加工阶段的主要任务:
确保加工零件的尺寸、形状和位置精度达到或基本达到图样规定的精度要求以及表面粗糙度要求。
此端盖零件首先以下底面作为粗基准加工上顶面,再以上顶面为精基准加工下底面,以下底面作为精基准进行钻孔等工序。
对于零件的孔的加工,以先粗后精的原则加工。
2.2.4.划分加工工序
数控机床工序划分的一般原则:
按所用的刀具划分:
适用于工件的待加工表面较多、机床连续工作时间过长、加工程序的编制和检查难度较大等情况,加工中心常采用。
按安装次数划分:
适用于加工内容不多的工件。
按粗、精加工划分:
适用于加工后变形大,需粗、精加工分开的零件,如毛坯为铸件、焊接件或锻件。
按加工部位划分:
适用于加工表面多而复杂的零件。
2.2.5.确定加工顺序
切削加工顺序的安排:
基准面先行:
先加工出作精基准的表面,后加工以精基面定位的表面。
先面后孔:
先加工定位平面和孔的端面,后加工孔以利于工件定位夹紧稳定可靠、保证孔与平面的位置精度、减少刀具磨损。
先粗后精:
先安排粗加工(如有必要中间可半精加工),后安排精加工。
先主后次:
先安排主要表面的加工(如装配基面、工作表面),后安排次要表面的加工(如键槽、紧固用的螺纹孔);
一般主要表面的半精加工之后,精加工之前进行。
结合上述零件图结构工艺性分析、工序划分的原则、加工顺序安排原则初步拟定三种加工方案。
方案如下:
(一)第一种加工方案:
铣上顶面—铣下底面—钻中心孔—钻削两侧孔—铣两侧Φ22孔—钻中间孔—扩中间孔—粗铰中间孔—精铰中间孔—去毛刺
(二)第二种加工方案:
铣上顶面—铣下底面—钻中心孔—粗钻中间孔—扩中间孔—粗铰中间孔—精铰中间孔—钻两侧孔—铣两侧Φ22孔—去毛刺。
(三)第三种加工方案:
铣上顶面—铣下底面—钻中心孔—钻削两侧孔—钻中间孔—钻削两侧孔—扩中间孔—粗铰中间孔—精铰中间孔—铣两侧孔—去毛刺。
综上三种方案其中第一种方案既具备刀具集中原则又具备先粗后精原则。
2.3.确定毛坯类型及工序尺寸及公差
零件结构简单可选取毛坯为铸件,毛坯的工序尺寸及公差的具体值如下:
(1)对于上顶面和下底面,因为基准不重合因此用根据工艺尺寸链方法获得。
经查表Z1=Z2=4mm,z1、z2为加工余量.工序经济精度为IT12级
(2)对于Φ13孔
工序名称
工序余量
工序经济精度
工序基本尺寸
工序尺寸及公差
钻
13
0.22
毛坯
(3)对于Φ22凹槽
铣
4.5
0.33
22
(4)对于Φ40孔
精铰
0.07
0.025
40
粗铰
0.15
0.074
40-0.07=39.93
扩
1.75
0.16
39.9-0.15=39.75
10
0.25
39.75-1.75=38
28
0.21
2.4.确定总加工余量与毛坯尺寸
根据毛坯类型与加工方案,毛坯尺寸为160mm,100mm,40mm,22mm, R20mm,R30mm,Φ60mm,其公差等级为IT13级。
毛坯图如下:
2.5.确定工件装夹与定位方案
1)尽可能做到设计基准工艺基准与编程计算基准的统一
2)尽量将工序集中减少装夹次数,尽可能在一次装甲后能加工出全部的加工表面
3)避免采用占人机人工调整时间长的装甲方案
4)夹紧的作用点应落在零件刚性较好的方位
针对该零件的结构特点,加工表面60外圆及其台阶和空隙时采用平口钳夹紧,铣削为轮廓是采用一面两孔定位方式
2.6.确定各工序的切削用量
背吃刀量、进给量、切削速度和主轴转速的确定。
选择切削用量时要在保证加工质量和刀具耐用度的前提条件下,充分发挥机床性能和刀具切削性能使切削效率最高,加工成本最低。
当刀具寿命一定时切削速度对生产率影响最大,进给量次之,被吃刀量最小;
故切削用量选择原则:
首先选择尽量大的背吃刀量,其次选择最大的进给量,最后选择最大的切削速度
(1)背吃刀量的选择:
根据加工余量确定,切削加工一般为粗加工、半精加工和精加工几道工序,各工序有不同的选择方法。
粗加工时(表面粗糙度≥12.5),在允许的条件下,尽量一次切除该工序的全部余量。
中等功率机床,背吃刀量可达8~10mm,但是对加工余量,一次走刀会造成机床功率或刀具强度不够,或加工余量不均匀引起振动,或刀具受冲击严重出现打刀等情况,则需要采用多次走刀;
如分两次走刀,则第一次背吃刀量尽量取大,一般为加工余量的2/3~3/4左右;
第二次背吃刀量尽量取小,一般为加工余量的1/4~1/3左右。
(2)进给量选择:
根据零件材料硬度,刀具进行查表选择。
确定铣刀每齿进给量后,进给速度可按下式计算:
式中:
为每齿切削量,为铣刀的齿数,为转速。
(3)切削速度的选择:
确定了背吃刀量、进给量和刀具耐用度,查表确定切削速度。
(4)主轴转速主要根据切削速度确定:
为切削速度,单位;
为刀具直径,单位。
综上选取各工序的切削用量如下:
1)铣基准面
选择加工中心虎钳夹具硬质合金端面铣刀
Ap=4mmf=40mm/minVc=70m/minnc=180r/min
2)钻13的孔
选择加工中心虎钳夹具13的钻头
Ap=23mmf=30mm/minVc=20m/minnc=500r/min
3)铣上表面
选择加工中心一面两孔定位硬质合金端面铣刀
Ap=5mmf=40mm/minVc=70m/minnc=180r/min
4)铣60外圆
选择加工中心一面两孔定位硬质合金立铣刀
Ap=0.5mmf=25mm/minVc=70m/minnc=360r/min
5)钻40的孔
选择加工中心一面两孔定位13的钻头
Ap=41mmf=40mm/minVc=23m/minnc=200/min
5)铣40的孔
Ap=0.5mmf=25mm/minVc=70m/minnc=360r/min
6)铣22的沉槽
7)精镗40的孔
选择加工中心一面两孔定位40的镗孔刀
Ap=41mmf=40mm/minVc=74m/minnc=600r/min
2.7.制定数控加工工艺卡
通过对端盖零件加工工艺分析和加工方案的比较及切削用量的确定,现制定端盖零件数控加工工艺卡。
(见附表一)
2.8.刀具的选择和刀具卡的制定
选择刀具主要考虑因素有工件材料、刀具材料、切削用量、工艺系统刚性等工艺条件及机床功率等。
2.8.1.数控铣刀
选取刀具时,要使刀具的尺寸与被加工工件的表面尺寸和形状相适应;
同时根据不同的工件材料和加工精度要求选择不同参数的铣刀进行加工。
加工较大的平面、较大的台阶面应选择面铣刀;
加工平面零件周边轮廓、凹槽、较小的台阶面应选择立铣刀;
加工空间曲面、模具型腔或凸模成型表面应应选择模具铣刀;
加工封闭的键槽应选择键槽铣刀;
加工变斜角零件的变斜角面应选择鼓形铣刀;
加工立体型面和变斜角轮廓外形常采用球头铣刀、鼓形铣刀;
加工各种直的或圆弧形的凹槽、斜角面、特殊孔应选择成型铣刀。
1)刀片断屑槽形的选择:
有L、M、H三种,选取M型
2)刀具齿数的选择:
粗齿:
适用于大余量粗加工和软材料或切削宽度较大的铣削加工;
当机床功率较小时,为使切削稳定,也常选用粗齿。
中齿:
系通用系统,使用范围广泛,具有较高的金属切削率和切削稳定性。
密齿:
主要用于铸铁、铝合金和有色金属的大进给速度切削加工
不等分齿距:
为防止工艺系统出现共振,使切削平稳时选用。
对于此零件选取粗齿。
3)主偏角的选择:
铣刀的主偏角是由刀片和刀体形成的,主偏角对径向切削力和切削深度影响很大。
主偏角与径向切削力成正比。
径向切削力的大小直接影响切削轴功率和刀具的抗振性能。
铣刀的主偏角越小,径向切削力越小,抗振性能也越好,但切削深度随之减小。
该零件所用铣刀主偏角取90°
4)铣刀直径的选择:
面铣刀直径主要根据工件宽度选择,同时要考虑机床的功率、刀具的位置和刀齿与工件接触形式等,也可将机床主轴直径作为选取的依据。
面铣刀直径可按D=1.5d(d:
主轴直径)选取。
一般,面铣刀的直径应比切宽大20%~50%。
铣刀直径D=80mm,长度L=220mm
立铣刀直径的选择主要应考虑工件加工尺寸的要求,并保证刀具所需功率在机床额定功率范围内。
小直径立铣刀,就主要考虑机床的最高转速能否达到刀具的最低切削速度要求。
选取立铣刀(GB1110-85),立铣刀直径D=10mm,长度L=72mm
2.8.2.钻头
标准麻花钻:
切削部分有两个主切削刃,两个副切削刃、一个横刃和两个螺旋槽组成。
在加工中心上钻孔,因无夹具钻模导向,受两切削刃上切削力不对称的影响,容易引起钻孔偏斜,故要求钻头的两切削刃必须有较高的刃磨精度。
此处选硬质合金锥柄麻花钻(GB1436-85)直径D=13mm,长度L=151mm硬质合金锥柄麻花钻(GB1438-85)直径D=38mm,长度L=349mm硬质合金锥柄扩孔钻(GB1141-84)直径D=39.6mm,长度L=349mm。
2.8.3.中心钻
主要用于孔的定位,由于切削部分的直径较小,故中心钻钻孔时应选取较高的转速。
A型不带护锥的中心钻:
加工直径d=1-10mm的中心孔时,通常采用A型;
B型带护锥的中心钻:
加工直径d=1-10mm中心孔时工序较长、精度要求较高的工件,为避免60度定心锥被损坏,一般采用B型;
C型:
带螺纹的中心钻;
R型弧形中心钻:
加工直径d=1-10mm中心孔时的定位精度要求较高的轴类零件(如圆拉刀),则采用R型。
该零件选取A型不带护锥直径为D=2mm,长度L=220mm中心钻。
2.8.4.铰刀
多用于加工中心。
铰孔的加工精度可达IT9~IT8级,表面粗糙可以达到1.6~0.8μm。
锥柄铰刀直径为10~32mm,直柄铰刀直径为6~20mm;
小孔直柄铰刀直径为1~6mm;
套式铰刀直径为1~6mm
此处选硬质合金莫氏锥柄机用铰刀(GB4252-2004),直径D=40mm.长度L=329mm
综上可制定数控加工刀具卡(见附表二)
2.9.数控加工程序说明
程序名为O0002
N100-N128铣上顶面,起刀点为X-146.089Y-49.998铣深Z-3mm
N130-N142钻Φ13孔左(右)孔起刀点X-60.Y0(X60.Y0)钻深为Z-49
N144-N202铣Φ22凹槽左(右)起刀点X-60.026Y-3.5(X60.026Y3.5)铣深Z-29
N208-N218钻中间孔Φ38起刀点X0.Y0钻深Z-55
把Φ38扩孔至Φ39.8(此程序未列出)
N2028-N2038铰中间孔Φ40起刀点X0.Y0铰深Z-45
2.10.数控加工仿真图(见附表三)
第三章总结
此次毕业设计是我们从大学毕业生走向未来工程师重要的一步。
从最初的选题,开题到计算、绘图直到完成设计。
其间,查找资料,老师指导,与同学交流,反复修改图纸,每个过程都是对自己能力的一次检验和充实。
通