西南科技大学--基于MCGS的锅炉温度控制系统设计Word格式文档下载.doc
《西南科技大学--基于MCGS的锅炉温度控制系统设计Word格式文档下载.doc》由会员分享,可在线阅读,更多相关《西南科技大学--基于MCGS的锅炉温度控制系统设计Word格式文档下载.doc(20页珍藏版)》请在冰点文库上搜索。
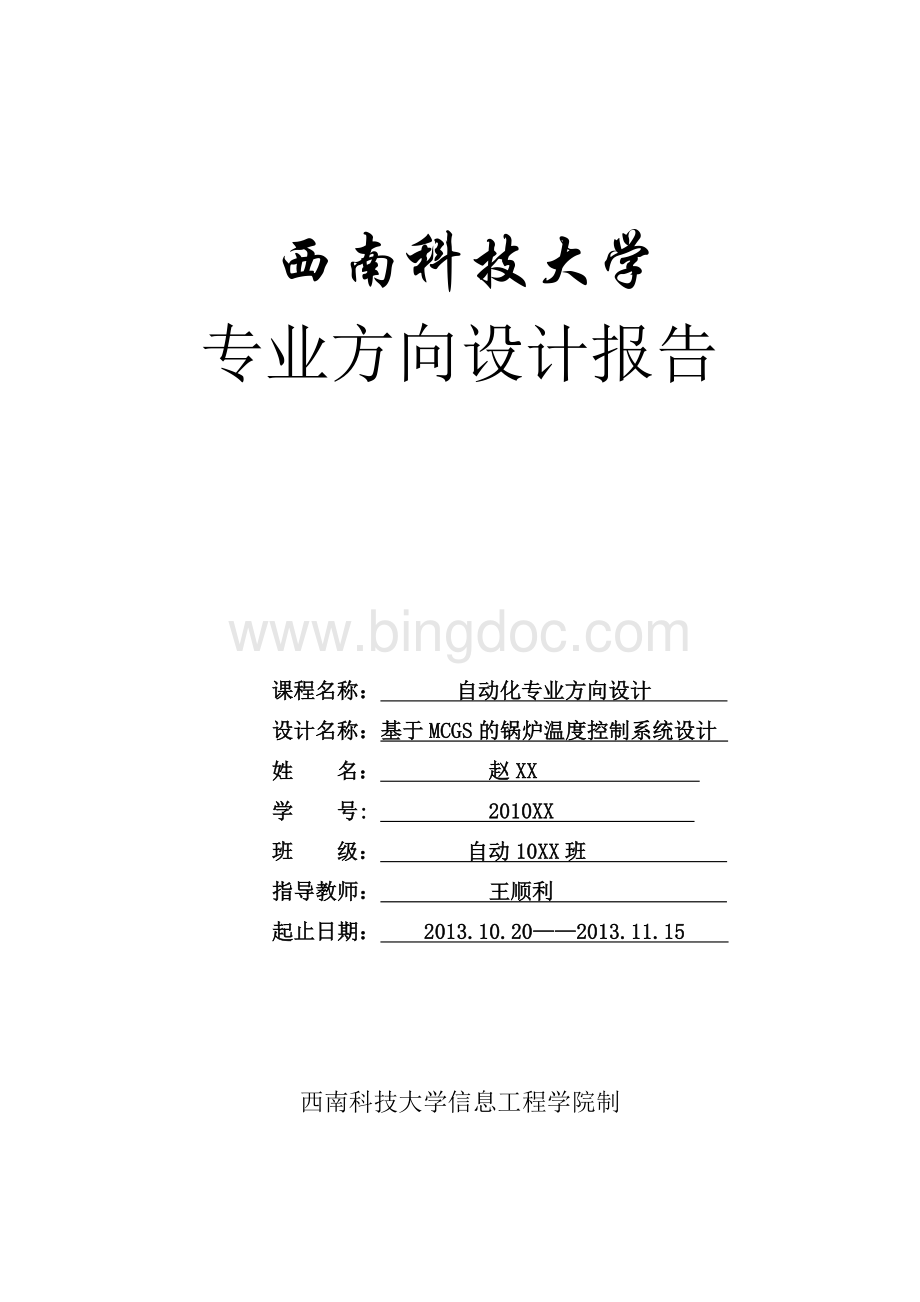
分析相关控制参数并设置的整个控制系统。
1、系统结构的整体设计
1)设计控制系统硬件结构;
2)针对具体的相关环节设计对相关器件进行选型,要求测温范围为0-100℃,选择合适类型的检测元件;
3)根据要求绘制系统控制流程图。
2、程序设计与实现
设计控制程序实现对锅炉温度控制并进行模拟显示,有效考虑反馈调节。
3、课程设计论文应完成的工作
论文摘要,中英文均要求。
关键词(3—5个),中英文关键词。
前言、方案论证及方案选择、系统的硬件、软件设计或实验模拟分析、调试及结论、致谢、参考文献
方向设计学生日志
时间
设计内容
2013.10.20—2013.10.25
查阅MCGS相关资料,了解MCGS基本操作及如何与PLC通信
2013.10.25—2013.10.27
对PLC、MCGS、传感器、可控硅执行机构进行分析
2013.10.27—2013.10.29
进行系统硬件连接
2013.10.29—2013.11.02
测试传感器、执行机构是否正常,有无偏差
2013.11.02—2013.11.04
编写程序
2013.11.04—2013.11.06
整定参数
2013.11.06—2013.11.08
整理资料,编写设计报告
基于MCGS的锅炉温度控制系统设计
摘要:
锅炉是工业生产中主要的供热设备。
电力、机械、冶金、化工、民用都需要锅炉提供热量,但是根据行业的不同,对锅炉的大小规模不尽相同。
作为重要的工业设备,在保证其安全和稳定运行的情况下则应考虑其自动生产,提高自动运行能力及工作效率。
本设计基于AE2000B实验设备上模拟现场锅炉温度控制系统,通过西门子S7-200PLC作为控制器,MCGS作为上位机,通过通信链接对锅炉温度进行实时监控,同时设计系列联锁,保证系统安全运行。
关键词:
锅炉温度AE2000BPLCMCGS
BasedontheMCGSboilertemperaturecontrolsystemdesign
Abstract:
Theboileristhemainheatingequipmentintheindustrialmanufacture.Theelectricpower,themachinery,themetallurgicalindustry,thechemicalindustryandthecivilallneedtheheattheboileroffers.However,accordingtodifferentindustries,Thesizeoftheboilervariesfromonetoanother.Asanimportantindustrialequipment,ifwecouldensureitssafeandstableoperation,weshouldconsideritsautomaticproductionandimprovetheautomaticabilityanditsworkingefficiency.ThisdesignisbasedonAE2000BexperimentaldevicetosimulatethespotboilertemperaturecontrolsystembyusingtheSiemensS7-200PLCasthecontrollerandtheMCGSasuppermachine.Meanwhile,thecommunicationlinkwillsupervisetheboilertemperaturetimelyandtheinterlockingserieswillguaranteethesafeoperationofthesystem.
Keywords:
boilertemperatureAE2000BPLCMCGS
1设计目的和意义
锅炉生产在国民是工业中占据着重要的地位,早期的锅炉自动化程度很低,监控系统不完善,导致系统故障不断,但是锅炉因为适合各种行业仍然被广泛使用,锅炉的广泛使用使锅炉现代化成为必然。
锅炉现代化的管理不但需要安全、高度自动化的控制方案,还需要考虑高效、节能、环保等方面的因素。
所以对于锅炉的自动运行这一方面还需要我们做控制的人不断的研究和探索,力争将锅炉实际运行生产达到安全、高效的高度。
本设计通过用PLC作为控制器,PID算法作为灵魂,对锅炉温度控制系统的设计,力争使锅炉控制系统结构简单、检修维护方便快捷、可靠性提高,同时增强控制系统的响应速度和稳定性,使锅炉控制系统的先进性整体提升。
2控制要求
采用北京昆仑公司的MCGS工业控制组态软件,通过RS232/RS485转换器使PC机与选定下位机(PLC)进行通信。
3设计方案论证
3.1锅炉部分分析
构成锅炉的温度控制方法有很多种,但基本都是基于锅炉的给热量和散热量平衡的关系来确定的,当给热量和散热量平衡时炉温保持在给定的范围内。
当某种因素出现变动时,从温度传感器采集的实际温度与给定温度进行比较,得到两者的差值,即偏差。
控制器根据实际偏差值的具体情况按照指定规律发出相应信号,控制被控量的大小,使温度恢复到给定值的范围内,从而实现对温度的自动控制。
根据不同类型的锅炉以及现场的具体情况有不同的控制方法。
从用途就可分为生活锅炉、工业锅炉、电站锅炉。
生活锅炉主要是在低压情况下运行,为日常生活提供热水,亦可称为热水锅炉,本设计即为此类锅炉的缩影;
工业锅炉基本在高压下进行生产,其需要提供大量热量;
电站锅炉主要是将水加热到高温高压的蒸汽状态,从而驱动汽轮机,进行发电,亦可成为蒸汽锅炉。
另一方面主要从燃料的角度区分锅炉,主要有燃煤锅炉、燃油锅炉、燃气锅炉、电加热锅炉等。
基于燃煤、燃油、燃气的三类锅炉均需要空气做助燃剂,当燃料与空气的比值适合时才能发挥最大的能效,因此此类控制系统必然会用到比值控制等复杂算法,同时燃烧的过程复杂、干扰多,还需要对烟气含氧量、炉膛火焰等情况进行监控,故而此类燃烧方式的锅炉大多需要复杂、精确地设计、调试验证及试运行后才能投入到现场生产中;
电加热锅炉因为其提供能量方式单一,调节加热器的电流或者电压大小即可对炉温进行控制,同时延迟不大,能源使用率较高等因素被受亲睐,但是其能提供的能量较少因此使用的规模不大。
表1不同燃料的锅炉性能分析
燃煤锅炉
燃气锅炉
燃油锅炉
电加热锅炉
锅炉效率
80%以下
90%
85%
100%
助燃剂
空气
无
备注
技术成熟、首次投资小、烟气污染大但是提供能量多,适合电厂蒸汽锅炉等规模较大场合
技术成熟、天然气需要储罐或者管道运输、燃料成本高
技术成熟、重油需储罐、烟气需要脱硫、燃料成本高
供热较小、无污染、适合小规模场合使用
基于实际条件及控制要求,本设计选择在AE2000B型实验装置下的电加热型热水锅炉作为对象。
AE2000B型过程控制实验装置是浙大中控根据工业自动化及相关专业教学特点,吸取了国外同类实验装置的特点和长处,并与目前大型工业自动化现场紧密联系,采用了工业上广泛使用并处于领先的AI智能仪表加组态软件控制系统、DCS(分布式集散控制系统),经过精心设计,多次实验和反复论证,推出的一套基于本科,着重于研究生教学、学科基地建设的实验设备。
AE2000型过程实验装置的检测信号、控制信号及被控信号均采用ICE标准,即电压1~5V、电流4~20mA。
3.2控制器分析
由于实际的工业现场情况复杂,干扰较多,因此在控制器方面因选择抗干扰能力强、运行稳定的控制器,综合单片机、PLC等控制器的特点,本设计选择西门子S7-200型PLC作为控制器。
常用的西门子S7-200系列的PLC有224或226,本次设计选用224作为控制器。
西门子S7-200系列PLC作为西门子推出的小型PLC,拥有体积小、通讯开放、程序和数据存储器较大、集成的RS485接口、扩展性良好、指令功能强大等特点,被广泛用于工业生产现场的小规模控制系统。
表2控制器选型分析
单片机
PLC
价格
便宜
贵
功能
随意开发
部分受限
稳定性
相对较差
好
其他
学习相对复杂、抗干扰能力弱、造价低
学习简单、工程造价高、抗干扰能力强、可靠
3.3组态软件分析
组态软件在国内是一个约定俗成的概念,并没有明确的定义,它可以理解为“组态式监控软件”。
是指用户通过类似“搭积木”的简单方式来完成自己所需要的软件功能,而不需要编写计算机程序,也就是所谓的“组态”。
组态软件,又称组态监控软件系统软件。
它是指一些数据采集与过程控制的专用软件。
它们处在自动控制系统监控层一级的软件平台和开发环境,使用灵活的组态方式,为用户提供快速构建工业自动控制系统监控功能的、通用层次的软件工具。
组态软件的应用领域很广,可以应用于电力系统、给水系统、石油、化工等领域的数据采集与监视控制以及过程控制等诸多领域。
目前常用的组态软件有西门子的WINCC、北京昆仑的MCGS、亚控的组态王、北京三维的力控,国外的组态软件大多只针对自己的PLC,而国内的组态软件基本能与几大主流的PLC进行配合使用。
表3主要组态软件情况对比
WINCC
MCGS
组态王
力控
所属公司
西门子
北京昆仑
亚控科技
北京三维
属性
国际产品
国内产品
知名度
较早出现
国内组态第二品牌
国内最早,装机量最多的组态软件
近几年发展的产品
兼容性
支持西门子产品
兼容性强
其他
软件加密不够严密,国内盗版多
基于VB开发、效率较低、系统稳定性差
国外组态软件的替代品,多用于需求较大场合
系统相对稳定、驱动比较完善、推广和售后都较好
本设计选择北京昆仑的组态软件MCGS作为上位机,MCGS是一套用于快速构造和生成计算机监控系统的组态软件。
它能够在基于Microsoft的各种32位Windows平台上运行,通过对现场数据的采集处理,以动画显示、报警处理、流程控制和报表输出等多种方式向用户提供解决实际工程问题的方案,在自动化领域有着广泛的应用。
4系统设计
本设计使用西门子S7-200型PLC作为控制器,北京昆仑的组态软件MCGS作为上位机,通过现场温度传感器进行温度采集,使用可控硅调节加热器两端电压等系列方法控制加热效果,达到控制的所需要的工艺要求。
目的在于设计过程中能够了解S7-200PLC是如何被运用于工业实际生产过程的,解决工业现场干扰多、情况复杂等情况下大多数控制器不稳定的问题。
通过在上位机上动手操作和观察,实时远程监控锅炉内水温的具体情况,并得到完整的炉温实时曲线。
同时监控工艺运行时是否正常,达到安全生产的目的。
4.1工艺分析
所选被控对象是常见的电加热锅炉,通过电加热棒与待加热液体直接进行热传递,将一定量的液体加热到工艺要求的温度。
图1锅炉加热系统流程图
待加热液体由丹麦泵直接抽到锅炉中,同时输送管道上面有电动调节阀,锅炉内部也有液位传感器,传感器与电动调节阀形成闭环控制回路,保证锅炉内部液体稳定,同时在程序内设定液位上下限,保证锅炉内运行安全。
在锅炉内有电加热棒并通过单相SCR可控调压装置控制其输出电压,同时锅炉内有温度检测装置,两者与控制器PLC构成闭环控制回路,达到调节温度的目的。
在本设计中要求控制锅炉温度,故而对于液位部分只检测锅炉内有无液体,将此液位作为参考值,在安全控制方面作为液位上、下限的报警值。
4.2硬件选型
本设计主要选择控制器、加热装置、温度检测装置、上位机选型等。
控制器选择西门子S7-200系列PLC,型号为224;
加热装置为电加热棒,可控硅调节其端电压,调压范围为0—220V;
温度检测装置选择铂热电阻PT100,其温度测量范围为0—100℃。
4.3硬件连接及I/O分配
锅炉温度控制系统主要有温度传感器、变送器、控制器PLC、带MCGS的PC机作为上位机、执行机构可控硅调压电路等构成,其结构如图2。
图2锅炉温度控制系统结构图
计算机上装有MCGS可作为上位机,同时计算机通过PC/PPI电缆通过RS485通信与PLC进行通讯,西门子S7-200PLC与模拟量模块EM235安装在同一导轨上,PLC的CPU模块224有24个I/O接口,其中有14个输入端、10个输出端,输入端口外接开始按钮、停止按钮、急停按钮,输出端口外接工作指示灯、报警指示灯、正在加热指示灯,模拟量模块EM235有4路模拟量输入端口、1路模拟量输出端口,其中模拟量输入端口根据外接电路的接法不同可以分为1—5V电压型和4—20mA电流型,模拟量输出端可选择V或者I来确定需要电流输出还是电压输出。
本设计选择3路数字量输入、2路数字量输出、1路模拟量标准电流输入、1路数字量标准电流输出,其具体分配情况见表4。
表4PLC硬件连接情况及I/O分配
名称
类型
地址
备注
开始按钮
数字量(BOOL)
I0.0
停止按钮
I0.1
常闭
急停按钮
I0.2
工作指示
M0.0/Q0.0
中间继电器/输出继电器
报警指示
M1.0/Q0.1
加热指示
M1.1/Q0.2
温度采集
模拟量(4—20mA)
AIW0
电流接法
可控硅输出
AQW0
温度实时值
VD14
比例参数设定
VD132
积分参数设定
VD140
微分参数设定
VD144
温度设定值
VD250
可控硅端电压
VD320
硬件连线主要有温度变送器的接线与PLC的接线、可控硅与PLC的接线。
温度变送器PT100与PLC的接线如图3。
图3温度变送器与PLC连接
可控硅与电加热棒构成一个电压可调的模块,通过调节给到电热棒两端的电压大小来改变电加热棒对锅炉内液体供热的大小,从而达到加热的目的,单相SCR可调压装置与PLC的接线如图4。
图4单相SCR可调压装置与PLC接线图
4.4输入、输出信号转换
由于采集的数据都为工程中的实际数据,单位、幅值和范围也不同,必须将其转换成标准形式才能被控制器PLC接受执行。
转换的第一步是将给定值或A/D转换后得到整数值由16位转换成浮点数,转换后的下一步是将实数进一步转换成标准化实数,锅炉温度测量范围是0~100℃,模拟量的标准电信号是4-20mA,A/D转换后数值为6400-32000,
设T为转换后的温度值,则其转换公式如下:
(1)
对于输出信号亦是同样的设计公式,设U为输出电压,其转换公式如下:
(2)
4.5系统框图
设计锅炉温度的闭环控制回路,其具体框图如图5。
图5锅炉温度闭环控制系统框图
4.6控制对象模型
本设计的锅炉水温控制系统科理解为一介滞后系统,其传递函数为:
(3)
5设计结果及分析
5.1水箱水位检测
水箱实际温度的检测是要把测得的温度量转化为0.0到1.0之间的数以便于PLC能够识别。
因为PID只能针对浮点型实数进行运算,因此要先把温度变送器输出的值转换成16位的整型存储在累加寄存器AC0中,再将AC0中的值转化为32位的双整型继续存放于AC0中,接着把AC0中的数由双整型转化为实型,仍然存放到AC0中。
鉴于实型数的小数点有6位,所以其相对来说还是比较精确的。
接下来就要把实数再转化成PLC能够识别的0.0~1.0之间数。
其具体程序见附录。
5.2输出到可控硅电压
经过PID运算后从AQW0输出的信号为6400—32000的标准值,可以直接加到可控硅模块控制电压大小,但是我们亦需要将其转换为可以识别的电压大小,其具体程序见附录。
5.3PID算法在S7-200PLC中的实现
S7-200的编程软件Micro/WIN提供了PID指令向导,PID控制程序可以通过指令向导自动生成,但是PID指令也能够被程序自动调用。
首先选择运用PID算法的回路,本系统就一个回路,故选择回路0,如图6所示。
图6回路选择
第二步选择好回路后设定回路的参数,由于本设计采用水作为加热液体,而选择的PT100也是0—100℃的测温,因此给定范围的低限和高限分别为0和100,回路的参数暂时先不设定,如图7所示。
图7给定值范围的设定
第三步设置回路输入输出项,输入和输出量都是单级性的模拟量,全部选择“使用20%偏移量”,因为S7-200的单极性模拟量输入输出信号的数值范围是6400—32000,所以输入项的量程为6400—32000。
如图8所示。
图8回路输入输出参数性质配置界面
5.3报警及系列连锁程序
程序除了温度采集、电压大小转换、PID程序以外还需要设计报警程序以及程序连锁等系列附加程序,保证设备安全运行。
添加的附加程序有:
超温报警、超绝对高温停机保护、无水不加热程序等。
这类程序虽然在系统正常运行时不会动作,但是在各类突发情况出现时能直接处理或者安全停机,达到保护设备的目的。
这些功能的具体程序见附录。
5.4控制系统仿真及参数整定
在PID参数整定中,工程整定法因其固有的优点而受到广大工程技术人员的欢迎。
同时工程整定法中的稳定边界法由于简单易行而仍在广泛的使用,但是稳态边界法在常规的实验中还是有其固有的弱点,如在做实验时必须把控制系统调到等幅震荡,这样就可能会影响实验设备受到损坏。
此时,我们就想到利用软件仿真的形式来实现对PID参数的整定,而MATLAB/Simulink就给我们提供了一个良好的软件平台。
下面我们在MATLAB/Simulink仿真环境下整定水箱温度PID控制参数。
常规的PID参数整定
根据PID控制模型,利用SIMULINK灵活的非线性设计功能,通过对系统对象分析及建模分析,综合实际情况可建立SIMULINK模型如图9所示:
图9PID控制的SIMULINK模型
根据传递函数的各项系数,通过调节PID的各个参数,得到不同数组下的曲线并对比分析。
当Kp=100、KI=0.01、KD=50的时候运行SIMULINK模型,得到仿真曲线图如图10所示,得到理想的PID运行曲线。
图10Kp=100、KI=0.01、KD=50时的仿真曲线图
从图11可以看出系统在稳态时有比较小稳态误差,超调量为8.2%,在暂态时最大超调量比较大,曲线也比较陡峭,这么长的调整时间要求非常高的控制系统,所以还必须进一步调整控制参数,以使得系统工作在最佳的控制状态,通过多次试验,当Kp=50、KI=0.01、KD=50时得到最佳的控制效果如图11所示。
图11Kp=50、KI=0.01、KD=50时的仿真曲线图
在不改变参数的情况下,给系统加一个干扰,如图12所示:
图12PID加扰动的SIMULINK模型
运行SIMULINK模型得到相应的仿真曲线如图13所示:
图13PID加扰动的仿真曲线
根据图常规PID的抗干扰性测试看出,本次试验得到的参数还是比较理想的。
经过常规PID的抗干扰测试,可以看出系统的响应曲线基本没有太大波动。
5.4上位机界面及监控
设计的控制系统采用MCGS作为上位机,通过上位机对PLC及运行情况进行监视,监视工艺流程及各类参数,同时可通过上位机可直接对现场运行情况进行操作,上位机具体界面如图14。
图14组态界面
6结束语
通过这次方向设计,我有了很大的收获。
首先感谢指导老师王顺利老师,他的悉心指导才使我做方向设计步步深入,同时感谢大学以来所有给我上课的老师,他们传授的知识让我大学有了很大的收获;
第二:
以前学习的很多理论知识很多已经忘记,这次设计使得我必须重新翻书查阅以前学习的知识,这是对以前知识的巩固;
第三:
明白了学习不能光动脑不动手,有很都看似已经弄懂了的知识在实际中完全不知怎么用,所以只有实践才能发现很多问题,才能把知识掌握得更加牢固,同时还能提高自己的动手能力,才能发现书本上的知识与实际运用是有很大的差距的。
第四:
要学会与他人交流,有交流就会有进步。
参考文献
[1]毕效辉,自动控制理论[M],北京,中国轻工业出版社,2012.1
[2]薛定宇,控制系统极端及辅助设计[M],北京,清华大学出版社,2006.3
[3]方康玲,过程控制系统[M],武汉,武汉理工大学出版社,2009.3
[4]邵裕森,过程控制工程[M],北京,机械工业出版社,2013.1
[5]陈建明,电气控制与PLC应用[M],北京,电子工业出版社,2010.1
[6]柴瑞娟,西门子PLC高级培训教程[M],北京,