变频器的工程应用实例.ppt
《变频器的工程应用实例.ppt》由会员分享,可在线阅读,更多相关《变频器的工程应用实例.ppt(85页珍藏版)》请在冰点文库上搜索。
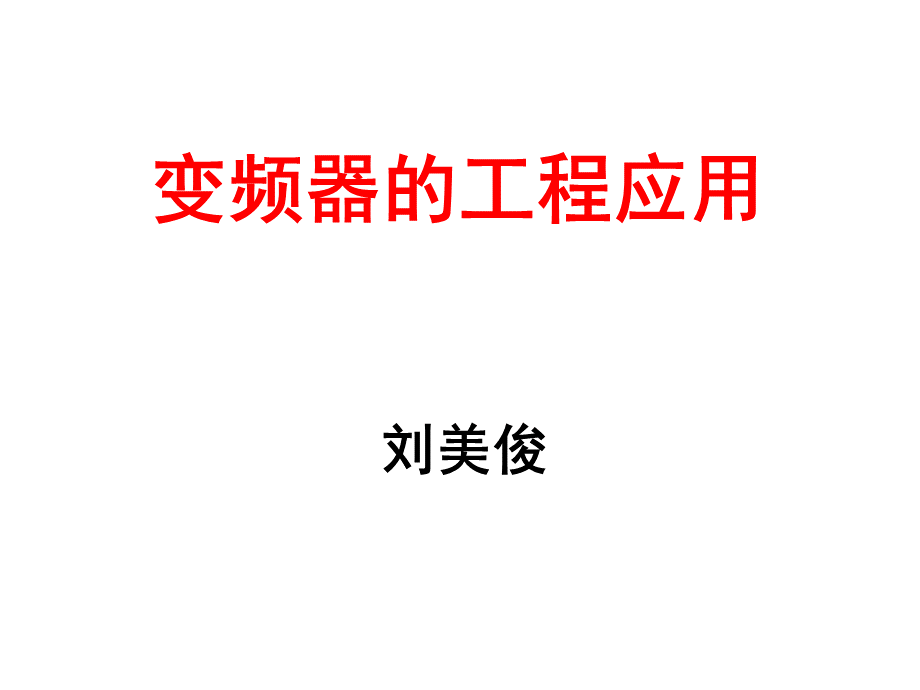
变频器的工程应用,刘美俊,西门子公司标准通用型变频器主要包括MM4、MM3系列变频器和电动机变频器一体化装置三大类。
其中,MM4系列变频器包括MM440矢量型通用变频器、MM430节能型通用变频器、MM420基本型通用变频器和MM410紧凑型通用变频器四个系列,这也是目前应用较为广泛的变频器。
下面重点介绍MM440变频器的操作方法及应用注意事项。
MM440变频器的电气安装,在变频器与电动机和电源线连接时必须注意以下几点:
1)变频器必须接地。
2)在变频器与电源线连接或更换变频器的电源线之前,应完成电源线的绝缘测试。
3)确信电动机与电源电压的匹配是正确的。
4)不允许把MM440变频器连接到电压更高的电源上。
MM440的开关量运行,MM440变频器有6个数字输入端口,用户可根据需要设置每个端口的功能。
从P0701P0706为数字输入1功能至数字输入6功能,每一个数字输入功能设置参数值范围均从099,工厂默认值为1,下面列出其中几个参数值,并说明其含义。
(1)参数值为1:
ON接通正转,OFFl停车。
(2)参数值为2:
ON接通反转,OFFl停车。
(3)参数值为3:
OFF2(停车命令2),按惯性自由停车。
(4)参数值为4:
OFF3(停车命令3),按斜坡函数曲线快速降速(5)参数值为9:
故障确认。
(6)参数值为10:
正向点动。
(7)参数值为11:
反向点动。
(8)参数值为17:
固定频率设定值。
(9)参数值为25:
直流注入制动。
MM440变频器数字输入控制端口开关量运行接线如图所示。
在图中SBlSB4为带自锁按钮,分别控制数字输入58端口。
端口5设置为正转控制,其功能由P0701的参数值设置。
端口6设为反转控制,其功能由P0702的参数值设置。
端口7设为正向点动控制,其功能由P0703的参数值设置。
端口8设为反向点动控制,其功能由P0704的参数值设置。
频率和时间各参数在变频器的前操作面板上直接设置。
系统操作步骤如下:
(1)连接好电路,检查线路正确后合上变频器电源空气开关Q。
(2)恢复变频器工厂默认值。
按下P键,变频器开始复位到工厂默认值。
(3)设置电动机参数,然后设P00100,变频器当前处于准备状态,可正常运行。
(4)设置数字输入控制端口开关操作运行参数,,1)电动机正向运行。
当按下按钮SB1时,变频器数字输入端口5为“ON”,电动机按P1120所设置的5s斜坡上升时间正向起动,经5s后稳定运行在560r/min的转速上。
此转速与Pl040所设置的20Hz频率对应。
松开按钮SB1,数字输入端口5为“OFF”,电动机按P1121所设置的5s斜坡下降时间停车,经5s后电动机停止运行。
2)电动机反向运行。
如果要使电动机反转,则按下按钮SB2,变频器数字输入端口“6”为“ON”,电动机按P1120所设置的5s斜坡上升时间反向起动,经5s后反向运行在560r/min的转速上。
此转速与P1040所设置的20Hz频率对应。
松开带锁按钮SB2,数字输入端口6为“OFF”,电动机按P1121所设置的5s斜坡下降时间停车,经5s后电动机停止运行。
3)电动机正向点动运行。
当按下正向点动按钮SB3时,变频器数字输入端口7为“ON”,电动机按P1060所设置的5s点动斜坡上升时间正向点动运行,经5s后正向稳定运行在280r/min的转速上。
此转速与P1058所设置的10Hz频率对应。
当松开按钮SB3时,数字输入端口7为“OFF”,电动机按P1061所设置的5s点动斜坡下降时间停车。
4)电动机反向点动运行。
当按下反向点动按钮SB4时,变频器数字输入端口8为“ON”,电动机按P1060所设置的5s点动斜坡上升时间反向点动运行,经5s后反向稳定运行在280r/min的转速上,此转速与P1058所设置的10Hz频率对应。
当松开按钮SB4时,数字输入端口8为“OFF”,电动机按P1061所设置的5s点动斜坡下降时间停车。
MM440模拟量运行,MM440变频器可以通过6个数字输入端口对电动机进行正反转运行、正反转点动运行方向控制,可通过基本操作板BOP或高级操作板AOP来设置正反向转速的大小;也可以由数字输入端口控制电动机的正反转方向,由模拟输入端控制电动机转速的大小。
MM440变频器为用户提供了两对模拟输入端口,即端口3、4和端口10、11,如下图所示。
模拟信号操作时的接线,图中,通过设置P0701的参数值,使数字输入5端口具有正转控制功能;通过设置P0702的参数值,使数字输入6端口具有反转控制功能;模拟输入3、4端口外接电位器,通过3端口输入大小可调的模拟电压信号,控制电动机转速的大小,即由数字输入端控制电动机转速的方向,由模拟输入端控制转速的大小。
由图可知,MM440变频器的1、2输出端为转速调节电位器RP1提供10V直流稳压电源。
为了确保交流调速系统的控制精度,MM440变频器通过1、2输出端为用户的给定单元提供了一个高精度的直流稳压电源,操作步骤,
(1)连接电路,检查接线正确后合上变频器电源空气开关Q。
(2)恢复变频器工厂默认值。
按下P键,变频器开始复位到工厂默认值。
(3)设置电动机参数。
设P00100,变频器当前处于准备状态,可正常运行。
(4)设置模拟信号操作控制参数。
1)电动机正转:
按下电动机正转按钮SB1,数字输入端口5为“ON”,电动机正转运行,转速由外接电位器RP1来控制,模拟电压信号从0V10V变化,对应变频器的频率从050Hz变化,通过调节电位器RP1改变MM440变频器3端口模拟输入电压信号的大小,可平滑无级地调节电动机转速的大小。
当松开按钮SB1时,电动机停止。
通过P1120和P1121参数,可设置斜坡上升时间和斜坡下降时间。
2)电动机反转:
当按下电动机反转按扭SB2时,数字输入端口6为“ON”,电动机反转运行,与电动机正转相同,反转转速的大小仍由外接电位器RP1来调节。
当放开按钮SB2时,电动机停止。
例1西门子MM440变频器的AOP面板仅能存储一组参数。
处理方法:
变频器选型手册中介绍AOP面板中能存储10组参数,但在用AOP面板做第二台变频器参数的备份时,显示“存储容量不足”。
其解决办法如下:
(1)在菜单中选择“语言”项。
(2)在“语言”项中选择一种不使用的语言。
(3)按FnA键选择删除,经提示后,按P键确认。
这样,AOP面板就可以存储10组参数。
造成这种现象的原因可能是设计时AOP面板中的内存不够。
MM440的维护实例,例2MM440变频器调试过程中发现只有参数P003和P004能被修改,其余参数都是只读,不能修改。
处理方法:
这是由于用户在调试过程中修改了参数P927(该参数用于定义修改参数的接口)造成的。
其定义如下:
Bit00:
PROFIBUS/CBBit01:
BOPBit02:
BOP链路的USSBit03:
COM链路的USS某位为“1”时,表示该位有效。
Bit01为“1”表示用户可通过BOP修改参数。
变频器显示面板7段显示结构图如图所示。
变频器显示面板7段显示结构图,例3怎样实现用编码器作为速度给定?
处理方法:
编码器装在与纱锭相连的测速轴上,作为变频器MM440的速度给定,如图所示。
用编码器作为速度给定,需要做以下参数设置:
(1)P1300不能为21或23,即不能为闭环速度或闭环转矩控制。
(2)P0400设为1或2,激活编码器对速度进行检测,如表所示。
(3)P1070设定为63。
编码器的连接,MM440变频器在料车卷扬调速系统中的应用,料车机械传动系统示意图,1交流电动机的选用炼铁高炉主卷扬机变频调速拖动系统在选择交流异步电动机时,需要考虑以下问题:
应注意低频时有效转矩必须满足的要求;电动机必须有足够大的起动转矩来确保重载起动。
针对本系统100m3的高炉,选用Y280S-8的三相交流感应电动机,其额定功率为37kW,额定电流为78.2A,额定电压为380V,额定转速为740r/min,效率为91%,功率因数为0.79。
本系统选用西门子MM440,额定功率55kW,额定电流110A的变频器。
该变频器采用高性能的矢量控制技术,具有超强的过载能力,能提供持续3s的200%过载能力,同时提供低速高转矩输出和良好的动态特性。
(2)制动单元。
从上料卷扬运行速度曲线可以看出,料车在减速或定位停车时,应选择相应的制动单元及制动电阻,使变频器直流回路的泵升电压UD保持在允许范围内。
可编程序控制器选用西门子S7-300,这种型号的PLC具有通用性应用、高性能、模块化设计的性能特征,具备紧凑设计模块。
由于使用了MMC存储数据和程序,系统免维护。
电源模块为PS-3072A,插入1号槽。
CPU为CPU315-2DP(保留PROFIBUS-DP接口,为今后组成网络作准备),型号6ES7315-1AF03-0AB0,插入2号槽。
数字输入模块选SM321DI16DC24V,型号6ES7321-1BH02-0AA0两块,一块插入4号槽内,地址范围为I0.0I0.7及I1.0I1.7;另一块插入5号槽内,地址范围为I4.0I4.7及I5.0I5.7。
数字输出模块选SM322DO16DC24V/0.5A,6ES7322-1BH01-0AA0型一块,插入6号槽内,地址范围为Q8.0Q8.7及Q9.0Q9.7。
MM440参数设置表,MM440运行频率表,MM440在离心机调速系统中的应用,其工艺步骤分为三步:
(1)慢速阶段23min,使混凝土分布钢模内壁四周而不塌落。
(2)中速阶段0.51min,防止离心过程混凝土结构受到破坏,这是从低速到高速的一个短时过渡阶段;(3)高速阶段615min,将混凝土沿离心力方向挤向内模壁四周,达到均匀密实成型,并排除多余水分。
各阶段的运行速度和运行时间视不同规格和型号的电杆而有所不同,其运行速度图如图所示,根据第3章变频器容量的选择方法进行计算,可选用37kW,额定电流75A的变频器。
考虑到改进设计方案的可行性、调速系统稳定性及性价比,采用西门子MM440,37kW,额定电流为75A的通用变频器。
该变频器采用高性能矢量控制技术,提供低速高转矩输出和良好的动态特性,同时具备超强的过载能力,可以控制电机从静止到平滑起动期间提供3s,200%的过载能力。
变频器的各项参数设置,基于变频器与PLC的恒压供水控制系统设计,将通往用户的用水水管中的压力变化经压力传感器采集给变频器,再通过变频器与变频器中的设定值进行比较,根据变频器内置的PID功能进行数据处理,将数据处理的结果以运行频率的形式进行输出。
当供水的压力低于设定压力,变频器就会将运行频率升高,反之则降低,并且可以根据压力变化的快慢进行差分调节。
由于本系统采取了负反馈,当压力在上升到接近设定值时,反馈值接近设定值,偏差减小,PID运算会自动减小执行量,从而降低变频器输出频率的波动,进而稳定压力。
供水系统方案,系统主电路图,PLC接线图,FR-A540变频器参数设定表,PLC程序流程,变频器在行车上的应用,行车和龙门吊车是目前工厂使用最多的起重设备,在行车的使用过程中,经常出现驱动大车行走的2台电动机在运行中不同步,造成行车整个车体相对于轨道出现偏移,使行车在行走中轮子挤压轨道,发出噪声,车体出现抖动,严重时使轨道移位。
为此,需要定时对行车轨道进行调整和校正,以保证行车的安全运行。
行车大车在行走过程中出现车体偏转,其原因是大车左右两边的轮子运行速度不一致,而两边轮子的速度分别取决于各自的驱动电机速度和传动机构速比。
由于制作工艺的限制,很难使两边速度完全一致。
为此要消除车体偏移,较好的办法是在运行过程中及时调整电动机的速度来矫正偏转,使两边轮子运行速度保持一致。
矫正行车偏转的方法有几种:
行车两大车电机中,一台采用交流绕线电动机来调速,另一台可采用直流电动机或转子滑差电动机来调速,或者仍采用绕线电动机,但通过串级调速来实现行车两边轮子的同步。
在上述方法中,采用直流电动机调速,系统需增设一台整流调压装置,且直流电动机存在换向火花等问题,不宜采用;采用转子滑差电动机调速,控制简单,但电机本身体积较大,行车上的安装位置不够;采用串级调速时,系统需增设逆变变压器和整流逆变装置,控制较复杂。
在上述三种调速方法中,还需用可编程控制器(PLC)来实现继电器线路与调速装置部分的逻辑连锁控制,整个系统线路复杂,投资费用高。
采用变频器来矫正行车电动机不同步,只需对原控制线路稍作改动,投资费用低,安装、维修方便,且系统的可靠性非常高。
行车构成示意图,行车两大车电动机仍采用原来的绕线式异步电动机,其中电机M2原控制方法不变,电机M1在原控制线路的基础上增设1台变频器,实现对该电机的变频调速,来调整行车的运行偏转。
为测量行车运行过程中的偏转,分别在行车车身左右两端靠近轨道处装设两个接近开关。
在行车前进过程中,如果右边轮子运行速度较慢,则车身偏转,接近开关KA1发出信号,说明此时电机M1需提速;反之,在前进过程中,当右边轮子运行速度较快时,车身偏移,使接近开关KA2发出信号,说明此时电机M1需减速。
为实现上述功能,选用ABB公司生产的200V系列变频器,型号为ACS143-4K1-1,,变频器矫正行车电机不同步接线图,KM1、KM2分别为大车前进、后退控制用接触器,其常开触点用来控制变频器的起停和正反转,KA2、KA1为左、右端接近开关,变频器D13、D14接线端用于连接变频器的速度给定信号,由接近开关控制。
给定速度设置如表所示。
当KA1、KA2都无信号输出时,说明行车运行正常,变频器保持输出频率50Hz不变。
在行车前进过程中(KM1为ON),当KA1闭合时,D13=1、D14=0,说明电机M1速度过慢,此时变频器输出频率增至55Hz,电机M1提速;反之,当KA2闭合时,D13=0、D14=1,变频率输出频率为45Hz,电机M1减速。
当KA1、KA2同时闭合时,D13=1、D14=1,说明系统出现故障,变频器报警。
当行车后退时,KA1、KA2的闭合与M1的增减速对应关系与前进时的对应关系相反,D13D14输出00正常50Hz01减速45Hz10加速55Hz11故障报警,在本控制线路中,通过变频器D18、D19运行端控制中间继电器KA5,实现与另一大车电动机运行的连锁,防止出现一台电动机运行、另一台电动机停止而造成大的故障。
依照本方法对大吨位行车的控制系统进行改进,行车在运行过程中能根据位置检测信号,实现对大车一台电机的实时变频调速,可以有效地克服行车运行中的不同步现象。
实验证明,这种改造方法效果良好,可靠性高,成本低,有较大推广价值。
线材卷绕机的变频调速,某钢铁公司连续线材轧制线由荒轧、飞剪、一中间轧、二中间轧、精轧及卷线机等机组组成。
其中精轧部分分四条线,每条线有两台卷线机,轮流将线材卷成盘卷。
线材轧机的平面布置如图1所示。
轧制原材料为60mm60mm、长12m、单重330kg的钢坯,产品为6.5mm的线材。
轧制线上原来的主传动系统都是直流调速系统。
精轧机组出口的最高轧制速度为29.8m/s。
卷线机的作用是把精轧机出来的成品线材卷成盘卷送出。
卷线机为钟罩式,其传动系统如图2所示,线材轧机的平面布置图,卷线机的传动系统示意图,卷线机将精轧机组出来的线材,通过转动的钟罩,成圈地按松卷方向放到滑板上卷成盘,再由推卷装置推到运输机上。
盘卷内径约850mm,外径约1150mm;盘卷大小与卷线机转速有关。
当精轧转速一定时,卷绕机转速高,则盘卷直径小,反之则大。
为保证盘卷外观整齐和减少精轧与卷线机之间堆积钢材,要求卷线机的转速能良好地跟随精轧机的转速变化。
卷线机的原拖动系统是由电子管,磁放大器,水银整流器变流装置组成的直流调速系统,控制线路十分复杂,同时,由于卷线机所处的环境温度高、振动大,故系统故障率高,维修频繁。
采用交流异步电动机变频调速系统代替直流拖动系统,对原有系统进行技术改造后,基本上解决了上述问题。
变频调速系统的器件选型,1主电动机选择主电动机容量,主要考虑以下因素:
(1)原直流电动机由于长期工作在基速以上(弱磁状态),所采用的“调磁调速电动机”为了增加转矩,加大了电枢的直径与长度,其尺寸比同容量的普通电动机大得多;
(2)电动机安装的周围环境温度高,且无法外加通风冷却装置;(3)交流电动机在基准频率以下工作时,其本身的散热功能变差;(4)交流电动机的短时过载能力不如直流电动机;(5)卷线机调速范围大,对过载能力要求较高。
基于以上考虑,技改时将交流电动机容量加大为原直流电动机的2倍左右,考虑到变频器的性能价格比,采用日本富士公司生产的G9S系列变频器,根据系统的控制要求,设计出系统的基本线路如图所示变频器调速系统的主要特点有:
(1)采用一台变频器控制一台电动机的工作方式,即“一拖一”;
(2)不需速度反馈装置;(3)保留原控制系统的操作方式、速度给定方式和信号显示方式;(4)省去原控制系统的整流变压器,保留原系统的直流平波电抗器作为变频器的直流电抗器,用来改善功率因数;(5)不需外加制动单元。
变频器的参数预置及调试,1最高频率、基本频率与上限频率的预置卷线机的额定转速为1500r/min,超速保护转速为1650r/min。
故基本频率预置为50Hz,最高频率预置为60Hz,上限频率预置为55Hz。
2频率增益的预置为保证卷线机的转速准确跟随精轧机的转速,两者的给定信号实际为同一信号。
原直流调速系统的速度给定信号按每伏200r/min设计,7.5V对应1500r/min,给定信号为08.5V。
变频器的给定信号为010V,10V时对应60Hz。
当给定信号为7.5V时,对应的给定频率为45Hz,对应的同步转速为1350r/min,达不到原系统的调速范围。
故将频率增益预置为125%。
3升速时间的预置精轧直流调速系统起动时,转速从0上升到1500r/min的给定积分时间为10s。
原卷绕机直流调速系统的给定积分时间为8s。
改为变频调速后,经动态测试,升速时间预置为5s为宜。
4降速时间的预置由于卷线机转动惯量大,如减速时间小于20s,会引起过电压跳闸。
经多次调试,将降速时间预置为30s,不但满足了生产工艺的要求,同时不需选用制动器件。
5拖动转矩、制动转矩极限值的预置通过多次调试,把拖动转矩限值预置为150%、制动转矩限值预置为30%较为合适。
6转差补偿的预置为提高系统的调速精度,本系统适当加入了转差补偿。
在调试过程中,转差补偿大于1Hz时,容易产生过电压跳闸。
实际预置为0.8Hz,完全可以满足调速精度的要求。
7输出频率信号的预置由于卷线机并无速度反馈装置,为了使操作台有一个电动机转速的指示,在操作台上设置了一块转速表。
此转速表实际上是010V的直流电压表,接在变频器的输出信号端“FMA”与“11”之间。
当变频器输出最高频率时,FMA端输出+10V。
表上的刻度是和变频器控制的电动机的同步转速成正比的。
调试中,为使操作台转速表的显示值和变频器显示的转速一致,将FMA端输出的直流电压调整比预置为125%。
卷线机变频调速系统经调试投入运行后,系统性能稳定,且完全能满足工艺控制要求,稳定性优于原来的直流调速系统,基本上做到了无故障运行,维护工作大为减少。
变频器在铣床中的应用,某厂用于机械零件加工的龙门铣床调速系统,原来采用三相半控桥不可逆直流拖动,分工作台、左主轴和右主轴三个进给方向。
其电气控制系统由于运行时间太长,直流调速插板已严重老化,同时,由于插板之间原来的连接线较多,由导线虚接造成的故障日渐增大,维修工作量不断加大,龙门铣床的调速系统急待技术改造。
变频器的控制方式,龙门铣床技术改造的对象是进给机构,其工作台进给和左、右主轴进给均属于恒转矩负载。
原来的直流调速系统的调速范围D=50,改造后的变频系统要达到501的调速比,必须选用带有矢量控制功能的高性能通用变频器。
矢量控制变频器组成交流调速系统可以有两种方案,一是使用速度传感器,检测出电机转速,再反馈给变频器;一是使用无速度传感器的矢量控制变频器,其调速范围可达到1001。
无速度传感器矢量控制是通过转矩电流的变化量的积分运算来推算电机的转速,有一定的推算误差。
如果要求进一步提高调速范围和精度,就必须选用带速度传感器的矢量控制变频器。
目前,市场上出售的带速度传感器的矢量控制变频器,调速范围可达10001,考虑到普通笼型电机安装速度传感器,不但增加工艺难度,而且加大了技术成本,而无速度传感器矢量控制变频器的主要技术指标。
已基本能满足技改的设计要求,所以初步决定选用日本春日KVFZ4110型无速度传感器矢量控制变频器。
该型号变频器的几项主要技术指标如下:
(1)调速范围。
无速度传感器矢量控制调速范围为1001。
(2)起动转矩。
1Hz时150%额定转矩;(3)频率精度。
频率精度为最高频率的0.1%。
变频器的容量计算及参数设定,1变频器容量计算在变频器容量计算前,要确定拖动负载的电机容量。
由于有原直流电机作参考依据,所以不必进行详细的转矩换算,只需选择与原直流电机容量相对应的笼型电机容量。
由于工作台拖动电机容量均大于左、右主轴进给电机容量,所以变频器容量的计算以工作台的电机为主要依据。
原工作台直流电机参数为:
PN=10kW,nN=1000r/min。
通过查电机手册,与原直流电机数据对应的笼型电机数据为:
电机型号Y160L-6,额定功率PN=11kW,转速nN=970r/min,额定电流IN=24.6A。
根据前面的分析,变频器连续运行时,其额定输出电流IINV应大于或等于电动机实际最大电流的1.1倍。
根据原来测试的数据换算,工作台进给的最大负载转矩为81Nm,换算到Y160L-6电机上的最大负载电流Imax19A,这样,变频器的额定输出电流应大于或等于1.119=20.9A。
查春日变频器手册,选择KVFZ4110型,其额定电流为24A,能满足上述要求。
此外,由于KVFZ4110型变频器不带标准制动电阻,所以还需要根据实际情况进行计算,选用合适的阻值和容量。
查春日变频器设计手册,制动电阻选100%制动转矩时的标准配置62,4kW。
常规设计的自冷式异步电动机,在额定工况及规定的环境湿度范围内,是不会超过额定温升的,但在变频调速系统中,情况有所不同。
自冷式异步电动机在20Hz以下频率运行时,转子风叶的散热能力变差,如果再在恒转矩负载条件下长期运行,势必造成电机温升增加,使调速系统的特性变坏。
所以,当自冷式异步电动机在低频运行并拖动恒转矩负载时,必须采取强制冷却措施,改善电机的散热能力。
变频器的功能参数设定,变频器在出厂时,所有的功能码一般都已设定为出厂设定值。
但是,龙门铣床调速系统有些功能要求,与变频器的出厂设定不尽相同,这些功能参数需重新设定,具体如下。
(1)控制模式选择(功能码F01):
设定为矢量控制方式;
(2)电机额定电压(功能码F03):
380V;(3)电机额定电流(功能码F04):
24.6A;(4)电机额定频率(功能码F05):
50Hz;(5)电机额定转速(功能码F06):
970r/min;,(6)最高频率(功能码F08):
50Hz;由于机床的进给机构属恒转矩负载,所以电机只能在额定频率以下的恒转矩控制区使用;(7)失速电平设置(功能码F46):
150%;在矢量控制方式下,该参数设置表示变频器输出最大电流的限幅值,为了获得大的输出转矩,应将该参数设为较大值。
(8)过负荷报警水平(功能码F71):
110%;(9)过负荷报警延迟时间(功能码F70):
3s;(10)电源投入再启动(功能码F75):
OFF;(11)自动调谐(功能码F07):
在上述参数设定后,将F07设定为RUN,等待约5秒钟,变频器会自动测定电机内部参数,以完成矢量运算与控制。
如果自动测试中发生异常报警,须参阅春日变频器产品说明书。
(12)加减速时间的设定:
加减速时间可用第三章介绍的加减速时间计算公式计算求得;若计算时有实际困难,也可采用以下方法:
先将加减速时间都设定为较大值,待变频器试运行后,关掉失速电平功能,再逐步减小设定值,以使变频器不发生报警的最后的值为最佳设定值。
加减速时间设定完后,失速电平功能恢复为ON状态。
变频器的连接,技改设计中,PLC选用日本立石株式会社的模块式C200H产品,该型号PLC的CPU单元为CPU01-