对手柄套的加工工艺和夹具设计.docx
《对手柄套的加工工艺和夹具设计.docx》由会员分享,可在线阅读,更多相关《对手柄套的加工工艺和夹具设计.docx(21页珍藏版)》请在冰点文库上搜索。
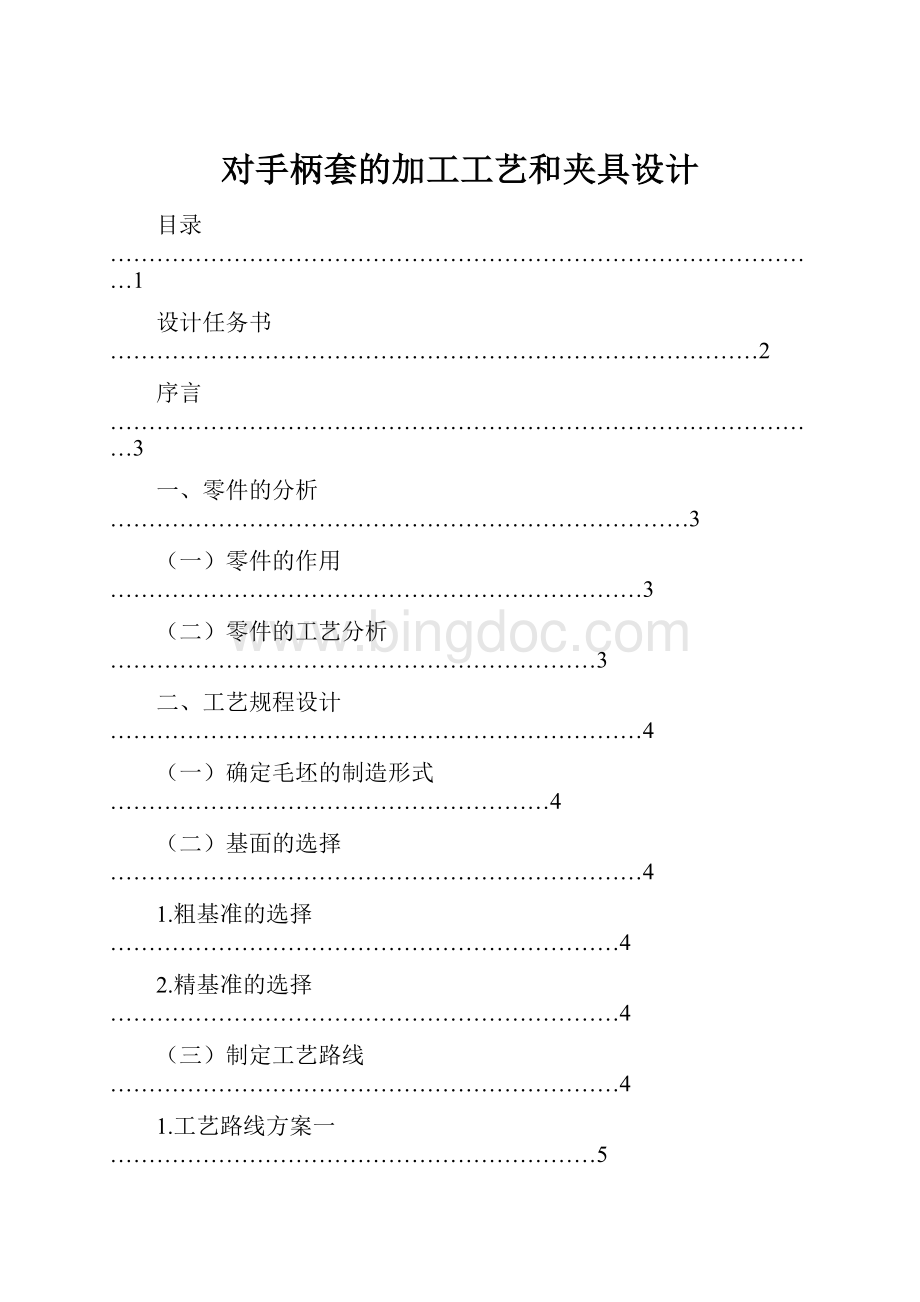
对手柄套的加工工艺和夹具设计
目录…………………………………………………………………………………1
设计任务书…………………………………………………………………………2
序言…………………………………………………………………………………3
一、零件的分析…………………………………………………………………3
(一)零件的作用……………………………………………………………3
(二)零件的工艺分析………………………………………………………3
二、工艺规程设计……………………………………………………………4
(一)确定毛坯的制造形式…………………………………………………4
(二)基面的选择……………………………………………………………4
1.粗基准的选择…………………………………………………………4
2.精基准的选择…………………………………………………………4
(三)制定工艺路线…………………………………………………………4
1.工艺路线方案一………………………………………………………5
2.工艺路线方案二………………………………………………………5
3.工艺方案的比较和分析………………………………………………6
(四)机械加工余量、工序尺寸及毛坯尺寸的确定………………………7
1.机械加工余量…………………………………………………………8
2.工序尺寸和毛坯尺寸的确定…………………………………………9
三、专用夹具的设计………………………………………………………………9
(一)设计主旨…………………………………………………………………9
(二)夹具设计…………………………………………………………………9
1.定位基准的选择………………………………………………………9
2.钻销力以及夹紧力的计算……………………………………………10
3.定位误差分析…………………………………………………………11
4.夹具设计及操作说明…………………………………………………14
四、课程设计心得体会…………………………………………………………16
参考文献……………………………………………………………………………17
序言
机械制造工艺与机床夹具课程设计是机械制造工艺与机床夹具课程设计课程教学的一个不可或缺的辅助环节。
它是我们全面运用课程及其有关选修课程的理论和实践知识进行加工工艺及夹具结构设计的一次重要实践。
我希望能通过这次设计巩固我们前面所学的知识,并深化我对它的理解,为以后更好地走向工作打下基础。
因知识和能力有限,设计过程难免会有许多不足之处,还请老师指正。
一、零件的分析
图1.1手柄套零件图
(一)零件的作用
题目给出的是机床用“手柄套”,如图1.1所示,它起着连接手柄和转轴的作用,主要是用来传递转矩,使转轴旋转,从而起到调控作用。
其中Ø12孔用来安装转轴,并通过两个Ø6H8mm孔进行轴向固定。
Ø8孔则用于安装手柄,借此来传递转矩。
Ø5H7mm孔只用于加工时的定位作用,通过它来保证3个径向孔的位置精度。
(二)零件的工艺分析
手柄套主要有两组加工表面,她们相互间有一定的位置精度。
现分述如下:
1.以Ø12H7mm孔为中心的加工表面。
它包括,Ø16mm孔,Ø12H7mm孔,左右两端面,Ø45mm外圆面以及定位用的Ø5H7mm孔,它们在加工时互为基准,彼此相互联系来保证形状位置精度。
另,工件的四个1x45°直角也可以并入该组加工表面。
2.以Ø8mm为主的加工表面
它包括,Ø8mm孔和两个Ø6H8mm孔,即径向的三个圆面加孔。
这两组表面以及表面组内之间,有一定的位置要求,主要是:
(1)Ø12mm孔轴线与Ø45mm右端面的垂直度公差为0.05mm;
(2)两个Ø6mm孔与Ø12mm孔轴线的位置度公差为0.12mm。
由上可知,对于这两组表面,可以先加工一组(第一组)表面,然后借助专用夹具以及定位孔加工另一组表面(第一组),并且通过一次装或互为基准来保证其位置精度。
1、工艺规程设计
(1)确定毛坯的制造形式
零件材料为45钢。
考虑其耐磨性其受到的局部冲击,选用锻件。
又因为零件年产量为4000件,可采用普通模煅,以提高生产效率并保证加工质量。
(2)基面的选择
基准的选择是工艺规程设计中的重要工作之一。
基面选择得正确、合理,可以保证加工质量,提高加工效率。
否则,就会使加工工艺问题百出,严重影响零件加工质量和效率。
1.粗基准的选择
因为此零件结构简单,选用Ø45mm外圆面作为粗基准即可。
但加工时注意,因为零件短小,不能以粗基准一次定位即完成初步加工,而需要两次使用粗基准,期间产生的二次定位误差可通过后序的半精、精加工来弥补。
2.精基准的选择
因为该零件各加工面有一定的形位精度要求,所以精基准的选择主要考虑基准重合和互为基准的原则。
当设计基准与工序基准不重合时,应该进行尺寸换算。
(3)制定工艺路线
零件的机械加工工艺过程是工艺规程设计的核心问题。
制定工艺路线的出发点,应当是使零件的几何形状、尺寸精度等技术要求能得到合理的保证。
在生产纲领已确定为大批生产的条件下,可以采用万能机床配以专用工夹具,并尽量使工序集中来提高生产率。
初次以外,还应考虑经济效果,以便降低生产成本。
工艺路线如下:
工序1:
普通模锻;
工序2:
正火;
工序3:
粗车右端面和部分外圆面。
以Ø45mm外圆面为基准,选用CA6140车床;
工序4:
粗车左端面和剩余的Ø45mm外圆面部分,钻Ø12mm孔。
以Ø45mm外圆面为基准,选用C365L式转塔式车床;
工序5:
半精车,精车Ø45mm外圆面。
以Ø12mm孔为基准,选用CA6140车床;
工序6:
半精车Ø45mm左端面,车Ø16mm孔,倒1x45°直角。
以Ø45mm外圆面为基准,并选CA6140车床;
工序7:
扩、铰、精铰Ø12mm孔,半精车,精车Ø45mm右端面,保证尺寸35mm,倒直角1x45°。
以Ø45mm外圆面为基准,选用C365L转塔式车床;
工序8:
钻,精铰Ø5mm孔,使用专用夹具CJ—01。
以Ø45mm左端面和Ø12mm孔定位,选用Z525钻床;
工序9:
钻Ø8mm孔,使用专用夹具CJ-02。
以Ø45右端面Ø12mm孔、Ø5mm孔定位,选用Z525钻床;
工序10:
钻成90°的Ø6mm孔,保证13尺寸和相应位置度,使用专用夹具CJ-03.以Ø45mm右端面、Ø12mm孔、Ø5mm孔定位,选用Z525钻床;
工序11:
去毛刺;
工序12:
清洗;
工序13:
终检。
以上工艺过程详见“机械加工工艺过程卡片”和“机械加工工序卡片”。
(4)机械加工余量、工序尺寸及毛坯尺寸的确定
“手柄套”零件材料为45钢,硬度为207-241HBW,毛坯重量约为0.46kg,生产类型为大批生产,采用普通模锻毛坯。
根据上述原始资料及加工工艺,结合《实用机械制造工艺设计手册》,分别确定各加工表面的机械加工余量、工序尺寸及毛坯尺寸如下:
1.机械加工余量
确定外圆表面沿轴线及径向方向的加工余量(Ø45mm及35mm),查《实用机械制造工艺设计手册》(以下简称《手册》)表2-7及2-9,其中锻件重量为0.4kg,锻件复杂数为S1,锻件轮廓尺寸≤315mm,采用一般加工精度F1,故轴向余量1.5mm∽2.0mm,取2mm,径向余量1.5mm∽2.0mm,取1.9mm。
2.工序尺寸和毛坯尺寸的确定
(1).外圆表面(Ø45mm)分步加工余量
查《手册》表7-2/7-5,结合1所得结果,拟定加工余量,如下:
粗车:
Ø46.8mm2Z=2mm
半精车:
Ø45.3mm2Z=1.5mm
精车:
Ø45.0mm2Z=0.3mm
(2).左右端面分步加工余量
由上述已确定了毛坯的长度为39mm。
查《手册》表7-2/7-4,结合1所得结果,拟定加工余量如下:
右端面
左端面
粗车:
37.8mmZ=1.2mm
粗车:
36.4mmZ=1.4mm
半精车:
35.8mmZ=0.6mm
半精车:
35.3mmZ=0.5mm
精车:
35mmZ=0.3mm
(3).内孔Ø12mm
毛坯为实心,不冲孔。
孔精度为IT7,参照《手册》表7-11,可确定工序尺寸及余量为:
钻孔:
Ø11.0mm
扩孔:
Ø11.85mm2Z=0.85mm
粗铰:
Ø11.95mm2Z=0.1mm
精铰:
Ø120+0.018mm2Z=0.05mm
(4).定位孔Ø5mm
孔具有较高的位置精度,参照《手册》表7-11,可确定工序尺寸及余量为:
钻孔:
Ø4.8mm
精铰:
Ø5.0mm2Z=0.2mm
(5).两个径向孔Ø6mm
Ø6mm孔具有较高的位置度,参照《手册》表7—11,可确定其工序尺寸及余量为:
钻孔:
Ø5.8mm
精铰:
Ø6.0mm2Z=0.2mm
由于毛坯及以后各道工序的加工都有加工公差,因此所规定的加工余量其实只是名义上的加工余量。
综合以上分析,可确定毛坯长度为39mm,直径为45.8mm,如下图4.2所示:
图4.2零件毛坯图
5确定切削用量及基本时间
切削用量一般包括切削深度、进给量及切削速度三项。
确定方法是先确定切削深度、进给量,再确定切削速度。
选择两个典型的工序,工序3粗车
外圆和工序7加工
12H7mm孔,进行钻-粗铰-精铰进行计算。
5.1工序30粗车
外圆的切削用量及基本时间
本工序为粗车
外圆面。
已知工件材料:
45钢,
,热轧制型材;机床为CA6140卧式车床;刀具:
硬质合金,YT5。
下面的相关数据根据《切削用量简明手册》确定。
CA6140机床中心高为200mm,查表1.1,选择刀杆
,刀片厚度4.5mm,由表1.3,选择车刀几何形状为平面带倒棱型,前角
,后角
,主偏角
,副偏角
,刃倾角
,刀尖圆弧半径
。
5.1.1工序30切削用量的确定
(1)确定切削深度
此工序直径加工余量为1.3mm,单边余量仅为0.65mm,可在一次走刀内切完,故
。
(2)确定进给量f根据表1.4,在粗车钢料,刀杆尺寸为
,
,工件直径为40~60mm,
,查表1.31,选择f=0.56mm/r.
(3)选择车刀磨钝标准及耐用度由表1.9,车刀后面最大磨损限度选择1.0mm,普通车刀寿命T=60min。
(4)确定切削速度v根据表1.10查得切削速度
查表1.28得切削速度修正系数为
修正后的切削速度为
按CA6140机床转速,选择n=11.8
,则实际切削速度
5.1.2检验机床功率
由表1.24,查得Pc=2.4kW。
切削功率的修正系数
-,
故实际切削时功率为
而机床主轴允许功率为
,
,故选用的切削用量可在CA6140机床上进行。
最后确定切削用量为:
。
5.1.3基本时间的确定
根据《机械制造工艺设计简明手册》表6.2-1,车外圆的基本时间为
,式中
取
,
查表6.2—2取
,
则基本时间
5.2工序70加工
12H7mm孔的切削用量及基本时间
本工序为加工孔加工,要求:
加工
12H7mm孔,进行钻-粗铰-精铰。
先钻孔
再粗铰、精铰孔,尺寸保证到
。
机床:
Z525立式钻床,刀具:
高速钢的标准钻头和标准铰刀。
查表2.12,直柄麻花钻直径
,刀具寿命T=45min;标准铰刀,刀具寿命T=40min。
5.2.1钻孔
5.2.1.1确定进给量f根据表2.7,查得f=0.25~0.31mm/r,由Z525钻床参数确定f=0.28mm/r。
5.2.1.2确定切削速度v根据表2.14,表2.13查得
,由表2.31得切削速度修正系数
,故
按机床转速参数,选择n=392r/min,则实际切削速度
5.2.1.3检验扭矩功率根据表2.32,表2.33,钻孔时扭矩及功率
,式中
,则
。
而转速为n=392r/mim的Z525型立式钻床能传递的扭矩为
。
。
经计算
,检验成立。
5.2.2铰孔
5.2.2.1确定进给量f根据表2.11查得f=0.65~1.4mm/r,按Z525钻床选择
三、专用夹具的设计
专用夹具能大大提高劳动生产率,保证加工质量,降低劳动强度,在批量和大量生产重意义重大。
经过设计任务要求,我需要设计的是第9道工序,即Ø8mm孔加工用夹具。
本夹具将用于Z525立式钻床。
刀具为一个高速钢麻花钻。
(一)设计主旨
本夹具主要用来钻Ø8mm通孔,技术要求不高,没有形位精度限制,且孔径不大,可一次钻销完成。
因此,本道工工序加工时,主要应考虑如何提高劳动生产率,降低劳动强度,而精度则不是主要问题。
(二)夹具设计
1.定位基准的选择
由零件图可知,零件对于Ø8mm孔的加工并没有位置及公差要求。
但考虑到零件右端面与Ø12H7mm中心孔的垂直度,右端面的精度较高以及右端面采用一面两销定位方式的方便性,此处的定位基准选择Ø12H7mm中心孔的右端面。
2.钻销力以及夹紧力的计算
(1)钻销力的计算:
材料为高速钢,则据《机械制造工艺与机床夹具课程设计指导》表3—4,查得钻销时轴向力、转矩计算公式为:
Ff=CFfdZFffYFfKFf
Mc=CMfdZMcfYMcKMc
式中,CFf=600,d=8mm,ZFf=1.0,f=195r/min,YFf=0.7,KFf=1,
CMf=0.305,ZMc=2.0,f=195r/min,YMc=0.8,KMc=1
代入数据,得:
Ff=600X0.008X(195/60)0.7X1=11N
Mc=0.305X0.0082.0X(195/60)0.8X1=5X10-6N·m
由于转矩的值太小,对工件的定位加工影响不大,故可以忽略不计。
(1)夹紧力的计算:
左端面及右端面与夹具上的开口垫圈及夹具体的摩擦系数分别为0.3及0.1,所以理论上,夹紧力:
F=Ff/u=11/(0.3+0.1)=27.5N
在计算钻销力时必须考虑安全系数,安全系数K=K1K2K3K4。
式中:
K1—基本安全系数,K1=1.5;
K2—加工性质系数,K2=1.1;
K3—刀具钝化系数,K3=1.1;
K4—断续切销系数,K4=1.1;
于是:
F′=KXFf=1.5X1.1X1.1X1.1X27.5=55N。
此时,F′已大于所需的27.5N夹紧力,故本夹具可以安全地工作。
3.定位误差分析
(1)定位元件及公差的确定
<1>本夹具采用一面两销定位,由于用于定位的两孔直径分别为5mm及12mm,故主要定位元件为一圆柱销和一菱形销。
1)确定两销的中心距两销中心距的偏差一般取两孔中心距偏差的1/5—1/3,当孔距公差大时,取小值;反之,取大值,以便于制造。
因此处孔距公差为0.08mm,故取0.026mm。
2)确定第一个定销直径尺寸d1取d1min=D1max,定位销的直径公差一般按g6、h7配合选取,最后取d1=12.008h7mm。
3)确定菱形销宽度b和B菱形销的结构尺寸已经标准化,查《机械制造工艺学》表5—1选取:
b=2mm,B=4.5mm。
4)计算菱形销直径尺寸先按下式计算出菱形销与孔配合的最小间隙,再计算菱形销直径尺寸d2,并按g6或f7选取偏差,然后圆整处理:
Δ2min≈2b(δLD+δLd)/D2
d2=D2-Δ2min
式中Δ2min—菱形销与孔配合的最小间隙,单位为mm;
b—菱形销的宽度,单位为mm;
δLD、δLd—为工件上两孔中心距公差和夹具上两销中心距公差,单位为mm;
D2—工件上菱形销定位孔直径,单位为mm;
D2—菱形销直径尺寸,单位为mm。
分别代入数据,得:
Δ2min≈2X2(0.08+0.026)/5=0.0848mm
d2=5-0.0848=4.9152mm
<2>定位销的设计
查《机床夹具设计手册手册》图2-1-3及表2-1-3,得定位销的结构及数据如下图3.3.1.2所示:
图3.3.1.2定位销的结构及数据
<3>钻套的设计
查《机床夹具设计手册手册》图2-1-146及表2-1-146,得钻套的结构及数据如下图3.3.1.3所示:
图3.3.1.3钻套的结构
其中,d=8F7mm,D=12m6mm,D1=22mm,D2=18mm,H=20mm,h=10m,h1=6mm,h2=12mm,h3=14mm,r=16mm,r1=1mm,m=7mm,m1=7mm,a=0.5mm,b=2mm,α=50°,δ=0.008mm,配钻套螺钉M6。
<4>钻套衬套的计设计
查《机床夹具设计手册手册》图2-1-174及表2-1-174,得钻套衬套的结构及数据如下图3.3.1.4所示:
图3.3.1.4钻套衬套的结构
其中:
d=18F7mm,D=26n6mm,D1=30mm,H=16mm,h=4mm,C=1mm,C1=2mm,
C2=1.5mm,a=0.5mm,b=2mm,δ=0.008mm。
<5>手柄的设计
查《机床夹具设计手册手册》图2-1-224及表2-1-222,得手柄的结构及数据如下图3.3.1.5所示:
图3.3.1.5手柄的结构及数据
(2)零件的位置误差
零件图上并没有对孔的公差及配合等进行规定,故孔的定位精度并不高。
即在实际工作过程中,夹具体对工件的一般误差,并不影响钻床对工件的加工。
1>由于Ø8mm孔的轴向定位是以右端面为基准的,而此处夹具的设计同样是以右端面为基准,即符合基准重合原则,误差为0。
2>从零件图上可知,Ø12mm孔与右端面的垂直度最大偏差为0.05mm。
所以,Ø8mm孔与右端面的垂直度最大偏差也为0.05mm。
3>圆柱位销的定位误差:
由于是孔的误差引起,故此误差为0.08mm。
4>磨损造成的误差一般不超过0.005mm。
5>钻模对刀误差:
因加工孔的孔径D’等于钻头孔径d,由于钻套孔径D的约束,一般情况下,D’大于D,即加工孔中心实际上与转套中心重合,因此,钻模对刀误差趋于0。
6>夹具相对于刀具的误差取0.01mm。
4.夹具设计及操作说明
本夹具用于在钻床上加工孔,采用了一面两销定位,六个自由度完全限制。
外加左端面的夹紧,夹具对工件在加工过程中的固定完全能达到要求。
因本工件的加工量为大批量生产,故夹具要尽量简单,且方便拆卸。
所以夹具又采用了手动螺旋压板机构对工件左端面的夹紧方式。
该夹紧机构操作简单、夹紧可靠。
四、课程设计心得体会
经过两个星期的艰苦奋斗,夹具设计结束了。
在我完成的那一刹那,心里是百感交集,心旷神怡,豁然开朗。
在两周的设计中,我遇到了很多的困难,我没有气馁,没有放弃,没有妥协。
而是通过一次又一次的计算,一次又一次的修改,反复的推敲,分析。
不懂的就看书,看不懂的就去问。
最终是,山重水复疑无路,柳暗花明又一村。
此次设计是对手柄套的加工工艺和夹具设计,其零件为模锻,具有体积小,零件简单的特点,由于面比孔易加工,在制定工艺规程时,就先加工面,再以面为基准来加工其它,其中各工序夹具都采用专用夹具,特别的对于加工Ø8mm孔工序中,选一面两销的定位方式,并以操作简单的手动夹紧方式夹紧,其机构设计简单,方便且能满足要求。
回顾这两周的设计,总体上说我还是学到了很多的东西。
通过这次课程设计,使我对零件制造过程、加工工艺和夹具设计都有了更进一步的认识,也加深了对大学3年中所学基础知识的学习和理解。
课程设计是理论联系实际的最有效方法。
在具体设计过程中,必须考虑到方方面面的问题,在理论上正确无误的设计,在实际中往往存在各种问题。
这样,在设计时就必须考虑所设计的机构是否合理,在实际运用中能否正常工作,而不仅仅考虑理论上的可行性,课程设计使我学会了从实际出发加工零件和设计夹具。
这次课程设计还使我懂得了理论与实际相结合是很重要的,只有理论知识是远远不够的,只有把所学的理论知识与实践相结合起来,从理论中得出结论,才能真正为社会服务,从而提高自己的实际动手能力和独立思考的能力。
生活就是这样,汗水预示着结果也见证着收获。
劳动是人类生存生活永恒不变的话题。
我想说,设计确实有些辛苦,但苦中也有乐,,一起工作可以让我们有说有笑,相互帮助,配合默契,多少人间欢乐在这里洒下,让我感觉我和同学们之间的距离更加近了;我想说,设计确实很累,但当我们研究出数据制成成果时,心中也不免产生兴奋;这次设计是我成功迈向成功的第一步
。
虽然这次设计中会有错误,做的也没有别人的好,但是这毕竟是我的第一次独立完成的设计。
我为之付出了汗水,百分百的心意。
不管结果的成绩会怎样,我已经努力过。
只有经过地狱的磨练才能创造天堂的美。
没有流过血的手指,弹奏不出世间的绝唱。
五、参考文献
[1]杨叔子主编.机械加工工艺师手册[M].北京:
机械工业出版社,2002
[2]吴拓,方琼珊主编.机械制造工艺与机床夹具课程设计指导书.北京:
机械工业出版社,2005
[3]孙本绪,熊万武主编.机械加工余量手册.北京:
国防工业出版社,1999
[4]李云主编.机械制造工艺及设备指导手册.北京:
机械工业出版社,1998
[5]王光斗,王春福主编.机床夹具设计手册[M].上海:
上海科学技术出版社,2000
[6]熊良山主编.机械制造技术基础.华中科技大学出版社,2000
[7]刘守勇主编.机械制造工艺与机床夹具.北京:
机械工业出版社,1999(5)
资料仅供参考!
!
!