滚动轴承故障诊断解析.docx
《滚动轴承故障诊断解析.docx》由会员分享,可在线阅读,更多相关《滚动轴承故障诊断解析.docx(24页珍藏版)》请在冰点文库上搜索。
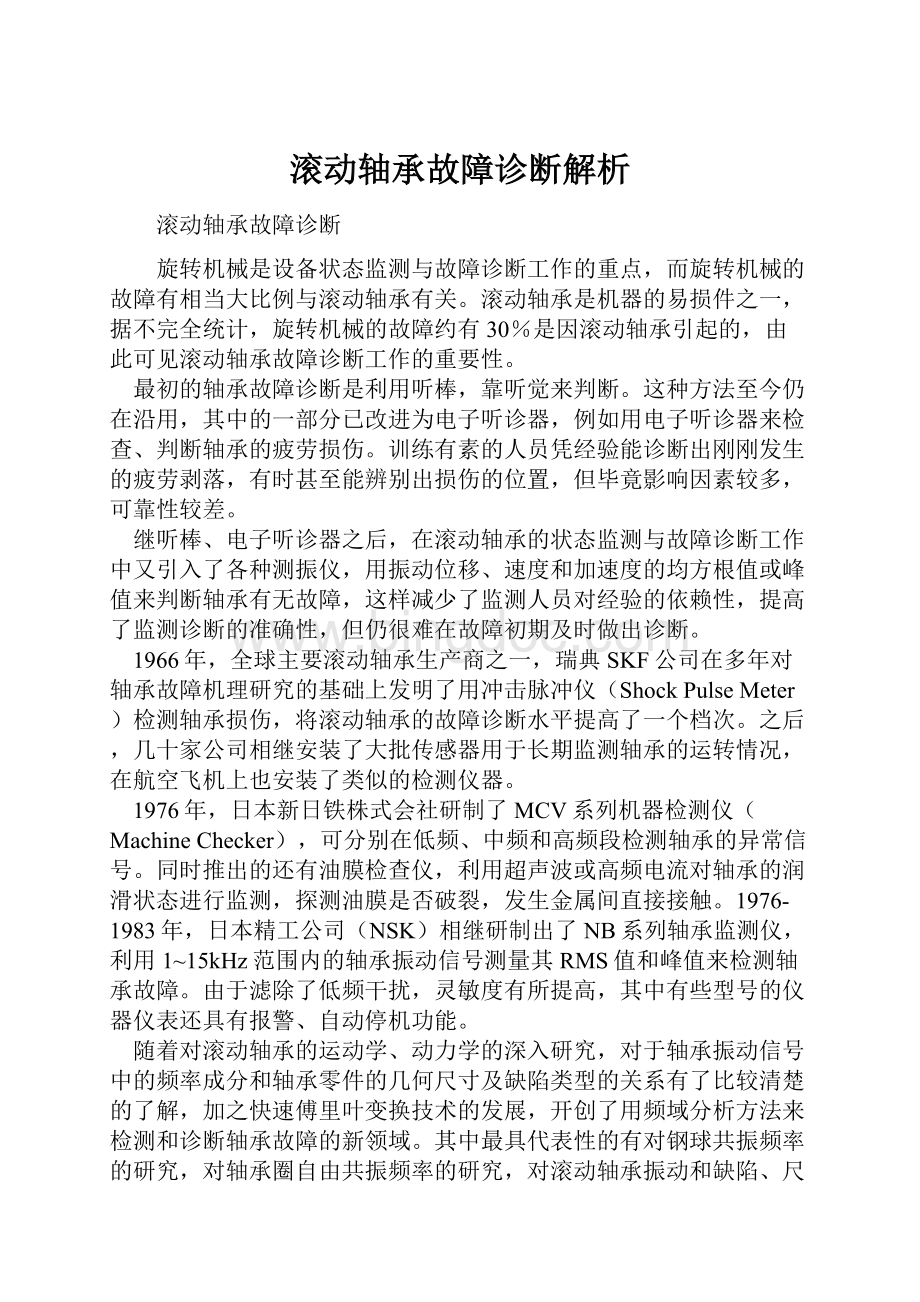
滚动轴承故障诊断解析
滚动轴承故障诊断
旋转机械是设备状态监测与故障诊断工作的重点,而旋转机械的故障有相当大比例与滚动轴承有关。
滚动轴承是机器的易损件之一,据不完全统计,旋转机械的故障约有30%是因滚动轴承引起的,由此可见滚动轴承故障诊断工作的重要性。
最初的轴承故障诊断是利用听棒,靠听觉来判断。
这种方法至今仍在沿用,其中的一部分已改进为电子听诊器,例如用电子听诊器来检查、判断轴承的疲劳损伤。
训练有素的人员凭经验能诊断出刚刚发生的疲劳剥落,有时甚至能辨别出损伤的位置,但毕竟影响因素较多,可靠性较差。
继听棒、电子听诊器之后,在滚动轴承的状态监测与故障诊断工作中又引入了各种测振仪,用振动位移、速度和加速度的均方根值或峰值来判断轴承有无故障,这样减少了监测人员对经验的依赖性,提高了监测诊断的准确性,但仍很难在故障初期及时做出诊断。
1966年,全球主要滚动轴承生产商之一,瑞典SKF公司在多年对轴承故障机理研究的基础上发明了用冲击脉冲仪(ShockPulseMeter)检测轴承损伤,将滚动轴承的故障诊断水平提高了一个档次。
之后,几十家公司相继安装了大批传感器用于长期监测轴承的运转情况,在航空飞机上也安装了类似的检测仪器。
1976年,日本新日铁株式会社研制了MCV系列机器检测仪(MachineChecker),可分别在低频、中频和高频段检测轴承的异常信号。
同时推出的还有油膜检查仪,利用超声波或高频电流对轴承的润滑状态进行监测,探测油膜是否破裂,发生金属间直接接触。
1976-1983年,日本精工公司(NSK)相继研制出了NB系列轴承监测仪,利用1~15kHz范围内的轴承振动信号测量其RMS值和峰值来检测轴承故障。
由于滤除了低频干扰,灵敏度有所提高,其中有些型号的仪器仪表还具有报警、自动停机功能。
随着对滚动轴承的运动学、动力学的深入研究,对于轴承振动信号中的频率成分和轴承零件的几何尺寸及缺陷类型的关系有了比较清楚的了解,加之快速傅里叶变换技术的发展,开创了用频域分析方法来检测和诊断轴承故障的新领域。
其中最具代表性的有对钢球共振频率的研究,对轴承圈自由共振频率的研究,对滚动轴承振动和缺陷、尺寸不均匀及磨损之间关系的研究。
1969年,H.L.Balderston根据滚动轴承的运动分析得出了滚动轴承的滚动体在内外滚道上的通过频率和滚动体及保持架的旋转频率的计算公式,以上研究奠定了这方面的理论基础。
目前已有多种信号分析仪可供滚动轴承的故障诊断,美国恩泰克公司根据滚动轴承振动时域波形的冲击情况推出的“波尖能量”法及相应仪器,对滚动轴承的故障诊断非常有效。
还有多种信号分析处理技术用于滚动轴承的状态监测与故障诊断,如频率细化技术、倒频谱、包络线分析等。
在信号预处理上也采用了各种滤波技术,如相干滤波、自适应滤波等,提高了诊断灵敏度。
除了利用振动信号对轴承运行状态进行诊断监测外,还发展了其他一些技术,如光纤维监测技术、油污染分析法(光谱测定法、磁性磁屑探测法和铁谱分析法等)、声发射法、电阻法等
简易诊断法确定轴承已经发生故障之后,进一步判定故障的类别和发生部位,以便采取相应对策。
滚动轴承的精密诊断与旋转机械、往复机械等精密诊断一样,主要采用频谱分析法。
由于滚动轴承的振动频率成分十分丰富,既含有低频成分,又含有高频成分,而且每一种特定的故障都对应特定的频率成分。
进行频谱分析之前需要通过适当的信号处理方法将特定的频率成分分离出来,然后对其进行绝对值处理,最后进行频率分析,以找出信号的特征频率,确定故障的部位和类别。
一、轴承内滚道损伤
轴承内滚道产生损伤时,如:
剥落、裂纹、点蚀等(如图1所示),若滚动轴无径向间隙时,会产生频率为nZfi(n=1,2,…)的冲击振动。
图1 内滚道损伤振动特征
通常滚动轴承都有径向间隙,且为单边载荷,根据点蚀部分与滚动体发生冲击接触的位置的不同,振动的振幅大小会发生周期性的变化,即发生振幅调制。
若以轴旋转频率f,进行振幅调制,这时的振动频率为nZfi士fr(n=1,2…);若以滚动体的公转频率(即保持架旋转频率)fc进行振幅调制,这时的振动频率为nZfi±fc(n=1,2,…)。
二、轴承外滚道损伤
当轴承外滚道产生损伤时,如剥落、裂纹、点蚀等(如图2所示),在滚动体通过时也会产生冲击振动。
由于点蚀的位置与载荷方向的相对位置关系是一定的,所以,这时不存在振幅调制的情况,振动频率为nZfo(n=1,2,…),振动波形如图2所示。
图2 外滚道损伤振动特征
三、滚动体损伤
当轴承滚动体产生损伤时,如剥落、裂纹、点蚀等,缺陷部位通过内圈或外圈滚道表面时会产生冲击振动。
在滚动轴承无径向间隙时,会产生频率为nZfb(n=1,2,…)的冲击振动。
通常滚动轴承都有径向间隙,因此,同内圈存在点蚀时的情况一样,根据点蚀部位与内圈或外圈发生冲击接触的位置不同,也会发生振幅调制的情况,不过此时是以滚动体的公转频率fc进行振幅调制。
这时的振动频率为nzfb士fc,如图3所示。
图3 滚动体损伤振动情况
四、轴承偏心
当滚动轴承的内圈出现严重磨损等情况时,轴承会出现偏心现象,当轴旋转时,轴心(内圈中心)便会绕外圈中心摆动,如图4示,此时的振动频率为nfr(n=1,2,…)。
图4 滚动轴承偏心振动特征
五、轴承部件损伤特征频率表
为方便轴承故障诊断,将以上与轴承部件损伤有关的特征频率列于表1中。
表1 轴承部件损伤特征频率表
续表
由于滚动轴承的故障信号具有冲击振动的特点,频率极高,衰减较快,因此利用振动信号对其进行监测诊断时,除了参考前面已经介绍的旋转机械、往复机械的振动测试方法以外,还应根据其振动特点,有针对性地采取一些措施和方法。
一、测点的选择
滚动轴承因故障引起的冲击振动由冲击点以半球面波方式向外传播,通过轴承零件、轴承座传到箱体或机架。
由于冲击振动所含的频率很高,每通过零件的界面传递一次,其能量损失约80%。
因此,测量点应尽量靠近被测轴承的承载区,应尽量减少中间传递环节,探测点离轴承外圈的距离越近越直接越好。
图1表示了传感器位置对故障检测灵敏度的影响。
在图1(a)中,假如传感器放在承载方向时为100%,则在承载方向士45°方向上降为95%(-5dB),在轴向则降为22%-25%(-12~13dB)。
在图1(b)中,当止推轴承发生故障产生冲击并向外散发球面波时,假如在轴承盖正对故障处的读数为100%,则在轴承座轴向的读数降为5%(-19dB)。
在图1(c)和(d)中给出了传感器安装的正确位置和错误位置,较粗的弧线表示振动较强烈的部位,较细的弧线表示因振动波通过界面衰减导致振动减弱的情形。
图1 传感器位置对故障检测灵敏度的影响
由于滚动轴承的振动在不同方向上反映出不同的特性,因此应尽量考虑在水平(x)、垂直(y)和轴向(z)三个方向上进行振动检测,但由于设备构造、安装条件的限制,或出于经济方面的考虑,不可能在每个方向上都进行检测,这时可选择其中的两个方向进行检测。
二、传感器的选择与固定方式
根据滚动轴承的结构特点,使用条件不同,它所引起的振动可能是频率约为1kHz以下的低频脉动(通过振动),也可能是频率在1kHz以上,数千赫乃至数十千赫的高频振动(固有振动),通常情况下是同时包含了上述两种振动成分。
因此,检测滚动轴承振动速度和加速度信号时应同时覆盖或分别覆盖上述两个频带,必要时可以采用滤波器取出需要的频率成分。
考虑到滚动轴承多用于中小型机械,其结构通常比较轻薄,因此,传感器的尺寸和重量都应尽可能地小,以免对被测对象造成影响,改变其振动频率和振幅大小。
滚动轴承的振动属于高频振动,对于高频振动的测量,传感器的固定采用手持式方法显然不合适,一般也不推荐磁性座固定,建议采用钢制螺栓固定,这样不仅谐振频率高,可以满足要求,而且定点性也好,对于衰减较大的高频振动,可以避免每次测量的偏差,使数据具有可比性。
三、分析谱带的选择
滚动轴承的故障特征在不同频带上都有反映,因此,可以利用不同的频带,采用不同的方法对轴承的故障做出诊断。
1.低频段
在滚动轴承的故障诊断中,低频率段指1kHz以下的频率范围。
一般可以采用低通滤波器(例如截止频率fb≤1kHz)滤去高频成分后再作频谱分析。
由于轴承的故障特征频率(通过频率)通常都在1kHz以下,此法可直接观察频谱图上相应的特征谱线,做出判断。
由于在这个频率范围容易受到机械及电源干扰,并且在故障初期反映故障的频率成分在低频段的能量很小,因此,信噪比低,故障检测灵敏度差,目前已较少采用。
2.中频段
在滚动轴承的故障诊断中,中频段指1~20kHz频率范围。
同样,利用该频率时也可以使用滤波器。
(1)高通滤波器
使用截止频率为1kHz的高通滤波器滤去1kHz以下的低频成分,以消除机械干扰;然后用信号的峰值、RMS值或峭度系数作为监测参数。
许多简易的轴承监测仪器仪表都采用这种方式。
(2)带通滤波器
使用带通滤波器提取轴承零件或结构零件的共振频率成分,用通带内的信号总功率作为监测参数,滤波器的通带截止频率根据轴承类型及尺寸选择,例如对309球轴承,通带中心频率为2.2kHz左右,带宽可选为1~2kHz。
3.高频段
在滚动轴承的故障诊断中,高频率段指20~80kHz频率范围。
由于轴承故障引起的冲击有很大部分冲击能量分布在高频段,如果采用合适的加速度传感器和固定方式保证传感器较高的谐振频率,利用传感器的谐振或电路的谐振增强所得到衰减振动信号,对故障诊断非常有效。
瑞典的冲击脉冲计(SPM)和美国首创的IFD法就是利用这个频段。
四、滚动轴承的简易诊断
利用滚动轴承的振动信号分析故障诊断的方法可分为简易诊断法和精密诊断法两种。
简易诊断的目的是为了初步判断被列为诊断对象的滚动轴承是否出现了故障;精密诊断的目的是要判断在简易诊断中被认为出现了故障的轴承的故障类别及原因。
1.滚动轴承故障的简易标准
在利用振动对滚动轴承进行简易诊断的过程中,通常需要将测得的振值(峰值、有效值等)与预先给定的某种判定标准进行比较,根据实测的振值是否超出了标准给出的界限来判断轴承是否出现了故障,以决定是否需要进一步进行精密诊断。
因此,判定标准就显得十分重要。
用于滚动轴承简易诊断的判定标准大致可分为以下三种。
(1)绝对判定标准
绝对判定标准是指用于判断实测振值是否超限的绝对量值。
(2)相对判定标准
相对判定标准是指对轴承的同一部位定期进行振动检测,并按时间先后进行比较,以轴承无故障情况下的振值为基准,根据实测振值与该基准振值之比来进行判断的标准。
(3)类比判定标准
类比判定标准是指对若干同一型号的轴承在相同的条件下在同一部位进行振动检测,并,将振值相互比较进行判断的标准。
需要注意的是,绝对判定标准是在标准和规范规定的检测方法的基础上制定的标准,因此必须注意其适用频率范围,并且必须按规定的方法进行振动检测。
适用于所有轴承的绝对判定标准是不存在的,因此一般都是兼用绝对判定标准、相对判定标准和类比判定标准,这样才能获得准确、可靠的诊断结果。
2.振动信号简易诊断法
(1)振幅值诊断法
这里所说的振幅值指峰值XP、均值X(对于简谐振动为半个周期内的平均值,对于轴承冲击振动为经绝对值处理后的平均值)以及均方根值(有效值)Xrms。
这是一种最简单、最常用的诊断法,它是通过将实测的振幅值与判定标准中给定的值进行比较来诊断的。
峰值反映的是某时刻振幅的最大值,因而它适用于像表面点蚀损伤之类的具有瞬时冲击的故障诊断。
另外,对于转速较低的情况(如300r/min以下),也常采用峰值进行诊断。
均值用于诊断的效果与峰值基本一样,其优点是检测值较峰值稳定,但一般用于转速较高的情况(如300r/min以上)。
均方根值是对时间平均的,因而它适用于像磨损之类的振幅值随时间缓慢变化的故障诊断。
日本NSK公司生产NB系列轴承监测仪和新日铁研制的MCV-21A型机械监测仪就是这类仪器。
可以测量振动信号的峰值或峰值系数,有的还可以测量RMS值或绝对平均值。
测量参数除加速度外,有的还包括振动速度和位移。
(2)波形因数诊断法
波形因数定义为峰值与均值之比(XP/X)。
该值也是用于滚动轴承简易诊断的有效指标之一。
如图2所示,当XP/X值过大时,表明滚动轴承可能有点蚀;而XP/X小时,则有可能发生了磨损。
图2 滚动轴承冲击振动的波形因数
(3)波峰因数诊断法
波峰因数定义为峰值与均方根值之比(XP/Xrms)。
该值用于滚动轴承简易诊断的优点在于它不受轴承尺寸、转速及载荷的影响,也不受传感器、放大器等一、二次仪表灵敏度变化的影响。
该值适用于点蚀类故障的诊断。
通过对XP/Xrms值随时间变化趋势的监测,可以有效地对滚动轴承故障进行早期预报,并能反映故障的发展变化趋势。
当滚动轴承无故障时,XP/Xrms,为一较小的稳定值;一旦轴承出现了损伤,则会产生冲击信号,振动峰值明显增大,但此时均方根值尚无明显的增大,故XP/Xrms增大;当故障不断扩展,峰值逐步达到极限值后,均方根值则开始增大,XP/Xrms逐步减小,直至恢复到无故障时的大小。
(4)概率密度诊断法
无故障滚动轴承振幅的概率密度曲线是典型的正态分布曲线;而一旦出现故障,则概率密度曲线可能出现偏斜或分散的现象,如图3所示。
(5)峭度系数诊断法
峭度(Kurtosis)β定义为归一化的4阶中心矩,即
式中x—瞬时振幅;
X—振幅均值;
p(x)—概率密度;
σ—标准差。
振幅满足正态分布规律的无故障轴承,其峭度值约为3。
随着故障的出现和发展,峭度值具有与波峰因数类似的变化趋势。
此方法的优点在于与轴承的转速、尺寸和载荷无关,主要适用于点蚀类故障的诊断。
图3 滚动轴承的损伤
英国钢铁公司研制的峭度仪在滚动轴承故障的监测诊断方面取得了很好的效果。
利用快装接头,仪器的加速度传感器探头直接接触轴承外圈,可以测量峭度系数、加速度峰值和RMS值。
图4为使用该仪器监测同一轴承疲劳试验的结果。
试验中第74h轴承发生了疲劳破坏,峭度系数由3上升到6[图(a)],而此时峰值[图(b)]和RMS值尚无明显增大。
故障进一步明显恶化后,峰值、RMS值才有所反映。
图中虚线表示在不同转速(800~2700r/min)和不同载荷(0~11kN)下进行试验时上述各值的变动范围。
很明显,峭度系数的变化范围最小,约为士8%。
轴承的工作条件对它的影响最小,即可靠性及一致性较高。
有统计资料表明,使用峭度系数和RMS值共同来监测,滚动轴承振动情况,故障诊断成功率可达到96%以上。
图4 轴承疲劳试验过程
滚动轴承的振动可由外部振源引起,也可由轴承本身的结构特点及缺陷引起。
此外,润滑剂在轴承运转时产生的流体动力也可以是振动(噪声)源。
上述振源施加于轴承零件及附近的结构件上时都会激励起振动。
一、滚动轴承振动的基本参数
1.滚动轴承的典型结构
滚动轴承的典型结构如图1所示,它由内圈、外圈、滚动体和保持架四部分组成。
图1 滚动轴承的典型结构
图示滚动轴承的几何参数主要有:
轴承节径D:
轴承滚动体中心所在的圆的直径
滚动体直径d:
滚动体的平均直径
内圈滚道半径r1:
内圈滚道的平均半径
外圈滚道半径r2:
外圈滚道的平均半径
接触角α:
滚动体受力方向与内外滚道垂直线的夹角
滚动体个数Z:
滚珠或滚珠的数目
2.滚动轴承的特征频率
为分析轴承各部运动参数,先做如下假设:
(1)滚道与滚动体之间无相对滑动;
(2)承受径向、轴向载荷时各部分无变形;
(3)内圈滚道回转频率为fi;
(4)外圈滚道回转频率为fO;
(5)保持架回转频率(即滚动体公转频率为fc)。
参见图1,则滚动轴承工作时各点的转动速度如下:
内滑道上一点的速度为:
Vi=2πr1fi=πfi(D-dcosa)
外滑道上一点的速度为:
VO=2πr2fO=πfO(D+dcosa)
保持架上一点的速度为:
Vc=1/2(Vi+VO)=πfcD
由此可得保持架的旋转频率(即滚动体的公转频率)为:
从固定在保持架上的动坐标系来看,滚动体与内圈作无滑动滚动,它的回转频率之比与d/2r1成反比。
由此可得滚动体相对于保持架的回转频率(即滚动体的自转频率,滚动体通过内滚道或外滚道的频率)fbc
根据滚动轴承的实际工作情况,定义滚动轴承内、外圈的相对转动频率为
一般情况下,滚动轴承外圈固定,内圈旋转,即:
同时考虑到滚动轴承有Z个滚动体,则滚动轴承的特征频率如下:
滚动体在外圈滚道上的通过频率zfoc为:
滚动体在内圈滚道上的通过频率Zfic为:
滚动体在保持架上的通过频率(即滚动体自转频率fbc)为:
3.止推轴承的特征频率
止推轴承可以看作上述滚动轴承的一个特例,即α=90°,同时内、外环相对转动频率为轴的转动频率fr,此时滚动体在止推环滚道上的频率为:
滚动体相对于保持架的回转频率为:
以上各特征频率是利用振动信号诊断滚动轴承故障的基础,对故障诊断非常重要。
4.滚动轴承的固有振动频率
滚动轴承在运行过程中,由于滚动体与内圈或外圈冲击而产生振动,这时的振动频率为轴承各部分的固有频率。
固有振动中,内、外圈的振动表现最明显,如图2所示
图2 滚动轴承套圈横截面简化图与径向弯曲振动振型示意图
轴承圈在自由状态下的径向弯曲振动的固有频率为:
式中n—振动阶数(变形波数),n=2,3,…;
E—弹性模量,钢材为210GPa;
I—套圈横截面的惯性矩,mm4;
γ—密度,钢材为7.86X10-6kg/mm3;
A—套圈横截面积,A≈bh,mm2;
D—套圈横截面中性轴直径,mm;
g—重力加速度,g=9800mm/S2。
对钢材,将各常数代入式得
有时钢球也会产生振动,钢球振动的固有频率为:
式中R—钢球半径;
E—弹性模量,钢材为210GPa;
γ—密度,钢材为7.86X10-6kg/mm3;
g—重力加速度,g=9800mm/S2。
5.滚动轴承特征频率表
为方便使用,将以上介绍的滚动轴承各特征频率列于表1中。
表1 滚动轴承特征频率表(假定外圈固定、内圈旋转)
二、正常轴承的振动信号特征
正常的轴承也有相当复杂的振动和噪声,有些是由轴承本身结构特点引起的;有些和制造装配有关,如滚动体和滚道的表面波纹、表面粗糙度以及几何精度不够高,在运转中都会引起振动和噪声。
1.轴承结构特点引起的振动
滚动轴承在承载时,由于在不同位置承载的滚子数目不同,因而承载刚度会有所变化,引起轴心的起伏波动,振动频率为Zfoc(图3)。
要减少这种振动的振幅可以采用游隙小的轴承或加预紧力去除游隙。
2.轴承钢度非线性引起的振动
滚动轴承的轴向刚度常呈非线性(图4),特别是当润滑不良时,易产生异常的轴向振动。
在刚度曲线呈对称非线性时,振动频率为fn,2fn.,3f.n,…;在刚度曲线呈非对称非线性时,振动频率为
…分数谐频(fn为轴回转频率)。
这是一种自激振动,常发生在深沟球轴承,自调心球轴承和滚柱轴承不常发生。
图3 滚动轴承的承载刚度和滚子位置的关系
图4 轴承的轴向刚度
3.轴承制造装配的原因
(1)加工面波纹度引起的振动
由轴承零件的加工面(内圈、外圈滚道面及滚动体面)的波纹度引起的振动和噪声在轴承中比较常见,这些缺陷引起的振动为高频振动(比滚动体在滚道上的通过频率高很多倍)。
高频振动及轴心的振摆不仅会引起轴承的径向振动,在一定条件下还会引起轴向振动。
表2列出的振动频率与波纹度峰数的关系。
表中,n为正整数,Z为球(滚动体)数,fic为单个滚动体在内圈滚道上的通过频率,fc为保持架转速,fbc为滚动体相对于保持架的转动频率。
表2 振动频率与波纹度峰数的关系
下面简单介绍一下这种振动的机理。
在图5中,轴承内圈加工过程中残留有波纹,球个数Z=8,内圈旋转,当内圈波纹峰数分别为nZ-1,nZ,nZ+1时,对外圈径向振动影响情况如下:
图5 内圈波纹率引起外圈径向振动的机理(n=1,Z=8)
在图中讨论编号为“1”的球与波峰接触时的情况。
当波峰为nZ时,外圈在径向无移动,