冷风切削技术在磨削中的应用Word格式文档下载.docx
《冷风切削技术在磨削中的应用Word格式文档下载.docx》由会员分享,可在线阅读,更多相关《冷风切削技术在磨削中的应用Word格式文档下载.docx(14页珍藏版)》请在冰点文库上搜索。
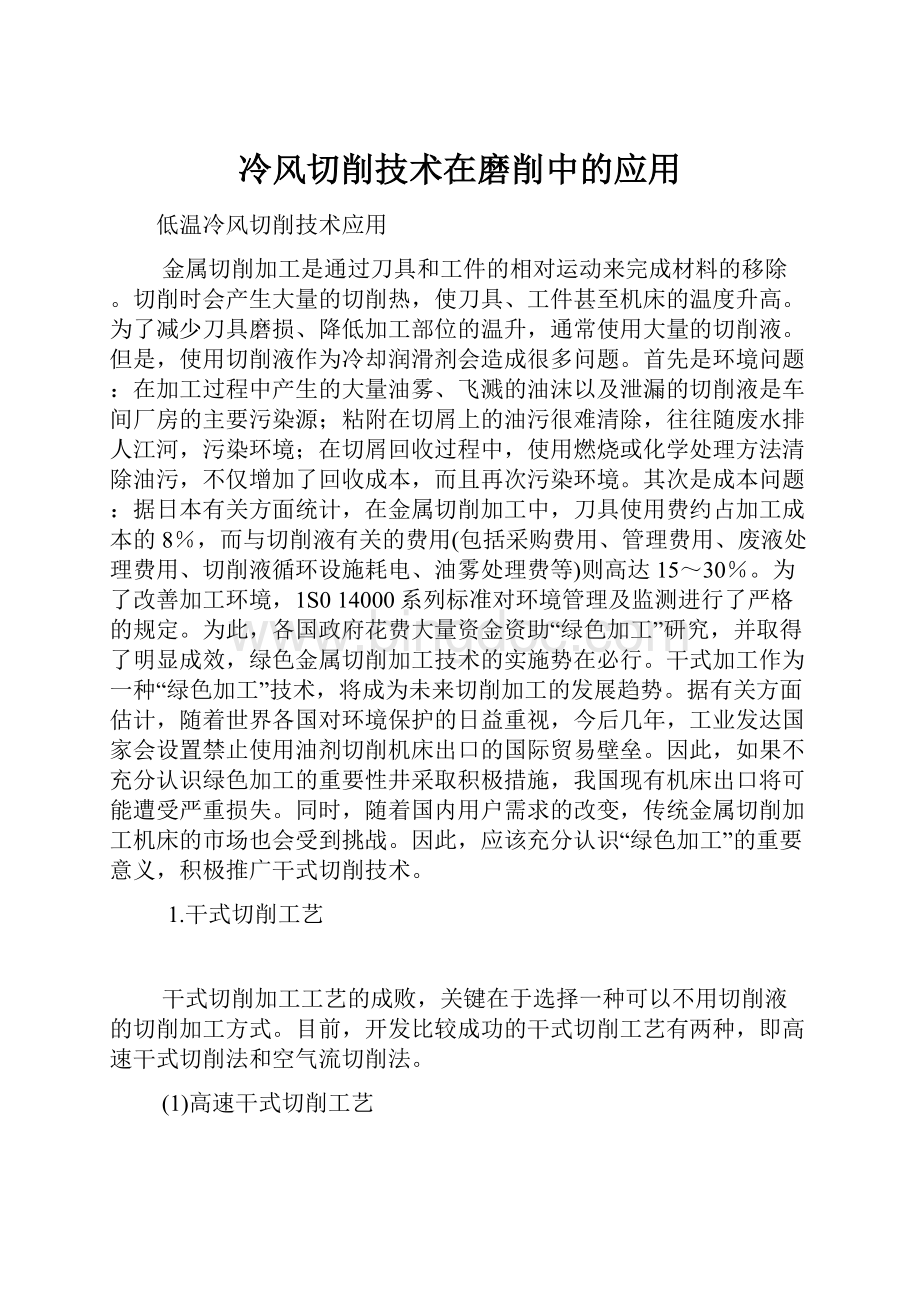
(1)高速干式切削工艺
高速干式切削就是在无冷却液、润滑油的条件下,采用很高的切削速度进行切削加工。
因此,干式高速切削需要在一定的切削条件下进行。
首先是选用很高的切削速度,尽量缩短刀具与工件的接触时间,再用压缩空气或其它方法移去切屑,以控制工作区域因切屑堆积而造成的温升。
随着机床制造技术的发展,提高机床的切削速度并非难事;
当切削参数设置正确时,80%的切削热量将被切屑带走,使切削点的温升降低。
高速干式切削法对刀具有严格的要求,适合高速干式切削的刀具必须具有以下特点:
①刀具材料应具有优异的耐高温性能,可在无切削液的条件下工作。
通常采用新型硬质合金、聚晶陶瓷和CBN材料。
②良好的刀具结构设计,使切屑与刀具之间的摩擦系数尽可能小以减少热堆积。
最有效的方法是采用刀具表面涂层工艺。
③比湿式切削刀具具有更高的强度和抗冲击韧性。
国外高速干式切削的研究工作开展较早,条件也较为成熟,西欧国家已有近1/3的企业开始采用。
但是,由于高速干式切削对加工条件要求比较苛刻,给机床在线稳定生产造成一定的难度,使用复杂刀具加工时更为突出,因此,该工艺在我国短时期内难以普及。
(2)空气流切削工艺
空气流切削法包括MQL(微量润滑)切削、低温冷风切削、氮气流切削及蒸气切削法。
MQL切削是在切削中用压缩空气加微量润滑剂代替切削油剂;
低温冷风切削是在MQL切削法的基础上降低压缩空气的温度进行切削,氮气流切削是在切削中用氮气流代替低温冷风;
蒸气切削则是在切削时用蒸气代替切削油剂。
1996年,日本横川技术研究所、工学院大学的横川和彦教授、横川宗彦副教授等人对低温冷风切削加工技术的研究获得成功。
低温冷风切削加工是在切削时使用-10℃~-100℃的低温冷风和非常微量的植物油代替冷却润滑剂实施切削的方法。
研究表明:
在金属切削过程中,如果只给加工点提供非常微量、润滑效果良好且未被氧化的植物油,加工点会因高温而丧失润滑性,使刀具很快磨损。
如果加工时提供低温冷风,加工点的高温化就可得到缓解,达到延缓刀具磨损的目的。
如果在给加工点提供低温冷风的同时,再加上润滑效果良好且未被氧化的微量植物油,不仅加工点的高温化可得到缓解,而且刀具的润滑性也可得到保证。
试验证明,采用低温冷风切削时,车刀的寿命可以延长两倍以上。
近几年来,国外对低温冷风切削技术的研究已趋成熟,低温冷风切削技术已为机床生产企业所接受并相继推出采用该技术的机床产品。
如日本安田工业公司的加工中心采用在电机轴、刀杆轴的中心插入绝热风管的结构,使-30℃的低温冷风直通刀刃,该结构太大改善了切削条件,更有利于低温冷风切削加工工艺的实施。
此外,日本三井精机推出的加工中心、冈本工作机械推出的平面磨床、森精机推出的车床等都使用了低温冷风切削技术。
为了保证切屑的迅速处理,这些机床的结构都作了较大的调整。
同时,与之配套的低温冷风发生系统的生产也实现了商品化,并正在成为日本机床行业新的销售热点。
2.低温冷风切削技术的特点
(1)勿需作加工尺寸补偿
在使用油剂切削时.由于油剂温度高,工件受油温的影响会发生膨胀,加工时往往需要进行尺寸补偿。
使用低温冷风切削工艺后,由于采用稳定的低温冷风,太大减少了工件的热变形,因此,勿需进行加工尺寸补偿。
(2)有利于提高加工精度
研究表明,冷风可以使加工点的温升低于60℃,工件加工界面残留应力趋于零,对提高加工精度具有重要意义。
(3)提高刀具寿命
试验表明:
在同一台机床上使用相同材料的车刀进行切削,分别用+10℃、-5℃、-10℃、-20℃、-30℃的冷风冷却切削点,试验结果太为不同:
以横刃面磨损至0.1mm为限,在风温为+10℃时切削长度为140m;
风温为-5℃时切削长度为330m;
风温为-10℃时切削长度为760m,风温为-20℃时切削长度为1220m,风温为-30℃时切削长度高达1400m。
从试验结果可知,采用低温冷风切削可明显提高刀具的使用寿命。
(4)提高加工效率
在使用油剂切削时,为了防止油雾扩散和油沫飞溅,加工时需要使用护罩,高速切削机床还设有全密封护罩。
护罩的使用阻碍了装卸工件,增加了频繁开启时间。
采用低温冷风切削可解决这个问题,明显提高加工效率。
此外,刀具寿命的延长也提高了机床的加工效率。
除此之外,由于机床不再使用切削油,因此,可以直接观察加工状态,有利于操作;
可以节约机床切削油循环系统、油雾分离装置等的制造费用,降低机床制造成本;
可以节约机床切削油循环系统占用的车间面积,降低零件加工成本;
同时,更有利于难切削材料的加工。
3.低温冷风发生装置的研究
要采用低温冷风切削技术,最重要的是必须配置相应的低温冷风发生装置。
目前国外如日本已有多家工厂生产这种装置,已形成商品的低温冷风发生装置的结构形式主要有:
氮气流发生装置、使用低沸点工质作冷媒的间接冷却装置以及通过压缩空气冷冻循环的间接冷却方式等,但其价格都比较昂贵。
(日本生产的低温冷风发生装置的价格随冷风排放量的大小不同,每台分别在150万日元~340日元之间)。
国内对低温冷风发生装置的研究也在顺利进行。
目前,实验室样机已经投入试验使用。
相信国产低温冷风发生装置的研制成功必将推动我国干式切削技术得到更广泛的应用和发展。
冷风发生装置及风冷却切削用技术(组图)
切削或磨削加工中使用切削液的主要作用是冷却和润滑,为了提高其性能往往都添加含有S(硫)、P(磷)、Cl(氯)等化学元素的极压添加剂.这些物质污染环境并对人体有害、而且使用完了的切削液必须进行处理,增加了费用。
因此,不使用切削液的干式切削和准干式切削已成为绿色切削工艺的研究热点,但由于在一定条件下,无任何冷却措施的干式切削还无法满足加工要求,还需要对刀具进行一定的冷却和润滑,因此出现了风冷却加工技术。
本文重点介绍有关风冷却的加工技术及装置。
1.风冷却加工系统
图1风冷却系统的构成
风冷却系统的构成如图1所示。
一般由压缩空气供给源、空气除湿器、空气冷却器、绝热管、微量供油装置、风嘴、吸尘管和集尘器构成。
从空气供给源来的空气经过除湿器将水分除去后,送入空气冷却器冷却至-30℃,再经绝热管由风嘴将冷风送至切削部位。
同时向加工点喷少量的无害植物油,以防锈并且有一定润滑作用。
在风嘴的对面设有集尘装置以收集废屑和风尘,通过集尘器内的过滤器将切屑滤去。
2.空气的冷却方法及要求
制冷的方法有很多,常见的制冷原理可归结为4种:
液体汽化制冷、气体膨胀制冷、涡流管制冷和热点制冷。
原则上讲这些制冷方式都可用于空气的冷却。
但目前作为切削用冷却空气的方法有使用液体氮等低沸点介质的间接冷却方式、使用制冷剂的压缩机循环间接制冷方式、利用压缩空气的绝热膨胀直接制冷方式和涡流管的制冷方式等。
使用低沸点介质的间接冷却
图2使用低沸点介质的间接冷却方式
图2为使用低沸点介质的间接冷却方式的原理图。
这种制冷方式使用氮等对人体无害、无环境污染的低沸点气体,可在有关工厂液化,再加入风冷却系统中,在常温常压下蒸发吸热,使空气冷却。
此种冷却方式由于液氮是在外部液化的,在系统内部仅存在和空气的热交换,因此冷却部分的结构简单。
另外,液氮的汽化温度是-180℃,因此可将空气冷却到-100℃以下,温度可由液氮的流量控制,过冷时可通过加热器加热。
但采用此种方式进行连续实际切削时需要大容量的储液器,因此不太实用。
另外,由于液氮等低沸点液体在外部制备,因而加大了整个系统的运行成本。
循环压缩式间接制冷
图3循环压缩式间接制冷方式
循环压缩式间接制冷方式如图3所示。
该方式使用低沸点的制冷剂,由压缩机、蒸发器、冷凝器和膨胀阀构成闭环冷却系统。
根据制冷效率和蒸发温度选用作为制冷剂的气体。
此种制冷方式广泛用于家用冰箱及冷冻仓库,在温度控制和能耗效率方面都比较理想。
经蒸发器蒸发的气体由压缩机加压到所定压力,在冷凝器中液化,储存到储液器中,储液器内的高压液体在设定压力以下经膨胀阀减压进入蒸发器,蒸发吸热将空气冷却,再变成气体回到压缩机,冷风温度可通过蒸发器内的压力和液体供给量进行设定。
此种制冷方式分为蒸发温度(压力)、冷凝温度(压力);
按能耗方式分为单级压缩循环、多级压缩二元冷冻循环等。
空气绝热膨胀直接制冷
图4空气绝热膨帐直接制冷方式
空气绝热膨胀的直接制冷方式如图4所示:
此种制冷方式是利用高压空气的绝热膨胀,降低冷却气体本身的温度,属于开放型的直接制冷方式。
由空气压缩机或管路来的常温、高压空气进入膨胀机,使其在设定压力以下膨胀,通过发电、外部机器驱动等消耗空气的能量使温度下降。
冷风出口温度由进入膨胀机气源压力和膨胀机的出口气体压力及膨胀机的性能决定。
目前能产生-90℃冷风的设备已经实用化。
涡流管直接制冷
1.喷嘴2.孔板3.涡流室4.控制阀
图5涡流管直接制冷方式
图5所示为涡流管制冷的原理图。
高压空气通过涡流管时将产生涡旋运动,由于涡流内外气体存在压力差(密度差)而产生温度差.中心部分的气体为低温气体,外侧为高温气体。
冷风的温度与入口气体压力和排出的气体流量有关。
此制冷方式不需要另外的动力,仅用一个涡流管即可,结构简单。
但由于需有一部分气体作为热气排出,因此,制冷效率要差一些。
实施风冷却切削加工对空气冷却系统的要求
实施风冷却切削技术的关键要控制好风冷却的4个要素:
温度、压力、流量和方向。
无论是哪种制冷方法都应满足以下要求:
应能与一般工厂现有风压配合使用;
输送管径要尽量大,以减少由管路造成的流量损失;
冷风温度和风量应可调;
冷风的输出应能够暂停;
要在短时间内使冷风温度达到要求;
风嘴应尽量接近冷却点,距冷却点20mm以上时冷风温度上升较多上述4种制冷方法。
目前日本应用最多,并且压缩机循环制冷方式已达到商品化。
3.风冷却切削的优缺点及研究方向
风冷却切削的优点:
因不使用切削液,因此,不产生Cl、S、P等元素,无化学污染,有利于环保:
节约了切削液的购入费用及其相关的设备费用和维护费用;
不需要处理切削液,防止了地球暖化,节省了处理费用;
不使用切削液而节省了地球资源;
由于不使用切削液其切屑可以直接利用。
但风冷却切削目前也存在以下问题:
切屑收集问题;
纯风冷却时刀具的润滑问题;
已加工工件的防锈问题;
冷风的噪声问题;
目前风冷却切削研究的主要方向有:
提高冷却性、减少冷却空气量;
降低风嘴的噪声;
开发润滑性好的刀具;
研究高效的切屑收集方法。
冷风切削技术在磨削中的应用探讨
一、概况
在汽轮机制造中,90%以上的部套、零件都需要进行金属切削加工,而金属切削加工离不开刀具。
一般来说,刀具制造的最后工序为磨削,磨削质量的好坏直接影响到刀具的应用质量、生产效率和寿命。
通常情况下,提高磨削质量的主要措施,一是砂轮的合理选取,二是磨削时冷却润滑液的选择。
对一般刀具制造而言:
平面、内、外圆磨削加工都可使用切削液,但在万能工具磨床(刀具磨床)、铲齿磨床和拉刀磨床精磨刀具时,由于机床结构的原因,就无法使用切削液。
此时如为提高加工效率,再选用较大的切削用量,则刀具表面极易出现烧伤、退火、裂纹等缺陷。
这些毛病都将直接影响到刀具的精磨质量和使用寿命、效率,并增加制造成本,而此时如采取使用干式(准)冷风切削工艺,就能较好地解决这一难题。
二、冷风切削技术的应用
冷风切削技术的基本原理
用低温空气代替切削液,是改善冷却条件的新办法。
冷风切削技术是近年来国际较为流行的一种加工方式,主要为防止(切削液等)污染、改善加工环境,提高切削效率、延长刀具使用寿命(特别是解决难加工材料的加工)降低加工成本的高效加工配套技术。
所以国际公认它是一种绿色切削技术,欧、美、日、俄等工业发达国家现已在较大范围推广应用。
冷风切削技术是用-10℃~-50℃左右的低温气体,混合微量无公害油剂(10~20毫升/小时)代替切削液进行润滑、降温和排屑,它是目前国际上广为流行的MQL(微量润滑)切削方法的延伸。
冷风切削加工系统主要由:
压缩空气源、空气粗过滤清洁系统、CTL系列低温冷风射流机(或中央冷风射流机)、高保温管道、微量油雾化器和各型冷风喷嘴等组成。
它通过空气粗过滤清洁系统过滤、净化车间压缩空气、再经CTL低温冷风射流机对这些空气进行低温处理,得到干燥而洁净的低温冷风,温度一般在-50℃以下,并可自由调节;
微量油雾化系统可按加工需要,生成非常微量的无公害油剂并混入冷风内,对切削点进行微量润滑。
工作时,只要打开冷风射流机的电源,按说明书启动设备,让低气流通过高保温管道和微量油雾化器,并将冷风喷嘴置于切削点附近、对准切削点,便可进行冷风切削了。
冷风切削设备的使用和主要参数的选用
冷风设备主要有下列部件组成:
空气压缩机、低温冷风射流机、微量油雾化器、喷射器、刀具(砂轮)等组成,我们应用的设备由重庆成田低温加工技术有限公司提供,其主要参数为进气压力0.6-0.8MPa,进气温度≤40℃,出气额定流量3.0NM3/min,出气压力≥0.3MPa,出气温度≤-50℃。
冷风切削技术的使用效果好坏,除和设备本身的性能、质量密切相关外还与正确、合理使用设备和参数选择有关,根据我们近三年对冷风设备的应用,我们认为有下列几点应予以重视和引起注意。
使用前的准备
要检查风源质量
一般来说,工厂使用的压缩空气,风源是由压缩空气总站通过管道输送到各使用车间的,由于常年使用,管内因生锈、气源中混入杂质、油污、积水等常会使管道风口堵塞,导致工作风量和压力显著下降,造成加工点得不到充分的冷却,因此在使用前,必须开机一段时间来检查风源的质量,如发现风源质量不好,则应立即采取疏通管道或增加过滤器等措施处理。
要检查保温管的密封和长度是否合理
连接冷风机和压缩空气出口处的保温管,是确保能长久低温供气的重要环节,保温管安装好后,要检查确保两端无泄露现象,为了避免管内温度升高和气压的稳定,保温管不宜过长,只要能满足正常工作就行,也不要因进气管卷曲影响供气质量。
要检查冷风机主要零件的联接质量和设备的排风口前不要有任何屏障
因设备在发货运输过程中的颠簸和装配中的不慎,常会出现联接件的松动(包括电器和机械零件),所以在开机前必须予以检查,排风口如有屏障,会造成设备排气不畅,从而使设备温度升高,不能长时间的正常工作。
冷风喷头与安装位置的确定
在加工过程中,为使砂轮得到良好、充分的冷却,宜用两个喷头同时将冷风喷射在工件和砂轮的表面。
喷头安装时应将其分别夹持在经改装过的百分表磁力座上,然后将其固定在机床的床身或刀架上。
工作时,让上下两个喷管的喷头同时对准被磨刀具的前后面进行喷射冷却。
冷风冷却温度的优选
使用冷风切削设备对冷风温度的优选至关重要,一般来说,冷风温度低一点好,在磨削加工时,如果选用-10℃~-25℃这一段温度区间,则由于冷风在保温输送系统等中间环节的损耗过大,喷出的气体实际温度相对较高,此时,由于磨削点得不到充分的冷却,会影响到冷风切削的最佳效果,但是,如果长时间选取设备最低(-50℃以下)温度区间,则将对制冷系统(低温冷风射流机)的使用寿命造成不良影响,经长时间摸索和探讨实践,我们认为:
磨削时优选冷风温度控制在-40℃~-45℃最为合理,这和日本相关资料,把冷风磨削温度控制在-40℃左右为最佳的论述完全一致。
冷风切削应用时的维护
刃磨刀具前、后刀面的机床,一般都不使用切削液,所以机床都未配置防护装置,而冷风切削技术在这些机床上使用,磨粒的飞溅会对操作工人的健康产生不利影响,为此,我们在这些机床上配置安装了防护罩,为了便于操作人员观察磨削情况,防护罩根据机床结构用透明有机玻璃板弯曲成型制成,可自由移动,同时还配备了吸尘器。
三、使用效果分析
将冷风切削技术应用于刀具制造上,一开始,我们在万能工具磨床上试用,选择被加工刀具的原则:
一是先选择修磨进口和价格昂贵的高性能高速钢刀具,二是复杂和需要成批制造的专用刀具。
考核试用效果的指标则为:
加工效率的提高、刀具寿命的延长、加工质量的改善和综合成本的降低等四个方面。
经过筛选,决定在磨削上采用冷风切削技术的刀具是我厂常用的关键刀具—纵树型轮槽半精、精铣刀以及加工叶片成组成型铣刀经生产验证对比发现:
使用冷风技术磨削加工这些刀具,主要获得如下效果:
刀具加工效率的提高
在切削速度、走刀速度基本不变的情况下,在加工材料为W2Mo9Cr4VCo8(M42)的轮槽铣刀时,采用冷风切削技术制造的刀具其吃刀深度(背吃刀量)由原来不用冷风切削时ap=0.02-0.03mm,增加到现在(采用冷风切削技术)的ap=0.05-0.06mm,而在加工材料为W6Mo5Cr4V2(M2)的大直径成型铣刀时,吃刀深度由原来干切削的ap=0.03-0.05mm,增加到现在(采用冷风切削技术)的ap=0.05-0.10mm,切削效率平均提高80%以上。
刀具使用寿命的延长
由于采用冷风切削技术后,切削力减小,磨削温度显著降低,所以刀面和刀刃基本未出现退火现象,减少了刀刃材料晶格局部相变的可能性,因此,经验证:
经采用冷风切削技术刃磨的刀具其加工工件长度和刃磨次数都有较大程度的增加,与传统刃磨方式相比,刀具寿命可延长30%左右。
加工表面质量的改善
冷风切削技术在刀具刃磨中的使用,能使刀刃更加锋利,特别在精加工中它可使加工表面粗糙度值降低将近一级(和传统刃磨方法相比),这样就可使涂层质量得到进一步提高,从而使刀具获得更高的耐用度。
初次试用证明,冷风切削技术在万能工具磨床、拉刀磨床和铲齿磨床上刃磨高速钢刀具是成功的,取得的效果也是显著的。
冷风切削技术在我厂刀具刃磨工艺中的应用已有两年多时间,由于在效率、寿命和质量方面的提高,因此,它的综合经济效益也是明显的。
冷风切削技术这一新型清洁加工技术在我厂刀具刃磨上的应用受到制造部门和使用部门的广泛欢迎。
大家认为,它的确是一种绿色切削和有利于环保的新技术,但应用中我们也发现在设备、工艺和最佳切削用量等的选配方面,还有待进一步完善和改进。
(end)
冷风切削技术在哈汽轮机公司试验成功
(本网讯通讯员杨松)日前,具有当今世界前沿技术之称的冷风切削技术在哈汽轮机公司试验成功,标志着重型机械行业清洁生产工作进入了一个崭新阶段。
重型机械行业一直沿用的是湿式切削方法。
该方法在低于180m/min的切削速度下能够获得理想的切削效果。
但随着数控化的普及、刀具制造技术的提高,金属切削机床的切削速度越来越快、加工效率越来越高,随之所产生的切削热和刀尖温升也不断提高,依靠常规加大切削液流量、降低切削温升的办法已不能收到理想的效果。
同时,切削液在金属切削过程中会带来自然环境的污染也引起了业内专家的重视。
另外,切削液费用也在逐年增加,使得机械零件加工成本也在逐年上升。
哈汽轮机公司为解决生产加工中的这些难题,进行了冷风切削试验。
冷风切削技术是干式切削技术的一种,属于半干式微量润滑切削(MQL)。
它采用空气加微量油雾代替冷却剂切削工艺,通过把喷射空气温度降低到零下30摄氏度以下喷向切削点,使切削点低温化,从而达到完成切削任务的目的。
早在20世纪90年代初,发达国家就拔专款资助以代替油剂湿式切削、清洁加工为目的干式切削加工工艺的研究。
1996年9月,ISO14000环境标准在欧洲通过以后,这一技术逐渐被推广。
试验中,哈汽轮机公司以高温合金材料轮盘加工为突破口,由副总工程师姚青文、课题组负责人顾祖慰、工具处孙盛丽等组成攻关小组与重庆大学科技园成田低温加工技术有限公司高级工程师张昌义进行了冷风切削技术研究。
在二分厂领导的大力支持下,经过多次反复论证和试验获得成功,不仅工作效率提高1至3倍,刀具使用寿命也提高了1至2倍。
三分厂、叶片分厂、工具处等单位加工过程中因油雾造成的环境污染,会对对职工身体健康造成的危害,一直是索绕公司领导心头的一件大事,虽然曾经多次到生产车间调研,研究解决办法,也采用了一些措施,但是还没有从根本上解决问题。
公司攻关小组经过认真研究,确立了《冷风切削在加工中应用》专项课题,正在上述单位进行推广试验并取得了阶段性进展。