大型机组油系统冲洗工法.docx
《大型机组油系统冲洗工法.docx》由会员分享,可在线阅读,更多相关《大型机组油系统冲洗工法.docx(14页珍藏版)》请在冰点文库上搜索。
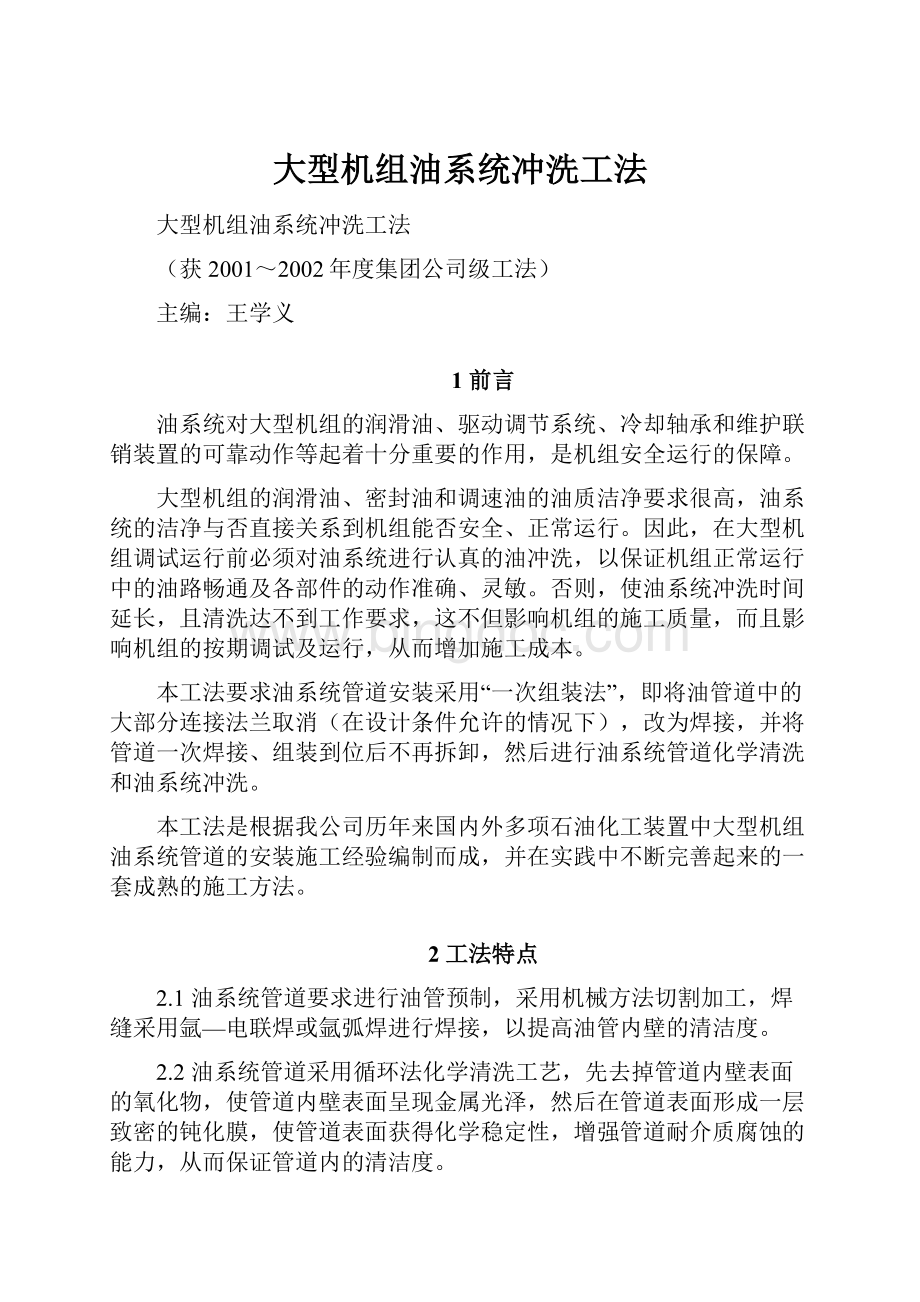
大型机组油系统冲洗工法
大型机组油系统冲洗工法
(获2001~2002年度集团公司级工法)
主编:
王学义
1前言
油系统对大型机组的润滑油、驱动调节系统、冷却轴承和维护联销装置的可靠动作等起着十分重要的作用,是机组安全运行的保障。
大型机组的润滑油、密封油和调速油的油质洁净要求很高,油系统的洁净与否直接关系到机组能否安全、正常运行。
因此,在大型机组调试运行前必须对油系统进行认真的油冲洗,以保证机组正常运行中的油路畅通及各部件的动作准确、灵敏。
否则,使油系统冲洗时间延长,且清洗达不到工作要求,这不但影响机组的施工质量,而且影响机组的按期调试及运行,从而增加施工成本。
本工法要求油系统管道安装采用“一次组装法”,即将油管道中的大部分连接法兰取消(在设计条件允许的情况下),改为焊接,并将管道一次焊接、组装到位后不再拆卸,然后进行油系统管道化学清洗和油系统冲洗。
本工法是根据我公司历年来国内外多项石油化工装置中大型机组油系统管道的安装施工经验编制而成,并在实践中不断完善起来的一套成熟的施工方法。
2工法特点
2.1油系统管道要求进行油管预制,采用机械方法切割加工,焊缝采用氩—电联焊或氩弧焊进行焊接,以提高油管内壁的清洁度。
2.2油系统管道采用循环法化学清洗工艺,先去掉管道内壁表面的氧化物,使管道内壁表面呈现金属光泽,然后在管道表面形成一层致密的钝化膜,使管道表面获得化学稳定性,增强管道耐介质腐蚀的能力,从而保证管道内的清洁度。
2.3采用分阶段逐步提高滤网密度的方法进行油冲洗,能尽快使油系统的清洁度符合要求。
2.4分阶段冲洗油系统能加快冲洗速度,缩短冲洗时间,从而提前调试、运行日期,降低施工成本。
3适用范围
本工法适用于石油化工装置的离心式压缩机组及中、小型汽轮发电机组等的油系统管道、设备的油冲洗。
4工艺原理
4.1采用机械和人工方法除去管道和设备内的尘土、杂物及油污。
4.2采用化学清洗法除去管道和设备内的锈蚀。
4.3采用分段进行油系统冲洗时,间断开停油泵,使油温在40℃~75℃范围内急冷急热,并向管内冲入氮气,以便冲洗油在系统内产生紊流,从而提高冲洗效果。
4.4提高油的流程,加大冲洗流量,以保证冲洗质量,缩短冲洗时间。
5工艺流程及操作要点
5.1工艺流程(见图1)
图1工艺流程
5.2操作要点
5.2.1油系统管道、设备的检验与清理
a)管材、管件、阀门和设备等应按设计文件和相关标准规范的要求进行检验,不合格者禁止使用。
b)清理不锈钢管时采用旧布在管内来回拖拉,然后采用大量的热水冲洗干净,最后烘干;φ3〃以下的碳钢管运用铁锤敲击的方法将杂物清出,然后用圆盘钢丝刷绑在长杆上来回拖擦管道内壁;φ3〃以上的碳钢管采用喷砂处理,喷砂结束后立即用压缩空气吹净。
清理干净的管子应及时封闭两端,以免二次污染。
c)油管道中的窥视镜、管件、阀门、三通等附件都要仔细清理。
对窥视镜、阀门逐一进行拆检,清除内部异物、杂质,如是铸造件则内刷有防护漆,需将漆片及脱落的型砂清理干净。
对阀门密封面进行研磨检查、然后进行强度和密封性试验。
d)油系统附属设备:
油箱、高位油箱、油冷却器、油过滤器、油泵及轴承箱必须逐一进行拆检、清理。
1)油箱的清理
首先检查油箱中的防护漆。
对质量不好的防护层应用喷砂法或脱漆剂除去,清除加强筋板处的焊渣,然后用汽油彻底清洗干净,最后用面团法粘出污垢、铁屑、焊渣等微粒,直至清洁为止。
2)油过滤器的清理
检查内部的防护漆情况,若油漆很好,只需用汽油清洗后再用面团粘尽即可,否则也应进行喷砂处理。
3)油冷却器的清理
对油冷却器进行抽芯检查,若发现内筒壁或列管有锈蚀、污垢等需要进行化学清洗时,必须先进行脱脂。
脱脂后,内筒可采用化学清洗或喷砂处理,若杂物、污垢等较少则只用蒸汽或压缩空气吹净即可。
油冷却器清洗完毕后重新组装,再用工作油进行试压。
4)高位槽的清理
高位槽安装之前,应进行喷砂处理或化学清洗,并经有关人员检查合格后,涂油漆保护、封闭。
5)油泵
解体检查泵壳内壁的铸造质量,若质量良好,用面团法粘净即可组装。
6)轴承箱及油腔的清理
打开轴承箱上盖彻底清除杂物,并用面团将杂物粘净。
油腔内用人工方法清除型砂并用压缩空气吹净,再用面团粘掉微小砂砾及杂物。
7)变速箱的清理
打开变速箱上盖,检查箱内防护漆及铸造型砂的质量。
若防护漆和型砂质量良好,只用汽油清洗后再用面粘法粘净即可。
否则用脱漆剂除掉油漆后,用人工和机械方法除掉型砂,再用面团粘净。
5.2.2油管道与设备连接
a)管子与设备连接的法兰处采用冲压成型的耐油垫片,垫片内孔无毛边,垫片内径必须与法兰密封面内径相同。
b)管子与设备连接时,不允许使设备承受附加外力,并不得使异物进入设备或元件内。
c)经质量检查员检查,合格后进行工序交接,设备和油管封闭由建设单位代表、监理、质检员共同检查合格后方可封闭。
5.3油系统循环油冲洗
5.3.1油冲洗准备
a)油系统管道和设备的吹扫及化学清洗应符合标准规范的规定,并经检查确认合格。
油系统各油泵试运转合格。
b)确认系统内阀门开启状态符合设计流程要求,确认油系统安全工作状态良好有效。
c)分别将润滑油、密封油、调速油系统中进入机器的各入口及错油门、油动机入口处的管道与冲洗油管道断开,并在设备或阀体入口处加设临时盲板,配置临时接管,将供、回油管路连接成一个循环系统,在回油总管的进油箱前增设临时检查过滤盒。
滤网可逐次采用100目~200目的滤网过滤,以便检查管道的油冲洗效果。
d)拆除油过滤器的滤芯,过滤器出口法兰装上临时滤网,规格逐次由小到大进行更换(一般为120目~200目),并在泵入口处加设180目~200目的临时滤网,其通流面积不小于管道截面积的三倍。
5.3.2油系统冲洗措施
a)利用油加热器或冷却器使油系统内的油进行加热或冷却,使油在一定温度范围内急热急冷,以达到剥离管内壁沉积物的作用。
油的加热、冷却曲线见图2。
冲洗油温最高75℃,最低35℃,交替循环进行。
图2油的加热、冷却曲线
b)提高油冲洗的流程,加大冲洗流量;在回油总管进入油箱前加节流孔板,使油管内部全部充满油,油系统较长时,可采用分段冲洗。
分段冲洗时,可以间断开停油泵及开关油路阀门,使冲洗油在管内产生旋涡流动;向管内充入氮气,使冲洗油在管内产生紊流,以提高冲洗效果;向油管充氮气冲洗时,充入的氮气压力应稍高于系统内的油压,充氮气应间断进行,每隔1~2小时充氮一次,每次2~5min。
c)冲洗油的冲洗流速应使油呈紊流状态。
在管壁光滑的管道中形成紊流的流速U可按照下式计算:
式中:
v—冲洗油的运动粘度,(m/s);
d—冲洗管道的内径,(cm)。
清洗用油泵供油的流速一般不大于1.5~2m/s.
d)在油冲洗的过程中,按照油路流向顺序用木锤敲打管壁(特别是焊缝、弯头、三通部分),使氧化物、焊渣等松动脱落,并将其除去。
此外,定期排放或清理油路的各死角和最低处积存的污垢。
e)从油管各视镜处查看冲洗油的流动情况均应正常。
f)在油冲洗中采用滤油机连续、循环过滤,直至油质洁净不含水为止。
5.3.3油系统冲洗过程
a)首先进行润滑油站系统的冲洗,此段冲洗回路包括整个油系统中主要的阀门和油冷却器、油过滤器、油箱等设备,且管线弯头多较复杂,是油系统冲洗的重点。
b)第一次油系统冲洗时,在回油总管入油箱前加100目的不锈钢丝网,起初每运行2小时清理一次滤网,逐步延长至8小时清理一次。
热油与冷油交替进行冲洗,时间不少于48小时。
目测过滤网内表面,当清洁度达到每平方厘米面积上不超过2点污物时为止。
第一次系统冲洗结束后,放掉冲洗油并清理油箱。
c)第二次油系统冲洗时,将清洁的冲洗油用过滤机注入油箱。
将回油总管入油箱前的不锈钢滤网更换为150目,过滤器出口处的不锈钢滤网更换为150目,在每个轴承进油管中加装180目的尼龙丝滤网。
将润滑系统各轴承上瓦拆除,下瓦错开进油孔或将上瓦取下,在下瓦两间隙处加装几层白布条,然后盖好轴承盖,进行油循环。
开始冲洗时每2~4小时检查一次并清洗过滤网,此后连续冲洗时每隔4小时检查一次,并记录杂质规格与数量。
当每平方厘米面积上目视可见软性杂质不超过2点时为合格。
第二次油系统冲洗结束后,排净冲洗油并清理油箱。
d)第三次油冲洗前先清洗过滤器芯和过滤器,并拆除过滤器出口滤网,然后将滤芯装入过滤器,将临时管道、盲板全部拆除,对未冲洗的调速油小管道(一般为不锈钢管)用压缩空气吹净,然后将所有油系统管道复位。
轴承全部清洗干净后安装好,使油通过所有部分。
冲洗时,油箱内要装合格介质油,在回油总管进油箱前更换上180目~200目的不锈钢丝网或尼龙丝网。
在轴承、密封油,调速油的进口处加设180目~200目的尼龙滤网,并把调速油的压强控制在正常操作压强,而密封油也应达到正常操作的油气压差。
按照正常流程用冲洗油连续运转4小时后,检查滤网,在每平方厘米面积上可见软性杂质不超过2点(允许有微量纤维杂物存在)时,连续运转20小时,当滤油器的前后压差增值不超过0.01~0.015Mpa时为合格。
油冲洗合格后拆除所有临时滤网,分析油箱内的油品,油品合格后作为机组试车用油。
5.4油冲洗要求
5.4.1采用过滤机向油箱注入合格的冲洗油,油位要达到最高液位。
进油箱的冲洗油再经180目~200目的滤网进行过滤,以防滤纸、纤维等杂质进入油箱。
5.4.2冲洗油与系统工作介质相溶,要保证冲洗油粘度低于工作介质粘度,或用工作油进行油冲洗。
5.4.3冲洗回路应使每一段内壁全部接触冲洗油,并联的各冲洗回路其管径应接近;冲洗回路中的死角管段,要另成回路冲洗。
5.4.4按照油冲洗操作方法进行冲洗,有条件时可用滤油机净油。
对临时滤网中收集到的杂质进行检查,无焊渣、砂砾、铁锈等杂物后,在油箱回油总管处定期取样化验冲洗油中的杂质含量,直至符合要求。
5.4.5系统油冲洗检查合格后,清洗油过滤器及轴承,拆除临时设施,装好流量、温度、压力等检测部件,将油管道与润滑油、调速油、密封油系统进行连接,并视具体情况换合格的工作油进行油循环。
5.4.6对符合油冲洗标准且合格的油系统,填写油冲洗记录,并经建设单位、监理单位、质量检查部门代表予以签字确认。
6材料
本工法油管道循环冲洗用料见表1(不包括化学清洗用料)
表1油管道冲洗消耗材料一览表
序号
名称
规格
单位
数量
备注
1
洗涤汽油
180#(120#)
Kg
50
2
煤油
Kg
80
清洗临时滤网及过滤芯用
3
白棉布
纯棉
m
20
4
海棉
δ=50mm
Kg
3
设备清洗用
5
白面粉
Kg
50
6
耐油橡胶、石面板
δ=2.5mm
m2
4
7
耐油橡胶、石棉板
δ=2mm
m2
2
8
不锈钢丝网
20目
m2
2
做临时滤网加强用
9
不锈钢丝网
100目120目150目
m2
各4
10
不锈钢丝网
180目200目
m2
各2
11
尼龙丝网
180目200目
m2
各3
12
滤纸
500×500
张
200
13
内衬钢丝透明胶管
1〃11/2〃2〃
m
各25
14
内衬线透明管
1〃11/2〃2〃
m
各30
15
碳钢板
σ=8mm
m2
2
做临时孔板、盲板
16
塑料刷布
2000×2000
m
30
17
毛刷
1〃2〃3〃
把
各2
18
钢丝刷
把
3
19
圆形棒刷
1〃11/2〃2〃
把
各3
20
木锤
把
6
7主要施工机具(见表2)
表2油管道冲洗施工机具一览
序号
名称
规格
单位
数量
备注
1
移动式空压机
6~8m3/min
台
1
2
滤油机
5~7m3/n
台
1
3
砂轮切割机
台
1
4
电动磨光机
φ100
台
1
5
电动磨头
φ6
台
1
6
长水平仪
2/1000mm
台
1
7
放大镜
φ8010~12倍
个
1
8
天平
台
1
9
氩焊弧机
台
2
8劳动组织及安全
8.1劳动力组织见表3
表3油管道冲洗劳动力安排
序号
工种
人数
备注
1
管工
8人
负责油管道安装及临时管线配置
2
电焊工
3人
负责焊接作业
3
起重工
2人
负责起重作业
4
电工
3人
负责电器作业
5
钳工
9人
负责油管道系统循环冲洗工艺的实测,负责油泵运转、维护、拆装、清洗临时滤网及过滤器芯等,每斑三人,8小时为一班
8.2安全措施
8.2.1施工前作好安全技术交底,施工时认真执行安全操作规程。
8.2.2施工现场消防道路畅通,并备有符合要求的消防措施。
8.2.3搞好文明施工,做到零部件、工具及施工材料都有储存设施,保持环境清洁。
8.2.4负责油冲洗人员应加强巡回检查,严防跑、冒、滴、漏等现象发生。
更换、清洗滤网时,应采取节油措施,防止污染厂房。
8.2.5作好工序交接,认真填写工序交接记录。
9质量要求
9.1质量管理
9.1.1施工前编制科学有效的施工方案并对施工人员进行技术交底。
9.1.2对施工人员进行质量意识教育,增强责任感。
9.1.3开展QC小组活动,运用全面质量管理指导施工。
9.1.4严格执行设计、标准规范及外商厂家的质量要求。
9.1.5强调工序质量,做好工序交接。
9.1.6坚持质量“三检制”,加大质量考核力度。
9.2质量标准明细见表4
表4质量标准明细
序号
标准代号
标准名称
1
GB50235—97
工业金属管道工程施工及验收规范
2
DL5011—92
电力建设施工及验收技术规范(汽轮机组篇)
3
SHJ519—91
乙烯装置离心式压缩机组施工技术规范
4
HGJ205—92
化工机器安装工程施工及验收规范(离心式压缩机)
5
SHJ516—90
催化裂化装置轴流压缩机—烟汽轮机施工技术规范
10效益分析
本工法与传统施工方法相比,具有技术先进、施工质量好、成本低、施工效率高的特点。
从1991年开始已在国内外几个石化装置中运用本工法进行施工,均取得了良好的经济效益和社会效益。
10.1经济效益
运用本工法可比其它冲洗方法缩短工期,不仅能保证试车油质量,而且能降低施工成本。
为机组调试和运行创造良好的条件。
与同期施工的兰化化肥厂氮压缩机组(三机组)、兰州煤气厂空分车间空压机组(二机组)油系统相比:
1油冲洗时间缩短了35~40天,提高工效3.5~4倍。
2节省人工315个。
3降低成本
本工法中所用的冲洗油经过滤,除去杂质和水分后可以用在其它机组油系统进行油冲洗。
而其他两台机组由于油冲洗时间过长,洁净度未达到规范要求,被迫分别交换冲洗油12吨。
消耗材料中的煤油、透明胶管、白钢丝网等均可回收再利用。
10.2社会效益
历年来在多项石化装置中运用本工法,均赢得了业主的一致赞誉,为装置早日试运转和投产,早出效益做出了贡献。
也为公司闯市场、求生存、求发展赢得了信誉。
11工程实例
11.1该工法首次成功应用于兰州兰化石化厂2.5万吨/年丙烯腈装置空压机组(五机组)油系统,取得了良好的效果。
1991年5月在该机组油系统管道施工中,使用了本工法,机组油系统冲洗仅用了10天时间,经过兰化公司质检部门、建设单位、制造厂(杭州汽轮机机厂、沈阳鼓风机厂、大连液偶合厂)代表共同检查,确认清洁度达到了合格标准,比同期施工的其它两台机组(三机组)油系统冲洗缩短工期35~40天,从而证明了本工法技术的先进性。
11.21994年6月,兰州兰化动力厂15万吨/年催裂化装置的主风机油系统,运用本工法冲洗只用了60小时,达到清洁度合格标准。
1994年8月,该装置富气压缩机组油系统冲洗采用本工法施工,机组油系统只循环了7天,油冲洗质量经过建设单位,监理单位、制造厂代表共同检查、确认油系统冲洗达到了合格标准。
为机组提前试运转创造了条件,保证了机组运行的顺利进行。
11.31997年2月~3月,兰州兰化公司30万吨/年合成氨装置中空压机组、氮压机组油系统按照本工法实施,两台机组共用一个油站的油系统冲洗只用了18天,经过德国西门子公司、瑞士苏尔寿公司专家确认达到了合格标准。
1997年4月~5月,同装置合成气压缩机组、冰机机组油系统管道也按照本工法施工。
两台机组共用一个油站的油系统,冲洗只用了20天时间,经过日本三菱公司专家确认达到合格标准。