钢结构加工流程.docx
《钢结构加工流程.docx》由会员分享,可在线阅读,更多相关《钢结构加工流程.docx(19页珍藏版)》请在冰点文库上搜索。
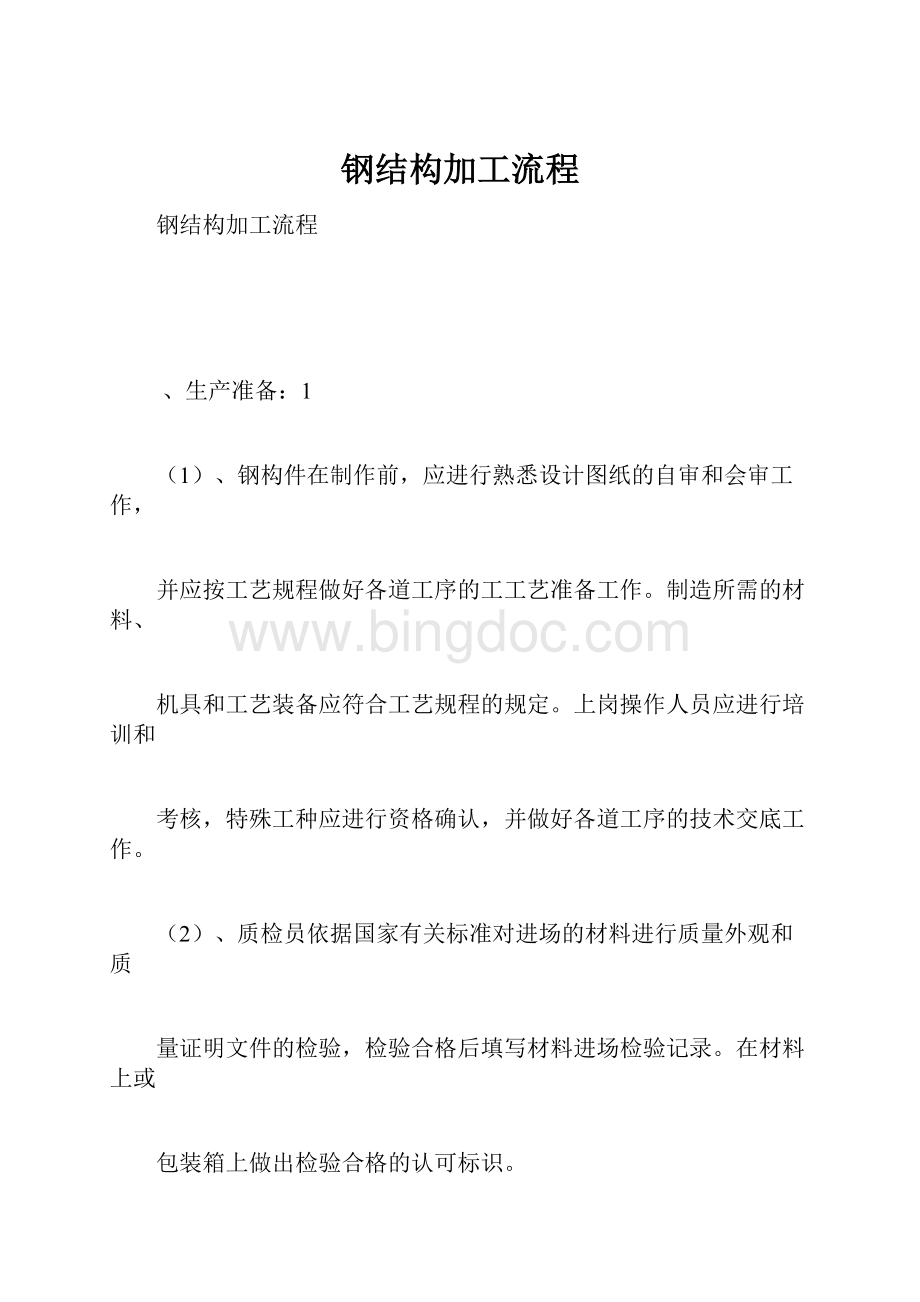
钢结构加工流程
钢结构加工流程
、生产准备:
1
(1)、钢构件在制作前,应进行熟悉设计图纸的自审和会审工作,
并应按工艺规程做好各道工序的工工艺准备工作。
制造所需的材料、
机具和工艺装备应符合工艺规程的规定。
上岗操作人员应进行培训和
考核,特殊工种应进行资格确认,并做好各道工序的技术交底工作。
(2)、质检员依据国家有关标准对进场的材料进行质量外观和质
量证明文件的检验,检验合格后填写材料进场检验记录。
在材料上或
包装箱上做出检验合格的认可标识。
(3)、进场材料,根据工程的要求及材料质量的具体情况进行复
验,必要时依据《金属板材超声波探伤方法》(GB4730-94)进行探伤,
经复验鉴定合格的材料方准正式入库,并做出复验标记,不合格材料
清除现场,避免误用。
(4)、焊材的选择与管理:
依据设计图纸提供的构件材料由主管
技术负责人选择相匹配的焊材,焊接工艺评定结果批准后方可使用。
焊接材料的管理:
焊条焊丝入厂时必须有齐全的质量证件及完整
的包装;按国家标准进行理化复验及工艺性评定。
焊材库的设置要按
规范配备齐全的通风干燥等设施,并设驻库检查及保管员,焊材出库
时严格遵守公司的管理规定,履行出库程序。
、放样和号料2.
(1)、放样应采用经过计量检定的钢尺,并将标定的偏差值计入
量测尺寸。
尺寸划法应先量全长后分尺寸,不得分段丈量相加,避免
偏差积累。
号料是以样板为依据,在材料上划出实样并打上各种加工
记号。
号料应使用经过检查合格的样板,避免直接用钢尺所造成的过
大偏差或看错尺寸而引起的不必要损失。
(2)、放样从熟悉图纸开始,首先应仔细阅读技术要求及说明,
并逐个核对图纸之间的尺寸和方向等。
特别应注意各个部件之间的连
接部位、连接方式和尺寸是否一一对应。
发现有疑问之处,应与有关
技术部门联系解决。
(3)、放样以1:
1的比例在样板台上弹出大样。
当大样尺寸过
大时,可分段弹出。
对一些三角形的构件,如果只对其节点有要求,
则可以缩小比例弹出样子,但应注意其精度。
(4)、先以构件的某一水平线的垂直为基准,弹出十字线,二线
必须垂直。
然后依据此十字线逐一划出各个点及线,并在节点旁注上
尺寸,以备复查及自检。
(5)、放样过程中碰到技术上的问题,要及时与技术部门联系解
决。
尺寸的变更,材料的代用,而产生与原图不相符处,要及与设计
单位联系作好更改。
(6)、放样结束,应对照图纸进行自检。
检查样板是否符合要求,
核对样板数量,并报质检员。
、划线、号料前首先根据料单清点样杆。
按号料要求整理好)7(.
样板。
(8)、熟悉样板、样杆上标注的符号和文字和含义。
搞清号料数
量。
(9)、准备并检查各种使用的工具,磨好石笔,保持样冲、圆规、
划针的尖锐及凿子的锋利。
(10)、号料前必须了解原材料的钢号及规格,检查原材料的质
量,如有疤痕、裂缝、夹灰、厚度不足等现象应调换材料,或取得技
术部门同意后方可使用。
(11)、号料的钢材必须摆平放稳,不得弯曲。
大型型钢号料,
应根据划线的方便来摊料,两根型钢之间要留有10厘米以上的间距,
以便于划线。
3、切割:
(1)、对于长条板件采取手工号料、多头直条数控切割机下料。
(2)、对于筋板、端板等各类节点板,在计算机上编制切割程序,
采取数控切割。
(3)、各类切割件切割前需对号料线、数控程序、进行审核,合
格后方可切割下料。
(4)、对于主梁翼板、腹板长度拼焊缝要错开200毫米以上。
(5)、切割后钢材不得有分层,断面上不得有裂纹,应清除切口
处的毛刺或熔渣和飞溅物。
组立前检查焊缝缝隙周围铁锈、污垢清理情况,组装后应检:
、组立3.
查组装形状尺寸,允许偏差应符合规范规定,检查合格后方可施焊:
4、矫正和成型
在钢结构制作过程中,由于原材料变形,气割、剪切变形,钢结
构成型后焊接变形,运输变形等,影响构件的制作及安装质量,一般
须采用机械或火焰矫正。
当采用火焰矫正时,加热温度应根据钢材性
能选定。
但不得超过900℃,低合金钢在加热矫正后应缓慢冷却。
5、制孔
(1)、门式刚架轻钢结构中的高强螺栓孔,普通螺栓孔,地脚
螺栓孔等应采用钻成孔,檩条等结构上的孔可采用冲孔。
制孔后应用
磨光机清除孔边毛刺,并不得损伤母材。
螺栓孔的允许偏差超过规范
规定时,不得采用钢块填塞,可采用与母材材质相匹配的焊条补焊,
打磨平整后重新制孔。
(2)、螺栓孔的加工采用数控钻床加工,对联接板要采用套钻
方法,以保证钢架的组装精度。
6、组装
钢结构构件的组装是遵照施工图的要求,把已加工完成的零件或
半成品装配成独立的成品构件。
零部件在组装前应矫正其变形并达到
符合控制偏差范围以内,接触表面应无毛刺、污垢和杂物,除工艺要
求外零件组装间隙不得大于是1mm,顶紧接触面应有75%以上的面积
紧贴,用塞尺检查,其塞入面积应小于25%,边缘间隙不应大于
,板叠上所有螺栓孔、铆钉孔等应采用量规检查。
组装时,配0.8mm
有适当的工具和设备,如组装平台或胎架、夹具、定位器等以保证组
装足够的精度。
为了保证隐藏部位的质量,应经质检人员检查认可,
签发隐蔽部位验收记录,方可封闭。
组装出首批构件后,必须由质检
部门进行全面检查,经合格认可后方可进行继续组装。
7、焊接
(1)、施焊前焊工应复查组装质量和焊接区域的清理情况,确认
材料及焊材是否进行了工艺评定,并应有工艺评定报告及焊接工艺;
焊工是否持有焊工证,持证者是否在有效期内操作。
(2)、焊条烘焙:
对有烘焙要求的焊材,必须按说明书要求进行
烘焙。
经烘干的焊材放入保温箱内,随用随取。
(3)、预热:
在建筑钢结构的焊接施工中,必须根据钢种、板厚、
接头的约束度和焊缝金属中含氢量等因素,来决定预见热温度和方法。
预热区域范围应为焊接坡口两侧各80—100mm;预热时应尽可能使加
热均匀一致。
普通碳素结构钢厚度大于34mm和低合金结构厚度大于
或等于30mm,工作地点温度不低于0℃时,应加温至于100—150℃
进行进行预热。
钢材预热方法可选用火焰加热或电加热。
但对于钢材
2的焊接区域进行预热时,宜选用电加的屈服极限强度大于460N/mm
热方法,原则上禁用火焰加热。
钢材预热温度的测定方法一般在钢材加热的反面距焊缝中心线
50mm处测定。
、背面清根:
在电弧焊接过程中,当接头有全熔透要求时,)4(.
对于V形、单边V形、X形、K形坡口的对接和T形接头的情况下,
背面的第一层焊缝容易发生未焊透、夹渣和裂纹等缺陷。
这类缺陷原
则上要从背面彻底清除后再进行焊接,这种作业叫做清根。
特别在定
位焊缝处更容易产生缺陷,必须注意背面清根工作。
(5)、引弧与熄弧:
严禁在焊缝区以外的母材上打火引弧。
在坡
口内引弧的局部面积应熔焊一次,不得留下弧坑。
对接和T形接头的
焊缝、引弧和熄弧,应在焊件两端的引入板和引出板开始和终止。
(6)、焊接顺序和熔敷顺序:
焊接顺序和熔敷顺序是关系到减少
焊接变形的重要因素。
在选择焊接顺序和熔敷顺序时应注意几点:
①尽可能减少热量的输入,并必须以最小限度的线能量进行焊接
②不要把热量集中在一个部位,尽可能均等分散。
③采用“先行焊接产生的变形由后续焊接抵消”的施工方法。
○4平行的焊缝尽可能地沿同一焊接方向同时进行焊接;
⑤从结构的中心向外进行焊接;
⑥从板的厚处向薄处焊接。
焊接完毕后应清除熔渣及金属飞溅物,
应在焊缝附近打上钢印代号。
(7)、多层焊:
多层焊焊接接头应连续施焊一次完成,每一层焊
道焊完后应及时清理,如发现有影响焊接质量的缺陷,必须清除后再
焊。
对于重要结构处的多层焊必须采用多层多道焊,不允许摆宽道焊
接。
多层焊过程中的层间温度若无特殊要求一般应与预热时的温度相
同。
.
(8)、焊接结束后的处理:
焊接结束后的焊缝及其两侧,必须彻
底清除焊渣、飞溅和焊瘤等。
无特殊要求时,一般根据焊接接头的残
余应力、组织状态、熔敷金属含氢量和力学性能等决定是否需要焊后
热处理。
焊接结束后,如发现焊缝出现裂纹时,焊工不得擅自处理,
应申报焊接技术负责人查清原因后,订出修补措施,方可处理。
(9)、不合格焊缝的返修:
施焊过程中产生的缺陷,应立即进行
适当处理。
焊后检查出不合格的地方,应与技术主管部门协商解决,
无特殊要求时按以下处理:
在焊缝的缺陷处,进行清理后再焊接。
焊
缝中有裂纹时,将焊缝裂纹全长清除后再焊,若采用超声波等方法清
楚地查出裂纹的界限,应从裂纹两端延长50mm加以清除后再焊。
由
于焊接引起母材上出现裂纹时,原则上应更换母材,但当得到质量检
验部门的认可也可进行局部修补处理。
凡不合格焊缝修补后应重新进
行检查。
低合金结构钢在同一处的返修不得超过两次。
8、焊接H型钢
(1)、H型钢组装前要检查各件尺寸、形状及收缩加放情况,合格后
用砂轮清理焊缝区域,清理范围为焊缝宽的4倍。
(2)、在翼板上画出腹板位置线后,按线组装,要求组装精度为腹板
中心线偏移小于2mm,翼缘板与腹板不垂直度小于3mm,定位点焊。
(3)、H型钢,型钢组装合格后,用门型自动埋弧焊机采取对称焊接H
焊前要将构件垫平,防止热变型,按焊接工艺规范施焊。
(焊丝直径
)5mm?
4—为
(4)、H型钢变形矫正:
焊完后H型钢在矫正机上矫正,保证翼缘板
与腹板不垂直度小于3mm,腹板不平度小于2mm,检测要用直角尺与
塞尺。
(5)、组装H型钢与节点板、连接板:
节点板、连接板的组装要保证
基准线与梁中心对齐,其误差小于0.5mm。
梁柱焊缝采用二氧化碳气
体保护焊,焊丝直径?
1.2mm,焊后用氧乙炔火焰矫正(如扭曲、侧弯
等)焊接变形,然后检验记录单要求检验各项指标,直至符合标准为
止。
9、超声波探伤
(1)、超声波是一种人耳不可闻的每秒钟振荡频率在20KHz以上
的高频机械波,它是利用由压电效应原理制成的压电材料超声换能器
而获得的。
(2)、对接焊缝探伤,可从工件单面二侧进行扫查。
T型焊缝的
探伤可从面板或腹板上进行,由于在面板上探测时需在面板上画基准
线,增加了附加工作量,实际工作会造成一定困难,因此,可从腹板
一面单侧进行。
(3)、超声波探伤按GB11345-89《钢焊缝手工超声波探伤方法
和探伤结果分析》执行。
10、磨擦面处理
磨擦面处理方法有:
采用抛丸处理方法。
在运输过程中试件磨擦
面不得损伤。
处理好的磨擦面,不得有飞边、毛刺、焊疤或污损等。
.
应注意磨擦面的保护,防止构件运输、装卸、堆放、二次搬运、翻吊
时连接板的变形。
安装前,应处理好被污染的连接面表面。
处理好的
磨擦面放置一段时间后会先产生一层浮锈,安装时须用钢丝刷清除浮
锈。
接触面的间隙与处理:
由于磨擦型高强度螺栓连接方法是靠螺栓
压紧构件间连接板,用磨擦力来完成构件之间内力传递,规范要求75%
以上的接触面,边缘间隙不大于0.8mm。
11、抛丸除锈
(1)、采用HP8016B型通过式抛丸清理机对构件表面进行抛丸
除锈,使用的丸料,必须分离出去油污和水份,否则油污和水份在抛
射过程中附在表面上,影响涂层的均匀性和密实性。
(2)、经除锈后的构件表面,应用毛刷等工具清扫,或用干净的
压缩空气吹净锈尘和残余磨料,然后方可进行下道工序。
(3)、构件除锈经验收合格后,应在表面返锈前涂完第一道底漆。
一般在除锈完后,如存放在厂房内,可在6h(视环境湿度而定)涂完
底漆,存放在厂房外,则应在当班涂完底漆。
(4)、除锈合格后的构件表面,如在涂底漆前已返锈,需重新除
锈。
如果返锈不严重,一般只进行轻度抛射处理即可,同样也需经清
理后,才可涂底漆。
12、涂装
在下列情况下,一般不得涂装,如要涂装,需要有防护措施:
、在有雨、雾、雪和较大灰尘的环境下,禁止在户外施工。
)1.
2)、涂层可能受到尘埃、油污、盐分和腐蚀性介质污染的环境。
3)、施工作业环境光线严重不足时。
4)、没有安全措施和防火、防爆工具器具的情况下。
5)、空气相对湿度超过85%;施工现场环境温度低于0℃;钢材表
面温度未高于大气露点3℃以上。