QC七种工具.docx
《QC七种工具.docx》由会员分享,可在线阅读,更多相关《QC七种工具.docx(13页珍藏版)》请在冰点文库上搜索。
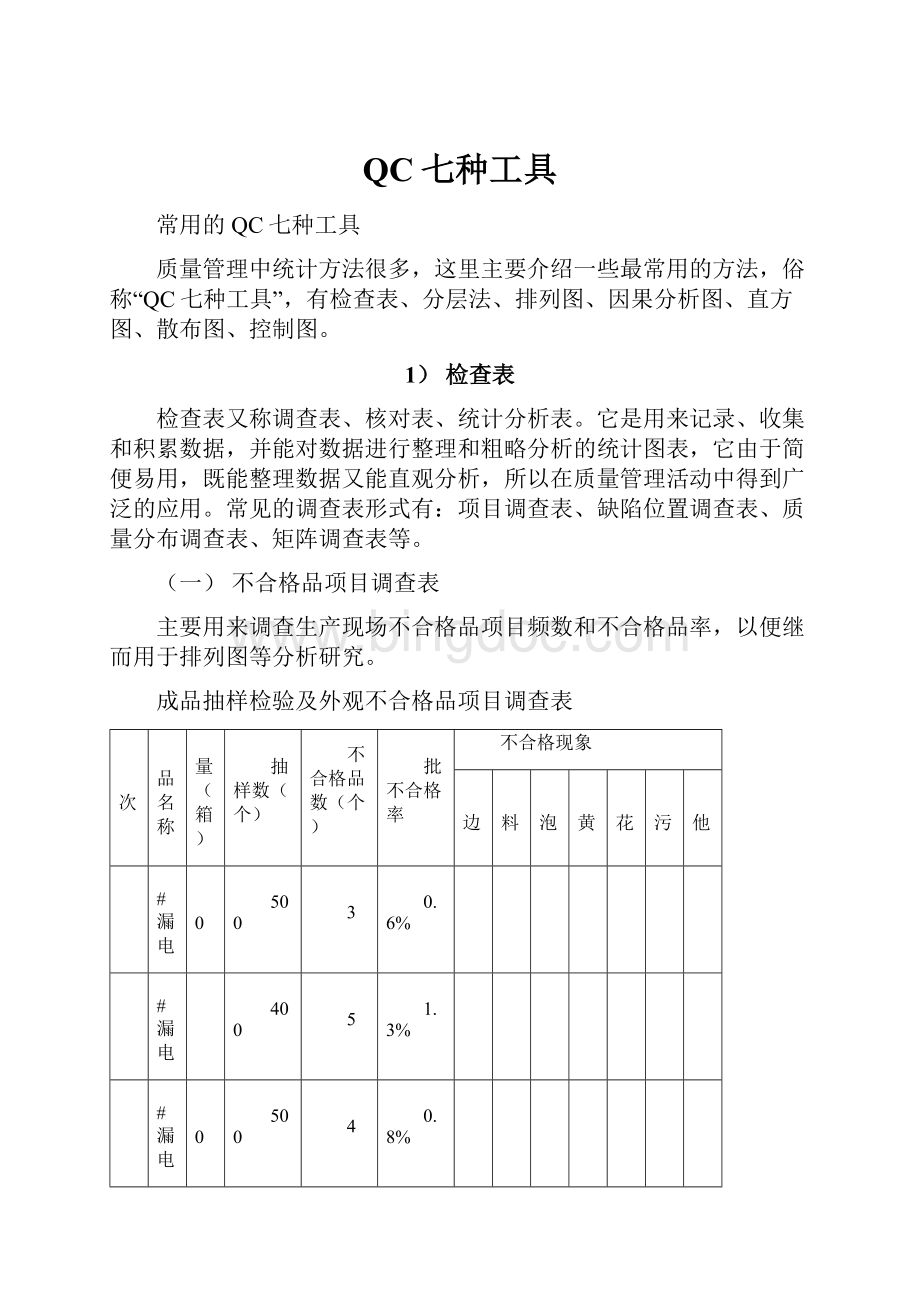
QC七种工具
常用的QC七种工具
质量管理中统计方法很多,这里主要介绍一些最常用的方法,俗称“QC七种工具”,有检查表、分层法、排列图、因果分析图、直方图、散布图、控制图。
1)检查表
检查表又称调查表、核对表、统计分析表。
它是用来记录、收集和积累数据,并能对数据进行整理和粗略分析的统计图表,它由于简便易用,既能整理数据又能直观分析,所以在质量管理活动中得到广泛的应用。
常见的调查表形式有:
项目调查表、缺陷位置调查表、质量分布调查表、矩阵调查表等。
(一)不合格品项目调查表
主要用来调查生产现场不合格品项目频数和不合格品率,以便继而用于排列图等分析研究。
成品抽样检验及外观不合格品项目调查表
批次
产品名称
批量(箱)
抽样数(个)
不合格品数(个)
批不合格率
不合格现象
飞边
缺料
气泡
发黄
水花
脏污
其他
1
4#漏电
10
500
3
0.6%
1
1
1
2
4#漏电
8
400
5
1.3%
2
1
1
1
3
4#漏电
10
500
4
0.8%
3
1
----
----
----
----
----
----
50
4#漏电
10
500
6
1.2%
4
1
1
合计
400
22500
168
0.7%
40
68
22
9
18
6
5
调查者:
王XX
日期:
____年___月___日
地点:
注塑车间
(二)缺陷位置调查表
许多产品或零件常存在气孔、疵点、碰伤、脏污等外观质量缺陷。
缺陷位置调查表可用来记录、统计、分析不同类型的外观质量缺陷所发生的部位和密集程度,进而从中找出规律性,为进一步调查或找出解决问题的办法提供事实依据。
这种调查分析的做法是:
画出产品示意图或展开图,并规定不同外观质量缺陷的表示符号。
然后逐一检查样本,把发现的缺陷,按规定的符号在同一张示意图中的相应位置上表示出来。
这样,这张缺陷位置调查表就记录了这一阶段(这一批)样本的所有缺陷的分布位置、数量和集中部位,便于进一步发现问题、分析原因、采取改进措施。
下图是反映橡胶手套各部位破损频数的缺陷位置调查表,“*”表示破损发生的位置:
(实际就是在实物图形上直接标出)
(三)质量分布调查表
质量分布调查表是对计量数据进行现场调查的有效工具。
它是根据以往的资料,将某一质量特性项目的数据分布范围分成若干区间而制成的表格,用以记录和统计每一质量特性数据落在某一区间的频数。
见下表是一张某零件重量实测值分布调查表。
从表格的形式看,质量分布调查表与直方图的频数分布表相似。
不同点:
质量分布调查表的区间范围是根据以往资料,首先划分区间范围,然后制成表格,以供现场调查记录数据;而频数分布表则是首先收集数据,再适当划分区间,然后制成图表,以供分析现场质量分布状况之用。
零件实测值公布调查表
调查人:
张某调查日期:
02年5月18日
调查数(N):
121件调查方式:
根据原始凭证统计
2)分层法
分层法就是根据使用目的将数据总体用合适的分类标准进行分类的方法。
它是数据收集和处理的最常用的方法,它可以使毫无头绪的错综复杂的因素条理化、系统化。
因此,在进行质量问题分析时,此方法便于找出主要的质量问题原因,以便采取适宜的措施较好地解决问题。
在此方法的实际应用中,常用的分层标准有:
(1)操作者的特征,诸如年龄、性别、技术水平、工种等;
(2)生产设备,如机床、工艺设备等;
(3)操作方法,指操作规程、工序名称;
(4)原材料,包括供应商、批次、成分;
(5)检验条件,包括检验员、检测仪器、检测方法等;
(6)时间,如日期、班次;
(7)环境条件,包括地区、气温、气压、湿度等。
为了说明这个问题,某柴油机厂在柴油机装配过程中经常出现漏气现象,为找出漏气的原因,抽检了50台柴油机,发现20台漏气,漏气率为40%。
经初步分析,。
经初步分析,认为导致漏气的原因主要二两个:
1、该工序中工人的操作方法有差异;2、装配时所用的某零件的性能有差异。
为弄清具体原因,运用分层法分别按操作和零件供应商分层进行统计分析,如下表所示:
按操作者统计分析按供应商统计分析表
操作者
漏气数
不漏气数
漏气率
供应商
漏气数
不漏气数
漏气率
甲
乙
丙
4
6
10
16
9
5
20%
40%
67%
A
B
C
2
10
8
14
10
6
12%
50%
57%
合计
20
30
40%
合计
29
30
40%
从上面两表中可以看出,为了降低柴油机漏气率可以采用如下措施:
1.推广甲的操作方法;2.在采购中多从A供应商处订货。
运用分层法进行数据分层往往可以按几个不同的层别而分别得到某一方面的结论。
但这样会隔绝不同层数据之间内在联系,不能反映出不同层别因素之间的相关性。
这样孤立分层分析有时会得出错误结论,在应用中应该注意这点。
为了避免这种错误结论,就必须将关联的因素综合进行考虑。
再用上例数据,得到如一综合统计分析表:
供应商
操作者
A
B
C
不漏气数
漏气数
漏气率
不漏气数
漏气数
漏气率
不漏气数
漏气数
漏气率
甲
7
0
0%
8
1
11.1%
1
3
75%
乙
6
0
0%
0
3
100%
1
3
75%
丙
1
2
66.7%
2
6
75%
2
2
50%
合计
14
2
12.5%
10
10
50%
6
8
57.1%
3)排列图
现场质量管理往往有各种各样的问题,我们应从何下手?
如何抓住关键?
一般说来,任何事物都遵循“关键的少数,次要的多数”的客观规律。
例如,大多数废品由少数人员造成,大部分设备故障停顿时间由少数故障造成,大部分销售额由少数用户占有等。
这一规律首先由意大利经济学家帕累托提出,并设计出一种能反映出这种规律的图,称为帕累托图(ParetoChart),又很贴切地译称为排列图。
米兰又认为企业80%的问题是20%的原因形成的,这又进一步推广了帕累托的成果。
排列图是找现影响产品质量主要因素的一种有效统计工具。
排列图一般如下图所示,由两纵坐标、一横坐标、一组方块、一条折线组成。
左侧是度量质量问题大小的纵坐标、既可表示质量问题出现的频率,又可表示由质量问题引发的费用损失。
右侧是表示累计百分比坐标、横坐标表示对质量问题有影响的项目或因素,并依据影响大小自左向右排列。
其高度表示各影响因素的大小。
折线为排列线,即帕累托线,其折点表示该点以前各因素影响的累计百分比。
因素分析时,通常把因素分为三大类,即包括在累计百分比0~80%、80~90%、90~100%的因素分别称为A、B、C类因素。
A类是主要因素,B类是次要因素,C类是一般因素。
下面结合实例说明排列图的具体作法。
事例:
为提高产品质量,对5月份生产的不合格品进行分类缺陷统计,按缺陷项目统计不合格数据,用排列图对此问题进行分析。
(1)收集数据
针对所存在的问题收集一定时间的数据,此期间不可过长,以免统计对象有变动;也不可过短,以免只反映一时情况而不全面。
然后将数据按原因、工序、人员、部位或内容等进行分类,并统计各项目的个数,即频数。
参见下表。
公司五月份成品质量统计
№
项目
频数
频率
累计
1
飞边
326
50.94%
50.94%
2
缺料
159
24.84%
75.78%
3
水花
70
10.94%
86.72%
4
发黄
30
4.69%
91.41%
5
气泡
25
3.91%
95.31%
6
脏污
10
1.56%
96.88%
7
其他
20
3.13%
100.00%
合计
640
100.00%
(2)数据计算
数据收集后,要按表的方式计算,表中各项影响因素要按影响大小顺序由大到小排列。
参见上表。
(3)作排列图
以左侧纵坐标为频数,横坐标按频数从大到小依次列出各项影响因素,将频数用直方表示;以右侧纵坐标为频率(即比率),依次将各工序的累计比率用折线表示。
成为若干个直方相连由左至右逐个下降,一折线由左至右逐个上升的图,即排列图,见上图。
(4)确定主次因素
根据因素分析的一般原则将累计百分比为0~80%、80~90%、90~100%的三个范围分别划分为A、B、C类因素。
本例由上图可以看出只要解决“飞边”及“缺料”问题,不合格率就会降低75.78%。
4)因果分析图
因果分析图法(Cause-and-EffectDiagram),也叫做石川图(IshikawaDiagram)或鱼骨图(Fish-BoneChart)。
它以结果作为特性,以原因作为因素,彼此间用箭头联系来表示因果关系。
因果分析图是一种发动员工动脑筋、找原因、集思广益的好办法,也特别适合于工作小组中民主管理,当出现某种质量问题,在没有弄清楚原因之前,可以就问题发动所有相关人员寻找可能的原因,把所有的原因都列出来,按其相互关系归纳整理、用箭头线反映在一幅图上。
因果图由质量问题和原因两部分组成,主干箭头所指的为质量问题。
主干上的大骨表示影响质量诸原因的基本分类,中骨、小骨、细骨等表示该原因从上层次到下层次的依次展开,
应用步骤:
1)明确分析对象,确定待分析的质量问题,将其定在图的顶端;
2)确定该质量问题中各原因的分类方法,将各基本分类标在大骨旁边;
例如:
分析工序加工质量问题时,可按其主要影响因素——人、机、料、法、环(4M1E)等分类,也可按照加工步骤如开线、压接、装配等分类。
3)召集与该质量问题有关的人员,参加“诸葛亮”会,充分发动群众,发扬民主,各抒己见,集思广益,找出各大原因的中原因、小原因、小小原因,并用箭头线标到所属的位置上。
4)从最高层次(即最末的一层)的原因(末端因素)中选取和识别少量(一般为3~5个)看起来对结果有最大影响的原因(一般称重要因素,简称要因),并对它们做进一步的研究,如收集资料料、论证、试验、采取措施、控制等。
下图是关于焊接质量差的因果分析图:
使用因果图注意事项:
1、画因果图时必须开“诸葛亮会",充分发扬民主,各抒已见,集思广益,把每个人的意见都客观地一一记录在图上。
2、确定要分析的主要质量问题(特性)不能笼统,一个主要质量问题只能画一张因果图;多个主要质量问题则应画多张因果图。
因果图只能用于单一目标的分析。
3、因果关系的层次要分明,最高层次的原因应寻求到可以直接采取具体措施为止。
4、“要因”一定要确定在末端因素(最高层次因素)上,而不应确定在中间过程上。
5、对末端因素,特别是“要因"应科学论证。
5)直方图
所谓直方图,就是将收集到的数据按其大小等间距地分成若干组,以组距为底边,以组内数据的个数为高做直方块而绘的图。
它是表示数据变化的一种常用工具,可以较直观地反映产品质量的分布状态。
可以判断工序是否处于受控状态,还可对总体进行批准、判断总体质量的分布状况。
在制作直方图时,首先要对数据进行分组,因此如何进行合理分组是最为关键的问题。
作直方图的目的是根据直方图的形状判断生产过程是否稳定及生产的质量如何。
为此须对直方图作正确的观察。
常见的直方图分布状态有如下几种:
1正常型。
特征为中部有个峰,两侧基本对称。
符合中间大两头小。
实际是正态分布状况,表明工序正常稳定。
2偏向型。
特片为图形偏向一侧,这种分布形成的原因多由操作者的习惯形成。
3锯齿型。
如果作图时的数据太少,而且分组又过多,或组距没有取最小单位的整数倍时常会出现此类情形,一般不是工序本身的原因。
4平顶型。
由某些缓慢变化的系统原因造成。
系统原因是指随工序长期反复进行,必定发生的误差。
5双峰型。
这类图形的特征是图中出现明显的两个顶峰,在两个顶峰之间是个谷,两侧的频数较低。
出现这种图形的原因多为数据分层不当,使得不同分布的数据混在一起所致。
6孤岛型。
这类图形的特征是质量特性值出现间断。
出现这类图形的原因可能是加工条件有变化。
如原因质地有变化,机床精度变化或工人熟练程度变化等。
6)散布图
散布图,又称散点图或相关图,是用来研究两个对应变量之间是否存在相关关系的一种作图方法。
例如,塑胶件成型时的注塑压力与尺寸、铜带的硬度与强度、员工的持续工作时间与产品质量等。
其优点在于直观简便。
它的做法是将两个由实验或搜集到的可能相关的变量数据用点描在坐标图上,通过观察分析其相关性。
散布图有六种典型形式:
(1)强正相关
一质量特征量变大时,另一质量特征量也有较大变大。
在这种形式下,控制住了一个变量,另一个变量也得到了控制。
如输电线路的电力损耗与线路上电流之间的关系,若能控制住电流大小,也就控制住了电力损耗大小。
(2)强负相关
两质量特征量之间关系表现为一个变量变大则另一质量特性量变小,仍以输电线路为例,输电线路在总负荷不变的条件下,输电线路电压越高,则电力损耗越小。
(3)弱正相关
其特征是一个质量特征量较大的变化会引起另一个质量特征量发生较小的同方向变化,在这种情况下,除考虑此因素的影响外,还须考虑其它因素的影响。
一般都可进行分层处理,寻找此影响因素之外的其它影响因素。
(4)弱负相关
此类相关性两质量特征量之间关系表现为一个质量特征量较大的变化会引起与其弱负相关因素较小的相反方向的变化。
这种情况下也可以进行要层处理,寻找其它影响因素。
(5)不相关
即一个质量特征量的变化不会引起另一个质量特征量的任何变化。
(6)非线性关系
其特征是两质量特征量之间变化在不同状态下有不同的方向。
7)控制图
控制图是一种用来分析和判断过程是否处于稳定状态所使用的过程管理图。
其作用是用来区分引起质量波动的原因是偶然的还是系统的。
控制图有两类:
一类用于分析生产过程中有关质量特性的变化情况,以判断工序是否处于稳定状态;另一类用于判断生产是否出现了异常情况。
控制图中,纵坐标表示样本的质量特性值,如螺栓的直径;横坐标表示受检样本的编号;上限线表示产品质量特性值的最大允许值;下限线则表示产品质量特性值的最小允许值;中心性是目标值,若样本特性值高于上限线或低于下限线,则表明工序处于不稳定状态。
控制图的种类:
1.按统计量分类
即按测定值性质的不同,控制图大致可分计量值控制图和计数值控制图两大类。
常用的各种控制图的特点和适用场合见下表:
控制图适用场合
类别
名称
控制图符号
特点
适用场合
计
量
值
控
制
图
平均值-极差控制图
最常用,判断工序是否正常效果好,但计算工作量大
适用于产品批量较大,且稳定、正常的工序
中位数-极差控制图
计算简便,但效果较差
同上
单值-移动极差控制图
简便省事,并能及时判断工序是否处于稳定状态。
缺点是不易发现工序分布中心的变化
因各种原因(时间、费用等)每次只能得到一个数据或希望尽快发现并消除异常因素
计
数
值
控
制
图
不合格品数控制图
Pn
较常用,计算简单,操作工人易于理解
样本数量相等
不合格品率控制图
P
计算量大,控制线凹凸不平
样本数量可以不相等
缺陷数控制图
C
较常用,计算简单,操作工人易于理解
样本数量相等
单位缺陷数控制图
U
计算量大,控制线凹凸不平
样本数量相等
2.按照用途分类
(1)分析用控制图
用全数连续取样的方法获得数据,进而分析、判断工序是否处于稳定状态。
利用控制图发现异常,通过分层等方法,找出不稳定的原因,采取措施加以解决。
(2)控制用控制图
按程序规定的取样方法获得数据,通过打点观察,控制异常原因的出现。
当点子分布出现异常,说明工序质量不稳定时,找出原因,及时消除异常影响因素,使工序恢复到正常的控制状态。