壳体工艺流程毕业设计说明书毕业论文Word文件下载.docx
《壳体工艺流程毕业设计说明书毕业论文Word文件下载.docx》由会员分享,可在线阅读,更多相关《壳体工艺流程毕业设计说明书毕业论文Word文件下载.docx(30页珍藏版)》请在冰点文库上搜索。
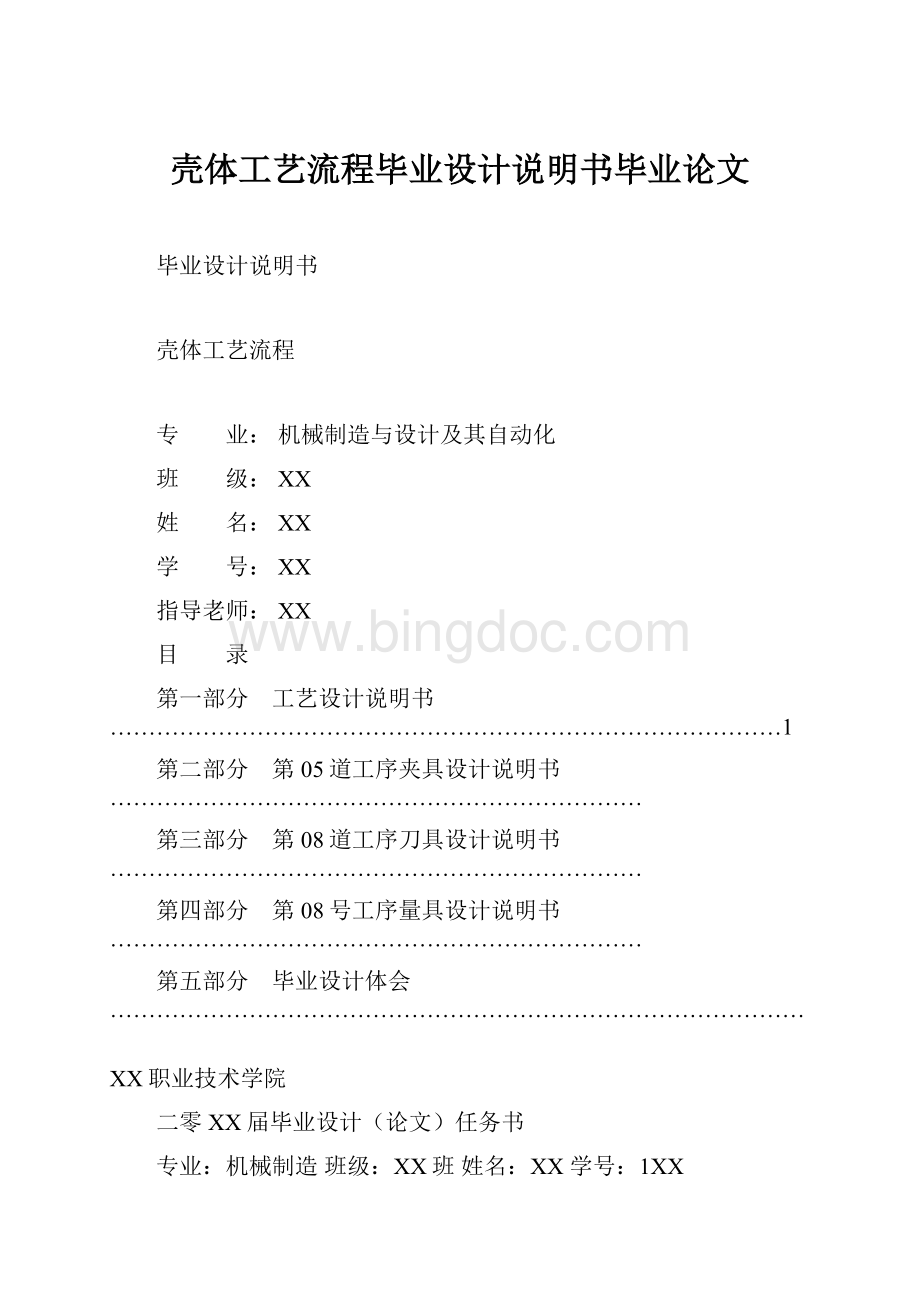
㈤设备及其工艺装备的确定
㈥切削用量及工时定额确定:
确定全部工序切削用量及工时定额。
㈦工艺文件制订:
1、编写工艺文件设计说明书:
2、编写工艺规程:
㈧指定工序机床夹具设计
1、工序图分析;
2、定位方案确定;
3、定位误差计算;
4、夹具总装图绘制;
㈨刀具、量具设计
四设计任务(工作量):
1、零件机械加工工艺规程制订设计说明书一份;
2、工艺文件一套(含工艺流程卡片、某一道工序的工序卡片、全套工序附图);
3、机床夹具设计说明书一份;
4、夹具总装图一张(A2图纸);
零件图两张(A4图纸);
5、刀量具设计说明书一份;
6、刀具工作图一张(A4图纸);
量具图一张(A4图纸)。
五起止日期:
2006年11月28日——2007年1月20日(共8周)
六指导教师:
黄雨田
七审核批准
教研室主任:
系主任:
八设计评语:
年月日
九设计成绩:
年月日
第一部分 工艺设计说明书
1.零件图工艺性分析
1.1零件结构功用分析:
壳体零件是机械中常见的一种零件,通常起支承作用。
它的应用范围很广,例如支承旋转轴上的轴承,等等。
由于它们功用的不同,壳体类零件的结构和尺寸有着很大的差异,但结构上仍有共同特点:
零件的主要表面为精度要求较高的轴承孔、零件由内孔、外圆、凸台、等表面构成。
1.2零件图纸分析:
由零件图可知,该零件形状较为复杂、外形尺寸不大,可以采用铸造毛坯。
由于该零件的两个φ28孔与轴承配合,它的表面质量直接影响两轴承的旋转精度与工作状态,,通常对其尺寸要求较高。
一般为IT5-IT7。
加工时两φ28孔的同轴度应该控制在0.01mm。
65
0.为孔的位置尺寸它直接影响孔在空间的位置,加工时可以将其加工精度降低,通过装配来提高精度。
1.3主要技术条件:
1.孔径精度:
两φ28孔的孔径的尺寸误差和形状误差会造成轴承与孔的配合不良,因此对轴承座孔的要求较高,其孔的尺寸公差为IT7,轴承座孔的形状精度一般控制在尺寸公差范围内即可。
2.孔的位置精度:
同一轴线上各孔的同轴度误差和孔端面对轴线的垂直度误差会使轴承装配到轴承孔内出现歪斜,从而造成径向跳动和轴向跳动,加剧了轴承的磨损,为此一般同轴上各孔的同轴度为最小孔尺寸公差之半。
3.主要平面的精度:
由于φ70底面的平面度直接影响联接时的接触刚度,并且加工过程中常作为定位基面,则会影响孔的加工精度,因此须规定底面必须平直。
2.毛坯选择
2.1毛坯类型
考虑到壳体工作时起支承轴承,要求材料要有很高的强度,并且该零件结构较为复杂,故选用铸造毛坯材料为HT200。
2.2毛坯余量确定
由书机械加工工艺设计资料表1.2-10查得毛坯加工余量为5,毛坯尺寸偏差由表1.2-2查得为
1.4.
2.3毛坯-零件合图草图
3.机械工艺路线确定
3.1定位基准的选择:
3.1.1精基准的选择:
选择壳体底面与两φ7孔作定位基准,因为φ25f7外圆柱面,及底面是装配结合面,且壳体底面又是轴承座孔空间位置的设计基准,故选择壳体底面与两φ7孔作定位基准,符合基准重合原则且装夹误差小。
3.1.2粗基准的选择:
以壳体上端面和壳体支撑外圆弧定位加工出精基准。
3.2加工顺序的安排:
壳体零件主要由孔和平面构成与箱体类零件大体相同,加工顺序为先面后孔,这样可以用加工好的平面定位再来加工孔,因为轴承座孔的精度要求较高,加工难度大,先加工好平面,再以平面为精基准加工孔,这样即能为孔的加工提供稳定可靠的精基准,同时可以使孔的加工余量较为均匀
3.3段的划分说明
加工阶段分为:
粗加工阶段、半精加工阶段、精加工阶段。
3.4加工工序简图
1、铸铸造、清理
2、热处理时效
3、粗车、半精车、精车:
4粗铣φ12凸台顶面:
5.钻2-φ7孔:
6.去毛刺:
7.φ40外圆两端面;
8.粗镗2-φ25内孔、半精镗、精镗2-φ28内孔:
9.检验:
10.钻、攻M5螺纹孔:
11.钻、攻3-M4螺纹孔:
12.钻、攻2-M7螺纹孔:
13.锪2-φ12沉头孔:
14.去毛刺:
15.终检:
4.工序尺寸及其公差确定
φ25f7
工艺路线
基本尺寸
工序余量
经济精度
工序尺寸
铸
φ30.5
5.5
1.4
粗车
φ27
3.5
12.5(IT11)
φ26.5
半精车
φ25.5
1.5
6.3(IT9)
精车
φ25
0.5
1.6(IT7)
φ28JS7
φ22
6
粗镗
3
6.3(IT11)
半精镗
φ27.5
2.5
3.2(IT9)
精镗床
φ28
0.01
5.设备及其工艺装备确定
所用的设备有:
CA6140、X62W、Z3025B×
10、X6120、T68、Z4012、验台、钳工台。
夹具有:
V形块、钻2-φ7孔专用夹具、车床专用夹具、一面两孔夹具、心轴、
刀具有:
90度车刀、硬质合金铣刀、φ7钻头、平板锉、开式自锁夹紧镗刀、φ5钻头、M5丝锥、φ4钻头、M4丝锥、φ7钻头、M7丝锥、圆锉刀
量具有:
游标卡尺、专用塞规。
6.切削用量及工时定额确定
(1)粗车、半精车、精车时:
(T1=T辅T2=T机T3=T工T4=T休)
1.粗车φ70底面时:
(车刀刀杆尺寸BXH取25X25)ap=2.5
由表5.3-1得:
:
f=1.0mm/r
由表5.3-20得:
v=59m/min
则n=318x59/70=268r/mm
工时定额:
由表3.3-1得:
装夹工件时间为0.42min
由表3.3-2得:
松开卸下工件时间为0.12min
由表3.3-3得:
操作机床时间为:
0.02+0.04+0.03+0.07+0.06+0.02+0.01+0.02+0.03+0.04=0.64min
由表3.3-4得:
测量工件时间为:
0.08+0.08=0.16min
T1=0.42+0.12+0.64+0.08=1.2min
由表5.4-1得机动时间为:
T2=0.07+0.05+0.02+0.03=0.17min
由表3.3-33得布置工作地、休息和生理时间分别为:
T3=56min、T4=15min
T基=lz/nfap=100x3.5/268x1x2.5=0.52min
则T总=T1+T2+T3+T4+T基=75min
2.半精车φ70底面时:
(车刀刀杆尺寸BXH取25X25)ap=1
f=0.7mm/r
v=80mm/r
则n=318x80/70=363.4r/mm
T1=0.64+0.16=0.8min
T基=lz/nfap=100x3.5/363.4x1x0.7=1.38min
则T总=T1+T2+T基=2.26min
3.粗镗环形槽:
(车刀刀杆尺寸BXH取25X25)ap=2
f=0.4m/r
v=90m/r
则n=318x90/40=715.5r/mm
T2=0.05+0.02+0.03=0.1m/r
T基=lz/nfap=0.2min
4.粗车φ25外圆时:
(车刀刀杆尺寸BXH取16X25)ap=2
由表3-1得:
f=0.5m/r
v=82m/r
则n=318x82/25=1043m/r
T基=lz/nfap=0.167min
则T总=T1+T2+T基=0.347min
5.半精车φ25外圆时:
(车刀刀杆尺寸BXH取16X25)ap=1
f=0.4m/r
v=100m/r
则n=318x100/25=1227m/r
T基=lz/nfap=0.34min
则T总=T1+T2+T基=0.52min
6.精车φ25外圆时:
(车刀刀杆尺寸BXH取16X25)ap=0.5
f=0.3m/r
v=107m/r
则n=318x107/25=1361m/r
T基=lz/nfap=0.857min
则T总=T1+T2+T基=1.75min
7.粗车φ25端面时:
v=74m/r
则n=318x74/25=941.2m/r
则T总=T1+T2+T基=1.1min
T总=T总1+T总2+T总3+T总4+T总5+T总6+T总7=82.07min
(2)铣φ12凸台顶面时:
切削用量:
ap=3.5
由表6.3-2得:
f=0.2m/r
由表6.3-21得:
v=120m/r
则n=318V/D=318x120/30=1272m/r
由表6.4-1得:
T2=lw+lf/fxn=1.45min
由表3.3-7得:
0.83min
由表3.3-8得:
0.14min
T1=2.27minT3=51minT4=15min
T基=lz/nfap=0.5min
则T总=T1+T2+T基=68.7min
(3):
钻2-φ7孔时;
由表7.3-1得:
f=0.36m/r
由表7.3-11得:
v=13m/r
则n=318V/D=318x13/7=590m/r
T2=lw+lf/fxn=0.1min
由表3.3-9得:
装夹工件时间为0.17min
由表3.3-10得:
松开卸下工件时间为0.15min
由表3.3-12得:
0.04min
T1=0.76minT3=47minT4=15min
则T总=T1+T2+T基=62.9min
(4):
粗铣、半精铣φ40两端面时;
粗铣时:
ap=2.5
由表6.3-21硬质合金铣刀铣削灰铸铁时v=120m/r
则n=318V/D=763.2m/r
T2=lw+lf/vf=2.63min
精铣时:
ap=1
f=0.12m/r
由表6.3-21硬质合金铣刀铣削灰铸铁时v=150m/r
则n=318V/D=954m/r
T2=lw+lf/vf=3.5min
操作时间为0.83min
0.14min
T1=2.27minT3=51minT4=15min
则T总=T1+T2+T基=80.53min
(5):
粗镗φ25内孔、半精镗、精镗φ28内孔时;
粗镗时:
ap=3
由表8.2-1得:
f=0.5m/rv=80m/r
则n=318V/D=1017.6m/r
T2=lw+lf/vf=0.03min
半精镗时:
f=0.2m/rv=100m/r
则n=318V/D=1272m/r
T2=lw+lf/vf=0.04min
精镗时:
ap=0.5
f=0.15m/rv=80m/r
则n=318V/D=1017.6m/r
T2=lw+lf/vf=0.07min
松开卸下工件时间为0.12min
0.16min
T1=1.34minT3=56minT4=15min
则T总=T1+T2+T基=72.62min
(6):
钻、攻M7螺纹孔时;
f=0.27m/r
v=15m/r
则n=318V/D=318x15/5=954m/r
T2=lw+lf/fxn=1.5min
装夹工件时间为0.04min
松开卸下工件时间为0.05min
由表3.3-11得:
0.32min
T1=0.43minT3=47minT4=15min
则T总=T1+T2+T基=62.73min
(7):
钻、攻3-M4螺纹孔时;
ap=2.
则n=318V/D=318x15/5=1192m/r
T2=lw+lf/fxn=2.1min
则T总=T1+T2+T基=63.93min
(8):
钻、攻2-M7螺纹孔时;
则n=318V/D=318x15/5=618.4m/r
则T总=T1+T2+T基=63.23min
(9):
锪2-φ12沉头孔时时;
则n=318V/D=318x15/5=397.5m/r
T2=lw+lf/fxn=1min
则T总=T1+T2+T基=62.63min
第二部分 第5道序夹具设计说明书
1.工序尺寸精度分析
由工序图可知此工序的加工精度要求不高,具体加工要求如下:
钻2-φ7孔,无其它技术要求,该工序在摇臂钻床上加工,零件属中批量生产。
2.定位方案确定
根据该工件的加工要求可知该工序必须限制工件五个自由度,即x移动、x转动、y转动、y移动、z转动,但为了方便的控制刀具的走刀位置,还应限制z移动,因而工件的六个自由度都被限制,由分析可知要使定位基准与设计基准重合。
选φ25外圆、底平面、为定位基准,以φ40外圆端面定位限制z转动。
(见工序图)
3.定位元件确定
1、选择定位元件:
由于本工序的定位面是φ25外圆、底平面、φ40外圆端面,所以夹具上相应的定位元件选为一个定位孔和两个平面。
2、确定定位元件尺寸、极限偏差和定位元件间位置尺寸及其极限偏差、定位元件尺寸:
由图可知此工序的加工精度要求不高,所以定位孔的尺寸由机床夹具设计手册知选用φ25H7/f7
3.定位误差分析计算
(1)分析计算孔的深度尺寸7的定位误差:
用φ25外圆表面定位,工件定位面是外圆表面,定位元件的定位工作面是φ25外圆面,定位基准是外圆母线,当工件外圆直径发生变化时其中心线在定位孔内左右移动。
定位误差计算如下:
△jb=1/2T(d)=1/2x0.021=0.0105
△db=1/2(△D+△d+△min)=(0.021+0.015+0.023)/2=0.0295
△dw=△jb+△db-=0.04≤T/3所以满足要求。
4.夹紧方案及元件确定
(1)计算切削力及所需加紧力:
工件在加工时所受的力有加紧力J、切削力F和工件重力G,三者作用方向一至,由机床夹具设计手册表1-2-7得切削力的计算公式:
Fx=667Ds
Kp=667x7x700
x650/726≈1083N
实际所需加紧力与计算加紧力之间的关系为:
F=KFx(K由表1-2-2查得为1.15)=1.15Fx==1245.45N
(2)设计钻套,连接元件及夹具体,钻模板:
由于此工件是中批量生产,固选用GB2264-80可换钻套,选用活动式钻模板。
根据钻床T型槽的宽度,决定选用GB2206-80宽度B=14,公差带为h6的A型两个定位键来确定夹具在机床上的位置。
夹具体选用灰铸铁的铸造夹具体,其基本厚度选为15mm,并在夹具体底部两端设计出供T型槽用螺栓紧固夹具用的U型槽耳座。
5.夹具总装草图
第三部分 第8道工序刀具设计
(精镗φ28JS7公差等级为IT7内孔)
1.刀具类型确定
此道工序保证的尺寸精度要求较高φ28内孔端面必须垂直,因此须90度闭孔镗刀。
2.刀具设计参数确定
序号
项目
数据来源或公式计算
采用值
1
刀具类型
表2-6、2-7
焊接式90度闭孔镗刀
2
刀片材料
YT5
刀杆材料
45钢
几何角度
表2-7、2-8、2-9
Λs=-4度γo=15度
αo=8度αo’=6度κr=90度κr’=56度γε=2mm
4
断削参数前面型式
表2-11、2-12(f=1.3mm/r)
带倒棱曲面圆弧卷削槽前面
Ln=3.5mγo1=-5度br1=0.045qn=2
5
过渡刃
表2-13(ap=0.5mm)
过渡刃和修光刃bε=0.18
刀片型号
表2-3
A416
L=16B=10C=5.5R=10
7
镗刀外型结构尺寸
表3-5(刀具设计手册)
DxL=10x100M=5
3.刀具工作草图
第四部分 第8道工序量具设计说明书
对轴承座孔φ28(JS7),首先确定被测孔的极限偏差,查公差书第三章极限与配合标准得φ28JS7的上偏差ES=+0.01mm,下偏差EI=-0.01mm。
公差等级为IT7。
1.量具类型确定
轴承座孔φ28的量具用塞规。
2.极限量具尺寸公差确定
(1)确定工作量规的制造公差和位置要素值,由公差书表6-1得IT7尺寸φ28的量规公差为T=0.0024mm,位置要素Z=0.0034mm.。
(2)计算工作量规的极限偏差:
φ28JS7孔用塞规:
通规:
上偏差=EI+Z+T/2=(-0.01+0.0034+0.0012)=-0.0054mm
下偏差=EI+Z-T/2=(-0.01+0.0034-0.0012)=-0.0078mm
磨损极限=EI=-0.01mm
止规:
上偏差=ES=+0.01mm