《技术标准》设备检修规程.doc
《《技术标准》设备检修规程.doc》由会员分享,可在线阅读,更多相关《《技术标准》设备检修规程.doc(629页珍藏版)》请在冰点文库上搜索。
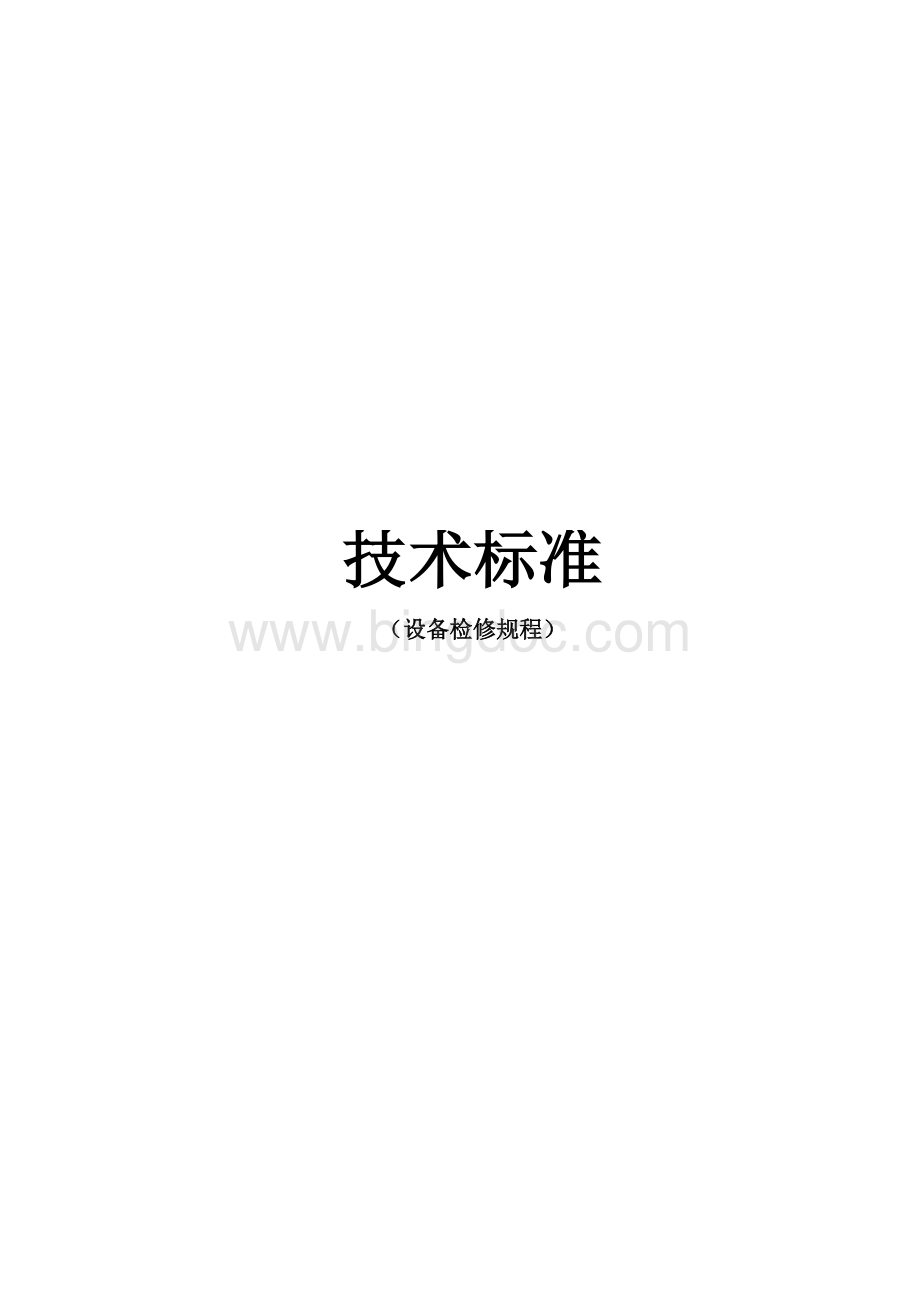
技术标准
(设备检修规程)
目录
1水轮机、发电机(机械部分)维护检修规程 1
2发电机(电气部分)检修规程 32
3主变压器检修规程 50
4调速器(机械)检修规程 63
5调速器(电气)检修规程 84
6继电保护及自动装置检修规程 101
7计算机监控系统检修规程 183
8机组励磁设备检修规程 211
9干式变压器检修规程 225
10110KV开关站设备检修规程 232
1110KV系统开关检修规程 239
12400V系统检修规程 246
13直流系统设备检修规程 256
14通讯系统检修规程 265
15工业电视系统设备检修规程 279
16空压机检修规程 288
17电梯检修规程 297
18清污机检修规程 318
19水泵检修规程 333
20弧门检修规程 350
21机组流道闸门启闭机检修规程 359
22桥式起重机检修规程 378
23船闸检修规程 399
24水情测报系统检修规程 419
25水工建筑物维护规程 433
26油泵检修规程 464
27滤油机检修规程 468
28发电机冷却水分析试验规程 481
29油质分析试验规程 495
30电动机检修规程 500
31热工仪表检修规程 527
32电力电缆检修规程 538
33柴油发电机(机械部分)检修规程 553
34柴油发电机(电气部分)检修规程 565
35电测仪表检修规程 579
36电气设备现场试验规程 593
37水工建筑物观测规程 620
1水轮机、发电机(机械部分)维护检修规程
Q/*****-JS-JX01-2017
1主题内容与适用范围
1.1本规程规定了***水电厂灯泡贯流式水轮机和发电机组的检修周期、检修内容及检修工艺要求。
1.2本规程适用于***水电厂灯泡贯流式水轮机和发电机组的检修维护及验收工作。
2引用标准
下列标准或资料包含的条文,通过在本标准中引用而构成本标准的条文。
2.1厂家提供的原始资料。
2.2DLT5038-94《灯泡贯流式水轮发电机组安装工艺导则》
2.3DL/T1066—2007水电站设备检修管理导则
3技术参数
3.1水轮机主要技术参数
型号:
K89/4Ⅱa设计水头:
6.55m
最大水头:
12.5m最小水头:
3m
设计水头下流量:
312m3/s额定出力:
18050kW
最大出力:
19100kW额定转数:
75r/min
飞逸转数:
205r/min转动惯量:
550T·M2
正向水推力:
2080kN反向水推力:
4905kN
最高效率:
95%中心线高程:
▽42.1m
吸出高度:
-5.1m
3.2发电机主要技术参数
型号:
SV588/80-195持续功率:
19500kVA
额定电压:
10.5kV电压范围:
±5%
额定电流:
1072A功率因数:
0.95
频率:
50Hz额定转数:
75r/min
飞逸转数:
207r/min转动方向:
往下游看为顺时针
转子内径:
6000mm空气间隙:
8mm
总重量:
212吨
3.3电厂使用的技术条件
电厂使用的最大水头:
8.69m电厂使用的最小水头:
2.28m
三台机组满载时水头:
6.14m上游正常高水位:
▽55.7m
正常尾水位:
▽48.9m三台机组的最大出力:
48300kW
最大引用流量312m3/s时水头损失:
0.41m
3.4主要尺寸
灯泡直径:
7200mm灯泡比:
1.14
喉管直径:
6116mm进水口尺寸(宽×高):
12600×18860mm
进水流道长度:
35400mm尾水出口尺寸(宽×高):
12850×9000mm
尾水管长度:
29500mm转轮直径:
6300mm
临界弯曲转数:
420.6r/min扭矩自然频率:
9.92Hz
导叶数:
16导叶高度:
2175mm
导叶开度:
0~83°轮毂比:
0.418
轮叶数:
4轮叶开度:
-8~35°
转轮室与轮叶间隙:
2.6mm导叶接力器直径:
300mm
导叶接力器行程:
1114mm轮叶接力器直径:
1200mm
轮叶接力器行程:
432mm主轴外径/内径:
900/220mm
主轴长度:
7955mm
4水轮发电机组检修种类、周期及停用天数
4.1根据机组检修规模和停用时间,将发电机组的检修分为A、B、C、D四个等级。
4.1.1A级检修是指对发电机组进行全面的解体检查和修理,以保持、恢复或提高设备性能。
4.1.2B级检修是指针对机组某些设备存在问题,对机组部分设备进行解体检查和修理。
B级检修可根据机组设备状态评估结果,有针对性地实施部分A级检修项目或定期滚动检修项目。
4.1.3C级检修是指根据设备的磨损、老化规律,有重点地对机组进行检查、评估、修理、清扫。
C级检修可进行少量零件的更换、设备的消缺、调整、预防性试验等作业以及实施部分A级检修项目或定期滚动检修项目。
4.1.4D级检修是指当机组总体运行状况良好,而对主要设备的附属系统和设备进行消缺。
D级检修除进行附属系统和设备消缺外,还可根据设备状态的评估结果,安排部分C级检修项目。
4.2检修间隔
在两次A级检修之间,安排1次机组B级检修;除有A、B级检修年外,每年安排1次C级检修,并可视情况,每年增加1次D级检修。
如A级检修间隔为6年,则检修等级组合方式为A—C(D)—C(D)—B—C(D)—C(D)—A(即第1年可安排A级检修1次,第2年安排C级检修1次,并可视情况增加D级检修1次,以后照此类推)
4.3检修时间
4.3.1A级检修时间75~85天;
4.3.2B级检修时间50~55天;
4.3.3C级检修时间10~12天。
5水轮发电机的维护与检查
5.1水轮机的维护与检查
5.1.1转轮(一年一次)
5.1.1.1转轮叶片与转轮室空蚀、裂纹、腐蚀检查处理。
5.1.1.2轮叶开关灵活性与到位情况检查。
5.1.1.3轮叶密封检查。
5.1.1.4轮叶间隙检查。
5.1.1.5检查水轮机是否有异声(每星期一次)。
5.1.2主轴密封漏水量测量(一年一至两次)。
5.1.3导水机构
5.1.3.1液压连杆与挠曲连杆检查(每星期一次)。
5.1.3.2导叶拐臂检查(一年一次)。
5.1.3.3导叶内外侧端部密封检查(每星期一次)。
5.1.3.4导叶立面间隙、端面间隙检查(一年一次)。
5.1.3.5导叶接力器密封检查(每星期一次)。
5.1.3.6调速环间隙检查(一年一次)。
5.1.3.7调速环加润滑油(三个月一次)。
5.1.4水轮机导轴承
5.1.4.1仪表指示与损坏情况检查(每星期一次)。
5.1.4.2各管道与接头漏油、漏水情况检查(每星期一次)。
5.1.4.3轴承运行温度及声音检查(每星期一次)。
5.1.5各部件渗漏情况检查(每星期一次)。
5.1.6设备定期工作及卫生工作(按运行规程进行)。
5.2发电机的维护与检查
5.2.1循环水泵检查(每星期一次)。
5.2.2风机及风冷器运行情况检查(每星期一次)。
5.2.3膨胀水箱水位检查(每星期一次)。
5.2.4吸潮器检查(每星期一次)。
5.2.5发电机导轴承、推力轴承温度检查(每星期一次)。
5.2.6各轴承油流量检查(每星期一次)。
5.2.7各油箱油位、油温检查(每星期一次)。
5.2.8轴承油泵、顶轴油泵、漏油泵、油雾泵等检查(每星期一次)。
5.2.9轴承油冷却器、过滤器检查(一年一至两次)。
5.2.10制动系统检查(每星期一次)。
5.2.11各部位渗漏情况检查(每星期一次)。
6水轮发电机检修主要项目
6.1水轮机C级检修项目一般包括以下内容
6.1.1主轴摆度测量(水导轴颈位置)。
6.1.2调速环加黄油。
6.1.3液压连杆和挠曲连杆测量、检查。
6.1.4液压连杆装置渗漏检查。
6.1.5主轴密封漏水量测量。
6.1.6导叶内外轴承密封检查。
6.1.7轮叶、转轮的空蚀、磨损情况检查、测绘、记录、摄影。
6.1.8轮叶端部间隙检查。
6.1.9轮叶密封、泄水锥与轮毂接合面的渗漏情况检查。
6.2发电机C级检修项目
6.2.1轴承油冷却系统检查。
6.2.2轴承油系统换油,油过滤器清扫、检查,油水报警器清扫。
6.2.3刹车系统检查。
6.2.4循环冷却系统检查。
6.2.5高位油箱清扫。
6.3水轮机B级检修项目主要包括以下内容
6.3.1空蚀处理。
6.3.2轮叶接力器检修(不含操作油管)。
6.3.3轮叶密封检修。
6.3.4水导轴承检修。
6.3.5主轴密封检修。
6.3.6组合轴承检修。
6.3.7导叶轴承检修。
6.3.8液压连杆、挠曲连杆检修。
6.3.9调速环检修。
6.3.10水轮机轴线调整。
6.3.11轮叶、导叶间隙测量及调整。
6.4发电机B级检修项目
6.4.1机组窜动量、上抬量测量。
6.4.2发电机循环水冷却系统检修。
6.4.3发电机循环风冷却系统检修。
6.4.4刹车系统检修。
6.4.5发电机空气间隙检查及风洞检查、清扫。
6.4.6轴承油系统全面检修。
6.4.7各结构部位检查。
7机械检修应遵守的通用规则
7.1各设备拆卸前,应查对原位置记号或编号,不清楚的应重新做并记录。
装复时应按原记号或编号安装。
7.2拆卸时先拆销钉后拆螺栓,装复时先装销钉后装螺栓。
各部件的安装顺序应按拆卸时的相反顺序进行。
7.3各部件加工面不应敲打或碰伤,如有损坏应修磨好。
各精细加工面应清扫干净并涂以防锈油,分类摆放,摆放时不应互相挤压,必要时应加标签。
7.4各零部件与空气或水接触的表面,均应刷防锈漆。
各设备、管道应按规定的颜色刷漆。
7.5装复时易进水或潮湿处的螺栓、结合面应涂以黄油或油铅粉,各连接螺栓均应牢固拧紧,各转动部位螺栓应加止动装置或点焊。
使用紧固胶和平面密封胶时要求如下:
紧固胶:
M16及以下螺钉用L241;M20~M36螺钉用L282;M36及以上螺钉用L276。
密封胶:
结合平面用510、515、574或598。
7.6橡胶制品应用煤油、柴油或乙醇清洗,不许用汽油、甲苯或丙酮清洗。
7.7水轮发电机转动部分使用电焊时,交、直流焊机的地线应接转动部分,火线为焊把。
为防止轴电流损坏轴瓦,一方面地线要紧挨施焊点固定牢靠,另外在离施工点最近处、转动部分与固定部分的间隙处要打铝楔子板。
施焊前,应报告机械主管工程师到现场监督。
7.8应严格按《电业安全工作规程》(热力和机械部分)的要求进行工作。
7.9检修过程中应认真做好设备的技术状况、运行磨损、系统和结构的改变及有关测试记录,并及时整理存档。
7.10应按检修质量三级验收制度进行验收。
检修完工后20天内应提交大修技术总结,对检修的质量、安全、节约、管理等总的工作情况及机组试运行情况进行总结。
7.11易损部件应有设备图纸,检修中应及时校对,当缺少图纸及设备异动时应及时绘制。
8主要部件的检修及工艺要求
8.1空蚀处理
8.1.1空蚀处理前,必须严格保证流道积水在工作点以下,且应搭设可靠的工作平台。
8.1.2轮叶间隙、主轴上抬量和窜动量已测量记录完毕。
8.1.3调速系统已泄压排油。
8.1.4水导轴承、转轮室水平和垂直方向上的百分表已架好,并已记录数值。
8.1.5用绘图用方格纸拓印空蚀部分实际面积,测量空蚀深度,并摄影。
然后计算空蚀强度与空蚀所产生的金属失重量。
8.1.6根据测量与计算结果确定空蚀处理工艺。
如空蚀轻微可采用金属涂层方法,若空蚀较严重,则必须进行补焊处理。
8.1.7用砂轮、风铲或碳弧气刨除掉空蚀损坏区域的金属,其清除深度一般应达到95%以上的面积露出基体金属,将高点和毛刺磨掉后用抛光机或打砂等方法进行抛光。
8.1.8用金属涂层进行空蚀处理时,在完成上述工作后,将空蚀部位清洗干净后进行预热,预热温度为80~100℃或加热部位变为灰白色,再将已调好的由金刚砂和胶粉等组成的涂层物质涂在已加热的空蚀部位并进行仿形处理,然后进行加热,加热过程中在涂层表面刷一遍胶,加热至涂层固化即可,在处理过程中应注意防止涂层不能流动和被划伤。
8.1.9用补焊进行空蚀处理时,应有严格的焊接工艺及防止设备热变形的方案。
8.1.9.1补焊必须采用直流焊机,焊条接正极,且焊条应选用与本体材质相近的抗汽蚀堆焊焊条。
轮毂材质为GS20Mn5型普通的合金高强度钢,成分:
C/0.17~0.23,Si/0.3~0.6,Mn/1~1.3,P/0.035,S/0.035,相当于国产ZG20SiMn。
8.1.9.2补焊应对称同步分层进行,以最大限度的减小空蚀部件的热变形。
8.1.9.3堆焊要求焊面平整、严密、无砂眼、气孔等缺陷。
8.1.9.4堆焊过的部位必须仿形打磨,表面粗糙度参数值要求小于12.5μm,堆焊与堆焊处及堆焊与本体处应平滑过渡,以保持原来的线型要求。
8.1.9.5补焊过程中须严密监视水导轴颈和转轮室处百分表的数值变化,以便及时修正焊接方位。
8.1.9.6补焊修复后,必须进行无损探伤检查,不应有裂纹、气泡等缺陷存在。
8.1.9.7转轮补焊后应作静平衡试验,消除不平衡重量。
轮叶补焊后,抗汽蚀裙边厚度不应降低。
8.1.9.8补焊修复后,无论轮叶密封是否更换,均应做叶片转动实验,要求叶片转动应灵活,在高位油箱油柱压力下保持6小时叶片密封处应无渗漏。
另外在轮叶、导叶协联调试无水状态下,轮叶全开、全关多次动作后观察密封处也应无渗漏。
8.2轮叶密封检修
8.2.1轮叶密封的拆卸
8.2.1.1检修前应检查轮毂油中是否含水,可通过检查轮叶密封处是否有渗漏油和平时观察尾水水面是否有浮油的现象以确定是否更换轮叶密封。
8.2.1.2更换密封前应将调速系统泄压、排油,拆卸泄水锥及轮叶接力器活塞缸M120螺母。
8.2.1.3轮叶密封由压环、紧固螺钉、人字橡胶密封、顶紧环、弹簧组成。
其中压环由四瓣组成,拆卸压环需盘动轮叶才可全部拆除。
8.2.1.4拆下轮叶密封分瓣压环,取出四层人字密封条,用砂纸、乙醇或丙酮清扫干净密封部位,取出人字密封时要记录人字密封接头位置。
8.2.2密封的安装
8.2.5.1顶紧环与轮叶枢轴的同心度必须符合图纸要求,为此可在顶紧环与密封槽之间插入细小的薄铜片,调整到获得良好的同心度为止。
8.2.5.2将“人”字型密封条在轮叶枢轴上滑动的部位涂上一层纯净黄油和机油混合物,以保证密封条唇边不被刮伤和拉伤。
8.2.5.3在安装密封条时,四圈密封条所有接头应遵循以下原则:
第二圈与第一圈接头错开180°,第三圈与第二圈接头错开90°,第四圈与第三圈接头错开180°。
8.2.5.4在安装密封条时,应使各圈密封条接触良好、严密,接头部位不应粘接,两接头之间应留1~2mm间隙。
8.2.5.5在安装分瓣压环和紧固螺钉时,要在盘动轮叶位置的情况下进行,在拧入定位螺钉时,使其刚刚接触到密封圈为止,然后对称四分之一圈、四分之一圈地逐渐拧入每个螺钉,一直到拧紧为止。
为了防止顶紧环扭曲,螺钉必须平稳、均匀、对称地拧紧,以保证顶紧环在一个平面上。
8.2.5.6为了便于安装各位置分瓣压盖,可将轮叶转动到另一端位置。
8.2.5.7再次打开分瓣压盖,检查密封圈压紧情况,如压紧情况不理想,可在分瓣压盖下配制适当的垫片,以保证密封效果。
8.2.5.8密封装置安装好后,将轮毂内充满油检查是否渗漏,无渗漏时再将高位油箱充满油,检查是否渗漏,无渗漏时将调速器升压至6.0MPa油压下做动作试验,保持正常油压10小时应无渗漏。
8.2.5.9如轮叶密封无渗漏,则用环氧树脂涂料将压环紧固螺钉头部空隙进行封堵。
否则应重新处理。
8.3水导轴承检修
8.3.1通过检查水导轴承的温升、间隙、主轴上抬量、顶轴油泵油压、主轴顶升高变化情况等判断是否修刮或更换水导轴承。
8.3.2拆除水导轴承前转轮与转轮室间隙、主轴上抬量、主轴窜动量已测量记录,调速系统已泄压排油,受油器浮动瓦已拆卸,制动系统已退出。
8.3.3在主轴密封+X和±Y方向架设百分表,监视主轴的径向变化;在转轮室+X和+Y方向架设百分表,监视轮叶端部径向间隙;在受油器支墩机座上架设百分表,监视操作油管+X和+Y方向径向变化。
8.3.4水导轴承的拆卸与测量
8.3.4.1拆卸水导轴承进、排油管、端盖和测温装置。
8.3.4.2测量水导轴承挡油环至水导瓦侧的轴向间距,挡油环合缝处间隙及径向间隙,拆卸挡油环。
8.3.4.3测量水导瓦侧至主轴密封支持环内法兰的间距,测量主轴至内管型壳法兰±X、±Y方向间距。
8.3.4.4测量水导瓦上、下游顶端部、两侧间隙(合缝上下两处间隙尤为重要)。
拔出大盖销定,拆卸M48螺栓,分解大盖并吊出竖井。
8.3.4.5在水导支持环的横筋板上,安装专用鞍座,水平按0.1mm/m调整,拧紧固定螺钉后即可在鞍座上安放专用液压千斤顶、活塞头和厚度1-3mm的紫铜板,其轴线应对正主轴轴线,将50MPa手摇泵接头与液压千斤顶接头连接严实。
8.3.4.6监视主轴密封处百分表,用手摇泵向液压千斤顶升压,待-Y处百分表变化0.15~0.25mm时,投入液压千斤顶锁定,同时用塞尺在水导下瓦底部测量间隙,校正主轴实际上抬量。
与此同时要检查并记录轮叶、主轴密封、受油器处百分表的变化值。
若主轴密封处+X方向百分表变化值大于0.02mm,则用30t螺旋千斤顶(千斤顶头部应垫1-3mm的紫铜板,其轴线应对正主轴轴线)在±X方向从内管型壳法兰上顶主轴,使主轴密封处+X方向百分表指示值回到0。
然后液压千斤顶卸压,落下主轴,主轴密封处+Y方向百分表应回到0。
按主轴密封处+X方向百分表变化值微调鞍座位置,再次升压顶起主轴,直至主轴上抬时主轴密封处+X方向百分表变化值小于0.02mm,落下主轴时主轴密封处+Y方向百分表回到0,且3次以上无变化,即可顶起主轴,待-Y处百分表变化1.5~2.0mm时,投入液压千斤顶锁定,对各百分表读数、记录,轮叶端部±X、-Y方向间隙用塞尺测量、记录。
8.3.4.7用塞尺检查扇形支座内、外圈径向间隙,拆卸内圈-Y方向两边第三个M24销钉螺栓和其余十个螺钉。
螺钉、销钉均有钢套,要注意应配对保存。
8.3.4.8用一台2吨链条葫芦配M48吊环微吊水导下瓦,拆卸下瓦与扇形板定位销钉及紧固螺钉,然后用M24螺钉拧入顶丝孔,向下游顶水导瓦下部扇形体,使水导瓦退出扇形支座。
8.3.4.9将水导瓦吊出竖井放在专用瓦枕上。
8.3.5外观检查及质量要求
8.3.5.1大盖与下瓦
(1)外壳应完整、无裂纹,且两侧接合面接触严密,无渗漏。
(2)油孔、测温控畅通,丝扣完好,无堵塞及渗漏。
(3)销钉及销钉孔应完好,无毛刺及剪切、撞击压痕。
(4)轴向两端面螺孔应完好平整、无毛刺、凹凸及渗漏痕迹。
(5)钨金表面、油孔、沟槽应完好,无变兰、硬结、脱胎、轴向划痕及电腐蚀斑点等,顶轴高压油洼应完好无毛刺。
(6)支承孔应完好无毛刺、喇叭口;钢套应完好无破损;销钉孔与钢套的配合孔要求为φ34H7/h6,各钢套长度要求为45.3h9,孔长要求为45H9。
(7)大盖与下瓦预装时,两侧接合面配合应严密,要求0.02mm塞尺不能插入,钨金面合缝处不许错口,瓦内径最大尺寸为φ900H0.09。
8.3.5.2轴颈
(1)轴颈段用刀口尺检查,应完好,无毛刺、裂纹、撞击压痕及电腐蚀斑点等。
(2)轴颈外径设计为φ899.5h-0.056,相对轴瓦最大配合间隙为0.646mm。
(3)轴颈段三个断面的不圆度应小于0.02mm。
(4)轴颈段三个断面中任何纵断面中的直径差应小于0.02mm。
(5)轴颈检查前、后都应淋洁净透平油、贴描图纸,并用薄膜和毛毯包扎好。
8.3.5.3扇形板座及瓦体支承
(1)座及支承应完整无变形,座及支承、压板、各螺孔应完好,座及支承的圆弧面无压凹伤痕,焊缝经探伤检查无缺陷。
(2)销钉及螺钉应无滑丝、变形,螺杆与螺母配合应严密。
销钉与钢套、钢套与孔的配合应严实;螺钉与钢套有1mm间隙,钢套与孔有2mm间隙,均为松动配合。
8.3.6轴承的清洗与修理
8.3.6.1轴承在修整前后及装复前都应清洗干净。
残留的涂料固结块、结合面、螺杆、螺孔等都应清洗修刮干净。
8.3.6.2轴瓦钨金面的异常情况必须逐级上报技术主管部门会商处理。
若需要修整,应由钳工手艺较好的人员用刮刀和铲刀进行修刮,不准使用砂布、锉刀等切削工具。
8.3.6.3支承及支承座经探伤检查,如发现有裂纹等缺陷,必须逐级上报技术主管部门会商处理。
8.3.6.4轴颈的毛刺、划痕,应用天然油石醮601或602抛光膏与机油、煤油的混合液进行研磨,研磨的纹路按“8”字形或仿“8”字形,不准轴向或周向直磨。
8.3.6.5大盖结合面的铲刮
(1)轴瓦与轴颈的配合间隙为φ900H0.09/φ899.5h-0.056,所以允许最大间隙为0.646mm,允许最小间隙为0.50mm,若超标应进行处理。
处理方法为铲刮大盖结合面,铲刮量取实测间隙与允许最大间隙、允许最小间隙平均值之差或允许最小间隙值。
(2)铲刮分两种。
一是轴承完全解体后铲刮:
大盖与下瓦吊出,铲刮大盖,装复时进行轴线检查和调整;二是轴承部分解体铲刮:
下瓦不动,拆下大盖并铲刮后检查下瓦表面和轴线。
(3)铲刮时用红丹粉作显示剂,基准为下瓦结合面,校验基准为一级的1m×0.75m平板,铲刮用T12或W18Cr4V做刀片。
(4)再次铲刮前,均应将大盖与下瓦接合面推磨3~5遍,最大、最亮点先铲、多铲,次亮点适当少铲,然后均匀大面积铲刮。
(5)精刮:
当预定铲刮量仅剩0.02~0.03mm时,应将下瓦、大盖与轴颈装复检测实际间隙值,方法采用压铅丝校验后进行精刮。
主要作用是消除轴瓦孔的锥形现象。
(6)所压铅丝直径应比间隙值大1/3左右,在大盖轴向两端50mm宽的环带内各放三条长150mm的铅丝后,按对角线顺序、