板坯中间包修复规程Microsoft Office Word 文档.docx
《板坯中间包修复规程Microsoft Office Word 文档.docx》由会员分享,可在线阅读,更多相关《板坯中间包修复规程Microsoft Office Word 文档.docx(25页珍藏版)》请在冰点文库上搜索。
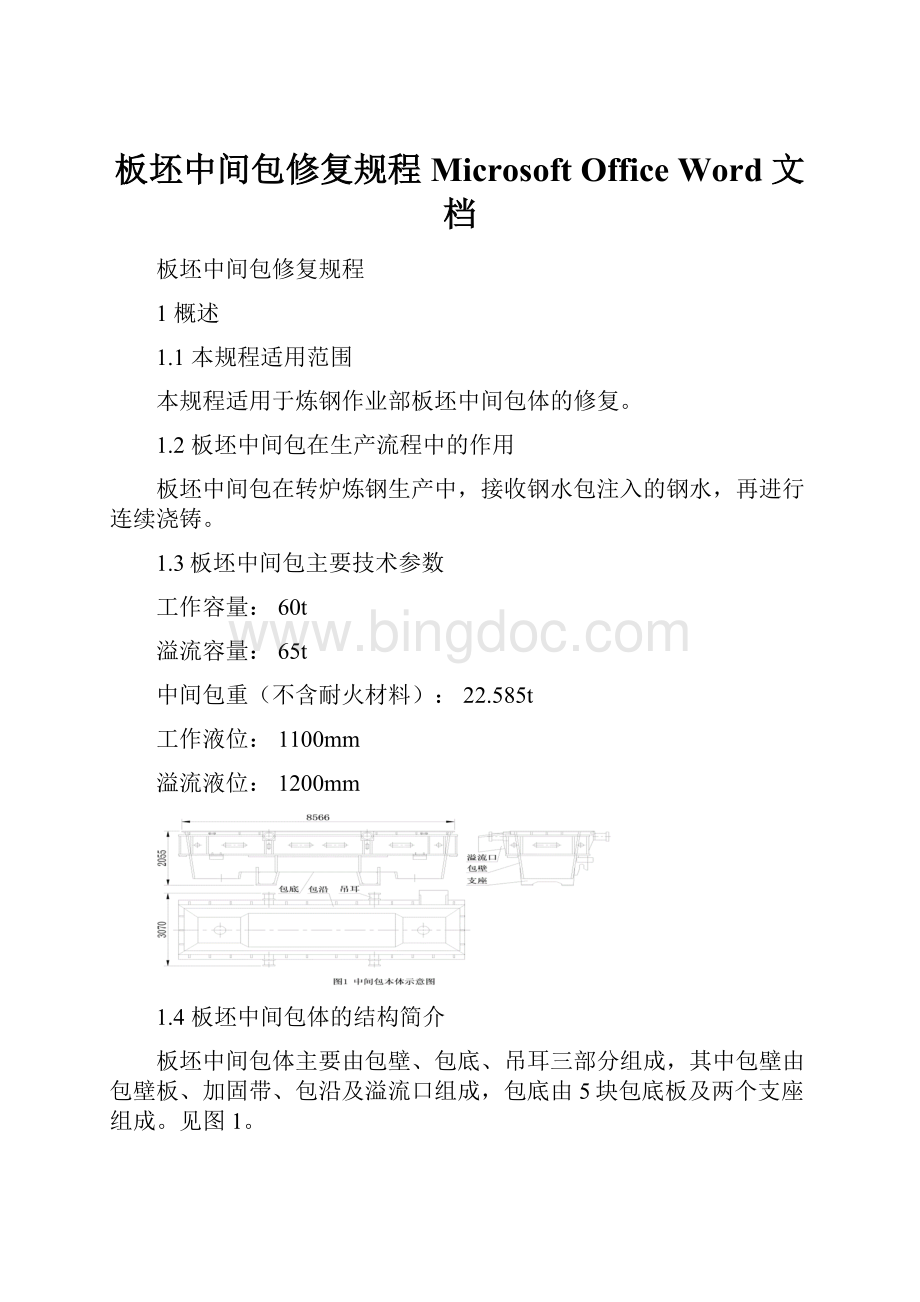
板坯中间包修复规程MicrosoftOfficeWord文档
板坯中间包修复规程
1概述
1.1本规程适用范围
本规程适用于炼钢作业部板坯中间包体的修复。
1.2板坯中间包在生产流程中的作用
板坯中间包在转炉炼钢生产中,接收钢水包注入的钢水,再进行连续浇铸。
1.3板坯中间包主要技术参数
工作容量:
60t
溢流容量:
65t
中间包重(不含耐火材料):
22.585t
工作液位:
1100mm
溢流液位:
1200mm
1.4板坯中间包体的结构简介
板坯中间包体主要由包壁、包底、吊耳三部分组成,其中包壁由包壁板、加固带、包沿及溢流口组成,包底由5块包底板及两个支座组成。
见图1。
中间包体的材料:
吊耳为机械加工件,材质设计为25CrMo,其余各件均由不同厚度的钢板制成,钢板的材质为:
包壁板及包底板为Q345-B,其余钢板为Q235-B。
2修复作业标准
2.1修复内容
2.1.1包壁板损坏部位的挖补。
2.1.2包底板的更换。
2.1.3吊耳的更换。
2.1.4包底支座的更换。
2.1.5包体钢板及焊缝裂纹的修复补焊。
2.2修复前的准备工作
2.2.1包壁板损坏部分挖补的准备工作
2.2.1.1修复人员的准备
电焊工的准备
持有电焊工资质证书的电焊工2名。
电焊工应熟知包壁的材质、焊接性能及焊接方法。
电焊工应严格执行本规程有关焊接的各项规定。
气焊工的准备
气焊工2名,用于旧件的拆除切割,新件的切割安装。
气焊工应熟知新、旧件的切割要求(切割线、坡口角度、切割面的质量等)。
铆工的准备
铆工2~4名,用于旧件挖补部分的划线、拆除及新件的制作安装。
铆工应熟知挖补部分的尺寸、新件制作的尺寸及安装要求等。
2.2.1.2设备工具的准备
焊接设备工具的准备
额定电流500A的电弧焊机(交直流均可)2台(含电缆及焊条夹钳)。
清除焊渣用的尖锤、手锤、砂轮磨光机,手砂轮、扁产等。
焊条筒2个。
碳弧气刨枪(含风管、电缆、碳棒、风源等)1套。
气割工具的准备
气割工具(含减压表、胶管等)2套。
铆工工具的准备
铆工用工具:
大锤、手锤、盘尺、盒尺、钢板尺、直角尺、洋冲、手砂轮等,按需准备。
2.2.1.3挖补材料的准备
电焊条的准备
电焊条型号E4303,焊条直径Φ3.2mm、Φ4mm。
焊条必须是正规焊条厂出品,有生产许可证和产品合格证。
受潮焊条、脱皮和粘有油锈焊条禁用。
焊条应放在焊条筒内使用,禁止随意乱放。
气割材料的准备
瓶装乙炔2瓶。
瓶装氧气2瓶。
2.2.1.4挖补备件的准备
备件用材料
备件材质Q345-B,厚度30mm。
备件的加工
按挖补的具体位置确定a、b的尺寸,并加工坡口,坡口可用机械加工,也可用气割切割,具体要求见图2。
要求切口及坡口表面平滑,无氧化铁渣、油、锈及其它污物。
2.2.2包底板更换的准备工作
2.2.2.1修复人员的准备
电焊工的准备
持有电焊工资质证书的电焊工2名。
电焊工应熟知包壁的材质、焊接性能及焊接方法。
电焊工应严格执行本规程有关焊接的各项规定。
气焊工的准备
气焊工2名,用于旧件的拆除切割,新件的切割安装。
气焊工应熟知新、旧件的切割要求(切割线、坡口角度、切割面的质量等)。
铆工的准备
铆工2~4名,用于旧件挖补部分的划线、拆除及新件的制作安装。
铆工应熟知挖补部分的尺寸、新件制作的尺寸及安装要求等。
2.2.2.2设备工具的准备
焊接设备工具的准备
额定电流500A的电弧焊机(交直流均可)2台(含电缆及焊条夹钳)。
清除焊渣用的尖锤、手锤、砂轮磨光机,手砂轮、扁产等。
焊条筒2个。
碳弧气刨枪(含风管、电缆、碳棒、风源等)1套。
气割工具的准备
气割工具(含减压表、胶管等)2套。
铆工工具的准备
铆工用工具:
大锤、手锤、盘尺、盒尺、钢板尺、直角尺、洋冲、手砂轮等,按需准备。
2.2.2.3挖补材料的准备
(1)电焊条的准备
电焊条型号E4303,焊条直径Φ3.2mm、Φ4mm。
焊条必须是正规焊条厂出品,有生产许可证和产品合格证。
受潮焊条、脱皮和粘有油锈焊条禁用。
焊条应放在焊条筒内使用,禁止随意乱放。
(2)气割材料的准备
瓶装乙炔2瓶。
瓶装氧气2瓶。
2.2.2.4更换备件的准备
由于包底板是由5块在不同的位置组焊而成,故备件的准备数量按更换的数量准备,每件的具体尺寸按旧件确定。
包底板于设计图纸中的序号为28(1块板)、30(2块板)、31(2块板),其材质为Q345-B,厚度:
件号31为55mm,其余均为30mm。
坡口的加工
1)坡口的型式见图3、图4。
图3的坡口型式用于包底板与包壁的连接焊缝。
图4(a)的坡口型式用于与包底板(件号30)的连接焊缝,图4(b)的坡口型式用于与包壁的连接焊缝。
2)坡口的加工方法
坡口的加工可用机械加工,也可用气割切割,要求气割表面平滑,无氧化铁渣、无油锈和其它污物。
2.2.3吊耳更换的准备工作
2.2.3.1修复人员的准备
电焊工的准备
持有电焊工资质证书的电焊工3名。
电焊工应熟知包壁的材质、焊接性能及焊接方法。
电焊工应严格执行本规程有关焊接的各项规定。
气焊工的准备
气焊工3名,用于旧件的拆除切割,新件的切割安装。
气焊工应熟知新、旧件的切割要求(切割线、坡口角度、切割面的质量等)。
钳工的准备
钳工2~4名,用于吊耳旧件的拆除及新件的安装。
钳工应熟知吊耳的各部尺寸、旧吊耳的拆除要求及新吊耳的安装要求。
2.2.3.2设备工具的准备
焊接设备工具的准备
额定电流500A的电弧焊机(交直流均可)3台(含电缆及焊条夹钳)。
清除焊渣用的尖锤、手锤、砂轮磨光机,手砂轮、扁产等。
焊条筒2个。
碳弧气刨枪(含风管、电缆、碳棒、风源等)1套。
气割工具的准备
气割工具(含减压表、胶管等)2套。
钳工工具的准备
钳工用工具:
手锤、大锤、洋冲、盒尺、盘尺、直角尺、钢板尺、划针、水平仪、手砂轮等。
加热设施的准备
煤气燃烧器按需准备,用于预热。
红外线测温仪1件。
石棉布5m2(1个吊耳用)、耐火纤维毡700×700mm1块、粘合剂0.5kg。
2.2.3.3更换材料的准备
电焊条的准备
电焊条型号E4303,焊条直径Φ3.2mm、Φ4mm。
焊条必须是正规焊条厂出品,有生产许可证和产品合格证。
受潮焊条、脱皮和粘有油锈焊条禁用。
焊条应放在焊条筒内使用,禁止随意乱放。
气割材料的准备
1)瓶装乙炔2瓶。
2)瓶装氧气2瓶。
2.2.3.4吊耳备件的准备
按设计图X4321B4-2的2/4图中的件号6准备新吊耳,按更换数量确定件数。
吊耳材质为25CrMo。
2.2.4包底支座更换的准备
2.2.4.1修复人员的准备
电焊工的准备
持有电焊工资质证书的电焊工2名。
电焊工应熟知支座的材质、焊接性能及焊接方法。
电焊工应严格执行本规程有关焊接的各项规定。
气焊工的准备
气焊工2名,用于旧件的拆除切割,新件的切割安装。
气焊工应熟知新、旧件的切割要求(切割线、坡口角度、切割面的质量等)。
铆工的准备
铆工2~4名,用于旧支座的拆除及新支座的安装。
铆工应熟知旧支座拆除及新支座的安装要求,并应熟知新件的各部位的尺寸及坡口型式等。
2.2.4.2设备工具的准备
焊接设备工具的准备
额定电流500A的电弧焊机(交直流均可)2台(含电缆及焊条夹钳)。
清除焊渣用的尖锤、手锤、砂轮磨光机,手砂轮、扁产等。
焊条筒2个。
碳弧气刨枪(含风管、电缆、碳棒、风源等)1套。
气割工具的准备
气割工具(含减压表、胶管等)2套。
铆工工具的准备
铆工用工具:
大锤、手锤、盘尺、盒尺、钢板尺、直角尺、洋冲、手砂轮等,按需准备。
2.2.4.3更换材料的准备
电焊条的准备
电焊条型号E4303,焊条直径Φ3.2mm、Φ4mm。
焊条必须是正规焊条厂出品,有生产许可证和产品合格证。
受潮焊条、脱皮和粘有油锈焊条禁用。
焊条应放在焊条筒内使用,禁止随意乱放。
气割材料的准备
瓶装乙炔2瓶。
瓶装氧气2瓶。
2.2.4.4支座备件的准备
由于中间包共有两个支座,其形状尺寸、材料等完全相同。
故本规程只按更换1件支座需用的备件准备。
备件用材料
材质为Q235-B,厚度30mm、50mm。
备件的下料加工
备件的件号一律引用了设计图中的件号(见图5、图6、图7、图8)。
按本规程图5件号15加工1件,图6件号25加工2件(左、右各1件),图7件号26加工2件,图8件号27加工1件。
图5、图6、图7、图8的零件尺寸如与旧件不符,要以旧件尺寸为准。
加工方法
用机械加工或气割加工,用气割加工时要求表面平滑并清除氧化铁渣(气割后可用手砂轮将切割面磨平)。
2.2.5包体钢板及焊缝裂纹的修复补焊准备工作
2.2.5.1修复人员的准备
电焊工的准备
持有电焊工资质证书的电焊工2名。
电焊工应熟知包壁的材质、焊接性能及焊接方法。
电焊工应严格执行本规程有关焊接的各项规定。
铆工的准备
铆工1名,用于包壁钢板裂纹部位坡口的划线。
铆工应熟知裂纹部位坡口加工的尺寸及要求。
2.2.5.2设备工具的准备
焊接设备工具的准备
额定电流500A的电弧焊机(交直流均可)2台(含电缆及焊条夹钳)。
清除焊渣用的尖锤、手锤、砂轮磨光机,手砂轮、扁产等。
焊条筒2个。
碳弧气刨枪(含风管、电缆、碳棒、风源等)1套。
铆工工具的准备
铆工工具:
手锤、洋冲、钢板尺、直角尺、盒尺等。
2.2.5.3修复补焊材料的准备
电焊条的准备
电焊条型号E4303,焊条直径Φ3.2mm、Φ4mm。
焊条必须是正规焊条厂出品,有生产许可证和产品合格证。
受潮焊条、脱皮和粘有油锈焊条禁用。
焊条应放在焊条筒内使用,禁止随意乱放。
2.3板坯中间包的修复方法
2.3.1包壁损坏部位的挖补方法
2.3.1.1将包体摆放在便于挖补的操作位置,并清除掉挖补部位的耐火材料。
2.3.1.2挖补部位的包壁拆除
在应挖补的部位包体的内侧划出拆除的切割线。
按切割线用气割割掉应挖掉部位的包壁,并在包体的切口处切割坡口,见图9,尺寸L、M按挖补尺寸确定。
2.3.1.3用手砂轮将切口及坡口表面磨平,清除氧化铁渣。
2.3.1.4挖补部位的新件安装
按图10安装新件,找好对口间隙及表面平度,错口量≤2mm。
新、旧件的点固焊
新件与旧件的对口间隙及表面平度找好后要进行点固焊,点固焊工艺参数、焊缝尺寸及焊缝间距等可参考表1所示:
点固焊工艺参数及焊缝尺寸参考表表1
焊条直径mm
焊接电流A
焊缝高度mm
焊缝长度mm
焊缝间距mm
Φ4
160~210
4~6
30~50
300~500
2.3.1.5新、旧件接缝的焊接
焊前检查
检查坡口及其两侧是否干净,如有污物、油、锈等要全部清除干净。
焊接
立缝采用多层焊,横缝采用多层多道焊,焊接工艺参数见表2所示:
焊接工艺参数表表2
焊接层次
焊条直径mm
焊接电流A
焊道宽度mm
焊道(层)厚度mm
第一层
Φ3.2
100~120
8~10
3~5
第二层及以后各层
Φ4
160~210
10~12
4~5
先焊长焊缝,后焊短焊缝,接焊缝的具体长度与距离可由1人或2人同时焊接1条或2条接缝,一律采用单面焊(即在包内施焊)。
每层焊道的起止点,要与上一层的起止点错开20~30mm。
电弧引弧要在坡口内进行,禁止在坡口外引弧。
每焊完一层将渣皮清除干净,检查焊道有无裂纹、未熔合、夹渣、气孔等缺陷,如有必须清除后再焊下一层。
焊缝全部焊完以后,清除渣皮,对焊缝进行全面外观检查,发现缺陷后,要及时处理完毕(焊接缺陷见后文)。
新件钻孔
在装焊的新件上钻孔Φ10mm、孔距500×500,参照旧包壁的孔的位置进行排列。
2.3.2包底板的更换修复方法
2.3.2.1拆除包体内部包底板更换位置的耐火材料,并按使用位置(包口朝上)放置平稳。
2.3.2.2包底板的拆除
由于包底板是由5块钢板组成,而且不在同一个平面上,需要换的包底板可能是1块或2块直至全部,本规程按全部包底板更换而编制的。
将包底板之间连接的焊缝用气割切断(共4条焊接)。
用气割切开包底板与包壁连接的焊缝及包底板与支座的连接焊缝,切口要距包壁3~5mm,并将包底板吊出包体,放在适当的安全位置。
2.3.2.3磨平切口
将切割时留在包壁上的3~-5mm焊缝用手砂轮磨掉,达到该处与包壁表面平度一致。
2.3.2.4新包底板的安装
按设计图X4321B4-2(1/4)、(2/4)及图11的a、b接头,安装新包底板(件号28、30、31)。
新、旧件的点固焊
新件与旧件的对口间隙、表面平度、安装位置找好后要进行点固焊,点固焊工艺参数、焊缝尺寸及焊缝间距等可参考表3所示:
点固焊焊接工艺参数及焊缝尺寸参考表表3
焊条直径mm
焊接电流A
焊缝高度mm
焊缝长度mm
焊缝间距mm
Φ4
160~210
4~6
30~50
300~500
2.3.2.5新、旧件接缝的焊接
焊前检查
检查坡口及其两侧是否干净,如有油、锈及其它污物要全部清除干净。
焊接
1)焊接顺序
先焊包体内侧接缝,再焊包体外侧接缝(焊包体外侧接缝时需将包体翻个,使包底朝上),而每侧又先焊包底板之间的接缝,再焊包底板与包壁连接的接缝。
2)焊接方法
a每侧接缝均由2人同时对称焊接两条接缝。
要求2人使用的焊条直径、焊接电流、焊接速度、焊层厚度等要保持一致。
b每条焊缝的每层均采用分段反向焊,分段长度350~400mm。
3)电弧引弧要在坡口内进行,禁止在坡口外任意引弧。
4)采用多层焊,每层焊道的起止点,要与上一层的起止点错开20~30mm,焊接工艺参数见表4所示:
焊接工艺参数及焊接厚度参考表表4
焊接层次
焊条直径mm
焊接电流A
焊层厚度mm
第一层
Φ3.2
100~120
3~5
第二层及以后各层
Φ4
160~210
3~5
5)每焊完一层将渣皮清除干净,检查焊道有无末熔合、裂纹、夹渣、气孔等缺陷,如有必须清除后再焊下一层。
6)焊缝全部焊完以后,清除渣皮,对焊缝进行全面外观检查,发现缺陷后要及时处理完毕(焊接缺陷见后文)。
2.3.3吊耳更换修复方法(本修复方法按吊耳材质为35CrMo制定的)
2.3.3.1将包体接常规位置放置平稳,达到安全可靠,拆除包内吊耳处的耐火材料。
2.3.3.2吊耳的拆除
将吊耳的位置中心留在包壁上。
切开吊耳与包壁及其支撑板连接的焊缝,切口要靠近吊耳,距吊耳小于5mm。
勿或少切伤与吊耳连接部位的其它件,将吊耳移开。
2.3.3.3用气割切割包体上与吊耳连接部位的坡口(见图12中的坡口Ⅰ、坡口Ⅱ及坡口Ⅲ)3处,并将坡口表面用手砂轮磨平,清除氧化铁渣。
2.3.3.4新吊耳的安装
接吊耳的原有位置并参照设计图纸X4321B4-2(1/4、2/4、3/4共3张图纸)安装新吊耳,找平、找正、找好同轴度,并予以固定(不点焊)。
2.3.3.5焊前吊耳的预热
预热部位
预热吊耳方形的两个侧面(见图13)。
预热方法
用煤气火焰预热,火焰的布置要在吊耳中心以下尺寸的1/2处,沿方形长度均匀布置(见图13)。
预热温度200~250℃。
测温方法及测温点
用红外线测温仪观测与连接件焊接处的吊耳部位。
2.3.3.6吊耳与各连接件接缝的焊接
焊接开始温度必须达到200~250℃。
焊缝Ⅰ、Ⅲ、Ⅳ、Ⅴ、Ⅶ采用多层多道焊,焊缝Ⅱ、Ⅵ采用多层焊。
焊接顺序及人员安排
由2人同时对称焊接焊缝Ⅰ(共2条),焊完再同时对称焊接焊缝Ⅱ(共2条)。
焊完后此2人分开,由1人焊接焊缝Ⅳ,另1人焊接焊缝Ⅲ,直至焊接完毕。
与焊缝Ⅰ焊接的同时,由1人在包体内部焊接焊缝Ⅵ(共2条),每层焊道要交替施焊,即焊完左侧的第一层再焊右侧的第一层,然后再焊左侧的第二层,完后再焊右侧的第二层,以此类推,直至焊完。
然后焊接焊缝Ⅴ及焊缝Ⅶ,仍用焊接焊缝Ⅵ的方法进行交替施焊直至焊完。
焊接要求
凡同时施焊的焊条直径、焊接电流、焊接速度、焊道宽度、焊层厚度均应保持一致,要连续焊接,一次焊完,不要停班隔夜。
焊条型号E4303。
焊接工艺参数及焊道尺寸见表5所示:
焊接工艺参数及焊道尺寸表表5
焊接层次
焊条直径mm
焊接电流A
焊层厚度mm
层间温度℃
第一层
Φ3.2
80~100
3~5
200~250
第二层及以后各层
Φ4
110~140
4~6
200~250
引弧要在坡口内进行,禁止在坡口外引弧。
焊接过程中,每隔10分钟测温一次,做好记录,直至焊接完毕或焊接缺陷处理完毕。
发现温度低于200℃,要停止焊接进行预热至200~250℃时再进行施焊。
每焊完一层将渣皮清除干净,检查焊道有无裂纹、未熔合、夹渣、气孔等缺陷,如有必须将缺陷清除后再焊下一层。
焊接全部完成以后,清除渣皮,对焊缝进行全面外观检查,出现焊接缺陷立即在预热温度200~250℃时进行修补(焊接缺陷见后文)。
焊后保温
焊缝经全面检查及缺陷处理完毕后,将吊耳及其周围>300mm部位用石棉布(或其它耐火保温材料)覆盖好。
包体内部吊耳与包壁的连接焊缝部位,用耐火纤维毡700×700mm1块,将吊耳端部(含包壁)贴好,覆盖范围要求焊缝两侧各>200mm。
2.3.4包底支座更换修复方法
2.3.4.1将包体底部朝上摆放平稳,达到安全可靠。
2.3.4.2包底支座(后文简称支座)的拆除
将支座的位置及距包底的高度留好记录。
切开支座与包体连接的焊缝,要求切口距包体3~5mm,然后移开支座。
2.3.4.3将留在包体3~5mm的焊缝用手砂轮磨掉,达到该位置的平面与包体的钢板平面一致。
2.3.4.4新支座的安装
按图14并参照设计图X4321B4-2(1/4、2/4、4/4)及旧有位置安装新支座(设计图中件号15、25、26、27)1套(或2套),并找平、找正,要求两个支座下平面平度一致。
支座点固焊
支座4个零件安装达到要求后要点焊固定,点固焊工艺参数及焊缝尺寸见表6所示:
夹固焊焊接工艺参数及焊缝尺寸表表6
焊条直径mm
焊接电流A
焊缝高度mm
焊缝长度mm
焊缝间距mm
Φ4
160~210
4~6
30~40
300~500
2.3.4.5支座的焊接
焊接顺序
按缝1(或2)、缝9、缝5和缝6(同时交替焊接)、缝3、缝4、缝7、缝8的排列顺序焊接,即先焊接缝1(或2),再焊2(或1),焊完后焊接缝9,以此类推直至焊缝全部焊完。
焊接方法
缝1(或2)的焊接
先平焊支座内口两层,停焊,在外口清焊根,然后由2人同时平焊内外口直至焊接完毕。
缝9的焊接
缝9共2条,由2人同时各焊1条,采用交替多层立焊,即每条缝的两面坡口,每层焊道交换焊接。
缝5和缝6的焊接
缝5和缝6各2条接缝,两侧共计4条,由2人同时分别各焊接缝5和缝6,均采用交替多层立焊,即焊完缝5第一层,再焊缝6第一层,再焊缝5第二层,焊完再焊缝6第二层,以此类推直至焊完。
缝3的焊接
先焊支座内部坡口,采用多层多道横焊,焊完后在外口清焊根,然后用多层多道焊的方法焊接外口,直至焊接完毕。
缝4的焊接
同缝3的焊接方法。
缝7的焊接
缝7共计2条,左右各1条,由2人同时各焊1条,采用多层多道焊,直至焊接完毕。
缝8的焊接
同缝7的焊接方法。
焊接工艺参数见表7和表8所示:
平焊、横焊工艺参数及焊道尺寸参考表表7
焊接层次
焊条直径mm
焊接电流A
焊道厚度mm
焊道宽度mm
第一、二层
Φ3.2
100~120
3~4
8~10
第三层及以后各层
Φ4
160~210
4~5
10~12
立焊工艺参数及焊道厚度尺寸参考表表8
焊接层次
焊条直径mm
焊接电流A
焊道厚度mm
第一、二层
Φ3.2
80~100
3~4
第三层及以后各层
Φ4
120~160
3~4
电弧引弧要在坡口内进行,禁止在坡口外引弧。
每焊完一层将渣皮清除干净,检查焊道有无裂纹、未熔合、夹渣、气孔等,如有必须清除后再焊下一层。
接缝全部焊完以后,清除渣皮,对焊缝进行全面外观检查,发现焊接缺陷要及时处理(焊接缺陷见后文)。
焊缝尺寸
各条焊缝厚度均要求将坡口填满后,再高出坡口3~4mm。
2.3.5包体钢板及焊缝裂纹的修复补焊方法
2.3.5.1将包体摆放在便于修复操作的位置,达到牢固安全可靠。
2.3.5.2用手电钻在裂纹两端各钻一个止裂孔Φ10~15mm,孔深为壁厚或裂纹深度。
2.3.5.3在裂纹两侧划出坡口线,其位置以裂纹为中心线向两侧各8mm(双面坡口)及各10mm(单面坡口)。
2.3.5.4坡口的加工
坡口型式的确定
钢板裂纹位置在加固带及以上时为单面U型坡口,开在包体内部(见图15a)。
钢板裂纹位置在加固带以下时,开双面U型坡口(见图15b)。
焊缝裂纹坡口均开在焊缝裂纹的一面为U型坡口。
坡口的加工
用碳弧气刨按裂纹两侧的划线刨出双U形和单U形坡口,达到图15的要求。
用手砂轮磨光坡口表面。
2.3.5.5坡口的补焊
双面坡口的补焊
焊条型号E4303。
采用多层焊,先焊坡口深度15mm的两层,停焊,再用碳弧气刨刨另一面坡口,将深度12mm刨成深度达17~18mm,再磨光新刨深的坡口。
然后由2人同时焊接两面坡口,直至焊接完毕。
补焊工艺参数见表9,要求2人同时补焊的焊条直径、补焊电流、补焊速度、焊层厚度应保持一致。
补焊工艺参数及焊层尺寸表表9
焊接层次
焊条直径mm
焊接电流A
焊层厚度mm
第一、二层
Φ3.2
100~120
3~4
第三层及以后各层
Φ4
150~200
3~4
电弧引弧要在坡口内进行,禁止在坡口外引弧。
每焊完一层将渣皮清除干净,检查焊道有无裂纹、未熔合、夹渣、气孔等缺陷,如有必须清除后再焊下一层。
补焊长缝(500mm以上)时,每层焊道起止点要与下一层起止点错开20~30mm。
补焊厚度要高出包壁钢板平面1~2mm。
补焊全部完毕后,清除渣皮,对焊缝进行全面外观检查,发现焊接缺陷需立即修补(焊接缺陷见后文)。
单面坡口的补焊
焊条型号E4303。
采用多层焊,补焊工艺参数及焊层厚度见表9。
、4)、5)、6)、7)同2.3.5.5-
(1)-3)、4)、5)、6)、7)。
焊缝裂纹