精品气门摇臂轴支座加工工艺设计.docx
《精品气门摇臂轴支座加工工艺设计.docx》由会员分享,可在线阅读,更多相关《精品气门摇臂轴支座加工工艺设计.docx(19页珍藏版)》请在冰点文库上搜索。
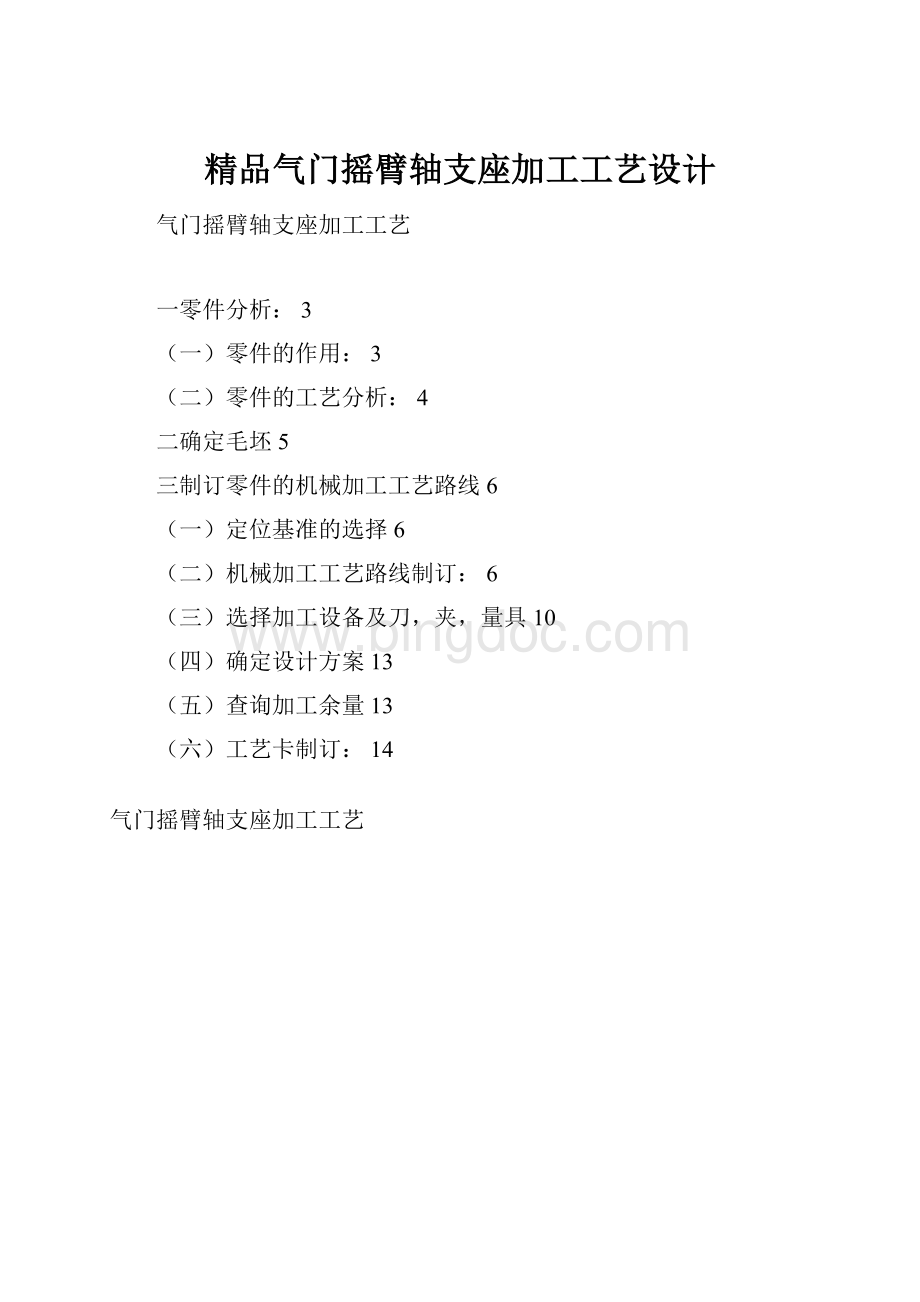
精品气门摇臂轴支座加工工艺设计
气门摇臂轴支座加工工艺
一零件分析:
3
(一)零件的作用:
3
(二)零件的工艺分析:
4
二确定毛坯5
三制订零件的机械加工工艺路线6
(一)定位基准的选择6
(二)机械加工工艺路线制订:
6
(三)选择加工设备及刀,夹,量具10
(四)确定设计方案13
(五)查询加工余量13
(六)工艺卡制订:
14
气门摇臂轴支座加工工艺
气门摇臂轴支座
一零件分析:
零件的作用:
气门摇臂轴支座是柴油机一个主要零件,是柴油机摇臂座的结合部,φ18(+0.0027~0)mm孔装摇臂轴,轴上两端各装一进排气门摇杆,φ
16(+0.11~+0.0)mm孔内装一减压轴,用于降低汽缸内压力,便于启动柴油机。
两孔间距为56正负0.05mm可保证减压轴在摇臂上打开气门,实现减压。
该零件通过φ11mm孔用M10螺杆与汽缸盖相连。
零件的工艺分析:
由图可知,其材料为HT200。
该材料具有较高的强度,耐磨性,耐热性及减震性,适用于承受较大应力,但是塑性较差,脆性较高,不适合磨削,而且加工主要集中在平面加工与孔加工上。
根据对零件图的分析,该零件需要加工的表面以及加工表面之间的位置要求如下:
22外圆的上端面以及与次孔相通的11通孔,粗糙度均为12.5;36mm下端面,根据该零件总体加工特性,我们将设其为整个加工过程的基准面,粗糙度为12.5,并且需要首先将此基准面加工出来;26外圆的前后端面,粗糙度为12.5;前后端面倒一45度的角,粗糙度为12.5;16的通孔,其所要求的精度较高,所以我们要求他的粗糙度为1.6,该孔的轴线与36mm下端面平面度为0.05;28外圆的前后端面,粗糙度为3.2;前后端面倒一45度的角,粗糙度为12.5;18的通孔,要求的表面粗糙度和位置精度很高,其粗糙度为1.6,孔的轴线与36mm下端面的平行度为0.05;通过对零件图的分析可知,36mm下端面和22mm上端面所要求的粗糙度都不是很高,所以不用精加工即可达到要求,且这两面作为加工过程主要的定位基准面,因此可以用粗加工或者半精加工来达到其精度要求,再以此作为基准采用专用夹具对其他部分进行加工,并且能够保证其他部分加工的精度要求。
二确定毛坯
零件材料为HT200,由于灰铸铁脆性高硬度低,但是铸造性能高,切削加工性能优良,所以毛坯可选择为铸造的方法。
为保证表面粗糙度,则可选择为砂型铸造法。
虽然没有要求是否大批量生产该零件,但是砂型铸造法可以为大批量生产提供效率保证。
并且,为消除残余应力,铸造后还应安排人工时效处理。
通过计算零件的长度宽度高度,我们将毛坯定为长83mm,宽37mm,高62mm,这样就把毛坯确定下来了。
零件毛坯图
三制订零件的机械加工工艺路线
在制定工艺方案时,我们需要对工序进行合理的划分,对基准进行选择,对工序集中度进行确定,对加工阶段进行划分,对加工方法进行确定。
(一)定位基准的选择
精基准选择:
此零件大部分将采用统一的定位基准,这样有利于保证连杆盖加工精度,其余各面孔的加工也能用它定位,这样使工艺路线遵循了“基准统一”原则,而且端面的面积,定位也比较稳定,夹紧方案也比较简单,可靠,操作方便。
粗基准选择:
选中间不加工的面,可保证对称,比如36mm上端面与28mm下端面。
“互为基准“原则当两个表面相互位置精度及尺寸、形状精度都要求较高时,可采用“互为基准”方法,反复加工。
所选的精基准应能保证定位准确、夹紧可靠、夹具简单、操作方便。
加工阶段会按照加工路线分,其中需要注意的是Φ18孔Φ
16孔的两个孔由于孔的直径较大,所以需要先打中心空,再进行
扩孔,镗孔。
(二)机械加工工艺路线制订:
工序一铸造毛坯
工序二清砂
工序三时效处理
工序四选择上端面和φ28的侧面
为基准,粗铣φ22mm下端面
工序五选择下底面和φ28的侧面
为基准,粗铣φ22mm上端面
工序六选择下底面、φ28的侧面
和宽度为22mm左侧面为基准,钻φ11m的孔
工序七选择下底面、φ11的孔和
宽度为22mm的小平面为基准
1.粗铣φ28mm外圆前端面
2.粗铣φ28mm外圆后端面
3.粗铣φ26mm外圆前端面
4.粗铣φ26mm外圆后端面
工序八选择下底面、宽度22mm的
左侧面为基准,其端面为辅助定位基准
1.钻削φ18的孔
2.钻削φ16的孔
工序九选择上顶面和φ28的侧面
为基准,半精铣φ22mm下端面
工序十选择下底面、φ18的孔及其
另一端面为基准
1.半精铣φ28mm的前端面
2.半精铣φ28mm的后端面
工序十一选择下底面、φ11的孔及其
端面为基准
1.扩φ18的孔
2.粗精铰φ18的孔
工序十二选择下底面、φ18的孔及φ
16的端面为基准
1.扩φ16的孔
2.粗铰φ16的孔
3.精铰φ16的孔
工序十三选择每个倒角面的另一侧面
和下底面为基准
1.对孔φ18和φ16的前侧
面进行45度倒角
2.对孔φ18和φ16的后侧
面进行45度倒角
工序十四选择上顶面、φ18的孔及φ
28的侧面为基准,钻φ3的孔
工序十五钳工去毛刺
工序十六终检
(三)选择加工设备及刀,夹,量具
由于生产类型为大批生产,故加工设备宜以通用机床为主,辅以少量起作用机床。
其生产方式为专用机床加专用夹具为主,辅以少量专用流水生产线,工作在各机床上的装卸及各机床的传送均由人工完成。
粗铣下端面,考虑到工件的定位夹紧方案及夹具结构设计等问题,采用立铣,选择Z52K立式铣床,选择直径D为φ60mmrc类刀,量具用游标卡尺。
粗精铣上端面,选择与铣床下端面相同的铣床X52K采用精铣床专用夹具及游标卡尺,刀口形直尺。
精铣下端面,同以上相同的铣床,夹具量具。
钻φ11mm孔,先用摇臂式钻床Z3025,采用锥柄麻花钻。
选择X52K立式铣床,选择直径D为200mm的C类可转位面铣刀,专用夹具和游标卡尺。
半精铣床M,N面,由于定位基准的转换,宜采用卧铣,选择X62W卧式铣床,选择与粗铣相同型号的刀具,采用精铣专用夹具和游标卡尺,刀口型直尺。
粗铣p面q面采用卧式双面组合铣床,因切削功率较大,故采用功率为5.5kw的ITX32型铣削头,选择直径为φ160mm的C类可转位铣刀,专用夹具,游标卡尺。
气门摇臂轴支座加工工艺装备选用
工序号
机床设备
刀具
量具
工序1铸
游标卡尺
工序2检
游标卡尺
工序3热处理
游标卡尺
工序4铣
卧式铣床X61
硬质合金端铣刀
游标卡尺
工序5铣
卧式铣床X61
硬质合金端铣刀
游标卡尺
工序6钻
立式钻床Z525
直柄麻花钻
¢11
卡尺、塞规
工序7铣
卧式铣床X61
硬质合金端铣刀
游标卡尺
工序8铣
卧式铣床X61
硬质合金端铣刀
游标卡尺
工序9钻
TX617卧式镗床
麻花钻、扩钻、机用铰刀
内径千分尺,塞规
工序10钻
TX617卧式镗床
麻花钻、扩钻、机用铰刀
内径千分尺,塞规
由于所查得的机械加工余量适用于机械加工表面
,
的加工表面,机械加工余量要适当放大。
分析本零件,除了¢18和¢16的
外,没有一个加工表面的表面粗糙度是小于1.6的,也就是所有的加工表面
,因此一般情况下这些表面的毛坯尺寸只需将零件的尺寸加上所查得的余量值即可,但是由于大部分表面加工都需经过粗加工和半精加工,因此余量将要放大,这里为了机械加工过程的方便,除了孔以外的加工表面,将总的加工余量统一为一个值。
如下表:
毛坯尺寸及机械加工总余量表
加工
表面
基本
尺寸
铸件尺寸
公差
机械加工总余量
铸件
尺寸
¢22上端面
42mm
2.6
4
50
36mm下端面
36mm
2.6
4
44
¢28前端面
37mm
2.6
4
45
¢28后端面
37mm
2.6
4
45
¢26前端面
16mm
2.2
4
24
¢26后端面
16mm
2.2
4
24
(四)确定设计方案
从对工件的结构形状分析,该工件上端面下端面均加工过,所以下端面为定位记基准,可限制三个自由度,φ28圆柱右侧用一开口V型块定位,可限制两个自由度,零件左侧用一V型块定位夹紧,这样可以保证定位准确,夹紧可靠。
夹具以夹局安装面,内六角螺钉,定位销定位,用T型槽螺栓连接。
本道工序的夹具应先用手动夹紧,手动回转,使夹具简单,操作方便。
表面轮廓是在一次装夹下完成加工的,定位精度由夹具保证。
此外,夹具还应标注形位公差。
(五)查询加工余量
零件的表面加工方法的选择
根据本零件图上所标注的各加工表面的技术要求,查《机械制造工艺设计手册》,,最后确定本零件各加工工序的余量:
机械加工工序间加工余量表
工序号
工步号
工步内容
加工余量/mm
工序4
1
粗铣¢22上端面
4
工序5
1
粗铣36mm下底面
3
2
半精铣36mm下底面
1
工序6
1
钻¢11通孔
11
工序7
1
粗铣¢28前端面
3
2
粗铣¢26前端面I
4
3
半精铣¢28前端面F
1
工序8
1
粗铣¢26后端面J
4
2
粗铣¢28后端面G
3
3
半精铣¢28后端面G
1
工序8
1
钻¢17的通孔
17
2
扩孔至¢17.85
0.85
3
粗铰至¢17.94
0.09
4
精铰至¢18H9
0.06
工序10
1
钻¢15通孔
15
2
扩孔至¢15.85
0.85
3
粗铰至¢15.95
0.10
4
精铰至¢16H9
0.05
工序11
1
钻¢3偏10°内孔
3
(六)工艺卡制订:
气门摇臂轴支座夹具设计
指导老师:
张俊纪
学生:
郎韵旭
学号:
20103921
日期:
2012.9.12
夹具设计的任务和目的
夹具设计是机械制造技术基础课程的一个重要实践环节,它要求学生会全面地综合运用本课程及其有关选修课程的理论和实践知识进行工艺及结构的设计。
设计任务
本次设计是对气门摇臂轴支座¢11孔加工的钻床夹具设计。
气门摇臂轴支座¢11孔加工专用夹具设计
为了提高劳动生产率,保证加工质量,降低劳动强度,需要设计专用夹具。
本次将为¢11孔加工设计专用夹具,本夹具将用于Z525立式钻床,刀具为硬质合金直柄麻花钻。
一.确定夹具的结构方案
1.确定定位方案,选择定位元件
根据我们所选择的工序来详细观察零件图,根据图中零件所要求的位置尺寸,以及形位精度要求,来确定夹具的结构方案。
本道工序的¢11孔的位置精度要求不高,只要与¢22外圆中心线同轴即可,且没有同轴度要求,且¢11孔德尺寸精度要求不高,故可以直接采用¢11的钻头钻削即可。
由于¢11孔表面粗糙度为12.5,故只需钻削加工即可达到要求。
该工序零件的装夹可以采用典型的“六点定位”原则进行装夹。
由于36mm下端面为该工件的主要定位基准,故以36mm下端面为主定位面,可以采用两个支承板进行定位。
由于¢28的外圆前或后端面较大,故可以以¢28外圆后端面做为导向面,可以采用与36mm下端面相平行的两个定位销进行定位,以¢28外圆柱面左端为止推面,可以采用固定式定位销进行定位。
2.确定导向装置
由于本工序的¢11孔加工精度不高,可以采用一次钻削加工即可达到尺寸精度和表面粗糙的要求,但钻孔时需要钻套来保证钻削加工时钻头的位置,从而保证¢11孔的位置精度。
由于该零件为大批大量生产,钻套有可能会磨损。
故可以采用可换钻套。
如装配图所示可换钻套与衬套的配合尺寸为¢18F7/m6,衬套和钻模板的配合尺寸为¢22F7/n6.
3.确定加紧机构
在机械加工工艺设计中,已经确定气门摇臂轴支座的生产类型为大批量生产,故在确定夹紧机构时,应该做到装夹方便、省时,省力的要求,在此工序夹具中选择螺旋夹紧机构夹紧工件。
如夹具装配图所示,在零件的前端夹具体上设计一个螺旋夹紧机构,通过转动手柄使夹紧元件的圆柱端面压紧¢28
外圆的前端面,从使零件在夹具体上被夹紧。
当加工完毕后,只需松动螺旋夹紧机构的手柄,零件即可从右端取出。
二.夹具体的设计
夹具体的设计应通盘考虑,使上述各部分通过夹具体能够有机的联系起来,形成一个整体。
考虑夹具与机床的连接,因为是在立式钻床床上使用,故不需要定向键,只需利用螺栓、螺母通过工作台上的T型槽与夹具体上的U型槽将夹具体夹紧即可;考虑到36mm下端面是用两个支承板进行定位的,故安装支承板位置的夹具体面需要加工,为了减少加工面积可以设计一个凸起4mm的方形凸台便于加工;考虑到便于排屑问题应在夹具体与工件¢11孔对应的地方钻削一个¢12的通孔。
考虑到在工件¢28外圆面得左端有一固定式定位销,故在夹具体上安装定位销的部位应由一凸起的加工圆台,便于定位销的定位和安装;考虑到夹具体的凸起方台和凸起圆台的加工,故在零件后面的定位销固定板应做成是可拆卸的,便于凸台的加工;由于夹具体的材料为铸件塑性较差、脆性较高,故不易进行螺纹加工,需要加工螺纹的地方应预留一个螺纹衬套孔便于螺纹衬套的安装。
三.方案选择
根据图纸要求,为保证加工质量,在工件上钻孔,工序基准应与设计基准相同。
工序基准为:
11、36×22底平面、
和
圆柱端面。
方案一:
工件以底平面作为主要定位面,限制3个自由度,以
孔定位一个移动自由度和一个转动自由度,还有一个移动自由度由短定位螺钉在
圆柱面定位。
采用螺旋移动压板式夹紧。
如图:
方案二:
工件以
孔作为主要定位面,限制4个自由度,底平面小端面,定位1个自由度,
圆柱面用短定位螺钉定位一个移动自由度。
直接采用心轴螺旋夹紧。
如图:
综上,进行两方案比较。
本工序的主要加工要求是
、
及保证两孔的距离和底平面的距离并保证两孔的中心轴与底平面的平行度。
两孔的精度和距离要求由钻模板保证。
而余下的就由定位方案决定。
方案一工件以底平面作为主要定位面,能保证两孔的中心轴与底平面的距离,也能保证两孔与底平面的平行度。
定位基准与工序基准重合。
方案二工件以
孔和底面小端面定位,
孔的精度不高定位4个自由度误差较大,而且长心轴在使用过程中也容易磨损,装夹费时,所以选用方案一。