钢箱梁加工制作方案2.docx
《钢箱梁加工制作方案2.docx》由会员分享,可在线阅读,更多相关《钢箱梁加工制作方案2.docx(14页珍藏版)》请在冰点文库上搜索。
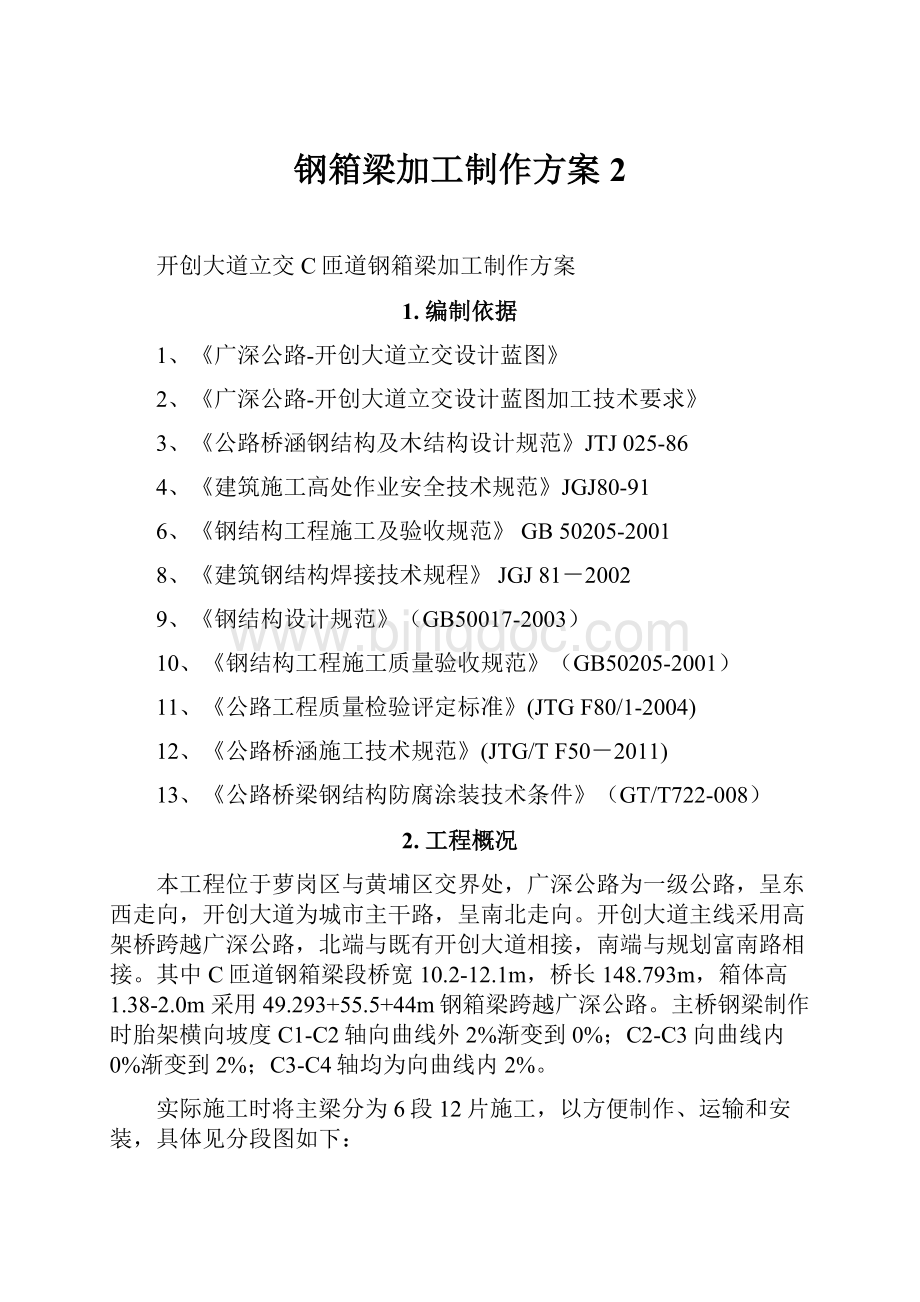
钢箱梁加工制作方案2
开创大道立交C匝道钢箱梁加工制作方案
1.编制依据
1、《广深公路-开创大道立交设计蓝图》
2、《广深公路-开创大道立交设计蓝图加工技术要求》
3、《公路桥涵钢结构及木结构设计规范》JTJ025-86
4、《建筑施工高处作业安全技术规范》JGJ80-91
6、《钢结构工程施工及验收规范》GB50205-2001
8、《建筑钢结构焊接技术规程》JGJ81-2002
9、《钢结构设计规范》(GB50017-2003)
10、《钢结构工程施工质量验收规范》(GB50205-2001)
11、《公路工程质量检验评定标准》(JTGF80/1-2004)
12、《公路桥涵施工技术规范》(JTG/TF50-2011)
13、《公路桥梁钢结构防腐涂装技术条件》(GT/T722-008)
2.工程概况
本工程位于萝岗区与黄埔区交界处,广深公路为一级公路,呈东西走向,开创大道为城市主干路,呈南北走向。
开创大道主线采用高架桥跨越广深公路,北端与既有开创大道相接,南端与规划富南路相接。
其中C匝道钢箱梁段桥宽10.2-12.1m,桥长148.793m,箱体高1.38-2.0m采用49.293+55.5+44m钢箱梁跨越广深公路。
主桥钢梁制作时胎架横向坡度C1-C2轴向曲线外2%渐变到0%;C2-C3向曲线内0%渐变到2%;C3-C4轴均为向曲线内2%。
实际施工时将主梁分为6段12片施工,以方便制作、运输和安装,具体见分段图如下:
构件清单如下:
构件编号
长度(m)
宽度(m)
高度(m)
重量(t)
1#主梁
25.2
5.04
1.6
48.4
2#主梁
24.3
5.04
1.6
48.7
3#主梁
23.1
5.04
2.0
51.5
4#主梁
23.1
5.04
2.0
51.5
5#主梁
25.4
5.04
2.0
56.7
6#主梁
25.6
5.04
2.0
57.1
7#主梁
24.8
4.84
2.0
54.0
8#主梁
26.7
4.84
2.0
57.0
9#主梁
18.5
4.84
2.0
41.7
10#主梁
20.6
4.84
2.0
44.1
11#主梁
20.7
4.84
2.0
41.0
12#主梁
22.7
4.84
2.0
43.2
C1横梁
10.3
1.5
1.4
10.3
C2横梁
10.3
3.8
2.0
25.1
C3横梁
12.0
4.4
2.0
31.2
C4横梁
10.4
1.8
1.4
12.4
考虑本工程箱体结构
3.施工工艺及质量目标
钢箱梁制作的质量目标是:
通过严格的生产管理制造满足图纸设计要求和满足规范要求的合格产品。
为保证达到质量目标各个生产工序的组织及质量检验如下:
1、钢箱梁分段划分:
见附图“全桥分段示意图”。
2、主要工艺流程:
技术准备主胎架制作构件下料、矫正顶、底板拼接无损探伤上胎架组装底板、加劲肋、横隔板、腹板、顶板焊接焊缝检查、探伤分段主尺度检查、火工矫正油漆涂装。
3、各分项工序说明、检验及质量要求:
(1)技术准备
a.图纸会审,详细阅读设计蓝图,对于蓝图不明确的问题填写图纸会审表格,经设计复核后给出答复。
b.材料计划,根据设计蓝图计算出该项目所需钢材材料,交物质部采购。
c.根据设计蓝图整体放样,在设计蓝图预拱度基础上添加焊接变形量。
d.材料进场,取样第三方材料送件及做焊接工艺评定。
(2)材料采购:
a.开创大道C匝道钢箱梁材料为Q345qC和Q235qC材质,钢箱梁顶、底板、腹板和墩顶横梁采用Q345qC钢板,其余加劲肋、隔板均为Q235qC钢板。
顶板为18-24mm,顶板U肋为6mm,I型加劲板为12mm,;底板为18-24mm,底板I型加劲板为12mm,边腹板厚为18mm,中腹板为16mm。
翼缘与腹板相接处采用6mm板做封板,隔板均为14mm。
b.钢箱梁所用钢板的钢号、规格应符合图纸和排版的规定,并备有合格证书,钢板进厂应进行复检并记录各批钢板的炉号,按规定每炉号不大于60吨确定数量送第三方检验,钢板厚度偏差:
板厚(mm)
5≤δ<8
8≤δ<16
16≤δ<30
公差(mm)
+0.8
+0.8
+1.3
公差(mm)
-0.4
-0.5
-0.6
钢板水平度允许偏差:
板厚(mm)
允许的不平度偏差(mm)
测量长度1000mm
测量长度2000mm
5≤δ<8
8
12
8≤δ<16
7
11
16≤δ<30
7
10
钢板表面质量:
钢板和型钢表面不应有裂纹、气孔、结疤、折叠、夹杂,钢材不应有分层。
如有上述表面缺陷允许清理,清理深度从实际尺寸算起,不应大于钢材厚度公差之关并应保证最小厚度,清理处应平滑无棱角。
对处理合格后的钢板进行打砂除锈,喷底漆预处理,车间底漆干膜厚度20~30μm。
c、焊条、焊剂、焊丝必须备有合格证书,碱性低氢型结构钢焊条应在350º~400ºC烘干1~2小时,烘干的焊条应放在100º~150ºC保温筒内随用随取。
埋弧焊剂应在350ºC烘干1~2小时,并防止使用过程中受潮。
(3)钢板的矫正,一般在冷态下用辊式矫正机或压力机进行,若在平台上用手锤矫正时,锤痕深度不超过以下规定:
对钢板在平面上为0.5mm,在立面上为1mm。
弯曲度较大的钢板在热态下矫正时,加热温度应控制在600~800ºC之间,矫正后钢材温度应缓慢冷却。
(4)下料、制作样板及号料时,应考虑焊接结构件的收缩量及装配间隙。
剪切钢板剪切面斜度不得大于1:
8,边棱上的堆积物、毛刺和凹凸应铲除、毛刺高度不得大于0.5mm,刻痕不得大于1mm。
气割钢板在厚度方向的偏斜差,板厚δ≤24mm时不超过2mm,δ>24mm时不超过2.5mm;切割边局部咬边深度不超过3.5mm,咬边长度不超过200mm,且总计咬边长度不得超过切割长度的20%,号料尺寸允许偏差±1mm,自动或半自动切割允许偏差±1.0mm,手工气割允许偏差±2mm,气割完成后应清除毛刺、割渣、波纹、崩坑等缺陷应修磨匀顺。
(5)胎架制作:
按图纸尺寸、圆弧、半径、预拱度曲线1:
1比例制作胎架。
胎架必需具备足够的平整度、强度和刚度并需检验合格后方可投入使用。
胎架应在平实场地内制作、架设,主骨架用[20钢拼成方形,间距1~1.2m均匀分布,并用角钢连成整体,槽钢上焊接δ20mm钢板作调整板,间距1m,高度按预拱度曲线,由水平仪测控,偏差不得超过2mm。
(6)拼板:
顶、底板和腹板的对接焊缝应相应错开200mm以上,长度方向板的拼接不小于1m,宽度方向板的拼接不小于300mm。
顶、底板和腹板的对接焊缝按Ⅰ级要求进行,采用单面坡口50º角钝边3mm,CO2焊打底,埋弧焊盖面,反面用碳刨清根,埋弧焊盖面完成。
边腹板与顶底板做熔透焊,其余焊缝为双面角焊缝。
(7)装配:
装配必须在检验合格后的胎架上进行,顶、底板单元应探伤合格、矫正完成后上胎架,装配前必须将各焊接及距焊接边缘20mm(自动焊30mm)范围内的铁锈、污垢、毛刺等清除干净。
装配时的临时点焊若是以后焊缝的一部分,则所用焊条及其要求应和正式焊缝一致。
在底板上划加劲肋、横隔板、腹板的定位线偏差不大于1.0mm。
加劲肋装配高度误差0~0.5mm。
垂直度误差≤0.5mm,两竖板中心偏移量≤2.0mm;横隔板和腹板的装配高度差±3.0mm,垂直度差≤3.0mm,中心偏移≤2.0mm,对角线差≤1.0mm。
(8)焊接:
重要构件的焊接必须由持证焊工担任。
焊接的顺序应保证使焊接构件的收缩应力和变形趋于最小,顶、底板焊接从中间往两端。
对接焊缝的首尾应加与母材等厚,相同坡口的工艺板,引弧与灭弧均应在工艺板上进行,以免产生未焊透及火口等缺陷。
焊接后必须及时将熔渣、焊瘤及飞溅清除后才进行下一次焊接。
埋弧自动焊后为保证缓冷,焊药应缓回收。
(9)焊接变形的矫正:
热态下不准在300~500ºC时进行机械矫正和锤击,以免产生脆裂,禁止在同一部位重复加热。
用气体火焰局部加热矫正时,其加热温度应在700~850ºC之间,不宜超过900ºC。
(10)焊接质量检查,所有焊缝都应进行外部检查,以判断有无下列不允许存在的缺陷:
烧穿、裂纹、鳞状高度不均匀,焊缝间断,露出弧坑及深度超过0.5mm。
4.工艺评定
1.焊接工艺评定
1)焊接工艺评定是编制焊接工艺的依据,应在钢箱梁制造开工前完成。
评定试验用的母材应与产品一致,尽可能选用C.S.P含量上限制备试板。
试板焊接时,要考虑坡口根部间隙、环境和约束等极限状态,以使评定结果具有广泛的适用性。
焊缝力学性能等方面和母材匹配。
焊缝的冲击韧性指标原则上与母材相等,按GB/T1591—2008标准执行。
2)根据本桥设计图纸的规定,编写《焊接工艺评定任务书》。
根据批准的焊接工艺评定任务书,模拟实际施工条件,逐项进行焊接工艺评定试验。
3)针对本桥钢箱梁的接头形式,初步拟订焊接工艺评定方案。
4)焊接工艺评定试验提供最终报告,经监理工程师审查、批准生效,并在生产中跟踪、检查、补充和完善施工工艺。
如生产过程中某焊接工艺产生不稳定低于质量要求时应立即终止使用。
5)试验报告按规定程序批准后,根据焊接工艺评定试验报告编写各种接头的焊接工艺指导书。
焊接工艺指导书经监理工程师批准后,根据焊接工艺指导书的内容组织施工。
2.工艺文件的编制
按照《技术总说明》和设计文件的要求,编制各个工序的工艺文件,用于指导生产,控制施工质量。
5.钢桥组装焊接工艺
拼装方式的选择
开创大道钢箱梁截面尺寸为1#、2#、3#、4#(5100×2000×25000)mm、5#、6#、7#、8#(5100-6050×2000×25000)mm和9#、10#、11#、12#(6050×2000×25000)mm,为了拼装方便且便于控制,采用倒装的形式,以顶板为基准面进行拼装,倒装时保证腹板和地面垂直,并严格按照设计起拱曲线控制起拱线形并添加千分之一的焊接变形量。
拼装的顺序是先铺设顶板,检验合格后安装箱梁内部横隔板,然后安装隔板,调整好线型后,安装腹板,最后安装底板。
开创大道钢箱梁6个分段12个片体,拼装时第一轮1#和2#分、3#和4#、5#和6#、7#和8#、9#和10#、11#和12#两段进行整体制作。
典型梁段拼装
现以典型标准段的拼装为例来进行阐述钢桥拼装的一般过程,其他分段的拼装过程类似。
步骤一:
拼装胎架的搭设
步骤二:
拼装顶板
步骤三:
安装隔板
步骤四:
安装中间腹板、中间内隔板的安装
步骤五:
安装两端腹板
步骤六:
安装底板
6.涂装工艺
6.1涂装技术要求
部位
配套编号
涂层
涂料品种
(防锈等级及粗糙度)
颜色
道数/最低干膜厚度(um)
所有钢板表面
表面预处理
喷砂处理
(防锈等级:
sa2.5级)
车间底漆
高超耐热车间底漆
灰色
1/20
主体钢结构外表面
二次表面处理
喷砂处理
(防锈等级:
sa3.0级)
(粗糙度:
Rz30um-80um)
S04
底涂层
环氧富锌底漆
灰色
1/60
中间涂层
环氧(厚浆)漆
灰色
2/100
面涂层
丙烯酸脂肪族聚氨酯面漆
浅灰色
2/80
总干膜厚度
240
主体钢结构内表面(含U肋内外表面)
二次表面处理
手工机械除锈
防锈等级:
sa3.0级)
(粗糙度:
Rz30um-80um)
S13
底涂层
环氧富锌底漆
灰色
1/50
面涂层
环氧(厚浆)漆
浅灰色
1/250
总干膜厚度
300
主体钢结构与砼接触面(顶板上表面)
二次表面处理
喷砂处理
(防锈等级:
sa3.0级)
(粗糙度:
Rz30um-80um)
S18
底漆
热喷铝
1/100
总干膜厚度
100
6.2喷砂、油漆施工顺序详述
1)打砂前检查分段表面,确认没有焊瘤、飞溅、毛刺等缺陷,自由边锐角打磨至R2。
2)清除分段表面的积水及杂物,并用清洁剂清除钢材表面的油脂、油污。
3)清除钢材表面的油污、水份、灰尘、盐分、焊接烟尘、粉笔或油漆记号。
4)分段用平板车运进油漆车间,放在专用支墩上。
5)准备通风、照明设备和脚手架。
6)保护不需打砂油漆的构件及设备。
7)环境控制:
检查并记录气温、钢板温度、相对湿度、油漆温度。
相对湿度不超过85%,钢板温度必须高于露点3℃。
当环境状况达不到上述要求时停止施工或加开除湿设备。
8)选用10~30目的铜矿砂,确保打砂后的粗糙度在30~80um之间。
9)检查压缩空气的压力、油水分离状况等,确保贮气罐内的空气压力在6~7㎏/cm2,且油水分离器工作正常。
10)砂枪距钢材表面约20~30cm,喷砂角度保持在60~80°,匀速移动,每分钟约0.5~1.0m。
11)打砂检查合格后,用干燥、清洁压缩空气吹去表面砂粒,并用工业吸尘器除尘。
12)喷砂合格后,在尽可能短的时间内喷底漆,一般要求不超过6小时。
喷漆后8小时内防止雨淋。
13)采用高压无气喷涂设备进行喷涂施工,大面积喷涂前对焊缝、边角、难以喷涂到的部位先进行预涂。
为缩短打砂表面在空气中的曝露时间,底漆喷涂前可以不进行预涂,但底漆干燥后应进行补涂。
14)喷漆前用100毫米宽的胶纸保护待焊接部位,,不需油漆的构件和设备也应预先保护。
15)每道油漆的喷涂参数见附页,此为指导现场施工的技术依据。
16)按照附页中的技术参数完成底漆、中间漆、面漆的施工,喷涂下道油漆前先对上道油漆缺陷进行修补、清洁,并先进行预涂。
17)整个分段油漆完工后,折除脚架和照明设备,用600T平板车把分段运到储存场地。
18)清除车间内的废砂,等待下一个分段进入。
6.3.喷漆施工的操作要领
1)领料检查:
核对所领材料是否为待施工部位油漆配套中规定的材料,检查油漆桶密封是否完好,若有破损、渗漏、涨桶现象,应在征得油漆供应商许可的情况下才能使用。
2)开桶检查:
若发现有凝胶、结快、变色等现象,则基本断定涂料已变质,应当废弃。
但轻微的沉淀结快经充分搅拌均匀后仍可使用。
3)开桶:
用风动搅拌机把基料、固化剂分别搅拌均匀,按照产品说明书中的混合比例把固化剂加入到基料中,搅拌均匀。
如有需要,再按产品说明书中的要求加入适量配套稀释剂,搅拌均匀。
4)喷涂施工前对待焊接的焊缝、不需涂漆的构件及设备进行保护。
5)一般采用先上后下、先内后外、先难后易的原则进行喷涂施工,喷涂时注意每道漆膜之间的搭接,一般搭接宽度为喷幅的1/2。
6)喷嘴距离构件表面的距离一般为30mm左右,尽量使喷枪与被涂构件表面保持垂直,运行速度均匀,避免因过快过慢引起膜厚不够或流挂、超厚现象。
7)喷涂拐角处,喷枪要对准中心线,确保两侧都得到均匀的膜厚。
8)喷涂过程中应经常使用湿膜卡,用于控制干膜厚度。
9)喷涂过程中要随时检查刚刚喷过的漆膜是否存在针孔、汽泡、鱼眼、流挂等缺陷,如有应马上停止喷涂施工,分析原因,检修设备,并试喷成功后再继续喷涂。
如发现露底时应立即补喷。
10)喷涂结束后应及时用清洁剂清洗喷漆设备,尤其是喷漆泵和喷枪,防止油漆留在其中固化导致设备无法正常使用。
11)喷涂完工后,依据产品说明书中的干燥时间等待油漆充分干燥,等油漆干燥后及时对露底、膜厚不够部位进行补涂,并处理涂层上的流挂、颗粒、桔皮等缺陷,并对焊缝、边角及难以喷涂部位进行预涂,准备下道油漆的施工。
6.4损坏区域修补程序
在吊装、运输分段时要警惕,避免破坏涂层,如果涂层已有损坏,按下述程序修补:
1)缺陷例如针孔、气泡、流挂、流淌、过喷、桔皮、鱼眼等应采用细砂纸轻轻打磨(手工或动力工具)缺陷边缘,用吸尘器或其它合适方法去除灰尘和附着不牢的碎片,然后补涂相同油漆。
2)露出钢材基底损坏部位用动力工具打磨至Sa3级,其它需补涂的部位首先除去油污、灰尘、可溶性盐,临近至少25mm的完好涂层用砂纸打磨成45°的坡度。
3)没有露出钢材基底的损坏区域首先除去油污、灰尘、可溶性盐,接着用砂纸把漆膜拉毛。
补涂的油漆的周边应覆盖完好的涂层25mm,后续补涂的涂层都应盖住前道涂层且再向周边延伸25mm。