基于ansys的框架式汽车大梁校正仪设计本科毕业论文.docx
《基于ansys的框架式汽车大梁校正仪设计本科毕业论文.docx》由会员分享,可在线阅读,更多相关《基于ansys的框架式汽车大梁校正仪设计本科毕业论文.docx(78页珍藏版)》请在冰点文库上搜索。
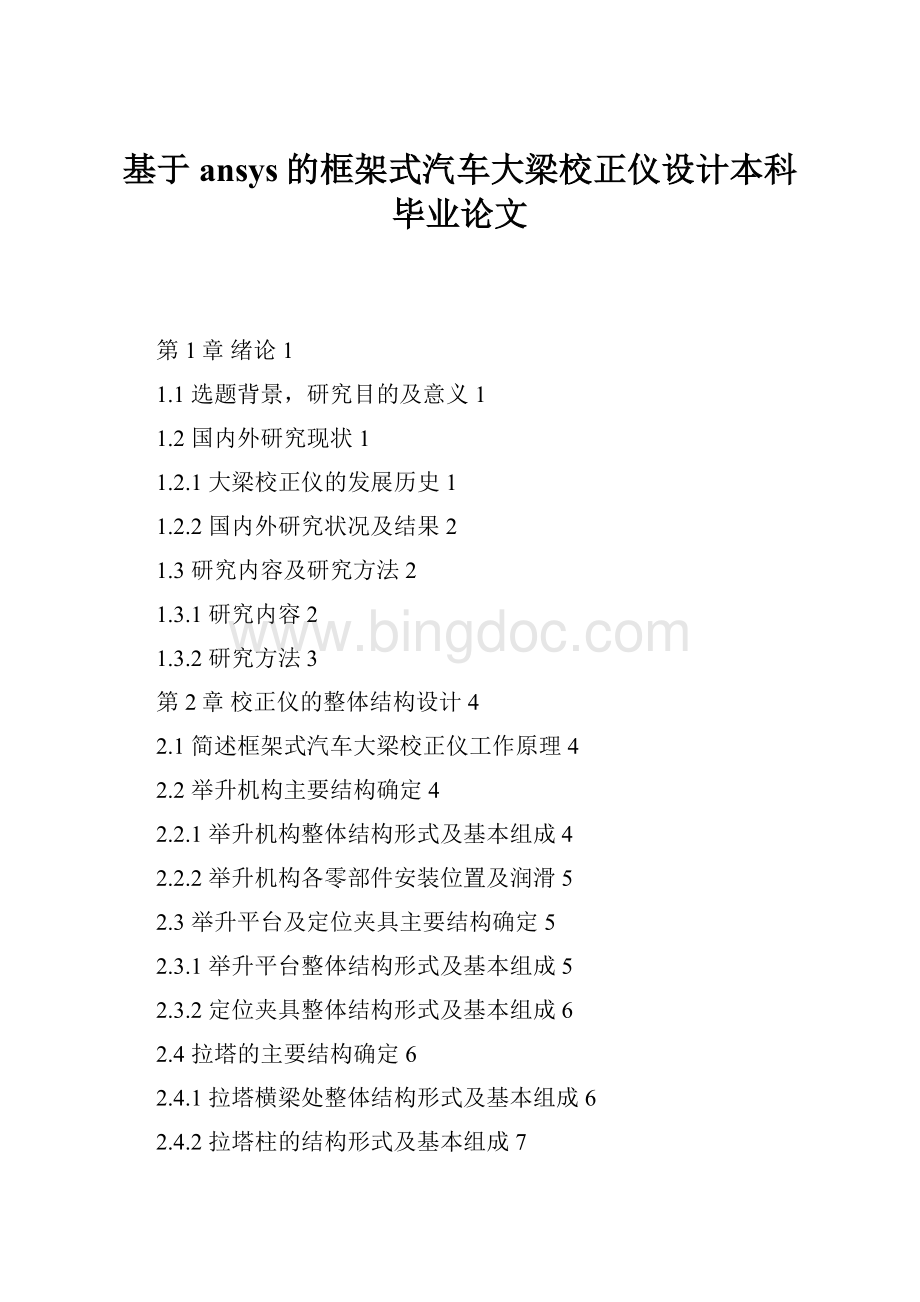
基于ansys的框架式汽车大梁校正仪设计本科毕业论文
第1章绪论1
1.1选题背景,研究目的及意义1
1.2国内外研究现状1
1.2.1大梁校正仪的发展历史1
1.2.2国内外研究状况及结果2
1.3研究内容及研究方法2
1.3.1研究内容2
1.3.2研究方法3
第2章校正仪的整体结构设计4
2.1简述框架式汽车大梁校正仪工作原理4
2.2举升机构主要结构确定4
2.2.1举升机构整体结构形式及基本组成4
2.2.2举升机构各零部件安装位置及润滑5
2.3举升平台及定位夹具主要结构确定5
2.3.1举升平台整体结构形式及基本组成5
2.3.2定位夹具整体结构形式及基本组成6
2.4拉塔的主要结构确定6
2.4.1拉塔横梁处整体结构形式及基本组成6
2.4.2拉塔柱的结构形式及基本组成7
2.5其它附件7
2.6确定框架式大梁校正仪各结构尺寸及材料7
2.6.1建立待修汽车基本参数模型8
2.6.2校正仪底部结构部分主要尺寸及材料的确定8
2.6.3校正仪中间结构部分尺寸及材料的确定8
2.6.4校正仪上部平台结构尺寸及材料的确定9
2.6.5定位夹具的尺寸及材料的确定11
2.6.6拉塔组件的尺寸及材料的确定12
2.6.7方凳及斜坡板凳的尺寸确定13
2.7设备各部件质量的估算及设计举升质量13
2.7.1估算拉塔组件的质量14
2.7.2估算平台上设备的质量14
2.7.3估算平台中部的质量14
2.7.4估算底板处的质量15
2.7.5实际设计举升质量15
2.8本章小结15
第3章校正仪的力学分析及校核16
3.1双铰接剪刀式举升机构的力学模型16
3.1.1举升机构力学模型建立与分析16
3.1.2举升机构主要关系参数的确定17
3.2液压机构力的分析与计算17
3.2.1确定载荷与液压缸推力的关系17
3.2.2计算液压缸的推力18
3.3举升机构的力学分析与计算19
3.3.1举升机最低状态时,各臂受力情况19
3.3.2举升机举升到最高位置时,各臂受力情况20
3.4定位夹具及拉塔的力学分析与计算22
3.4.1定位夹具的受力分析22
3.4.2拉塔的受力分析22
3.5主要零部件的强度校核23
3.5.1举升臂AOB的强度校核23
3.5.2举升臂COD的强度校核25
3.5.3液压缸上端支承轴的强度校核27
3.5.4连接举升臂销轴的强度校核27
3.5.5平台内横梁的强度校核28
3.5.6定位夹具的强度校核29
3.5.7定位夹具支撑横梁的强度校核30
3.5.8拉塔的强度校核31
3.5.9拉塔处液压缸支撑销轴的强度校核32
3.6本章小结33
第4章校正仪液压系统的选择与计算34
4.1液压系统的选择34
4.1.1液压系统的介绍34
4.1.2液压系统的选型34
4.2液压系统的计算35
4.2.1举升处液压缸行程的计算35
4.2.2举升处液压系统工作压力的计算36
4.2.3关于拉塔处液压系统的相关选择36
4.3本章小结36
第5章校正仪三维建模与整机装配37
5.1CATIA软件简介37
5.2利用CATIA进行三维建模38
5.2.1底坐板的建立38
5.2.2举升臂AOB的建立39
5.2.3液压缸支承轴的建立39
5.2.4上平台的建立40
5.2.5夹具的建立40
5.2.6拉塔柱的建立42
5.3整机装配42
5.3.1CATIA装配功能概述43
5.3.2装配的CATIA零件图43
5.3.3CATIA整机装配图及爆炸图48
5.4本章小结50
第6章校正仪主要零部件有限元分析51
6.1ANSYS有限元分析软件介绍51
6.2ANSYS与CATIA接口的建立51
6.3利用ANSYS对主要零部件进行分析52
6.3.1定位夹具卡钳的有限元分析52
6.3.2液压缸支撑轴的有限元分析56
6.3.3举升臂的有限元分析59
6.3.4拉塔柱的有限元分析62
6.4本章小结65
结论66
参考文献67
致谢68
附录A69
附录B72
附录C73
附录D74
第1章绪论
1.1选择背景、研究目的及意义
随着汽车市场的不断发展与壮大,与之相协调的汽车维修行业也迅速发展起来。
目前在汽车事故中对大梁及钣金的修复十分常见。
而随着对售后服务的要求的不断提升,也为了更好的发展企业,各维修厂家已经开始了激烈的服务竞争。
汽车大梁校正仪是在因交通事故碰撞所致车身损坏,以及大梁变形等的技术数据恢复中重要的维修设备。
在以往的事故后维修时,很多企业选择了更换零部件,但是这样往往会增加客户的损失及保险公司的负担。
汽车大梁校正仪的出现避免了高额的更换费用,这样既减少了顾客的损失,也可促进制造设备企业市场的发展。
利用大梁校正仪专业设备方可保证对汽车大梁的维修的质量水平。
然而对于在维修中为了保证汽车安全的定位,方便的使用,高维修水平等众多关键要素,必须设计质量及安全可靠的设备。
因此,为了满足维修企业对占地空间的要求及保证维修质量。
对框架式汽车大梁校正仪进行深入研发将对我国在这一领域发展有实质性的意义。
本课题基于计算机仿真平台,应用CAD/CAE领域比较领先的设计软件AutoCAD进行二维草图绘制,使用了当前先进的三维设计软件CATIA进行三维建模及整机装配,在产品投入生产之前运用ANSYS软件进行质量分析,可及时发现并更改设计中的缺陷,完善设计方案,减少产品开发周期,提高研发的质量和效率,为此设备的生产实际提供一些有价值的理论支持。
1.2国内外研究现状
1.2.1大梁校正仪的发展历史
汽车大梁校正仪的发展已经有了将近30年的历史。
它的出现主要是基于剪式汽车举升机的框架的改装。
由于举升机历史较长,技术较成熟,所以在80年代期间,美国及欧洲就率先通过对剪式举升机的改造而研发出框架式大梁校正仪。
九十年代欧洲通过出口到中国市场逐渐把它的产品推向亚洲地区。
90年代中期,在我国山东地区逐渐出现了很多此类设备制造企业,目前在国内市场发展史已经是标新立异。
经过几十年的发展,剪式举升机及一些定位夹具已经更新了很多代,框架式汽车大梁校正仪至今也经历了许多变化与改进。
目前欧美已经将其产品出口至全世界,我国山东地区少数企业也已经打破传统局面,将设备出口至芬兰等北欧国家。
而框架式大梁校正仪使用方便,占地空间较小,也受到很多实力雄厚的特约维修站的欢迎。
1.2.2国内外研究状况及成果
框架式汽车大梁校正仪目前是市场上主流的产品之一。
欧洲及美国目前在这方面的技术处于领先地位,并且不断的主导市场的发展方向。
所以市面上此产品主要由欧洲及美国设计制造,他们已经在精确恢复技术方面取得了很大成就。
在这其中美式大梁校正仪凭借价格优势及外观而市场占有率较高,但随着维修质量要求的提高,夹具设备的不断升级,欧式凭借其功能的强大,操作灵活及占地面积小等优势逐渐在市场上走俏。
但由于进口设备的高价格及售后服务不方便等因素,仍然只是少数大型维修企业及汽车4S店会购置进口设备。
90年代末,在我国山东地区出现了一些制造汽车大梁校正仪的中小型企业。
由于起步较晚,所以目前多数企业是借鉴国外的先进技术。
随着时间的推移,目前市场上自主的品牌已经逐渐成熟起来,并且在不断地扩大销售网络于全国,基本在各大省会城市均有销售代理,且价格范围较广,多数在3-6万元左右。
但质量水平,技术创新性等方面与进口品牌还有一定的差距,而且产品类型主要以平台式为主。
但是自主品牌却已经出口至欧洲及非洲。
由此可见目前中国汽车维修设备市场对框架式汽车大梁校正仪的需求将会不断上升。
目前框架式汽车大梁校正仪主要有以下功能特点:
(1)能实现单拉臂可多角度拉伸,同时能对事故车进行360°遥控拉伸;
(2)定位系统是模块式,能具有高通用性;(3)定位夹具高度可调,能方便上下车辆的准确定位;(4)配备举升平台和上车导板,移动支架,电脑底盘测量系统等附属件。
随着市场的发展,提高汽车大梁校正仪的高水平技术与整体制造水平是在市场上获得良好口碑的关键要素。
1.3研究内容及研究方法
1.3.1研究内容
(1)分析框架式汽车大梁校正仪的结构形式及工作原理,根据以下参数:
最大举升高度1060mm,工作台长度2300mm,工作台高度230-1060mm,工作台宽度950mm,降到最低点为230mm,拉塔工作范围360度,液压系统最大工作压力16Mpa,气源压力要求0.8Mpa,拉塔牵引最大拉力70KN,完成方案设计及质量校核计算。
利用AutoCAD完成校正仪的二维总体结构设计,然后CATIA建立三维模型,在将关键零部件模型通过专用模型数据转换接口导入ANSYS软件进行有限元分析,获得校正仪在载荷工况作用下的应力、应变及变形状,然后用CATIA整机虚拟装配。
(2)拟解决的主要问题
1)框架式汽车大梁校正仪总体方案设计;
2)利用AutoCAD完成大梁校正仪二维结构设计;
3)利用CATIA完成大梁校正仪的三维建模;
4)利用ANSYS软件对关键零部件进行有限元分析;
5)CATIA虚拟装配。
1.3.2研究流程如图1.1所示。
图1.1研究流程图
第2章校正仪整体结构设计
2.1框架式汽车大梁校正仪工作原理
框架式汽车大梁校正仪是基于举升机基础上附加定位夹具,拉塔等装配成的。
汽车通过斜坡式方凳驶上一定高度后,通过可调位置的夹具夹紧不同的汽车裙边后定位汽车。
然后驱动液压系统通过支撑横轴推举汽车至一定高度,此时因为大梁受损的部位不同,需要调整拉塔的方向。
拉塔是通过卡钳卡在平台上的,因此可实现360°范围工作。
拉塔定位后把拉链一端的钩子钩在受损部位,通过驱动另一个液压缸使拉塔向后拉动链子实现拉伸大梁的作用。
2.2举升机构主要结构确定
2.2.1举升机构整体结构形式及基本组成
本课题设计的内容主要是基于小型剪刀式举升机的结构设计,剪刀式举升机的市场较成熟,类型也很丰富。
按照剪刀的大小分为大剪式举升机(又叫子母式),还有小剪(单剪)举升机;按照驱动形式又可分为机械式、电控液压式、气液驱动式;按照安装形式又可以分为藏地安装,地面安装。
因为此次设计所要举升的重量为2t以下的乘用车,所以采用双铰接剪叉式液压驱动举升机就完全符合设计理念。
为了适合大小维修企业,对地基没有过多要求,采用平板直接放在地面安装即可。
整体结构形式草图如图2.1所示。
图2.1举升机整体结构形式
①—上平台②—举升臂③—液压系统④—滑道角钢⑤—底座⑥—固定铰支座
从整体结构来看,双铰接剪叉式举升机由举升臂、滑动装置,上下平台,电控液压系统四大部分组成。
在达到举升高度时,由于选择的液压系统中活塞杆的行程要大于实际举升所需行程,所以必须在滑道处加以挡块来限制其举升高度。
由于本次设计采用斜坡式方凳来使汽车上升到举升位置,再加之利用安全性较高的电控液压系统来控制,所以避免了另加液压缸自锁装置,即节省成本有保证安全操作。
双铰接式举升机有两组完全相同的举升臂机构,分别放于左右两侧滑轮之间。
举升机由电气系统控制,由液压系统输出液压油作为动力驱动活塞杆伸缩,带动两侧举升臂同时上升、下降、锁止。
举升机一侧上下端为焊接在横梁及底板上的固定铰支座,举升臂由销连接固定在铰支座上。
另一侧上下端为滑轮在角钢内滑动,举升臂通过轴与滑轮连接。
液压缸通过举升横向支承轴来举升整个平台,举升臂以固定铰支座一侧为支点,滑轮向内或向外滑动,使举升机上升下降,当达到适当的举升位置时,利用电控台及挡块锁止。
剪刀式举升机操作方便,结构简单且易于维修,占地面积小,适用于大多数轿车的维修,且安全可靠。
2.2.2举升机构各零部件安装位置及润滑
举升臂一侧底端通过焊接在底板上的固定支座及上部横梁上的绞支座来固定,底板是一块中间去除材料的矩形钢板,绞支座通过销轴固定举升臂,在连接处个留有间隙以便润滑及减少摩擦。
另一侧通过与举升臂焊接的短轴套进滚针轴承来实现滚动,并且在滑道加厚板及不等边角钢上涂有脂润滑剂。
每侧两个举升臂通过销轴连接,为减少剪应力的作用,在举升臂连接处焊有钢板,其中摩擦处都要油脂润滑。
液压缸底部固定在底板的固定支座上,活塞杆作用在上端支撑轴上,活塞杆由三个套筒来固定位置,并留有一定的间隙。
为了在聚生过程中更加稳定,每侧整个举升臂安装位置均在同一水平平面内,且在两侧举升臂之间焊有横向稳定板。
整个装置虽然要求装配精度不高,但是各铰接处均有一定的摩擦,所以必须采用润滑脂润滑。
2.3举升平台及定位夹具主要结构确定
2.3.1举升平台整体结构形式及基本组成
举升平台主要由一个弯成方形的钢板和焊在内部的槽型钢组成。
在两侧分别有一对卡钳及托盘卡在钢板上。
在平台中间则通过方管横梁来稳定,且在横梁上焊有固定绞支座。
在平台内壁槽钢上焊有槽型钢滑道,两侧对称焊接。
在卡钳的侧面上各焊接一个方管,作为举升梁和夹具支撑。
如图2.2所示。
①—外横梁②—托盘③—横梁卡钳
2.3.2定位夹具整体结构形式及基本组成
夹具是用来支撑整个汽车的关键零部件,通过四个卡钳分别卡住汽车的裙边。
其中为了满足不同汽车的车宽及裙边的后度差异,需要把其中一个卡钳设计为可移动式。
两个卡钳由螺栓连接。
卡钳固定在一个方形钢板上,钢板下端焊接有一个圆柱体,圆柱放在一个粗型螺栓内,螺栓可以通过伸缩来控制夹具的高度,以适应不同的车高。
夹具底端通过方形钢板焊接在一个方管上,方管套在另一个方管上,这样可以实现左右灵活移动。
结构如图2.3所示。
图2.3夹具组件主要结构形式
①—卡钳②—连接螺栓③—夹具螺栓柱④—夹具支撑柱⑤—加强筋⑥—滑动套管
2.4拉塔的主要结构确定
2.4.1拉塔横梁处整体结构形式及基本组成
拉塔横梁是用来支撑拉塔柱和液压系统的关键部件。
靠近平台一端的固定是靠一个卡钳与托盘掐在平台钢板上,其中为了满足拉塔的可旋转性,在横梁一端平板上开有三个销轴孔。
液压缸支承座焊接在横梁上,且留有一定的间隙,同时需要脂润滑减少摩擦。
横梁的另一端是连接拉塔柱的两块钢板。
如图2.4所示。
图2.4横梁组件主要结构形式
①—拉塔柱夹板②—拉塔横梁③—固定铰支座④—活动插销⑤—固定插销⑥—托盘⑦—支撑立板⑧—卡钳⑨—上平台
2.4.2拉塔柱的结构形式及基本组成
拉塔柱是整个大梁校正仪的关键所在,液压活塞杆通过推拉塔柱上的销轴来驱动拉塔,拉塔往后倾同时拉动了挂在拉塔柱上的铁链,铁链一头通过钩子来拉大梁。
拉塔柱由方管构成,其竖向焊有方块用来挂住铁链。
这个结构较为简单,但是每个衔接处及销轴连接处都需要脂润滑。
结构如图2.5所示。
图2.5拉塔柱主要结构形式
①—挡块②—拉塔立柱③—拉链④—夹板⑤液压系统
2.5其它附件
除了上述主要结构外,在汽车准备进入维修阶段时候,我们还需要将其举升至一定的高度,以便举升机将其举升。
因此需要几个长条方凳及一对斜坡式方凳,将汽车开上去之后方可进行下一步。
方凳结构简单,均为钢板与方管焊接而成(如图2.6)。
其他拉链及钩子均为选购件,满足使用强度即可,这里不做详细的介绍了。
图2.6方凳组合简图
2.6确定框架式大梁校正仪各结构尺寸及材料
2.6.1建立待修汽车基本参数模型
为了尽量满足市场常见车型的维修,本设计首先建立了一个常见乘用车车模型。
根据表2.1所列车身参数信息。
参数信息表2.1
车型
捷达先锋
吉利帝豪EC718
车身长/宽/高(mm)
4415/1674/1415
4635/1789/1470
前/后轮距
1429/1422
1502/1492
轴距
2602
2650
车重
1114
1310
最小离地间隙
137
167
本设计会根据吉利轿车和大众轿车的车身信息确定框架式大梁校正仪相关配合的尺寸适用范围。
参数信息表2.2
技术数据
数值
单位
工作台长/宽
2300/950
mm
举升高度范围
230~1060
mm
拉塔工作范围
360
°
2.6.2校正仪底部结构部分主要尺寸及材料的确定
(1)经实地参考测量及表2.1,2.2中的参数来支撑地板主要尺寸:
长1480mm,宽920mm,厚为12mm。
材料为Q235钢,为了节省材料,中间去除部分材料。
如图2.7所示。
图2.7底板结构尺寸
上图2.7为去除材料的尺寸(注:
此说明书中所有图中尺寸均代表实际尺寸,单位mm)。
(2)在底板一端焊有支座及轴承滑道,因举升装置中举升臂一端需要固定在绞支座上,而另一端为滑动装置,为了使举升臂尺寸相同,需保证其各端处于同一高度。
参考举升机的绞支座确定其主要尺寸:
高80mm,宽60mm,厚15mm。
,材料为Q235钢.销轴处孔直径为30mm(参考销轴规格),销轴长取78mm,液压缸处销轴长度100mm,中心孔距底板55mm,垫片采用GB/T848-2002,材料为标准35钢(以下销轴材料均同)。
加厚滑道厚度25mm,上面焊有角钢,其安装位置由内侧举升臂及焊接在举升臂上的短轴来确定。
2.6.3校正仪中间结构部分尺寸及材料的确定
(1)首先设定举升到最大高度时,两举升臂夹角为90°。
举升臂上支点设定在上平台中心线的位置,上平台高度钢板取90mm,底板厚度取12mm。
由此计算举升臂的长度L=(1060-90/2-12)/cos45°=1418.45mm,这里取L=1420mm,宽度取70mm,厚度取18mm,材料为45钢。
其中安装举升臂的绞支座距离取25mm(7mm配合间隙)。
每两个交叉的举升臂连接处之间各焊接一个长160mm,宽70mm,厚18mm的加厚板。
在中间处均开有直径为30mm的孔,用于穿插销轴。
销轴的尺寸参照GB882-86初选d=30,长为100mm。
其中两个内侧的举升臂还需要有与液压缸配合的孔,孔径即需要穿插的液压缸支承轴轴径,初选D=40mm,材料为40Cr。
垫片及开口销采用国标值,销轴长度在后面小节计算。
(2)举升臂内侧稳定横梁焊接钢板长度等于两侧举升臂距离。
宽45mm,厚10mm。
材料为45钢。
焊接位置距离举升臂端部取110mm。
(3)两个液压缸的活塞杆据离内侧举升臂为120mm。
活塞杆顶部套管与横轴装配处有两个长85mm,内径40mm的套筒,和一个长265mm,内径40mm的中间套筒组成。
液压缸底部安装位置跟上部对应相同。
2.6.4校正仪上部平台结构尺寸及材料的确定
(1)举升平台是整个平台的基础,为了满足拉塔在360度内均可工作,需要设计一定的转角,如图2.8所示。
图2.8平台主要轮廓结构
①—内横梁②—槽型钢滑道③—内贴槽型钢
由技术参数可知平台长度2300mm,宽950mm,这里高度取90mm,厚度20mm,钢板材料使用Q235。
折角后尺寸如上图2.8所示。
平台钢板的内部焊接有热轧槽型钢,槽型钢的型号采用五号,其具体尺寸参照GB/T707-1988,其各段长度以完全焊接在钢板的内壁上为准,。
(2)举升平台内部横向需要稳定及安装绞支座和滑道,所以焊接两个长835mm的方管,由GB/T3094-2000选择高50mm,宽70mm型。
安装位置因上部槽型钢滑道的影响,两个横梁采用非对称安装方式(见图2.7)。
(3)内壁焊接滑道槽型钢由GB/T707-1988可选,高63mm,宽40mm。
因举升位置最低点高230mm,可以求得在最低点时举升臂与地面的夹角:
解得α=7°。
因举升最大高度时夹角为90°。
所以1420*cos7°-1420*cos45°=405.32mm,这里取525mm作为槽型钢滑道长度。
其安装位置由举升最大高度时上端绞支座的位置确定。
(4)在举升汽车时我们需要在平台上安装举升支撑臂来支撑起裙边,举升臂与平台的连接需要必须满足随汽车的不同的轴距而移动。
所以需要用卡钳及托盘连接来二者。
卡钳及卡盘卡在高90mm的平台钢板上安装,并且卡钳及托盘顶端恰好接触高50mm的槽型钢上,其二者材料均选45钢。
其具体结构尺寸如图2.9所示。
图2.9卡钳及卡盘主要结构及尺寸
卡钳宽度取与横梁方管的宽度相同,横梁方管参照标准规格表取厚度6mm,宽70mm,卡盘宽度130mm。
插销长100mm,材料为45钢。
卡盘立柱中心位置据卡钳表面25mm。
(5)举升臂的移动是通过焊接在一端侧面的短轴来插入滚针轴承内孔中来实现的,为了限定滚针轴承的轴向位置,采用阶梯轴,其在滑道方向的限制通过焊接一个铁块即可,其结构简单,尺寸没有严格规定,阶梯轴尺寸见图2.10中φ35和φ25,其一端与焊接在平台内壁的槽型钢有5mm间隙。
图2.10举升臂及轴的结构尺寸
通过上图尺寸L=60mm可以确定两侧举升臂的间距,因此底端支座间距,液压支撑轴尺寸也可确定。
取液压缸支承轴长度为L=635mm,垫片及销轴端面尺寸由φ40确定其标准值。
滚针轴承型号参照厂家实际可提供的型号为308-226C,内径25mm,外径45mm,厚30mm,优先选购耐磨的材料。
(6)上部横梁处支座尺寸:
高度75mm,宽45mm,厚15mm,材料为Q235钢。
安装位置以根据上平台举升臂安装尺寸确定。
两个支座距离与下部绞支座相同。
2.6.5定位夹具的尺寸及材料的确定
(1)定位夹具结构较为复杂,我们这里主要参照CAD二维草图来说明详细尺寸。
所有结构尺寸如图2.11所示。
图2.11夹具结构尺寸
由于夹具高度可调,这里说明最低时H=240mm。
定位夹具体的卡钳,圆柱螺栓,加强筋,坐板等均为45钢。
因其需要随不同车宽而移动,所以只需要满足对称装配即可。
其中控制卡钳移动的螺栓及垫片参照GB/T6712.1-2000采用公称直径M16,附加M16垫片,其长度L取105mm。
2.6.6拉塔组件的尺寸及材料的确定
(1)拉塔立柱选用的方管按GB/T3094-2000选择正方形截面方管,边长80mm,厚度8mm,整个长度取1200mm,材料45钢。
拉塔立柱上焊接的定位块由高30mm,宽30mm,长40mm的钢块组成,材料Q235钢。
支撑轴夹板厚20mm,材料Q235钢。
销轴按标准规格取φ30,长度145mm,材料为40Cr。
其结构尺寸如图2.12。
图2.12拉塔结构尺寸
(2)拉塔横梁采用正方形截面方管,边长70mm,厚8mm,长720mm,材料Q235钢。
连接处对称焊接的钢板厚度分为20mm,25mm两处,其中从焊接端到横梁一端厚度为25mm,材料Q235钢。
销轴与上节销轴尺寸相同,材料为40Cr。
具体结构尺寸如图2.13。
图2.13横梁处结构尺寸
(3)横梁处两个液压缸位置绞支座的厚均为15mm,底坐板宽均为80mm,绞支座边缘与底板边缘对齐焊接,材料均为Q235钢。
具体结构尺寸如图2.14。
图2.14拉塔横梁结构尺寸
(4)拉塔横梁与平台连接处各结构尺寸如图2.15。
图2.15连接处结构尺寸
①—主视图②—俯视图
材料除横梁采用45钢外其余均为Q235钢。
销轴直径均采用标准值φ20,垫片及开口销由直径参照手册确定。
(5)拉链的选择厂家提供的直径10mm,外长50mm,外宽34mm,长度2.5m左右