动力总成悬置系统布置设计研究.docx
《动力总成悬置系统布置设计研究.docx》由会员分享,可在线阅读,更多相关《动力总成悬置系统布置设计研究.docx(18页珍藏版)》请在冰点文库上搜索。
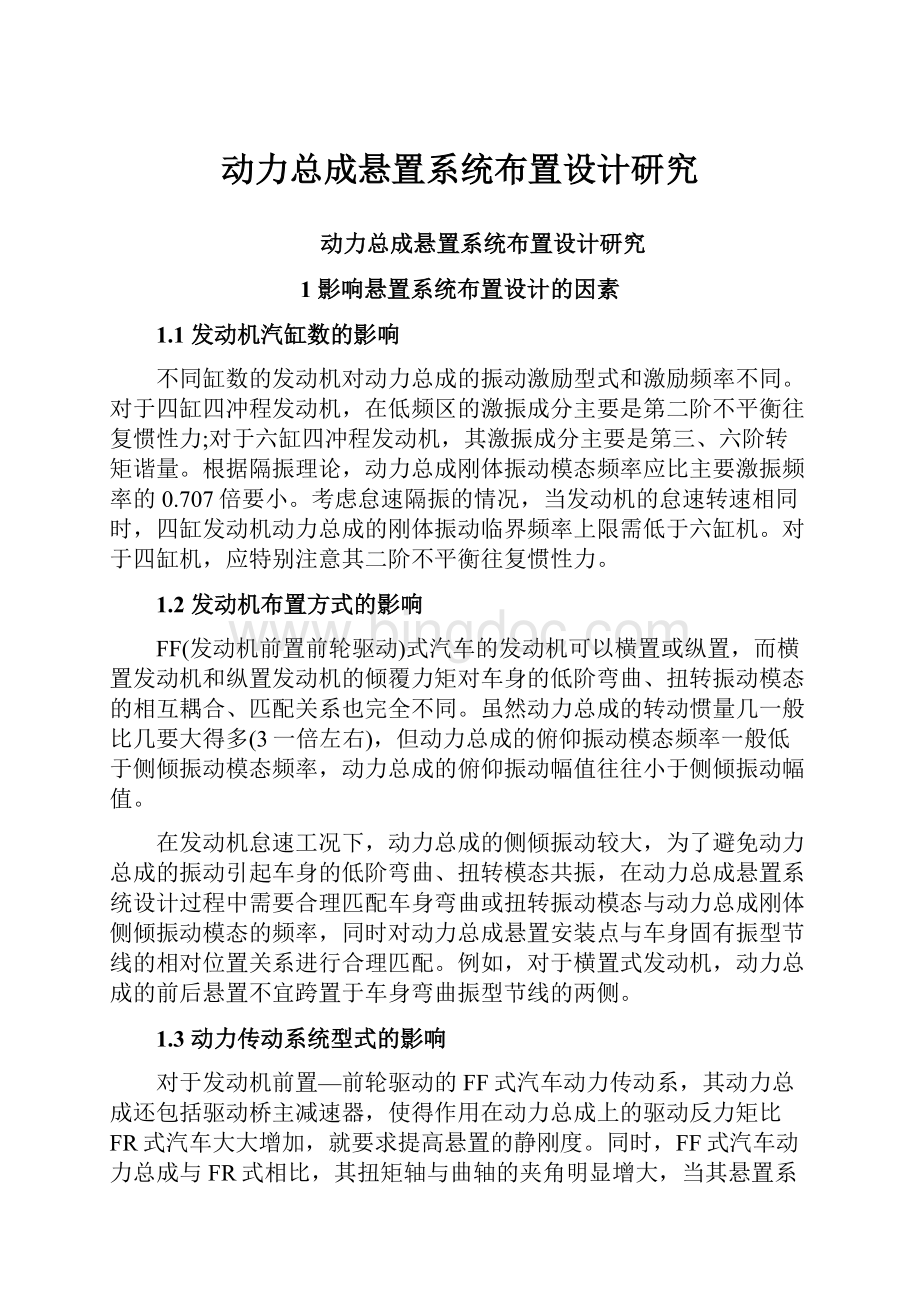
动力总成悬置系统布置设计研究
动力总成悬置系统布置设计研究
1影响悬置系统布置设计的因素
1.1发动机汽缸数的影响
不同缸数的发动机对动力总成的振动激励型式和激励频率不同。
对于四缸四冲程发动机,在低频区的激振成分主要是第二阶不平衡往复惯性力;对于六缸四冲程发动机,其激振成分主要是第三、六阶转矩谐量。
根据隔振理论,动力总成刚体振动模态频率应比主要激振频率的0.707倍要小。
考虑怠速隔振的情况,当发动机的怠速转速相同时,四缸发动机动力总成的刚体振动临界频率上限需低于六缸机。
对于四缸机,应特别注意其二阶不平衡往复惯性力。
1.2发动机布置方式的影响
FF(发动机前置前轮驱动)式汽车的发动机可以横置或纵置,而横置发动机和纵置发动机的倾覆力矩对车身的低阶弯曲、扭转振动模态的相互耦合、匹配关系也完全不同。
虽然动力总成的转动惯量几一般比几要大得多(3一倍左右),但动力总成的俯仰振动模态频率一般低于侧倾振动模态频率,动力总成的俯仰振动幅值往往小于侧倾振动幅值。
在发动机怠速工况下,动力总成的侧倾振动较大,为了避免动力总成的振动引起车身的低阶弯曲、扭转模态共振,在动力总成悬置系统设计过程中需要合理匹配车身弯曲或扭转振动模态与动力总成刚体侧倾振动模态的频率,同时对动力总成悬置安装点与车身固有振型节线的相对位置关系进行合理匹配。
例如,对于横置式发动机,动力总成的前后悬置不宜跨置于车身弯曲振型节线的两侧。
1.3动力传动系统型式的影响
对于发动机前置—前轮驱动的FF式汽车动力传动系,其动力总成还包括驱动桥主减速器,使得作用在动力总成上的驱动反力矩比FR式汽车大大增加,就要求提高悬置的静刚度。
同时,FF式汽车动力总成与FR式相比,其扭矩轴与曲轴的夹角明显增大,当其悬置系统采用V型布置方案时,往往由于布置空间和布置位置的限制,难以使得悬置组在布置达到使悬置组的弹性中心落在扭矩轴上的目标。
因此,有必要在整车总布置初期预留必要的空间。
1.4整车隔振性能要求对动力总成悬置系统设计的影响
为了抑制路面激起的整车振动,可适当配置动力总成悬置系统的垂向振动模态频率,使其起到控制整车振动的动力吸振器的作用,由动力总成吸收经过悬架传递上来的振动,从而减小车身的振动。
这往往要求动力总成悬置系统有较高的垂向刚度。
2不同动力总成型式下的悬置布置设计
2.1前置后驱式(FR式)汽车
前置后驱式(FR)汽车经常采用对称布置的三点或四点式悬置系统,二者隔振原理基本相同。
在FR式汽车动力总成悬置系统中,多在动力总成质心的左右各有一悬置,在变速器后部选用一点或两点悬置,组成三点或四点式悬置系统。
动力总成质心附近的悬置支承了动力总成质量的60%—80%,起主要隔振作用,被称作主悬置。
而变速器后部悬置的垂直方向刚度较低,主要起限制动力总成振幅的作用,防止其产生俯仰运动,被称作止动式悬置。
动力总成有六个刚体模态,在耦合振动系统中的某一模态受到激发的同时,其它模态振动也受到激发,不利于控制系统的振动。
理想的解耦式振动系统中,悬置系统的弹性中心与动力总成的质心重合,这样六个刚体模态完全解耦。
但由于动力总成在汽车上的安装空间受到限制,无法实现完全解耦。
AdamOpel汽车动力总成采用的三点式悬置系统中,在发动机前部的两侧各有一个与垂直方向倾斜一定角度的解耦式主悬置,在变速器后部有一止动式悬置,如图2-1所示。
考虑到动力总成中扭矩波动、往复惯性力引起的扭振和垂直振动对整车乘坐舒适性有重要影响,因此图3.2所示的悬置系统将扭转振动与垂直振动解除耦合,从而在一定程度上改善了悬置系统的隔振特性。
图2-1FR式汽车动力总成悬置系统
2.2前置前驱动(FF式)汽车
动力总成前置前驱动汽车(简称FF式汽车)结构紧凑,空间利用率高,高速行驶时具有良好的平顺性和安全性,在中、低档轿车中得到了广泛应用。
在FF式汽车中驱动反力矩直接作用在动力总成悬置上,故动力总成悬置除支承动力总成质量、扭矩波动、往复惯性力外,还应支承驱动反力矩作用(考虑到差速器变速比,驱动反力矩是动力总成输出力矩的3—4倍以上),因此,为限制动力总成的振幅,悬置应具有较高刚度,但这与采用低刚度悬置以隔离发动机中高速运转时的振动、噪声的要求相矛盾。
为克服这一矛盾,应在悬置系统中采取相应措施。
动力总成横置的FF式汽车驱动轴平行于发动机曲轴,动力总成输出扭矩和驱动反力矩都作用在动力总成前后悬置上,见图2-2a。
动力总成纵置的FF式汽车驱动轴垂直于发动机曲轴,扭矩激励作用在两前悬置上,驱动反力矩作用在变速箱悬置上,见图2-2b。
由图2-2可知,动力总成横置或纵置时,FF式汽车动力总成悬置系统受力状况有明显差别。
图2-2FF式汽车悬置系统所受力矩
2.2.1动力总成横置时FF式汽车悬置系统配置规律
动力总成横置的FF式汽车悬置系统与FR式汽车相比,尚未形成统一的配置方式。
其原因是:
不同生产厂家设计原则不同、发动机舱布置紧凑、对悬置的隔振水平要求高等。
动力总成横置的FF式汽车采用的三点式悬置系统突破了FR式汽车动力总成悬置系统的局限,有下面三种主要方式:
(1)在图2-3a所示三点式悬置系统中,在动力总成质心前有两悬置,分别布置在发动机、变速器与车架之间,质心后有一与汽车纵轴偏转一定角度的悬置通过横向支座连接变速器输出半轴和车厢前壁,可支承汽车的起步力矩。
(2)在图2-3b所示三点式悬置系统中,质心前部有一悬置通过横梁与纵梁相连,质心后有两悬置与转向轴相连。
(3)在图2-3c所示三点式悬置系统中,左右悬置与车架直接相连,其连线通过动力总成质心,动力总成质心下侧另有一悬置与车厢前部相连,起支承转矩作用。
(4)图2-4所示的四点式悬置系统在动力总成横置的FF式汽车上也得到了广泛应用。
悬置系统中前后悬置安装在T型副车架上,发动机顶部悬置和变速箱置固定在整体式车架上。
在悬置系统设计中,应严格控制弯曲模态振型节点在悬置系统中的位置。
由图2-5可知,当振型节点在前、后悬置之间时,座椅接地点垂直振动水平有所提高;当振型节点在后悬置之后时,座椅接地点垂直振动水平有所降低,这种现象被称作“相量消减”。
由图2-6可知,当激振频率趋于动力总成刚体共振频率时,节点位置向前移动。
这时,系统包括动力总成绕打击中心A作俯仰运动的刚体模态和一阶弯曲模态。
由于刚体共振频率前后的弯曲模态相位相反,因此弯曲振动节点在上述两个弹性模态作用下在刚体共振频率点附近产生移动。
为保证节点位于后悬置之后,应使怠速频率低于动力总成共振频率。
如果车体尺寸太大,无法将动力总成弯曲模态共振频率提高至怠速频率之上,那么应安装动力吸振器,如将散热器与动力总成弹性连接,以在汽车怠速时抑制动力总成的弯曲共振。
这样当汽车怠速时,动力总成悬置系统中只有刚体模态受到激发,振动节点减为一个,并移向打击中心。
将图2-5中前悬置后移,可减少悬置到动力总成扭转轴的距离,降低了悬置系统的扭转刚度,使汽车对动力总成的垂直振动不敏感。
同理,降低图中发动机顶部悬置,可减少动力总成沿纵向向汽车传递的力,使车体对动力总成纵向振动不敏感。
图2-7所示四点式悬置系统中,左、右悬置与车架直接相连,二者靠近动力总成惯性主轴,使动力总成垂直振动和扭转振动解除耦合;此外,在动力总成前后各有一悬置沿汽车纵向中心线布置,通过对纵向振动不敏感的支座,分别固定在汽车前横梁和车厢前壁上。
2.2.2动力总成纵置的FF式汽车悬置系统配置规律
动力总成纵置的FF式汽车有助于整车质量平衡,工作平稳,尤其有利于降低小型汽车的低速振动。
因为悬置在动力总成弯曲振动节点处不引起车架振动,所以适于安装低刚度的主悬置,由图2-8a可知,纵置直列五缸发动机FF式汽车在动力总成质心处振幅为零,适于安装五点式悬置系统。
因为动力总成前部、中间悬置处振幅约为变速器悬置处的l/3,所以主悬置应布置在前部、中间悬置位置。
此外,应在变速器尾部安装低刚度的止动式悬置。
在纵置直列四缸发动机FF式汽车的动力总成上,无任何一点振动幅值为零,不适于前述节点布置原则,其悬置系统原理与FR式汽车相同,但为支承驱动反力矩作用,应适当提高变速器悬置的刚度。
2.3全轮驱动式汽车动力总成悬置系统的配置方式
与传动系其他布置型式相比,全轮驱动式汽车对动力总成悬置系统提出了更高的要求:
(1)传动系是一个复杂的高刚度扭振系统;
(2)悬置应支承因前轮驱动引起的附加驱动反力矩;
(3)牵引力增加后,意味着悬置因负载变化支承的动载荷增加;
(4)全轮驱动式汽车动力总成尺寸增加,振动质量加大,动力总成的弯曲共振频率有所降低。
如前文所述,全轮驱动式汽车动力总成多布置在汽车前部。
由于动力总成质量增加,发动机侧悬置应布置在发动机附属设备的后部,而变速器悬置有两种方案可供选择:
其一,支承在变速器尾部,组成三点或四点式悬置系统用“长基”表示;
其二,通过副车架与车架相连,组成五点式悬置系统,用“短基”表示,如图2-9所示。
在“长基”悬置系统中,由于动力总成俯仰振动和垂直振动耦合,俯仰振动吸收了大量的振动能量,降低了动力总成的振动强度,从而改善了乘坐舒适性。
此外,“长基”悬置系统还具有悬置数量少,副车架强度要求低的优点。
在“短基”悬置系统中,扭转刚度是常量,且作用距离短,有利于优化动力总成振型,降低噪声水平,并可省略变速器悬置,减少了振动力的传递。
3悬置的布置设计要点
发动机动力总成是通过橡胶悬置支承在副车架上的,而橡胶悬置块是粘弹性元件,二者构成了振动系统,对于这个复杂的振动系统,悬置点的数量和悬置的布置形式直接影响着整个振动系统的固有特性以及振动的解耦情况。
一般轿车动力总成悬置系统通常包括3一4个悬置元件,其中的1一2个为液阻悬置,悬置系统隔振性能的好坏不仅与每个悬置的性能有关,而且与这几个悬置组合后的特性相关。
悬置系统的隔振设计包括:
确定每个悬置元件的静动态特性、安装位置和安装方位。
3.1悬置支承点的数目
悬置点的数目可以有3、4、5及6点等四种类型。
悬置点的数目一般根据发动机变速箱总成的尺寸(特别是长度尺寸)、重量、用途和安装方式等决定的。
3点及4点悬置在汽车上的应用最为普遍,悬置点的数目增多将难以保证各点的受力均衡,当车架变形时发动机和车架失去顺从性,使个别支点因发生错位而受力过大,反而影响可靠性。
3点式悬置与车架的顺从性最好,因三点决定一个平面,不受车架变形的影响。
而且自振频率低,抗扭转振动的效果好。
值得推荐的是前悬置采用两点左右斜置,后端一点紧靠惯性主轴的布置方案。
这种布置具有较好的隔振功能,在4缸机上得到广泛的应用。
而前一点后两点的三点式多用于6缸机。
4点式悬置的稳定性好,能克服较大的转矩、反作用力,但扭转刚度较大,不利于隔离低频振动,必须经过合理设计才可满足4缸机的要求。
4点式悬置在6缸机上的使用最为普遍。
5点式悬置一般仅用于重型汽车上,因为其发动机变速箱总成的重量和长度太大,为了避免发动机缸体后端面与飞轮壳结合面上产生过大的弯矩,不得不在变速箱上增加一个辅助支点,从而形成5点式悬置。
但必须经过负荷计算确定辅助支点的刚度,辅助支点的刚度不能太大必须有足够的柔性,以避免因车架变形而损坏变速箱。
本文研究的动力总成使用的是三点式悬置,这种方式在日系小排量发动机FF横置的轿车应用十分广泛。
3.1.1三点支撑
三点支承的发动机悬置,在我国大客车行业是一种较为常见的形式。
上柴D6114系列发动机和康明斯B系列、C系列及M系列发动机均可采用这种结构形式。
三点支承具有结构简单、占用空间少、容易设计和不易产生定位干涉等优点;其缺点是稳定性较差,特别是对冷却系统由皮带驱动和装非独立式空调的大客车,发动机的定位不可靠,悬置系统容易损坏。
3.1.2四点支承
四点支承是大客车最为普遍的发动机悬置结构[28]。
绝大多数发动机,如斯太尔WD615系列、WD612系列和WD618系列,日野J08C,杭发X6130等均为四点支承;上柴D6114系列发动机和康明斯B系列、C系列发动机也可采用四点支承。
四点支承具有发动机定位可靠、稳定性好的优点;其缺点是容易产生定位干涉,对有关零件设计和加工的尺寸精度要求较高,前悬置支架容易和水箱支架发生干涉。
本文研究的发动机动力总成悬置系统就是采用的四点悬置。
3.1.3五点支承
所谓五点支承,是指在典型的四点支承的基础上,在变速器上加辅助支承。
重汽公司在早期开发的斯太尔6091H26型中档旅游大客车底盘,即采用了这种五点支承形式。
大量实践证明:
对于城市和旅游大客车,如果没有装配液力或电涡流缓速器,一般没有必要采用五点支承的悬置形式。
3.2悬置支承点的位置
悬置点有前悬置和后悬置之分。
3点式悬置系统有前2后1和前1后2两种布置方案。
悬置点的位置应视具体结构空间和隔振要求而定。
本文508动力总成采取前2后1布置方案。
实际上一般在发动机或变速箱上均己提供了预留的螺孔或凸台,以供安装悬置支架。
甚至有多组螺孔或凸台以便选用。
这些螺孔中前悬置用的大多数分布在缸体前端面下部或缸体前中部的左右侧面上,后悬置用的分布在飞轮壳两端变速箱底部或两侧。
在确定悬置点的位置时,必须进行悬置点的载荷计算,然后校核各支点位置是否满足发动机制造厂对支点位置的要求及对关键部位的载荷的要求。
再根据撞击中心理论调整前后悬置的相对位置,并适当调整悬置点的横向位置及高度方向位置。
悬置的最佳安放位置是悬置通过动力装置的自由扭矩转动轴,此时,悬置只承受发动机的力和力矩。
除此之外,还需考虑,下面几个因素:
1.悬置的位置应尽可能的安放在发动机振动较小的地方,即节点。
这样传递到悬置的振动也很小,安放点一定要远离动力装置反节点。
2.悬置应安放在车架或车身振动传递率最小的位置,即节点。
这个位置对振动的传递最不灵敏,车体上的响应可以达到最小。
3.悬置的放置要尽可能使动力装置的六个模态解耦,解耦后,动力装置就相当于六个独立系统,对一个模态进行控制时,其余模态不受影响。
4.对于车身——悬架系统来说,隔振系统必须有良好的动力吸振效果,一般来说,悬架系统承受垂向作用力的地方是安装悬置的好位置,因为这里一般刚度较高,质量集中,通常也是车身第一弯曲模态节点。
要同时满足上面这些要求是不现实的。
对同一结构来说,某一个振动模态节点位置对于另一个模态可能是反节点。
对一个悬置来说,要求一端与动力装置模态节点相连,另一端与车体模态节点相连,也很难实现。
另外,布置还受安装空间的限制,所以上述原则只是给出一个参考。
动力总成悬置系统的布置设计与发动机缸数、发动机布置方式、汽车动力传动系的型式及整车隔振性能要求等诸多因素有关。
汽车动力总成传动系统形式的多样性对动力总成隔振悬置系统提出了不同的设计要求,导致了动力总成悬置系统的布置方式的多样性。
3.3悬置布置形式
悬置是具有三向刚度的弹性元件,按照这三个刚度轴线和参考坐标轴线间的相对位置关系,悬置系统弹性支承的布置方式可以分为以下三种。
3.3.1平置式
这是一种传统的布置型式,它布局简单、安装容易,易于控制。
在这种布置方式中,每个悬置的三个互相垂直的刚度轴αβγ分别和悬置系统的坐标系ox、oy、oz平行,如图3-1所示。
由于通过发动机重心的各坐标轴方向平行于悬置的各弹簧作用线,故沿着某一轴方向的线位移在其余两弹簧中不产生恢复力;同样,绕某一轴回转的角位移在平行于此轴的弹簧中不产生恢复力。
图3-1平置式图3-2斜置式
3.3.2斜置式
这是一种目前汽车发动机中用得最多的布置方式。
在这种布置方式中,弹性支承的三个刚度轴相对于参考坐标轴存在一定的角度关系,一般斜置式的弹性支承都是成对地对称布置于垂向纵剖面的两侧,但每对之间的夹角可以不同,坐标位置也可任意,如图3-2所示。
这种布置方式的最大优点是:
它既有较强的横向刚度,又有足够的横摇柔度,因此特别适用于像汽车发动机这样既要求有较大的横向稳定性,又要求有较低的横摇固有频率以隔振由不均匀扭矩引起的横摇振动。
此外,它可以通过斜置角度,布置位置以及悬置两个方向上的刚度比等适当配合来达到——横摇解耦的目的,这是平置式较难做到的。
斜置式悬置布置还有一个特点:
系统六个自由度的刚度都和悬置的倾斜角θ有关,因此只要合理选择倾斜角,就能使系统的六个固有频率落在所期望的范围内。
在实际工作中选择倾斜角要比消除耦合振动容易实施,并且能够取得良好的隔振效果。
3.3.3会聚式
这种布置方式的特点就是所有悬置的主要刚度轴会聚相交于同一点,如图2-7所示。
除了有良好的稳定性外,会聚式的最大优点就是可以通过调节悬置倾斜角和安装位置,来获得六个完全独立的悬置系统的振动模态,而无需将各悬置布置在包含发动机重心的平面内,因此具有一定的价值。
但是这种布置型式实施起来并不容易,而且一般汽车发动机并没有纵向激励,斜置式完全能够满足隔振要求,因此会聚式悬置布置方式应用并不广泛。
图3-3会聚式
3.4动力总成安装角
发动机支承的基本形式如图3-4所示,θ为发动机的安装角,φ为发动机主惯性轴与曲轴中心线的夹角,一般为12°~15°。
主惯性轴位置可由试验测得。
发动机本体相对其主惯性轴振动,因此,主惯性轴的位置是发动机支承设计的基点,支承点的布置与发动机主惯性轴密切相关。
理想的支承系统是各支承点位于通过主惯性轴的平面上,且关于主惯性轴对称分布。
但是由于发动机机舱空间及发动机曲轴的安装要求,不可能把悬置支承点安装在过主惯性轴的平面内,所以发动机总成安装时一般都有一个倾角θ,使悬置支承点靠近过主惯性轴的平面。
图3-4发动机安装角及主惯性轴
3.5左右悬置点纵向距离的选择和优化
能利用缸体和飞轮壳上预留螺孔的前提下,悬置点的纵向位置应尽可能满足下列条件:
3.5.1撞击中心理论
对于研究的508动力总成悬置系统来说,将因路面冲击引起的右悬置处的剧烈扰动和由传动轴引起的左悬置处的扰动在另一端悬置处产生的响应最小化,是撞击中心理论的出发点。
对于外激频率较低的发动机来说,可采用撞击中心理论确定前后悬置点的纵向位置。
即如图3-5所示,使前后悬置点在互为撞击中心的位置O1O2上
图3-5撞击中心理论示意图
这样当一个支点受一个垂向力作用时,另一个支点上的响应力为零。
换言之,如果一个元件上遇到一个很大的垂向冲击力,由于另一个元件处于其撞击中心,故在这个元件上不会引起反应,反之亦然。
这样前后悬置上的垂向冲击力不会相互影响,从而可取得良好的隔振效果。
按照撞击中心理论应满足:
3.5.2将悬置点布置在机体一弯模态的节点上
对于较大型的高速发动机而言,悬置点应布置在机体弯曲振动的节点上。
因为机体实际上不是绝对刚体,在高频力作用下它将出现类似直梁的弯曲振动。
如果将悬置点布置在机体弯曲振动的节点上,既可避免机体的弯曲振动力传给车架,也可防止道路不平引起的振动。
通过车架而激起机体的弯曲振动。
因为在节点上不可能激起梁的振动。
通常只需考虑机体的一阶弯曲模态,自振频率大约在80Hz左右。
对于经常行驶在条件较差的道路上的车辆来说,这种结构布置更具有实用意义。
当然这种布置还取决于整车布置的空间条件,有可能难以实现。
这种布置方式如图3-6所示。
图3-5发动机弯曲振动的节点示意图
这种理论适用于曲轴方向尺寸较大的动力总成。
3.5.3单轴平动及转动振动解耦
以Z向移动和
向转动解耦为例,说明单轴平动及转动振动解耦方法。
图3-6Z向和
向振动解耦
3.6悬置点的横向距离
一般情况下,悬置点的横向距离由缸体或飞轮壳的宽度及悬置支架的悬臂尺寸决定,变化的余地不大。
一般来说悬置点的Y向距离越大则稳定性越好,但使悬置系统扭转刚度增大,对隔离扭转振动不利。
研究的动力总成悬置系统现有设计中后悬起防扭拉杆的作用,后悬的布置就应充分考虑这个因素。
3.7左悬、右悬及后悬置的功能对比
左悬、右悬及后悬置共同承担着整个悬置系统的全部功能,但由于所处的位置不同,对它们的要求各有特点:
(l)左右悬置布置在扭矩轴附近,承受绝大部垂向载荷。
因为左悬置元件到发动机变速箱总成重心的距离比右悬置要远。
右悬置元件的压缩刚度必然比左悬置的要小。
(2)后悬置距扭矩轴较远,主要承受扭转载荷。
为了保持一定的扭转自振频率扭转刚度,后悬置离开惯性主轴越远其刚度应越小。
这一点可从悬置系统的扭转刚度公式中可以看出,刚度小意味着振动时变形大、吸振能力强。
可见后悬置承担着大分扭转隔振和吸振功能,而左右悬置则占次要地位。
(3)对右悬置来说,它离动力总成重心较近,支撑着动力总成的大部分重量。
所以垂向刚度较大。
它离扭矩轴较近处于扭转激振较小的部位,不承受大的扭转振动幅,因此主要倾向于隔离垂向振动。
(4)左悬处在发动机动力输出端,受传动系统不平衡力的严重干扰和外部轴向推力的冲击,因此左悬置必须具有显著的吸振功能。
总之,四缸机和六缸机、柴油机和汽油机、轿车和载重车、轻型车和重型车等等对悬置系统都有不同的要求。
作为设计者应结合使用特点,注意观察和广泛收集现有各种悬置的结构方案,吸取成功和成熟的经验,应善于分析对比和借鉴。
这是工作不可缺少的重要环节。