生产加工工艺流程及加工工艺要求.docx
《生产加工工艺流程及加工工艺要求.docx》由会员分享,可在线阅读,更多相关《生产加工工艺流程及加工工艺要求.docx(12页珍藏版)》请在冰点文库上搜索。
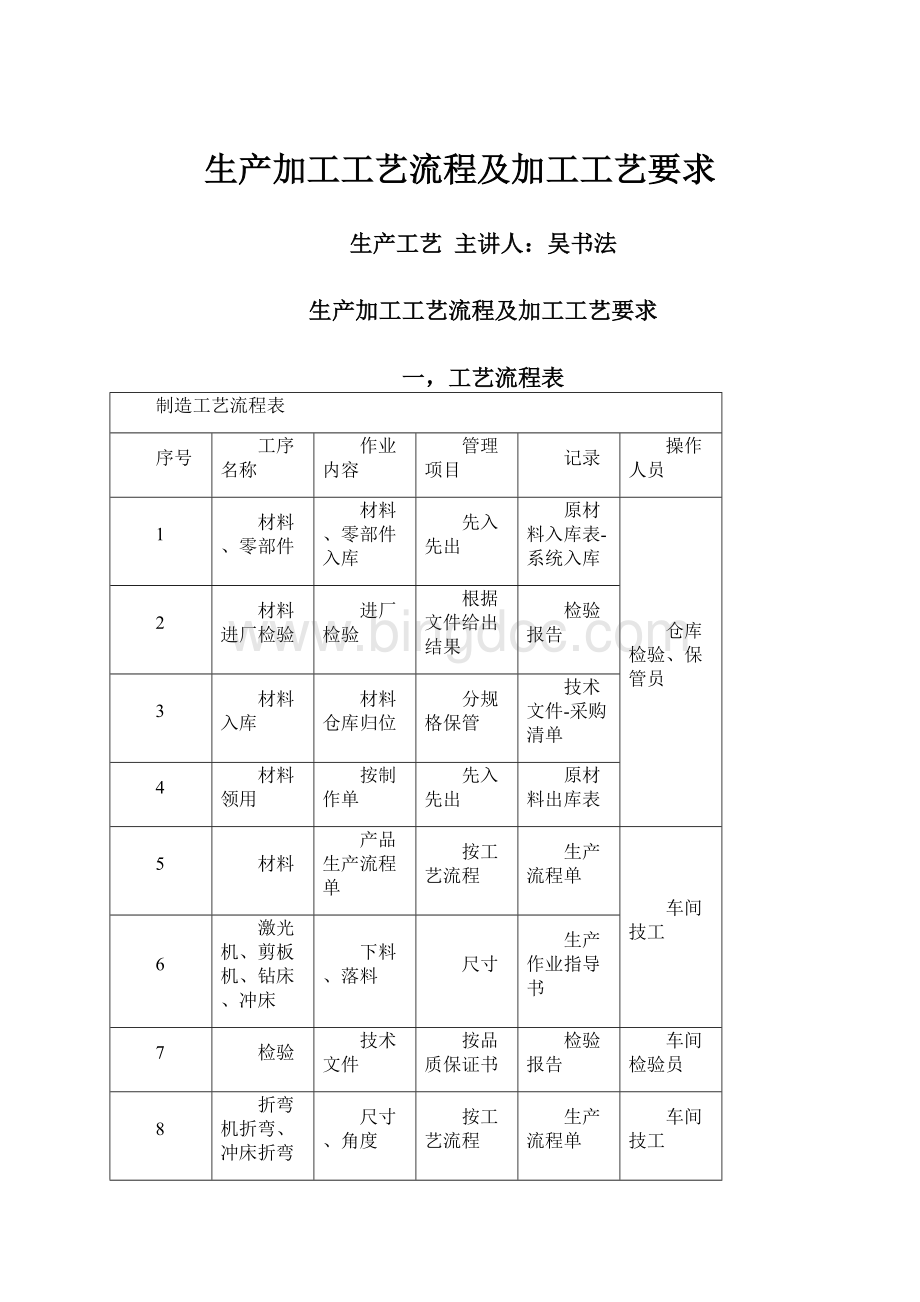
生产加工工艺流程及加工工艺要求
生产工艺主讲人:
吴书法
生产加工工艺流程及加工工艺要求
一,工艺流程表
制造工艺流程表
序号
工序名称
作业内容
管理项目
记录
操作人员
1
材料、零部件
材料、零部件入库
先入先出
原材料入库表-系统入库
仓库检验、保管员
2
材料进厂检验
进厂检验
根据文件给出结果
检验报告
3
材料入库
材料仓库归位
分规格保管
技术文件-采购清单
4
材料领用
按制作单
先入先出
原材料出库表
5
材料
产品生产流程单
按工艺流程
生产流程单
车间技工
6
激光机、剪板机、钻床、冲床
下料、落料
尺寸
生产作业指导书
7
检验
技术文件
按品质保证书
检验报告
车间检验员
8
折弯机折弯、冲床折弯
尺寸、角度
按工艺流程
生产流程单
车间技工
9
检验
尺寸、角度
按品质保证书
检验报告
车间检验员
10
焊接
按图加工
尺寸
生产作业指导书
车间技工
11
整形
校正
尺寸
生产作业指导书
车间技工
12
清洁处理
除焊渣、毛刺处理
清洁处理
生产作业指导书
车间技工
13
检验
表面清洁度
按品质保证书
检验报告
车间检验员
14
外协喷漆
表面着色
应无色差
生产作业指导书
外协管理员
15
检验
表面着色
应无色差
检验报告
检验员
16
装配
产品装配
产品的结合性
生产流程单
车间技工
17
产品调试
产品检验
产品性能
生产流程单
车间技工
18
成品、专用件检验
最终检验
按品质保证书
检验报告
检验员
19
铭牌、标签
打制铭牌、贴标签
品质保证书
生产流程单
检验员
20
包装作业
包装作业
包装状态
生产流程单
包装操作工
21
入库
入库包装
成品入箱
成品入库表-系统入库表
仓库检验、保管员
22
拍照上传
按产品发货单
品质保证书
生产作业指导书
装箱班
注:
从原材料入库到成品入库,根据产品标准书的标准要求规定,全程记录及管理。
二,下料工艺
我们公司下料分别使用:
①数控激光机下料②剪板机下料③数控转塔冲下料④普通冲床下料⑤芬宝生产线下料⑥火焰切割机下料⑦联合冲剪机下料
今天重点的讲一下:
①②
1两台激光下料机。
型号分别为:
HLF-1530-SM、HLF-2040-SM
2操作步骤
2.1开机2.1.1打开总电源开关2.1.2打开空气压缩机气源阀门,开始供气2.1.3打开稳压电源2.1.4打开机床电源2.1.5打开冷干机电源,待指针指在绿色区间内,再打开冷干机气阀2.1.6打开切割辅助气体(气体压力参照氧气、氮气的消耗附图)2.1.7待数控系统开机完成,松开机床操作面板上的急停按钮,执行机床回零操作2.1.8打开激光器电源开关,(夏天等待30分钟)打开水冷机,待水温在“低温21℃,高温31℃”,再打开机床操作面板上的“激光开关”按钮,等待按钮上方LED灯由闪烁变为常亮。
开机完成。
2.2常规操作步骤2.2.1在【JOG】状态下,按下【REF.POINT】,再按回零键,执行回零操作2.2.2在2.1生效的情况下,按下“标定”键,执行割嘴清洁和标定程序。
2.2.3根据相应的板材,调节焦距位置、选择合适大小的割嘴,然后调整割嘴中心。
2.2.4打开导向红光,用手轮或控制面板,将切割头移动到板材上方起点位置,关闭导向红光,关闭防护门。
2.2.5打开所用切割程序,确定无误后一次点击“AUTO”,“RESET”,“CYCLESTART"。
2.2.6切割结束将Z轴抬高再交换工作台,取出工件摆放整齐,做好标识。
注意:
标定时将进给倍率旋转到100﹪,标定过程中“标定”键上方LED灯保持闪烁,直至其常亮。
如果失败重新标定。
注意:
切割时将手放在“CYCLESTOP"键上方,以防意外可随时按下切割停止键。
2.3关机2.3.1关闭激光器2.3.2按下操作面板上的急停按钮2.3.3切断辅助气体、关掉冷干机气阀2.3.4关闭激光器电源开关、冷干机电源、稳压电源2.3.5关闭总电源
3编程3.1绘制零件图及生成程序3.1.1采用机带软件“CNCKAD"来新建一个零件,和CAD制图新建相同(省落)。
在弹出对话框中设置零件的尺寸、材质、厚度、气体等参数,点击确定3.1.2绘制零件图:
同CAD绘图。
3.1.3删除所用的辅助线,只保留图形线并设置为白色3.1.4保存为“DFT”格式。
3.2图形检查,确保零件图无误。
3.3自动切割;以自动设置切割路径,删除旧路径,重新生成新的切割路径,勾选“删除已添加的冲压”
3.4生成机器程序,点【NC】之后,不断的按下一步,最后按确定便可。
3.6.2文件共享;A:
将零件程序放入电脑中的共享文件夹“YAWEI”中。
B:
在机床操作界面中,选择“YAWEI”,进入后选择并复制所要导入的程序。
C:
将所要导入的文件,复制到机床“零件程序”文件夹下。
3.7程序的选择与执行;关闭防护门,选中程序,点击执行,在“AUTO”状态下,按一下“RESET”,再按“CYCLESTART”,程序执行。
3.8程序修改;需要修改程序,点击“程序修改”,进入修改画面,便可以修改程序。
4工艺过程4.1数控编程切割工艺4.1.1绘图及图形类型的转换(要求零件外轮廓闭合)。
4.1.2确定材料、尺寸和零件排样。
4.1.3使用激光切割:
圆角工艺(获得锐角倒钝)或回路工艺(获得锐角);自动载入气体类型、切割速度,并设置退料
4.1.4加工顺序优化,生成数控加工程序,传输程序。
4.2切割穿孔技术先用冲孔功能冲出一小孔然后再用激光从小孔处开始切割。
4.3切割气体和气体压力的选用和设定(参照氧气、氮气的消耗附图)4.3.1碳钢:
切割碳钢使用纯氧气作为辅助气体,根据板材的厚度选择适用的割嘴。
2mm以下板材;压力<2bar、2~5mm板材,压力为1.5bar、6~12mm板材,压力为1.3bar。
4.3.2不锈钢:
切割不锈钢使用高压氮气(N2)作为辅助气体。
压力为10bar。
注意:
A;当转换气体时,应排除气袋内不同的气体。
B;切割过程中,如果出现飞溅应停止切割。
或出现程序丢失也应该停止切割,有酒精清洗镜片,用擦镜纸清洁镜片,并执行“标定”程序清洗割嘴。
板材厚度
焦距【"】
焦点位置
切割功率[w]
切割速度m/min
O2压力[bar]
喷嘴直径(复合)
喷嘴高度mm
1
5
0
800
6000
2
1.2
1.0
2
5
+0.5
1000
4000
2
1.2
1.0
3
5
+1
1200
3000
1.5
1.5
1.3
4
7.5
+1
1500
2000
1.5
1.5
1.3
5
7.5
+1
1600
1800
1.5
1.5
1.3
6
7.5
+1
1800
1500
1.3
1.5
1.3
8
7.5
+1.5
1800
1200
1.3
1.5
1
剪板机工艺
1,按工艺卡片的规定,用钢板尺量出刀口与挡料板两端的距离,反复测量数次,然后试剪一小块料核对尺寸正确与否,如尺寸公差在规定的范围内,即可进行入料剪切,如公差不符合要求,应重新调整定位距离,直到符合规定要求为止。
然后进行纵挡料板调整,使纵与横板刀口成90︒,并紧牢固。
2,开车试剪进料时应注意板料各边相互垂直,首件检查符合工艺卡片的规定后,方可进行生产,否则应重新调整纵横挡料板。
3,辅助人员应该配合好,在加工过程中要随时检查尺寸、毛刺、角度,并及时与操作人员联系。
4,剪裁好的半成品或成品按不同规格整齐堆放,不可随意乱放,以防止规格混料及受压变形。
5,为减少刀片磨损,钢板板面及工作台台面要保持清洁,剪板机床面上禁止放置工具及其他材料。
6,剪切板材的宽度不得小于20mm。
7,根据生产量采用合理的裁剪方法,先下大料,后下小料,尽量提高材料的利用率。
8,零件弯曲、有条纹要求的,应按其料纹、弯曲方向进行裁剪。
钢板剪切截断面的毛刺应符合表一的规定;
表一单位毫米
料厚
毛刺高
料厚
毛刺高
0.1~0.7
≤0.05
1.9~2.5
≤0.18
0.8~1.2
≤0.08
3~4
≤0.25
1.3~1.8
≤0.12
5
≤0.3
表二单位毫米
材料厚度(t)
单面间隙(z)
0.25
0.05
0.40
0.07
0.50
0.07
1.0
0.07
1.5
0.12
2.5
0.15
3.0
0.20
4.0
0.35
6.5
0.42
Z=6~7﹪*t式中;z-间隙t-材料厚度
9,每次剪板时系统根据输入的不同材料、板厚自动计算出相应的刀口间隙及剪切角,同时你可以按照图纸要求和需要作适当的修改。
折弯机工艺
材料厚度与弯边圆角半径和模具的配合关系见表1。
表1板料厚度与弯边圆角和模具的配合
模具
材料厚度t,mm
<1
>1~2
>2~3
>3~4
>4~5
>5~6
>6~7
>7~8
>8-9
最大折弯圆角R,㎜
2~3
3.5~4
4~5
4.5~5
9~5
11~7
11~7
12~8
13~5
凹模深度h,㎜
6
8
12
15
18
22
25
28
32~36
凹模宽度b,㎜
≮8
≮16
≮24
≮32
≮40
≮48
≮56
≮64
≮72
不同的材料厚度,其最大允许折弯长度见表2。
表2最大允许折弯长度
板料厚度,㎜
1-2
2.5
3
4
5
6
8
最大允许折弯长度,㎜
3150
2800
2500
1800
1100
600
200
注:
屈服强度不超过26Kg/mm2的金属材料。
板料折弯的最小搁置尺寸c与板料的厚度有关(见图1)。
板料厚度1mm~3mm的搁置尺寸c为3mm;板料厚度大于3mm的搁置尺寸c等于板料厚度
角尺边折弯最小极限尺寸amin(见图2)与板料厚度、折弯圆角半径和搁置尺寸的关系见图;
几种典型折弯形式的弯边次序一般是先外后内,可参见图6所示。
“双折边”应先折成锐角后压边。
模具的选择
行程(mm)=开口高度—中间板高度—上模高度—下模座高度—(下模高度—0.5V+t)t为板料厚度(mm)
使用不同的模具组合可以获得不同的模具组合高度,用来加工不同的零件。
板料在弯曲过程中外层受到拉应力,内层受到压应力,从拉到压之间有一层既不受拉力又不受压力的过渡层成为中性层,中性层在弯曲前后长度保持不变,所以中性层是计算弯曲件展开长度的基准。
常见的影响折弯系数的因素:
板厚、材质、下模宽度、下模肩宽R、上模尖端R、材料轧制方面、其他……
由于时间的关系,今天我们就学习到这里,如有特殊操作,在联系我。
谢谢大家!