总装工艺设计说明书.docx
《总装工艺设计说明书.docx》由会员分享,可在线阅读,更多相关《总装工艺设计说明书.docx(19页珍藏版)》请在冰点文库上搜索。
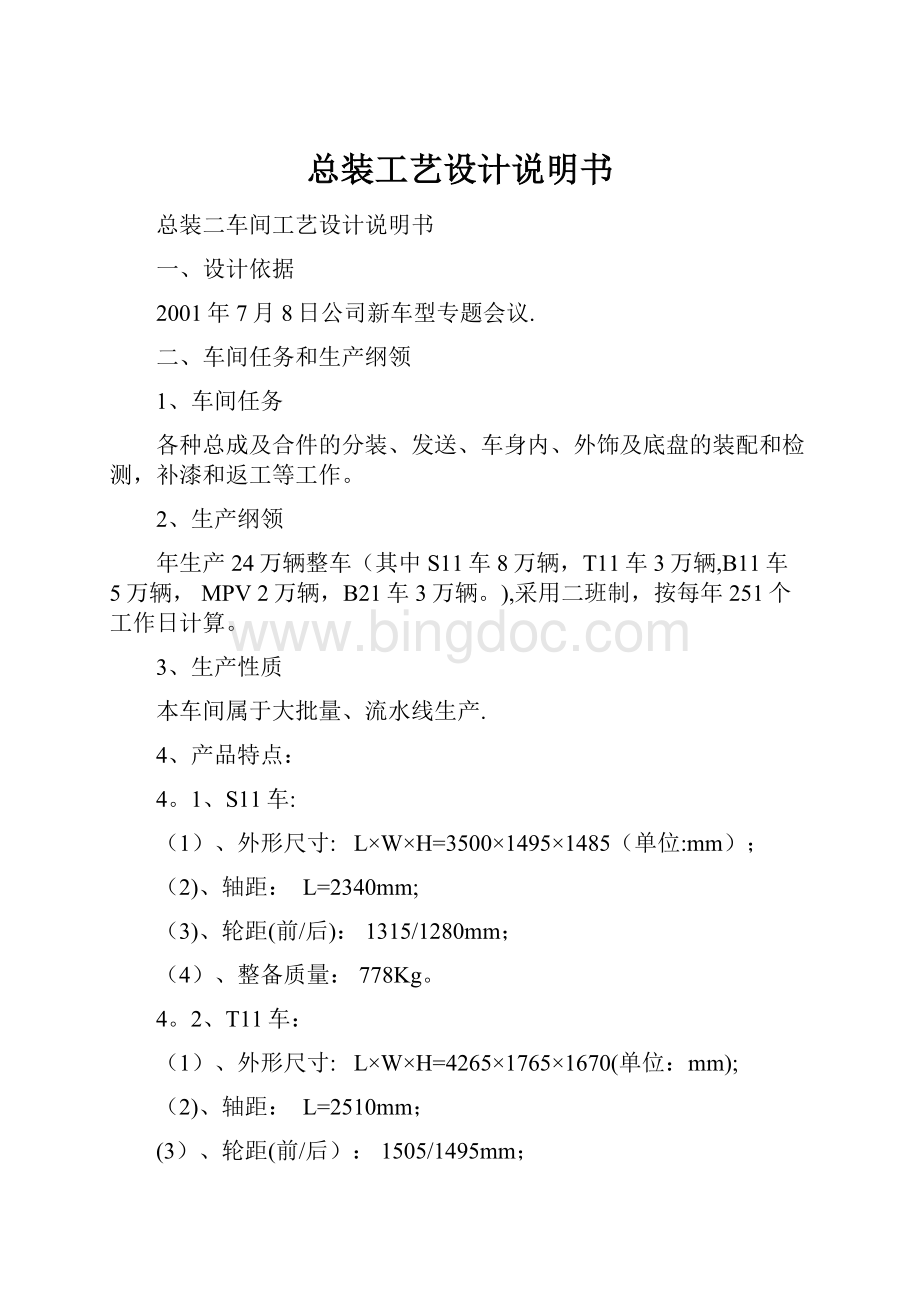
总装工艺设计说明书
总装二车间工艺设计说明书
一、设计依据
2001年7月8日公司新车型专题会议.
二、车间任务和生产纲领
1、车间任务
各种总成及合件的分装、发送、车身内、外饰及底盘的装配和检测,补漆和返工等工作。
2、生产纲领
年生产24万辆整车(其中S11车8万辆,T11车3万辆,B11车5万辆,MPV2万辆,B21车3万辆。
),采用二班制,按每年251个工作日计算。
3、生产性质
本车间属于大批量、流水线生产.
4、产品特点:
4。
1、S11车:
(1)、外形尺寸:
L×W×H=3500×1495×1485(单位:
mm);
(2)、轴距:
L=2340mm;
(3)、轮距(前/后):
1315/1280mm;
(4)、整备质量:
778Kg。
4。
2、T11车:
(1)、外形尺寸:
L×W×H=4265×1765×1670(单位:
mm);
(2)、轴距:
L=2510mm;
(3)、轮距(前/后):
1505/1495mm;
(4)、整备质量:
1425Kg。
4。
3、B11车:
(1)、外形尺寸:
L×W×H=4770×1815×1440(单位:
mm);
(2)、轴距:
L=2700mm;
(3)、轮距(前/后):
1550/1535mm;
(4)、整备质量:
1450Kg。
4。
4、MPV:
各参数暂未定.
4.5、B21车:
(1)、外形尺寸:
L×W×H=4670×1780×1435(单位:
mm);
(2)、轴距:
L=2670mm;
(3)、轮距(前/后):
1515/1500mm;
(4)、整备质量:
1350Kg。
5、生产协作
本车间装配用油漆车身通过悬挂式输送机从涂装二车间及涂装三车间输送过来,发动机由发动机厂用叉车运输过来,其他外协作件均由外协厂家提供.
三、工作制度和年时基数
1、采用二班制,每班工作8小时,全年按251个工作日计算,工作负荷率为85%考虑.
2、年时基数计算如下表:
工作制度
单位
工人
设备
工作地
二班制
小时
1706。
8
3413.6
4016
四、设计原则和主要工艺说明
1、设计原则
(1)、本车间主要任务是S11、T11、B11、MPV及B21五种整车的装配、检测及调整.每种车型在生产线上初步分为一次内饰、底盘装配、二次内饰、检测等工段。
(2)、整车的装配以人工装配为主,辅以关键的夹、辅具,紧固的拧紧主要通过气动工具及电动工具来实现;以客户的订单作为组织生产的指导原则.
(3)、工艺水平应能满足产品精度要求,并与相应的生产纲领相适应。
充分利用国产设备,关键设备(主要指检测线设备和生产线的加液设备)采用进口设备,确保产品的质量。
(4)、尽量考虑多品种系列化生产需要,组织必要的柔性生产线生产。
(5)、坚持“少投入,多产出”的原则,缩小投资规模,尽量选用精度、效率均能满足要求的国产设备.
(6)、土建要符合国情,在可能的条件下,适当提高密封、防尘等。
(7)、此次设计将S11与T11混线,B11、MPV及B21车混线,其中S11与T11线的生产节拍为2×8×251×60×0。
85/140000=1。
46≈1。
5(min),考虑到实际生产是个爬坡过程,设计节拍在1。
3-4.0min范围内可调;B11与MPV线的生产节拍为:
2×8×251×60×0。
85/100000=2。
05≈2(min),设计节拍为1.2-3。
6min范围内可调。
其中0。
85为设备的负荷率,251为年工作日。
2、主要工艺设计说明
(1)、油漆好的车身由积放式悬挂输送机由涂装二车间及涂装三车间送到总装车间的储存线上,涂装二车间输送过来的油漆车身储存线共9条,其中1条为直通道,另8条为五种车型的储存通道,总储存量约300台.涂装三车间输送过来的油漆车身储存线共6条,其中1条为直通道,另5条为五种车型的储存通道,总储存量约140台.加上涂装二车间及涂装三车间到总装二车间通廊的储存量,总储存量约为500台,约为总装二车间达到设计产量时的半个班次产量。
(2)、由储存链上放下的车进入工艺段进行装配。
包括:
A、一次内饰:
二条线的一次内饰装配均在推板滑撬上进行。
主要包括:
车门上附件(仅指S11及T11线),空调蒸发器,仪表板,前围隔热垫,地毯,顶棚,A、B柱护板,整车车身线束,前、后风挡玻璃,雨刮器等件的装配。
B、底盘装配:
二条线的底盘装配均在推杆链上进行。
主要包括:
动力总成,后轴总成,排气管,制动油管,油箱及油管等装配。
C、二次内饰和整车调整:
二条线的二次内饰及整车调整均分别在推杆链和双边板式输送机上进行。
主要包括:
前、后保险杠,前大灯,四门护板,外后视镜,车轮,制动液、空调液、动力转向液、防冻液、清洗液的加注,四门二盖的调整,发动机预热调整,底盘件复查等。
D、整车性能检测。
主要包括:
整车的四轮定位,灯光检测,转毂试验,尾气排放,路试,淋雨密封性试验等。
其中包括整车在静态和动态下所检查出的问题的返工。
E、整车进行最终检查并交车。
F、S11及T11、B11及MPV的动力总成分装由在合装线的旁边各自的分装线完成。
分装线采用滚道输送线,在平面内进行循环。
二条装配线的动力总成合装均由AGV(AutomaticGuidedVehicle自动导引小车)来完成,合装的内容为各自的动力总成、后轴总成及排气管总成等。
AGV上的夹具(以S11、T11线为例)分为二块,前面一块为动力总成的夹具,后面一块为后轴总成的夹具。
在夹具设计时要求对不同车型的后轴总成夹具实现兼容,对不同车型的动力总成夹具(合装夹具与分装夹具相同)要求其与AGV相对定位保持不变,上部支撑部件可不同,这样在动力总成上AGV时将动力总成及夹具整体从分装线上移到AGV即可。
G、B11、MPV装配线同时辅以车门分装线及仪表板分装线,二条分装线的生产节拍均为:
2×8×251×60×0.85/100000=2。
05≈2(min),设计节拍为1.2—3.6min范围内可调.在B11、MPV生产线上同时还配备一定数量的装配机械手,以减轻工人的劳动强度。
H、保险杠、转向柱、柱式悬挂等分总成在带专用夹具的工作台上进行装配。
J、为提高生产效率,装配时广泛采用气动工具和电动工具,二条线在产量达到一定规模时,其车轮螺栓紧固将采用定扭矩组合扳手。
3、主要技术要求
(1)、初步估算S11及T11车在线装配时间约为8小时,生产线平均工作密度为2。
5,生产节拍为1。
5min,设备的负荷率为0.85,车位数=8×60/(2。
5×1。
5×0.85)≈150个车位,一期实排出113个(待产量增加需要增加车位时,将车间内西北角的外协件从临时存放地移出,可增加约20个车位)。
其中一次内饰车位48个(增加后可达到68个),底盘装配车位17个,二次内饰、液体加注、四门二盖调整及整车静态检测等48个车位。
估算B11及MPV车在线装配时间约为7小时,生产线平均工作密度为2.5,生产节拍为2.0min,设备的负荷率为0。
85,车位数=7×60/(2。
5×2.0×0。
85)≈99个车位,实排出97个,其中一次内饰车位约38个,底盘装配车位约15个,二次内饰、液体加注、四门二盖调整及整车静态检测等车位44个。
B11及MPV车门分装线装配工作量约为75min,分装线平均工作密度为2.0,生产节拍为2。
0min,设备的负荷率为0。
85,车位数=75/(2.0×2。
0×0.85)=22个车位,实际排出20个;B11及MPV仪表板分装线装配工作量约为40min,分装线平均工作密度为1。
1,生产节拍为2。
0min,设备负荷率为0。
85,车位数=40/(1。
1×2。
0×0.85)=21个车位,实际排出22个车位。
(2)、二条线的一次内饰均采用推板滑撬线,二条线的底盘装配和二次内饰均采用积放式悬挂式输送机.S11及T11推板滑撬线有效车位长48个,滑撬外廓尺寸:
LXW=6000X3000(单位:
mm);B11及B21推板滑撬线有效车位38个,滑撬外廓尺寸:
LXW=6000X3000(单位:
mm).S11及T11积放链有效车位48个,车位间距为:
5821。
6mm;B11及B21积放链有效车位43个,车位间距为:
6434。
4mm。
主要来完成整车线束、前后风挡玻璃、仪表板、转向柱、全车衬垫、四门门锁、玻璃升降器、四门玻璃、燃油及制动管路、动力总成,前后保险杠、制动液加注、车轮装配等工作.
(3)、二条线的整车液体加注及四门两盖间隙的调整在双边板式输送机上进行。
主要完成座椅、制冷剂、防冻液的加注、汽油加注、加水及四门二盖的调整等工作。
S11及T11线双边板式输送机有效车位共17个,车位间距为:
5821.6mm;B11及MPV线双边板式输送机有效车位共16个,车位间距为:
6434.4mm。
(4)、整车下线后进行100%的静态和动态检验.主要有底盘重要紧固力矩的复检,静态下各种性能的检查.整车定位参数、制动性能及尾气排放.全部合格后在室外的试车跑道上进行路试,路试的主要项目包括:
最小转弯半径、加速性能、在各种特种路面的专项测试等。
路试做完合格后,整车进行淋雨密封性试验,淋雨密封性要满足QC/T900-97标准的各项指标要求.
(5)、在整车装配过程中,为保证生产的持续高效地进行,S11与T11通用一种吊具,B11与MPV通用一种吊具。
五、劳动量
序号
1
2
3
4
5
工作内容
整车装配
分总成合装
整车测试
整车返工
合计
劳动量(h)
S11、T11
10
4.5
0。
3
0。
2
15
B11、MPV
9
6.5
0。
3
0.2
16
六、设备
1、设备见《设备明细表》
2、工作位置见《总装二车间工艺平面布置图》
3、有关说明
(1)、机械化运输设备
A、积放式悬挂输送机主要技术参数
序号
项目
单位
数据
备注
1
装配节拍
S11、T11
min
1.5
B11、MPV
min
2.0
2
劳动量
S11、T11
h
13
B11、MPV
h
14
3
平均工作密度
S11、T11
人
2.5
B11、MPV
人
2.5
4
车位数
S11、T11
个
113
B11、MPV
个
97
5
工位间距
S11、T11
mm
5821。
6
B11、MPV
mm
6434。
4
6
输送机工
作速度
S11、T11
m/min
1.3—4
B11、MPV
m/min
1。
2-3.6
7
输送方式
S11、T11
连续可调
B11、MPV
连续可调
B、机械化运输设备链速计算:
V=(A×T)/(F×60)
式中:
V—机械化运输设备链速,A—年生产钢领(台/年)
T—吊具(车位)节距(米/台)
F-设备年时基数(小时)
S11、T11线的工艺链链速:
V=140000×5.8216/(3413.6×60)=3。
98(m/min)
生产线的生产节拍为:
T=节距/链速=5。
8216/3.98=1.46≈1。
5(min);
B11、MPV线的工艺链链速:
V=100000×6.4344/(3413.6×60)=3。
14(m/min)
生产线的生产节拍为:
T=节距/链速=6。
4344/3。
14=1。
96≈2。
0(min)。
C、机械化输送设备分储存链和工艺链二部分,储存链和工艺链构成各自的闭环,具体接口位置等非标设计时定。
(2)、淋雨线设计满足淋雨试验标准(QC/T900—97)的要求,具体数据由非标设计时定.
(3)、整体工艺设计考虑设5条检测线,一期先上2条(满足整体年产10万辆的生产能力),待产量上来之后再考虑上其他3条。
整车返工区同时配置一定汽保设备以确保下线返工车辆的检测。
二条线的在线设备中液体加注设备均采用移动式设备以满足生产节拍要求.
七、人员
序号
名称
人数
备注
Ⅰ班
Ⅱ班
合计
1
生产工人
720
720
1440
2
辅助工人
80
80
160
3
工人小计
800
800
1600
4
技术管理人员
35
30
65
合计
835
830
1665
八、车间组成及面积
1、车间面积组成
序号
名称
面积(m2)
备注
一、生产面积
1、
生产线
22756
2、
检测线
5304
3、
返工区
9480
小计
37540
二、辅助面积
1、
通道
14576
2、
外协件临时存放地
7632
3、
其他
2302
小计
24510
三、办公、生活面积
1、
办公室
1044
2、
更衣间
1130
小计
2174
总计
64224
2、厂房说明
(1)、厂房共8跨,其中24m跨共6跨,18m和12m跨各1跨,总宽174m;柱距12m,长为300m和228m.屋架下弦标高为8。
7m,地面载荷为3000Kg/m2。
总面积为414×132+228×42=64224m2。
(2)、厂房柱网尺寸:
12×24m、12×18m和12×12m。
(如《总装车间工艺平面布置图》所示)
(3)、生活间:
在厂房的东侧69-70柱之间,宽6m、长174m的面积做二层结构的办公楼,底层作辅助办公用地,二层作为办公室用。
一层的高度为4。
0m,二层的高度为3.0m,荷载为250kg/m2。
在厂房北侧靠边56-68柱长72m,宽15.5m的面积做高度为3。
6m的更衣室。
(4)、悬挂载荷及屋架梁要求(未考虑公用动力管线、空调等的负荷):
A、屋面为单顶双面屋脊,两侧向厂房屋脊处有5%的坡度,屋架下弦最低点标高为8。
7m。
B、在整个厂房内的每根24m跨、18m跨和12m跨的屋架梁段上,各个吊点均能承受3500kg的垂直力和水平力300kg.受力位置未定,但每一个梁段承受不超过18000kg的垂直总负荷和2000kg的水平总负荷。
具体吊点分布见《总装车间工艺平面布置图》中的A—A剖视图.
C、每根立柱除承受屋架梁负荷外,还要承受距柱边约0.1m的垂直力3000kg。
D、关于驱动站和张紧站:
驱动站的重量约为1800Kg,张紧站重量约为1250Kg;另外驱动站检修平台的重量约为1500Kg,拉紧站修理平台重2000kg。
作用于驱动框架上的总水平力为2500Kg,张紧站水平力为1000Kg。
各平台均用四个吊杆吊到辅助吊梁或屋架梁上。
(5)、厂房屋面架设风机,要求厂房内每小时换气二次.
3、工艺平面布置
具体详见《总装工艺平面布置图》
九、材料消耗
待具体工艺设计做完后定.
十、物料运输
1、年运输表
2、
序号
物料名称
单位
数量
起运点
到达点
运输方式
一、运入
1、
油漆车身
S11、T11
辆
140000
涂装车间
总装车间
机械化
B11、MPV
辆
100000
涂装车间
总装车间
机械化
2、
发动机
S11、T11
台
140000
发动机厂
总装车间
电动叉车
B11、MPV
台
100000
发动机厂
总装车间
电动叉车
3、
外协件
S11、T11
吨
91000
物流中心
总装车间
电动叉车
B11、MPV
吨
88000
物流中心
总装车间
电动叉车
二、运出
合计
S11、T11
吨
7800
总装车间
地点待定
电动叉车
B11、MPV
吨
8000
总装车间
地点待定
电动叉车
说明:
(1)、检验合格的油漆车身分别从涂装二车间和涂装三车间由输送链送入储存链上,由储存链直接上工艺链进行装配.
(2)、大的总成件如发动机总成、变速箱总成经检验合格后由电瓶叉车直送装配工位旁。
(3)、在总装车间的西侧和北侧各设一个外协件临时存放地。
质保部检验合格的件入物流中心库,再送到此处临时存放,根据生产线旁的生产管理看板所填写的情况由电动平板车将件送到装配线或分装工位旁.
(4)、汽油自车间的南侧的试车跑道内的埋地储油罐通过埋地的输送管路送至汽油加注机,其它液体在厂房内设专用仓库存放,由电动叉车送至加注工位旁。
2、车间内的物流运输方式
车间内工位间的外协件的转运主要通过电动叉车和专用转运小车来实现,叉车的选用原则上其起重量不超过1吨。
十一、节能及能耗
1、节能措施及节能效果(略)
2、动能消耗表
序号
名称
规格
单位
消耗量
备注
1
电力
Kw
4000
小时最大
2
压缩空气
0。
6Mpa
m3/h
12000
小时最大
3
生产用水
一般
m3/h
0.5
小时平均
循环
0.4
4
蒸气
0.6—0.7Mpa
t/h
2。
8
小时最大
3、说明:
1、
(1)、为保证在没有天然采光或采光不足的情况下能正常工作,在厂房内全面积范围内设厂房结构照明,在工作地另设工艺照明。
全车间照度不低于150Lux,装配线、分装区、检测线及返工区等工作区域均需设工艺照明,保证车内、外混合照度不低于350Lux;补漆工作区、油漆检查区等工作区域也需设工艺照明,保证车内、外混合照度不低于500Lux;AUDIT间照度不低于800Lux。
(2)、为保证适宜的工作环境,在厂房内设置屋面通风和工作区域内的工位送风.工位送风前期主要采用风扇和自然风,后期采用空调送风。
十二、职业安全卫生、环境保护
1、安全卫生
(1)、根据国家和地方有关安全卫生方面的政策,以及《工业企业设计卫生标准》、《工业企业噪声标准》等规范,设计中对确保安全生产和职工人身安全、改善工人劳动条件和环境等方面均采取切实可行的保护措施。
(2)、一般性安全保护措施
A、厂房内设置PVC涂料(或水磨石)地面、通道、安全楼梯等。
B、厂房内通道以不同颜色标出,宽度按《机械工业职业安全卫生设计规定》的要求设计。
在设计中厂房内通道的宽度定为4m。
(个别通道宽度例外)
C、厂房内设醒目的安全标志。
D、输送机跨通道、作业区时,下方设金属安全护网,上、下坡设捕捉器。
E、电器设备及汽油输送系统装设可靠的安全接地装置。
(3)、防机械伤害
A、对高速运转的零件均设置安全防护装置,防异物飞出伤及人身。
B、所有平台设有围栏、扶梯等。
C、地坑要有围栏或盖板等。
(4)防振动
设计中选用优质的气动工具,以减小振动对操作者的伤害。
(5)、防毒、防尘、防有害气体
生产过程中产生对周围有害的排放物主要为面漆返工区的烤漆产生的漆雾、整车返工区、整车发动机调整和尾气分析处的尾气。
面漆返工主要在补漆线和点修补间内进行,补漆线和点修补间在工艺设计时已考虑了排气;在发动机预热调整处设废气抽吸系统,及时排出有害气体;在整车返工区及检测线均采用地面抽风的型式进行排气;底盘喷蜡间在设计时考虑通风装置.
(6)、防静电措施
所有易产生静电作用的设备、管路均设置防静电的接地装置.
(7)、防雷击措施
汽油储存罐放置处考虑防雷击措施。
(8)、防火、防爆措施
根据国家消防规范及地方部门的相关要求,设计中将采用下列消防措施:
A、各建筑物间的防火间距符合《建筑设计防火规范》的要求,各主要建筑物周围设置环形通道,保证消防车能达到任何位置。
B、根据厂房内的危险级别,确定建筑物的耐火等级。
厂房内烤漆房,汽油加注区为一级防火区,采用CO2、泡沫灭火剂或干粉灭火剂.油脂、油漆、石蜡等化学品集中由涂装车间或化学品库存放。
C、保证各建筑物均有两个以上的安全出口.
D、建筑结构设计按地震基本烈度七级设防。
(9)、对土建、公用设施的设计要求
A、厂房设计、施工必须符合国家规定的防火等级,厂房墙壁、立柱、屋架应刷防火涂料.
B、在办公室和其他辅助用地要设置隔断。
C、办公室共设外线电话6部,内线电话11部;计算机网络线布置待办公室区域最后确定后与生产部共同确定。
2、环保
环境保护设计坚持“以预防为主,防治接合,综合治理”的原则,主要遵循的规定有:
(1)、《建设项目环境保护设计规定》
(2)、《大气环境质量标准》
(3)、《地面水环境质量标准》
(4)、《城市区域环境噪音标准》
(5)、《工业“三废”排放试生标准》
(6)、《汽油车怠速污染物排放标准》
(7)、安徽省、芜湖市有关环境保护方面的规定
根据环境影响评价大纲要求,区域大气环境质量控制在城市《大气环境质量标准》的二级标准内,噪音应符合《城市区域环境噪音标准》
十三、工艺概算
工艺投资概算表
序号
项目名称
投资(万元)
备注
S11、T11
B11、MPV
1
设备
6500
6800
2
工位器具
70
80
3
气动、电动、手动工具
480
370
4
厂房柱基基础及钢结构
1400
1300
5
厂房地坪及设备基础
1350
1250
6
厂房内照明及工艺管线
200
150
7
其他
300
250
8
合计
10300
10200
十四、主要数据和技术经济指标
序号
名称
单位
数据
备注
一、主要数据
1、
年产量
辆
240000
2、
年总劳动量
小时
3220000
3、
设备总数
台
171
4、
厂房总面积
平方米
64224
生产面积
平方米
37540
辅助面积
平方米
24510
5、
人员总数
人
1665
操作工人
人
1440
辅助工人
人
160
6、
电力安装容量
Kw
4000
7、
工艺总投资
万元
20500
二、技术指标
1、
每平方米面积年产量
台/平方米
3。
74
2、
每平方米生产面积年产量
台/平方米
6.39
3、
每工人年产量
台/人
150
4、
每操作工人年产量
台/人
166。
7
5、
每台主要生产设备年产量
辆/台
1403.5
6、
每台主要设备占厂房面积
平方米
375.6
7、
每台产品劳动量
小时
13、14
8、
主要生产设备平均负荷率
%
85
9、
每台产量占工艺总投资
元
854。
2
十五、存在的问题和建议
1、本次工艺设计是在缺少相关资料仅靠拆车和参照A11总装线原先经验的基础上做出的工艺布置,实际施工过程中工艺布置进行局部调整将难以避免。
2、本次工艺设计将B11与B11的MPV、B21混线生产,由于B11的MPV、B21车型未最终确定,对车门分装线及仪表板分装线来说吊具的兼容来说有一定风险,但只要车型确定后,可将其吊具作适当调整后即可满足生产要求.
3、S11、B11按现有产品配置表定义来看均是一车多机的装配,对动力总成分装线的分装夹具设计来说,可能是一套夹具不能解决问题.现在解决的办法是,先期用单个分装台来进行分装,待发动机及变速箱的型式确定后,再考虑上分装线。
4、整车