工艺设计说明书.docx
《工艺设计说明书.docx》由会员分享,可在线阅读,更多相关《工艺设计说明书.docx(40页珍藏版)》请在冰点文库上搜索。
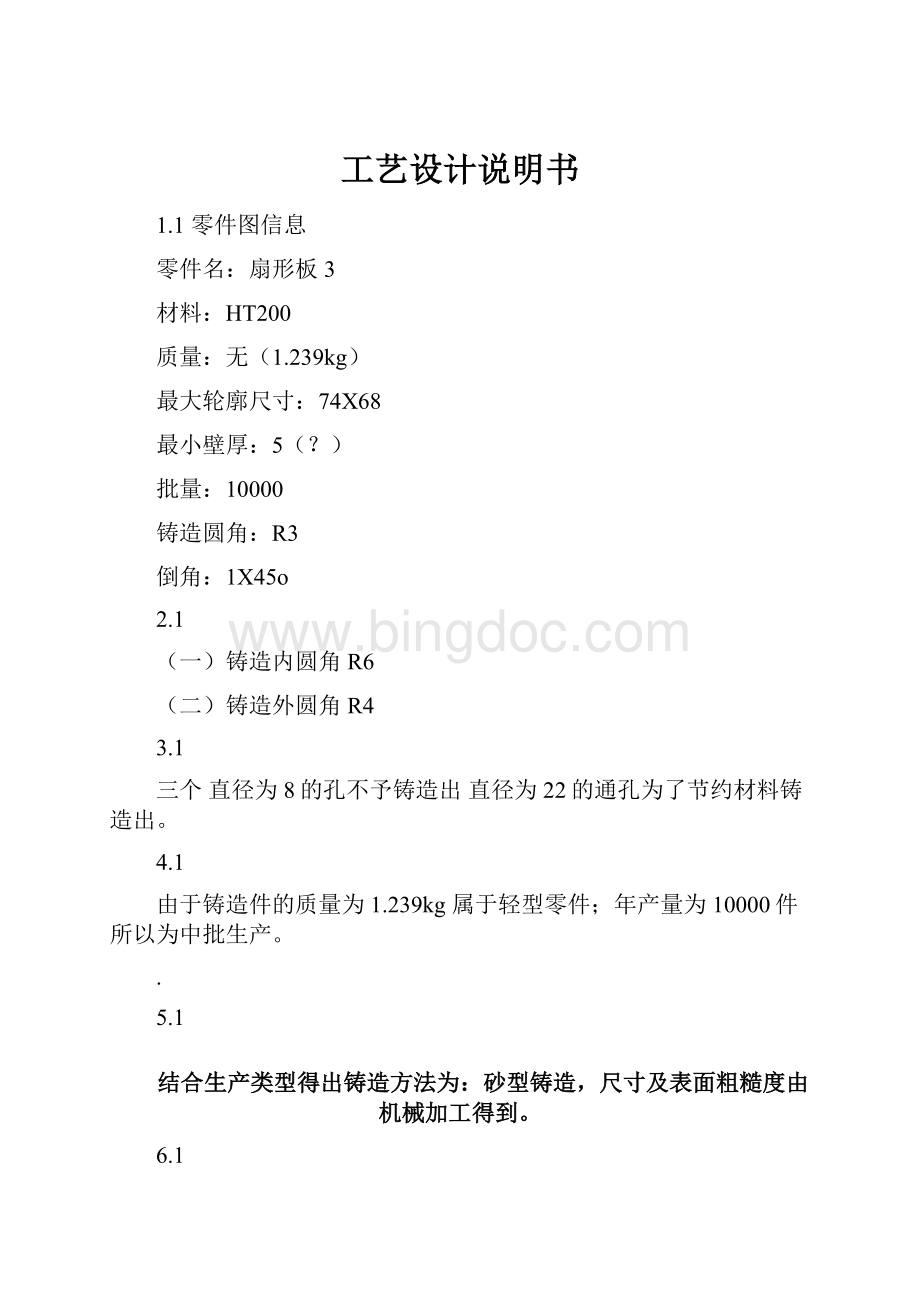
工艺设计说明书
1.1零件图信息
零件名:
扇形板3
材料:
HT200
质量:
无(1.239kg)
最大轮廓尺寸:
74X68
最小壁厚:
5(?
)
批量:
10000
铸造圆角:
R3
倒角:
1X45o
2.1
(一)铸造内圆角R6
(二)铸造外圆角R4
3.1
三个直径为8的孔不予铸造出直径为22的通孔为了节约材料铸造出。
4.1
由于铸造件的质量为1.239kg属于轻型零件;年产量为10000件所以为中批生产。
.
5.1
结合生产类型得出铸造方法为:
砂型铸造,尺寸及表面粗糙度由机械加工得到。
6.1
选择湿型
7.1
首选手工造型、砂箱造型
8.1
表面粗糙度为6.3的为分型面
9.1
1工艺分析
2.2工艺设计要求的内容
对铸件的结构工艺性,应综合考虑以下四个方面的要求:
1、合金的铸造性能对铸件结构的要求
为了保证铸件质量,必须首先考虑合金的铸造性能对铸件结构的要求。
(1)铸件应有合理的壁厚为避免浇不足、冷隔、铸铁件白口组织等缺陷,铸件壁厚不宜设计过薄。
但铸件壁厚也不能设计过厚,否则,会使铸件中心部分晶粒粗大,降低合金的力学性能指标,且容易在中心区出现缩孔、缩松等缺陷。
对于中小型铸件来说,铸件壁厚既不要小于最小壁厚
(表2.1),又要尽量在临界壁厚
(表2.2)以下。
一般认为,各种合金的临界壁厚可按最小壁厚的3倍来估算。
表2.1砂型铸造的最小壁厚
合金种类
铸件轮廓尺寸/mm
<200×400
200×200--400×400
400×400--800×800
>800×800
灰铸铁
3--4
4--5
5--6
6--12
孕育铸铁
5--6
6--8
8--10
10--20
球墨铸铁
3--4
4--8
8--10
10--12
可锻铸铁
3--5
4--6
5--7
-
碳钢
5
6
8
12--20
铝合金
3--5
5--6
6--8
8--12
锡青铜
3--5
5--7
7--8
-
黄铜
≥6
≥8
-
-
表2.2砂型铸造时铸件的临界壁厚
铸造合金种类或牌号
铸件质量/kg
0.1--2.5
2.5--10
>10
HT100、HT150
8--10
10--15
20--25
HT200、HT250
12--15
12--15
12--18
HT300
12--18
15--18
25
HT350
15--20
15--30
25
球墨铸铁
10--18
15--20
50--60
可锻铸铁
6--10
10--12
-
碳钢
15--18
20--25
-
铝合金
6--12
6--12
10--14
锡青铜
-
6--8
-
由于轮廓尺寸为74X68,质量1.239kg,HT200
最小壁厚为:
3——4,
临界壁厚为:
12——15
满足要求。
(2)铸件圆角及过渡尺寸铸件壁的厚薄交界处应采取逐渐过渡,壁与壁之间应采用合适的圆角连接,否则易造成应力集中,引起裂纹等缺陷。
壁间的连接应避免交叉和锐角,可防止因局部金属聚集而形成热节,从而引起缩孔或缩松。
在铸件壁的转弯处要有结构圆角。
在内外圆角的具体尺寸,与相邻壁的厚度有关,也可以查表
(铸造内圆角、铸造外圆角)得到准确的数值。
壁厚越大,圆角尺寸也相应增大。
对于小型铸铁件,外圆角半径一般取2--8mm,内圆角半径一般取4--16mm。
通常,铸件圆角半径可取相邻两壁厚度平均值的1/3--1/5。
铸造内圆角mm
a≈bb<0.8a
R1=R+aR1=R+b+c
(a+b)/2
R值
a
≤50°
51°--75°
76°--105°
106°--135°
136°--165°
>165°
铸钢
铸铁
铸钢
铸铁
铸钢
铸铁
铸钢
铸铁
铸钢
铸铁
铸钢
铸铁
≤8
4
4
4
4
6
4
8
6
16
10
20
16
9--12
4
4
4
4
6
6
10
8
16
12
25
20
13--16
4
4
6
4
8
6
12
10
20
16
30
25
17--20
6
4
8
6
10
8
16
12
25
20
40
30
21--27
6
6
10
8
12
10
20
16
30
25
50
40
28--35
8
6
12
10
16
12
25
20
40
30
60
50
36--45
10
8
16
12
20
16
30
25
50
40
80
60
46--60
12
10
20
16
25
20
35
30
60
50
100
80
61--80
16
12
25
20
30
25
40
35
80
60
120
100
81--110
20
16
25
20
35
30
50
40
100
80
160
120
111--150
20
16
30
25
40
35
60
50
100
80
160
120
151--200
25
20
40
30
50
40
80
60
120
100
200
160
201--250
30
25
50
40
60
50
100
80
160
120
250
200
251--300
40
30
60
50
80
60
120
100
200
160
300
250
>300
50
40
80
60
100
80
160
120
250
200
400
300
c和h值
b/a
0.4
0.5~0.65
0.66~0.8
C
≈0.7(a-b)
≈0.8(a-b)
≈a-b
h
≈8c(铸铁);≈9c(铸钢)
铸造外圆角mm
表面的最小边尺寸P
R
外圆角a
≤50°
51°--75°
76°--105°
106°--135°
136°--165°
>165
≤25
2
2
2
4
6
8
26--60
2
4
4
6
10
16
61--160
4
4
6
8
16
25
161--250
4
6
8
12
20
30
251--400
6
8
10
16
25
40
401--600
6
8
12
20
30
50
601--1000
8
12
16
25
40
60
1001--1600
10
16
20
30
50
80
1601--2500
12
20
25
40
60
100
>2500
16
25
30
50
80
120
(一)铸造内圆角R6
(二)铸造外圆角R4
3)铸件壁厚应力求均匀铸件壁厚若相差悬殊,使锻件冷却先后不一致,会形成较大的内应力,导致铸件变形甚至开裂;或在厚大因补缩困难而产生缩松、缩孔等缺陷。
(4)尽量避免有过大的水平面铸型在浇注时,如果型腔内有较大的水平面。
当液态金属上升到该位置时,由于断面突然扩大,上升速度减慢,灼热的液态金属较长的时间烘烤顶部型面,极易造成夹砂、浇不足、冷隔等缺陷。
同时,也不利于非金属夹杂物和气体的排除。
因此,应尽量设计成倾斜壁,以防止上述缺陷的产生。
(5)铸件的厚壁处应考虑补缩方便当铸件中必须有厚壁部分时,为了不使其产生缩孔,铸件的结构应具备定向凝固和补缩条件。
特别是对于凝固时收缩较大的合金,如铸钢、高强度灰铸铁、球墨铸铁和黄铜等,一般考虑把铸件的厚壁部分放在上部,以便于用冒口进行补缩,防止产生缩孔和缩松。
2.铸造工艺对铸件结构的要求
考虑铸造工艺对铸件结构的要求,主要是为了简化造型操作,以提高劳动生产率。
(1)简化铸件结构,减少分型面,针对零件图,从简化铸件结构出发,看是否可通过简化使铸造工艺变得比较简单。
如对中小铸件来说,当孔径小于30mm,糟的截面积尺寸小于30mm×20mm时,可以不予铸出,留待以后钻孔或将糟铣出更为经济合理。
但有些铸件很小,孔径虽小于30mm,但若不铸出时会明显增加金属耗费和加工工时,或会形成过分的金属聚聚积,可能导致缩孔或缩松时,则略小于30mm的孔也可以铸出。
对铸件上不加工的孔,一般均应铸出。
通过简化铸件结构,使分型面只有一个,可以顺利地采用两箱造型,从而可避免采用两个或两个以上的多箱造型的方法,以降低错型、偏芯等缺陷的可能性。
三个直径为8的孔不予铸造出直径为22的通孔为了节约材料铸造出。
(2)尽量使分型面平直。
(3)尽量减少或不用型芯。
能用一个型芯铸出型腔的,就不要使用两个型芯;能自带型芯的,就不要另造型芯。
对尺寸较小,易于用机械加工方法得出的孔或内腔,不用型芯铸出铸出。
对于内腔形状简单,可用砂垛来形成的,则不用型芯铸出,称为
自带型芯。
自带型芯砂垛若位于下半铸型,也叫“堆砂”,应满足H/D<1(H--自带型芯铸孔高度,D--铸孔直径);自带型芯若位于上班铸型,也叫“吊砂”,其高度H应低些,一般满足H/D=0.25--0.3。
为了造型操作方便,自带型芯铸孔的起模斜度应适当增大。
(4)尽量避免造型时取活块。
在单件小批生产条件下,铸件侧壁上如果有凸台,可采用活块造型。
但活块造型操作难度较大,造型工作量也大。
在生产批量较大或机器造型时,可把离分型面不远的凸台延伸到便于起模的地方,可免去或减少起活块操作。
(5)垂直壁应考虑结构斜度。
垂直于分型面的非加工面,应设计有一定的结构斜度,这样不但便于起模,而且也因模样不需要较大啊的松动而提高了铸件的尺寸精度。
(6)考虑型芯的固定、清理和出气在设计铸型型芯时应考虑型芯在铸型中固定牢靠、平稳,排气通畅,清理出砂方便。
3.切削加工对铸件结构的要求
由于对铸造毛坯的切削加工往往在零件制造成本中占有很大的比例,因此所设计的铸件应考虑以下两点:
(1)减少切削加工量如果能使铸件结构可减少车削、铣削、刨削、钻削、镗削、等加工量,则可有效地降低加工成本。
(2)利于切削加工这里包括为便于铸件在机床上安装平稳,或为了使铸造工艺过程简化,切削加工易于进行,而将整体式铸件改为组合式铸件。
另外,为了便于切削加工时的进刀、退刀,在铸件的加工面上应留空刀槽
4.考虑节约金属材料的铸件结构
在铸件结构设计时,还应考虑节约金属材料问题。
如铸件壁厚在满足使用性能的前提下不要厚。
应按照铸件各部位对强度的不同需要合理地分配金属,避免为铸件某处需提高承载能力,而将整个铸件的尺寸都增加。
若能减掉铸件上不必要的多余的金属材料,尽量避免实心厚壁结构,采用工字型结构等,都可以有效地节约金属材料,达到降低成本的目的。
2生产类型确定
由于铸造件的质量为1.239kg属于轻型零件;年产量为10000件所以为中批生产。
.
3铸造方案确定
在设计中铸造方案确定包括以下几个内容:
1、铸造方法的确定
2、浇注位置的确定
3、分型面的确定
4、砂箱中铸件数目的确定
1、铸造方法确定:
铸造方法比较表格查询
铸造方法
砂型
熔模
金属型
压力
低压
离心
陶瓷型
比较项目
适用金属
无限制
无限制,以铸钢件为主
无限制,以铸造非铁合金为主
铝、镁、锌等低熔点合金
以铸造非铁合金为主
以铸铁、铜合金为主
无限制,以铸钢件为主
适用铸件大小
几克到数百吨
25Kg以下
以中小件为主
一般10Kg以下,中型件也可
以中小件为主
几公斤到数吨
以大、中铸件为主
经济批量
无限制
100-5000件
大批、大量
最少1000件
成批、大量
几百件
单件、小批
铸件尺寸精度
IT15-IT14
IT14-IT11
IT14-IT12
IT13-IT11
IT14-IT12
内孔尺寸偏差大
IT13-IT12
铸件表面粗糙度μm
50-100
(12.5-25)
3.2-12.5
(0.8-1.6)
3.2-50
(0.8-1.6)
1.6-25
(0.4-0.8)
1.6-25
(0.2-0.4)
0.8-25
(0.2-0.8)
3.2-12.5
(0.8-1.6)
铸件内部质量
结晶粗
结晶粗
结晶细
结晶细,内部有气孔
结晶细
结晶细
结晶粗
铸件加工余量
大
小或不加工
小
小或不加工
小
内孔加工余量大
小或不加工
生产率
低、中
低、中
中、高
最高
中
中、高
低
最小壁厚
2.5-5
0.5-0.8
铝合金2-3铸铁>4
0.5-1
一般最小0.7
6
1
应用举例
要求不高的中小件,大型或复杂件
刀具、刀杆、机床零件、辅件
水暖器材、活塞、一般的铸造非铁合金铸件
要求较高的铸造废铁合金铸件、汽车、电器仪表应用件
箱体、壳体、缸盖、纺织机械零件
要求组织致密的回转体铸件、铁管、缸套、铜套
厚大的精密铸件、锻模、冲模、压铸模、模版
注:
在铸件表面粗糙度一栏中:
1)、括号外为可以达到的粗糙度;
2)、括号内为采取特殊措施才可以达到的粗糙度。
结合生产类型得出铸造方法为:
砂型铸造,尺寸及表面粗糙度由机械加工得到。
2、铸型种类
铸型选择
铸型种类
主要特点
应用情况
干型
铸型经烘干,水份少,强度高,透气性好,可避免由湿型而引起的一些铸造缺陷。
但燃料耗费多,成本高,工艺过程复杂,生产周期长,劳动条件差,不易实现自动化
结构复杂,质量要求高的单件,小批生产的中大型铸件
表面干燥型
只将铸型表面层烘干(烘干厚度约为10-80mm),克服干型的部分缺点,保持干型的一些优点。
降低了成本,提高了生产率
结构复杂,质量要求高的单件,小批生产的中大型铸件
湿型
铸型不烘干。
优点是成本低、生产率高、劳动条件得到改善易于实现机械化、自动化。
但铸型水份多,强度低,易产生呛火,夹砂、气孔、冲砂、粘砂、涨箱等铸造缺陷
单件,成批和大量生产的中小件,机械化,自动化的流水线生产中。
自采用膨润土活化砂后,大大扩大了湿型的应用范围
自硬型
铸型靠型砂自身的化学反应而硬化,一般不需要烘干,或经低温烘烤。
优点是强度高、粉尘少、效率高。
但成本较高,易生产粘砂等缺陷。
由于砂子回用困难,为了减少自硬砂的用量,可采用复砂铸型,即用普通砂作为背砂,用自硬砂作为面砂。
自硬砂根据使用粘结剂的不同有水玻璃类和树脂类等。
目前我国由于树脂供应困难故以水玻璃类应用最广。
水玻璃类根据使用硬化剂的不同可分为:
1、二氧化碳法:
利用吹二氧化碳气体使铸型硬化,硬化快,效率高。
2、加热法:
利用加热使铸型硬化,耗费燃料,生产周期长。
3、硅铁粉法:
在型砂内加入硅铁粉经化学反应而硬化。
此法硬化快,效率高,但放出氢气,所以大量采用时应注意有发生爆炸的可能。
4、炉渣自硬砂法:
在型砂内加入炼钢炉渣而硬化。
此法利用废料,成本低,但需破碎设备。
5、赤泥自硬砂法:
型砂中加入赤泥,硬化较慢,一般需经200度左右的烘烤,但成本较低。
各种铸件均可采用,但以铸钢件,中大型铸件应用较多
水泥砂铸型
用普通水泥,或双快(快干,快凝)水泥蔚粘结剂制成铸型,具有自硬,干强度高,发气量少,初砂性能好等优点,有利于保证铸件质量和尺寸精度,造型方便,旧砂可回用。
但硬化周期较长,制备好的型砂保存事假不宜太长
适用于单件、成批生产,特别是机床等类型的中大型铸件
石灰石砂铸型
用破碎成粒状的石灰石砂,来代替一杆的硅砂做成自硬性铸型。
具有硅粉尘少,易清理的优点,因而对消除工人的矽肺病有利。
但应用于大件时有缩沉,及一氧化碳中毒现象,而且旧砂回用困难。
目前主要应用于铸钢件的生产中
流态砂铸型
由于在赤泥自硬砂中加入发泡剂而使型砂具有一定的流动性,因此灌入砂箱内,不需人工捣实,自行硬化。
具有造型效率高,劳动条件好等优点,但易出现粘砂和缩沉缺陷,砂子也难回用
应用于中大型铸型及砂芯
铁模复砂型
是最近发展起来的一种制造厚大球铁件的铸型。
铁模用一般灰铸铁制成,砂层可用树脂砂,钒土水泥流态砂等。
复砂层厚约为5-15mm左右。
这种铸型刚度大,有利于利用球铁的缩前膨胀,可减轻或消除球铁内的缩孔和缩松。
提高了质量,降低劳动强度,但铸型费用高,旧砂不可回用
应用于成批大量生产厚大的球铁铸件如曲轴等
选择湿型
3、造型、造芯方法选择
常见的铸型有砂型、金属型、薄壳型等。
其中,以砂型铸造最为常用。
造型和造芯方法可分为两大类:
手工和机器。
应全面考虑铸件结构特点、技术要求、生产批量、车间条件等因素,选择合适的方法。
3.1造型方法:
手工造型
造型方法
主要特点
应用情况
砂箱造型
在专制的砂箱内造型,操作比较方便,劳动量较小
大、中、小铸件,大量、成批和单件生产均可采用
劈箱造型
将模样和砂箱分成相应的几块,分别造型,然后组装起来。
这样使造型、烘干、搬运、和箱检验都比较方便
常用于成批生产的大型复杂铸件,如机床床身、大型柴油机的机身
叠箱造型
将几个甚至十几个铸型重叠起来浇注,可节约金属,充分利用生产面积
可用于成批的中、小件、小型铸钢件应用较多
脱箱造型
造型后将砂箱取走,在无箱或加箱套的情况下浇注
用于大量、成批或单件生产的小件
地坑造型
在车间地坑中造型,不用砂箱或只用盖箱。
操作较麻烦,劳动量大,生产周期长
对于单件生产的中、大型铸件,当缺少相应的砂箱时,常采用此法
刮板造型
用专制的刮板刮制铸型。
可节省制造模样的材料和工时。
操作麻烦,生产率低
多用于单件小批生产、外形简单的回转体铸件
组芯造型
铸型由多块砂芯组装而成,可在砂箱、地坑中或用夹具组装
用于单件或成批生产、结构复杂的铸件
流态砂造型
这是一种先进的造型方法。
将可流动型砂灌入砂箱,不用紧实,靠硬化剂使铸型硬化。
这种造型方法简单省力,卫生条件好,生产率高
多用于单件或成批生产的中、大件,成批生产的小件也可采用
机器造型
造型种类
主要特点
应用范围
震实式
靠造型机的震击来紧实铸型。
机器结构简单,制造成本低。
但噪声大,生产率低,对厂房基础要求高,劳动繁重
可用于大量或成批生产的中、小件,应用较少
震压式
在震击后加压紧实铸型。
造型机的制造成本低,生产率较高,噪声大
可用于大量或成批生产的小件,常用于脱箱造型
微震压实式
在微震的同时加压紧实铸型。
生产率高,机器较易损坏
用于大量或成批生产的中、小件
压实式
用较低的比压压实铸型。
机器结构简单,噪声较小,生产率较高
用于大量或成批生产的矮小铸件
高压造型
用较高的比压压实铸型。
生产率高,铸件尺寸准确,易于自动化。
但机器结构复杂,制造成本高
用于大量生产的中、小铸件
射压式
用射砂填实砂箱,再用高比压压实铸型。
生产率高,易于自动化
用于大量生产的中、小铸件
抛砂造型
用抛砂的方法填实和紧实铸型。
机器的制造成本较高
用于大量或成批生产的大型铸件
首选手工造型、砂箱造型
3.2造芯方法
手工造芯
造芯方法
主要特点
应用范围
芯盒造芯
用芯盒的内表面形成砂芯的形状,砂芯尺寸准确,可制造小而复杂的砂芯
各种形状、尺寸和批量的砂芯均可采用
刮板造芯
与刮板造型相似
用于单件小批生产、形状简单的回转体砂芯
机器造芯
造芯种类
主要特点
应用范围
压实式
一般以压缩空气为动力,生产率较高
用于小砂芯的大量、成批生产
震实式及翻台震实式
目前,这种机器应用得较普遍,但噪声大,生产率不高,对厂房基础要求高
适用于制造内部不填焦炭块的中、大砂芯的成批、大量生产
挤压式
利用机械传动,将芯砂从成型管连续压出而制成砂芯
用于大量生产的截面形状尺寸不变的小砂芯
射芯式
使芯砂悬浮在压缩空气流内,以高速射入芯盒内而制成砂芯。
砂芯紧实度均匀,尺寸准确,操作方便,生产率高,易于机械化
用于成批、大量生产中、小型的简单和较复杂的砂芯,多用于油砂、合脂砂。
水玻璃砂
热芯盒射芯式
把以呋喃I型为粘结剂,氯化铵为催化剂的芯砂射入经预热的芯盒内,硬化后取出,得到表面光滑,尺寸精确,强度较高的砂芯。
操作方便,生产率高,易于清理,改善了劳动条件。
不需另设烘烤设备,易于机械化
用于成批、大量生产中、小型形状复杂的砂芯
壳芯式
以热塑性固态酚醛树脂为粘结剂,乌洛托品为固化剂的芯砂,利用自重加入热芯盒,并补加吹压,待形成薄壳后,经摇摆把多余的芯砂倾倒回储砂斗,形成薄壳砂芯。
操作简单,生产率高,节省芯砂,劳动条件好
用于成批、大量生产中型的,形状比较复杂的芯砂
没有不用选了
4浇注位置确定
(1)应将铸件的重要加工面或主要受力使用面等要求较高的部位放在下面。
例如,机床床身,导轨面是关键部分,其浇注位置应当是把导轨面放到最下面。
床身浇注位置1-出气孔2-直浇道
(2)薄壁铸件应将薄而大的平面放在下面或侧面、倾斜。
浇注位置的选择应有利于铸型的充型和型腔中气体的排出,所以,薄壁铸件应将薄而大的平面放到下面或侧面,以防止出现浇不足和冷隔等现象。
对流动性差的铸造合金应特别注意这个问题。
如下图
电动机端盖
(3)当铸件壁厚不均,需要补缩时,应从顺序凝固的原则出发,将厚大部分放到上面或侧面,以便安放冒口和冷铁。
当铸件需要冒口补缩时,最好使补缩部位处于铸件的上部,便于安放冒口补缩。
对于机械加工要求较高的零件,如起重机卷筒(见下图),或者对于表面质量要求高而不经加工就使用的零件(如钢锭模)可采用雨淋式浇注系统。
对收缩较小的灰铸铁,当壁厚差别不大时,也可以将厚部分放到下面靠自身上部的铁水补缩而不用冒口。
起重机卷同
(4)确定浇注位置时应尽量减少砂芯的数量。
确定浇注位置时应尽量减少砂芯的数量,这样有利于砂芯的定位、稳固、排气和检验方便。
而且,较大的砂芯应尽量使芯头朝下,尽量避免砂芯吊在上箱或悬臂或仅靠芯撑来固定。
可采用多个铸件共用一个砂芯来减少砂芯的数量。
选择表面粗糙度为3.2的放在下面,这样会有掉砂。
5分型面的确定
(1)分型面一般选取在铸件的最大截面上。
以便顺利取出模样,同时应注意减低砂箱的高度,便于取模。
如图所示:
(2)尽量将铸件的重要加工面或大部分加工面和加工基准面放到同一个砂箱中,而且尽可能的放在下箱。
以便保证铸件尺寸精度,减少铸件的飞边毛刺。
如图所示:
(3)尽量使分型面是平面。
为了便于生产操作,减少制造工艺装备的费用。
分型面应尽量采用平面,但在大批大量生产时,有时也要采用不平的分型面(如凹凸面、折面、曲面等)。
如摇臂铸件和曲轴铸件选用了曲面分型后使清理工作量可大为减少,同时铸件整齐美观。
(4)应尽量减少分型面的数量。
当机器造型时,通常只用一个分型面,而手工造型时,可根据需要,选择两个以上的分