电阻焊点焊培训资料教材.docx
《电阻焊点焊培训资料教材.docx》由会员分享,可在线阅读,更多相关《电阻焊点焊培训资料教材.docx(11页珍藏版)》请在冰点文库上搜索。
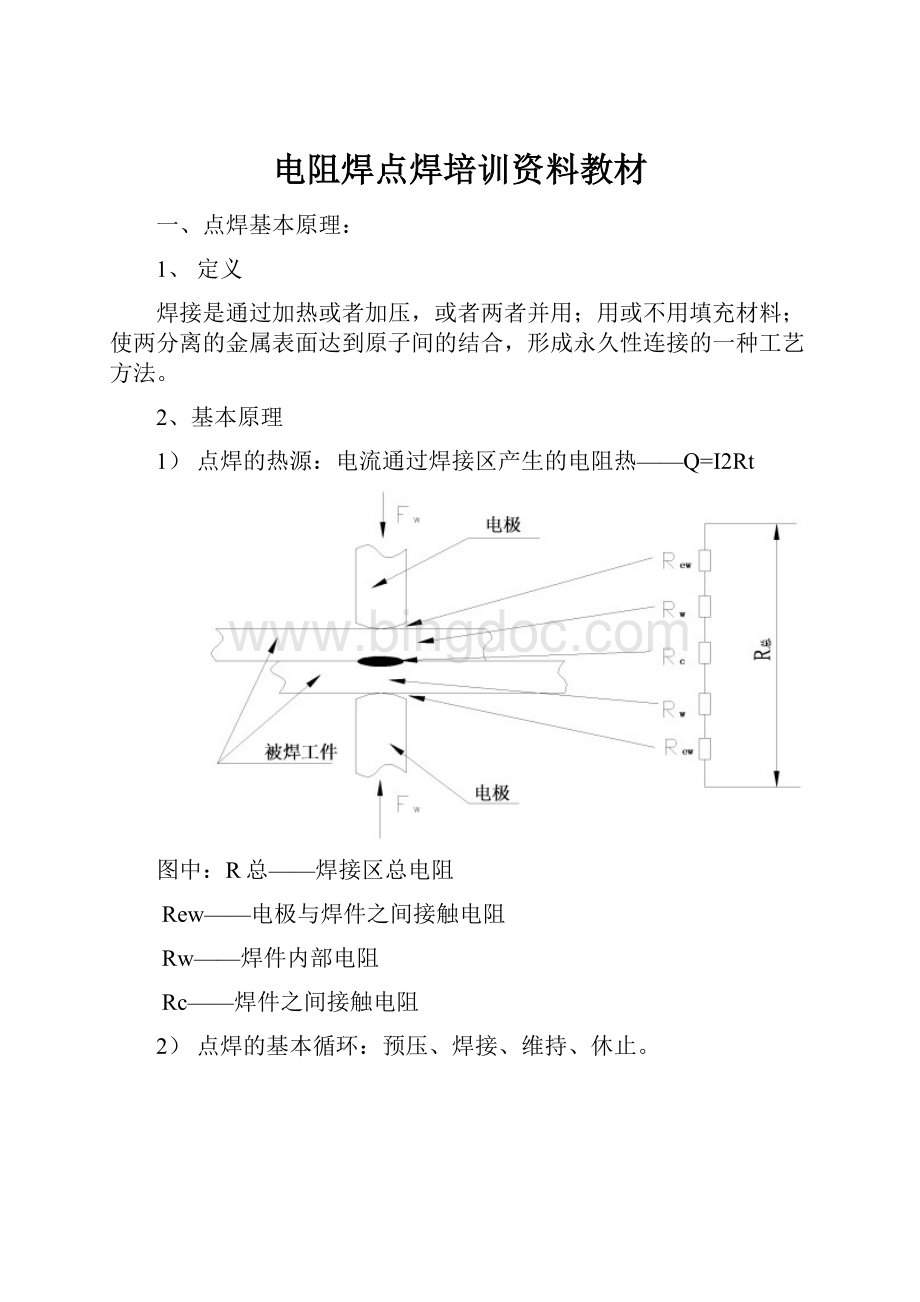
电阻焊点焊培训资料教材
一、点焊基本原理:
1、定义
焊接是通过加热或者加压,或者两者并用;用或不用填充材料;使两分离的金属表面达到原子间的结合,形成永久性连接的一种工艺方法。
2、基本原理
1)点焊的热源:
电流通过焊接区产生的电阻热——Q=I2Rt
图中:
R总——焊接区总电阻
Rew——电极与焊件之间接触电阻
Rw——焊件内部电阻
Rc——焊件之间接触电阻
2)点焊的基本循环:
预压、焊接、维持、休止。
一个完整的点焊形成过程包括预压程序,焊接程序,维持程序,休止程序。
在预压阶段没有电流通过,只对母材金属施加压力。
在焊接程序和维持程序中,压力处于一定的数值下,通过电流,产生热量熔化母材金属,从而形成熔核。
在休止程序中,停止通电,压力也在逐渐减小。
预压的作用:
在电极压力的作用下清除一部分接触表面的油污和氧化膜,形成物理接触点。
为以后焊接电流的顺利通过及表面原子的结合作好准备。
焊接、维持的作用:
其作用是在热和机械(力)的作用下形成塑性环、熔核,并随着通电加热的进行而长大,直到获得需要的熔核尺寸。
休止的作用:
其作用是是液态金属(熔核)在压力作用下更好的冷却结晶。
1、工艺参数的匹配及影响因素
3.1点焊工艺参数及其选择
1)点焊焊接参数:
焊接电流,焊接时间,焊接压力,电极端面直径。
a焊接电流:
焊接时流经焊接回路的电流称焊接电流。
对点焊质量影响最大,电流过大产生喷溅,焊点强度下降。
b焊接时间:
电阻焊时的每一个焊接循环中,自电流接通到停止的持续时间,称焊接通电时间。
时间长短对点焊质量影响也很大,时间过长,热量输入过多也会产生喷溅,降低焊点强度。
焊接电流和焊接时间是通过控制箱进行控制的,可以利用编程器进行设定。
c电极压力:
通过电极施加在焊件上的压力。
当压力过小,易产生喷溅;压力过大时,使焊接区接触面积增大,电流密度减小,熔核尺寸下降,严重时会出现未焊透的缺陷。
一般认为,在增大电极压力的同时,适当加大焊接电流或焊接时间以维持焊接加热程度不变。
焊接压力是通过压缩空气产生的,所以点焊时的气压值决定了焊接压力,一般要求的气压为:
0.4——0.6Mpa
d电极头端面尺寸:
电极头是指点焊时与焊件表面相接触的电极端头部分。
电极头端面尺寸增大时,由于接触面积增大,电流密度减小,散热效果增强,均使焊接区加热程度减弱,因而熔核尺寸减小,,使焊点承载能力降低。
电极头端面尺寸的增大△D<15%D。
端面直径一般要求在ф6——8mm,超过8mm就需要及时进行修磨
2)根据工件的材料、板厚按下表的工艺参数选择。
板厚(mm)
电极直(mm)
焊接压力(N)
通电时间(s)
焊接电流(A)
1.0
5
1000--2000
0.2—0.4
6000--8000
1.2
5
1000--2500
0.25—0.5
7000--10000
1.3
6
1500--3500
0.25-0.5
8000--12000
2.0
8
2500--5000
0.35—0.6
9000--14000
3.0
10
5000--8000
0.6—1.00
14000--18000
4.0
11
6000--9000
0.8—1.2
15000--20000
5.0
13
8000--10000
0.9—1.5
17000--24000
6.0
15
1000--14000
1.2—2.00
20000--26000
3)根据工艺参数修整电极直径到确定尺寸。
电极的端面直接与高温的工件表面接处,在焊接过程中反复承受高温、高压,端面变形是着重考虑的问题。
通常电极的顶角α≥120°,以利于端面散热和增强抗变形能力;边缘需要倒圆(R0.75mm),焊点压痕边缘能圆滑过渡,以提高接头的抗疲劳强度。
具体见图示:
电极的端面直径d最大值:
4.8mm(0.8mm板件)、6.4mm(1.0mm板件)、6.4mm(1.2mm板件)、6.4mm(1.5mm板件)、8.0mm(2.0mm板件)。
4)利用与被焊件相同材料及板厚的试板进行试焊,检查质量合格后方可进行焊接生产
3.2点焊产热的影响因素
1)电阻的影响
R=2Rew+2Rw+Rc
2)焊接电流和焊接时间的影响
焊接电流和焊接时间的适当配合,以反映焊接区加热速度快慢为主要特征,分为硬规范(采用大焊接电流、小焊接时间参数)和软规范(采用小焊接电流、适当长焊接时间参数)。
硬规范——大焊接电流、短的焊接时间
软规范——小焊接电流,适当延长焊接时间参数
两种规范在调节I、T使之组成不同的硬、软规范时,必须相应改变电极压力Fw。
硬规范电极压力大,软规范反之。
3)电极压力的影响
焊接电流I和电极压力Fw适当配合的特征:
A焊接过程中不产生喷溅;
B规范选择在喷溅临界曲线附近(无飞溅区内)可获得最佳焊接质量。
4)电极形状及材料性能的影响
电极的功能:
向工件传导电流、向工件传递压、迅速导散焊接区的热量力。
合格的电极头
5)工件表面状况的影响
在焊接前对板件表面的油污、灰尘进行处理,以保证焊点质量。
二、操作要领:
1、安全规范
1)正确佩戴劳保用品,专用手套、劳保鞋、面罩、围裙、防护眼睛。
2)现场危险源识别。
2、焊接设备检测
1)焊接压力一般不予检测,但必须检查气压表,气压表范围0.3~0.6Mpa,当气压<0.3Mpa时,严禁使用焊钳(焊接加油口座焊钳除外);
2)焊装车间定期对焊接设备、工装进行维护保养,如实填写设备、工装点检纪录卡;
3)电极头修磨标准:
每焊接300焊点修磨依次,焊接6000焊点更换一次电极头(允许10%的标准点数偏差)
3、焊点保护
1)增加铜片
2)电极头修磨
A:
电极修磨频次规定
①在焊接点数达到400~500点时要求修磨电极一次;
②对于特殊电极、三层板以上的焊接电极、安全焊点焊接电极应300点修磨电极一次;
③焊接6000焊点更换一次电极头(允许10%的标准点数偏差);
当电极使用出现以下情况时,必须停止焊接,立即修磨电极:
①电极边沿发毛或端面直径超过8mm
②极接触端直径小于6mm
③电极面不平,有明显凹坑或者太尖
④上下电极错位,修磨电极无法达到理想效果时,可调整电极
不合格的电极头
电极的磨损会使接触表面直径增大,使焊接电流密度减小,形成加热不足及焊不牢。
因此对电极直径增加规定了范围,见下表。
超过规定范围,必须进行修整或更换,然后方可焊接。
现场工程师、巡检人员根据焊点质量现场情况,可要求员工立即进行电极修磨。
电极直径范围要求
电极接触表面直径(mm)
4
5
6
8
10
11
12
13
电极接触表面最大直径(mm)
5
7
8
10
12
14
15
16
3)焊钳姿态:
焊接时,电极头与板件垂直,保证焊接压力,确保焊接质量。
4)车间稳定特殊工序、关键工位操作人员的稳定,避免因人员流动造成质量问题。
4、吹水
环境温度低于零下4度时,必须对焊钳水管(机器人内部焊钳)进行吹水。
5、电极帽管理
焊装车间实行电极帽统一修磨,所有焊钳的电极帽分规格型号,在规定的时间点实行统一更换,送库房由专业维修工统一修磨。
二、检查方法
1、焊点检查项目:
焊点数:
偏差≤5%标准点数;
焊点间距:
偏差≤15%标准间距(当夹具上焊接位置有干涉时,焊点间距可不作严格规定,但连续焊点处必须限制偏差);
焊点直径:
偏差≤15%标准直径;
焊点压痕:
h<0.15*板件厚度;
焊点表面裂纹:
不允许;
电极粘损:
不允许;
焊点毛刺:
不允许;
焊点骑边:
≤8%标准点数,且不连续;
表面缩孔:
不允许;
焊点未焊透:
不允许;
焊点不平整、板件变形:
不允许(焊接时垂直焊接);
板件表面烧伤、烧穿:
不允许;
板件装配间隙:
0.1~2mm;
焊点最小点距:
12mm(0.8mm、1.0mm板件)、14mm(1.2mm、1.5mm板件)、16mm(2.0mm板件);
焊点最小边距:
4.5mm(0.8mm板件)、5mm(1.0mm板件)、5.5mm(1.2mm板件)、6mm(1.5mm板件)、7mm(2.0mm板件);
焊点熔核直径:
4.6~5.3mm(0.8mm板件)、5.3~5.8mm(1.0mm板件)、5.5~6.2mm(1.2mm板件)、6.3~6.9mm(1.5mm板件)、7.1~7.9mm(2.0mm板件)。
2、检验方法:
1)点焊撕裂试验(关特工序每周一次,其余每月一次),优质焊点的标志是:
在撕开试样的一片上有圆孔,另一片上有圆凸台。
2)拉伸试验(每月一次)
3)在线非破坏性试验(每天抽检):
检验时,利用扁铲对准焊点附近的两板件之间,用锤子敲入,直到能够看到两板之间有熔核连接为合格。
4)整车撕裂试验(半年一次)。
3、常见焊点缺陷及原因
1)、虚焊(未焊牢)
虚焊产生的原因:
电极端部直径过大,焊接电流过小。
2)、焊点压痕太深(板件凹陷)
焊点压痕太深产生的原因:
焊接电流太大,电极端部尺寸太小,电极压力不适当。
3)、焊点扭曲(板件变形)
焊点扭曲产生的原因:
上下电极未对正,电极端部在通电时滑移,电极端部整形不良,工件与电极不垂直。
4)、过烧(易烧穿)
过烧产生的原因:
焊接电流大,电极压力太小
5)、电极粘损(电极损坏)
电极粘损产生的原因:
电极修磨不到位,电极压力过小。
6)、飞溅大(火花大)
飞溅大产生的原因:
电极压力不足,焊接电流过大,通电时电极移动,上下电极错位。
7)、焊点周围上翘
焊点周围上翘产生的原因:
焊接电流过大,电极压力太大,电极端部过小,工件接触不良,上下电极不正。
8)、裂纹、缩孔、针孔
裂纹、缩孔、针孔产生的原因:
焊点未凝固前卸去电极压力,电极压力不足,焊接电流过大,通电时电极移动。
附:
“焊点八荣八耻”
四、焊点强度影响因素
1、电极压力的影响
电极压力对两电极间总电阻R有显著的影响,随着电极压力的增大,R显著减小,此时焊接电流虽略有增加,但不能影响因R减小而引起的产热的减小,因此,焊接强度总是随着电极压力的增大而降低。
解决办法:
(1)是在增大电极压力的同时,适当地增大焊接电流或延长焊接时间,以弥补电阻减小的影响,可以保持焊接强度不变。
(2)电极压力过小将引起飞溅,也会使焊点的强度降低。
2、电极形状对焊接强度的影响
点焊是一种通过电极施加压力并利用电流通过接头的接触面及邻近区域产生的电阻热进行焊接的方法,因此机械力和电阻热的适当配合是获得优质电阻焊接头的必要条件。
不同的机械作用力,即点焊时的电极压力,可使焊核组织由铸态转变为锻态,接头强度将会更高。
电极形状对接头性能也有很大影响,在其他参数不变时,电极端部越小,则焊核直径越小,熔深越大,对提高接头性能没有好处;电极端部越大,则焊核熔深越小,直径越大,太大时则不易形成焊核,影响焊点的强度性能。
因此在点焊过程中应密切关注电极形状,及时锉修,以保证焊接质量的稳定。