铝合金把手压铸模具讲解.docx
《铝合金把手压铸模具讲解.docx》由会员分享,可在线阅读,更多相关《铝合金把手压铸模具讲解.docx(38页珍藏版)》请在冰点文库上搜索。
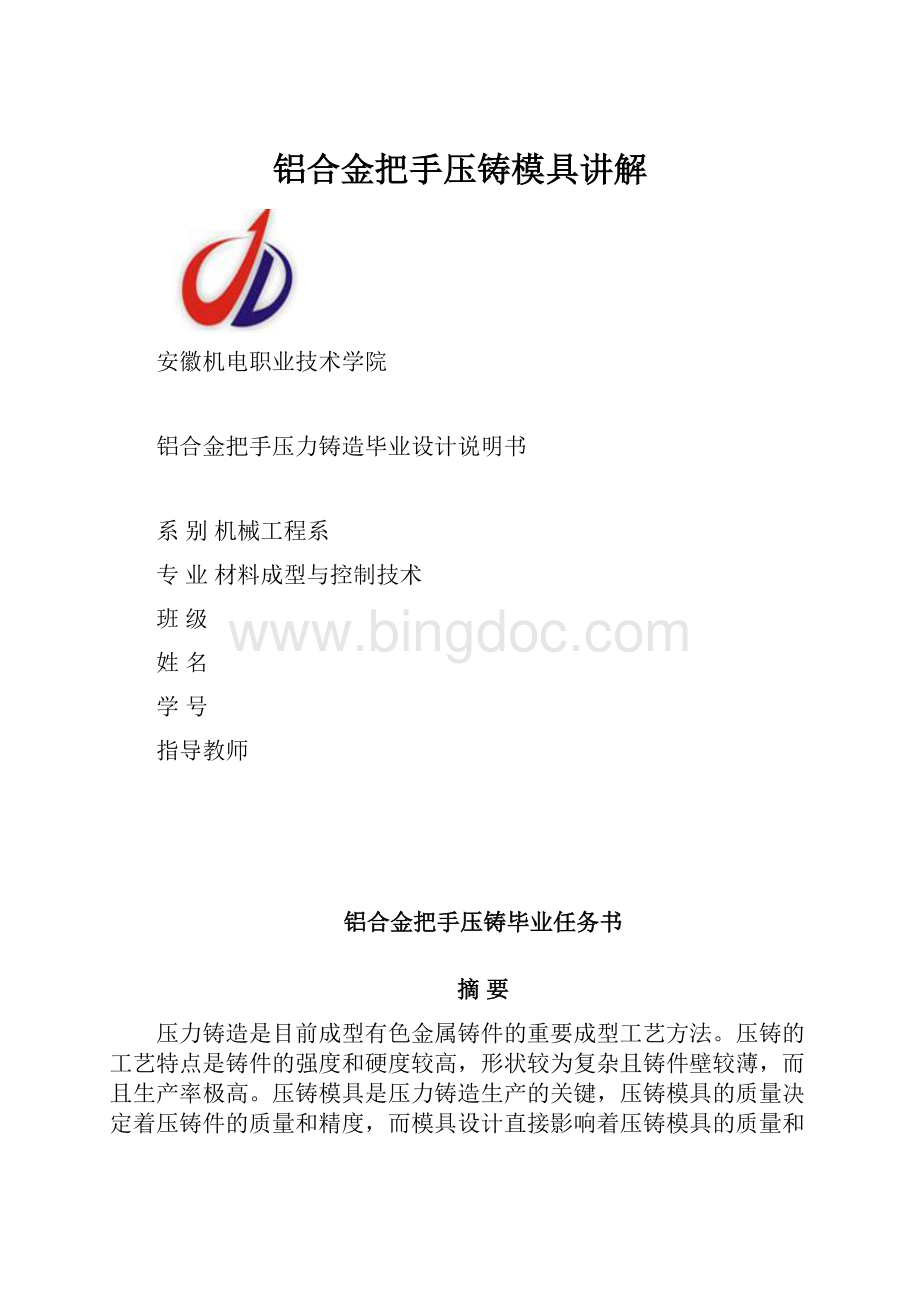
铝合金把手压铸模具讲解
安徽机电职业技术学院
铝合金把手压力铸造毕业设计说明书
系别机械工程系
专业材料成型与控制技术
班级
姓名
学号
指导教师
铝合金把手压铸毕业任务书
摘要
压力铸造是目前成型有色金属铸件的重要成型工艺方法。
压铸的工艺特点是铸件的强度和硬度较高,形状较为复杂且铸件壁较薄,而且生产率极高。
压铸模具是压力铸造生产的关键,压铸模具的质量决定着压铸件的质量和精度,而模具设计直接影响着压铸模具的质量和寿命。
因此,模具设计是模具技术进步的关键,也是模具发展的重要因素。
根据零件的结构和尺寸设计了完整的模具。
设计内容主要包括:
浇注系统设计、成型零件设计、抽芯机构设计、推出机构设计以及模体结构设计。
根据铸件的形状特点、零件尺寸及精度,选定了合适的压铸机,通过准确的计算并查阅设计手册,确定了成型零件以及模体的尺寸及精度,在材料的选取及热处理要求上也作出了详细说明,并在结合理论知识的基础上,借助于计算机辅助软件绘制了各部分零件及装配体的立体图和工程图,以保障模具的加工制造。
采用Pro/ENGINEER、AutoCad来实现铝合金把手的三维设计及模具成型零件设计,分析制件的成型质量和完成分型面的设计,再采用EMX组件来实现模架的装配,并在产品设计及模具装配过程中,辅助以必要的理论计算,为了使动、定模能够准确地动作,导向定位机构利用导柱与导套的配合。
顶出机构是推杆推出的一次脱出机构。
通过计算和查阅相关参数,确定了浇注系统和溢流系统各部分的尺寸及压铸工艺参数,绘制了铸件毛坯图和工艺图。
通过计算锁模力选定压铸机型号。
根据确定的压铸工艺方案和压铸机类型设计了压铸型,对成形部分尺寸进行了详细的计算,通过查阅相关手册确定了压铸型主要零件的结构尺寸,并对压铸型总厚度、动模座板行程和压室充满度进行了校核,绘制了压铸型全套图纸。
关键词:
压力铸造;压铸模具;AutoCad;
目录
1.前言2
1.1选题背景和意义2
1.2相关文献综述2
2.零件设计5
2.1零件分析5
2.2 初步确定设计方案 6
3.压铸件工艺分析7
3.1压铸合金工艺分析7
3.2压铸件工艺分析7
3.3分型面的选择7
4.排溢系统和浇注系统及冷却系统的设计8
4.1浇注系统的设计8
4.1.1.1内浇口分为以下几种:
8
4.2排溢系统的设计14
4.3冷却系统的设计16
5.压铸模结构设计17
5.1压铸机的选择18
5.2型腔和型芯尺寸的设计20
5.3镶块、型芯、模板的设计21
5.4滑块的设计24
5.5斜销的设计24
5.6垫块的设计24
5.7导柱、导套的设计24
5.8浇口套的设计25
5.9推出机构、复位机构的设计25
5.10模具装配图设计27
5.11压铸模的技术要求27
6.压铸机校核28
6.1压室容量的核算28
6.2模具厚度的计算28
6.3动模行程的核算28
7.压铸工艺流程29
8.结论29
9.谢辞30
10.参考文献31
1.前言
1.1选题背景和意义
压铸是最先进的金属成型方法之一,是实现少切屑,无切屑的有效途径,应用很广,发展很快。
目前压铸合金不再局限于有色金属的锌、铝、鎂和铜,而且也逐渐扩大用来压铸铸铁和铸钢件。
压铸件的尺寸和重量,取决于压铸机的功率。
由于压铸机的功率不断增大,铸件形尺寸可以从几毫米到1~2m;重量可以从几克到数十公斤。
国外可压铸直径为2m,重量为50kg的铝铸件。
压铸件也不再局限于汽车工业和仪表工业,逐步扩大到其它各个工业部门,如农业机械、机床工业、电子工业、国防工业、计算机、医疗器械、钟表、照相机和日用五金等几十个行业。
在压铸技术方面又出现了真空压铸、加氧压铸、精速密压铸以及可溶型芯的应用等新工艺。
薄壁压铸件在压铸工艺技术中,普遍都认为是有一定难度的。
由于壁薄就带来充型难;出模难;易变形;精度难以保证等等。
因此对模具的浇注系统,排气系统,模具结构,压铸工艺参数都必须严格、周密的考虑,用于压铸生产的合金材料有铝合金、纯铝、锌合金、镁合金、铜合金、铅合金、锡合金等。
压铸该把手压铸件在浇注系统、模具结构、压铸工艺等方面有一细列技术问题。
在本次设计中,解决了该把手压铸件浇注系统如何开设,如何保证充填过程中充填阻力最小,排气条件最好;模具结构如何满足该把手压铸件结构的需要;压铸工艺又如何适该把手压铸件工艺等要求。
对于实际生产有重要意义。
1.2相关文献综述
(一)压铸概念
压力铸造是液态和半固态金属在活塞的高压作用下以较高的速度充填铸型型腔,并在压力作用下凝固获得铸件的方法。
高压和高速充填压铸型是压铸的两大特点。
它常用的压射比压是从几千至几万kPa,甚至高达2×105kPa。
充填速度约在10~50m/s,有些时候甚至可达100m/s以上。
充填时间很短,一般在0.01~0.2s范围内。
(二)压铸机的选择
实际生产中并不是每台压铸机都能满足压铸各种产品的需要,而必须根据具体情况进行选用,一般应从下述两方面进行考虑:
(1)按不同品种及批量选择
在组织多品种,小批量生产时,一般要选用液压系统简单,适应性强,能快速进行调整的压铸机,在组织少品种大量生产时,要选用配备各种机械化和自动化控制机构的高效率压铸机;对单一品种大量生产的铸件可选用专用压铸机。
(2)按铸件结构及工艺参数选择
铸件外形寸尺,重量、壁厚等参数对选用压铸机有重要影响。
铸件重量(包括浇注系统和溢流槽)不应超过压铸机压定的额定容量,但也不能过小,以免造成压铸机功串的浪费。
一般压铸机的额定容量可查说明书。
压铸机都有一定的最大和最小型距离,所以压型厚度和铸件高度要有一定限度,如果压铸型厚度或铸件高度太大就可能取不出铸件。
(三)压铸工艺
在压铸生产中,压铸机、压铸合金和压铸型是三大要素。
压铸工艺则是将三大要素作有权的组合并加以运用的过程。
使各种工艺参数满足压铸生产的需要。
(四)压力和速度的选择
压射比压的选择,应根据不同合金和铸件结构特性确定。
对充填速度的选择,一般对于厚壁或内部质量要求较高的铸件,应选择较低的充填速度和高的增压压力;对于薄壁或表面质量要求高的铸件以及复杂的铸件,应选择较高的比历和高的充填速度。
(五)浇注温度
浇注温度是指从压定进入型腔时液态金属的平均温度,由于对压室内的液态金属温度测量不方便,一般用保温炉内的温度表示。
浇注温度过高,收缩大,使铸件容易产生裂纹、晶粒粒大、还能造成粘型;浇注源度过低,易产生冷隔、表面花纹和浇不足等缺陷。
因此浇注温度应与压力、压铸型温度及充填速度同时考虑。
(六)压铸型的温度
铸压型在使用前要预热到一定温度,一般多用煤气、喷灯、电器或感应加热。
在连续生产中,压铸型温度往往升高,尤其是压铸高熔点合金,升高很快。
温度过高除使液态金属产生粘型外,铸件冷却缓慢,使晶粒粗大。
因此在压铸型温度过高时,应采期冷却措施。
通常用压缩空气、水或化学介质进行冷却。
(七)充填、持压和开型时间
(1)充填时间
自液态金属开始进入型腔起到充满型腔止,所需的时间称为充填时间。
充填时间长短取决于铸件的体积的大小和复杂程度。
对大而简单的铸件,充填时间要相对长些,对复杂和薄壁铸件充填时间要短些。
充填时间与内浇口的截面积大小或内浇口的宽度和厚度有密切关系,必须正确确定。
(2)持压和开型时间
从液态金属充填型腔到内浇口完全凝固时,继续在压射冲头作用下的持续时间,称为持压时间。
持压时间的长短取决于铸件的材质和壁厚。
持压后应开型取出铸件。
从压射终了到压铸打开的时间,称为开型时间,开型时间应控制准确。
开型时间过短,由于合金强度尚低,可能在铸件顶出和自压铸型落下时引起变形;但开型时间太长,则铸件温度过低,收缩大,对抽芯和顶出铸件的阻力亦大。
一般开型时间按铸件壁厚1毫米需3秒钟计算,然后经试任调整。
(八)压铸用涂料
压铸过程中,为了避免铸件与压铸型焊合,减少铸件顶出的摩擦阻力和避免压铸型过分受热而采用涂料。
对涂料的要求:
(1)在高温时,具有良好的润滑性;
(2)挥发点低,在100~150℃时,稀释剂能很快挥发;
(3)对压铸型及压铸件没有腐蚀作用;
(4)性能稳定在空气中稀释剂不应挥发过决而变稠;
(5)在高温时不会析出有害气体;
(6)不会在压铸型腔表面产生积垢。
(九)铸件清理
铸件的清理是很繁重的工作,其工作量往往是压铸工作量的10~15倍。
因此随压铸机生产率的提高,产量的增加,铸件清理工作实现机械化和自动化是非常重要的。
(1)切除浇口及飞边
切除浇口和飞边所用的设备主要是冲床,液压机和摩擦压力机,在大量生产件下,可根据铸件结构和形状设计专用模具,在冲床上一次完成清理任务。
(2)表面清理及抛光
表面清理多采用普通多角滚筒和震动埋入式清理装置。
对批量不大的简单小件,可用多角清理滚筒,对表面要求高的装饰品,可用布制或皮革的抛光轮抛光。
对大量生产的铸件可采用螺壳式震动清理机。
2.零件设计
2.1零件分析
根据零件图得知,该零件材料:
ZL102,最小壁厚:
3mm,最大壁厚:
4.5mm,铸造公差:
IT14,该铸件是:
最大直径:
24mm,高:
3mm的圆台跟直径:
16mm,高:
22mm的圆台组合在一起的零件且中心有一个直径:
7mm,深:
15mm的圆柱型腔
具体形状如果下图:
图2.1—1零件三维图形
图2.1—2零件二维图形
2.2 初步确定设计方案
(1)此铸件的材料为ZL102,应在适当的温度下流动性较好是浇注,使能充满
型腔
(2)铸件的精度为IT14级,采用压力铸造的方法能达到此精度。
(3)确定压铸工艺及模具制造能力。
(4)确定压铸模结构(包括型腔数目,模板的尺寸设计,导柱、导套尽量使用国标能缩短制造周期,以及采用型芯、型腔镶块节约贵重金属)。
(5)模具设计是要留收缩率尺寸
3.压铸件工艺分析
3.1压铸合金工艺分析
铝合金压铸件具有以下特点:
1)铝合金有良好的压铸导电和导热性能,其密度较小ρ=2.7kg/m³,比强度和比刚度高,高温和低温的力学性能好。
2)铝合金熔铸工艺简单,成型及切削性能良好,有较高的力学性能及抗腐蚀性,是代替钢铸件的最具潜力的合金。
3)铝合金表面易形成一层与基体结合牢固的氧化膜,故大部分铝合金在淡水、海水、浓硝酸、硝酸盐、汽油及各种有机物中均有良好的耐腐蚀和抗氧化的化学稳定性及熔点都很高,故在高温工作时仍有良好的抗腐蚀和抗氧化性能。
4)铝有较大的比热容和凝固潜热,大部分的铸铝合金均有较小的结晶温度范围,组织中亦常含有相当数量的共晶体,其线收缩率较小,故具有良好的充填性能、较小的热裂倾向。
但铸铝合金仍有相当大的体收缩,易在最后凝固处生成大的集中缩孔。
5)铝合金和铁有很强的亲和力,易粘度,应在冷室压铸机上压铸。
3.2压铸件工艺分析
为了从根本上防止压铸件产生缺陷,比以低成本,连续不断地生产高质量的压铸件,必须使压铸件的结构适合于压铸。
主要对铸件的壁厚、圆角、筋、出型斜度,孔,螺纹、加工余量、文字、标志、图案等进行分析。
对次铸件壁厚均匀适合压铸。
铸件本身有斜度且能减少出型时与型壁的摩擦。
铸件边缘有孔且与型芯方向一致,所以在铸造时铸出。
铸件上有螺纹与型芯方向垂直,不宜在铸造时铸出,且螺纹的铸造模具加工时相当的困难,所以螺纹在铸件铸出后进行加工。
3.3分型面的选择
压铸模的动模和定模有一个接合面,这个接合面称为分型面。
分型面受到压铸件在模具中的位置、浇注系统设计、压铸件的尺寸精度、嵌件的位置、压铸件的推出和模具的排气等各种因素的影响,因此,在选择分型面时应遵循以下几项基本原则:
1)分型面应选在压铸件外形轮廓尺寸最大的截面处。
2)分型面的选择应使压铸件开模后留在动模。
3)分型面的选择应保证压铸件的尺寸精度和表面质量。
4)分型面的选择应有利于排气。
5)分型面的选择应有利于模具的加工。
6)分型面的选择应尽量防止或减少侧向抽芯。
7)分型面的选择应尽量减小压铸件在分型面的投影面积。
8)分型面的选择应尽量考虑到金属液的流程不宜太长。
该压铸件的分型面有以下几种:
根据选择分型面的基本原则,选用(a)分型面比较合适。
4.排溢系统和浇注系统及冷却系统的设计
4.1浇注系统的设计
浇注系统主要由:
直浇道、横浇道、内浇口和余料等组成。
4.1.1内浇口的分类与设计
4.1.1.1内浇口分为以下几种:
直接浇口侧浇口
中心浇口点浇口
4.1.1.2内浇口位置的选择
在浇注系统的设计中,内浇口的设计极为重要,在确定内浇口的位置之前,要根据压铸件型腔的基本要求情况和分型面的不同类型,合金的不同种类和收缩变形情况,压铸机设计及压铸件使用性能等因素,充分预计所选内浇口的位置队金属液充填型腔时流动状态的影响分析充填过程中可能出现的死角区和裹气部位,以便布置适当的溢流和排气系统,在选择内浇口的位置时应遵循一下几项原则:
1)内浇口导入的金属液应首先充填型腔深处难以排气的部位,而不宜立即封住分型面,造成排气不畅。
2)内浇口位置的应使流入型腔的金属液尽量减少曲折和迂回,避免产生过多的涡流,减少包卷气体。
3)内浇口一般设置在压铸件的厚壁处,有利于金属液充满型腔后补缩流的压力传递。
4)内浇口的位置应考虑到减少金属液在型腔中的分流,防止分流的金属液在汇合处造成冷接痕或冷隔现象。
5)内浇口的位置应尽量避免金属液直冲芯型,减少动能损失,防止冲蚀和产生粘膜,尤其应避免冲击细小型芯或螺纹型芯,防止产生弯曲和变形。
6)根据压铸件的技术要求,凡精度要求较高、表面粗糙度值低且不加工的部位,不宜布置内浇口,以防止去除浇口后留下痕迹。
7)内浇口的设置应考虑模具温度场的发布,以便使型腔远端充填良好。
8)在设计内浇口时,还应考虑浇注系统的切除方法。
根据内浇口的选择原则选择侧浇口为该压铸件的内浇口
如果下图:
4.1.1.3内浇口的尺寸计算
(1)内浇口截面积的计算:
AgUg=A1V1=V/τ
式中:
Ag—内浇口的横截面积,㎡
Ug—内浇口处金属液充填型腔的充填速度,m/s
A1—压室横截面积,㎡
V1—压室内金属液的流动速度,m/s
V—型腔和溢流槽的体积,m3
τ—充填时间,s
不同壁厚的压铸件,其内浇口出金属液充填时间和充填速度的经验数据刻参考下表:
推荐的充填时间和充填速度(此表摘抄于《压铸成型工艺玉模具设计》)
压铸件的平均壁厚,δ/mm
充填时间δ/s
充填速度Vg/(m/s)
1
0.010~0.014
46~55
1.5
0.014~0.020
44~53
2
0.018~0.026
42~50
2.5
0.022~0.032
40~48
3
0.028~0.040
38~46
3.5
0.034~0.050
36~44
4
0.040~0.060
34~42
5
0.048~0.072
32~40
则可选τ=0.050s,Vg=40m/s
溢流槽内金属液的质量约占零件质量的30%
所以V=[3.14×122×3+3.14×82×7+3.14×15×(82-3.52)]×(1+0.3)
≈6760.8125mm3
所以Ag=6.76×10-6/0.05×40≈3.38×10-6m2=3.38mm2
由于该压铸件较小所以先定为一模6件
所以内浇口的总结面积A总=Ag×6=20.28mm2
(2)内浇口的尺寸计算:
内浇口的深度见下表(此表摘抄于《压铸成型工艺玉模具设计》)
铸件壁厚,δ/mm
0.6~1.5
>1.5~3
>3~6
>6
合金种数
复杂件
简单见
复杂件
简单见
复杂件
简单见
复杂件
简单见
内浇口深度/mm
铅、锡合金
0.4~0.8
0.4~1.0
0.6~1.2
0.8~1.5
1.0~2.0
1.5~2.0
20~40
锌合金
0.4~0.8
0.4~1.0
0.6~1.2
0.8~1.5
1.0~2.0
1.5~2.0
20~40
铝、镁合金
0.6~1.0
0.6~1.2
0.8~1.5
1.0~1.8
1.5~2.5
1.8~3.0
40~60
铜合金
—
0.8~1.2
1.0~1.8
1.0~2.0
1.8~3.0
2.0~4.0
40~60
根据上表可以查得,内浇口深度取,2.0mm
Ag=(D+d)×h×1/2
则可取h=2mm,d=1.38mm,D=2mm
4.1.2横浇道的设计
横浇道是金属液从直浇道末端向内浇口之间的一段通道,其作用是将金属液引入内浇口,同时当压铸件冷却时用来补缩合传递静压力。
4.1.2.1横浇道的设计
横浇道主要的设计要点如下:
1)横浇道的横截面积从直浇道的末端到内浇口止,应逐渐缩小,否则横浇道中出现横截面积扩大使流过该处的金属液出现负压,由此必然会吸收分型面上的空气,并增加金属液流动过程中的涡流。
2)多型腔压铸模的一次横浇道截面积应大于二次横浇道的截面积之和。
3)横浇道截面积在任何情况下均应大于内浇口的截面积。
4)为了减少金属流动阻力,达到均衡流速,横浇道不宜突然收缩与扩张。
5)为了改善模具的热平衡条件,根据工艺需要可以设置盲浇道,同时盲浇道兼有容纳冷金属和气体的作用。
4.1.2.2横浇道的结构形势
横浇道的结构有以下几种:
因为该压铸件设计为一摸多件,所以选择(e)式作为该压铸件的横浇道。
4.1.2.3横浇道的截面积形状与尺寸
横浇道的截面积形状根据压铸件的结构特点而定,一般以扁梯形为主,特殊情况下才用双扁梯形、长梯形、窄梯形、圆形或半圆形。
根据该压铸件的结构,这里选择扁梯形横浇道截面积。
其计算如下:
Ar=(3~4)Ag=(3×3.38~4×3.38)=10.14mm2~13.52mm2,
横浇道截面积如图所示:
因为该压铸件为铝合金压铸件所以h≥b/3
所以取b=5mm,h=3mm
4.1.3直浇道的设计
直浇道是传递压力的首要部位,由于该压铸件的材料是铝合金所以才用冷室压铸机,而选择的内浇口为侧浇口,所以选用压室偏置时的直浇道。
卧室冷室压铸机用直浇道
根据零件所需的金属液质量等相关计算确定D为Φ20mm。
4.2排溢系统的设计
排溢系统是排气系统和溢流系统的总称。
4.2.1溢流槽的设计
4.2.1.1溢流槽的作用
1)容纳最先进入型腔的冷污金属液和混入其中的气体与氧化夹杂,防止压铸件产生冷隔、气孔和夹渣。
2)在选定浇注系统的情况下,溢流槽的设置可与浇注系统一起,共同起到控制金属液流动状态的作用,防止局部产生涡流,造成有利于避免压铸件缺陷的充填。
有时也用来转移缩孔、缩松、涡流包气和产生冷接痕的部位。
3)调节模具的温度分布,改善模具的热平衡状态,尤其对薄壁或充填较长的压铸件,可以减少压铸件表面流痕、冷隔和充填不足的现象。
4)在某些情况下,溢流槽可作为压铸件脱模时推杆推出的位置,防止压铸件变形及避免压铸件表面留有推杆的痕迹。
5)在压铸件对动、定模部分的包紧力接近相等时,为了防止压铸件留在定模,此时可在动模上设置溢流槽,增大压铸件对动模的包紧力,使分型时压铸件确保留于动模,便于推出机构推出脱模。
4.2.1.2溢流槽位置的选择
溢流槽位置的选择应遵循以下一些原则:
1)溢流槽应开设在金属液最先冲击的部位,排除金属液流前头的气体和冷污金属液,稳定流态状态,减少涡流。
2)溢流槽应开设在两股金属液流会合的地方,清除集中于该处的气体、冷污金属液和涂料残渣等。
3)溢流槽应开设在内浇口两侧或金属液不能顺利充填的死角区域,起到引流充填的作用。
4)溢流槽应开设在压铸件局部壁厚的地方,并且增大其容量和溢流口的厚度,以便将气体、夹渣和缩松转移到该处,改善压铸件壁厚处的质量。
5)溢流槽应开设在金属液最晚充填的地方,以改善模具的热平衡状态和充填排气条件。
6)溢流槽应开设在防止压铸件的变形。
4.2.1.3溢流槽的形状与尺寸的确定
根据选择原则该压铸件的溢流槽开设在分型面上,其基本形式如图:
选择(a),其尺寸如下
对于铝、镁合金查相关资料可得:
t取0.5~0.8,R取1mm
4.2.2排气槽的形式
1)分型面上开设的排气槽。
2)推杆与模具的配合间隙排气。
3)利用固定型芯的前端配合间隙排气。
4)利用型芯的固定部分制出排气沟槽排气。
5)深型腔处利用镶入的排气塞排气。
4.2.2.2排气槽的截面积与尺寸的确定
排气槽的截面积对于常用的锌、铝合金,在内浇口出充填速度、充填时间、压射比压机模具温度等有关工艺参数选定的情况下,可以认为:
a.排除气体的流速与气体压力、气体热状态的性质、气体的密度以及气体在型腔内的比容等有关。
b.气体通过排气槽逸出遵循连续流动原理。
c.排气时间近似等于金属液充填时间。
d.排出的气体包括型腔内、浇注系统内及压室内流入金属液后尚未充满的部分。
e.认为空气密度在温度90~315℃之间不变。
f.假定充填型腔过程中型腔内流动气体的温度等于模具型腔温度。
g.考虑在型腔充填过程中排气槽的开放度会影响排气。
根据上述要求通过推导、排气槽面积的计算公式:
A=2.24×10-3V/τk
式中:
A—排气槽总的截面积mm2
V—型腔、浇注系统、溢流槽及压室注入金属液后尚未充满部分的容积之和cm3
τ—排气时间,即等于充填时间s
k—排气槽开放度,金属液充填分型面上的型腔时容易先堵塞排气槽,k取0.1~0.3。
取k=0.2
压铸件的平均壁厚与充填时间的推荐表(此表摘抄于《压铸成型工艺玉模具设计》)
铸件平均厚度/mm
充填时间/s
铸件平均厚度/mm
充填时间/s
1
0.010~0.014
5
0.048~0.072
1.5
0.014~0.020
6
0.055~0.064
2
0.018~0.026
7
0.066~0.100
2.5
0.022~0.032
8
0.076~0.116
3
0.028~0.040
9
0.088~0.138
3.5
0.034~0.050
10
0.100~0.160
4
0.040~0.060
取τ=0.050
A=2.24×10-3×[(6760+2028)×6+π402×15]×10-3/(0.050×0.2)≈25.32mm2
4.3冷却系统的设计
4.3.1压铸模的冷却方法
压铸模的冷却方法主要有:
风冷和水冷两种。
4.3.1.1风冷:
风冷冷却的锋利通常来自鼓风机或压缩空气。
冷却的方法式奖压缩空气对准压铸模动模和定模的成型部分进行反复喷吹,以使模具热量尽快散发到空气中,从而降低模具温度。
风冷得优点是压缩空气能将模具内涂刷的涂料吹匀并加速驱散涂料所挥发出的气体,减少压铸件因涂料挥发出的其他所造成的气孔。
风冷的缺点是冷却速度较慢,通常才用人工方法进行,不能实