《采购与仓储管理》期末复习知识点.docx
《《采购与仓储管理》期末复习知识点.docx》由会员分享,可在线阅读,更多相关《《采购与仓储管理》期末复习知识点.docx(27页珍藏版)》请在冰点文库上搜索。
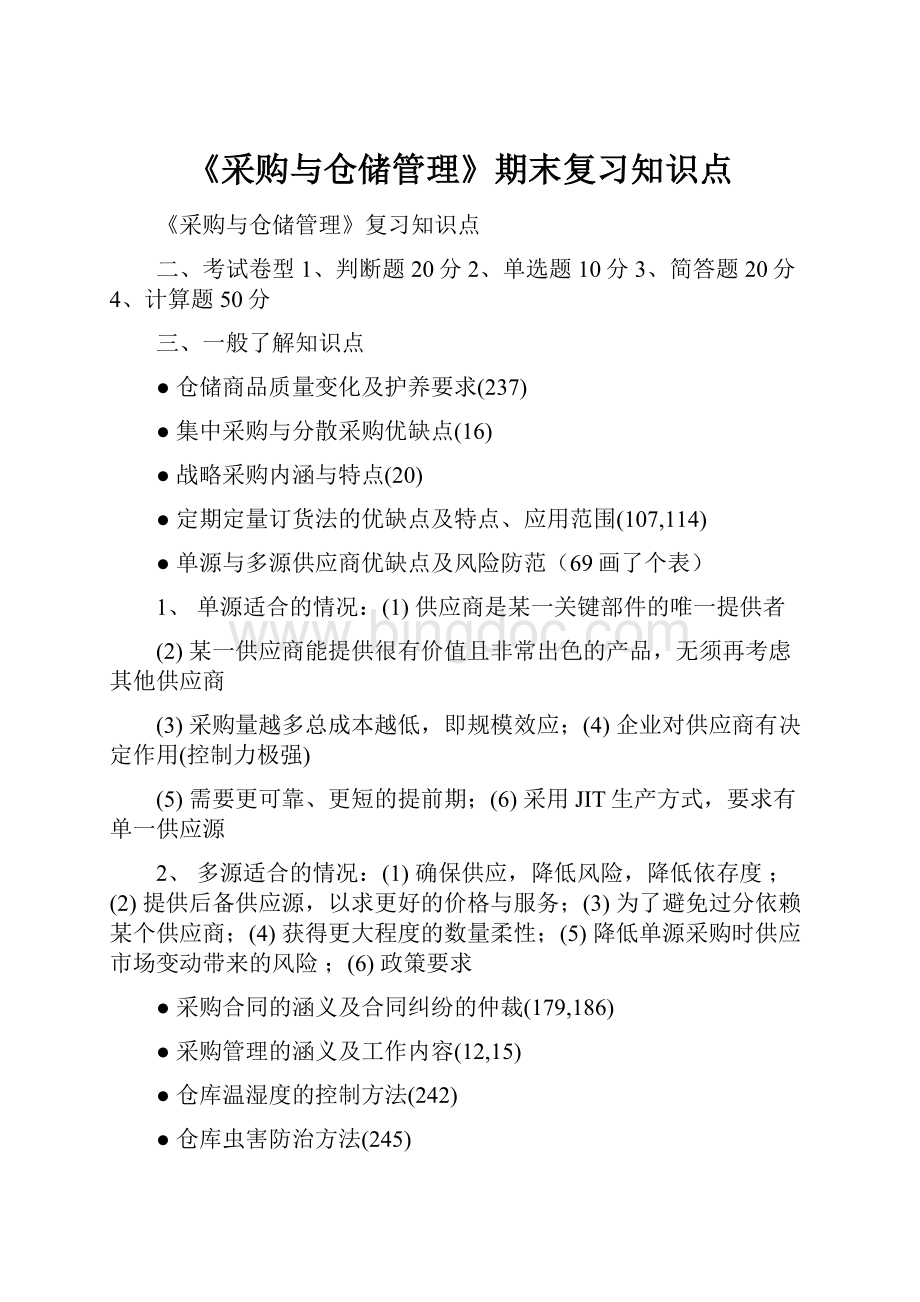
《采购与仓储管理》期末复习知识点
《采购与仓储管理》复习知识点
二、考试卷型1、判断题20分2、单选题10分3、简答题20分4、计算题50分
三、一般了解知识点
●仓储商品质量变化及护养要求(237)
●集中采购与分散采购优缺点(16)
●战略采购内涵与特点(20)
●定期定量订货法的优缺点及特点、应用范围(107,114)
●单源与多源供应商优缺点及风险防范(69画了个表)
1、单源适合的情况:
(1)供应商是某一关键部件的唯一提供者
(2)某一供应商能提供很有价值且非常出色的产品,无须再考虑其他供应商
(3)采购量越多总成本越低,即规模效应;(4)企业对供应商有决定作用(控制力极强)
(5)需要更可靠、更短的提前期;(6)采用JIT生产方式,要求有单一供应源
2、多源适合的情况:
(1)确保供应,降低风险,降低依存度;
(2)提供后备供应源,以求更好的价格与服务;(3)为了避免过分依赖某个供应商;(4)获得更大程度的数量柔性;(5)降低单源采购时供应市场变动带来的风险;(6)政策要求
●采购合同的涵义及合同纠纷的仲裁(179,186)
●采购管理的涵义及工作内容(12,15)
●仓库温湿度的控制方法(242)
●仓库虫害防治方法(245)
●商品霉变防治方法(248)
●冷藏仓库的温度要求(250)
●采购方式的分类及其特点(5)
●采购组织类型(30)
●采购岗位及其职责划分(32)
●供应商的分类及其特点(81)
●供应商管理的涵义(69)
●供应商选择与管理的基本环节(70)
●资源市场调查的内容(74)
四、重点掌握知识点
●采购申请流程(43)
●采购管理内容(15)
●MRP采购的特点(122)
●整体采购成本及其构成
整体采购成本又称战略采购成本
是除采购成本之外考虑到原材料或零部件在本企业产品的全部寿命周期过程中所发生的成本,它包括采购过程中的市场调研、自制或采购决策、产品预开发中供应商的参与、供应商交货、库存、生产、出货测试、售后服务等整体供应链中各环节所产生的费用。
●控制采购成本的主要方法
价值分析法(ValueAnalysis,VA)(适用于新产品:
针对产品或服务的功能加以研究,以最低的生命周期成本,透过剔除、简化、变更、替代等方法,来达到降低成本的目的。
)
谈判(谈判是买卖双方为了各自目标,达成彼此认同的协议过程。
谈判并不只限于价格方面,也适用于某些特定需求。
使用谈判的方式,通常期望采购价格降低的幅度约为3%-5%。
)
早期供应商参与(在产品设计初期,选择伙伴关系的供应商参与新产品开发小组。
通过供应商早期参与的方式,使新产品开发小组依据供应商提出的性能规格要求,极早调整战略,借助供应商的专业知识来达到降低成本的目的。
)
杠杆采购(避免各自采购,造成组织内不同单位,向同一个供应商采购相同零件,却价
格不同,但彼此并不知的情形,无故丧失节省采购成本的机会。
应集中扩大采购量,而增加议价空间的方式。
)
联合采购(主要发生于非营利事业的采购,如医院、学校等,通过统计不同采购组织的
需求量,以获得较好的折扣价格。
这也被应用于一般商业活动之中,如第三方采购,专门替那些需求量不大的企业单位服务。
)
为便利采购而设计(在产品的设计阶段,利用协办厂的标准与技术,以及使用工业标准
零件,方便原材料取得的便利性。
这可以大大减少自制所需的技术支援,同时也降低生产成本。
)
价格与成本分析(这是专业采购的基本工具,了解成本结构的基本要素,对采购者是非
常重要的。
如果采购不了解所买物品的成本结构,就不能算是了解所买的物品是否为公平合理的价格,同时也会失去许多降低采购成本的机会。
)
标准化采购(实施规格的标准化,为不同的产品工程或零件使用共通的设计、规格,或
降低订制工程的数目,以规模经济量,达到降低制造成本的目的。
但这只是标准化的其中一环,应扩大标准化的范围,以获得更大的效益。
)
目标成本法
●供应商管理内容(92)
供应商与资源市场的调查
供应商的选择与开发
供应商绩效考评与使用
供应商关系管理(激励与控制)
●对供应商管理的策略
完善合同;分类管理;有效的信息沟通;建立激励机制;帮助供应商成长;在供应商管理中应用“6Σ”;动态管理;结束关系
1、分类管理策略
(1)新供应商:
资质审查;价格谈判;合同条件(付款、交货期等);履约管理;
(2)合同供应商:
已建立互信关系;价格谈判是重点;强化订单备货周期、经济批量、订单执行率的分析
(3)战略供应商:
建立长期合作关系;信息共享;电子采购减少交易成本;供应商按单生产与准时供货;供应商配送;供应商管理库存;双赢。
2、“6Σ”管理法
通过“6Σ”的实施,可使公司及其供应商确定工程执行的过程,降低合作工程的实现成本,并可以估测节约幅度、计算回报率。
“6Σ”供应商管理计划的步骤:
识别对象----成本评估---优先排序---特性分析---执行计划----成果评估
3、供应商动态管理机制:
供应商的主动引入和主动退出;供应商动态调整
供应商动态管理的实施:
1)密切追踪供应商的发展变化;2)密切注意供应链环境的发展变化;3)及时调整管理策略
4、友好结束供应商关系
(1)原因:
对供应商的表现不满;供应商破产或遇到无法预测的风险;相互之间失去信任
(2)策略:
积极的态度;平和的语调;专业的理由
●如何防范被供应商控制
(1)加大库存;
(2)寻找几家供应商;(3)让最终客户参与;(4)充分利用信息;(5)协商长期合同;(6)联合采购;
(7)注意业务经营的总成本,尤其是潜在的节约成本的机会
①送货:
送货数量和次数
②延长保修期:
保修期从首次使用产品的时间算起
③付款条件:
放宽正常的付款条件
(8)增强相互依赖性;(9)心理战术。
利用供应商的垄断形象
●物料工艺消耗定额、供应系数、供应定额计算
工艺消耗定额=单位产品净重+工艺性损耗
供应系数=非工艺消耗定额/工艺消耗定额
物资供应定额=工艺消耗定额×(1+供应系数)
●基于消耗定额、产品净重、工艺损耗等技术指标的物资需求量与采购量的计算
原材料消耗=生产性消耗+非生产性消耗
生产性消耗:
有效消耗(净重);工艺性损耗(加工工艺的损耗)
.非生产性消耗:
非工艺性损耗(运输、储存、搬运等损耗)
物资消耗定额=有效消耗(净重)+工艺性损耗+非工艺性损耗=工艺消耗定额+非工艺性损耗定额
工艺消耗定额=单位产品净重+工艺性损耗
物资需要量的确定
基本公式:
某种物资需要量=生产耗用量+运输耗损量+保管耗损量-利用废料量
式中:
生产耗用量=工艺消耗定额×产量
工艺消耗定额=单位产品净重+工艺性损耗
或某种物料的需要量=计划产量×物料供应定额
其中:
物料供应定额=工艺消耗定额×(1+供应系数)
工艺消耗定额=单位产品净重+工艺性损耗
供应系数=非工艺消耗定额/工艺消耗定额
1主要原材料需要量计算
某主要材料需求量=(计划产量+技术上不可避免的废品数量)×单位产品材料消耗定额-计划回收的废品数量×单位材料消耗定额
例:
某工厂年计划生产活塞2500台,其中每个活塞胆钢材消耗定额为2公斤,废品率为15%,且技术部门统计废品回收利用率可达20%,那么,做活塞一年需用的钢材量为多少?
钢材年需要量=(2500+2500×15%)×2-2500×15%×20%×2=5750-150=5600KG/年
2辅助材料需要量的确定
某辅助材料需要量=(计划产量+废品量)×辅助材料消耗定额
不便于制定消耗定额的辅助材料采用间接计算
例:
某厂计划今年房屋大修工程投资20万元,而目前已知的是去年房屋大修投资10万元,实耗木材40立方M,今年木材需要量应为多少?
木材需要量=(40/10)×20×(1-5%)=76立方M
如果万元定额为3.5立方M,则木材需要量=3.5×20=70立方M
3燃料需用量的计算
实际品种的燃料需求量=计划产量×标准燃料消耗定额×发热量换算系数
4设备维修用料耗用量的计算
耗用量=大中小修修理单位总数×每一个修理单位的材料消耗定额
每一个修理单位的材料消耗定额=每修理单位材料平均消耗量=修理某类设备用料的全年消耗总数/某类设备的全年修理单位总数
物料储备定额
1、经常储备(周转储备)
(1)以期定量法
经常储备定额=平均每日需用量×(物资供应间隔天数+检验天数+使用前准备天数)
其中:
供应间隔天数=∑(某批物资入库量*该批物资供应间隔天数)/∑每次入库量
平均每日需要量=计划期物资需要量/计划天数
例1:
物资供应间隔天数的计算
(2)经济订购批量法
总费用(C)=采购费+订货费+库存持有成本
例:
某工厂对某种物资年需求量为8000公斤,订购费用为每次5元,单位物资保管费用为0.5元,求经济订购批量?
解:
2、保险储备定额
保险储备定额=平均每日需要量×保险储备天数
其中:
保险储备天数=平均误期天数=∑(某批物资(误期)入库量*该批物资误期天数)/∑每批误期物资入库量
例:
按上例1,假设平均供应间隔天数为30天,超过30天为误期,求平均误期天数?
平均误期天数=(24×8+16×5+24×4+20×2)/(24+16+24+20)=5天
例3:
某厂全年需用某种单价为10元的配件10000件,据生产与财务估计,此配件的保管成本为平均存货价值的20%,订购成本每批100元,公司有效工作日为300天,2006年到货情况统计如下表所示:
月份
1
2
3
4
5
6
7
8
9
10
11
12
延期天数
0
4
0
0
8
0
0
5
8
0
0
3
延期交货数量
0
60
0
0
21
0
0
15
30
0
0
20
问题:
1、该厂采购这种配件的经济储备批量为多少?
2、公司配件仓库的保险储备定额应设多少?
经济储备定额
平均延期天数
保险储备定额
保险储备定额=保险储备天数×平均每日需要量=5.4×10000/300=180件
标准差作为保险储备量
例4:
某种材料预期用量和实际用量的统计资料如下:
月份
预期用量(顿)
实际用量(顿)
预期和实际之差
差异之平方
①
②
③
④=②-③
⑤=④2
1
260
250
+10
100
2
220
225
-5
25
3
260
275
-15
225
4
230
240
-10
100
5
275
280
-5
25
6
270
260
+10
100
7
245
240
+5
25
8
270
280
-10
100
合计
700
若取标准差的2倍作为保险储备量,则保险储备≈19吨
3、季节性储备定额
季节性储备定额=平均每日需用量×季节性储备天数
例:
某企业所需要的某种物资,是由水上航运到厂的,每年12月15日停航,到来年3月15日开航,每日用料800公斤,每月按30天计算,则:
季节性储备定额=800×30×3=72000(公斤)
4、储备定额之间的关系
最高储备量=经常储备定额+保险储备定额
最低储备量=保险储备定额
平均储备量=经常储备定额/2+保险储备定额
三、计划期未(初)储备量的计算
基本公式
计划采购量=计划期需要量+计划期末库存量-计划期初库存量-可利用资源量
1、期末储备量的计算
可以认为上期的期末储备就是下期期初储备,为保证下一期的生产目的,也可认为就是最高储备量。
期末储备量=最高储备量=经常储备量+保险储备量=平均每日需用量×(物资供应间隔天数+检验天数+使用前准备天数+保险天数)
实际工作中通常采用50%—75%的经常储备量加保险储备量作为期末库存量。
2、期初库存量的计算
编制计划的时间在计划期开始以后:
用根据实际盘点数确定
编制计划的时间在计划期开始之前则:
计划期期初库存量=前期期初实际库存量+前期预计收入量-前期预计需要量
例:
假设编制计划的时间是2018年10月,则1-9月的收入和需用量可查,10-12月的收入和需用量得进行预计,计算结果如下表,得到的2018年期末预计库存量就是计划期2018年期初的库存量。
2018年计划期期初库存量=0.42+3.98-4.00=4.00
四、采购量的确定
采购计划量=该种物资的需要量+计划期末库存数量-计划期初库存量-企业内部可利用资源
物资平衡计划表
采购量=272+20-40-52=200顿
例:
某企业预计计划期内生产A产品400台,每台产品净重0.5吨,材料利用率为80%,允许废品率1%,计划期回收废料为1.5吨,编制计划时实际库存为40吨,计划期初前到货50吨,计划期初消耗60吨,计划期未库存为20吨,求物资采购量。
解:
物资需用量=400(1+1%)×0.5÷80%-1.5=251吨
计划期初库存量=40+50-60=30吨
计划期末库存量=20吨
物资采购量=251+20-30=241吨
案例:
某制造企业物料采购供应计划编制
某机械制造公司计划2018年第四季度生产甲产品600台,根据工艺部门提供的资料,已知构成甲产品(零件)耗用各材料的净重及单位产品所必需的工艺损耗情况(如表1)。
另据生产供应部门的统计报告,已知2018年前3季度制造单位甲产品各有关材料非工艺损耗情况(如表2)与2018年第三季度末甲产品所需材料库存情况(如表3),为保证2018年持续安全生产,公司物料仓储部门也计划甲产品所用各材料在年末保持适当的期末库存(如表4)。
表1单位甲产品(零件)耗用各材料的净重及单位产品所必需的工艺损耗
物料种类
构成产品净重
(公斤/台)
加工切削损耗
(公斤/台)
大型钢
30
0.3
中型钢
200
3
小型钢
100
2
中厚板
70
0.5
优质钢
200
1
无缝钢
100
2
表2单位甲产品(零件)2018年1-3季度各有关材料非工艺损耗情况统计
物料种类
非工艺损耗(公斤/台)
大型钢
0.5
中型钢
8
小型钢
1.5
中厚板
2
优质钢
2.5
无缝钢
5
表32018年第三季度末甲产品所需材料现有库存情况(如表3)
物料种类
数量(公斤)
大型钢
2000
中型钢
3000
小型钢
1000
中厚板
2000
优质钢
2500
无缝钢
2000
表4甲产品所用各材料年末计划库存
物料种类
数量(公斤)
大型钢
1000
中型钢
2000
小型钢
2000
中厚板
1000
优质钢
1500
无缝钢
1500
试计算:
甲产品的所需物料工艺消耗定额?
甲产品的所需物料供应系数?
甲产品所需物料供应定额?
第四季度甲产品的各物料的需求量?
第四季度甲产品的各物料的计划采购量?
解:
根据物资供应定额公式:
物资供应定额=工艺消耗定额×(1+供应系数)
其中:
工艺消耗定额=单位产品净重+工艺性损耗
供应系数=非工艺消耗定额/工艺消耗定额
1、甲产品的所需物料工艺消耗定额
物料种类
构成产品净重(公斤/台)
加工切削损耗(公斤/台)
甲产品的所需物料工艺消耗定额(公斤/台)=单位产品净重+工艺性损耗
大型钢
30
0.3
30.3
中型钢
200
3
203
小型钢
100
2
102
中厚板
70
0.5
70.5
优质钢
200
1
201
无缝钢
100
2
102
2、甲产品的所需物料供应系数
物料种类
甲产品的所需物料工艺消耗定额(公斤/台)
非工艺损耗(公斤/台)
供应系数=非工艺消耗定额/工艺消耗定额
大型钢
30.3
0.5
0.0165
中型钢
203
8
0.0394
小型钢
102
1.5
0.0147
中厚板
70.5
2
0.0284
优质钢
201
2.5
0.0124
无缝钢
102
5
0.0048
3、甲产品所需物料供应定额
物料种类
甲产品的所需物料工艺消耗定额(公斤/台)
供应系数=非工艺消耗定额/工艺消耗定额
物资供应定额=工艺消耗定额×(1+供应系数)
大型钢
30.3
0.0165
30.8
中型钢
203
0.0394
211
小型钢
102
0.0147
103.5
中厚板
70.5
0.0284
72.5
优质钢
201
0.0124
203.5
无缝钢
102
0.048
106.9
4、四季度甲产品的各物料的需要量
根据公式:
各物料的需要量=计划产量×物资供应定额
或=工艺消耗定额×(1+供应系数)
物料种类
物资供应定额=工艺消耗定额×(1+供应系数)
甲产品的产量(台)
各物料的需要量(公斤)=产量×物资供应定额
大型钢
30.8
600
18480
中型钢
211
126600
小型钢
103.5
62100
中厚板
72.5
43500
优质钢
203.5
122100
无缝钢
106.9
64200
5、第四季度甲产品的各物料的计划采购量
根据采购计划平衡公式:
物资采购量=物资需用量+计划期末库存-期初库存
物料种类
四季度期末计划库存(公斤)
各物料的需要量(公斤)
四季度期初现有库存(公斤)
四季度物资计划采购量(公斤)
大型钢
1000
18360
2000
17360
中型钢
2000
126600
3000
125600
小型钢
2000
62100
1000
63100
中厚板
1000
43500
2000
42500
优质钢
1500
122100
2500
121100
无缝钢
1500
64200
2000
63700
例2:
MRP物料采购计划编制
假设某公司生产A产品,现在接到客户的订单,要求出产的日期和数量如下:
产品结构层次
现有库存
采购预算编制
(1)采购预算金额=本期应购数量×购入单价;
(2)采购预算金额=物料需求计划(MRP)的请购量×标准
●价格折扣条件下的采购批量计算(116-120)
●购储总费用计算
●MRP采购计划编制逻辑与计算(125—130)
●供应商考核与选择的指标与方法(86)
供应商选择的方法
(一)定性选择方法:
1.直观判断法;2.考核选择;3.招标选择;4.协商选择
(二)定量选择法:
5.线性权重法;6.层次分析法;7.采购成本法;8.作业成本法
7.采购成本法
某企业生产的机器上有一种零件需要从供应链上的其他企业购进,年需求量为20000件,有3个供应商可以提供该种零件,他们的价格不同,质量也有所不同。
另外,这3个供应商的交货提前期、提前期的安全期及要求的采购批量均不同。
详细的数据见下表所示:
供应商
价格
(元/件)
合格品率
%
提前期
(周)
提前期的安全期
(周)
采购批量
(件)
A
9.80
88
5
2
3000
B
11.60
94
8
3
4500
C
11.40
96
3
1
2500
1、如果零件出现缺陷,需要进一步处理才能使用。
每个有缺陷的零件处理成本为8元。
处理成本主要是用于返工的费用。
2、考虑缺陷零件增加的安全量(补偿有缺陷零件的额外库存),企业用下列方式计算考虑提前期和安全期的库存数量
式中:
K——根据质量可靠性(95%)确定的系数,取K=1.64
s——标准偏差,在这里取s=80,即每周的零件数量偏差为80件;
LT——交货提前期;
LTS——交货提前期的安全期。
3、零件库存保管费用为库存价值的25%;
请依据上述给定的资料,为该企业选择供应链上的合适供应商
解:
为了比较分析评价,从购置成本(价格)、质量成本与保管成本三个方面评价零件的供应成本和排名:
1、计算质量成本
有缺陷零件的处理成本可根据不同供应商的零件质量水平来计算,结果如下:
供应商
缺陷率(%)
缺陷零件数
(件/年)
缺陷处理成本
(元/年)
单位零件质量成本
(元/件)
A
12
2400
19200
0.96
B
6
1200
9600
0.48
C
4
800
6400
0.32
注:
年缺陷零件数=年需求量×缺陷率;
年缺陷处理成本=年缺陷零件数×单位零件缺陷处理成本;
单位质量成本=年缺陷处理成本/年需求量
2、计算单位保管费率
下面以供应商A为例计算库存保管费用。
给供应商A设定的安全库存为:
供应商A要求的订货批量为3000件
由安全库存和订货批量引起的平均库存资金占用(库存物资价值)如下:
(347+3000/2)×9.80=18100.6元
分别计算ABC供应商,得到:
供应商
平均库存资金占用(库存物资价值)(元)
A
18100.6
B
31146
C
17236.8
零件库存保管费用,按库存价值的25%计算,则:
供应商
平均库存资金占用(库存物资价值)
(元)
①
年平均保管费用
(元)
②=①*25%
单位零件保管成本
(元/件)
③=②/20000
A
18100.6
4525.15
0.23
B
31146
7786.5
0.39
C
17236.8
4309.2
0.22
3、根据价格、质量成本、保管费用的综合评价:
供应商
价格(元/件)
质量成本(元/件)
保管成本(元/件)
总成本(元/件)
排序
A
9.80
0.96
0.23
10.99
1
B
11.60
0.48
0.39
12.47
3
C
11.40
0.32
0.22
11.94
2
结论:
通过对三家供应商的供货运作绩效的综合评价,在价格、质量、交货时间及订货批量方面,供应商A最有优势,最后选择供应商A为供应链上的合作伙伴。
●应用权重法选择供应商
线性权重法
某企业针对其采购的某种物资对其供应商进行考评,假定提供此种物资的供应商有四家,分别是ABCD,有关供应商的统计资料数据(在一定时间内)见下表所示:
供应商
收到的物资数量
(件)
验收合格的物资数量
(件)
供应商提供的物资价格
(元/件)
合同完成率
(%)
A
3000
2700
150
90
B
2000
1900
130
92
C
5000
4100
120
85
D
600
600
160
94
企业按照以