搪瓷工艺Word格式.docx
《搪瓷工艺Word格式.docx》由会员分享,可在线阅读,更多相关《搪瓷工艺Word格式.docx(27页珍藏版)》请在冰点文库上搜索。
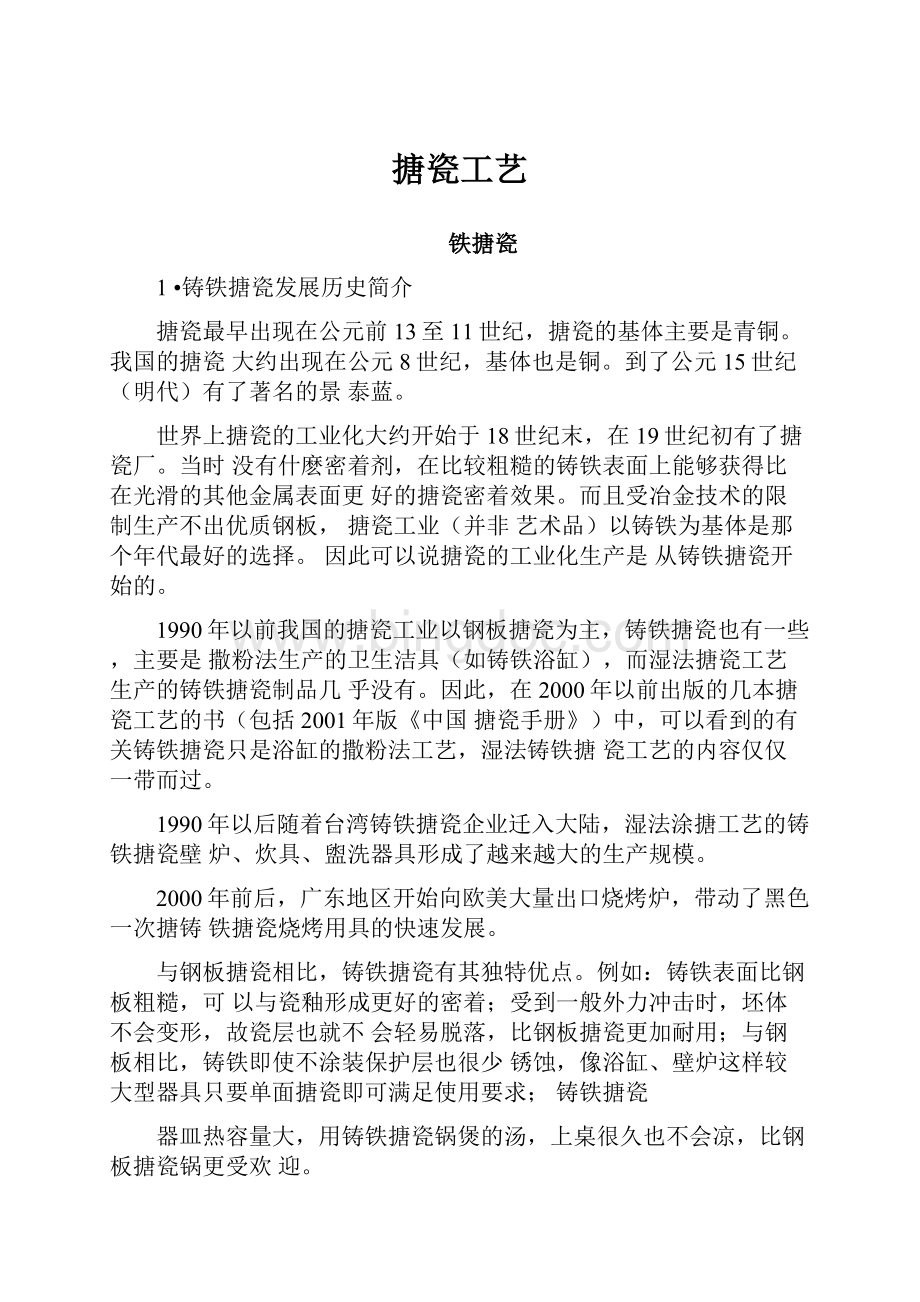
硅:
2〜2.6
硫:
v0.1
磷:
0.1〜0.5
2-3主要化学成分对铸铁和搪瓷的影响
铸铁中的合金元素分为阻碍石墨化元素(CSi、P)和促进石墨化元素
(Mn、S)两大类。
a.碳(C)
较高含量的碳能增加铸铁的强度,但搪瓷烧成时碳含量越高,分解出的二氧化碳越多,造成瓷层气泡。
薄壁产品碳含量应适当高一些,以增加坯体强度;
厚壁产品碳含量可适当低一些,以减少瓷层气泡或针孔
b.硅(Si)
硅含量过高使铸铁变脆,过低则翻砂困难。
硅促进化合碳转变成石墨,可减少瓷层气泡或针孔。
C.磷(P)
磷增加铁水的流动性,使薄壁或大型铸件合格率提高;
磷含量过高,会降低铸件的强度和韧性(变脆)。
铸铁中磷含量很小,对搪瓷质量无影响。
d.硫(S)
硫对铸造和搪瓷都有害,硫增大收缩量并降低铁水的流动性,使浇铸不良;
硫阻碍石墨化过程,使铸铁硬脆,并增加瓷层气泡或针孔。
e.锰(Mn)
锰含量低于0.5%,使铸铁材质变软;
高于2%使材质变硬。
锰与硫化合生成硫化锰进入熔渣,漂浮在铁水的上面,从而降低铸铁中的硫含量。
硫化锰还易于在铸件表面析出,因此对毛坯仔细打磨和抛丸,可减少瓷层气泡或针孔。
2-4•与搪瓷有关的铸铁性能
2-4-1铸铁的机械性能
布氏硬度143〜229
抗拉强度>
100MPa
抗弯强度>
260MPa
抗压强度>
500MPa
制造搪瓷化工设备用的铸铁还须检验抗弯强度。
2-4-2铸铁的物理性能
2-4-2-1热膨胀
铸铁的热膨胀不仅与其化学成分有关还与铸造工艺有关,型模的湿度、浇铸后的冷却速度以及脱模时间的早晚都会影响铸件的热膨胀。
因此搪瓷厂应要求铸造厂制定严格的铸造工艺,以保持铸件的尺寸一致。
铸件在搪瓷前处理和瓷釉烧成过程中,当温度超过600r时,膨胀系数
会发生突变,且热膨胀不可逆,一般伸长1〜2%或更多。
搪瓷厂在按客户
来样设计模具图时必须考虑到铸件的受热伸长量。
灰口铸铁在高温热处理后的膨胀系数,平均在400x10-7/r左右。
2-4-2-2铸铁的吸气性
在加热熔化过程中,金属不断吸收与其相接触的气体的性质,叫做“吸
气性”。
铁水凝固过程中,金属吸收的气体不断以气泡形式析出,若气泡留在铸
件中则形成气孔称为“析出性气孔”。
这种气孔在铸件浇铸时的上部或最后
凝固部位最为密集,是造成瓷层气泡或针孔的原因之一。
2-4-2-3铸铁内气体的扩散
气泡和针孔是铸铁搪瓷最常见的缺陷。
除了瓷釉高温流动性等影响因素
外,瓷层出现气泡或针孔与铸铁中气体的饱和程度有直接关系。
铸铁吸入的气体越多,瓷层产生的气泡也越多。
有人认为铸铁中溶解的氢或烧成时吸收的气体比在钢板中容易扩散。
事
实证明情况正好相反。
例如,厚钢板单面搪瓷一般不会产生鳞爆,但单面铸铁搪瓷却能产生鳞爆。
气体在铸铁内部不易扩散还反映在铸铁烤网的“耐烧试验”上,铸铁烤网在刚出炉的最初24小时内,经过600C下保温1小时瓷
面可以不起泡,但出炉3天以后再做以上试验,则80%以上要起泡。
为避免以上问题的出现,在铸铁搪瓷生产中要尽量避免气体的产生和吸入。
最大厚度6mm铸铁样板单面搪瓷上的鳞爆样板背面
2-4-2-4铸造应力及减小变形的措施
内力:
金属内原子间距离发生变化而产生的吸力和斥力统称为“内力”。
应力:
单位面积上的内力称为“应力”。
铸造应力:
铸件在凝固及冷却过程中,收缩受到阻碍时,在铸件内部产
生的应力称为“铸造应力”。
铸造应力按内力不同可分为两种:
拉应力:
内力为吸力时称为“拉应力”;
压应力:
内力为斥力时称为“压应力”。
铸件各部位冷凝时冷却速度不一致,冷却较慢的部分形成拉应力,冷却较快的部分形成压应力
铸造应力按产生原因分为“热应力”、“相变应力”和“机械阻碍应力”造成应力的原因消除后,铸件中仍存在的应力称为“残余应力”。
由热应力引起的弯曲变形,凹面总是在铸件冷却较慢的一边。
这一点可以作为生产中产品发生变形时判断变形原因是加热时铸件摆放不当还是铸件本身造型有问题的根据。
铸造应力过大,超过铸件强度时,就会使铸件损坏。
热应力形成过程T形梁
铸造过程减少铸件产生应力的措施:
a.尽量选择收缩系数小的材料;
b.米用同时凝固原则;
c.缓慢冷却,以减小铸件各部位的温差;
d.采用退让性好的型砂;
e.事先做出反变形量(模具设计时,在铸件可能产生变形的相反方向做出变形量,这种事先做出的变形量叫做“反变形量”)。
消除铸件内应力的方法:
a.自然时效:
将铸件平稳放置,长时间储存。
b.人工时效:
铸件退火。
c.震动时效:
通过震动可以消除应力。
2-5铸件的主要缺陷及在搪瓷生产中的克服方法
2-5-1气孔
典型的气孔分为“析出性气孔”和“侵入性气孔”。
后者是由于铁水与砂型发生化学反应产生的气体未能逸出,造成常集中在铸件浇注部位上部的体积较大的气孔。
这两种气孔对搪瓷的损害几乎无法克服。
由此可以总结出如下规律:
对于搪瓷质量来说,铸件浇铸时形成的上表面比下表面容易出针孔或气泡;
最容易出针孔或气泡的位置是冒口。
其原因是在铁水中较轻的炉渣、杂质和气泡更容易向上漂浮。
这是生产中判断造成缺陷的罪魁祸首是搪瓷工艺还是铸件的重要依据。
按照这一规律,铸件的主要面应设计为浇铸时的模具下面,次要面设计为上面,有利于提高铸件的搪瓷合格率。
2-5-2砂眼
浇注时型砂脱落造成铸件上出现的凹坑。
小于2mm勺砂眼可用半干底釉填补,2〜5mm勺砂眼或小断裂(并非冷隔)可用二氧化碳保护焊修补,有过大砂眼的铸件应列为废品。
2-5-3鉄粒
铸件表面或铸件内气泡壁上不大的金属颗粒。
此部位在搪瓷烧成后容易产生针孔或气泡。
鉄粒与整个铸件的显微结构不一样,容易造成瓷层断裂。
前处理时必须用砂轮将鉄粒磨平,用二氧化碳保护焊将铸件外露气泡补平。
2-5-4粘砂
较牢固粘附在铸件表面的型砂。
铸件上残存的型砂使搪瓷表面产生针孔或气泡。
前处理时需仔细打磨和加大喷砂力度。
2-5-5冷隔
铸件浇铸和冷却过程中产生的裂缝。
搪瓷烧成时会裂开造成脱瓷或气泡。
这样的铸件没有办法挽救,应列为废品。
2-5-6白口
白口在厚壁或大型铸件上很少出现,多发生在小直径网条上,主要由浇铸时冷却过快所致。
白口小直径网条轻轻敲击即会断裂,断裂截面呈银白色。
这是铸件进厂验收时采用铸件自由坠落法检验是否白口的依据。
白口必然导致瓷层产生气泡,有时还会脱瓷。
前处理高温退火有可能挽救轻微白口的铸件,较大面积白口的铸件应列为废品。
2-5-7壁厚不均
砂箱错位造成铸件壁厚不均已属变形,应列为废品;
产品设计时应尽量缩小壁厚差别。
壁厚差别大则铸造应力大,易造成脱瓷。
2-5-8表面沾污
铸件可能被石墨、铁锈、机油污染。
搪瓷前处理时严格按照工艺规定退
火、喷砂可解决。
2-5-9渣眼
也称“夹渣”,熔渣被包裹在铸铁中。
易导致瓷层出针孔或开裂。
有夹渣的铸件应列为废品。
2-5-10挠曲
挠曲即铸件变形。
平板形或其他造型简单的铸件可结合退火时整形,大多数造型不可整形。
不可整形的挠铸件列为废品。
3铸铁搪瓷瓷釉
铸铁搪瓷瓷釉的配方设计首先要遵守搪瓷瓷釉的基本设计规则,例如:
底釉
熔体对坯体金属应有良好的浸润性、对氧化铁有良好的溶解作用、有较宽的烧成幅度、有足够的密着等等。
面釉应有一定的耐酸耐碱性能、良好的光泽和遮盖力、适当的软化温度和表面张力等等。
在满足这些基本规律以后就要进一步满足铸铁的特殊要求了。
3-1铸铁瓷釉配方设计时应该考虑的铸铁性质
a.铸铁表面比较粗糙
粗糙的铸铁表面可以与瓷釉形成较好的机械密着,故铸铁底釉配方中可以不
引人或少引人密着剂。
b.铸铁内的气体
铸铁组织内溶解有气体,铸件里存在一定数量的“析出性气孔”和“侵入性气孔”,其中容纳了气体。
这些气体都是造成搪瓷瓷层气泡和针孔的隐患。
c.铸铁的主要化学成分遇热容易产生气体
游离状态的碳遇热会产生二氧化碳,化合状态的FmC遇热会分解出碳,并进一步氧化成一氧化碳和二氧化碳。
这也是造成搪瓷瓷层气泡和针孔的隐患。
d.热膨胀
铸铁的热膨胀取决于它的化学成分。
铸铁的主要化学成分对铸铁的热膨胀影响各异,有资料介绍0〜500C铸铁各主要化学成分对热膨胀的贡献因数:
表1.铸铁化学成分对热膨胀的贡献因数
成分
因数
磷
6
铁
4.26
锰
4
硫
石墨
3
硅
-4
化合状态的碳
-15
铸铁的非铁化学成分比钢板多很多且所处状态变化较大,它们对铸铁的膨胀系数影响各异,使得膨胀系数有一定幅度的波动。
灰口铸铁高温热处理后的膨胀系数,在0〜500°
C范围内平均为400X
10-7/C左右。
而0〜500C范围内钢板的膨胀系数是421X10-7/C,那么铸铁
瓷釉的膨胀系数应该比钢板瓷釉略小,但是铸铁瓷釉对金属基体的热膨胀波动要有更强的适应能力。
e、.铸件的应力
体积相同时,铸铁坯件的残存应力比钢板坯件的大得多。
这就要求铸铁
瓷釉要有更好的弹性。
瓷釉化学成分中K2ONa2OAI2Q能够增强瓷层弹性,
从下表的对比可以看出现有铸铁瓷釉的弹性要高于钢板瓷釉。
表2.瓷釉成分中K2ONazOAI2Q含量范围
瓷种类釉
K?
O+Na2O(%)丿
AI203(%
钢板钛面釉
10〜15
0〜3
铸铁湿法钛面釉
12〜19
3〜5
铸铁撒粉法面釉
15〜21
6〜7.5
磨加的粘土以及存在于瓷层中的细小气孔,可使瓷层的弹性得到很大程度的
关于BQ对瓷釉弹性的影响,有不同的说法。
有人认为“B2Q的含量在15%以下时,随含量的增加,弹性增加;
而含量在15%以上时,则随含量的增加
而弹性变差”。
还有人认为“BQ的含量在15%^右时才开始对瓷釉的弹性产生有利的影响”。
3-2铸铁瓷釉
铸铁搪瓷最常见的缺陷是气泡和针孔。
要想克服这些缺陷,一是在搪瓷烧成时尽量少产生气体,要求铸铁瓷釉的熔点要低,可以低温烧成,减少气体产生;
二是铸铁瓷釉烧成时能够让气体容易扩散,要求铸铁瓷釉的高温粘度要适当小一些,让已经产生的气体易于排出;
三是底釉层形成细小气孔,既增加瓷层弹性,又容纳铸铁基体产生而来不及从瓷层逸出的气体。
以上三点就是瓷釉配方设计普遍规则指导下铸铁搪瓷瓷釉配方设计的特定规则。
3-2-1铸铁底釉
铸铁搪瓷有两种涂搪方法:
撒粉法和湿搪法。
这两种工艺截然不同,由此而出现了搪瓷瓷釉中配方结构和熔制工艺差别最大的两种底釉。
3-2-1-1撒粉法底釉
撒粉法操作的关键点是面釉干粉撒在灼热铸铁坯件上即时熔化并粘附。
从所需的烧成温度与瓷釉成本综合考虑,面釉干粉的熔化温度一般不会低于840C,面釉烧成温度则为850〜870C,再反推底釉的烧成温度应该是860
890°
C。
表3.撒粉法铸铁底釉配方示例:
原料名称
A(重量份)
B(重量份)
石英
38.0
长石
57.0
6.0
硼砂
65.0
50.0
硼酸
12.0
-
纯碱
8.0
硝酸钠
萤石
5.0
氧化钻
0.3
1.0
合计
196.3
100
磨加物:
熔块
76.0
40.0
20〜30
粘土
6〜10
0〜1.5
膨润土
0〜2
亚硝酸钠
0〜1
水
65〜75
3-2-1-2湿搪法铸铁底釉
湿搪法铸铁底釉有两种。
一种是25〜35份的钻镍底釉与75〜65份的石
英、长石、硼砂、粘土等加水50份磨制成釉浆;
另一种是以石英、长石、硼
砂为主料均匀混合后熔制到半熔融状态时出炉,磨制成细粉待用。
后者通常称为“白底釉”,在目前被普遍采用。
白底釉瓷层厚度应控制在80〜110卩m之间,烧成温度一般为760〜780C。
表4.白底釉配方示例
A(重量份)
46.0
56.0
10.0
36.0
18.0
3.0
0.5
红丹
氧化镁
3-2-2铸铁面釉
撒粉法和湿搪法两种铸铁面釉较大的区别是,撒粉法铸铁面釉的烧成温
度一般为850〜870C,而湿搪法只有720~760C。
3-2-2-1撒粉法铸铁面釉
撒粉法所搪的底釉是很薄的一层(60~100卩m>
面釉层却很厚(可达1000卩m,因此面釉的膨胀系数很受重视,一般应为260〜320X10-7/C,这样可避免瓷层受张力而开裂或脱瓷。
撒粉法铸铁面釉软化点应保持一定高度,若面釉过软,很厚的未凝固瓷层容易在烧成时塌落。
撒粉法生产的产品一般为卫生洁具,对重金属含量没有严格要求,比较注重耐水、耐碱和耐酸性能。
表5•撒粉法铸铁面釉配方示例
化学组成
钛釉
锑釉
锆釉
SiO2
K2O
Na2OF
B2O3
P2O5
TiO2
ZrO2
Al2O3
MgOBaOCaOCuO
CaF2
PbO
28.50〜34.96
0.74〜2.84
13.96〜14.39
3.50〜5.83
24.80〜26.69
1.65〜1.73
7.37〜11.36
6.05〜13.78
0.88〜0.96
36.5
11.8
15.5
4.3
2.7
4.0
18.8〜26.5
14.2〜17.0
0.3〜4.0
5.4〜7.5
1.0〜5.0
7.3〜10.0
19.7〜22.8
3.5〜4.8
7.0〜8.1
3.0〜3.6
0.4〜4.0
Sb2O3
Na2SiF6
3-
11.2
11.0
2-2-2湿搪法铸铁面釉
湿搪法铸铁面釉的膨胀系数一般为300x10-7/C左右,烧成温度为
720~760C。
在成分和理化性能指标方面与普通钢板面釉没有明显区别。
湿搪法适用于造型比较复杂和棱角线条清晰的铸铁搪瓷产品。
除了壁炉和装饰品以外,大部分此类产品都是炊事(煲汤、烧烤)用具。
产品绝大部分出口到欧美,对面釉中重金属含量、耐酸耐碱性能和耐温激变性能要求比较严格。
表6.湿搪法铸铁面釉配方示例
15〜17
24〜26
长石粉
20〜24
7〜9
33〜37
30〜34
2〜4
4〜6
钛白粉
14〜16
碳酸钠
8〜12
氟硅酸钠
5〜7
碳酸锂
碳酸镁
2
磷酸二氢钾
磨加物
氯酸钾
0-0.3
尿素
030.5
色素
3-6
50
48
3-3釉浆和釉粉的制备
3-3-1釉浆的制备
铸铁搪瓷用釉浆与钢板搪瓷用釉浆一样都是用球磨机磨制,二者主要的区别在于生产钢板搪瓷的厂家多用大容量球磨机,而生产铸铁搪瓷的厂家采用小容量球磨机要多一些。
这是因为铸铁搪瓷产品单件重量大,烧成时间长,按件计算的班产量低,消耗的釉浆少。
3-3-2釉粉的制备
国产撒粉法面釉大多是釉块,需要在搪瓷厂磨制成釉粉。
磨制干粉的球磨机内壁和球石要保持干燥。
最好专用。
为方便出粉和保持清洁,要给球磨机装一个外套。
磨制干粉的球磨机
瓷釉磨制前要彻底烘干。
潮湿的釉块磨制时会粘附在内壁或球石上,大大降低效率,且含水量大的釉粉会降低铸铁搪瓷产品合格率。
磨制干粉最好采用气流粉碎设备。
其优点是生产效率高,可减少杂质混入。
气流粉碎机主机气流粉碎流程示意图
4•湿法喷涂铸铁搪瓷工艺
4-1铸件进厂验收
a.收货品种和数量与送货单上的数字是否一致,并累计该品种的总收货量不可超过订单的总量。
b.测量进厂铸件的尺寸是否在图纸所注公差范围内。
C检查来货铸件表面质量:
平整度、变形量、砂眼数量、粘砂程度、飞刺及断裂。
d.平板形网状产品用离地面1.5m的高度将铸件平面自由坠落,检验是否
白口。
4-2前处理
4-2-1打磨
烧烤炉的烤网、烤板一类平板形铸件要先把长和宽的尺寸打磨到符合图纸规定,俗称“打大磨”
铸件表面的飞刺(广东地区称为披峰)、鉄粒、凸起等一般用角磨机打磨平整,尖锐的棱角用直磨机磨至圆滑。
小断裂或2〜5mm勺孔洞用二氧化碳保护焊修补并打磨平整。
4-2-2退火
退火的作用:
去除石墨、有机物污染,消除铸件部分应力、表面脱碳。
一般退火温度在750〜800C,退火时间为10〜30min(退火时间随铸件大小适当调整)。
有轻微白口的铸件应把退火温度提高到850C。
退火时铸件摆放要水平、稳妥,避免变形。
用于亚光一次搪的铸件可以不退火。
4-2-3喷砂(抛丸)
喷砂(抛丸)的作用:
能去除表面夹杂物和退火时生成的氧化层、使表面粗糙,增加制品的密着、部分消除内应力。
喷丸主要有金刚砂(SiC)、铸钢丸、白
口铸铁丸、钢丝切丸等。
喷丸的直径一般在0.8~1.5mm,喷丸以有棱、角的为佳。
小直径无棱角的钢丸会把铸件表面打得比较光亮,对产品烧成后的密着极为不利。
烘手器外壳、壁炉组件等单面搪瓷铸件和大型铸件适宜喷砂处理。
喷砂所用压缩空气要严格除水、除油,否则会污染铸件。
小件及双面搪瓷的铸件适宜抛丸处理。
抛丸操作时弹丸对铸件有很大的冲击力,要制定合理的抛丸工艺,防止铸件变形
抛丸比喷砂的劳动条件好得多
吊挂式抛丸机
除吊挂式抛丸机外,有条件的工厂还应配备圆盘式平抛机。
平板式铸件适用这种抛丸机。
该机工作时是弹丸自上而下打在平放的铸件上,清污的同时还有使少量变形的铸件恢复平整的整形作用。
4-3湿法喷涂铸铁搪瓷的搪烧流程及操作要点
4-3-1搪烧流程
[铸件检验]铸件修补]底釉喷涂]t[底釉烘干]t[检验修补]F底釉烧成]t
[面釉烧成]-[粉坯清整]-[面釉烘干]-[面釉喷涂]-[底釉洇湿]-[检验修补]-Jf
Jf
[成品检验]t[配套包装]
4-3-2操作要点
4-3-2-1铸件检验
有断裂、变形、较大孔洞、抛丸不到位、尺寸超过公差、打磨不到位等缺陷的铸件要拣出,不得进入搪烧工序。
4-3-2-2铸件修补
铸件上直径小于2mm的孔洞可用半干底釉填平,直径超过2mm的孔洞用二氧化碳保护焊补实并打磨平整;
局部较多的细小针孔可用半干底釉抹至平整;
前
处理遗漏的少量毛刺、凸起点要用角磨机或钢锉清除;
还显尖锐的棱角用钢锉锉圆滑。
4-3-2-3底釉喷涂
白底釉喷涂要均匀,涂层厚度70~110卩m,涂层过厚容易造成制品脱瓷。
喷涂时使用压力罐供釉浆不但能提高喷涂效率,还能使喷涂更连贯、涂层更均匀。
压力罐价格大约每个上万元,使用小型隔膜泵更经济实惠,喷涂效果也很好
4-3-2-4底釉烘干
底釉彻底烘干对烧成质量至关重要。
烘干温度200~260C,烘干时间
25~40min。
若底釉烘干不彻底,烧成后容易发生底釉层开裂和脱瓷。
一次搪产品亚光和亮光釉喷涂后的烘干都不那么严格,一般干燥即可。
烘干温度和时间都可以减少一些。
4-3-2-5检验修补
底釉烘干后要逐个检验喷涂质量,需做好以下工作:
a.上沿不涂瓷釉的器皿,用蘸水的海绵擦去沿上的干粉。
b.局部漏喷的要补喷,并重新彻底烘干。
c.粉层碰坏的要修补,小面积粉层破坏处可用毛笔蘸底釉浆轻轻刷上。
小面积修补后需再次烘干。
d.釉浆滴落或飞溅造成的釉粉凸起以及棱、角处釉浆流淌堆积的粉梗要用手指抹平。
e.亚光黑粉层上若有较大缺陷,不可修补,需整体洗净重喷。
若修补,烧成后修补处会有明显水印。
4-3-2-6底釉烧成
底釉的烧成温度为760~780C,烧成时间为12~1