电镀工艺培训教材Word文件下载.docx
《电镀工艺培训教材Word文件下载.docx》由会员分享,可在线阅读,更多相关《电镀工艺培训教材Word文件下载.docx(24页珍藏版)》请在冰点文库上搜索。
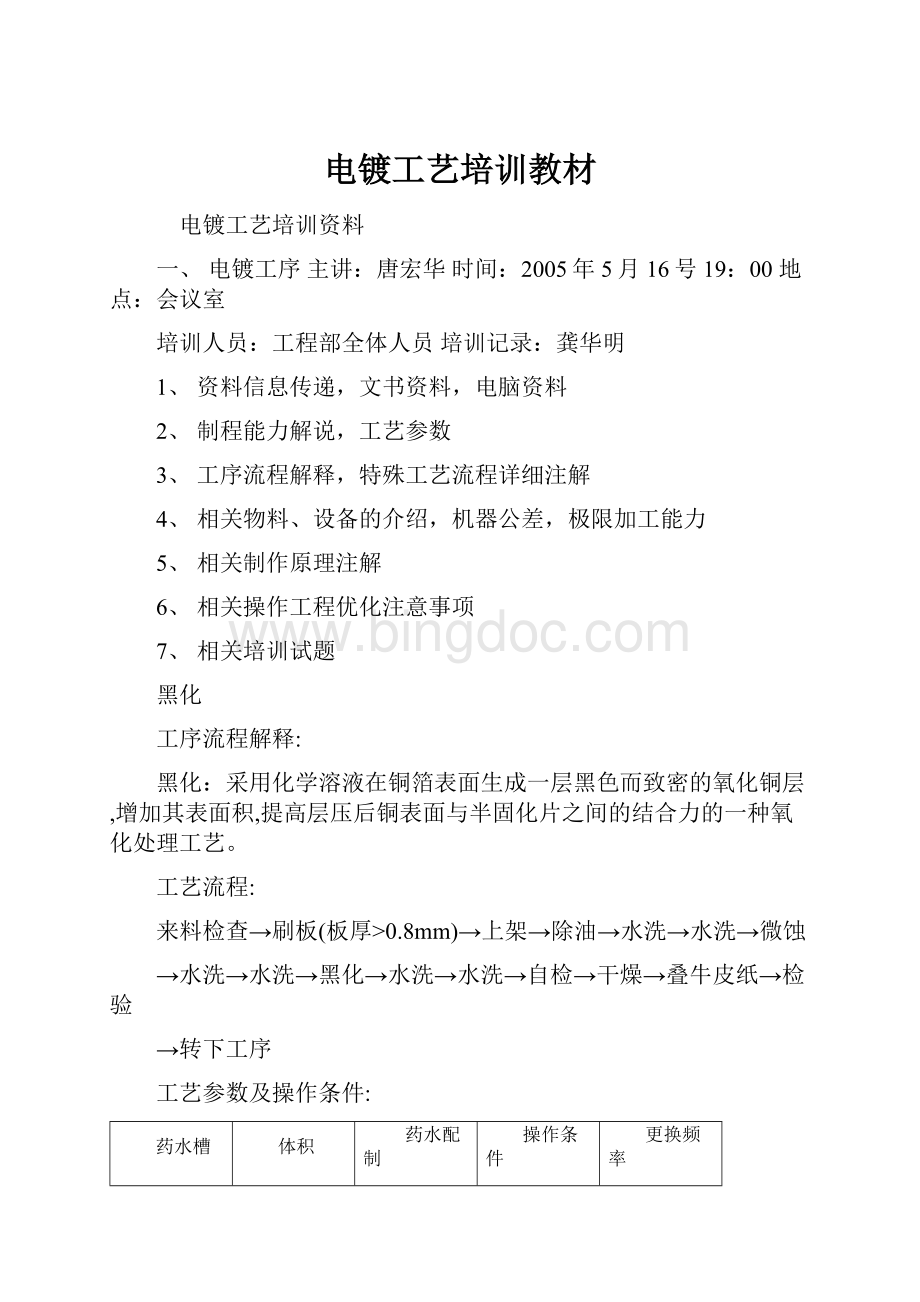
分析添加,生产量达500m2时更换。
工艺点原理说明:
来料检查:
来件表面应无任何抗蚀层覆盖及油污,如有则重新褪膜或用细砂纸打磨干净。
刷板:
将目检合格板逐件放入刷板机进行磨刷处理。
其操作详见《电镀磨板机操作规》,刷磨后表面应光亮均匀,无脏物等。
<
注:
板厚小于0.8mm或线宽小于10mil之板,省略磨板作业>
上架:
将待黑化板逐件装入黑化篮中并固定好。
操作中轻拿轻放,注意别擦花线路。
除油:
清除板面指纹.油污及轻微氧化。
除油后检查板面,如不能形成均一的水膜,表明尚残留油污,须重新除油处理。
微蚀:
去除铜面氧化,污物及有机杂质,利于黑化。
微蚀时严格控制微蚀时间,处理过长会导致线条变细,严重时露基材。
微蚀后板面呈均一的粉红色。
黑化:
通过化学反应在层铜面上生成黑色而致密的氧化铜层,增加其表面积,提高层压的结合力。
黑化时严格控制操作时间,黑化过长会导致生成的黑化层太厚,反而影响层压的结合力并在后工序中易遭到酸液浸蚀形成粉红圈。
高频前处理:
通过化学反应在孔壁吸附一层活性剂,以调整孔壁极性,提高孔金属化良率的一种孔化前处理工艺。
工艺流程:
高频多层印制板孔化前处理工艺流程
上架→溶胀→水洗→水洗→除胶渣→预中和<
H2SO4+H2O2>
→水洗→中和→水洗→水洗→清洗烘干→接高频双面印制板孔化前处理工艺流程
高频双面印制板孔化前处理工艺流程
烤板→高频活性剂处理→滴流→敲孔→热水洗→溢流水洗→手工刷洗或丝印磨板机轻刷→清洗烘干→接双面板沉铜工艺流程
工艺点原理说明:
配方
备注
高频活性处理剂
20L
原液使用
手工摇摆及震动
时间:
8-10分钟
液位不够时补加原液
生产量达到10M2∕L时换缸
除胶渣线工艺参数及操作条件详见《沉铜工序作业指导书》
①除胶渣:
详见《沉铜工序作业指导书》。
②烤板:
120℃烘烤15–20分钟,干燥孔壁水分,避免污染高频活性处理剂。
③高频活性剂处理:
通过化学反应在孔壁吸附一层活性剂,以调整孔壁极性,提高孔金属化的一次良率。
④滴流:
垂直滴流1–2分钟,让药水充分回流,减少带出量。
⑤敲孔:
双手持板边在槽沿敲打5–10下,让孔药水流出,避免堵孔。
⑥热水洗:
用50℃的热水清洗,以加强板面清洗效果。
⑦手工刷洗:
用软毛刷在板面来回刷洗10–20下,清除板面吸附的污质杂物,防止沉铜后出现板面粗糙;
对0.8mm以上材质较硬的板或手工刷洗不干净的板也可采用丝印磨板机轻刷处理,以彻底清洁板面。
⑧清洗烘干:
清洁板面,干燥孔壁水份,提高活性剂在孔壁的附着力。
物料特性说明:
①高频活性处理剂:
遇水会生成沉淀,使药水失效,因此严禁将水带入槽;
另高频活性处理剂具有极强的腐蚀性,操作中戴胶手套作业。
除胶渣+沉铜:
:
除胶渣:
采用强氧化剂药水咬蚀树脂,粗化孔壁,暴露层铜环横截面,确保层间有效连接的一种前处理工艺。
沉铜:
采用化学方法在经过催化的孔壁树脂上沉积一层导电铜层,实现层与层之间的电气互连。
它本身是一种自身的催化氧化还原反应,在化学反应过程中,还原剂放出电子本身被氧化,铜离子得到电子还原为金属铜。
沉铜工艺流程示意图
磨板→上料→溶胀→溢流水洗→溢流水洗→除胶渣→预中和(H2SO4+H2O2)→溢流水洗→中和→溢流水洗→溢流水洗→清洁整孔→溢流水洗→溢流水洗→微蚀→水洗→酸洗→水洗→预浸→活化→水洗→水洗→还原I→还原II→化学铜→溢流水洗→溢流水洗→接沉铜加厚工艺流程。
沉铜加厚工艺流程示意图
上架→浸酸→沉铜加厚→下板→清洗烘干→转检孔
槽名
配方(控制围)
操作条件
溶胀
PTL20130-40%(V/V)
65-750C6-8分钟
振动过滤
5000M2/次或
2月/一次
NaOH4-6g/L
除胶渣
KMnO450-70g/L
75-850C12-18分钟振动
半月/次或
K2MnO4≥25g时更换
NaOH35-45g/L
预中和
H2SO42-3%(V/V)
室温10-20秒
2天/次
H2O22-3%(V/V)
中和
PTL20315-25g/L
40-500C4-6min
振动
半月/一次
H2SO44-6%(V/v)
清洁整孔
整孔剂9%(V/v)
65-750C5-8min
2月/一次或
5000m²
/一次
NaOH16-24g/L
微蚀
(NH4)2S2O880-100g/L
室温1-2min
40-50m²
/次
H2SO41-1.5%(V/v)
酸洗
H2SO490-180g/L
每周/一次
预浸
PC-649.5-10.5ml/L
室温0.5-1min
3-7天/一次
H2SO41.5-1.6mL/L
活化
PC-6530-40mL/L
PH值10.8-11.5
35-450C5—8min
振动.过滤
Cu²
+≥300ppm
NaOH4g/L
H3BO35g/L
还原I
PC-665-8mL/L
室温5-8min
或槽液浑浊时更换
还原II
PC-661-2mL/L
室温0.5-1min
每天/一次
H3BO30.5g/L
化学铜
CuSO48-12g/L
温度:
45-550C
时间:
15-30min
过滤、振动
空气搅拌
两月/一次
NaOH6-8g/L
EDTA2Na30-40g/L
HCHO2.5–4.0g/L
添加剂A14-16mg/L
添加剂B14-16mg/L
磨板:
通过机械刷磨方式平整孔口毛刺,并清洗表面氧化及污渍,如有刮伤、残胶应先用细砂纸打磨后磨板。
放板、接板、上料须戴手套操作,磨板机操作见《电镀磨板机操作规》。
刷轮刷幅通过磨痕试验调至1.2-1.8cm。
溶胀:
膨松软化基材,便于高锰酸钾咬蚀树脂胶,除去钻孔所产生的碎屑污物。
溶胀时注意控制浓度、温度,否则溶液会出现浑浊分层现象,导致孔壁树脂溶胀不均。
采用高锰酸钾氧化树脂,粗化孔壁,暴露层铜环横截面,利于层间的有效连接。
除胶渣作业须严格控制处理时间,时间过短,胶渣除不干净,会影响层间的电气互连。
除胶过度,会产生严重的灯芯效应,导致孔间绝缘不良,对于高TG多层板及孔径≤0.4MM,板厚≥3.0MM之多层板,时间适当延长5-10分钟,以确保除胶质量。
预中和(H2O2+H2SO4):
中和强碱性物质,提高中和剂的工作效率。
预中和槽液是一种微蚀液,会腐蚀铜面,时间过长会导致层铜环凹陷,孔口露基材等不良现象,因此处理时间一般≤15秒钟。
中和:
使MnO2等高价锰化物转化为水溶性的低价锰化物,以利于活化剂的吸附。
清洁整孔:
清洁孔壁并调整孔壁极性。
槽液含有表面活性剂,须用较大水量冲洗,否则残留板面会影响微蚀的均匀性。
微蚀:
清洁粗化铜面,清除残余有机物,提高沉铜层与基材铜的结合力。
微蚀时严格控制微蚀时间,微蚀过度会导致层铜环凹陷,孔口露基材等不良现象。
微蚀不足会导致镀层间接合力差,出现分层起泡现象。
酸洗:
清洁铜面上从微蚀槽带出的复合氨盐。
酸洗浸泡时间不可过长,否则会侵蚀层黑化层导致层粉红圈。
预浸:
去除铜面轻微氧化,降低孔壁表面力,促进活化剂吸附。
活化:
使钯离子吸附于孔壁。
活化液为碱性离子钯,须定期检测槽液PH值,PH值过高或过低均将严重影响活化液的活性,一般控制在10.8-11.5之间为宜。
还原I、II:
将钯离子还原为钯原子作沉铜催化剂。
还原液易分解,须定期补加,连续生产时每2H做还原试验一次。
化学铜:
使Cu2+转化为Cu原子沉积于孔壁及板面,实现层与层之间的电气互连。
沉铜前
必须检测槽液温度和PH值,并密切注意沉铜起始反应效果。
加厚铜:
采用电沉积方法在孔及板面沉积一层导电铜层,增加孔铜厚度,以满足后工序工艺加工的要求。
对于高频板及板厚≤0.6MM之板,沉铜加厚时采用双挂具作业,以均衡电流分布。
图电:
图电铜:
采用电镀原理在客户所需要的图形线路上电沉积一层铜,增加线路及孔铜厚度,以满足客户的电气性能要求。
图电锡:
采用电镀原理在有效线路上电沉积一层锡抗蚀层,保护线路。
工艺流程
来料烘烤→冷却→上料→除油→溢流水洗→溢流水洗→微蚀→溢流水洗
→溢流水洗→酸洗→电铜→溢流水洗→溢流水洗→酸洗→电锡→溢流水洗
→溢流水洗→下料→转褪膜
工艺参数及操作条件:
体积
药水配方(控制围)
更换时间
除油2#
480L
SE-250(200-250ml/l)
25-400C
4-6min
生产2400-2500m2时更换或每月更换一次
微蚀2#
NaHSO4(30-40g/L)
28-320C
60-120sec
每月更换一次
H2O2(8-12g/l)
稳定剂3.8-4.2%(V/V)
酸洗2#
H2SO4(90-180g/L)
室温1min
每半月/一次
电铜
1500L
H2SO4(CP)(160-220g/L)
20-320C
10-60min
1.2-2.0ASD过滤,阴极摆动
分析添加
CuSO45H2O(60-100g/L)
CL-30-80ppm
PCM-PLUS2-2.5mL/L
室温
每半月一次
电锡
SnSO4(35-45g/L)
10-15min
1.0-1.6ASD过滤阴极摆动
阴极振动
H2SO4(170-210g/L)
EC-A15-35mL/L
EC-B35-45mL/L
工艺点原理说明
烘烤:
湿膜板用1200C烘15分钟固化油墨,防止电镀时油墨脱落,引起渗镀等不良现象发生。
烘烤时插架作业,烘烤后须冷却至室温才能电镀。
上料:
戴手套作业,持拿板边,小心别刮花板面,须拧紧螺丝以防掉板。
板子两面线路密度相差太大时应交叉上板,以均衡电流分布。
除油:
清除板面油渍污物及轻微氧化。
除油后检查板面状况,如不能形成均一的水膜,说明板面尚残留油污,须重新除油处理。
微蚀:
清除板面氧化、有机杂质,微观粗化铜表面,提高电镀铜与底铜的接合力。
酸洗:
清除板面轻微氧化,使铜原子具有活性,便于电镀时铜的沉积。
电铜:
加厚线路铜层,使其符合客户电气性能要求。
电铜时必须打开空气搅拌。
电铜前仔细查看流程卡,根据有效电镀面积操作电流,根据铜厚要求操作时间。
当图电有效面积≤30%时,电流密度控制在1.2-1.5ASD;
当孔铜要求20-25UM时,图电时间60分钟;
当孔铜要求1OZ或层数≥8层时,图电时间120分钟,但电流密度要适当调小,一般控制在1.2ASD即可。
电锡:
抗蚀刻保护层,保护线路。
对于厚铜箔板﹙铜厚≥2OZ﹚,镀锡时间在原有基础上延长5-10分钟,以提高其抗蚀性能。
镀锡后下板时须将手套清洗干净,如残留酸液,会导致发黑流锡。
电镀镍金:
电镀镍:
采用电沉积方法在有效线路上电镀一层镍阻挡层,防止铜与金之间相互渗析。
电镀金:
采用电沉积方法在镍面上电镀一层金,防止镍面钝化,确保其可焊性。
工艺流程:
全面镀镍金工艺流程:
上架→酸性除油→水洗→水洗→微蚀→水洗→水洗→浸酸→图电铜→水洗→水洗→酸洗→水洗→水洗→图电镍→水洗→水洗→图电金→水洗→水洗→清洗烘干→自检→转退膜工序000.0
镀金手指工艺流程:
裁边→贴兰胶带→压兰胶→上架→除油→水洗→水洗→微蚀→水洗→水洗→酸洗→水洗→电镍→水洗→水洗→稀盐酸活化→水洗→镀金手指→水洗→撕兰胶带→柠檬酸洗→纯水洗→热纯水洗→清洗烘干→自检→贴红胶带〈化金板印可剥兰胶〉→转下工序
药水槽
槽液成份
酸性除油
200-250ml/L
室温
产量600m²
或
30-40g/L
8-12g/L
3.8-4.2%
60-120Sec
连续生产每周
更换一次
酸洗
H2SO4:
140-180g/L
1-3分钟
电铜
1800L
CuSO4.5H2O:
60-90g/L
160-220g/L
CL:
30-80ppm
铜光剂:
2-2.5ml/L
20-32℃
镀铜时间:
30-60分钟
1.2-2.0A/dm²
连续过滤
阴极摆动
电镍
350L
NiSO4:
240-360g/L
NiCL240-60g/L
H3BO3:
30-50g/L
ST-901A:
13-17ml/L
ST-901W:
1-2ml/L
55±
5℃
PH值:
3.8-4.5
镀镍时间:
20-30分钟2.0-3.0A/dm²
连续过滤
全板电金
金含量:
0.5-2.0g/L
开缸剂:
200g/L
添加剂:
1.3ml/L
室温-35℃
4.0-5.0
比重:
8-12Be
0.2-0.3A/dm²
镀金时间:
20-180秒
金手指
15L
金盐:
3.0-5.0g/L
温度30-40℃
3.5-4.2
比重:
8-12Be
1.0-2.0A/dm2
60-300秒
上架:
戴干净手套作业,双手拿板边,手指不得进入图形有效区域,板子两边线路密度相差太大时应交叉上板,以均衡电流分布.锁板时螺丝需拧紧,防止掉板。
除油:
清除板面轻微氧化,使铜原子具有活性,便于电镀时铜的沉积。
当孔铜要求20-25UM时,图电时间60分钟。
电镍:
在图形线路上镀一层镍,阻挡铜与金的相互渗析。
对于厚铜箔板﹙铜厚≥2OZ﹚,镀镍时间在原有基础上延长5-10分钟,以提高其抗蚀性能。
全板电金:
电镀表面焊接层,防止镍面钝化,满足线路板的可焊性,耐腐蚀性及低接触电阻等性能。
镀金时必须带电上槽。
电金手指:
系在插头上电镀硬质合金成份,增强其耐磨性。
电金手指后须用柠檬酸及热纯水清洗,以防金手指氧化变色。
蚀刻
退膜:
采用NaOH碱溶液退除非线路区域的抗蚀或抗电镀油墨,暴露铜面,便于后工序蚀刻药水的腐蚀。
蚀刻:
采用碱性CuCL2溶液腐蚀裸露铜面,而被锡抗蚀层保护的线路保留下来,最终形成客户所需要的线路图形。
退锡:
退除线路图形上的锡抗蚀层,裸露铜层线路,以满足后工序工艺加工的要求。
层线路〈负片〉蚀刻流程示意图
烤板→检查→蚀刻→氨水洗→压力水洗→水洗→吹干→自检→插架
→退膜→清洗烘干→蚀检→转黑化工序
镀锡板蚀刻流程示意图
上架→退膜→水洗→刷洗→检查→蚀刻→氨水洗→压力水洗→水洗
→吹干→自检→退锡→清洗烘干→蚀检→转下工序
镀金板蚀刻流程示意图
→吹干→自检→柠檬酸洗→纯水洗→热纯水洗→清洗烘干→蚀检→转下工序
退膜、蚀刻、退锡工艺参数
退膜
250L
NaOH30-50g/L
层湿膜50±
50C
浸泡5-10min
干膜:
室温∽400C
1-5分钟
去膜时间超过10min,应清理退膜槽油墨残渣或更换退膜槽。
一般2-3天/一次或400M2/一次。
碱性蚀刻
Cu2+130-160g/L
CL-170-210g/L
速度:
500-5000mm/min
压力:
1.5-3.0kg/cm2
40-550C
8.2-8.8
1.18-1.23
用废板调节蚀刻速度,
注意蚀刻不净或蚀刻过度。
氨洗段
54L
氨水:
5-10L
连续生产1-2天更换1次
退锡
180L
退铅锡药水原液使用
温度:
400C以下
压力:
0.5-1.5Kg/cm2
退板面积达到2-3.0m2/L时更换药水或退锡速度
<21.5HZ时更换。
烤板:
层湿膜板蚀刻前150℃烘烤5-10分钟,以固化油膜,提高油膜的抗蚀性能。
烘烤后须冷却至室温才可蚀刻。
退膜:
退膜时严格控制退膜温度及退膜时间,温度过低或时间过短会导致退膜不净,温度过高或时间过长会导致流锡。
刷洗:
对于线宽≤8MIL之板,清洗时必须用细软毛刷擦洗板面,以清除细线路间残存的抗蚀油墨/膜渣。
蚀刻前应仔细查看流程卡,然后根据铜箔厚度调整蚀刻速度﹙详见蚀刻速度参考表﹚,对于线宽≤8MIL之板或对蚀刻效果不清楚时,应以较快的速度放板,以防过腐蚀。
氨水洗:
清除板面上带出的蚀刻药水。
退锡前须100%自检,重点检查板边高电流区及细密线路间有无蚀刻干净,OK方可退锡。
柠檬酸洗:
针对金板,蚀刻后用柠檬酸洗清洁金面,防止金面氧化变色。
化镍金
化学镍:
采用化学反应原理在经过催化的裸铜表面沉积镍镀层的一种工艺。
在反应过程中,还原剂放出电子本身被氧化,镍离子得到电子还原为金属镍,在沉积过程中有磷的夹杂,其镀层实质是镍磷合金。
化学金:
采用置换反应原理在镍镀层表面置换一层薄金镀层,防止镍面钝化,确保其可焊性。
上架→酸性除油→水洗→水洗→微蚀→水洗→水洗→酸洗→水洗→水洗→预浸→活化→水洗→水洗→后浸→水洗→水洗→化镍→水洗→水洗→镍活化→水洗→水洗→化金→水洗→水洗→热水洗→下架→清洗烘干→转检验
化学镍金线工艺参数
参数
项目
围
ICPclean-9180-120ml/L
35±
1-3min
过硫酸铵80-100g/L
H2SO415-25ml/L
25-30℃
0.5-2min
药水循环
手工摆动
酸浸
H2SO490-180g/L
室温时间:
1-2min
预浸
35%HCl80-90ml/L
1-3min
活化
ICPACCELA200ml/L
铜含量超过0.5g/L
或补充量达到
3-4MTO时更换
后浸
98%H2SO435-45g/L
化学镍
UPC-M80-120ml/L
UPC-0140-60ml/L
80-85℃
20-30min
PH:
4.4-5
补充量达到
4-5MTO时更换
镍活化
35%HCl30-40ml/L
化学金
GOLDAE70-80ml/L
金盐1.0-2.0g/L
3-10min
4-6
镍含量超过
0.3g/L时更换
热纯水洗
40-50℃
1-2min
每天一次
工艺点原理及特性说明:
酸性除油:
采用强氧化剂药水腐蚀铜面,清除板面有机杂物,微观粗化铜表面,确保化镍层与底铜层之间的接合力。
微蚀时严格控制微蚀时间,处理过长会导致孔铜变薄,严重时孔壁露基材。
清除铜面上从微蚀槽带过来的复合氨盐。
预浸:
清除铜面轻微氧化,防止杂质带入活化槽,减少槽液污染。
活化:
采用化学反应原理在铜面置换一层催化钯层,以便于化镍在铜面上的沉积。
活化时严格控制时间:
活化过短生成的金属钯减少会造成漏镀;
活化过长因钯的附着量过多会造成渗镀;