常见钻井事故处理.docx
《常见钻井事故处理.docx》由会员分享,可在线阅读,更多相关《常见钻井事故处理.docx(63页珍藏版)》请在冰点文库上搜索。
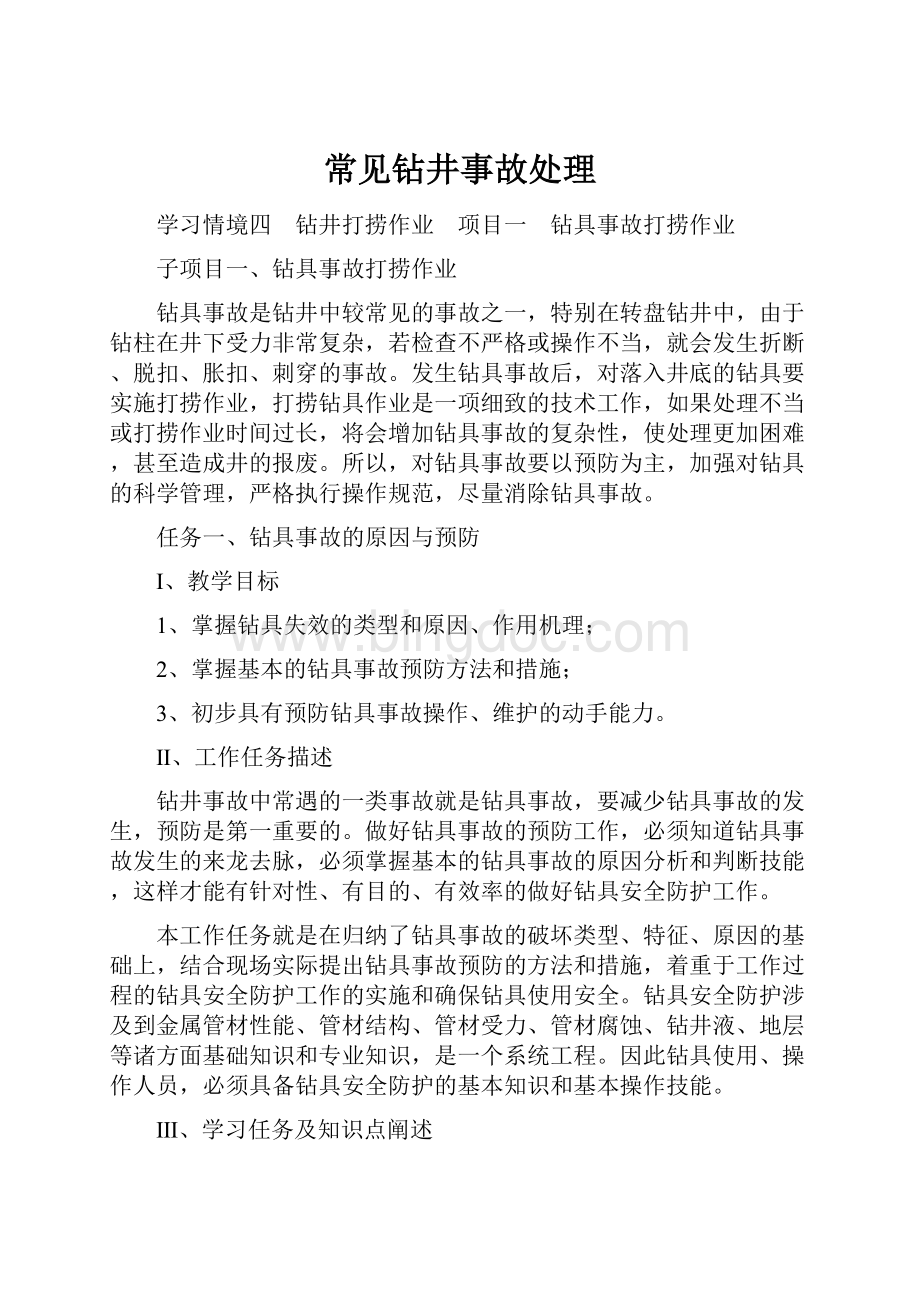
常见钻井事故处理
学习情境四 钻井打捞作业 项目一 钻具事故打捞作业
子项目一、钻具事故打捞作业
钻具事故是钻井中较常见的事故之一,特别在转盘钻井中,由于钻柱在井下受力非常复杂,若检查不严格或操作不当,就会发生折断、脱扣、胀扣、刺穿的事故。
发生钻具事故后,对落入井底的钻具要实施打捞作业,打捞钻具作业是一项细致的技术工作,如果处理不当或打捞作业时间过长,将会增加钻具事故的复杂性,使处理更加困难,甚至造成井的报废。
所以,对钻具事故要以预防为主,加强对钻具的科学管理,严格执行操作规范,尽量消除钻具事故。
任务一、钻具事故的原因与预防
Ⅰ、教学目标
1、掌握钻具失效的类型和原因、作用机理;
2、掌握基本的钻具事故预防方法和措施;
3、初步具有预防钻具事故操作、维护的动手能力。
Ⅱ、工作任务描述
钻井事故中常遇的一类事故就是钻具事故,要减少钻具事故的发生,预防是第一重要的。
做好钻具事故的预防工作,必须知道钻具事故发生的来龙去脉,必须掌握基本的钻具事故的原因分析和判断技能,这样才能有针对性、有目的、有效率的做好钻具安全防护工作。
本工作任务就是在归纳了钻具事故的破坏类型、特征、原因的基础上,结合现场实际提出钻具事故预防的方法和措施,着重于工作过程的钻具安全防护工作的实施和确保钻具使用安全。
钻具安全防护涉及到金属管材性能、管材结构、管材受力、管材腐蚀、钻井液、地层等诸方面基础知识和专业知识,是一个系统工程。
因此钻具使用、操作人员,必须具备钻具安全防护的基本知识和基本操作技能。
Ⅲ、学习任务及知识点阐述
学习和理解钻具事故的产生原因、破坏的机理、破坏特征等理论知识,是更好的掌握和实施钻具安全防护工作的基础。
通过对钻具事故发生过程的原因探讨,才能真正掌握钻具事故预防的方法和措施;才能做好钻具安全防护的工作。
学材
钻具失效在世界各油田普遍存在,原因各不相同,失效机理也很复杂,但都与钻具结构,材料特性,地层情况,钻井工艺和使用水平有关。
我们知道石油钻具的受力状况和井下环境非常恶劣,长期处在内外充满钻井液的狭长井眼里工作,承受拉、压、弯、扭、液力等载荷作用,同时还伴随着各种复杂振动,使其成为钻井设备工具中的一个薄弱环节,在钻井过程中钻具任何部位失效都可能造成严重的后果,甚至使井报废。
美国的统计和估算表明,钻具的断裂事故在14%的井上发生,平均发生一次损失106000美元,这是正常消耗以外的巨额费用。
据统计,我国各油田每年发生钻具事故约五、六百起,我国每年必须用数亿元人民币的外汇购置各种规格的钻杆和钻铤,经济损失巨大。
因此只有开展钻具失效研究,掌握钻具失效的客观规律,针对实际情况,提出相应的预防措施,才能防止钻具事故或最大程度地降低钻具破坏,提高油田的经济效益。
一、钻具的破坏类型
由于钻具工作条件的恶劣,所以其失效形式也多种多样。
归纳起来,其主要失效形式可分为:
1、断裂
断裂在钻具失效事故中所占的比例较大,占全部失效的50%左右,导致断裂失效的主要原因是疲劳破坏,也有一定数量的氢脆破坏。
钻具折断分为丝扣折断和本体折断。
2、刺穿、脱扣和胀扣失效
刺穿、胀扣和脱扣失效是仅次于断裂失效的主要失效形式。
脱扣、胀扣失效在钻杆和钻铤上都有发生,主要原因是使用不当造成的。
刺穿失效主要发生在钻杆上,钻铤和加重钻杆、扶正器上也有发生,但是较少。
脱扣分为拉脱和倒扣。
3、表面损伤
表面损伤包括腐蚀、磨损和机械损伤三方面。
4、过量变形
过量变形是由于工作应力超过材料的屈服极限引起的。
如钻杆接头在受载情况下螺纹部分的拉长,钻杆本体的弯曲和扭转,这都是由使用不当造成的。
二、钻具失效的原因
钻具失效中以断裂失效比例最高,刺穿、脱扣和胀扣次之,在表面损伤中,以腐蚀和磨损为失效的主要原因。
在这些主要失效原因中,有的是独立的,有的又是互相影响的。
下面对断裂失效、刺穿、腐蚀等失效原因进行分析。
1、断裂失效
四川川东地区1996年~1997年期间发生了303起钻具井下事故,其中钻杆、钻铤断裂就达142次,占总数的46.9%;塔里木油田在1995年~1998年期间钻杆、钻铤失效66次,其中断裂事故就达38次,占失效的57.6%。
导致断裂的主要因素是疲劳,也有一定数量的脆性断裂。
疲劳断裂的原因一是钻具使用时间久,达到正常使用寿命;二是井下钻具受力严重,载荷复杂,如严重跳钻、大井斜角、大狗腿角等。
脆性断裂与材料质量不合格有极大关系,另外环境和使用也会导致脆性断裂。
1)钻具疲劳
材料在交变应力作用下,经过长时间(或较多的应力循环周次)运转后所发生的“突然”失效或破坏,统称材料的疲劳现象。
疲劳是钻具失效的最主要形式。
有资料报道,钻具的失效大约有80%是由于疲劳引起的。
据波斯弯地区钻具失效的统计,在三年时间内,累计每钻进进尺1981.2m(6500ft)就有一起与疲劳有关的钻具失效。
⑴疲劳失效表现的形式
疲劳失效在钻具上的表现形式主要是钻铤螺纹处发生疲劳断裂和在钻杆加厚过渡区间产生疲劳裂纹,引起钻杆疲劳刺穿,甚至断裂失效。
在钻具的疲劳失效中,钻铤的疲劳失效更为突出。
石油管材使用研究表明有80%以上的钻具失效属于疲劳或疲劳相关的失效,其中绝大部分发生在钻铤的螺纹连接处。
1992年全国钻具失效总况的统计结果表明,钻铤的失效次数大致为钻具总失效事故的48.7%;长庆油田第三钻井工程处1994年共断钻铤87根(钻铤外径177.8mm,螺纹为NC50牙形),内螺纹断裂占86%,外螺纹断裂占14%。
内螺纹断裂位置在距台肩面100~120mm处,外螺纹断裂位置在距台肩面18~25mm处,失效部位断口截面光滑具有疲劳断裂特征;四川川东地区1996~1997年间发生了142起断裂事故中,螺纹断裂就占110起,占总数的77.5%;据统计,大庆油田钻铤损失占钻具失效总数的88.4%,而钻铤损坏基本上都在钻铤螺纹连接处;华北油田2002~2005年钻铤失效78起,占总失效的46.7%。
其中螺纹连接失效75起,占钻铤失效的96.1%。
螺纹连接处的应力集中是钻铤最薄弱环节,也是钻铤疲劳失效多发区。
钻杆疲劳失效主要表现在钻杆加厚区间由于截面突变,在加厚区间引起应力集中。
在频繁交变应力作用下,加厚区产生微小裂纹,加之钻井液等复杂因素的影响,最终导致刺穿、刺漏和裂缝,甚至发生钻杆断裂事故。
川南矿区在20世纪90年代曾对10口井使用的钻杆进行探伤检查,发现34根E75钻杆、17根X95钻杆、5根S135在内加厚过渡区部位产生裂纹。
塔里木油田在1995年~1998年三年间钻杆和加重钻杆失效35次,断裂和刺穿就高达22次,占62.8%;2003年7月至9月勘探三号钻井平台在东海海域富阳一井的钻井施工过程中,共计发生9次钻杆刺漏现象,钻杆刺漏位置基本都在距端面0.60m处。
⑵疲劳失效特征
①钻铤失效特征
ⅰ、钻铤的疲劳断裂,大多数发生在井斜变化大,方位变化大的“狗腿”井段。
当应力集中较大,结构强度和材料韧性不足时,钻铤的疲劳失效极易发生;
ⅱ、钻铤疲劳断裂均发生在接头的螺纹部位。
外螺纹的断裂面一般在台肩处螺纹的第1~2牙附近,内螺纹接头断裂面一般在距螺纹消失端第4~6牙处,即位于内、外螺纹连接的最后啮合处;
ⅲ、钻铤的疲劳断裂裂纹一般起源于螺纹根部,并具有多源特征,与各种因素引起的应力集中增大有关;
ⅳ、钻铤疲劳断裂与尺寸有很大的关系,尺寸越大越容易发生。
内外螺纹连接后的弯曲强度比对钻铤的疲劳失效有严重影响,弯曲强度大容易引起外螺纹疲劳,反之则容易引起内螺纹疲劳失效;
ⅴ、钻铤的疲劳失效与钻铤材料的性能有关,低韧性的材料更容易发生早期疲劳失效。
②钻杆疲劳失效特征
ⅰ、钻杆的疲劳断裂与钻铤的疲劳断裂一样,大多数发生在井斜变化大,方位变化大的“狗腿”井段;
ⅱ、钻杆断裂基本发生于距离内、外螺纹接头台肩450~550mm处。
纵向剖开后,此部位恰好为内加厚过渡区与管体交界处;
ⅲ、钻杆失效与钢级及使用地区无关。
失效钻杆在四川、新疆、长庆、大港、华北、胜利等油田都普遍存在,包括X95、G105和S135各级钢级。
⑶影响钻具疲劳失效的因素
①钻具振动
钻具振动是导致钻具疲劳损坏的主要因素之一。
它一般分为横向振动、纵向振动和扭转振动。
研究表明,纵向振动对钻具寿命影响最大,产生的纵向冲击力可高达840KN;横向振动导致连接的螺纹加速疲劳而扭断;扭转振动引起疲劳、脱扣等。
钻具的剧烈振动引起钻具连接螺纹发生疲劳断裂,钻铤螺纹受到的影响最为严重。
②弯曲强度比
在石油钻井过程中,下部钻具要受到弯曲载荷的作用,而钻具结构最薄弱的环节是接头处,许多井下复杂情况的出现,都是由于螺纹连接处发生断脱而造成的。
弯曲强度比是指公扣和母扣抗弯刚度保持适当的比例。
经分析了大量钻铤螺纹损坏实例后,认为弯曲强度比的最佳值应为2.5:
1,许用范围为1.9:
1~3.2:
1。
一般情况下要根据实际情况选用适合的弯曲强度比,以保证内、外螺纹接头弯曲疲劳强度相平衡。
在钻具外径容易磨损、井下有腐蚀介质的情况下(此时内螺纹接头疲劳次数多),应选择较大的弯曲强度比。
反之,在外螺纹接头疲劳频繁发生的地区,应选择较小的弯曲强度比。
③钻铤螺纹载荷分布不均
钻铤公扣与母扣联接时,公扣借着某一力矩旋入母扣,为了保证螺纹部分能够密封,必须在螺纹台肩面旋合后在给与一定的上扣拧紧扭矩,使台肩面和螺纹沿节经部位相互挤压,产生一定的弹性变形,从而造成一定的台肩负荷。
上扣完毕,螺纹就承受了一定的初始应力。
螺纹上载荷的分布并不均匀,前几牙螺纹承担了大部分载荷。
其中第一个螺纹牙载荷就高达39.5%,第二个螺纹达23.9%,而到达第7个螺纹载荷几乎不受力。
因此上扣扭矩所产生的螺纹载荷主要集中在靠近台肩面的前4个螺纹。
螺纹牙载荷分布极为不均衡,在公螺纹的根部、母螺纹的底部最后啮合区是螺纹变形、扭曲、断裂等失效的高频区。
2)钻具脆性断裂
脆性断裂是指材料断裂前不产生或仅仅产生很小的塑性变形,断裂过程中单位体积所消耗能量很低的断裂过程。
⑴脆性断裂失效原因
脆性断裂失效原因主要包括结构设计或焊接工艺不良造成很大的截面突变,出现应力集中或裂纹,环境温度的降低,材料的成份、冶炼、加工工艺不当,残余应力未消除等。
但是同一材料制成的不同构件在不同环境下服役时,其失效方式可能是脆性的,也可能是韧性的,它取决于材料的成份、冶炼、热处理等热加工的内在因素,也取决于应力状态(多轴应力、应力集中大小等)、加载速度、环境温度和介质等外在因素。
⑵脆性断裂的失效机理
钻具脆断失效主要是由材料表面的尖锐缺陷、螺纹根部尖角等应力集中源和材料韧性不足引起的。
疲劳和脆断失效,与材料的冲击韧性均有一定的关系。
脆性断裂失效非常“突然”,失效前没有什么明显的征兆,
2、刺穿失效
刺穿失效是仅次于断裂失效的主要失效形式,刺穿主要发生在钻杆上,而失效部位绝大部分都发生在钻杆加厚过渡区。
中国东海PH油田1998年至2001年发生61起钻杆刺穿事故,刺穿位置距离接头端面0.5~0.7m,基本上处于钻杆过渡带;塔里木油田2001年7月~2003年5月在通径127mm钻杆上有21口刺漏失效井共89次发生了刺漏,其中77.5%发生在钻杆本体加厚过渡带;华北油田2002~2005年间在鄂尔多斯盆地共发生钻具刺穿刺漏75起,占总失效的45%。
其中钻杆失效69次,失效部位发生钻杆内加厚过渡区的达66次,占刺穿失效的95.6%。
⑴刺穿失效的原因
①钻杆加厚过渡区间的截面突变,引起应力集中,导致钻杆疲劳,产生微裂纹;
②带有腐蚀性的高压钻井液在应力作用下,侵入微裂纹,使裂纹扩展;
③钻井液中的硫化氢、二氧化碳、溶解氧对钻杆的腐蚀损伤造成壁厚减薄,点蚀、蚀坑的产生引起腐蚀疲劳失效;
④带有固体颗粒的钻井液高速流经变截面的过渡区间,对截面产生冲击和摩擦。
⑵冲蚀的机理
冲蚀是指含有固体离子流的冲击磨损,属于腐蚀磨损的范畴。
冲蚀失效是指钻井液中的固体小颗粒等按一定速度或角度对钻杆表面进行冲击所造成的一种材料损耗现象。
冲蚀是冲击和腐蚀两大因素共同作用的结果,但是冲击起主导作用。
冲击和腐蚀联合作用,其破坏速度远远大于各自单独作用。
冲蚀失效主要发生在钻杆加厚过渡区和螺纹连接部位。
钻具冲蚀失效的主要特征是含有固体粒子的高压钻井液以高速沿一定方向冲击钻具表面,造成金属的流失。
最常见的是钻杆内加厚过渡表面区表面的冲蚀坑、冲蚀孔洞及螺纹连接部位冲蚀造成的螺纹及密封面损伤。
3、腐蚀失效
腐蚀是导致和加速钻具的断裂、刺漏等失效主要原因。
美国一家钻井公司曾作过这样的统计,在该公司所有降级或报废的钻杆中,因内壁全面腐蚀、点蚀、腐蚀疲劳等造成的就占75%以上。
石油管材使用研究表明,60%的失效是直接或间接地由腐蚀引起。
华北油田因钻具腐蚀疲劳,钻具使用寿命很短。
最长为98000m,最短的仅为7300m,平均为46000m,与国外的150000m使用寿命相距甚远,由此而造成的经济损失高达2000多万元。
钻具的腐蚀失效主要表现在钻井液对钻具的腐蚀疲劳和腐蚀损伤两方面。
1)腐蚀疲劳
在腐蚀环境中造成的破坏,通常称为腐蚀疲劳破坏。
这种破坏是目前造成钻具早期破坏最常见的原因之一。
由于腐蚀的缘故,使钻具截面积减小或者形成腐蚀小坑造成应力集中点,都使得疲劳强度大为降低,或者实际上不存在什么疲劳强度。
腐蚀疲劳规律是比较复杂的,目前对腐蚀疲劳的机理仍有不少争论,比较流行的观点是腐蚀应力集中、选择性电化学侵蚀、钝化膜的开裂、介质吸附和氢致开裂等。
①腐蚀应力集中
腐蚀造成的表面蚀坑引起应力集中,促使裂纹萌生。
实验证明腐蚀裂纹多在半圆形的蚀坑底部出现,如钻杆的腐蚀疲劳失效即是如此。
②选择性电化学侵蚀
疲劳过程中产生集中变形区,这种区域的位错组态或杂质沉淀与基体不同,在动态过程中这个形变集中区首先发生阳极溶解,随着疲劳过程的滑移形态的反复进行,溶解不断进行,从而出现腐蚀沟,引起应力集中而导致裂纹萌生。
③钝化膜开裂
许多金属都能形成钝化膜,但疲劳过程表面滑移台阶能破坏钝化膜,裸露出的金属在介质中发生阳极溶解。
当钝化膜被修复后溶解停止,下一循环的滑移开始又重复同一过程,结果形成了微观沟槽,并使滑移越集中该处,以至最终形成腐蚀疲劳裂纹。
④介质吸附和氢致开裂:
在金属材料表面分解的氢通过扩散进入金属,在三轴应力状态的裂纹尖端塑性区集聚成原子团使微裂纹形成。
微裂纹与主裂纹前缘相连接而使裂纹向前推进。
2)腐蚀损伤
⑴腐蚀损伤的主要失效形式
①腐蚀还原氢可进入材料,使材料发生脆化,即应力腐蚀;
②腐蚀所产生的蚀坑、沟槽等可引发其它类型的失效。
例如在交变载荷作用下,蚀坑可作为疲劳裂纹源,在蚀坑底部产生裂纹,最后导致腐蚀疲劳;
③化学腐蚀引起钻具几何尺寸变化,如管壁减薄、承载能力下降、螺纹连接和密封受到损坏等。
上述三方面中,前两者是腐蚀间接的或与其它因素共同作用的结果,因而导致突发性的失效,而且通常发生在钻井过程中,所以危害很大;后者是腐蚀的直接结果,虽需要一个较长时间的腐蚀累计过程,但它只能控制。
⑵应力腐蚀失效机理
腐蚀损伤是腐蚀还原产物氢原子进入金属,使材料发生脆化,在水溶液中,这种脆化称为应力腐蚀。
金属材料在拉伸应力和一定的腐蚀介质同时作用下所导致的开裂称为应力腐蚀开裂。
应力腐蚀开裂是环境引起的一种常见的失效形式,它是在一定的拉伸应力和腐蚀介质共同作用时,在低于抗拉强度而介质腐蚀性又较轻微的情况下发生开裂。
开裂之前没有显著的变形或其它明显可见的宏观征兆,因此常被忽视而疏于防范,以至酿成严重后果。
美国杜邦化学公司曾分析在4年中发生的金属管道和设备的685例破坏事故中,有近60%是由于腐蚀所引起,而在腐蚀造成的破坏中,应力开裂占13.7%。
根据各国大量的统计,在不锈钢的湿态腐蚀破坏事故中,应力腐蚀开裂甚至高达60%,居各类腐蚀破坏事故之冠。
应力腐蚀开裂是环境开裂中最广泛的失效形式之一,是一个复杂的力学——化学破坏过程。
应力腐蚀开裂只有当材料在不发生剧烈均匀腐蚀的介质中才发生。
一般促使材料发生应力腐蚀开裂的介质可以在以下几种条件下发生:
①介质中含有促使材料表面形成钝化膜,但又含有破坏钝化膜完整性的离子;
②介质能向合金材料提供足够量的氢以引起氢致开裂,并且合金材料在该介质中均匀腐蚀速度很低;
③只有在拉应力作用下才能引起应力腐蚀,压应力反而能阻止或延缓应力腐蚀。
拉应力可来源于构件加工或焊接的残余应力或外载荷。
⑶化学腐蚀的机理
钻具的腐蚀源很多,硫化氢、二氧化碳、溶解氧和溶解盐等都对钻具有不同程度的腐蚀作用,腐蚀源不同,其腐蚀机理也不尽相同。
下面是对各种腐蚀做一分析。
①硫化氢腐蚀机理
硫化氢主要由地层产生,但也可以由含硫有机处理剂的热分解而产生。
硫化氢溶解于水形成一种弱酸,对钻具有腐蚀作用。
但它的主要作用不在于腐蚀,而在于使钢材发生氢脆破坏。
氢原子有个特性,在有硫化物的环境中以原子形式存在,在其他的环境中以分子形式存在。
氢原子是所有原子中最小的原子,它能渗入钢材或其他金属材料并扩散到材料内部,而且最容易集中到材料受力最大的区域,但当氢原子脱离了硫化物的环境后,很快结合成氢分子,氢分子的体积要比氢原子大许多倍,它能破坏钢材的组织结构,降低钢材的韧性,产生各种微小的裂纹。
氢原子又继续聚积到裂纹尖端,并使裂纹发展,直至钢材不能承受外界负荷时,会突然发生断裂,这种现象称为脆化。
氢脆的敏感性由下列因素决定:
ⅰ、钢材的屈服强度低于630MPa的普通碳素钢一般不会发生氢脆断裂,强度越高,产生破坏的时间越短;
ⅱ、合金钢的硬度大于Rc22时容易遭到破坏;硫化氢浓度越高,氢脆破坏的时间越短;
ⅲ、溶液的pH值的降低,氢脆断裂的趋势增长,pH值维持在9.0以上,则氢脆破坏可显著减少;
ⅳ、温度超过83℃,氢脆断裂的敏感性降低;外界施于钢材的应力越大,氢脆断裂的时间越短。
在大量硫化氢气侵的情况下,钻井液pH值可下降到4~5左右。
由于钻井液中HS
和S
离子的存在使氢原子结合成氢气的反应受到阻碍这一特殊效应,使得即使井筒里只含有少量的硫化氢,钻具就有可能发生硫化物应力腐蚀开裂和氢断裂。
除此之外,硫化氢还会使钻具发生电化学失重腐蚀。
硫化氢造成的电化学失重腐蚀的主要形态是全面腐蚀和溃疡状腐蚀,在钻柱表面形成大量形状、大小、深度各异的腐蚀坑和腐蚀条带,导致壁厚减薄、穿孔、甚至破裂。
②二氧化碳腐蚀机理
常温常压下二氧化碳的腐蚀也许似乎微弱的,但是对于钻具来说,井筒里是高温、高压和高浓度的二氧化碳环境,因此这时二氧化碳的腐蚀是非常显著的,甚至年腐蚀量达十几个毫米左右。
二氧化碳环境中钻杆的损害主要是快速的电化学失重腐蚀,其形态也大多是不均匀全面腐蚀。
CO2可来自地层,可以来自有机材料热降解、重晶石粉或膨润土中的盐酸盐、苏打粉或碳酸氢钠的化学过度处理。
防止CO2气侵必须根据CO2的来源采取相应的措施。
选用耐二氧化碳腐蚀材料,如Cr含量大于5%的材料具有很较好的抗CO2腐蚀能力。
③溶解氧的腐蚀机理
溶解氧腐蚀是钻具使用寿命下降的最重要原因,虽然硫化氢和二氧化碳气侵引起的后果是严重的,但毕竟能造成大量硫化氢和二氧化碳气侵的情况并不多,最普遍存在的是由钻井液中溶解氧引起的各种形态的腐蚀,如疲劳腐蚀、缝隙腐蚀和点蚀。
溶解氧腐蚀是在中性和碱性环境中发生的,而钻井液的pH值大多数是中性。
钻具的氧腐蚀速率基本上受氧的扩散控制,即提供给钻具表面的氧越多,腐蚀速率越大。
温度较低时氧的点蚀倾向较大,而温度升高时则转向全面腐蚀。
④电化学腐蚀机理
钻具在钻井液中类似于电极在电解液中,也可以产生导电反应,不同金属之间,不同的钢材化学成分之间就会产生导电现象。
如铜和钢连在一起放入水中,则铜为阴极,钢为阳极,产生电流,钢被腐蚀。
但钢与易反应的金属如铝和镁等连在一起放入水中,则钢为阴极,铝镁成为阳极,产生电流,铝镁被腐蚀,而钢得到了保护。
新钻杆与旧钻杆连接在一起,则新钻杆起阳极作用,旧钻杆起阴极作用,新钻杆先被腐蚀。
钻具的氧化皮与钢材本身之间的差异,也会产生电流,使钢本身进一步遭到腐蚀。
受应力的金属对不受应力的金属呈负电位,也可形成电池效应。
当电流流过钢材时,会带走微量的金属分子,并沉积于电流的另一端,这样就会形成伤疤,引起应力集中或造成疲劳破坏。
⑤细菌腐蚀机理
影响腐蚀的细菌可分为需氧菌和厌氧细菌两大系列,需氧菌在有氧存在的环境中发生反应,而厌氧细菌在无氧的环境中发生反应。
一些需氧细菌会使硫转化成硫酸,加剧腐蚀;而一些亚硫酸盐还原菌存在于厌氧环境,它们也会造成硫化氢对钢的直接腐蚀和使阴极解极化。
在含有氧的流体中,也会在活泼的腐蚀坑区发现亚硫酸盐还原菌,因为那里氧气的浓度变得很低。
最常见的细菌腐蚀是硫酸还原菌的腐蚀,硫酸还原菌的主要成分为氢化酶,能使硫酸盐分解产生H2S和H2,使金属被腐蚀成金属硫化物,而H2从阴极逸出,阴极被解极化,使腐蚀反应连续不断的进行。
在细菌的生物化学腐蚀中,除硫酸盐类还原细菌外,还有铁细菌、硫细菌、腐生菌和一些藻类也会对金属造成腐蚀,它们可以吸附在金属表面,形成双金属腐蚀电路。
另外,它们还可以积垢,形成电化学腐蚀电路,造成电化学腐蚀。
4、钻具其它失效类型
1)脱扣、涨扣
⑴脱扣
钻具在井下受拉力较大的情况下,丝扣被拉滑开的现象称为脱扣。
这主要的原因是由于丝扣上卸次数过多,磨损严重;或丝扣没有上紧;钻井液冲刺、腐蚀。
大尺寸井钻杆脱落是较常见的事故。
大尺寸井造成钻具脱扣的原因是:
①钻头和扶正器直径大,钻进或划眼时扭卡严重;
②过大的扭矩释放时,下部钻铤的惯性加速度(即钻铤瞬时的转速高于钻杆)导致钻杆脱扣;上扣扭矩达不到标准,也是造成脱扣的因素。
③将连接螺纹的规范搞错,把尺寸相近而又不是同一规范的公母螺纹连接在一起,因为它们咬合不紧,在运转过程中容易磨损而造成钻具脱落。
⑵涨扣
钻进时加压过大,或发生连续蹩钻,或在遇阻遇卡时强扭,或因为地面上扣扭矩不够,下井后蹩钻引起无控制再紧扣等,把钻杆母螺纹胀大、胀裂,造成钻具胀扣失效脱落。
脱扣、胀扣失效与使用关系密切,大多是使用不当造成的。
因此为了避免此类事故发生,使用时应按照操作规程执行。
2)表面裂纹
表面损伤属于磨损失效类型。
钻具在工作过程中,其外壁尤其是接头部位要与井壁或套管接触,承受剧烈的磨料磨损,会产生外表面磨损伤痕;由于钻具工作于钻井液之中,而钻井液是一种含砂量多、粘度大、相对密度大,并且具有一定腐蚀性的工作液。
因此,钻具在承受磨料磨损的同时,还承受钻井液循环的冲蚀磨损。
钻具在旋转钻井过程中,接头外壁很容易发生磨料磨损失效。
对于这种失效,其基本对策就是大幅度提高接头面工作的硬度。
3)过量变形
钻具构件的过量变形失效是由于工作载荷超过构件的屈服强度引起的。
构件的屈服强度低或者是工作载荷过大常会导致钻具出现使用过量塑性变形,若使用过量塑性变形过大、频率高,则就会出现钻具过量变形失效。
过量变形主要是人为因素造成,失效所占比例并不大,其预防主要是使用时按操作规程操作即可避免。
钻压是钻具失效的重要参数。
钻压的大小直接决定钻柱中和点的位置,也决定钻铤在井眼内的弯曲变形。
钻压过大易造成钻柱弯曲变形厉害,中和点上移,在各种振动作用下,钻具发生失效事故。
井径扩大导致钻具弯曲应力明显加剧,且钻铤较钻杆更为严重。
在钻井过程中发现,井径扩大导致钻柱失效次数也明显增加。
如井径扩大率23.7%,失效7次,全部发生钻铤部位,由此可见,井径扩大对钻柱,特别是中和点以下的受压钻铤影响非常大。
振动引起钻具的断裂、钻杆丝扣脱落、掉牙轮和下部钻柱的偏磨,是钻具失效最重要的因素之一。
振动可分为纵向振动、横向振动和扭转振动。
钻具在给定钻具组合条件下具有自身振动的固有频率,当转速接近固有频率所对应的转速时,就会引起钻具共振。
在不同的地层、井深、钻压及转速下,钻具表现出不同的振动形态。
⑴纵振破坏
钻具纵振是钻具最重要的一种破坏形式,其危害也最大,主要表现在以下几方面。
①纵振在钻柱的中性点附近产生交变的轴向应力,与其