飞轮课程设计说明书.docx
《飞轮课程设计说明书.docx》由会员分享,可在线阅读,更多相关《飞轮课程设计说明书.docx(19页珍藏版)》请在冰点文库上搜索。
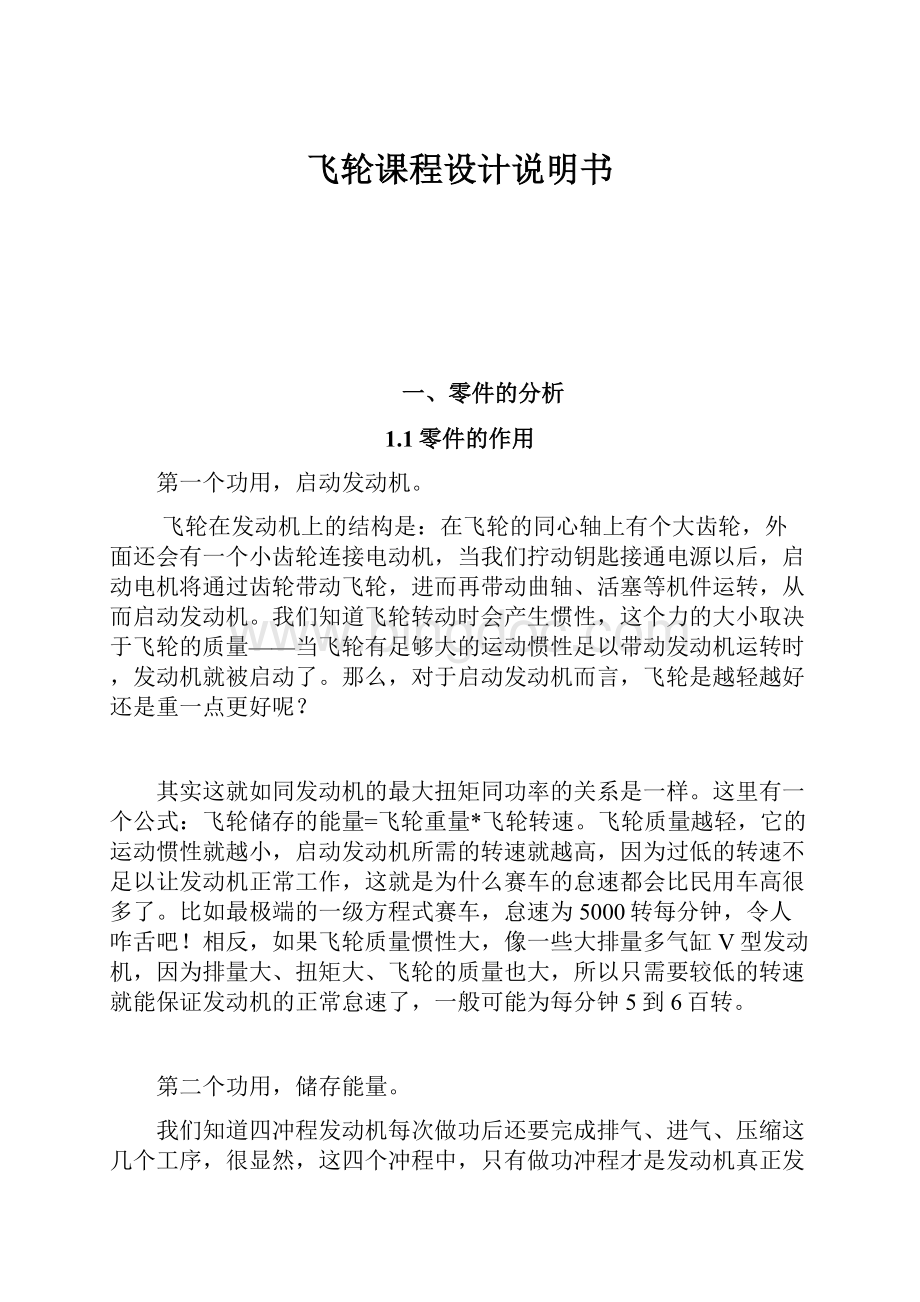
飞轮课程设计说明书
一、零件的分析
1.1零件的作用
第一个功用,启动发动机。
飞轮在发动机上的结构是:
在飞轮的同心轴上有个大齿轮,外面还会有一个小齿轮连接电动机,当我们拧动钥匙接通电源以后,启动电机将通过齿轮带动飞轮,进而再带动曲轴、活塞等机件运转,从而启动发动机。
我们知道飞轮转动时会产生惯性,这个力的大小取决于飞轮的质量——当飞轮有足够大的运动惯性足以带动发动机运转时,发动机就被启动了。
那么,对于启动发动机而言,飞轮是越轻越好还是重一点更好呢?
其实这就如同发动机的最大扭矩同功率的关系是一样。
这里有一个公式:
飞轮储存的能量=飞轮重量*飞轮转速。
飞轮质量越轻,它的运动惯性就越小,启动发动机所需的转速就越高,因为过低的转速不足以让发动机正常工作,这就是为什么赛车的怠速都会比民用车高很多了。
比如最极端的一级方程式赛车,怠速为5000转每分钟,令人咋舌吧!
相反,如果飞轮质量惯性大,像一些大排量多气缸V型发动机,因为排量大、扭矩大、飞轮的质量也大,所以只需要较低的转速就能保证发动机的正常怠速了,一般可能为每分钟5到6百转。
第二个功用,储存能量。
我们知道四冲程发动机每次做功后还要完成排气、进气、压缩这几个工序,很显然,这四个冲程中,只有做功冲程才是发动机真正发力的冲程,而其它几个冲程中该气缸不仅没有输出能量,反而需要耗费不少能量。
我们试想一下,如果没有一个可以存储能量的机件,那么动力输出将是非常不平顺的——在某个缸做功的时候,动力会以爆发的形式输出;而当没有气缸做功的时候,动力又会迅速降低,甚至是负值,那么这样工作状态的发动机显然是无法让人接受的。
飞轮的意义就在于此。
做功后热能转化为动能驱动活塞,通过曲轴带动飞轮旋转,利用飞轮所具有的较大惯性将能量存储起来。
当某缸做功时吸收部分能量,而当没有气缸做功时则释放部分能量,这样一增一降,才能保证曲轴旋转的均匀性。
这时有人会说:
要是一台V12发动机不就没事了。
不对!
V12发动机的这种冲击间隔肯定会比直4发动机要小得多,但是这不代表就会没有,而且出于成本和曲轴旋转平顺性的考虑,飞轮的作用是不可替代的。
从上面的原理我们可以看出,如果飞轮的质量大,那么这种曲轴转速的均匀性就会更好,表现出来就是发动机的平顺性更好,但如果想要实现发动机转速的快速提升,可就很费力了。
也就是说,如果飞轮的质量过大,发动机会运转的更平稳,不会有突然的急加速和急减速,但是发动机的响应性会变差,让人感觉迟钝。
这也就是我们常说的舒适性很好,但运动性不强.
1.2设计要求
汽车飞轮设计的基本要求:
(1)在任何行驶条件下,能可靠地传递发动机的最大转矩。
(2)接合时平顺柔和,保证汽车起步时没有抖动和冲击。
(3)分离时要迅速、彻底。
(4)从动部分转动惯量小,减轻换挡时变速器齿轮间的冲击。
(5)有良好的吸热能力和通风散热效果,保证离合器的使用寿命。
6)避免传动系产生扭转共振,具有吸收振动、缓和冲击的能力。
(7)操纵轻便、准确。
(8)作用在从动盘上的压力和摩擦材料的摩擦因数在使用过程中变化要尽可能小,保证有稳定的工作性能。
(9)应有足够的强度和良好的动平衡。
(10)结构应简单、紧凑,制造工艺性好,维修、调整方便等
图1为零件三视图,图2为零件三维图。
飞轮零件简图
1.3零件的工艺分析
(1)主要加工精度要求
1)Φ200mm外圆与Φ38+0.0250mm内孔同轴度公差为Φ0.05mm。
2)键槽10±0.018mm对Φ38+0.0250mm内孔轴心线对称度公差为0.08mm。
3)零件加工后进行静平衡检查。
4)铸造后时效处理。
5)未注明铸造圆角R5。
6)未注倒角2×45°。
(2).其余技术要求:
1)铸造后时效处理。
2.1确定毛坯的制造形式
零件材料为QT500-5,考虑到汽车,货车运行时经常需要挂倒档以倒行或辅助转向,因此零件在工作过程中经常受到冲击性载荷,采用这种材料零件的强度也能保证。
由于零件成批生产,而且零件的轮廓尺寸不大,选用球墨铸铁,铸造精度为2级,能保证铸件的尺寸要求,这从提高生产率和保证加工精度上考虑也是应该的。
选择毛坯时应该考虑的因素有:
零件的生产纲领、零件材料的工艺性、零件的结构形状和尺寸、现有的生产条件。
由于飞轮零件的材料要求选用HT200,抗拉强度和塑性低,但铸造性能和减震性能好,因此应选用毛坯类型为铸件,较高强度铸铁,基体为珠光体,强度、耐磨性、耐热性均较好,减振性也良好;铸造性能较好,需要进行人工时效处理。
该零件是大批量生产,零件的轮廓尺寸不大,所以企业选用机械砂型铸造,其生产效率比手工制砂型高数倍至数十倍,特别适合大批量生产,虽然设备昂贵,但工人的技术水平要求较低,对中小型锻件的质量稳定性也有明显提高。
2.2毛坯的设计
2.2.2确定零件毛坯的机械加工余量
查机械工艺师手册,结合公司实际情况,将零件各加工面毛坯余量及公差列入下表2-1。
简图
表面代号
基本尺寸
余量
余量公差
备注
A1-A3
-
-
-
实心
B1
Φ200
Φ3
±1
B2
Φ100
Φ3
±1
B3
95
2
±1
B4
110
2
±1
B5
110
2
±1
表2-1
2.2.3绘制轴的毛坯简图
轴的毛坯简图的绘制方法和步骤如下:
(1)用双点画线画出飞轮的主视图。
只画主要结构,次要细节简化不画,非毛坯制造的孔不画。
如图2-2
图2-2
(2)将加工总余量按尺寸用粗实线画在加工表面上。
如图2-3
图2-3
(3)标注毛坯的主要尺寸。
如图2-4
图2-4
2.4制定工艺路线
2.4拟定飞轮的工艺路线及定位基准
表2-2飞轮机械加工工艺路线
工序号
工序名称
工序内容
工艺装备
1
铸造
铸造
2
清砂
清砂
3
热处理
人工时效
4
清砂
细清砂
5
涂漆
非加工表面涂防锈漆
6
车
夹Φ100mm毛坯外圆,以Φ200mm外圆毛坯找正,车右端面,照顾22.5mm,车Φ200mm外圆至图样尺寸,钻车内孔Φ38+0.0250mm至图样尺寸,倒角2×45
C620
7
车
倒头,夹Φ200mm外圆,车左端大端面,保证尺寸95mm,车Φ100mm端面保证尺寸110mm,倒角2×45
C620
8
划线
在Φ100mm圆的端面上划10±0.018mm键槽线
9
插
以Φ200mm外圆及右端面定位,按Φ38+0.0250mm内孔中心线找正,装夹工件,插10±0.018mm键槽
B5020专用工装或组合夹具
10
钻
以Φ200mm外圆及一端面定位,10±0.018mm键槽定向钻4×Φ20mm孔
Z525专用钻模
11
钳
零件静平衡检查
专用工装
12
检验
按图样要求,检查各部尺寸及精度
13
入库
入库
工艺分析
1)飞轮为铸件,在加工时应照顾各部加工余量,避免加工后造成壁厚不均匀,如果铸件毛坯质量较差,应增加划线工序。
2)零件静平衡检查,可在Φ38+0.0250mm孔内装上心轴,在静平衡架上找静平衡,如果零件不平衡,可在左大端面(Φ200mm与Φ160mm之间)上钻孔减轻重量,以最后调到平衡。
3)Φ200外圆与Φ38+0.0250mm内孔同轴度检查,可用心轴装夹工件,然后再偏摆仪上货V形块上用百分表测出。
4)键槽10±0.018mm对Φ38+0.0250mm内孔轴心线的对称度检查,可采用专用检具进行检查。
1.粗基准的选择
①选用的粗基准必须便于加工精基准,以尽快获得精基准。
②粗基准应选用面积较大,平整光洁,无浇口、冒口、飞边等缺陷的表面,这样工件的定位才稳定可靠。
③当有多个不加工表面时,应选择与加工表面位置精度要求较高的表面作为粗基准。
④当工件的加工表面与某不加工表面之间有相互位置精度要求时,应选择该不加工表面作为粗基准。
⑤当工件的某重要表面要求加工余量均匀时,应选择该表面作为粗基准。
⑥粗基准在同一尺寸方向上应只使用一次。
2.精基准的选择
(1)零件已加工的表面作为定位基准,这种基准称为精基准。
合理地选择定位精基准是保证零件加工精度的关键。
(2)选择精基准应先根据零件关键表面的加工精度(尤其是有位置精度要求的表面),同时还要考虑所选基准的装夹是否稳定可靠、操作方便。
(3)精基准的选择原则:
①基准重合原则。
尽量选择设计基准作为精基准,避免基准不重合而引起的定位误差。
②基准统一原则。
尽量选择多个加工表面共享的定位基准面作为精基准,以保证.各加工面的相互位置精度,避免误差,简化夹具的设计和制造。
③自为基准原则。
精加工或光整加工工序应尽量选择加工表面本身作为精基准,该表面与其他表面的位置精度则由先行工序保证。
④互为基准原则。
当两个表面相互位置精度以及各自的形状和尺寸精度都要求很高时,可以采取互为基准原则,反复多次地进行加工。
(4)在选择基准时不能同时遵循各选择原则(甚至相互矛盾)时,应根据具体情况具体分析,以保证关键表面为主,兼顾次要表面的加工精度。
2.5主要工序切削用量及工序尺寸的确定
三、夹具设计2.5.1确定加工余量
主要由查表,配合经验法类比法确定加工余量及工序尺寸。
将相关数据列表4-1中。
表2-3飞轮加工余量与工序尺寸表
工序号
加工表面
基本尺寸
加工余量
公差等级
工序尺寸及公差
表面粗糙度
μm
6
车右端面
110+2
2
110
12.5
钻孔
Φ37
18.5×2
IT11
Φ37
12.5
扩孔
Φ37.8
0.4×2
IT10
Φ37.8
6.3
铰孔
Φ38
0.1×2
IT7
Φ38+0.0250
1.6
7
车左大端面
95+2
2
95
12.5
车Φ100端面
110+2
2
110
12.5
9
插槽
10
10
IT9
10±0.018mm
3.2
2.5.2确定切削用量
根据加工余量和装夹情况,确定走刀次数和背吃刀量;
查表结合经验确定主轴转数和刀具进给量,数据见表4-2
表2-4飞轮加工切削用量汇总表
工序号
加工部位
加工内容
刀具材料
走刀
次数
背吃刀量
mm
主轴转数
r/.min
进给量
mm/r
6
右端面,Φ38+0.0250内孔
车右端面
硬质合金
1
2
600
0.2
钻孔
高速钢
1
18.5×2
400
0.2
扩孔
高速钢
1
0.4×2
600
0.3
铰孔
高速钢
1
0.1×2
150
0.2
7
左大端面,Φ100mm端面
车左大端面,
硬质合金
1
2
600
0.2
车Φ100mm端面
硬质合金
1
2
600
0.2
9
10±0.018mm键槽
插10±0.018mm键槽
硬质合金
10
1
10
4×Φ20mm孔
钻4×Φ20mm孔
高速钢
1
20
400
0.2
2.5.3确定工时定额
因飞轮为成批生产,因此可以采用经验估算法计算各工序的工时定额。
主要利用经过实践而积累的统计数据及进行部分计算来确定,计算结果见表4-3在实际生产中,时间定额需要不断修正。
表2-5飞轮机械加工工时定额
工序号
工序名称
工序内容
工序时间(分)
1
铸造
铸造毛坯
2
清砂
清砂
3
热处理
人工时效
4
清砂
细清砂
5
涂漆
非加工表面涂防锈漆
6
车
车右端面
钻车Φ38内孔
15
7
车
车左端大端面
车Φ100mm端
5
8
划线
在Φ100mm圆的端面上划10±0.018mm键槽线
5
9
插
插10±0.018mm键槽
7
10
钻
钻4×Φ20mm孔
16
11
钳
零件静平衡检查
12
检验
按图样要求,检查各部尺寸及精度
3.1问题的提出
夹具是一种装夹工件的工艺装备,它广泛地应用于机械制造过程地切削加工、热处理、装配等工艺过程中。
机床夹具按在不同生产类型中的通用性,可以分为通用夹具.专用夹具.可调夹具.组合夹具等
因为是中批量生产,为了提高劳动生产率,保证加工质量,降低生产成本,减轻劳动强度需要设计专用夹具,经过分析,决定设计第55道工序钻2-M10螺纹孔的专用夹具。
3.2定位基准的选择
拟定加工路线的第一步是选择定位基准。
定位基准的选择必须合理,否则将直接影响所制定的零件加工工艺规程和最终加工出的零件质量。
基准选择不当往往会增加工序或使工艺路线不合理,或是使夹具设计更加困难甚至达不到零件的加工精度(特别是位置精度)要求。
因此我们应该根据零件图的技术要求,从保证零件的加工精度要求出发,合理选择定位基准。
此道工序后面还有精加工,因此本次工序没有较高的技术要求,也没有较高的平行度和对称度要求,所以我们应考虑如何提高劳动效率,降低劳动强度,提高加工精度。
我们采用已加工的大端面、Φ85孔及键槽为定位基准,为了提高加工效率,缩短辅助时间,决定用简单的螺母作为夹紧机构,利用钻模板和钻套实现快速定位加工。
3.3切削力及夹紧力计算
由于本道工序主要完成工艺孔的钻孔加工,钻削力。
钻削力
式(5-2)
钻削力矩
式(5-3)
式中:
代入公式(5-2)和(5-3)得
本道工序加工工艺孔时,夹紧力方向与钻削力方向相同。
因此进行夹紧力的计算无太大意义。
只需定位夹紧部件的强度、刚度适当即能满足加工要求。
3.4钻套与钻模板设计
M10的加工需钻,然后攻丝,因为钻后还要攻丝,为了我们钻后能及时的的攻丝,满足加工要求。
故选用多孔钻模板,将之直接旋转以更换钻套,以减少更换钻套的辅助时间。
根据工艺要求:
。
即先用Φ8.8mm的麻花钻钻孔,根据GB1141—84的规定钻头上偏差为零,故钻套孔径为Φ9mm。
再用标准M10丝锥攻丝,钻套孔径为Φ10.2mm
图4钻套与钻模板
3.5夹具设计及操作简要说明
如前所述,在设计夹具时,应该注意提高劳动生产率避免干涉。
应使夹具结构简单,便于操作,降低成本。
提高夹具性价比。
本道工序为钻床夹具选择了螺母夹紧方式。
本工序为切削余量小,切削力小,所以一般的手动夹紧就能达到本工序的要求。
本夹具的最大优点就是结构简单紧凑。
夹具的夹紧力不大,故使用手动夹紧。
为了提高生产力,使用快速螺旋夹紧机构。
夹具体如图6装配效果如图5。
图5螺母与开口垫圈
图6夹具体
图7夹具装配三维图
四、设计心得
为期三周的工艺、夹具课程设计基本结束,回顾整个过程,我觉得受益匪浅。
课程设计作为的重要的教学环节,使理论与实践更加接近,加深了理论知识的理解,强化了生产实习中的感性认识。
本次课程主要经过了两个阶段。
第一阶段是机械加工工艺规程设计,第二阶段是专用夹具设计。
第一阶段中认真复习了有关书本知识学会了如何分析零件的工艺性,学会了查各类工艺手册。
选择加工余量,确定毛胚的形状,大小等,绘制出了毛胚图。
又根据毛胚图和零件图构想出了两种工艺方案,比较其中较合理的方案来编制工艺。
其中运用了基准选择,切削用量计算等方面的知识。
还结合了我们生产实习中所看到的实际情况来选择设备,填写工艺文件。
而在夹具设计阶段,学习运用了工件定位,夹紧及零件结构设计等方面的知识。
工艺设计是我们学完了大学的全部基础课、技术基础课以及大部分专业课之后进行的.这是我们在进行毕业设计之前对所学各课程的一次深入的综合性的总复习,也是一次理论联系实际的训练,因此,它在我们三年的大学生活中占有重要的地位。
通过本次设计,我基本掌握了一个比较简单零件的加工工艺过程分析,工艺文件的编制,专用夹具设计的方法和步骤。
学会查阅手册,选择使用工艺设备等。
总的来说,这次设计,使我在基本理论的综合运用以及正确解决实际问题方面得到了一次较好的训练。
提高了我独立思考问题,解决问题创新设计的能力,为以后的设计工作打下了较好的基础。
五、参考文献
[1]陈宏钧.实用金属切削手册[M].北京:
机械工业出版社,2005.1.
[2]强毅.设计制图实用标准手册[M].北京:
科学出版社,2000.1.
[3]李洪.机械加工工艺手册[M].北京出版社,1996.1.
[4]陈宏钧.实用机械加工工艺手册[M].北京:
机械工业出版社,2003.1.
[5]杨叔子.机械加工工艺师手册[M].北京:
机械工业出版社,2001.8.
[6]马贤智.机械加工余量与公差手册[M].中国标准出版社,1994.12.
[7]王先逵.机械制造工艺学[M].北京:
机械工业出版社,1995.11.
[8]莫雨松.互换性与技术测量[M].中国计量出版社,2000.1.
[9]何玉林,贺元成.机械制图[M].重庆大学出版社,2000.8.
[10]王光斗,王春福.机床夹具设计手册[M].上海:
上海科学技术出版社,2000.11.