非金属夹杂物检验技术发展.docx
《非金属夹杂物检验技术发展.docx》由会员分享,可在线阅读,更多相关《非金属夹杂物检验技术发展.docx(25页珍藏版)》请在冰点文库上搜索。
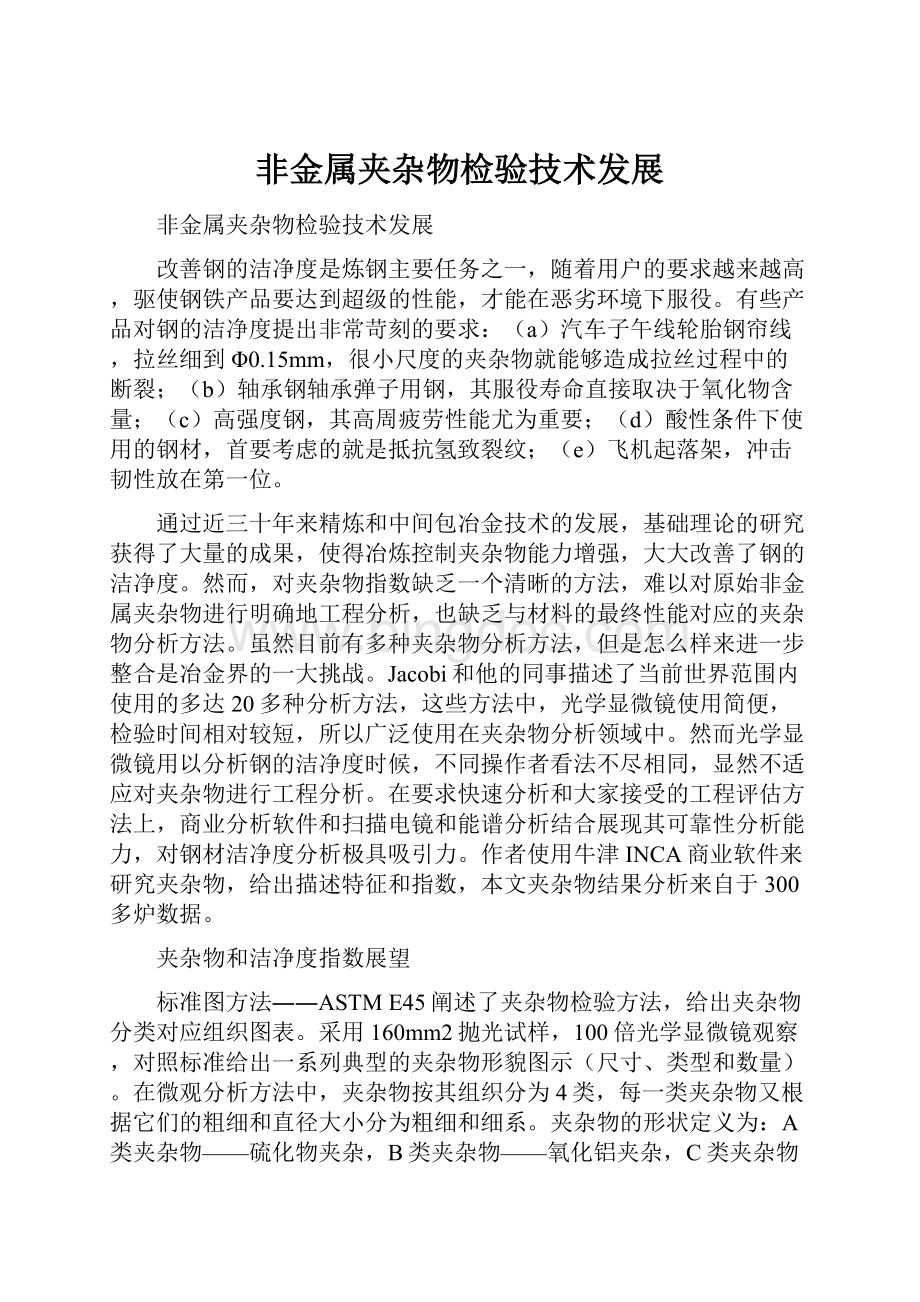
非金属夹杂物检验技术发展
非金属夹杂物检验技术发展
改善钢的洁净度是炼钢主要任务之一,随着用户的要求越来越高,驱使钢铁产品要达到超级的性能,才能在恶劣环境下服役。
有些产品对钢的洁净度提出非常苛刻的要求:
(a)汽车子午线轮胎钢帘线,拉丝细到Φ0.15mm,很小尺度的夹杂物就能够造成拉丝过程中的断裂;(b)轴承钢轴承弹子用钢,其服役寿命直接取决于氧化物含量;(c)高强度钢,其高周疲劳性能尤为重要;(d)酸性条件下使用的钢材,首要考虑的就是抵抗氢致裂纹;(e)飞机起落架,冲击韧性放在第一位。
通过近三十年来精炼和中间包冶金技术的发展,基础理论的研究获得了大量的成果,使得冶炼控制夹杂物能力增强,大大改善了钢的洁净度。
然而,对夹杂物指数缺乏一个清晰的方法,难以对原始非金属夹杂物进行明确地工程分析,也缺乏与材料的最终性能对应的夹杂物分析方法。
虽然目前有多种夹杂物分析方法,但是怎么样来进一步整合是冶金界的一大挑战。
Jacobi和他的同事描述了当前世界范围内使用的多达20多种分析方法,这些方法中,光学显微镜使用简便,检验时间相对较短,所以广泛使用在夹杂物分析领域中。
然而光学显微镜用以分析钢的洁净度时候,不同操作者看法不尽相同,显然不适应对夹杂物进行工程分析。
在要求快速分析和大家接受的工程评估方法上,商业分析软件和扫描电镜和能谱分析结合展现其可靠性分析能力,对钢材洁净度分析极具吸引力。
作者使用牛津INCA商业软件来研究夹杂物,给出描述特征和指数,本文夹杂物结果分析来自于300多炉数据。
夹杂物和洁净度指数展望
标准图方法――ASTME45阐述了夹杂物检验方法,给出夹杂物分类对应组织图表。
采用160mm2抛光试样,100倍光学显微镜观察,对照标准给出一系列典型的夹杂物形貌图示(尺寸、类型和数量)。
在微观分析方法中,夹杂物按其组织分为4类,每一类夹杂物又根据它们的粗细和直径大小分为粗细和细系。
夹杂物的形状定义为:
A类夹杂物——硫化物夹杂,B类夹杂物——氧化铝夹杂,C类夹杂物——硅酸盐夹杂,D类夹杂物——球状氧化物夹杂。
再根据夹杂物厚度尺寸分为粗细和细系两种。
尽管分类名称暗示了夹杂物组成,但是这个分类是严格按照夹杂物组织形态来分类的,而不管其夹杂的成分如何。
夹杂物名称沿用有其历史原因,四类夹杂物在0.5mm2的视场下,按照夹杂物的数量和长度来确定等级水平。
ASTM E45标准中对于洁净度的描述有5中方法:
方法A为最差视场法;方法B为长度法;方法C氧化物和硅酸盐法;方法D低夹杂物含量法;方法E是SAM评定法,反映钢中大型B类和D类夹杂的级别数和出现频率。
这种标准图评定方式仍然是工业上广泛使用的常规技术,尽管这种方式能够快速评估钢的洁净度,但对于研究分析来说是不够的。
夹杂物计数和测量技术――本文Wilson描述了Lukens钢厂洁净度评估方法。
在平行于轧制方向上的横截面取样,试样抛光面为40.3mm2,在250倍显微镜下对夹杂物进行测量。
对硫化物和氧化物夹杂簇、最大长度夹杂簇和独立夹杂进行检测。
按照Wolson的观点,经过轧制延伸后夹杂的密度和簇状夹杂物最大的长度是最为重要的夹杂物性参数。
显而易见,这个方法并不适用于所有的钢种,特别是在夹杂物轧制中不参与延展或很少延展的情况下的产品质量评估。
夹杂物体积分数——钢的韧性与第二相粒子的体积分数呈现指数型函数关系。
比如硫化锰夹杂、氧化物夹杂或者碳化物粒子。
假如这些夹杂微粒均匀分布,最简单的方法是通过计算它们的面积分数(面积分数已经用来估计粒子的体积分数)来评估洁净度,这种方法使用简单,能够被确定第二相粒子体积分数与钢的机械性能之间的关系。
(公式1)
这里
ΣAα 是所确定夹杂相面积总和,
AT 是测量的总面积
使用夹杂物的体积分数来作为评价钢的洁净度参数是非常有用的,作者还在文章的后部给出了一个表达各夹杂物之间距离的关系公式,从总体上说,夹杂颗粒之间的距离从物理意义上说比夹杂的体积分数更有意义,特别是夹杂物体积分数很小的洁净钢来说,难以用体积分数来计算表达夹杂平均尺寸、数量和面积。
椭圆型夹杂间距——Baker和他的同事研究了一个表达式,计算参与延伸变形硫化锰夹杂间距,假设板坯内的球状硫化锰夹杂经过热轧后变形为椭圆形硫化锰夹杂。
(公式 2)
这里
θ 是所选定的椭圆形硫化锰夹杂倾斜角。
λ 是夹杂的宽高比。
f 是夹杂的体积分数
钢板的洁净度——Otatani给出钢的洁净度公式,是在400倍光学显微镜下,看到的夹杂长度和宽度都大于3μm,。
(公式 3)
这里
d 是洁净度,
w 是夹杂宽度,
l 是夹杂长度,
a 是夹杂形状指数,
f 是视场中夹杂数量,
A 是视场面积(36.1μm2)
公式3是类似于公式1。
最近的夹杂距离——D是指相邻夹杂簇中心之间的最短距离,簇状粒子是三维随机分布的,该公式由Chandrasekhar给出。
当随机检测直线簇状夹杂指定的夹杂粒子之间的距离,其间距为:
(公式 4)
这里
D 是夹杂粒子之间的平均距离,
NL 是单位长度上夹杂粒子的数量,
f 是夹杂粒子体积分数,
xAl 是夹杂粒子算术平均值,
σAl 是标准偏差。
当随机检测指定簇状夹杂粒子之间的距离,由下式确定:
(公式 5)
当用体积方式检测簇状夹杂粒子之间的距离,由下式确定:
(公式 6)
Kocks修正了最为邻近的两个或者三个夹杂粒子之间的平均距离为:
(公式 7)
前述的公式依据是找到最为相邻的随机分布的夹杂物簇,给定的距离为x和x+dx,这样公式只能严格的限制在较低的体积分数下的点状颗粒夹杂或者小颗粒夹杂分布计算。
使用先前的公式来计算夹杂之间的间距将会导致严重的错误,为了克服公式5、6和7的错误,Bansl和Ardell研究了下列的表达式,在一定的体积(Δ3)和平面上(Δ2),考虑随机出现的单个分布球状夹杂之间的间距。
(公式. 8,9)
这里
r 是夹杂半径,
Fv 是夹杂的体积分数,
Γ() 代表不完全γ函数。
公式8和9对计算球状或点状夹杂物特别有效,对不是球状夹杂的计算不是非常精确的,此外,过于复杂的计算公式不适用于日常的试样夹杂分析计算。
一种新的夹杂物特点和指数概念
试样准备——从轧制后钢板横截面1/4地方提取厚度试样,试样的截面积为160mm2,平行于轧制方向,固定在酚醛树脂里进行自动抛光或人工抛光,抛光使用极细磨料要求表面平滑度达到1μm,抛光过程要注意重要的一点是试样不能接触水,防止溶解夹杂物,试样的清洁只能使用酒精。
SEM/EDS分析技术——试样如何准备和需要什么样的检验设备,关键是看分析夹杂物的精度。
使用电镜扫描,对试样抛光面积按照程序逐次扫描,然后用能谱进行成分等特征分析。
设备设定包括定义SEM参数,SEM/EDS上夹杂物分析程序按照ASTME2142标准进行。
标准有三种描述。
由于使用方便的缘故,大多数人使用第三种。
特别细小的夹杂物并非有害,使用SEM/EDS对抛光试样表面检测非金属夹杂物时,小于1μm夹杂长度忽略不计。
1μm长度的定义是人为确定的,目的是避免过长的扫描电镜工作时间。
一旦扫描结束,OxforINCAFeature软件进行储存和根据成分来分类夹杂,其它的商业软件也具有夹杂物分类的功能,EDS分析结果给出相应夹杂物的类型、化学成分、尺寸、分布和对所得到的结果统计,OxforINCAFeature软件给出各类夹杂物数据和预分类。
夹杂物分类流程在下面的章节给予描述。
夹杂分类——抛光试样取自平行于轧制方向或者垂直于轧制方向,夹杂物分类软件根据可识别的夹杂物进行分类,有三个阶段(图1-3),在第一阶段,非金属夹杂物归类是按其化学成分分类,而不管他们是否是内生夹杂还是外生夹杂。
图1 夹杂分类一级
在这个阶段上,夹杂的化学分类主要考虑是碳氮化物,还是硫化物或者是氧化物,这些分类是Kiessling和他同事以及Ghosh同事进行的。
下一个阶段是建立清晰的分析,再来区分这些氧化类夹杂是是外生夹杂还是内生夹杂。
外生氧化物夹杂通常颗粒较大,沿着轧制方向碾压破碎,时常可见线条状的破碎夹杂,成为呈线性布置的若干单独小颗粒。
假定外生夹杂最小的长度为7μm,而内生夹杂小于7μm,以此尺寸来界定内生夹杂和外生夹杂。
如果簇状内生夹杂(CaO或者CaS)尺寸上超过了7μm,根据化学成分分析结果确定这个簇状夹杂仍然归类为内生夹杂。
这里设定当线条状夹杂颗粒是球状的,其面积达到和超过132μm2后,就认为是外生夹杂。
图2 夹杂分类2级
第二级分类是将不同的夹杂按照化学成分归类,硫化物夹杂分为硫化锰夹杂,复杂硫化物夹杂或者球状硫化物夹杂。
氧化类夹杂分为氧化硅夹杂,复杂氧化物夹杂,氧化钙夹杂和氧化铝夹杂。
这些夹杂分类的标准按照其夹杂主要成分确定,或者根据夹杂物中元素的相对浓度进行分类(图2)。
图3 夹杂分类3级
第三级夹杂物分类包含识别外生夹杂来源,取决于夹杂成分。
夹杂分为4类:
(a)二次氧化,(b)中包/钢包耐材,(c)钢包/中包覆盖剂,(d)浸入式水口侵蚀物。
在这级分类中,夹杂物按照它们的基本成分来确定是哪一种,如图3所示。
其它不包含在图1-3中的夹杂认为不可分类,按照分析结果放在不可分类组中。
用户发现有些夹杂不见了,通过调整分类能够容易将其归纳到所需要的类型中去。
非金属夹杂指数技术——夹杂指数概念的研究和发展,使用功能强大扫描电镜和软件对抛光试样平面进行检测和分析,计算夹杂之间平均距离。
SEM/EDS分析技术提供每一个确定的夹杂面积信息,建立在SEM/EDS输出的数据,其相应的软件发展用于确定夹杂间距(TIS)。
1.从夹杂物分布建立夹杂一排面积,如得到,A1,A2,A3---An
2.夹杂面积总和,我们获得试样夹杂总体面积,总面积等于
3.试样总扫描面积AScan,
4.这里是试样总面积减去夹杂物总面积,
得出公式12,将其除以夹杂物个数开平方,得到TIS。
(公式12)
λT 是TIS以μm计量
fi 是钢中所有夹杂面积分数,量纲为μm2
如果公式用于分析氧化物/硫化物夹杂和氮化钛夹杂颗粒,分别由λOS和λTN表示。
从公式12看出,TIS是平均夹杂物之间的距离,使用公式12来确定夹杂之间的平均距离,考虑洁净度指数似乎注意下列假定和限制条件:
假定
●试样平面上的夹杂物分布可以代表夹杂的体积分布,注意到夹杂的评判是沿着轧制方向的平面来确定的,在该平面上的夹杂颗粒之间的距离和其它平面相比为最小,这是由于夹杂沿着轧制方向进行了延伸(图4)。
换句话说,使用轧制方向的平面来评判夹杂间距代表最为恶劣的洁净度。
然而,计算出来的夹杂颗粒在尺寸和形状上是均匀的,实际上是随机分布的。
Carti和他的同事使用Herta和Bansal公式计算分析最近间距,表明在平面上得到平均最近的距离大于体积上的最小间距,当其夹杂颗粒体积分数增加时候,其夹杂间距减小。
Carti按照Bansal公式计算的2μm夹杂颗粒数据作图,见图5。
因此,作为一定尺寸的球状夹杂颗粒,如果知道了在平面中的夹杂间距,就能够合理的估算出最近的夹杂之间距离和夹杂颗粒之间的间距。
图4 取样位相夹杂形态关系
图5 根据Bansal公式夹杂颗粒中心点之间最近距离
●仅仅测量大于1μm的颗粒和夹杂,小于1μm的颗粒和夹杂没有害处。
●注意:
夹杂之间空旷地带被考虑假设为一个方块。
表1 SEM-BasedINCAFeature软件分析结果
OxfordINCAFeatureinclusionrating
Interparticlespacings
试样ID
氧化物/硫化物数量密度(个./mm2)
氧化物/硫化物
尺寸密度
(μm/mm2)
Ti(C,N)
数量
(个./mm2)
Ti(C,N)
尺寸
密度
(μm./mm2)
最大外生夹杂颗粒
面积(μm2)
氧化物/硫化物平均
间距
(μm)
TiN平均间距
(μm)
总体颗粒间距
(μm)
R
10
29
3
7
0
315
615
280
限制因素:
●特别脏的钢则需要TIS技术使用另外的计算方法。
试样表面或亚表面的大颗粒外生夹杂特别重要的试样尤其重要,这种夹杂物分布在表面附近的情况下,对产品性能如弯曲和延展性都将产生重要的影响,基于这个理由,钢的洁净度评介除了TIS数值之外,还需要其它相关的夹杂物特性来表示。
●粗大的富钛和富铌颗粒就认为是非金属夹杂。
●TIS一个缺点是,假如两个试样具有相同的夹杂尺寸和种群,一个试样夹杂弥散分布,另一个试样集中分布,但是在TIS分析是不能加以区别,会给出相同的TIS数值。
公式优点——公式优于现有的公式地方为:
1考虑夹杂占据的空间,这就意味着该公式能够对所有形状和尺寸的夹杂检测和计算。
2能够对钢中所有的夹杂类型和特别的颗粒夹杂进行计算,这样就可以研究夹杂、颗粒夹杂间距和产品质量的关系。
3概念简单,功能强大,能够容易地处理任何颗粒和感兴趣的独立相,而不管这些颗粒和相在基体内是随机的还是均匀分布的。
4在试样特定的平面内或者体积内,根据相应的机械特性可以计算夹杂间距。
洁净度报告—洁净度分析完成,按照用户要求给出报表。
报表由四部分组成,下面段落来描述。
夹杂指数(尺寸和数量密度,夹杂间距):
见表1所述,用公制尺寸和数量单独或者复合阐述。
表1 基于扫描电镜INCA 软件夹杂分析结果
OxfordINCA特定夹杂指数
夹杂间距
试样ID
氧化物/硫化物数量密度
(个/mm2)
氧化物/硫化物尺寸密度
(μm/mm2)
Ti(C,N)数量密度
(个/mm2)
Ti(C,N)尺寸密度
(μm/mm2)
外生夹杂最大颗粒面积
μm2
氧化物/硫化物夹杂平均间距
(μm)
TiN夹杂平均间距
(μm)
总体平均夹杂间距
(μm)
R
10
29
3
7
0
315
615
280
内生夹杂三元图:
在三元相图看内生夹杂的产生分布(图6a-6d)。
各图表达为(a)CaO,Al2O3和S,(b)MnS,CaO和Al2O3,(c)MgO,Ti,和N,(d)Ti,Nb和N。
图a产生的夹杂是硫化物、氧化物和钙与铝夹杂。
图形表达是实用的方法,尽可能研究夹杂物改性的效率,例如,观察到聚集的夹杂物在三元相图的硫含量这侧,表示了钢中具有较高的硫化锰夹杂倾向,其次,考虑氧化钙和三氧化二铝夹杂的相对位置,来评估整个钢包精炼过程中是非常重要的。
图6 (a)Al2O3-CaO-S,(b)Al2O3-MnS-CaO,(c)Ti-MgO-N,(d)Nb-Ti-N三元相图
表2由基于扫描电镜INCA软件确定的外生夹杂
中间包耐材
钢包/中间包覆盖剂
总数
平均面积
(μm2)
最大面积
(μm2)
总数
平均面积
(μm2)
平均面积
(μm2)
0
0
0
3
399
633
钢包耐材
浸入式水口能力
总面积
总数
平均面积
(μm2)
平均面积
(μm2)
平均面积
(μm2)
平均面积
(μm2)
0
0
0
0
0
0
1197
外生夹杂:
外生夹杂虽然数量少,但是这类夹杂大多数非常有害。
表2给出了外生夹杂的起源和数量,表中显示了外生夹杂按照分类给出最大尺寸和平均尺寸。
典型的光谱分析和扫描电镜照片见图7。
按照图3显示软件步骤,外生夹杂按其相应的成分和组成确定成因。
图7 外生夹杂:
(a)x-射线,(b)典型的扫描电镜图
最大夹杂到试样表面距离:
给出了最大外生夹杂到试样表面距离,这个参数对弯曲能力特性评估是有价值的。
夹杂空间分布:
在钢抛光试样上发现所有的夹杂和分布情况可以图像显示,见图8。
两种不同钢种洁净度肉眼可见夹杂分布,可以进行比较。
图8 试样抛光表面夹杂空间分布图
临界TIS数值-TIS给出钢的所有洁净度指数,虽然并不单独作为钢的洁净度唯一指标,但是发现对测量硫化锰夹杂或者总体氧化物线状夹杂是非常有用的,TIS数值增加,说明硫化锰夹杂聚集程度减小,所以TIS数值能够作为精炼有效的技术指标。
TIS参数研究的运用
这段给出TIS和某些重要冶炼参数之间的关系实例。
钢中硫含量和TIS关系-钢的基体具有良好的展性和韧性,但是无延伸的硫化锰夹杂的存在非常有害,有些研究表明,机械性能是随着硫含量增加而恶化,特别是展性和韧性。
图9和图10表明了TIS和硫含量之间的对应关系,随着硫含量增加,TIS数值减小。
图9 夹杂间距和硫的关系-实验1
图10 夹杂间距和硫的关系-实验2
和不同精炼时间的对比-调查延长钢水精炼时间的效果,跟踪了三炉钢,A炉钢精炼时间是常规的;B炉钢硫含量较低,而且延长了精炼时间;C炉钢水采用真空脱气处理。
在表3中看出夹杂尺寸密度、试样单位面积夹杂物总量和每类夹杂情况。
最大的外生夹杂以面积来表达,氧化物/硫化物三元图见图11,对应TIS和氧化物和硫化物线状夹杂总长,表明随着增加氧化物和硫化物线状夹杂长度增加,对应的TIS数值减小(图12)。
表3 高或低洁净度和TIS数值对比
OxfordINCA特定夹杂指数
夹杂间距
试样ID
氧化物/硫化物数量密度
(个/mm2)
氧化物/硫化物尺寸密度
(μm/mm2)
Ti(C,N)数量密度
(个/mm2)
Ti(C,N)尺寸密度
(μm/mm2)
外生夹杂最大颗粒面积
μm2
氧化物/硫化物夹杂平均间距
(μm)
TiN夹杂平均间距
(μm)
总体平均夹杂间距
(μm)
A炉
60
213
32
114
266
129
176
104
B炉
6
17
6
16
1692
409
417
287
C炉
4
10
1
1
1757
515
1226
474
图11 不同精炼时间内生夹杂三元相图
图12 外生夹杂间距的影响
钙/硫比和TIS对比-文献中采用钙硫比来表达成品钢材的洁净度和产品性能。
从实验得出的钙硫比对应氧化物/硫化物夹杂间距,具有非常好的相关关系,见图13。
对优化当前的钙硫比达到良好的洁净度有着非常好指导作用。
见图14。
图13 氧化物/硫化物和Ca/S比夹杂间距关系-实验数据
图14 氧化物/硫化物和Ca/S比夹杂间距关系-生产数据
运用TIS技术优化冶炼工艺
夹杂间距的概念用于工程分析和工艺改进非常有用,下面是一些实例。
钙处理球化效率-不同钙处理球化剂用于夹杂物改性对钢的洁净度指标是非常重要的,使用三种球化剂来进行评估。
使用三种球化剂的结果表示在图15中,结果显示使用这三种球化剂对TIS数值有着显著的差别。
图15 不同钙球化剂夹杂变性效率比较-方块图表示分布。
注意:
Minitab用星号表示异常值
渣系优化-渣系对脱硫和吸附非金属夹杂扮演着最重要的角色,调查了两种渣系对钢洁净度的影响。
渣系2从操作者角度上看似有效,但是为保证钢的洁净度而不能使用这个渣系,对比两种渣系产生的TIS数值,见图16,可以看出两种渣系产生的洁净度指标是类似的。
(不明白要表达什么意见。
)
图16 夹杂中不同渣对间距的影响-方块图表示分布。
注意:
Minitab用星号表示异常值
钙处理优化-钙处理效率在一定程度上取决于喷射进入钢中的金属钙量。
钙在钢包中氧化和脱硫导致钢中钙含量每一炉变化值都很大,钙处理优化钢实验在图17给与总结,优化后的钙处理钢具有较大的非金属夹杂间距。
图17 钙处理对夹杂间距的影响-方块图表示分布。
注意:
Minitab用星号表示异常值
合金含量和夹杂间距关系-某些夹杂起源于加入的合金,推测这些夹杂随着合金含量的增加而增加。
这里研究的是氮化钛夹杂,相应的关系见图18。
图18 钛含量和TiN夹杂间距关系
使用TIS评介钢的质量-本文分析研究各种的参数对夹杂间距的影响,这个TIS参数可用于产品的质量控制。
钢中夹杂不均匀分布会造成夹杂含量变化,好的方法是采用取自不同部位若干个试样分析估计,这些试样的均值就具有代表性了。
试样的数量多少按照ASTME45标准中试样制取指导进行。
重现性和再现性
同样试样连续测定,意在参数重现,看其评定的偏差值。
选用钙处理后的洁净钢试样进行分析,在40mm2面积上连续扫描3次,结果见表4。
实验结果表明只有很小的差别,最终的TIS数值上仅仅有3μm的差别。
非确定的夹杂第一次扫描和后两次扫描看到的结果相差较大,可能是电子束污染了试样的表面造成洁净度的改变。
另外的一个实验体现再现性,使用扫描电镜和场发射扫描电镜常规的钨丝对同一点进行分析,其结果见表5。
仅仅有很小的差别在碳氮化钛,富含铌和氧化物夹杂相差不大,硫化物夹杂相差200多个,主要是场发射扫描电镜能够检测到很小颗粒的夹杂所致,能够看到低于1μm夹杂。
然而,硫化物夹杂在TIS数值体现是很小的差别(250对243μm)。
表4 B1D635-B11(1/2in.HX450)钢重现性结果
夹杂类型
扫描1(夹杂数量)
扫描2(夹杂数量)
扫描3(夹杂数量)
Ti(C,N)
353
332
338
FeNb
16
17
18
硫化物
307
304
317
氧化物
76
94
96
小计
752
747
769
所有夹杂
1003
885
913
不确定夹杂
251
138
144
O/SIS(μm)
304
299
293
TiNIS(μm)
310
319
316
TISIS(μm)
217
218
215
表5 SEM和FE-SEM再现性实验比较结果
夹杂类型
扫描电镜
场发射扫描电镜
Ti(C,N)
69
40
FeNb
5
8
硫化物
1095
1304
氧化物
1591
1579
小计
2760
2931
夹杂总数
2854
3008
未确定夹杂
94
77
O/SIS(μm)
254
245
TiNIS(μm)
1529
1898
TISIS(μm)
250
243
概述和结论
使用最新的技术技术来比较钢中不同类型的非金属夹杂,基于扫描电镜的INCA软件,作者能够确定检测到夹杂平均间距,给出公式进行计算,这个公式计算的结果称为夹杂总体的间距(TIS),已经成功运用在优化工艺和改善钢的洁净度上。
TIS概念提供了一个平台,适用于评介和优化钢的洁净度,这个概念简单而能力强大,集合夹杂物分类商业软件,使用各种电镜来实现,总体说,TIS技术用于研究第二相粒子均匀分布或随机分布非常实用。
致谢
作者感谢StevenHansen,EdDiccicio,TerryRusso,TonyCerasi,TomToner,RandyPetty,JasongThomas,MichaelCooke,RobManning,MikeSchmidt,MilesHaberkorn,YufengWangandKeithYaylor在SSAB研究中给予的支持。
特别感谢ChrisAmsden,他研究了独特的抛光技术,避免夹杂蹦离和溶解。
唐杰民2014年12月译自《Iron&SteelTechnology》