套筒挤压成型模具设计Word格式.docx
《套筒挤压成型模具设计Word格式.docx》由会员分享,可在线阅读,更多相关《套筒挤压成型模具设计Word格式.docx(28页珍藏版)》请在冰点文库上搜索。
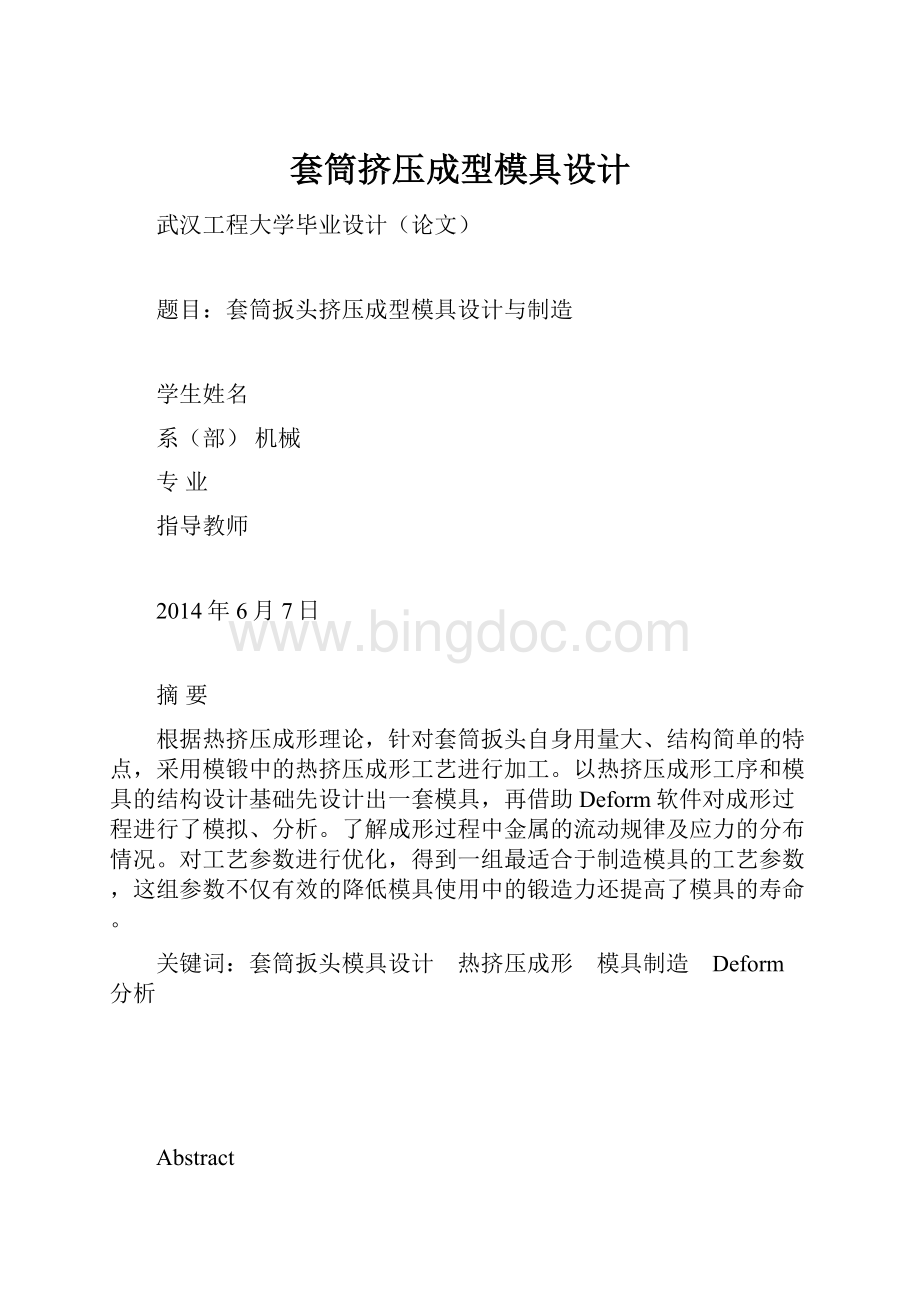
第三节套筒扳头热挤压成型工艺方案的确定…………………………………………7
第四节热挤压的质量问题及预防………………………………………………………10
一、磨损………………………………………………………………………………10
二、热疲劳裂纹………………………………………………………………………10
三、破裂………………………………………………………………………………10
四、模具发生塑性变形………………………………………………………………10
第五节毛坯的尺寸计算…………………………………………………………………11
第六节热挤压力的计算…………………………………………………………………12
第七节小结………………………………………………………………………………13
第三章热挤压模具的结构设计…………………………………………………………13
第一节热挤压模具材料的选择…………………………………………………………13
第二节模具设计…………………………………………………………………………15
一、凹模的设计与计算………………………………………………………………15
二、上凸模的设计与计算……………………………………………………………16
三、下凸模的设计与计算……………………………………………………………18
第三节小结………………………………………………………………………………19
第四章Pro/E3D建模……………………………………………………………………20
第一节Pro/E3D建模…………………………………………………………………20
第一节小结…………………………………………………………………………22
参考文献………………………………………………………………………………………23
致谢……………………………………………………………………………………………24
前言
现代工业的迅猛发展使挤压技术得到越来越广泛的应用,对挤压模具的设计与制造的要求越来越高。
我们都知道挤压模具是挤压生产的主要工艺准备,它的设计是否合理对挤压件的表面质量、尺寸精度、生产率以及经济效益等影响很大。
所以说提高挤压模具的设计水平和挤压模具的各项技术指标,对现代工业的发展使十分必要的。
挤压模具设计广泛应用于机械、汽车、五金制品等行业中。
由于金属材料的冷、温、热变形,所以挤压模具分为冷挤压模具、温挤压模具、热挤压模具,从设计中可以看出是热挤压模具的设计。
热挤压模具一般都是由模架、导向装置、紧固装置、卸料装置、冷却装置和热加压模具工作部分(凸模和凹模等)组成。
它一般将坯料加热到热锻温度,所获得的热挤压件具有良好的力学性能。
生产实践证明,热挤压是一种生产效率高、劳动强度低、加工质量好、省料、省工和成本低的金属压力加工方法。
这种先进的加工方法,可以取代或部分取代金属切削加工,为机械加工实现少无切削创造了条件。
制定套筒扳手的热挤压成形工艺,坯料加热温度的确定,成形过程中的润滑计算热挤压力,挤压速度,运用CAD技术实现成形模具CAD建模,并采用有限元软件DEFORM-3D实现套筒扳手的挤压成型模拟和分析,运用Pro∕E3D进行建模,提高了自己的动手能力,互相请教,巩固了自己所学的知识,并且运用好学院的图书馆书籍。
第一章绪论
第一节本课题的目的和意义
应用3D-CAD软件实现套筒扳头挤压模具设计,并采用有限元软件DEFORM-3D实现套筒扳头挤压成形模拟与分析技术是当前比较先进的CAD/CAE设计,仿真理念。
集合本专业知识,通过该项目的研究与实施,培养学生运用3D-CAD软件进行挤压成形模具设计及其成形分析,提高综合素质设计,分析能力及解决生产实际问题的能力,加强和提升所学专业知识,同时拓展专业广度,符合我校应用型人才培养模式。
第二节本课题的主要研究内容及技术要求
1.学习,掌握套筒扳头热挤压成形工艺流程;
2.学习理解挤压模具相关参数的计算与分析,运用CAD技术实现成形模具CAD建模;
3.熟练掌握DEFORM-3D有限元软件及其应用技术;
4.模拟,仿真挤压成形过程,分析影响正常成形的因素,对成形模具设计进行优化,最后进行模具制作。
一、套筒扳头的制造工艺确定
针对套筒扳头自身的特点,利用热挤压成形理论,制定套筒扳头热挤压的成形工艺。
二、套筒扳头的模具设计
结合套筒扳头用量大结构简单的特点,设计热挤压制造套筒扳头,其中以模具结构的设计和模具制造为重点。
模具设计包括成形工艺方案的确定、毛胚尺寸的计算、挤压力的结算、模具各部分零件尺寸的确定、模具材料的选取、模具的强度及寿命的校核。
三、DEFORM的优化设计
模具按照理论依据和经验公式进行设计,得出的模具结构不一定为最优。
再利用Deform对其分析优化,改变其中结构工艺参数,使其工作应力尽量降低,提高模具的寿命,再用Deform分析的到的最优的资料去指导模具的生产。
第三节小结
本章概述了套筒扳头的特点及其制方法,并要利用Deform软件对模具成形过程进行分析,从而指导模具的生产。
第二章套筒扳头热挤压模具设计
第一节热挤压工具概述
所谓热挤压就是在挤压前将毛坯加热到金属再结晶温度以上的某个温度下进行的挤压(见下表2—1),从而获得所需要的热挤压件的一种加工方法。
一般碳钢的热挤压加工温度区间见图2—1所示:
表2-1金属的再结晶温度
金属
再结晶温度(℃)
熔点(℃)
Pb
室温以下
327.4
Sn
232
Zn
200
419.4
Mg
150
650
Al
660
Cu
1083
Ni
600
1455
Fe
450
1539
C0.1%钢
580~600
C0.25%钢
600~630
C0.15%钢
630~650
图2-1碳钢的加工温度区域
由图2--1可见热挤压时,毛坯是在很高的压应力作用下产生塑性变形。
所以包括高温下塑性很低的材料,均可以承受很大的变形而不发生破坏。
热挤压工艺过程包括:
毛坯的制备——毛坯预热和加热——涂敷玻璃润滑剂——挤压——卸下模具(凸、凹模)、芯棒,清除制件上的玻璃润滑剂——精加工。
挤压可以分为两大类:
正挤压和反挤压。
正挤压的特点是被挤压金属的流动方向与凸模(冲头)的运动方向一致,而凹模则是固定不动的。
如图2—2:
图2-2正挤压过程示意图
(a)凸模接触热料,金属坯料开始流动
(b)凸模完成挤压,滑块回到下死点位置
(c)凸模向上运动,离开挤压件
反挤压的特点是金属流动方向与凸模的运动相反。
采用反挤压能制成圆形、正方形、矩形以及其它形状的空心零件。
如图2—3
图2-3反挤压过程示意图
(b)凸模完成挤压,滑块回到下死点位置
热挤压基本上有如下几种形式如图2—4所示。
其中a、c、d的形式应用最广。
a应用于挤压筒形零件,c应用于挤压管形零件,d应用于棒形零件。
b也是应用于挤压棒形零件,此形式由于毛坯相对于挤压筒壁没有滑动,所以摩擦力比d小,而且一般情况下不采用。
但是近来这种形式有时也用于挤压有色金属零件。
图2-4挤压方式
a)深孔反挤压b)实心反挤压c)空心正挤压d)实心正挤压
热挤压工艺是先进的金属压力加工方法之一。
挤压件的机械加工余量较小,表面质量和尺寸精度也较高,热挤压件的表面光洁度高,尺寸精度也可达IT6--7级。
因此,在零件要求不太高的情况下,热挤压件无需再进行机械加工,从而可以节约大量的金属材料和机加工工时,因此热挤压加工工艺是一种很有发展前途的金属加工方法。
第二节热挤压工艺中的重要工艺参数
在热挤压成形过程中,坯料的加热温度、润滑条件、挤压速度及模具的过渡圆角等都对热挤压成形起着关键的作用。
一、坯料加热温度的确定
在热挤压前毛坯要先要预热,目的是防止毛坯晶粒粗大,表面产生裂纹,提高生产率和节约能源。
一般来说,在保证金属坯料不产生过烧和过热的前提下,总是希望被挤压金属的坯料温度愈高愈好,金属的塑性就越好,也就更容易金属坯料的变形。
但是金属坯料的加热温度不能无限的高,因为金属坯料的加热温度过高,不仅会产生严重的氧化和脱碳,而且还可能出现过热和过烧现象。
因此,金属坯料的加热温度,必须严格控制在一定的范围内,通常是将金属坯料的加热温度控制在低于金属坯料熔化温度150—250℃之间。
二、成形过程中的润滑
润滑剂选用的合适与否直接影响热挤压工艺的成败。
对于钢,使用各种各样的玻璃粉或者玻璃纤维作润滑剂。
它们不仅起润滑作用(摩擦系数
=0.027—0.033),还在毛坯和模具之间起隔热作用。
根据热挤压工艺特点,一般要求润滑剂有如下性能:
(一)具有良好的润滑性能
在热挤压时,为使坯料与模具隔离,避免两者的直接接触,帮助金属流动、提高金属的填充性,降低挤压力,因此要求润滑剂在热挤压温度范围内要具有良好的润滑性能。
(二)具有良好的脱模性能
在热挤压时,模具的温度一般在200—300℃,有时甚至高达400--500℃,而挤压件的温度远高于模具温度,当挤压过程结束时,如果润滑剂具有良好的脱模性,则挤压件与模具可即刻分离出去,从而减少了挤压件传到模具上的热量,也就控制了模具的温升。
三、模具材料的选用
热挤压模具在材料的变形过程中,要经受高的变形抗力和热应力的综合作用,单位压力可高达2000—2500Mpa,连续生产时模具温度可以高达到500--600℃甚至更高,因此在进行工艺设计时,模具材料应满足下列要求:
四、成形设备特点
在钢质机械零件的热挤压过程中,目前越来越多地采用专用的热挤压设备,针对热挤压工艺生产的特点,用于热挤压生产的设备应满足下列要求:
(一)设备必须具有足够的强度和刚度
(二)足够的打击能量和精确的导向
(三)要有合适的挤压速度
第三节套筒扳头热挤压成型工艺方案的确定
根据套筒扳手零件的结构特点以及热挤压工艺的要求,图2---5所示的零件图,此次毕业设计针对此零件进行了工艺分析,设计了一套可供生产使用的热挤压成形模具。
图2-5扳头零件图
热挤压工艺方案可以如下图2--6所示:
下料→墩粗、锯平→挤压成形
图2-6套筒扳手热挤压工艺简图
在套筒扳手成形工艺方案中,墩平工序后是要进行退火和磷化处理的。
套筒扳手热挤压材料采用25号钢。
生产套筒扳手的全部流程为:
备料---原材料酸洗、磷皂化---拉拔---下料磷皂化---墩平---退火---酸洗、磷皂化---成形---热处理(渗碳淬火或碳氮共渗)---包装入库。
各主要工序工作特点分析:
(一) 准备主要为后工序提供稳定的工作直径,以及低而稳定的材料硬度。
(二) 下料本工序要求下料长度稳定,重量公差稳定在
以内。
(三) 加热为确保零件内孔对脱碳层的要求,坯料采用中频加热方式,在加热过程中应严格控制坯料的加热温度。
(四) 墩平通过墩平工序消除马蹄形、压塌等缺陷,墩平上下断面并在上断面中心打出一中心窝,在下端面边缘形成倒角,为下道工序做准备。
(五) 润滑在生产过程中,将圆柱形毛坯表面涂上水剂石墨,然后感应加热至490℃,放入组合凹模的模具中。
(六) 成形本工序所需要完成的是挤压内孔和下端的四方,采用一次反挤压成形工艺,即杆部反挤头部正挤的复合挤压成形工艺可以解决上述问题,其工艺流程如图2所示。
由于采用了六角头和四方头孔均反挤,坯料与凹模之间无相对运动产生的摩擦力,从而降低了挤压力。
该方案模具结构简单,生产效率高J31—100型曲柄压力机活动横梁到工作台面距离为1250mm,行程长,凸模设计为中空结构,成形杆部的模腔在凸模上,可以完成脱模。
套筒扳手热挤压工艺的生产过程是:
下料-加热-挤压-热处理-精加工。
图2-7成型过程
第四节热挤压的质量问题及预防
套筒扳手的热挤压是属于模锻中的热模。
模锻工序的镦粗变形过程可能会产生以下一些缺陷,影响镦粗件的质量。
所以要了解这些失效形式,才能有效的采取相应的措施。
常见的失效形式有以下几种。
一、磨损
磨损是模具与毛坯在高压下相对摩擦的结果,磨损使模具表面不平并且出现沟痕,这种沟痕有可能引起应力集中造成模具破裂。
二、热疲劳裂纹
热疲劳裂纹是由于模具表面热冷交替反复变化引起异符号的热应力的反复作用而产生的。
热裂纹成龟裂状,多发生在模具的突出部,因为突出部容易急冷急热。
当模具材料的导热性差,热膨胀系数大,使用温度范围和润滑剂选用不合适时,更容易产生热裂。
磨损和热疲劳裂纹属于正常失效。
三、破裂
产生破裂的原因:
(一)采用的模具材料冲击韧性低;
(二)模块没有锻透,组织不均,甚至内部有缺陷;
(三)热处理不当,有实效裂纹;
(四)模块内的纤维方向安排不当。
防止模具破裂,在设计时应当考虑以下几点:
(一)确保在模锻时,模具发生模锻时,模具内的应力值低于材料允许强度极限;
(二)尽量减少应力集中情况;
(四)多余能量的吸收问题;
(五)选用适当的模具材料并对模块的锻造和纤维方向的布排提出要求。
四、模具发生塑性变形
模具发生塑性变形的原因是因为模具的硬度过低或锻件的变形抗力过大所引起的。
热短时由于冷却不好,模具温升较高,引起模具退火而变软。
而当坯料温度过低时锻件的变形抗力便会增大。
第五节毛坯的尺寸计算
根据零件确定毛坯为圆棒料,规格为Ф45X71mm。
就能确定毛坯的形状如图2—8:
图2-8零件毛坯形状图
首先根据挤压件图计算出套筒挤压件的重量为0.163kg,挤压件的重量加上1%的烧损率(由于采用中频感应加热),再加上1%的锯边重量:
即毛坯的重量=挤压件的重量×
(1+1%+1%)=0.8315kg
再根据毛坯与零件质量不变原理有:
V
=V
毛坯体积V0=挤压件体积VP+0.01V0+0.01V0
=1.1424×
105mm3
选用毛坯的规格为Ф45×
71mm
毛坯的高度h0=V0/A0=1.27×
105/
R
=71mm
采用热挤压成形工艺,需对材料的许用变形程度进行验证,许用变形程度用断面收缩率ε来表示挤压过程中毛坯的变形程度为:
%
(1)
<
完全满足要求
式中
---断面收缩率
---许用断面收缩率
---挤压前毛坯与凹模的接触面积(
)
----挤压后毛坯与凹模的接触面积(
)
第六节热挤压力的计算
已知挤压方法为反挤压,被挤压的材料为25钢,终挤压温度不低于900℃,查得900℃时25钢的抗拉强度δb为77Mpa,挤压力可采用经验公式计算如下:
F反=0.785d
kδb
=0.785×
64.9
×
3.125×
77
d---反挤压模凸模直径(mm)
k---校正系数(d/t)其中t=挤压件壁厚
δb---挤压终了温度时材料的极限强度(Mpa)
结合Deform优化分析得挤压力=1515N
根据挤压力和挤压所需行程选取3150KN的万能液压机。
3150KN的万能液压机的参数如下;
液压系统最高工作压力P=32MPa,在本系统中选用P=25MPa;
主液压缸公称吨位3150KN;
主液压缸用于冲压的压制力与回程力之比为8%,塑料制品的压制力与回程力之比为2%,取800KN;
顶出缸公称顶出力取主缸公称吨位的五分之一,取650KN;
顶出缸回程力为主液压缸公称吨位的十五分之一,210KN
行程速度
主液压缸快速空行程V=50mm/s
工作行程V=10mm/s
回程V=50mm/s
顶出液压缸顶出行程V=50mm/s
回程V=80mm/s
经过DEFORM-3D优化分析,压力机的工作速度=260mm/s,
热挤压温度=260℃
因为该零件在挤压成形过程中所需的任意参数都在3150KN的万能液压机的公称范围内,因此选用3150KN的万能液压机是能满足要求。
第七节小结
本章阐述了有关套筒扳手热挤压的有关基础知识和需要注意的有关问题,并且确定了套筒扳手热挤压成形的工艺方案,热挤压中常见的问题及解决方法,毛坯的体积,热挤压力的计算和压力机的选择。
第三章套筒扳头热挤压模具设计
第一节热挤压模具的材料选择
对于热挤压模具,由于其工作环境十分恶劣,在挤压生产中长时间的承受高温、高压、强摩擦及循环载荷的冲击作用,导致模具使用寿命低且损耗大,通常模具费用占挤压生产成本的10%—15%。
因此,延长模具寿命,降低模具成本,是挤压生产过程中,人们最为关心的一个重要问题。
一、热挤压模具材质选择条件
实践证明,模具的寿命不仅与挤压工艺、模具设汁制造工艺过程有关,而且还与模具的材质选择有重要的关系。
俗话说“先天不良,后天难以改良。
”便是这个道理。
大量的事实说明,对于热挤压模具的材质,必须具备以下条件:
(一)具有足够的高温强度。
即模具材料在500℃以上温度范围的挤压变形过程中,能承受高温、高压作用,不发生屈服变形和断裂,保证挤压制品获得所需尺寸精度。
(二)具有良好的抗磨损性能。
即在高温、强摩擦的挤压条件下,模具材料能抵抗金属制品长时间的、高速的、激烈的摩擦作用,而不过早出现磨损,尤其对模具工作带表面更显重要。
(三)具有足够高的抗疲劳性。
在挤压过程中,模具能承受周期性循环载荷作用而不发生断裂损坏,因此,模具材料必须具备良好的抗冲击韧性。
(四)具有良好的导热性能。
热挤压模具处于高温挤压变形过程中,由变形金属产生的大量变形热及模具与变形金属之间产生的摩擦热,直接传递给模具导致温度升高,为防止模具局部出现“过烧”现象,模具材料应具有良好的导热性能,能向外快速地散发热量。
(五)具有良好的热处理淬透性和可氮化性。
即模具材料在热处理过程中,应保证模具的强度、力学性能均匀一致。
同时,模具在使用过程中,可多次进行表面氮化处理,提高模具表面强度的耐磨性。
除此之外,模具材料还应具有良好的抗回火稳定性,良好的抗腐蚀性,较低的膨胀系数,良好的工艺制造性能,以及价格的合理性等。
在上述性能中,模具材料的高温强度、抗磨损、抗热疲劳、热处理淬透性及良好的工艺制造性能,是模具材料选择的首要条件。
二、热挤压模具材料与性能
热挤压模具材料,主要是在含碳量为0.3%~0.45%的钢中,添加W,Mo,V,Cr,Ni等合金元素的高合金亚共析钢。
添加上述合金元素,可提高模具的高温强度、耐热性、抗热磨损等性能。
目前,我国用于热挤压生产的模具材料,基本上:
是3Cr2W8V,4CrSMoSiVl等高温耐热钢。
对于3Cr2W8V模具钢,其特点是有较好的高温强度,但存在较高的脆性和热裂性,不适合用于挤压断面形状复杂的铝合金制品挤压模具。
4CrSMoSiVl(即H13)模具钢,是近年来国内外广泛用于热挤压铝合金等制品的一种模具材料,其特点是:
具有良好的抗疲劳性能和综合机械力学性能,同时又具有良好的热处理淬透性。
因此,在这套模具中的凸凹模我们选用4CrSMoSiVl(即H13)模具钢。
模柄40Cr
上模板:
45
下模板:
凹模压紧圈:
40Cr
凸模:
H13
凹模:
凸模压紧圈:
导柱:
20
导套:
第二节模具的设计
结合经验公式和DEFORM-3D优化分析的结果设计凸模和凹模的形状,计算凸模和凹模的尺寸。
一、凹模的设计与计算
凹模形状设计如图3--1
图3-1凹模
(1)凹模的内腔直径
D=De(1+λ)=64×
(1+1.4%)=64.9mm
De---挤压件外径
λ---热挤压见冷却时的收缩率;
取λ=1.2%~1.5%
(2)凹模底部外径D5
D5=(2.5~3.0)D
=(2.5~3.0)×
64.9=173.4mm
(3)D1=D