气相沉积法.docx
《气相沉积法.docx》由会员分享,可在线阅读,更多相关《气相沉积法.docx(13页珍藏版)》请在冰点文库上搜索。
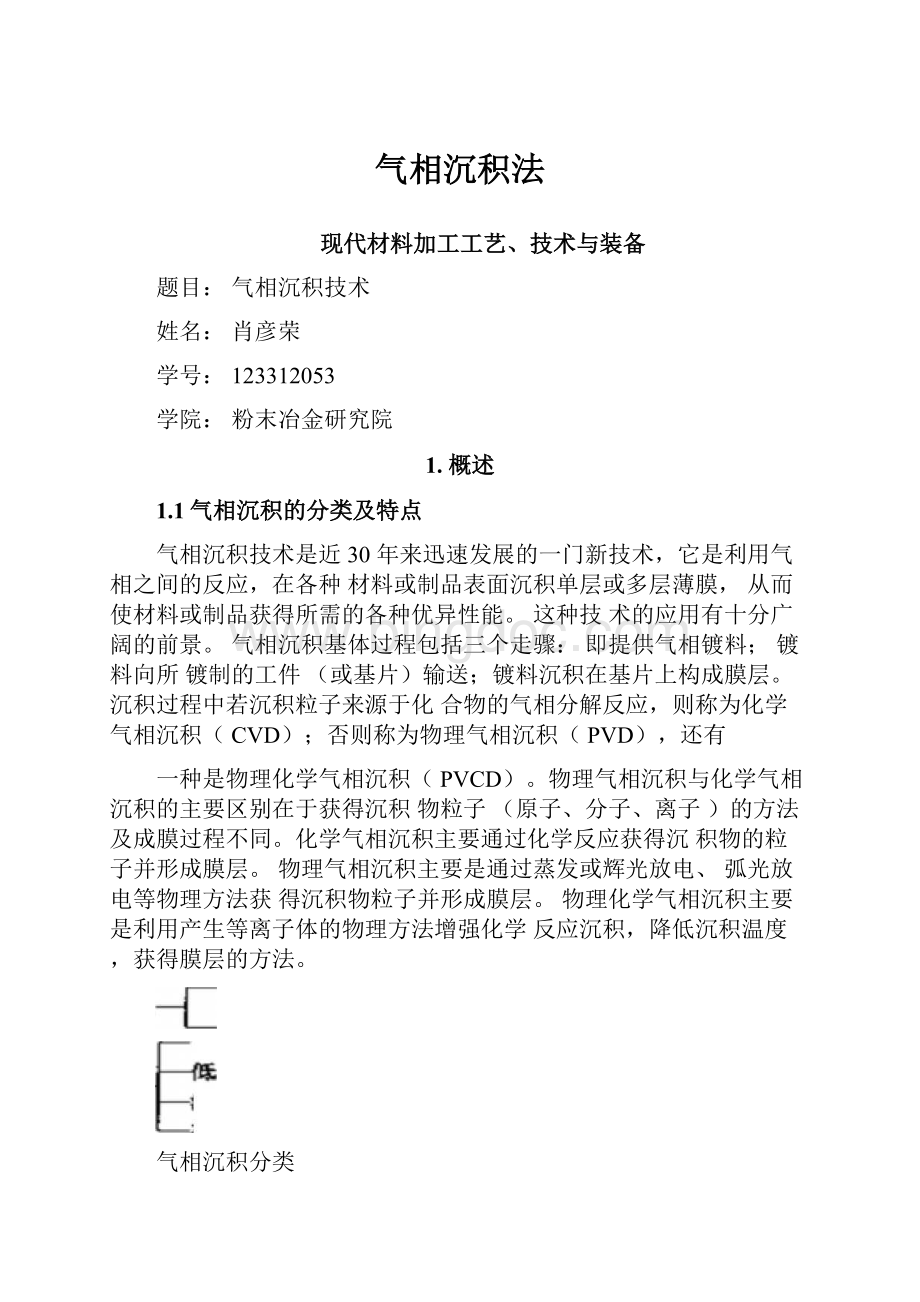
气相沉积法
现代材料加工工艺、技术与装备
题目:
气相沉积技术
姓名:
肖彦荣
学号:
123312053
学院:
粉末冶金研究院
1.概述
1.1气相沉积的分类及特点
气相沉积技术是近30年来迅速发展的一门新技术,它是利用气相之间的反应,在各种材料或制品表面沉积单层或多层薄膜,从而使材料或制品获得所需的各种优异性能。
这种技术的应用有十分广阔的前景。
气相沉积基体过程包括三个走骤:
即提供气相镀料;镀料向所镀制的工件(或基片)输送;镀料沉积在基片上构成膜层。
沉积过程中若沉积粒子来源于化合物的气相分解反应,则称为化学气相沉积(CVD);否则称为物理气相沉积(PVD),还有
一种是物理化学气相沉积(PVCD)。
物理气相沉积与化学气相沉积的主要区别在于获得沉积物粒子(原子、分子、离子)的方法及成膜过程不同。
化学气相沉积主要通过化学反应获得沉积物的粒子并形成膜层。
物理气相沉积主要是通过蒸发或辉光放电、弧光放电等物理方法获得沉积物粒子并形成膜层。
物理化学气相沉积主要是利用产生等离子体的物理方法增强化学反应沉积,降低沉积温度,获得膜层的方法。
气相沉积分类
气相沉积一般在密封系统的真空条件下进行,除常压化学气相沉积(NPLVD)系统的压强
约为一个大气压外,都是负压。
沉积气氛在真空室内反应,原料转化率高,可以节约贵重材料资源。
气相沉积可降低来自空气等的污染,所得到的沉积膜或材料纯度高。
能在较低温度下制备高熔点物质如各种超硬涂层。
适于制备多层复合膜、层状复合材料和梯度材料。
如在硬质合金刀具表面用CVD法沉积TiC-Al2O3-TiN的复合超硬膜;用PCVD法沉积Ti-TiC系的多
层梯度材料等。
1.2气相沉积的基本过程
气相物质的产生:
一是使镀料加热蒸发产生气相物质;二是用具有一定能量的离子轰击靶材(镀料),从靶材上轰击出镀料原子。
气相物质的输送:
在真空中进行,避免气体碰撞妨碍气相镀料到达基片。
气相物质的沉积:
气相物质在基片上沉积是一个凝聚过程。
根据凝聚条件的不同,可以形成非晶态膜、多晶膜或单晶膜。
2.物理气相沉积(PVD)
2.1概述
物理气相沉积(PhysicalVaporDeposition,PVD)技术表示在真空条件下,采用物理方法,将材料源——固体或液体表面气化成气态原子、分子或部分电离成离子,并通过低压气体(或等离子体)过程,在基体表面沉积具有某种特殊功能的薄膜的技术。
物理气相沉积的主要方
法有,真空蒸镀、溅射镀膜、电弧等离子体镀、离子镀膜,及分子束外延等。
发展到目前,物理气相沉积技术不仅可沉积金属膜、合金膜、还可以沉积化合物、陶瓷、半导体、聚合物膜等。
真空蒸镀基本原理是在真空条件下,使金属、金属合金或化合物蒸发,然后沉积在基体表面上,蒸发的方法常用电阻加热,高频感应加热,电子柬、激光束、离子束高能轰击镀料,使蒸发成气相,然后沉积在基体表面,历史上,真空蒸镀是PVD法中使用最早的技术。
溅射镀膜基本原理是充氩(Ar)气的真空条件下,使氩气进行辉光放电,这时氩(Ar)原子电离
成氩离子(Ar+),氩离子在电场力的作用下,加速轰击以镀料制作的阴极靶材,靶材会被溅射出来而沉积到工件表面。
如果采用直流辉光放电,称直流(Qc)溅射,射频(RF)辉光放电引起
的称射频溅射。
磁控(M)辉光放电引起的称磁控溅射。
电弧等离子体镀膜基本原理是在真空条件下,用引弧针引弧,使真空金壁(阳极)和镀材(阴极)之间进行弧光放电,阴极表面快速
移动着多个阴极弧斑,不断迅速蒸发甚至“异华”镀料,使之电离成以镀料为主要成分的电弧等离子体,并能迅速将镀料沉积于基体。
因为有多弧斑,所以也称多弧蒸发离化过程。
离子镀基本原理是在真空条件下,采用某种等离子体电离技术,使镀料原子部分电离成离子,同时产生许多高能量的中性原子,在被镀基体上加负偏压。
这样在深度负偏压的作用下,离子沉积于基体表面形成薄膜。
物理气相沉积技术基本原理可分三个工艺步骤:
(1)镀料的气化:
即使镀料蒸发,异华或被溅射,也就是通过镀料的气化源。
(2)镀料原子、分子或离子的迁移:
由气化源供出原子、分子或离子经过碰撞后,产生多种反应。
(3)镀料原子、分子或离子在基体上沉积。
物理气相沉积技术工艺过程简单,对环境改善,无污染,耗材少,成膜均匀致密,与基体的结合力强。
该技术广泛应用于航空航天、电子、光学、机械、建筑、轻工、冶金、材料等领域,可制备具有耐磨、耐腐饰、装饰、导电、绝缘、光导、压电、磁性、润滑、超导等
特性的膜层。
随着高科技及新兴工业发展,物理气相沉积技术出现了不少新的先进的亮点,如多弧离子镀与磁控溅射兼容技术,大型矩形长弧靶和溅射靶,非平衡磁控溅射靶,孪生靶技术,带状泡沫多弧沉积卷绕镀层技术,条状纤维织物卷绕镀层技术等,使用的镀层成套设备,向计算机全自动,大型化工业规模方向发展。
2.2真空蒸镀
2.2.1真空蒸镀原理
(1)真空蒸镀是在真空条件下,将镀料加热并蒸发,使大量的原子、分子气化并离开液体镀料或离开固体镀料表面(升华)。
(2)气态的原子、分子在真空中经过很少的碰撞迁移到基体。
(3)镀料原子、分子沉积在基体表面形成薄膜。
2.2.2蒸发源
将镀料加热到蒸发温度并使之气化,这种加热装置称为蒸发源。
最常用的蒸发源是电阻蒸发源和电子束蒸发源,特殊用途的蒸发源有高频感应加热、电弧加热、辐射加热、激光加热蒸发源等。
2.2.3真空蒸镀工艺实例
以塑料金属化为例,真空蒸镀工艺包括:
镀前处理、镀膜及后处理。
真空蒸镀的基本工艺过程如下:
(1)镀前处理,包括清洗镀件和预处理。
具体清洗方法有清洗剂清洗、化学溶剂清洗、超声波清洗和离子轰击清洗等。
具体预处理有除静电,涂底漆等。
(2)装炉,包括真空室清理及镀件挂具的清洗,蒸发源安装、调试、镀件褂卡。
(3)抽真空,一般先粗抽至6.6Pa以上,更早打开扩散泵的前级维持真空泵,加热扩散泵,待预热足够后,打开高阀,用扩散泵抽至6×10-3Pa半底真空度。
(4)烘烤,将镀件烘烤加热到所需温度。
(5)离子轰击,真空度一般在10Pa~10-1Pa,离子轰击电压200V~1kV负高压,离击时间为5min~30min,
(6)预熔,调整电流使镀料预熔,调整电流使镀料预熔,除气1min~2min。
(7)蒸发沉积,根据要求调整蒸发电流,直到所需沉积时间结束。
(8)冷却,镀件在真空室内冷却到一定温度。
(9)出炉,.取件后,关闭真空室,抽真空至l×l0-1Pa,扩散泵冷却到允许温度,才可关闭维持泵和冷却水。
(10)后处理,涂面漆。
2.3溅射镀膜
溅射镀膜是指在真空条件下,利用获得功能的粒子轰击靶材料表面,使靶材表面原子获得足够的能量而逃逸的过程称为溅射。
被溅射的靶材沉积到基材表面,就称作溅射镀膜。
溅射镀膜中的入射离子,一般采用辉光放电获得,在l0-2Pa~10Pa范围,所以溅射出来的粒子在飞向基体过程中,易和真空室中的气体分子发生碰撞,使运动方向随机,沉积的膜易于均匀。
近年发展起来的规模性磁控溅射镀膜,沉积速率较高,工艺重复性好,便于自动化,已适当于进行大型建筑装饰镀膜,及工业材料的功能性镀膜,及TGN-JR型用多弧或磁控溅射
2.4电弧蒸发和电弧等离子体镀膜
这里指的是PVD领域通常采用的冷阴极电弧蒸发,以固体镀料作为阴极,采用水冷、使冷阴极表面形成许多亮斑,即阴极弧斑。
弧斑就是电弧在阴极附近的弧根。
在极小空间的电流密度极高,弧斑尺寸极小,估计约为1μm~100μm,电流密度高达l05A/cm2~107A/cm2。
每个弧斑存在极短时间,爆发性地蒸发离化阴极改正点处的镀料,蒸发离化后的金属离子,在阴极表面也会产生新的弧斑,许多弧斑不断产生和消失,所以又称多弧蒸发。
最早设计的等离子体加速器型多弧蒸发离化源,是在阴极背后配置磁场,使蒸发后的离子获得霍尔(hall)加速效应,有利于离子增大能量轰击量体,采用这种电弧蒸发离化源镀膜,离化率较高,所以又称为电弧等离子体镀膜。
由于镀料的蒸发离化靠电弧,所以属于区别于第二节,第三节所述的蒸发手段。
2.5离子镀
离子镀技术最早在1963年由D.M.Mattox提出,1972年,Bunshah&Juntz推出活性反应蒸发离子镀(AREIP),沉积TiN,TiC等超硬膜,1972年Moley&Smith发展完善了空心热阴极离子镀,l973年又发展出射频离子镀(RFIP)。
20世纪80年代,又发展出磁控溅射离子镀(MSIP)和多弧离子镀(MAIP)。
2.5.1离子镀
离子镀的基本特点是采用某种方法(如电子束蒸发磁控溅射,或多弧蒸发离化等)使中性粒子电离成离子和电子,在基体上必须施加负偏压,从而使离子对基体产生轰击,适当降低负偏压后,使离子进而沉积于基体成膜。
此时如通入CO2,N2等反应气体,便可在工件表
面获得TiC,TiN覆盖层,硬度高达2000HV。
离子镀的重要特点是沉积温度只有500℃左右,
且覆盖层附着力强,适用于高速钢工具,热锻模等。
离子镀的优点如下:
①膜层和基体结
合力强。
②膜层均匀,致密。
③在负偏压作用下绕镀性好。
④无污染。
⑤多种基体材料均适合于离子镀。
2.5.2反应性离子镀
如果采用电子束蒸发源蒸发,在坩埚上方加20V~100V的正偏压。
在真空室中导人反
应性气体。
如N2、02、C2H2、CH4等代替Ar,或混入Ar,电子束中的高能电子(几千至几万电子伏特),不仅使镀料熔化蒸发,而且能在熔化的镀料表面激励出二次电子,这些二次电子在上方正偏压作用下加速,与镀料蒸发中性粒子发生碰撞而电离成离子,在工件表面发生离化反应,从而获得氧化物(如Te02:
Si02、Al203、Zn0、Sn02、Cr203、Zr02、In02等)。
其特点是沉积率高,工艺温度低。
2.5.3多弧离子镀
多弧离子镀又称作电弧离子镀,由于在阴极上有多个弧斑持续呈现,故称作“多弧”。
多弧离子镀的主要特点如下:
(1)阴极电弧蒸发离化源可从固体阴极直接产生等离子体,而
不产生熔池,所以可以任意方位布置,也可采用多个蒸发离化源。
(2)镀料的离化率高,一般达60%~90%,显著提高与基体的结合力改善膜层的性能。
(3)沉积速率高,改善镀膜的效率。
(4)设备结构简单,弧电源工作在低电压大电流工况,工作较为安全。
英文指"PhysicalVaporDeposition"简称PVD.是镀膜行业常用的术语.
PVD(物理气相沉积)镀膜技术主要分为三类,真空蒸发镀膜、真空溅射镀和真空离子镀膜。
对应于PVD技术的三个分类,相应的真空镀膜设备也就有真空蒸发镀膜机、真空溅射镀膜机和真空离子镀膜机这三种。
近十多年来,真空离子镀膜技术的发展是最快的,它已经成为当今最先进的表面处理方式之一。
我们通常所说的PVD镀膜,指的就是真空离子镀膜;通常所说的PVD镀膜机,指
的也就是真空离子镀膜机。
物理气相沉积(PVD)是通过蒸发,电离或溅射等过程,产生金属粒子并与反应气体反应形成化合物沉积在工件表面。
物理气象沉积方法有真空镀,真空溅射和离子镀三种,目前应用较广的是离子镀。
3.化学气相沉积(CVD)
3.1基本原理
化学气相沉积法(ChemicalVaporDeposition(CVD))是通过气相或者在基板表面上的化学反应,在基板上形成薄膜。
化学气相沉积方法实际上是化学反应方法,因此。
用CVD方法
可以制备各种物质的薄膜材料。
通过反应气体的组合可以制备各种组成的薄膜,也可以制备具有完全新的结构和组成的薄膜材料,而且即使是高熔点物质也可以在很低的温度下制备。
化学气相沉积方法和物理气相沉积的主要区别在于,CVD方法伴随着某种化学反应过程:
3.2CVD的分类
CVD技术根据反应类型或者压力可分为:
(1)低压CVD(LPCVD)
(2)常压CVD(APCVD)
(3)亚常压CVD(SACVD)
(4)超高真空CVD(UHCVD)
(5)等离子体增强CVD(PECVD)
(6)高密度等离子体CVD(HDPCVD)
(7)快热CVD(RTCVD)
(8)金属有机物CVD(MOCVD)
3.3反应形式
用化学气相沉积法可以制备各种薄膜材料、包括单元素物、化合物、氧化物、氮化物、碳化物等。
采用各种反应形式,选择适当的制备条件——基板温度、气体组成、浓度和压强、可以得到具有各种性质的薄膜构料。
化学气相沉积的化学反应形式主要有热分解反应、氢还原反应、金属还原反应、基板还原反应、化学输运反应、氧化反应、加水分解反应、等离子体和激光激发反应等。
3.4反应参数
用化学气相沉积方法制备薄膜材料时,为了合成出优质的薄膜材料,必须控制好反应气体组成、工作气压、基板温度、气体流量以及原料气体的纯度等。
原料应选用室温下的气体或者具有很高蒸气压的固体和液体。
如果在室温下得不到很高的蒸汽压,可进行加热;若在空温下蒸气压过高。
可以进行水冷。
常用的原料是氢化物、卤化物、有机金属化合物、或者使用它们和氧化剂、还原剂的混合气体。
气体的组成比对提高CVD膜的质量和均匀性相当重要。
在单质金属和硅薄膜的制备过中,浓度和生长速度关系密切;制备化合物薄膜时,气体组成和薄膜组成有直接关系;制备氧化物和氮化物薄膜时,一般采用大于化学当量比的氧和NH3的浓度;采用卤族化合物的氢的还原反应制备簿膜时由于这种反应为可逆反应,因此必须适当控制氢的浓度,防止可逆反应的发生。
CVD各种化学反应是在封管、开管或者减压条件下进行的。
封管法适合于化学输运反应,开管法是在大气压下供应反应气体的方法,利用减压法可以制备均匀的薄膜。
控制CVD反应的最重要的参数是温度。
因此,用CVD法制备薄膜时一定要首先控制好温度
3.5CVD反应过程
CVD反应是在基板表面和气相中发生的各种反应的组合,其反应过程和所用的装置结构、
原料种类以及膜的种类有关。
近年来,根据对反应气体和排出气体的光谱以及其他方而分析,对CVD反应过程有了比较明确的了解。
CVD反应过程为:
反应气体到达基板,反应气体分子吸附在基板表面,在基板表面发生化学反应、成核。
生成物脱离基板表面。
生成物在基板表面扩散等。
3.6CVD装置
一般来讲,CVD装置往往包括以下几个基本部分:
(1)反应气体和载气的供给和计量装置;
(2)必要的加热和冷却系统;(3)反应产物气体的排出装置或真空系统。
如同在物理气相沉积时的情形一样。
针对不同的薄膜材料和使用目的。
化学气相沉积装置可以具有各种不同的形式。
其分类的方法可以是按照沉积过程中的温度(低温、高温)、压
力(常压、低压)、加热方式(冷壁、热壁式)等。
并且,在CVD装置中也可以辅助以各种物理手段,如等离子体或热蒸发技术等。
在低压化学气相沉积过程进行的同时,利用辉光放电等离子体对沉积过程施加影响的技术称为等离子体辅助化学气相沉积(PECVD技)术。
从这种意义上来讲,传统的CVD技术依赖于较高的衬底温度实现气相物质间的化学反应与薄膜的沉积,因而可以称之为热CVD技术
3.7特点
1)在中温或高温下,通过气态的初始化合物之间的气相化学反应而沉积固体。
2)可以在大气压(常压)或者低于大气压下(低压)进行沉积。
一般来说低压效果
要好些。
(3)采用等离子和激光辅助技术可以显著地促进化学反应,使沉积可在较低的温度下进行。
(4)镀层的化学成分可以改变,从而获得梯度沉积物或者得到混合镀层。
(5)可以控制镀层的密度和纯度。
(6)绕镀性好,可在复杂形状的基体上以及颗料材料上镀制。
(7)气流条件通常是层流的,在基体表面形成厚的边界层。
(8)沉积层通常具有柱状晶结构,不耐弯曲。
但通过各种技术对化学反应进行气相扰动,可以得到细晶粒的等轴沉积层。
(9)可以形成多种金属、合金、陶瓷和化合物镀层。
3.8CVD的方法
3.8.1等离子体化学气相沉积(PCVD)借助外加电场的作用引起放电,使原料气体变成等离子体状态,成为化学上活泼的激发分子、原子、离子和原子团等,促进基材表面化学反应形成薄膜的方法。
PCVD法可分为:
直流法(DCPCVD)、射频法(RFPCVD和)微波法(MWPCVD)等。
直流PCVD技术的特点是沉积温度低-如PCVD沉积TiN膜,成膜温度仅为500℃,而传统的CVD为1000℃左右,因此可在不耐高温的材料上沉积成膜。
膜与基材结合强度高-这是由于离子具有溅射清洁表面和轰击效应。
成膜速度快。
可制膜层材料的范围广-由于等离子体的激发,使得难以发生反应的成膜材料沉积成膜。
其缺点是不能沉积非金属基体或膜。
3.8.2金属有机化合物化学气相沉积(MOCVD)金属有机化合物是一类含有碳-氢金属键的物质,在室温下呈液态,并有较高的蒸气压和较低的热分解温度(金属乙酰丙酮)。
通过载气把气体发生器中气化的金属有机化合物输运到反应室中,被加热的基片对金属有机化合物的热分解产生催化作用,从而在其上产生薄膜。
MOCVD的技术特点是沉积温度低,可沉积单晶、多晶、非晶的多层和超薄层、原子层薄膜,可以大规模、低成本制备复杂组分的薄膜和化合物半导体材料;可在蓝宝石、尖晶石基材表面上实现外延生长;增加一种MO源可以增加沉积材料中的一种组分或一种化合物;使用两
种或更多MO源可以沉积二元或多元、二层或多层的表面材料,工艺的通用性较广。
MOCVD的缺点是:
1)沉积速度较慢,仅适宜于沉积微米级的表面层;2)原料的毒性较大,设备的
密封性、可靠性要好,并谨慎管理和操作。
3.8.3激光诱导化学气相沉积(LCVD)
LCVD是一种在化学气相沉积过程中利用激光束的光子能量激发和促进化学反应的薄膜沉积方法。
LCVD所用的设备是在常规的CVD设备的基础上添加激光器、光路系统及激光功率测量装置。
先将基片预置于充满活性气体的反应室中,然后采用激光束照射基板,诱导化学反应发生并沉积出薄膜的过程。
LCVD技术的特点是LCVD与常规的CVD相比,可大大降低基材的温度,防止基材中杂质分布受到破坏,可在不能承受高温的基材上合成薄膜。
例如用一般CVD制备SiO2、Si3N4、AlN薄膜时基材需加热到800~1200℃,而用LCVD则需380~450℃。
LCVD与PCVD相比,可以避免高能粒子轰击在薄膜中造成的损伤。
4.气相沉积的应用
1.耐磨膜:
高速钢刀具(滚齿刀、插齿刀、钻头、扩孔钻、拉刀、铣刀、铰刀、车刀等)沉积TiN,成型加工模具沉积TiC,硬质合金刀片表面沉积TiN、A12O3等;
2.润滑膜:
近年来开发出用A1、Cr、Co、Ni、Pt、Au、Ag、Ta、W、Cu等金属与MoS2共沉积。
例如用90%MoS2加5%Au制成复合靶可得到MoS2-Au共沉积膜,摩擦系数比MoS2膜小而稳定,磨损率低,抗潮能力远优于单一MoS2膜。
3.防蚀膜:
气相沉积A1、Cr、Fe、Pt、Au、Ni以及多层金属已广泛用于腐蚀防护。
离子镀铝处理飞机上螺钉、衬套、飞机的起落架及机翼蒙皮等零件。
5.PVD和CVD对比
CVD的工艺温度高,但高温下得到的镀层结合强度要更好些。
CVD镀层比各种PVD镀层略厚一些,且镀层的表面略比基体的表面粗糙些。
CVD反应发生在低真空的气态环境中,具有很好的绕镀性,薄膜均匀性好。
CVD需严格控制工艺条件,否则,系统中的反应气体或反应产物的腐蚀作用会使基体脆化,高温会使TiN镀层的晶粒粗大。
CVD法所获得的薄膜内应力较低,可镀覆较厚的膜层。
CVD和PVD两种工艺的成本,最初的设备投资PVD是CVD的3~4倍,而PVD工艺的
生产周期是CVD的1/10。
在CVD的一个操作循环中,可以对各式各样的工件进行处理,而PVD就受到很大限制。
综合比较,在两种工艺都可用的范围内,采用PVD要比CVD代价高。
CVD和PVD两种工艺的操作运行安全问题,PCD是一种完全没有污染的“绿色工程”。
而CVD的反应气体、反应尾气都可能具有一定的腐蚀性、可燃性及毒性,反应尾气中还可能有粉末状以及碎片状的物质,因此对设备、环境、操作人员都必须采取一定的措施加以防范。
6.总结
物理气相沉积技术工艺过程简单,对环境改善,无污染,耗材少,成膜均匀致密,与基体的结合力强。
该技术广泛应用于航空航天、电子、光学、机械、建筑、轻工、冶金、材料等领域,可制备具有耐磨、耐腐饰、装饰、导电、绝缘、光导、压电、磁性、润滑、超导等特性的膜层。
随着高科技及新兴工业发展,物理气相沉积技术出现了不少新的先进的亮点,如多弧离子镀与磁控溅射兼容技术,大型矩形长弧靶和溅射靶,非平衡磁控溅射靶,孪生靶技术,带状泡沫多弧沉积卷绕镀层技术,条状纤维织物卷绕镀层技术等,使用的镀层成套设备,向计算机全自动,大型化工业规模方向发展。
化学气相沉积是近几十年发展起来的制备无机材料的新技术。
化学气相淀积法已经广泛用于提纯物质、研制新晶体、淀积各种单晶、多晶或玻璃态无机薄膜材料。
这些材料可以是氧化物、硫化物、氮化物、碳化物,也可以是III-V、II-IV、IV-VI族中的二元或多元的元素间
化合物,而且它们的物理功能可以通过气相掺杂的淀积过程精确控制。
目前,化学气相淀积已成为无机合成化学的一个新领域。