支座 铸造工艺课程设计.docx
《支座 铸造工艺课程设计.docx》由会员分享,可在线阅读,更多相关《支座 铸造工艺课程设计.docx(25页珍藏版)》请在冰点文库上搜索。
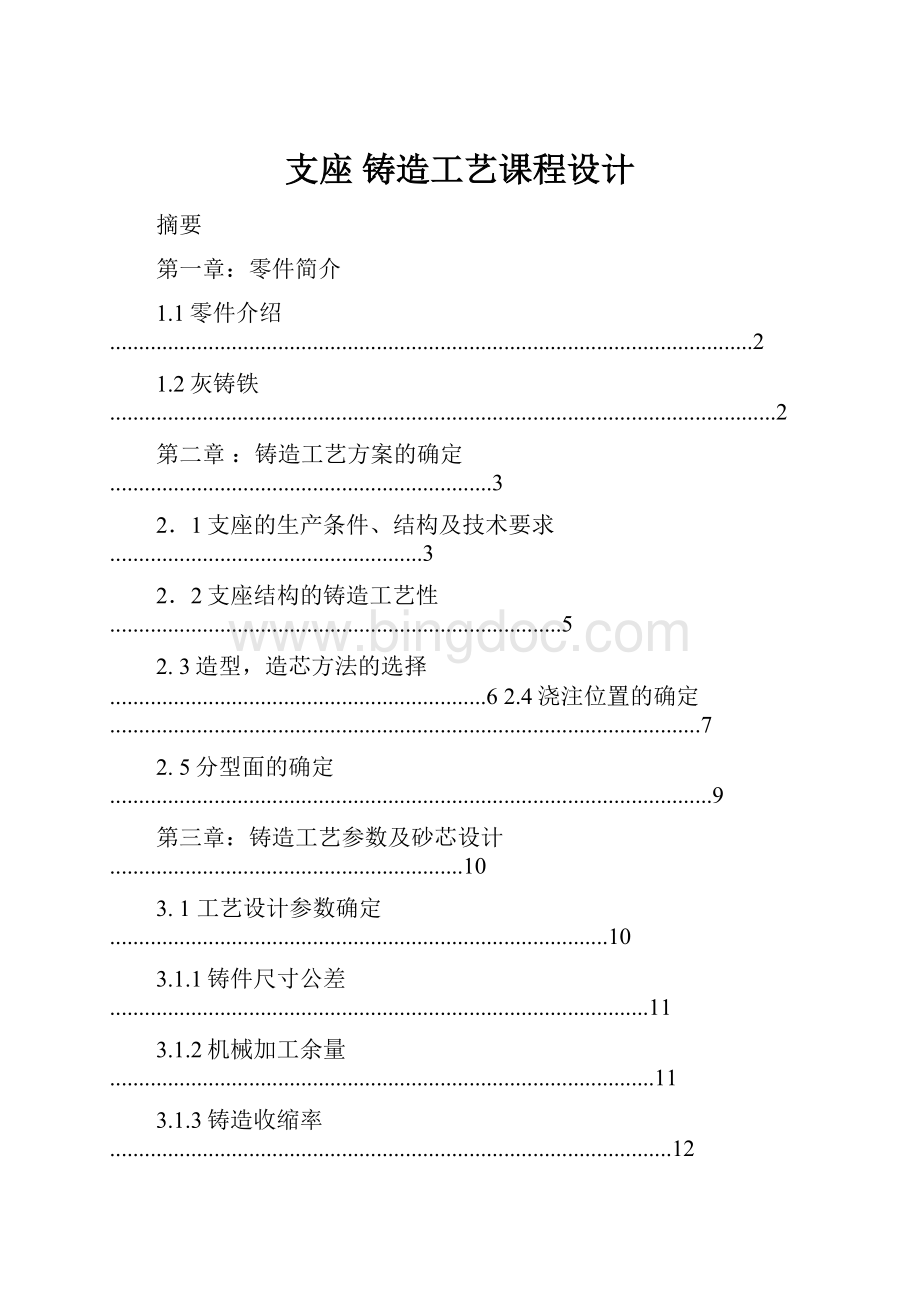
支座铸造工艺课程设计
摘要
第一章:
零件简介
1.1零件介绍...............................................................................................................2
1.2灰铸铁...................................................................................................................2
第二章:
铸造工艺方案的确定..................................................................3
2.1支座的生产条件、结构及技术要求......................................................3
2.2支座结构的铸造工艺性..............................................................................5
2.3造型,造芯方法的选择.................................................................62.4浇注位置的确定......................................................................................................7
2.5分型面的确定........................................................................................................9
第三章:
铸造工艺参数及砂芯设计.............................................................10
3.1工艺设计参数确定......................................................................................10
3.1.1铸件尺寸公差.............................................................................................11
3.1.2机械加工余量..............................................................................................11
3.1.3铸造收缩率.................................................................................................12
3.1.4起模斜度.......................................................................................................12
3.1.5最小铸出孔和槽........................................................................................13
3.1.6铸件在砂型内的冷却时间......................................................................14
3.1.7铸件重量公差.............................................................................................14
3.1.8工艺补正量..................................................................................................14
3.1.9分型负数......................................................................................................14
3.1.10反变形量...........................................................................................14
3.1.11非加工壁厚负余量................................................................................14
3.2砂芯设计.........................................................................................................15
3.2.1芯头的设计......................................................................................................16
3.2.2砂芯的定位结构..............................................................................................16
3.2.3压环、防压环和集砂槽芯头结构...............................................................16
3.2.4芯骨设计.........................................................................................................16
3.2.5砂芯的排气....................................................................................................16
3.2.6砂芯负数.......................................................................................................16
第四章:
浇注系统及冒口、冷铁、出气孔等设计
4.1浇注系...........................................................................................................17
4.1.1选择浇注系统类型......................................................................................17
4.1.2计算浇注时间并核算金属上升速度.........................................................17
4.1.3计算阻流截面积..........................................................................................17
4.1.4确定浇口比..................................................................................................18
4.1.5计算内浇道截面积......................................................................................18
4.1.6计算横浇道截面积.......................................................................................18
4.1.7计算直浇道截面积........................................................................................19
4.1.8浇口窝的设计................................................................................................20
4.1.9浇口杯的设计.................................................................................................20
4.2冒口的设计...........................................20
4.3冷铁的设计.....................................................................................................21.
4.4出气孔的设计...............................................................................................21
第五章砂型铸造设备选用......................................................................21
5.1造型工部设备选用.................................................................................21
5.2制芯工部设备选用..................................................................................21
5.3清理工部设备选用..................................................................................21
设计心得.............................................................................................................22
参考文献............................................................................................................22
1.1零件介绍
支座是指用以支承容器或设备的重量,并使其固定于一定位置的支承部件。
还要承受操作时的振动与地震载荷。
如室外的塔器还要承受风载荷。
支座的结构型式主要由容器自身的型式和支座的形状来决定,通常分为立式支座、卧式支座和球形容器支座三类。
立式支座又分为悬挂式支座、支承式支座、支承式支脚,支承式支腿、裙式支座等;卧式支座分鞍式支座、圈座和支腿式支座等;球形容器支座分支柱式、裙式、半埋式和V形支承等。
1.2灰铸铁
灰铸铁的组织和性能
[组织]:
可看成是碳钢的基体加片状石墨。
按基体组织的不同灰铸铁分为三类:
铁素体基体灰铸铁;铁素体一珠光体基体灰铸铁;珠光体基体灰铸铁。
[力学性能]:
灰铸铁的力学性能与基体的组织和石墨的形态有关。
灰铸铁中的片状石墨对基体的割裂严重,在石墨尖角处易造成应力集中,使灰铸铁的抗拉强度、塑性和韧性远低于钢,但抗压强度与钢相当,也是常用铸铁件中力学性能最差的铸铁。
同时,基体组织对灰铸铁的力学性能也有一定的影响,铁素体基体灰铸铁的石墨片粗大,强度和硬度最低,故应用较少;珠光体基体灰铸铁的石墨片细小,有较高的强度和硬度,主要用来制造较重要铸件;铁素体一珠光体基体灰铸铁的石墨片较珠光体灰铸铁稍粗大,性能不如珠光体灰铸铁。
故工业上较多使用的是珠光体基体的灰铸铁。
[其他性能]:
良好的铸造性能、良好的减振性、良好的耐磨性能、良好的切削加工性能、低的缺口敏感性。
第二章铸造工艺方案的确定
2.1支座的生产条件、结构及技术要求
●产品生产性质——大批量生产
●零件材质——HT250
●零件的外型示意图如下图所示,支座的零件图如图2.2所示,支座的外形轮廓尺寸为260mm*260mm*240mm,主要壁厚30mm,最大壁厚50mm。
铸件除满足几何尺寸精度及材质方面的要求外,无其他特殊技术要求。
图2.1支座外型示意图
图2.2支座零件图
2.2支座结构的铸造工艺性
零件结构的铸造工艺性是指零件的结构应符合铸造生产的要求,易于保证铸件品质,简化铸件工艺过程和降低成本。
审查、分析应考虑如下几个方面:
1.铸件应有合适的壁厚,为了避免浇不到、冷隔等缺陷,铸件不应太薄。
2.铸件结构不应造成严重的收缩阻碍,注意薄壁过渡和圆角铸件薄厚壁的相接拐弯等厚度的壁与壁的各种交接,都应采取逐渐过渡和转变的形式,并应使用较大的圆角相连接,避免因应力集中导致裂纹缺陷。
3.铸件内壁应薄于外壁铸件的内壁和肋等,散热条件较差,应薄于外壁,以使内、外壁能均匀地冷却,减轻内应力和防止裂纹。
4.壁厚力求均匀,减少肥厚部分,防止形成热节。
5.利于补缩和实现顺序凝固。
6.防止铸件翘曲变形。
7.避免浇注位置上有水平的大平面结构。
对于支座的铸造工艺性审查、分析如下:
(1)支座质量的估算
经计算零件的V=0.25*3.14*(0.26*0.26*0.1+0.16*0.16*0.14-0.1*0.1*0.24)约为0.006236M^3.灰铸铁的密度为6.9
一箱一件质量为m=V*6900=40.58kg查《铸造技术与应用案例》PAGE172表5.3-2得该铸件为一中型铸件。
支座大批量生产的工艺出品率约为85%,可估计铸型中铁水总重量G
G=40.58/85%≈50.621kg.
支座铸件的轮廓尺寸为270mm*245mm*245mm。
砂型铸造条件下该轮廓尺寸允许的最小壁厚查《铸工实用技术手册》PAGE30表2.1-1得:
最小允许壁厚为4~5mm。
而设计支座的最小壁厚为39mm。
符合要求。
支座设计壁厚较为均匀,只在顶部有个环形的凸台,壁厚为59mm,但该处距离较短,笔者在此用明顶冒口来补缩。
2.3造型,造芯方法的选择
支座的轮廓尺寸为260mm*260mm*240,铸件尺寸较小,属于中型零件且要大批量生产。
采用湿型粘土砂造型灵活性大,生产率高,生产周期短,便于组织流水生产,易于实现机械化和自动化,材料成本低,节省烘干设备、燃料、电力等,还可延长砂箱使用寿命。
因此,采用湿型粘土砂机器造型,模样采用木模是合理的。
在造芯用料及方法选择中,如用粘土砂制作砂芯原料成本较低,但是烘干后容易产生裂纹,容易变形。
在大批量生产的条件下,由于需要提高造芯效率,且常要求砂芯具有高的尺寸精度,以增加其强度及保证铸件质量。
选择使用射芯工艺生产砂芯。
采用热芯盒制芯工艺热芯盒法制芯,是用液态固性树脂粘结剂和催化剂制成的一种芯砂,填入加热到一定的芯盒内,贴近芯盒表面的砂芯受热,其粘结剂在很短的时间内硬化。
而且只要砂芯表层有数毫米的硬壳即可自芯取出,中心部分的砂芯利用余热可自行硬化。
2.4浇注位置的确定
铸件的浇注位置是指浇注时铸件在型内所处的状态和位置。
确定浇注位置是铸造工艺设计及铸件缺陷控制中重要的环节,关系到铸件的内在质量,铸件的尺寸精度及造型工艺过程的难易程度。
初步对支座对浇注位置的确定有:
方案一如图2.3、方案二图2.4
图2.3浇注位置确定方案一示意图
图2.4浇注位置确定方案二示意图
确定浇注位置应注意以下原则:
1.铸件的重要部分应尽量置于下部
2.重要加工面应朝下或直立状态
3.使铸件的答平面朝下,避免夹砂结疤内缺陷
4.应保证铸件能充满
5.应有利于铸件的补缩
6.避免用吊砂,吊芯或悬臂式砂芯,便于下芯,合箱及检验
对于方案一如图2.3进行综合分析如下:
1.铸件的内表面(如图2.3所示)为重要加工面,而该铸件较高冲击力较大,充型不平稳,容易发生飞溅,氧化和卷入气体的现象,使铸件产生砂眼,冷豆,气孔和夹渣等缺陷。
2.对于方案二如图2.4进行综合分析如下:
方案二采用底注式浇注系统是内浇道开设在型腔底部的浇注系统。
其优点是金属液充型平稳,避免了金属液冲击型芯,飞溅和氧化及由此引起的铸件缺陷;型内气体易于逐渐排除,整个浇注系统充满较快。
利于横浇道撇渣。
铸件的重要加工面侧面位于侧立面,比较光洁,产生气孔、非金属夹杂物等缺陷的可能性小。
综合比较,方案二更加科学可行。
2.5分型面的确定
分型面是指两半铸型相互接触的表面。
分型面的优劣在很大程度上影响铸件的尺寸精度、成本和生产率。
初步对支座进行分型有:
方案一,二,三如下图所示
图2.5分型面确定方案
而选择分型面时应注意一下原则:
1.应使铸件全部或大部分置于同一半型内
2.应尽量减少分型面的数目
3.分型面应尽量选用平面
4.便于下芯、合箱和检测
5.不使砂箱过高
6.受力件的分型面的选择不应削弱铸件结构强度
7.注意减轻铸件清理和机械加工量
对方案二如图2.5进行综合分析如下:
1.铸件没有能尽可能的位于同一半型内,这样会因为合箱对准误差使铸件产生偏错。
也有可能因为合箱不严在垂直面上增加铸件尺寸。
2.砂芯不能全部位于下半型内。
3.上箱难于取出模样。
对方案一如图2.5进行综合分析如下:
1.上箱难于取出模样。
对方案三如图2.5进行综合分析如下:
1.铸件位于同一半型内,这样不会因为合箱对准误差使铸件产生偏错。
也不会因为合箱不严在垂直面上增加铸件尺寸。
4.砂芯全部位于下半型内。
5.上箱易于于取出模样。
此方案较之方案一与方案二更加科学可行。
第三章铸造工艺参数及砂芯设计
3.1工艺设计参数确定
铸造工艺设计及铸件缺陷控制参数通常是指铸型工艺设计时需要确定的某些数据,这些工艺数据一般都与模样及芯盒尺寸有关,及与铸件的精度有密切关系,同时也与造型、制芯、下芯及合箱的工艺过程有关。
这些工艺数据主要是指加工余量、起模斜度、铸造收缩率、最小铸出孔、型芯头尺寸、铸造圆角等。
工艺参数选取的准确、合适,才能保证铸件尺寸精确,使造型、制芯、下芯及合箱方便,提高生产率,降低成本。
3.1.1铸件尺寸公差
铸件尺寸公差是指铸件公称尺寸的两个允许的极限尺寸之差。
在两个允许极限尺寸之内,铸件可满足机械加工,装配,和使用要求。
支座为砂型铸造机器造型大批量生产,由《铸造工艺设计及铸件缺陷控制》查表3-5得:
支座的尺寸公差为CT8~12级,取CT9级。
支座的轮廓尺寸为260mm*260mm*240,由《铸造工艺设计及铸件缺陷控制》查表3-4得:
支座尺寸公差数值为2.8mm。
3.1.2机械加工余量
机械加工余量是铸件为了保证其加工面尺寸和零件精度,应有加工余量,即在铸件工艺设计时预先增加的,而后在机械加工时又被切去的金属层厚度。
支座为砂型铸造机器造型大批量生产,由《铸造工艺设计及铸件缺陷控制》查表3-8得:
支座的加工余量为E~G级,取F级。
支座的轮廓尺寸为260mm*260mm*240,由《铸造工艺设计及铸件缺陷控制》查表3-7得:
支座加工余量数值为2.5mm.但在分型面及浇注系统设置中,不得已将重要加工面底面朝上放置,这样使其容易产生气孔、非金属夹杂物等缺陷,所以将采取适当加大加工余量的方法使其在加工后不出现缺陷。
将侧面的加工余量调整为4mm,将顶面和底面的加工余量调整为5mm。
如下图所示
3.1.3铸造收缩率
铸造收缩率又称铸件线收缩率,用模样与铸件的长度差除以模样长度的百分比表示:
ε=[(L1-L2)/L1]*100%
ε—铸造收缩率
L1—模样长度
L2—铸件长度
支座受阻收缩率由《铸造工艺设计及铸件缺陷控制》查表3-1得:
取受阻收缩率为0.9%。
3.1.4起模斜度
为了方便起模,在模样、芯盒的出模方向留有一定斜度,以免损坏砂型或砂芯。
这个斜度,称为起模斜度。
起模斜度应在铸件上没有结构斜度的,垂直于分型面的表面上应用。
初步设计的起模斜度如下:
外型模的高100的起模斜度由《铸造工艺设计及铸件缺陷控制》查表3-13得:
粘土砂造型外表面起模斜度为а=0°30',a=1.4mm。
外型模的高140mm的起模斜度由《铸造工艺设计及铸件缺陷控制》查表3-13得:
粘土砂造型外表面起模斜度为а=0°25',a=1.8mm。
3.1.5最小铸出孔和槽
零件上的孔、槽、台阶等,究竟是铸出来好还是靠机械加工出来好,这应该从品质及经济角度等方面考虑。
一般来说,较大的孔、槽等应该铸出来,以便节约金属和加工工时,同时还可以避免铸件局部过厚所造成热节,提高铸件质量。
较小的孔、槽或则铸件壁很厚则不易铸出孔,直接依靠加工反而方便。
根据支座的轮廓尺寸260mm*260mm*240由《铸造工艺设计及铸件缺陷控制》查表3-11得:
最小铸出孔约为15-30mm
支座的孔Φ60如图3.2所示)考虑加工余量后直径为52mm,厚度为45mm。
该孔直径比较大,高径比也不大,则应该铸出。
支座的孔Φ100(如图3.2所示)考虑加工余量后直径为92,厚度为40mm。
该孔直径较大,高径比较大,应该铸出。
支座的孔Φ200如图3.2所示)考虑加工余量后直径为192mm,厚度为40mm。
该孔直径比较大,高径比也比较大,则应该铸出。
支座的直径为Φ12和Φ6(如图3.2所示)的螺纹孔明显比最小铸出孔径小,机械加工比较经济,所以不铸出。
3.1.6铸件在砂型内的冷却时间
铸件在砂型内的冷却时间短,容易产生变形,裂纹等缺陷。
为使铸件在出型时有足够的强度和韧性,铸件在砂型内应有足够的冷却时间。
支座的冷却时间由《铸造工艺设计及铸件缺陷控制》查表1-25得:
冷却时间为30~60min。
3.1.7铸件重量公差
铸件重量公差是以占铸件公称重量的百分比表示的铸件重量变动的允许范围。
尺寸公差为CT9级。
查表4-3《铸造技术与应用案由例》得:
支座的重量公差为MT9级。
得重量公差为8kg。
3.1.8工艺补正量
在单件小批量生产中,由于选用的缩尺与铸件的实际收缩率不符,或由于铸件产生了变形等原因,使得加工后的铸件某些部分的壁厚小于图样要求尺寸,严重时会因强度太弱而报废。
因此工艺需要在铸件相应的非加工壁厚上增加层厚度称为工艺补正量。
但支座在大批量生产前的小批量试产过程中将进行调整,所以设计中不考虑工艺补正量。
3.1.9分型负数