脱硫岗位培训教材.docx
《脱硫岗位培训教材.docx》由会员分享,可在线阅读,更多相关《脱硫岗位培训教材.docx(72页珍藏版)》请在冰点文库上搜索。
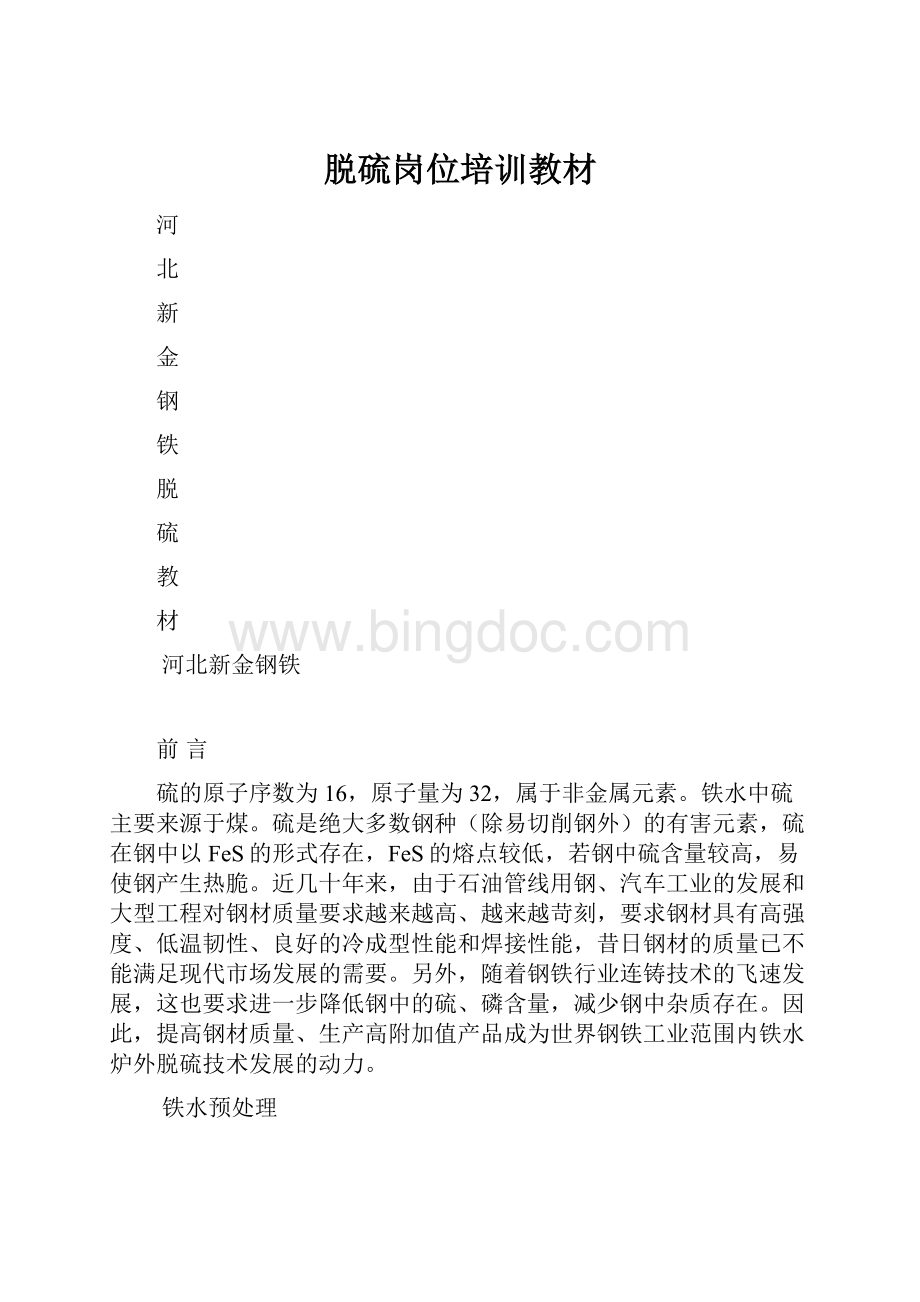
脱硫岗位培训教材
河
北
新
金
钢
铁
脱
硫
教
材
河北新金钢铁
前言
硫的原子序数为16,原子量为32,属于非金属元素。
铁水中硫主要来源于煤。
硫是绝大多数钢种(除易切削钢外)的有害元素,硫在钢中以FeS的形式存在,FeS的熔点较低,若钢中硫含量较高,易使钢产生热脆。
近几十年来,由于石油管线用钢、汽车工业的发展和大型工程对钢材质量要求越来越高、越来越苛刻,要求钢材具有高强度、低温韧性、良好的冷成型性能和焊接性能,昔日钢材的质量已不能满足现代市场发展的需要。
另外,随着钢铁行业连铸技术的飞速发展,这也要求进一步降低钢中的硫、磷含量,减少钢中杂质存在。
因此,提高钢材质量、生产高附加值产品成为世界钢铁工业范围内铁水炉外脱硫技术发展的动力。
铁水预处理
所谓铁水预处理是指高炉铁水在入炼钢转炉以前,为提高入炉铁水质量而进行的脱硫、脱磷、脱硅及提取铁水中有价元素(如提钒)等一系列冶金处理,称为铁水预处理。
铁水预处理能显著改善炼钢炉脱硫、脱磷的条件,降低非金属夹杂,提高钢的纯净度和钢材质量。
由于高炉和转炉的脱硫能力有一定限度,因而在现代钢铁企业中,炉外脱硫是决定钢水中最终硫含量的主要工艺环节,它可有效减轻高炉和炼钢炉的冶金负荷,实现生产过程的自动化和连续性,因而在钢铁工业得到广泛应用,现已成为现代钢铁企业优化工艺流程,提高产品质量必不可少的环节,是实现转炉少渣冶炼,提高钢材洁净度的必要条件。
其中,铁水炉外脱硫的基本原理是使用与硫的亲合力比铁与硫的亲合力大的元素或化合物,将硫化铁转化为更稳定的、极少溶解或完全不溶于铁液的硫化物,同时创造良好的动力学条件,以加速铁水中硫向反应区的扩散和扩大脱硫剂与铁水之间的反应面积,从而达到脱硫目的。
由于我国目前生铁质量离现代工业发展的要求还很远,生铁一级品(标准[S]≤0.03%)的质量比例低。
为了保证生铁脱硫的要求,高炉不得不采用保守的操作方法,即采用高炉温、高碱度、大渣量操作,导致焦比高、产量低,高炉高产低耗的目标难以实现。
即使铁水硫含量达到一级品的标准,对炼钢来说还是偏高,炼钢过程中还需进行脱硫处理,致使炼钢时渣量大、冶炼周期长、炼钢工序产量低、消耗高。
如果采用高炉铁水炉外脱硫处理技术,既可以减轻高炉的脱硫负担,又可以使炼钢工艺甩掉脱硫处理环节,实现高产低耗的目标。
例如,加拿大多米尼翁钢铁公司的对比实验表明,高炉渣碱度从1.2降低到1.06,能使焦比下降36kg/t.铁,生产率提高13%,成本大大下降;但是铁水平均硫含量从0.02%上升到0.043%,需要进行炉外处理。
此外,降低高炉渣碱度还有利于排除碱金属氧化物,有利于高炉的顺行和减少故障,另外,采用低硫铁水炼钢能减少石灰加入量和渣量约25kg/t.铁,能使铁的收得率提高约0.6个百分点。
由以上分析可知,采用铁水预脱疏工艺有以下优点:
a.铁水含硫量可以降低到超低含量,有利于转炉冶炼优质钢和特殊钢,有利于钢铁产品升级换代,生产出具有高附加值的优质钢材。
b.能保证炼钢吃精料,降低转炉炼钢的生产成本,提高生产力,节约炼钢能耗。
c.提高高炉的生产能力,高炉工序几乎可不考虑产品硫含量,使高炉的脱硫负担减轻,可降低炉渣碱度,减少渣量,减轻碱金属的危害,有利于冶炼低硅铁,使高炉稳定、顺行,降低焦比和节约能耗。
d.可有效地提高铁、钢、材系统的综合经济效益。
国内外铁水预处理脱硫技术的发展状况
国外发展状况
硫作为有害元素必须在精炼过程中加以去除。
在炼铁过程中去除硫要比在炼钢过程中容易得多。
因此,早期较为一致的看法是把去硫的任务尽量交给炼铁。
但在高炉中去硫要花较大的代价,意味着必须提高渣碱度,增加渣量,从而导致渣量增加。
而炼钢过程是个氧化过程,即便是脱除并不算多的硫,也要花费大力气,使指标受到影响。
基于以上这些原因,早在十八世纪末转炉底吹空气时代,就有人提出进行铁水炉外脱硫的设想。
不久便出现了转鼓脱硫法(Kalling)。
转鼓脱硫是通过绕水平轴线旋转的直筒炉体,使熔剂与铁水良好混合接触,可以在15min内脱除大约90%的硫。
然而,这种方法由于容积比太大(v/t=0.5m3/t),温降过大以及由于衬壁寿命等问题没有得到广泛采用。
六十年代中期又出现了以水平偏心摇动包体,实现铁水与脱硫剂混合来达到脱硫目的的摇包法脱硫(Shaking)。
此方法是靠水平偏心摇动,借助达到某一临界速度时所产生的海岸击浪现象,使脱硫剂与铁水达到良好接触而起到脱硫作用。
摇包法脱硫较之转鼓法有了一定的进展,其特点是变容器转动为容器摇动,且容积比也明显减少,降为0.25m3/t,因而温度损失变小,罐壁寿命也有所提高。
七十年代曾经在工业中得到应用。
处理包容一般在30t以下,最大的一个是日本洞岗的50t摇包。
转鼓和摇包都是属于容器运动法,这种方法动力消耗大,并且容量也受到一定的限制。
继摇包法脱硫出现不久,在联邦德国莱茵钢厂和日本广佃厂相继开发成功搅拌法脱硫装置。
这种方法的特点是无须容器运动,靠插入铁水内部的搅拌器,使铁水转动与脱硫剂混合接触,来实现脱硫的目的。
由容器运动法演变发展成搅拌法是铁水脱硫技术的一个很大进步。
搅拌法分为两种形式,即莱茵法和KR法。
两种方法的最大区别点是搅拌器的插入深度不同。
莱茵法搅拌器只是部分地插入铁水内部,通过搅拌使罐上部的铁水和脱硫剂形成涡流搅动,互相混合接触同时通过循环流动使整个包内铁水都能达到最佳脱硫区段以实现脱硫。
KR法是将搅拌器沉浸入到铁水内部而不是在铁水和脱硫剂之间的界面上,通过搅拌形成铁水运动旋涡使脱硫剂散开并混入铁水内部,加速脱硫过程。
由于搅拌法是利用机械搅拌作用使铁水与脱硫剂均匀混合达到脱硫的目的。
因此,脱硫剂利用率高,消耗较低。
据日本广佃厂经验,达到90%脱硫率的碳化钙消耗为3kg/t左右。
搅拌器的寿命可达到80—100炉,耐火材料消耗约0.3kg/t.铁水。
其缺点是设备复杂,处理前必须扒除铁水浮渣,所以存在脱硫后的二次扒渣,铁水温度损失大,一般要降低50℃左右,铁水罐寿命低。
基于这些缺点,搅拌法的推广在国内外都受到限制,我国除武钢引进了日本技术外,其余厂家都没有采用此法。
进入七十年代,由于喷射冶金的发展,喷吹法预处理铁水技术随之出现。
喷吹法主要有原西德的THYSSEN的ATH法(斜插枪法)、新日铁的TDS(顶吹法)和炉前铁水沟连续脱硫法;由于喷吹法具有设备简单、投资少、操作灵活方便,冶金效果好,处理铁水量大和费用低等特点,很快得到钢铁生产厂家的认同和推广,成为目前铁水预处理的主要方法,不仅用于铁水预处理脱硫,而且还用于铁水脱硅和同时脱除硫、磷。
喷吹法最早是由西德奥古斯蒂森冶金公司(AUGUSTTHYSSEN—HUETTEAG)于1969年试验成功的,称为ATH法。
它是在265t混铁车内斜插一根内径为2.54cm的喷枪,表面涂上耐火材料,每分钟吹入108kg炭化钙复合脱硫剂,处理时间为8min;输送气体压力为0.6MPa,喷枪倾角为60。
,粉剂浓度约为40-60kg/Nm3。
不久,日本新日铁公司于1971年试验成功混铁车顶喷粉脱硫法,简称TDS法。
它是在250t或300t的混铁车垂直插入一支内径为2.5cm的双孔喷枪,插入深度为1.0-1.5m,喷枪外面裹着耐火材料,处理时间为10min,供粉速度为40—70kg/min,用N2输送,气体流量为5-10Nm3/min,粉剂浓度约为8-10kg/Nm3。
喷吹法又可分为混合喷吹和复合喷吹两大类。
混合喷吹法是将两种或几种脱硫粉剂事先按一定比例混合好,然后用同一个喷粉罐经喷枪喷入铁水罐中进行脱硫。
这种方法简单、控制方便、投资少。
缺点是脱硫剂用量配比不易准确控制,不灵活,脱硫效果不理想,命中率低,粉剂消耗大,粉剂利用率低,约是复合喷吹粉剂消耗的1.5—2.1倍,从而带来了渣量大、喷溅大、铁损高、温降大等系列问题,使得成本增加,因此,近年来该方法正在逐步被淘汰。
复合喷吹是将两种或几种脱硫粉剂用各自专用的喷粉罐,经称量后再输送到同一根喷枪中进行喷吹的脱硫工艺。
其特点是脱硫粉剂的配比可根据现场的需求灵活调整,粉剂消耗低、控制稳定、调节灵活、设备高效、喷溅少、渣量少、铁损少、脱硫效果好。
同时喷粉罐向喷枪供料均采用粉料流态化沸腾床和可调喉口技术,以保证粉剂流量波动小,喷吹管道畅通,保证了稳定的粉料定量供应。
国内发展状况
我国从50年代末开始采用苏打粉铁水沟脱硫技术。
但由于我国从平炉改造到转炉比较晚,因此铁水炉外脱硫至二十世纪七十年代才逐渐发展起来。
1976年武钢从新日铁引进KR法脱硫技术,1985年宝钢采用TDS法脱硫技术,1988年太钢引进三脱(脱硫、脱磷、脱硅)技术,1998年本钢引进加拿大(CaO十Mg粉)复合喷吹脱硫技术,同年宝钢引进美国(CaO--Mg粉)复合喷吹脱硫技术,1999年鞍钢引进美国(CaO-Mg粉)复合喷吹脱硫技术。
至今,武钢、鞍钢、攀钢、宝钢、太钢、包钢、齐钢、天钢、上钢一厂、冷水江铁焦总厂、承钢、酒钢、宜钢、重钢、涟钢、鄂钢等厂均建立了高炉铁水炉外喷吹脱硫站,还有不少厂进行了工业实验研究。
它们多以石灰系脱硫剂脱硫为主,电石系和金属镁脱硫剂则相对较少。
随着连铸技术的飞速发展和市场对钢质量要求的日益严格,铁水脱硫也在不断发展和日趋完善。
提高钢材质量、生产高附加值产品的需求成为全世界范围内铁水脱硫技术的发展动力。
现在要求炼钢铁水的硫含量一般不能超过0.010%,甚至达到0.005%—0.001%。
如石油管线用钢,硫限量在0.002%—0.005%之间。
当今,采用铁水脱硫技术已成为钢铁企业质量水平的一个标志。
炉外脱硫方法及特点
铁水沟铺撒冲法是在高炉出铁过程中连续地往出铁沟或盛铁罐内撒入脱硫剂。
该方法操作简单,但脱硫效率较低,且不够稳定。
机械搅拌法是在高炉出铁槽上装设搅拌器,出铁时加入脱硫剂进行搅拌。
搅拌器的旋转方向与铁水流动方向相反。
日本钢管(NKK)技术研究采用一种多级机械搅拌方式进行铁水脱硫,谓之NKK脱硫法,因反应器内形如蚕状又称为蚕式法。
脱硫剂随同铁水自一端流入,经旋转搅拌,混合反应后,从另一端流出。
铁水在反应器内的平均停留时间为2—4min,处理铁水的温度为1450℃,用CaC2作脱硫剂,用量3kg/t.铁,可以达到70%的脱硫率,该方法具有设备费用较低、处理能力较强的优点。
铁水沟喷粉脱硫法的喷吹点设在高炉出铁沟附近,两支喷枪顺流布置。
脱硫粉气流垂直喷向铁水流,喷吹的脱硫剂对铁水产生冲击和搅拌作用,在铁水沟中进行脱硫反应。
涡流反应器法的涡流器安装在铁水罐上方,使铁水从切线方向流入形成涡流运动,将渣料卷入铁流中。
在铁水流量为1.5—2.0t/min,脱硫剂用量为铁水量1.6%的试验中,脱硫效果达42%—43%。
吹气搅拌法主要有顶吹法、底吹法(PDS或CLDS)和气升泵法三种。
顶吹法和底吹法预先将脱硫剂加到铁水表面,然后通过顶枪或罐底的透气砖往铁水中喷吹气体进行搅拌。
它们设备费用低,操作简便,但脱硫效果不及搅拌法好。
气升泵法向气升泵吹入气流将铁水不断升入泵筒体。
当筒体内铁水超过罐内液面高度时,通过筒体上部的许多孔眼喷撒的脱硫剂与铁水发生脱硫反应。
镁脱硫法的镁以镁焦、镁锭、镁粉、镁合金及白云石的团块等形式加入铁水中进行脱硫。
用镁脱硫的最重要问题是要控制镁的气化速度,以免发生爆炸。
镁脱硫时采用的主要方法有插罩法、插杆法、三明治法、压力室法、可倾罐法、T-Nock流槽法和喷吹法等。
镁脱硫法速度快、渣量少、温度损失少,但费用高、操作控制困难。
喷吹法在1970年由原西德蒂森公司研究成功并投入应用了ATH法,它将一支外衬耐火材料的喷枪与水平方向成60。
角斜入鱼雷罐内,用载气向熔池内喷射固体粉末脱硫剂进行脱硫处理。
随后,日本新日铁公司开发出了TDS法。
它将喷枪从上部垂直插入鱼雷罐内,脱硫剂从喷枪的两侧孔喷入铁水中。
由于喷吹法是在喷吹气体、脱硫剂和铁水三者之间充分搅拌混合的情况下进行脱硫的,因此脱硫效率高、处理时问短、操作费用较低.并且处理铁水量大、操作方便灵活。
因而受到人们的极大重视,成了目前应用最广泛的的铁水脱硫处理方法。
喷吹法又可分为混合喷吹和复合喷吹两大类
脱硫剂的选择
脱硫剂是决定脱硫率和脱硫成本的主要因素之一。
常用的脱硫剂主要有钠系、钙系以及镁系等,其发展是伴随着脱硫工艺及方法的进步而变化发展的。
二十世纪三十年代,随着铺撒法在铁水预脱硫中的开始运用,钠系脱硫剂,特别是苏打粉脱硫剂开始在工业中被采用。
以后随着脱硫方法的变化,各种脱硫剂随着被应用,尤其是镁焦法脱硫曾延续相当长时间。
二十世纪六十年代开始,在欧洲一些国家特别是美国开始使用复合脱硫剂。
如AMCO厂用石灰—镁(4:
1)脱硫;在YOUNSTAWN厂使用盐包镁(含88-92%镁,用54%NaCl、20%MgCl2、13%CaCl2、13%KCl盐作外衣)为脱硫剂,还在其中使用75%石灰和25%铝来做脱硫剂,以及石灰—碳脱硫剂等。
日本川崎厂为保证石灰—碳脱硫剂性能良好,还在其中掺入0.2%—0.3%的硅油。
进入二十世纪七十年代后,在世界范围内广泛采用电石粉(CaC2)为脱硫剂,多以复合脱硫剂的形式在工业中应用,并掺入一定数量碳酸钙粉、氟化钙粉、碳粉等;加入碳酸钙的目的是活跃金属熔池,起促进剂的作用;加入氟化钙是为了化渣,改善流动性;加入少量碳粉,目的是想要在罐口上部形成还原性气氛。
而复合脱硫剂以其具有比单一脱硫剂脱硫效率高、成本低、环境污染小而得到优先使用。
电石脱硫剂脱硫能力强,但价格较贵,进入二十世纪八十年代以来,逐渐减少使用;近年来,镁基脱硫剂在国外得到了广泛的应用,在国内只有少数几个厂家引进美国技术。
但是,随着市场对钢材质量要求的提高,镁基脱疏剂也正在得到国内许多厂商的关注。
苏打粉(Na2CO3)
苏打粉的脱硫反应为
Na2CO3=Na2O+CO2
Na2CO3+[S]+[Si]=Na2S+SiO2+3CO
Na2CO3+[S]+2[C]=Na2S+3CO
苏打粉脱硫特点:
a.Na2CO3有很强的脱硫能力。
在1350℃时,其脱硫能力与电石相当,而大大高于石灰粉的脱硫能力。
b.苏打粉不仅可以脱硫,而且可以同时脱磷。
c.用苏打粉处理铁水,处理后渣中的苏打呈水溶性,可以用湿法回收苏打,重复使用。
d.苏打在1250℃易挥发产生白色浓雾;另外,苏打粉脱硫生产的Na2S,一部分被氧化成SO2和Na2O,其反应为:
2Na2S(l)+3O2(g)=2SO2(g)+2(Na2O)
Na2O可能被还原成气体钠,钠蒸汽连同一氧化碳在空气中燃烧,也生成大量烟雾,这些烟雾污染空气,堵塞管道,加剧侵蚀。
e.苏打粉的沸点低,在铁水中易挥发,且碳酸钠分解要吸收大量热量,从而引起铁水的降温,不适应低温钒钛铁水预处理。
f.苏打在高温下分解生成的氧化钠呈液体,它在渣中的含量高时,渣就变得很稀,不易扒渣,且对罐内耐火材料侵蚀严重。
g.在钒钛铁水中采用苏打粉脱硫还会发生如下反应:
5FeO+2[V]+Na2CO3=2NaVO3+CO2+5Fe
钒进入脱硫渣相被扒除,增加了钒的损失。
h.苏打粉的来源短缺,成本高;而从渣中回收苏打重复使用时,要增加额外的设备投资和生产费用。
再加上用苏打粉进行脱硫进行铁水脱硫处理会导致铁水钒的损失,不利于有益元素钒的回收,所以不适应用于钒钛铁水的预处理脱硫。
石灰粉(CaO)
石灰粉的脱硫反应为:
CaO(s)+[S]+C=CaS(s)+CO…………………………
(1)
当[Si]高时
4CaO(s)+2[S]+[Si]=2CaS(s)+2CaO.SiO2(s)……
(2)
石灰的反应
(2)生成了致密的硅酸二钙壳层,降低了石灰的脱硫反应速率。
石灰粉脱硫特点:
a.石灰粉资源丰富,价格低,易加工,使用安全。
b.脱硫产物为固体渣,对铁水容器内衬耐火材料侵蚀轻微,扒渣方便,但由于脱硫能力较电石差,故耗量大,渣量多,且固体渣包裹着大量铁珠,铁损较大。
c.石灰流动性差,在料罐易“架桥”堵料,同时石灰极易吸水潮解,潮解生成的Ca(OH)2,不但影响脱硫效果,而且污染环境,因此,石灰粉需要在干燥氮气密封存储在单独料仓内。
d.在石灰脱硫过程中,铁水中的Si被氧化生成SiO2,SiO2将与CaO作用生成2CaO.SiO2,相应的消耗了有效CaO量,而且在石灰粉粒表面形成致密的2CaO.SiO2阻碍了[S]向CaO粉粒的扩散,影响了脱硫速度和脱硫效率,所以石灰粉的脱硫效率只是电石粉的1/4—1/3。
为此,可在石灰粉中配加适量的CaF2、Al或Na2CO3等成分,破坏石灰粉粒表面的2CaO.SiO2,改善石灰粉的脱硫状况。
因为,加Al后使石灰粉粒表面形成了低熔点钙的铝酸盐,提高脱硫效率约20%;加入Na2CO3可以使CaO反应速度常数由0.3增长为1.2;若加入CaF2反应速度常数可提高2.5。
e.石灰脱硫反应为吸热反应,脱硫过程铁水温降大。
电石粉(CaC2)
电石粉的脱硫反应为:
CaC2(S)+[S]=CaS(S)+C石墨
电石粉脱硫特点:
a.在高硫铁水中,电石分解出的Ca离子与S的结合力强,因此有很强的脱硫能力。
b.电石脱硫反应为放热反应,可减少脱硫过程铁水的温度。
c.脱硫产物CaS的熔点很高,为2450℃,在铁水表面形成疏松的固体渣,有利于防止回硫,易于扒渣,且对铁水罐等容器的内衬侵蚀较轻。
d.由于电石的强脱硫能力,故耗量少,渣量也少。
e.电石是工业产品,价格比石灰贵。
f.电石粉极易吸潮,在大气中与水接触时,迅速产生如下反应:
CaC2(S)+2H2O=Ca(OH)2+C2H2
CaC2(S)+H2O=CaO+C2H2
这个反应降低了电石粉的纯度和反应强度,而且反应生成的可燃气体C2H2,极易产生爆炸,C2H2气体在空气中的浓度达到2.7%时就会发生爆炸,所以应相应地增加检测、防爆、防燃设施,给工艺设备增加了复杂性和不安全性,因此,在运输和保存电石粉时要采用氮气密封。
另外,电石粉和其它脱硫剂混合使用时,也会吸取其它脱硫剂的湿气而发生上述反应,故电石粉应单独储存在料仓内。
金属镁脱硫(Mg)
镁粉脱硫铁的反应式为:
a.镁脱硫反应式
Mg(s)Mg(l)Mg(g)[Mg]………
(1)
Mg(g)+[S]=MgS(s)………………………………………
(2)
[Mg]+[S]=MgS(s)………………………………………(3)
镁脱硫分三步进行:
a.镁在高温铁水中由固体到液体、气体转变及在铁水中溶解过程;
b.镁蒸汽与铁水中的[S]反应生成不溶于铁水的硫化镁,脱去的硫占铁水中硫的3—8%。
c.溶解镁与铁水中的[S]反应生成不溶于铁水的硫化镁,起主要脱硫作用。
另外镁与铁水中氧、渣中氧反应导致镁的损失。
Mg+O=MgO
镁脱硫特点:
a.镁有较强的脱硫能力,1350℃时,镁粉进行铁水炉外脱硫,脱硫反应的平衡常数可达3.17×103,反应平衡时,铁水中含硫量可达1.6×10-5%,大大高于氧化钙脱硫能力。
b.镁的沸点为1107℃,镁加入铁水后,变为镁蒸汽,形成气泡,部分反应在气—液相界面上进行;另外,由于金属镁变成镁蒸汽,使反应区流体搅拌良好,大大增加了镁的脱硫效果。
c.镁在铁水中有较大的溶解度,溶解镁起主要脱硫作用。
铁水经镁饱和后能防止回硫,这部分饱和镁在铁水处理后的运输过程中仍能起脱硫作用。
d.由于镁的沸点低,在高温下为气体,故镁难以加入到铁水中去,工艺上常采用镁-焦、镁-铝、镁-白云石、镁-石灰粉等方式把镁加入铁水中。
e.实际生产中已证实,用镁脱硫的反应速度快,脱硫效率高,可使铁水中硫含量≤0.005%,适用于大量处理铁水。
f.镁脱硫单耗少,渣量少,处理时间短,铁损和热损少,采用钝化镁解决了其贮运的安全问题。
g.镁的挥发损失大,控制不当可引起严重喷溅或爆炸等事故。
h.脱硫产物为固态硫化镁,易于扒渣,对耐火材料侵蚀轻微。
h.镁价格高,处理成本高。
金属镁系脱硫剂
金属镁的脱硫能力很强,国外早在七年代就先后发展了石灰—镁过程、石灰一盐镁粒过程和镁粒过程,1975年又开始采用天然气喷吹镁粒的脱硫工艺。
为了防止镁的挥发损失和控制其挥发速度,人们进行了不少研究工作。
如,格鲁吉亚某厂通过铁水罐底部吹入镁粒,可提高镁的利用率;Irons等人的工作:
其一,喷吹“包盐镁粒”,其组成为88-92%Mg,8-12%卤化物(或NaCl、或KCI、或CaCl2、或MgCl2),其粒度为0.25mm—1.6mm;其二,控制镁的挥发速度,在镁粒中掺入一定量的三氧化二铝、氧化钙或氟化钙等粉剂,其粒度为0.01mm—0.1mm。
因为氟化钙会侵蚀包衬,而含熟石灰脱硫剂会引起喷溅,故在生产中建议使用50%镁粒+50%CaO的脱硫剂。
Mg-CaO复合喷吹脱硫
1、脱硫反应
a.镁脱硫反应式
Mg(s)Mg(l)Mg(g)[Mg]………
(1)
Mg(g)+[S]=MgS(s)………………………………………
(2)
[Mg]+[S]=MgS(s)………………………………………(3)
b.流化石灰脱硫反应式
CaO(s)+[S]+C=CaO(s)+CO…………………………
(1)
当[Si]高时
4CaO(s)+2[S]+[Si]=2CaS(s)+2CaO.SiO2(s)……
(2)
石灰的反应
(2)生成了致密的硅酸二钙壳层,降低了石灰的脱硫反应速率。
Mg-CaO复合脱硫效果分析
a.Mg脱硫能力强,利用率高时可达到50%;流化石灰粉的利用率在2%—3%左右。
b.MgS的密度小、渣量小,易上浮入渣;而单纯采用CaO粉脱硫时间长、渣量大、温降大。
c.Mg脱硫反应放热,Mg蒸汽产生强烈的搅拌作用,铁水中Mg饱和后很难回硫。
d.Mg脱硫不生成大量的烟尘,而CaO形成固体的脱硫渣有利于扒渣及延长罐衬寿命。
e.CaO粉为载体,防止Mg粉直接与管壁接触产生摩擦,有利于减小管道的阻力。
f.CaO/Mg的喷粉速度比值控制在2—4,喷粉效果比较好;一般CaO的喷粉速度控制在28—40kg/min,Mg粉控制在9—13kg/min;当CaO的喷粉速度>40kg/min,脱硫率随着速度提高而下降,>60kg/min,脱硫率下降更加明显。
g.铁水温度高,脱硫效率增高,因为温度高有利于[S]的扩散,传质速度快;但铁水温度过高,镁挥发损失大。
h.部分Mg与渣中的氧反应生成MgO放热,起到一定的热源补偿,但复合脱硫的平均温降在8—14℃之间。
复合喷吹脱硫中CaO的作用
a.加入的石灰粉成为大量气泡的形成中心,缩小了镁气泡的直径,减缓了镁气泡的上浮速度,加快了镁在铁水中的溶解,从而提高Mg的利用率。
b.加入的石灰粉起到镁粉分散剂的作用,避免大量镁瞬间汽化造成喷溅。
c.在复合喷吹脱硫加入一定的CaO粉,也能起到一定的脱硫作用。
d.CaO在参加反应的同时被当成了实际的载体。
铁水脱硫时镁的损失
镁在铁水表面蒸发而损失;
镁和渣中或大气中氧反应生成MgO;
镁和氮反应生成Mg3N2;
镁溶解于铁水中部分未参与脱硫反应而损失。
Mg-CaO复合喷吹脱硫的影响因素
铁水初始[S]对脱硫率的影响
铁水初始[S]与脱硫率的关系如图所示。
由图可知,铁水初始[S]越高,其脱硫效果越好,因为初始[S]越高,[S]的活度越大,脱硫反应越易进行。
钙镁比(CaO/Mg)对脱硫的影响
钙镁比(CaO/Mg)与脱硫量的关系如图所示。
由图可知,随着钙镁比(CaO/Mg)的增加,单位脱硫剂的脱硫量降低。
正常情况下,CaO/Mg的喷粉速度比值控制在2:
1—4:
1比较合适,喷粉效果比较好。
一般CaO的喷粉速度控制在25—40kg/min,Mg控制在8—14kg/min;当CaO的喷粉速度>40kg/min,脱硫率随着速度提高而下降,CaO的喷粉速度>60k