炼铁毕业设计Word文档格式.docx
《炼铁毕业设计Word文档格式.docx》由会员分享,可在线阅读,更多相关《炼铁毕业设计Word文档格式.docx(71页珍藏版)》请在冰点文库上搜索。
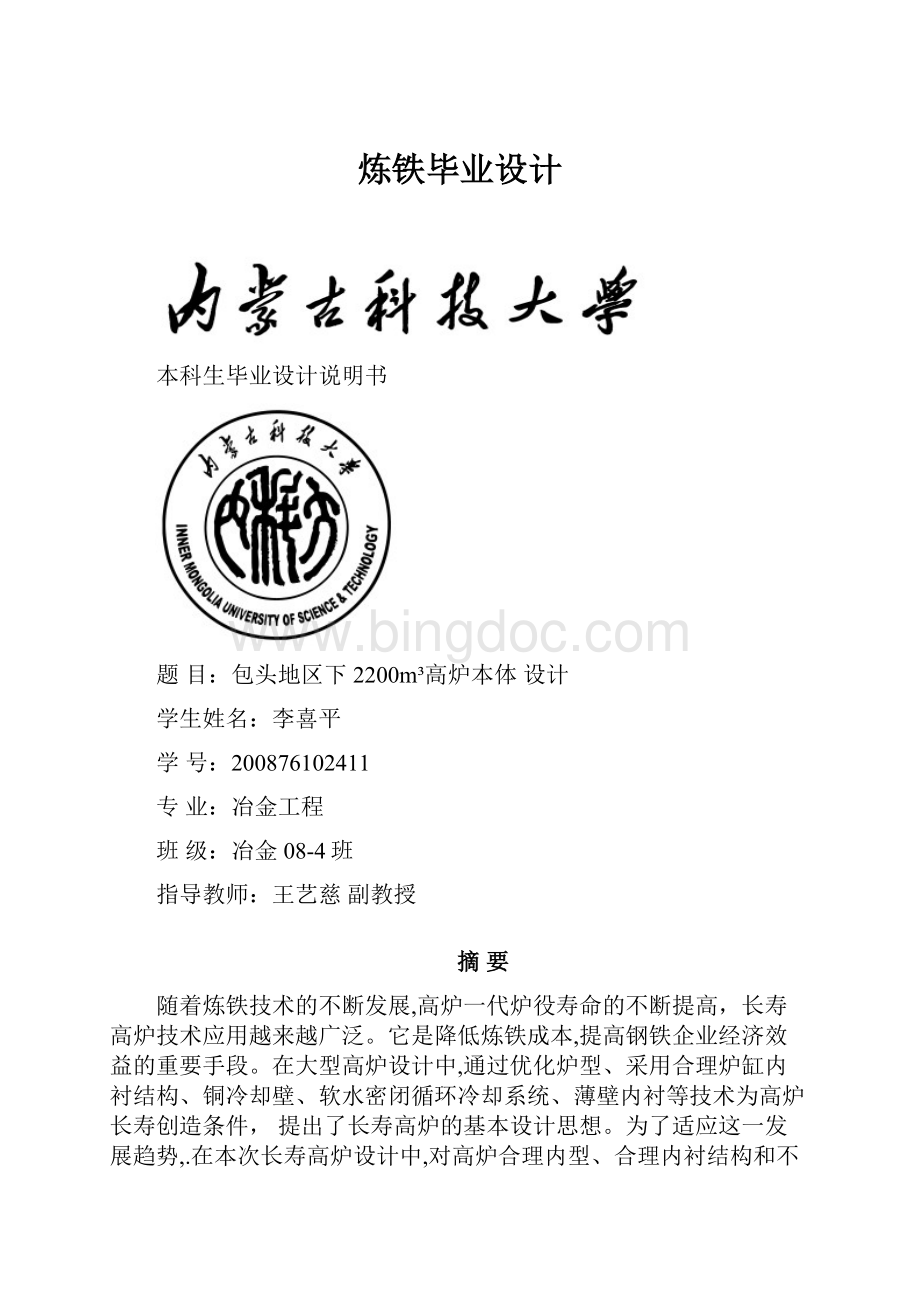
矮胖型
DesignofLongLifeBF
ABSTRACT
BFcampaignlifeiscontinuouslyincreasedasunceasingdevelopmentofironmakingtechnology.Itisbeingusedmoreandmoreabroad.ThelongcampaigntechnologiesofblastfurnaceisoneofthemostimportantmeasureswhichreducetheironmakingproductioncostandimprovetheeconomicprofitsofIronandSteelCompany.InthedesignoflargeBF,thetechnologieslikeoptimizedBFprofile,reasonablehearthlining,copperstave,softwaterclosedcirculatingcoolingsystemandthin-walledliningetc.wereappliedtoprolongBFcampaignlife.Thebasicconceptofdesigninglongcampaignblastfurnacewasputforward.Inordertoadapttothetrend,duringdesigninglongcampaignblastfurnace,therational;
furnaceprofile,rationalfurnaceliningstructureandselectionofdifferentrefractoriesforvariousareas,coolingmethodandsystem(includingcoolerstructureandmaterial,coolingwaterandsoon)andconcernedaspectsmustbecomprehensivelyconsidered.
KeyWords:
BF;
Longevity;
DesignofFurnaceBody
第一章文献综述
一.1研究背景
高炉本体包括高炉基础、钢结构、炉衬、冷却设备、以及高炉炉型设计等。
随着钢铁生产的集中化、专业化、协作化,我国炼铁设计迅猛发展,高炉大型化、现代化、高效化、长寿化加快,并取得了令人瞩目的技术成就。
其中高炉大型化的炼铁原料、设备、操作技术综合发展的结果,也是衡量一个国家的高炉生产与建设水平的重要指标。
1750年,英国的工业革命开始了。
在燃烧上用焦炭代替木炭,这种转变使炼铁业突破了束缚,不再为木炭的短缺而陷入困境。
因为不仅民用燃烧需要大量木料,而且为了提高农业产量也在大量砍伐森林。
因此,对于人口密度高的国家,要靠木炭来增加铁的产量是不易的。
到18世纪末,煤和蒸汽机已使英国的炼铁业彻底改革,铁的年产量从公元1720年的2.05×
10000吨/年(大多是木炭铁)增加到1806年2.5×
100000吨/年(几乎全是焦炭铁)。
估计,每生产一吨焦炭需煤3.3吨左右。
但是,高炉烧焦炭势必增加碳含量,以致早期的焦炭生铁含碳在1.0%以上,全部成为灰口铁即石墨铁。
高炉的尺寸在18世纪内一直在增大。
从公元1650年约7米,到1794年俄国的涅夫扬斯克高炉已增高到13.5米。
因为焦炭的强度大,足以承担加入的炉料的重量。
大多数的炼炉采用炉缸、炉腹和炉身三部分按比例构成。
19世纪末,平滑的炉衬公认为标准的炉衬,这基本上已经是现在的炉型。
炉底直径约10米,炉高约30米。
全部高炉都设有两只以上的风嘴。
另一个巨大的进步就是采用热风。
20世纪后,现代钢铁业就蓬勃发展起来。
近代钢铁工业发源于西欧,首先兴起于英国,其次是法国和西德,到现在都有一百年以上的历史。
炼钢工业从工艺原理到设备,例如贝塞麦炉、托马斯炉、平炉到氧气转炉和电炉等,一个超过一个,大约每隅二十年左右,炼钢工业就有很大的革新[1]。
为了进一步提高劳动生产率,降低成本,增加生铁产量,从60年代初世界制造出容积为2000m³
以上的高炉。
从最早的热风小高炉,容积约50m³
,发展到现在的大型高炉,经历了将近一百年。
高炉炼铁的基本原理没有变,但是高炉炉体以及外围设备却大大地革新了。
六十年代后期,大型高炉日产量已经超过4000吨;
七十年代以来,大型高炉发展的迅速甚至超过人们的预料。
从1970年到1976年的几年中,世界已建成投产104座大型高炉,容积在4000立方米以上的有18座。
可以说,从七十年代开始,高炉大型化的发展就达到历史上未有的高潮。
如表1.1主要产铁国家的高炉座数和生产能力。
表1-1七十年代世界主要产铁国家的高炉座数和生产能力
日本美国苏联西德英国法国
项目197119701971197019711970197119701971197019711970
1970年年年年年年年年年年年年
高炉座数646522821911313210493718097
生产能力(万吨773474751000089799000370423432000
/年)
到1972年为止日本有30座大于2000m³
高炉投入生产,日本钢管福山四高炉,炉容4197m³
于1971年4月25日开炉,日产能力10000吨。
日本已建和计划兴建的大型高炉如下表所示。
大于2000m³
高炉数量约占国外总数的一半【3】。
苏联大于2000m³
高炉有17座(1971年),最大的为3000m³
,日前正在设计5000m³
的。
美国大型高炉有2427m³
,美国七十年代,日产7000吨的高炉炉容都在2210-2830m³
。
荷兰、加拿大、波兰、法国也有大型高炉,炉容分别为2156、2006、2000和2100m³
高炉越建越大,1970-1977年日本已有12座4000-5000立方米高炉投产,1976年日本4000立方米以上高炉生产的生铁占全国总产量30.6%【1】,表1-2
表1-2日本高炉座数与炉容情况
高炉内容积1976年1977年
2000立方米以下3530
2000-3000立方米1919
3000-4000立方米77
4000立方米以上1112
共计7268
近些年,国外钢铁工业已经完成结构调整、专业分工、技术升级,正处于企业购并、资源整合阶段,规模扩张已从发达国家转向以亚洲为主的发展中国家。
日本、韩国及欧洲国家的大型钢铁企业通过加大科技投入、开发核心技术、实施知识产权战略等方式,巩固自身在国际竞争中的地位,并借助规模、资金、专有技术、服务网络等优势,通过出口装备向发展中国家输出技术,获得高额利润。
一.2我国高炉大型化的发展现状
我国刚毅额工业底子薄,刚解放时,全国只有7座高炉,1949年的钢产量仅为15.8万吨,居世界第26位,设备水平极为落后。
改革开房以前,由于种种原因,高炉大戏规划发展速度一直比较缓慢。
改革开放以后,我国话大力气投资建造了一大批高炉,其中也有一些总体设备水平较高的大型、特大型高炉。
然而虽然新建的高炉星罗密布,但1000m³
以上的高炉座数与1000m³
一下的中、小型高炉座数相比却为数很少。
且这些中、小型高炉的装备水平大多都比较落后。
到1989年,50m³
一下的小高炉座数比1983年翻了两番多,占全国高炉总容积的比例也翻了一番多。
1989年后,我国虽又陆续投产了一些大、中型高炉,但小高炉的见着速度也不落后。
据冶金部统计,1994年我国重点企业有100-4350m³
的高炉79座,总容积86153m³
,骨干企业有36-1260m³
的高炉139座,总容积33788m³
,地方和乡镇小企业大多为30-50m³
的高炉。
而在1994年的全国生铁总产量(9642万吨)中,重点企业占54%,这一比例同10年前的1984年相比,却下降了16%,地方企业和乡镇小铁厂的生铁产量则上升了16%。
这些小高炉不仅生产工艺和设备技术水平落后,生产效益低,对环境污染严重,而且能耗高,能源浪费严重。
小高炉的入炉焦比大多在800kg左右,有的甚至在1000kg以上,比我国较好水平的高炉高出一倍多,送风系统漏风严重,节能环保等综合利用更谈不上,生产出的生铁质量也无保证。
虽然这批小高炉在我过钢铁供求矛盾紧张的情况下为我国的钢铁生产予以补充,但其给能源和矿产资源造成的浪费十分可观。
可见,我国高炉大型化虽有发展,但总体看,高炉技术装备水平低。
其特点是大、中、小高炉并存,炉子多,分布广,平均炉容小,生产效益低,能耗高,经济技术指标差,产品质量较低,环境污染较严重。
图1.1日本、美国、前苏联以及我国1949-1995年的钢产量发展情况
图1.1为日本、美国、前苏联以及我国1949-1995年的钢产量发展情况。
我国近十几年来虽然相继投产了一批大、中型和特大型高炉以及相配套的炼钢,轧钢等钢铁生产设备,使我国的钢铁产量有了大幅度提高,1995年的钢产量达到9400万吨,名列世界第二,生铁产量达到10171万吨,跃居世界第一,但人均拥有量仍处落后地位。
目前我国人均粗钢拥有量不足70kg。
远低于人均粗钢拥有量约1吨的日本和约0.5吨的美国,甚至低于约150kg的世界平均水平。
因此,我国钢铁工业仍需大力发展。
针对我国情况来看,我国的炼铁工业在发展如COREX熔融还原等短流程炼铁新工艺的同时,高炉炼铁在今后相当长的一段时间内仍是生产生铁的主要工具。
因此,各地应根据情况建造1000m³
以上甚至3000-4000m³
左右具有现代化水平的高炉,以形成具有一定规模的大、中型钢铁企业为宜。
同时要注意提高原燃料质量,对现有的300m³
及其以上的生产指标较好的中小型高炉,应提高原燃料质量,加强精料、综合鼓风、节能环保、综合利用等工艺和设备方面的改造,提高现代化程度,提高效益。
由于历史发展原因,我国高炉容积过小、座数过多、环境污染严重的问题非常突出。
据统计,我国高炉总数有3229座,其中炉容在1000-4350m³
的48座,100-983m³
的181座,<
100m³
的3000座,平均炉容仅83m³
即便是按我国通称的大、中型高炉(>
)计算,平均炉容也只有625m³
平均单炉年产铁量约43万t。
在我国,不论是大型钢铁厂还是中小型钢铁厂,都存在着高炉座数过多、炉容过小的问题,一个厂的高炉座数少则4座、5座,多则达10座,既造成劳动生产率低下,生产组织管理困难,并且有些高炉因装备过于陈旧,对环境污染也很严重。
这种状况不改变,无法参与国际市场竞争。
在我国,有一种观点认为,建小高炉投资少、建设快,那怕高炉座数多一点,多用点人,还是合算的,因为我国人口多,工资水平低。
这种观点是不正确的、简单算一笔账就能看清间题。
以大型高炉、转炉等没备构成的宝钢,人均年产钢约800t,而国内多数其他钢铁厂人均年产钢仅100200t,若年均工资同为每人20000元,则前者吨钢人工费为25元,后者为100-200元,差别明显,据统计我90年代建设的一批不同容积的高炉(300-4000m3),无论按单位炉容或吨铁能力投资计算,都在同一个范围,并未表现出小高炉的投资比大高炉有明显降低。
提高劳动生产率,除高炉大型化以外,还可以从提高利用系数着手,目前我国一大批中小高炉利用系数已高达2.5-3.5,大型高炉已达到2.0左右,潜力己经不大了,在炉容大型化方面却有很大的空间。
当今,我国市场经济的发展,特别是经济全球化的发展,为我国高炉大型化提出了迫切的要求,而科学技术的进步又为我国高炉大型化创造了充分的条件。
首钢从上世纪70年代改造2号高炉开始到90年代初完成了高炉大型化改造,平均炉容从原来的832m³
增加到2005m³
;
鞍钢正着手将装备非常陈旧的7座600–960m³
的高炉改建为2座3200m³
的现代化大高炉,改造完成后,高炉将从10座减少到5座,平均炉容将从原来的1407m³
增加到2228m³
同时还要将8台陈旧的75㎡烧结机改建为2台360㎡的烧结机。
马钢原有9座300m³
级高炉,上世纪90年代建起1座2500m³
高炉,停了几座小高炉,己经向高炉大型化迈出了第一步。
一.3高炉用耐火材料的发展
耐火材料是影响高炉寿命的重要因素之一。
依其使用部位的不同,对耐火材料的要求也不尽相同[5]。
(1)炉底、炉缸耐火材料
我国大中型高炉的炉缸炉底自50年代末采用碳砖综合炉底以来,在相当一段时期内,其寿命都在10年以上。
但随着高炉冶炼强度的不断提高,炉缸寿命依然存在着问题。
炉缸炉底烧穿而导致高炉停炉的现象在国内外屡见不鲜。
如邯钢1260m,高炉,1992年7月投产,1995年4月炉缸烧穿[7]。
炉缸炉底的破损是由于炉墙砖衬的厚度减薄到一定程度时,导致冷却水温度升高,高炉的安全受到威胁。
炉缸炉底破损最主要的特征是在炉缸炉底交界处产生“蒜头状”侵蚀。
“蒜头状”异常侵蚀的发展,使炉墙耐火材料的厚度减薄,冷却水温度升高,发展到一定程度时,必须停炉,否则可能会造成炉缸烧穿。
因此,“蒜头状”侵蚀是限制炉缸炉底寿命的一个十分重要的因素。
炉缸的侵蚀机理主要有:
铁水和碱金属的侵蚀和渗透;
耐火材料冷热端的巨大温差造成的热应力:
同时出铁时铁水的流动对此部分耐火材料产生冲刷。
为提高炉缸的使用寿命,一方面是加大死铁层的深度,抑制铁水环流对耐火材料的冲刷,另一方面是采用高质量的耐火材料。
目前,炉缸炉底的耐火材料的选用主要有两种方案,一种是在优质高导热碳砖上砌筑陶瓷质耐火材料;
一种是采用高导热的微孔、超微孔碳砖,防止铁水和碱金属的侵入。
炉缸炉底用耐火材料的很重要的一点是实现微孔或超微孔,减少孔径大于lμm的气孔:
实现气孔封闭,消除或减少铁水向碳砖内的渗透,使铁水对碳砖的侵蚀只能在碳砖表面进行,从而减缓对碳砖的侵蚀速度,延长高炉的寿命。
其次耐火材料的导热系数对其的冷却效果有重要的影响,提高导热系数可降低耐火材料的温度,提高其抗侵蚀能力。
(2)高炉炉腹至炉身下部耐火材料
炉腹至炉身下部是高炉内衬最薄弱的环节,该部位的耐火材料,在生产中由于受到高温及强热震、初成渣和铁水的侵蚀、碱金属及锌的侵蚀、炉料磨损和煤气流的冲刷以及CO,及H20的氧化等,许多高炉在炉役早期砖衬便受到严重的侵蚀,高炉只能靠冷却器及形成的渣皮维持生产,随着冷却设备的烧坏,炉壳红热变形甚至烧穿,高炉只好被迫停炉中修。
从理论上来讲,高炉砖衬维持的时间越长,冷却器工作的环境也越好,冷却器的寿命就越长,高炉的寿命也就越长。
因此,根据炉体不同部位炉衬的侵蚀机理合理地选用优质的耐火材料,是保证高炉长寿的重要途径之一。
此区域耐火材料的选择主要有两种观点[8]:
一种是追求高导热系数,通过冷却使内衬热面温度低于800℃(即对耐火砖破坏作用出现时的临界温度),将800℃等温线推至耐火砖衬热表面或渣壳内,这样的砖衬可视为“永久砖衬”,其代表产品是美国UCAR公司的小块热压碳砖,它导热系数高(32W/m.K),抗热冲击性能好,抗渗透性、抗碱性好,对于原料条件不稳定、大量使用球团矿,炉况经常波动的高炉是比较适用的:
另一种观点正好相反,认为应该通过选择耐火材料使炉内热损失减到最低,而耐火材料本身应该能在高温下经受住任何侵蚀,这样就对耐火材料提出了更高的要求,其代表性产品为法国SAVOIE公司产品,SIALON结合的刚玉砖和碳化硅砖(导热系数分别为3.5W/m.K和15W/m.K),这种砖具有良好的抗碱性和抗氧化性[9]。
目前这一部位国内普遍采用抗铁水渗透性、抗渣性、抗碱性、抗氧化性较好,并有优良机械性能的SiC系列耐火砖。
但是在国内使用国产氮化物结合的SiC砖没有获得明显的效果。
炉墙的温度场和耐火材料的性能是决定炉身下部炉衬寿命的两个重要方面。
设计、操作等因素对炉身下部寿命的影响均通过这两个方面反应出来。
对于炉墙的设计有两种不同的观点:
一是采用高导热性的耐火材料,使炉墙的总热阻较小,这样可以有效地冷却炉衬;
另一种观点是采用低导热系数的耐火材料,使炉墙的总热阻较高。
认为这样可以减少热量的损失,有效地保护冷却系统和炉壳。
J.VanLaar等人认为[8]:
高炉炉衬一冷却系统的热负荷是由高炉操作方式决定的,与炉衬一冷却系统。
一.4高炉冷却
实践证明:
冷却方式、冷却器的结构参数、材质、布置方式以及水质等对高炉寿命有极大的影响。
一.4.1高炉冷却方式的发展
高炉冷却方式的发展大致可分为三个阶段:
直流供水冷却系统、敞开式供水冷却系统、闭环式循环冷却系统(含汽化冷却系统和软水密闭循环冷却系统)。
与之联系在一起的高炉冷却水的发展经历了工业水(即未经处理的地表水或地下水)、净化水、软水或纯水几个阶段:
1)直流供水冷却系统。
这是一种最廉价的方式,但有许多缺点:
造成水管腐蚀、结垢;
由于水中微生物多而在冷却水管内繁殖,造成水管堵塞:
耗费大量的水资源和电能,对地表水体的热污染非常严重。
这种供水冷却方式己基本上被淘汰。
2)敞开式供水冷却系统。
这种供水方式与直流供水冷却方式相比,耗水量少,对环境污染轻,经处理后,水的结垢能力和腐蚀性大为降低,对冷却器冷却能力的破坏较小。
但因冷却水常暴露在空气中易被污染,水质的腐蚀性及微生物造成的破坏仍不可忽视,水质的稳定成为突出的问题。
3)闭环式循环冷却系统。
闭环式循环冷却系统有两种形式:
汽化冷却系统和软水密闭循环冷却系统。
其工作原理是把经软化的水变成汽、水二相混合物,利用它比水大几倍到几十倍的热交换系数从冷却构件中吸收大量的热量,除了水升温吸收的显热外,还有水汽化吸收的潜热,强化了热交换;
由于饱和汽的比重小,仅为水的1/1000,因而汽水混合物与水的比重差形成了自然循环的推动力,所以它又被称为自然循环冷却系统。
这种冷却方式的优点是:
耗水量小,基本不需要动力,即使在事故停电的情况下也可保证冷却系统的正常运行:
因使用软水,可保证构件水管不结垢,冷却强度稳定。
但因用汽化冷却的平均冷却壁温度高达250℃(水流冷却时平均为130℃左右),在高炉强化生产、炉内出现高热负荷冲击时,冷却构件有可能会因过热而被烧毁。
为适应高炉强化生产的需要,世界范围内的高炉冷却方式都在向软水密闭循环冷却系统方向发展。
一.4.2高炉冷却器的发展
(1)冷却板
冷却板的材质有铸铁、钢和铜几种类型,目前普遍应用的主要是铜冷却板,铜冷却板的优点为:
①对耐火材料提供良好的支撑作用:
②由于铜的高导热性,使冷却强度大大增加,砌体寿命延长;
③损坏的冷却板易于从炉体外部更换。
其缺点为:
①只能冷却所在炉壳的局部位置,冷却面积相对狭小。
②炉役后期炉衬失去后,冷却板突出,侵占炉容,阻碍炉料运动;
③铜的机械强度在温度超过130℃时很快降低,破损极快。
④对于全冷却板高炉,炉壳因开孔较多而导致应力集中。
尽管有这些缺点,全冷却板高炉也取得了较好的炉龄指标,如日本君津3号高炉寿命为10年零8个月,单位产铁量达7906t.m³
,改进后预计寿命可达15年。
宝钢1号和攀钢4号高炉也引进了新日铁密集式冷却板,使用情况良好[12]。
在冷却板形式方面,最早的设计是双通道冷却板,该冷却板的冷却水通道面积大,水流速低,换热系数低,冷却板的前端常因冷却强度不足导致其温度升高而破损。
为保证铜冷却板的机械强度,必需使冷却板温度低于130℃。
要达到这种冷却效果,则需使冷却板前端通道内水流速达到1.1~1.5m/s,因而产生了多通道冷却板,以保证在耗水量不变的条件下提高冷却水流速,从而提高其冷却强度。
为解决因冷却板前端破损导致的冷却板失效问题,又设计出了双室多通道冷却板(即两路进水,两路出水)。
当一室破损时,另一室可继续起冷却作用。
目前最新设计的冷却板是单室六通道铜冷却板,冷却强度极高,常用于风口至炉身下部之间的高热负荷区域。
(2)冷却壁
冷却壁能够在大部分热量到达炉壳之前将其带走,从而能有效地保护炉壳,使其免受热影响。
目前,国内外高炉冷却设备发展的趋势是以冷却壁和板壁结合为主。
目前,传统的灰铸铁材质的高炉冷却壁正在逐步淘汰,现多为球墨铸铁材质。
随着高炉强化熔炼水平的提高,球墨铸铁冷却壁越来越难以满足要求。
铸钢冷却壁作为新一代高炉冷却壁,由于材质与冷却水管材质相近,与球墨铸铁冷却壁相比,具有伸长率高、抗拉强度大、熔点高、抗热冲击性强及整体导热性能好等优点,应用范围逐步扩大。
高导热性的紫铜冷却壁的国产化及应用也得到很快的发展。
国外早在1982年就开始对铸钢冷却壁进行了研究和开发。
国内武钢设计院,钢铁研究总院等单位在“八五”、“九五”期间对钢冷却壁进行了大量的研究开发工作。
现在国内有部分钢铁企业使用钢冷却壁,如济钢、南钢和鞍钢等,效果较好。
但由于钢液温度高,在浇注、凝固过程中,冷却水管很容易发生变形和熔化穿透,这一难题一直没有得到有效解决,使铸钢冷却壁工业规模化生产应用受到一定的影响
近年来尽管国内有不少单位在冷却壁的结构、材质、制造方法及提高冷却效果上作了不少有益的探索。
但囿于原有的认识基础和制造条件,还没有形成一整套有效的生产长寿型冷却壁的设计及制造技术。
国外高炉冷却壁的设计及制造技术发展较快,尤其以日本新日铁为代表在引进前苏联冷却壁制造技术的基础上,经过不断完善和开发,已把高炉一代炉役寿命提高到15年以上。
铜冷却壁自开发至今20余年,已经在多达40余座高炉上使用,这说明此项新技术在生产中已经得到了充分的考验,已经被大家所认同。
在高炉上试用成功使人们对铜冷却壁有了新的认识,在高炉上的使用也从开始时的一段逐步扩大到3段、5段,甚至更多,从炉身下部扩大到炉腹、炉腰。
根据有关资料介绍:
不莱梅钢铁厂2号高炉(3550m³
),在大修时使用了8段铜冷却壁,除了炉腹、炉腰、炉身各两段外,炉缸还用了两段。
其中部分铜冷却壁为上一代使用过的旧铜冷却壁,磨损仅为1mm,经清洗后重新使用。
这些情况说明了铜冷却壁已进入普遍推广阶段,使用范围也在扩大,更令人们振奋的是它可以用到第2代炉役上,是一种长寿的冷却设备。
2005年,武钢机制公司生产的铸铜冷却壁已经用于武钢7号高炉,并计划在4号、2号、5号高炉的新建或大修中使用。
由于铜冷却壁的成本太高,与中小企业现有的承受能力不相适应,推广应用铸钢冷却壁,将会取得了较好的效果。
铜冷却壁不仅具有性能优势,而且在实际应用过程中,可以显著降低炼铁成本,呈现出极强的应用后劲。
随着铜冷却壁的国产化进程的加快,成本的不断降低和技术的不断成熟,可以预见,铜冷却壁在我国的使用,特别是在大型高炉上的使用将会不断加快。
纵观冷却壁的发展过程,包括材质和结构两方面的改进。