PFMEA制程潜在失效模式及后果分析Word格式文档下载.docx
《PFMEA制程潜在失效模式及后果分析Word格式文档下载.docx》由会员分享,可在线阅读,更多相关《PFMEA制程潜在失效模式及后果分析Word格式文档下载.docx(23页珍藏版)》请在冰点文库上搜索。
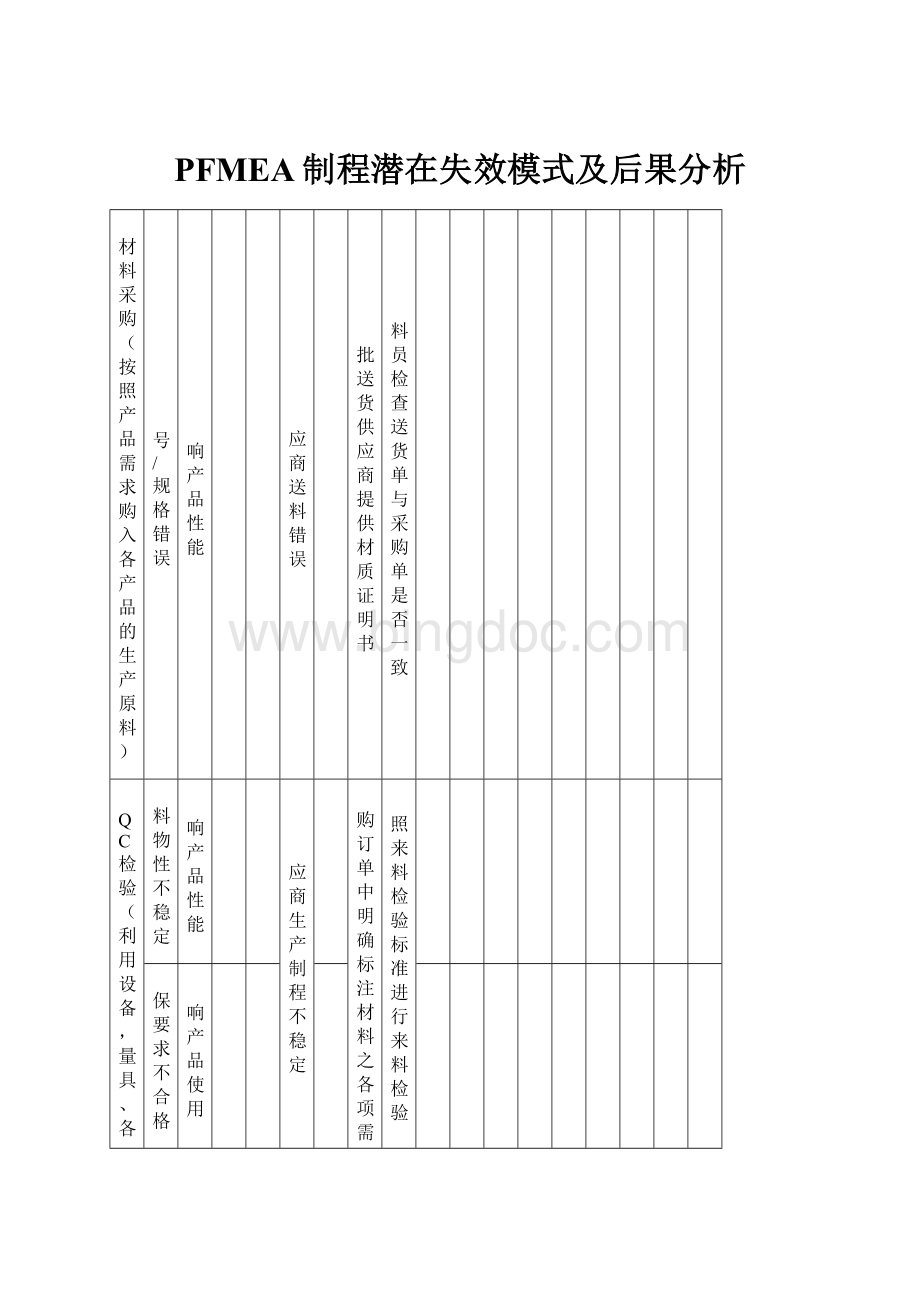
领错材料,影响后工序生产
放置区域划分不明,无隔离区域标识
材料分区域放置,各材料上方明确标识牌号、批号、供应商等信息
管理人员定期巡检确认
45
标识单填写错误
岗前培训,技能培训实施
变质
仓库贮存条件与产品要求不符
仓库的温湿度管理设定
温湿度记录表填写,1次/天
超过原材料贮存有效期
材料定期盘点
材料盘点,1次/月
领料(按照生产计划从仓库领取后工序用材料)
领错材料
材料标识错误
入库前材料上贴来料管理票
配料(将领取材料按一定配方比例称重、分类的过程)
配料时各组分比例错误
称量器具失准
量具的定期点检
定期点检:
1次/天,定期校正:
1次/半年
30
员工配错重量
员工岗前培训,技能培训实施
管理人员监控实施
炼胶(将配好粉状材料通过设备,工艺转化为一定尺寸的块状体)
色差
材料配比错误
按照《配方表》作业
每批次对比标准样板
18
材料混合不均匀
按照《混炼操作工艺卡》作业
硬度不稳定
每批次进行硬度测试
胶料存放时间过长
硫化成型不良增加
放置时间记录错误
36
分散不均
搅拌时间不足或薄通次数不够
按照.《混炼操作工艺卡》作业
每批次按快检标准检测
裁切(通过设备,在一定的工艺参数条件下转化为各规格的胶条)
长、宽、厚度不符合要求
影响硫化成型生产
裁切刻度未调试精准
按照胶料裁切标准作业
按照裁切标准QC检验记录
12
硫化成型(将备好的胶料,通过设备、摸具,在一定的工艺参数条件下转化为各形状的产品)
尺寸不合格
影响产品装配使用
成型压力、温度过高或不足
按照《成型操作工艺卡》工艺参数生产
1.QC首件检验实施2.生产过程中自检实施
模具老化,模腔受损
生产前模具自检
材料收缩率不稳定
收缩率检测/每手料
外观缺陷
生产工艺条件设定错误
1.QC首件检验2.生产过程中自检实施
生产操作不规范
20
机器动作异常
机器设备的定期点检,保养及测评
1.机器点检:
1次/天2.QC定期监察机器设备点检、保养及维护记录
生产环境不符合要求
产品有污染或交叉污染
非指定机器,场所生产
1.生产计划指定FCM车间生产
生产计划,管理人员监控实施
现场5S管理不足
2.严格按照《GMP操作规范》实施
IPQC检验(利用量具,检验标准等检验产品)
误判
导致不合格品流出
质量判定标准不明确
1.按《QC工程表》作业
2.签发标准生产样板和限度样板参照比对
3.检测设备的定期鉴定/校准/维护/保养
QC抽样检验
测量误差
48
修边(将成型后产品飞边清理干净的过程)
冲切治具刀口损伤
1.按《后加工作业指导书》作业2.岗前培训,技能培训实施3.参照标准样本自检
QC,管理人员巡查指导
漏修
人为作业失误
24
二次硫化(通过设备,在一定工艺条件下烘烤产品的过程)
硫化不足
不能满足环保和食品安全要求。
温度偏低、时间不足
按照《后加工作业指导书》作业
1、操作员每车自测1次
2、QA每车记录监控2次,遇异常反馈和跟进
90
1、设置参数固定,在温度达到要求方才开始计时(计时器自动计时开始)
2、增加报警器
生产/技术部
行政管理维修课。
2011-05-25
1、设置参数固定,温度达到要求后计时器开始自动计时
2、报警器设置
排气不充分
水煮(通过设备、按一定的工艺参数用沸水煮产品的过程)
异味
时间不足
QA监测温度和排气记录:
1次/批
FQC检验(利用检验标准检验产品的过程)
漏检
人为失误
品质意识培训
QC抽样检查
包装(将检查后合格品按一定的标准装入包装袋(箱)中的过程)
包装数量错误
出货数量与订单不符
员工点数错误
1.按照《包装作业指导书》作业2.包装后称重确认
标签错误
出货产品类别与订单不符
标签填写错误
按照《包装作业指导书》作业
包装材料错误
放置,运输过程中造成产品外观缺陷
包装方式不明确
批次混淆
影响产品追溯
标识填写错误
尾数记录错误
按照《尾数管理规定》作业
仓库(将包装后产品移动至仓库放置、贮存的过程)
违规摆放
外箱挤压变形导致产品变形
负荷过重超出纸箱承受强度
1.按照《仓库管理规定》放置产品2.员工岗前培训,技能培训实施
标识错误
出货产品与订单不符
摆放区域划分不清楚,无隔离区域标识
16
OQC检验(利用量具,检验标准等检验产品的过程)
按照待出货产品清单检验产品
填写出货检验记录表
出货(将合格产品送付客户指定场所的过程)
产品移动错误
影响客户使用
产品标识错误
每箱产品贴上成品票
仓管员检验实物与清单是否一致
产品损坏
不合格品流出到客户处
运输途中包装破损
产品移动过程中按《产品放置规定》作业
本司人员进行送货与交货确认
Severity:
对可能引起的后果严重程度的评估等级
后果
判定准则:
后果的严重度
严重度
无警告的严重危害
可能危害机器或装配操作者,潜在失效模式严重影响产品安全运行或包含不符合政府法规项,严重程度很高.失效发生时无警告。
有警告的严重危害
可能危害机器或装配操作者,潜在失效模式严重影响产品安全运行或包含不符合政府法规项,严重程度很高,失效发生时有警告。
9
很高
生产线严重破坏,可能100%的产品得报废,产品系统无法运行,丧失基本功能,顾客非常不满。
高
生产线破坏不严重,产品需筛选部分(低于100%)报废,产品系统能运行,但性能下降,顾客不满意。
7
中等
生产线破坏不严重,产品需筛选部分(低于100%)报废,产品系统能运行,但舒适性或方便性项目失效,顾客感觉不舒适。
低
生产线破坏不严重,产品需要100%返工,产品或系统能运行,但有些舒适性或方便性项目性能降下,顾客有些不满意。
很低
生产线破坏不严重,产品经筛选,部分(少于100%)需要返工,装配或其它等项目不符合要求,多数顾客发现有缺陷。
轻微
生产线破坏较轻,部分(少于100%)需要在生产线上其它工位返工,装配或其它等项目不符合要求,有一半顾客发现有缺陷。
很轻微
生产线破坏轻微,部分(少于100%)产品需要在生产线上原工位返工,装配或其它等项目不符合要求,很少顾客发现有缺陷。
无
没有影响
Occurrence:
产生失效的潜在可能性的评估等级
失效发生的可能性
每1000PCS产品,可能的失效率
CPK
频度等级
很高:
失效几乎是不可避免
≥100PCS
<0.33
高:
经常发生
20PCS
≥0.51
50PCS
≥0.33
10PCS
≥0.67
中等:
时有发生
5PCS
≥0.83
低:
很少发生
0.5PCS
≥1.33
2PCS
≥1.00
很低:
基本上不会发生
0.1PCS
≥1.50
1PCS
≥1.17
极低:
不会发生
<0.01PCS
≥1.67
Detection:
查找失效原因的难易程度的评估等级
探测性
评价准则
可能发生情况
不易探测度数
几乎不可能
问题出现后,现有的控制方法无法发现
不能检测或不用检查
很微小
问题出现后,检查发现的可能性很微小
只有在出货前检验工序可能发现
微小
问题出现后,检查发现的可能性微小
仅仅目视检查
很小
问题出现后,检查发现的可能性很小
双重的目视检查
小
问题出现后,检查发现的可能性小
通过图表方法控制,比如做统计分析
问题出现后,检查发现的可能性中等
在产品离开生产区后,借助检测设备进行检查
中上
问题出现后,检查发现的可能性中上
在后工序可以发现;
在试生产或首件检查时可以发现
问题出现后,检查发现的可能性高
在该工序就可以发现或在后工序通过多层次检查都不可能接受的不良
问题出现后,检查发现的可能性很高
在本工序生产自检或自动化检测(辅助设备)都可以发现不可能流出不良品
几乎肯定
问题一以出现就肯定可以立即发现
通过防错(防呆)措施确保不能发生
●RPN=S×
O×
D(RPN等于S乘O乘D的乘积)
编制/工程师
审核/生产经理
审核/品质经理
审核/工程经理
核准/技术经理