铝阳极氧化着色工艺规程.docx
《铝阳极氧化着色工艺规程.docx》由会员分享,可在线阅读,更多相关《铝阳极氧化着色工艺规程.docx(24页珍藏版)》请在冰点文库上搜索。
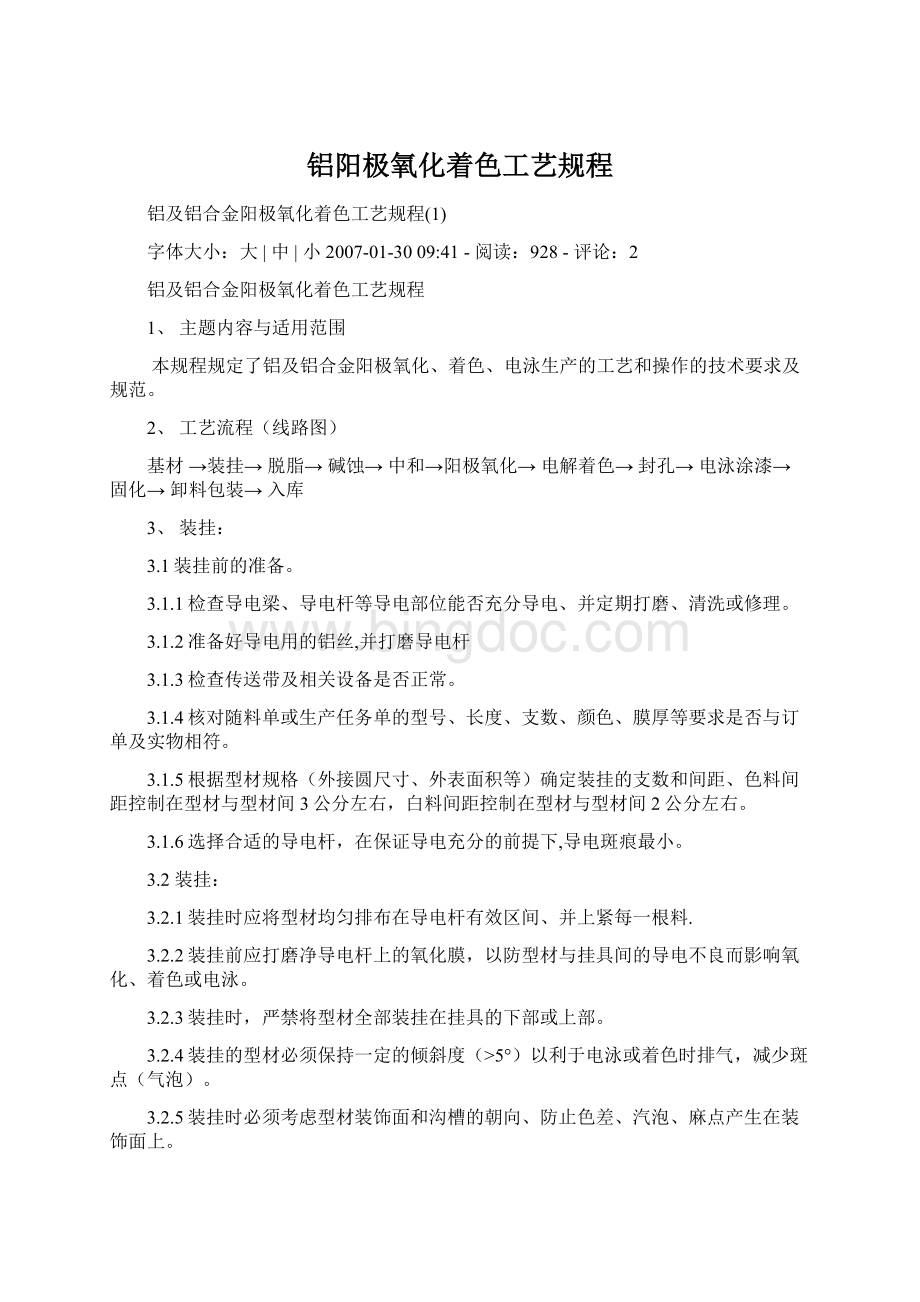
铝阳极氧化着色工艺规程
铝及铝合金阳极氧化着色工艺规程
(1)
字体大小:
大|中|小2007-01-3009:
41-阅读:
928-评论:
2
铝及铝合金阳极氧化着色工艺规程
1、主题内容与适用范围
本规程规定了铝及铝合金阳极氧化、着色、电泳生产的工艺和操作的技术要求及规范。
2、工艺流程(线路图)
基材→装挂→脱脂→碱蚀→中和→阳极氧化→电解着色→封孔→电泳涂漆→固化→卸料包装→入库
3、装挂:
3.1装挂前的准备。
3.1.1检查导电梁、导电杆等导电部位能否充分导电、并定期打磨、清洗或修理。
3.1.2准备好导电用的铝丝,并打磨导电杆
3.1.3检查传送带及相关设备是否正常。
3.1.4核对随料单或生产任务单的型号、长度、支数、颜色、膜厚等要求是否与订单及实物相符。
3.1.5根据型材规格(外接圆尺寸、外表面积等)确定装挂的支数和间距、色料间距控制在型材与型材间3公分左右,白料间距控制在型材与型材间2公分左右。
3.1.6选择合适的导电杆,在保证导电充分的前提下,导电斑痕最小。
3.2装挂:
3.2.1装挂时应将型材均匀排布在导电杆有效区间、并上紧每一根料.
3.2.2装挂前应打磨净导电杆上的氧化膜,以防型材与挂具间的导电不良而影响氧化、着色或电泳。
3.2.3装挂时,严禁将型材全部装挂在挂具的下部或上部。
3.2.4装挂的型材必须保持一定的倾斜度(>5°)以利于电泳或着色时排气,减少斑点(气泡)。
3.2.5装挂时必须考虑型材装饰面和沟槽的朝向、防止色差、汽泡、麻点产生在装饰面上。
3.2.6易弯曲、变形的长型材,在型材的中间部位增加一支挂具或采用铝丝吊挂以防型材间碰擦或触碰槽内极板,而擦伤或烧伤型材表面。
3.2.7选用副导杆时,优先选用截面小的副杆,采用铝丝绑扎时,一定要间隔均匀,上紧铝丝防止因料移动而引起大面积的擦伤。
3.2.8截面大小、形状悬殊的型材严禁装挂在同一排上。
3.2.9装挂或搬运型材,必须戴好干净手套,轻拿轻放、爱护、防护好型材表面,严禁野蛮操作。
3.2.10装挂或搬运型材时必须加强自检和互检,不合格的型材严禁装挂,表面沾有油污或铝屑(毛刺)的型材必须采取适当的措施处理干净。
3.2.11剔除不合格型材后,必须按订单支数及时补足。
3.2.12装挂区的型材不宜存放太久,以防废气腐蚀型材表面。
3.2.13认真填写《装挂记录》和《氧化工艺流程卡》上装挂部分的记录,准确计算填写每挂氧化面积,随时核对订单,确保型号、支数、颜色不出差错。
3.2.14认真做好交接班手续和工作区的环境卫生。
4、氧化台生产前的准备工作:
4.1检查各工艺槽的液面高度,根据化验报告单调整各槽液浓度,确保槽液始终符合工艺要求,并经常清除槽液中的污物。
4.2检查行车、冷冻机、整流器、循环酸泵、水泵、转移车、固化炉等设备是否正常,如有异常应及时排除,严禁带病运行。
4.3检查纯水洗槽和自来水洗槽的PH(或电导率)和洁净度、不符合工艺要求的应及时更换或补水溢流。
4.4打开碱蚀、热纯水槽、封孔槽的蒸汽或冷却水,打开氧化槽、着色槽、电泳槽的循环冷却系统,确保槽液均匀、温度达到工艺要求。
4.5检查罗茨风机和抽、排风机,并在生产前开启。
4.6认真核对《氧化工艺流程卡》,明确生产要求,准备好比色用色板。
5、氧化台操作的通用要求:
5.1每次吊料不准超过两挂,并且两挂之间必须保持一定的间距,以防型材之间的碰擦伤。
5.2型材吊进、吊出槽液时必须斜进、斜出,倾斜度应控制在30°左右。
5.3掉入槽内的型材必须及时取出补挂在排上,损伤报废的
型材必须及时通知装挂组按订单补足支数。
5.4除碱蚀和着色外,型材吊出槽液后应流尽槽液以减少浪费和污染。
5.5当吊料转移必须跨越其它型材时,必须保持转移型材的水平度,以减少型材上的槽液流下,污染型材和导电梁。
5.6每道工序均应及时认真填写《氧化工艺流程卡》,并签字。
6、脱脂:
6.1工艺参数
槽液成分:
酸性脱脂剂2~3%
槽液温度:
室温
脱脂时间:
1~3min
6.2操作要求:
6.2.1核对工艺流程卡,明确生产要求,同一颜色,同一型号,同一订单或相近规格的型应同时或优先吊入脱脂槽,以方便后道工序的操作。
6.2.2脱脂结束时,应及时将型材吊出脱脂槽,以防型材表面起砂。
6.2.3脱脂后的型材表面应均匀湿润,保持水膜在30S内不破裂,水流不程线滴流方可进入下一工序槽,并经二级水洗后才能转入碱蚀工序。
6.2.4水洗槽液面应无油污飘浮
7、碱蚀:
7.1工艺参数:
槽液成分:
平光碱蚀砂面碱蚀
NaOH:
40~50g/l45~60g/l
添加剂(NaOH的):
1/12~1/151/6~1/8
槽液温度:
40~45℃45~55℃
碱蚀时间:
1~3min10~30min
7.2操作要求:
7.2.1碱蚀时,应打开送风排风机。
7.2.2碱蚀结束时应尽快吊出型材,流尽槽液后立即转移至水槽水洗,以防型材表面产生碱蚀斑纹或流浪。
7.2.3严格控制碱蚀工艺参数,确保碱蚀后的表面质量均匀一致。
7.2.4碱蚀后的型材必须经二级溢流水洗、上下移动、反倾斜充分洗净型材表面和内孔中的碱液,以防残留碱液污染其它槽液。
镁合金的前处理及氧化处理
字体大小:
大|中|小2006-12-1612:
57-阅读:
111-评论:
0
镁合金压铸件的表面处理及氧化处理
按照表面成膜过程中有无外加电压作用,将现有镁合金压铸件的表面处理技术归纳为化学成膜技术和阳极氧化成膜技术二大类。
分别介绍了化学成膜技术中的铬化处理、磷化处理、锌置换处理、化学腐蚀处理等4类表面处理技术和阳极氧化成膜技术中的常规阳极氧化、等离子体微弧阳极氧化等2类表面处理技术,同时还简要地介绍了作者新近开发的镁合金压铸件交流等离子体微弧氧化处理技术,论述了上述各种技术的特点,总结了在各种表面处理过程中获得高质量膜层应注意的关键问题,并明确了镁合金压铸件表面处理技术今后的发展方向。
能源危机与环境污染问题的日益突出,使得符合"符合性能优良、可近终形加工、可回收"材料发展方向的镁合金脱颖而出,成为本世纪最受亲睐的一种应用材料。
在目前和今后相当长的一段时期内,高效、节能的镁合金压铸件仍将是镁合金的主要应用产品。
由于镁的负电性强(-2.36VSCE),在大气中的耐蚀性极差,所以在使用前必须对镁合金压铸件根据具体要求进行适当的表面处理。
在镁合金压铸件的生产成本中,表面处理这部分就占40%左右,因此表面处理对镁合金压铸件的生产和应用至关重要。
目前,镁合金压铸件的表面处理研究不尽相同,不象铝合金表面处理那样成熟和规范,这在一定程度上制约了镁合金压铸件的应用,本文拟对现有的镁合金压铸件的表面处理技术进行简要的归纳,并分析其关键技术问题和发展方向。
一.镁合金压铸件的表面处理技术
镁合金压铸件的表面一般需要依次进行预处理(清理、脱脂、酸洗等)、镀膜、涂装(喷漆、喷塑、镀金属等)等处理,通常所说的镁合金压铸件的表面处理指的是镀膜这道工艺,其主要作用是在压铸件表面形成与油漆、塑料或金属附着性能好的具有耐腐蚀性的保护膜层。
目前,在镁合金压铸领域中主要采用的是湿法表面处理方法,也就是,使用处理溶液进行的表面处理方法。
现有的表面处理技术不尽相同,我们根据成膜条件,将镁合金压铸件的表面处理技术归纳为化学成膜和阳极氧化成膜二大类,下面分别予以介绍。
表1铬化处理规范
序号配方工艺规范膜层颜色
成分含量/g/LPH值温度/℃时间/min
1铬酐(CrO3)
氧化镁(MgO)
硫酸(H2SO4)(ρ=1.84)45
8-9
0.1-1室温0.5-0.75黄色
2重铬酸钠(NaCr2O7o2H2O)
硫酸镁(MgOS4o7H2O)
硫酸锰(MgOS4o5H2O)
铬酐(CrO3)110-170
40-75
40-75
1-22-4
用CrO3调85-沸腾10-20深黑色
表2磷化处理规范
序号配方工艺规范膜层颜色
成分含量/g/LPH值温度/℃时间/min
1磷酸(H3PO4)(ρ=1.75)
磷酸二氢钡(Ba(H2PO4)3)
氟化钠(NaF)5-8(ml/L)
40-70
1-21.3-1.990-9810-30深灰色
2硫酸锌(ZnSO4oH2O)
焦磷酸钠(Na4P2O7)
氟化钠(NaF)或氟化锂(LiF)
碳酸钠(Na2CO3)30
120
3-5
5702-15
表3锌置换处理规范
序号配方工艺规范
成分含量/g/LPH值温度/℃时间/min
1硫酸锌(ZnSO4oH2O)
焦磷酸钠(Na4P2O7)
氟化钠(NaF)或氟化锂(LiF)
碳酸钠(Na2CO3)30
120
3-5
5702-15
表4化学腐蚀处理液
序号配方
成分含量/g/L
1铬酐
硝酸(70%)60-120
90-110cc/l
2氢氟酸(70%HF)54-220cc/l
表5常规阳极氧化处理规范
序号配方工艺规范
组分含量/g/L温度/℃起始电流密度最终电压/V时间/min
1铬酸
高锰酸钾20
6020-300.6130
2苛性钠
纯碱50
5020-302-35030
3重铬酸钾
磷酸二氢钠100
5050-551.5-25-630-40
4苛性钠
磷酸三钠50-55
30-3570-751.5-2430-40
表6等离子体微弧阳极氧化处理规范
序号配方工艺规范
组分含量/g/L温度/℃电流密度/A/dm2时间/min
1NaAlO21020-401530
1.化学成膜
化学成膜技术主要是指镁合金压铸件通过在化学溶液中进行一定时间的接触、利用工件与化学处理液之间的化学反应在工件表面形成保护膜层的一类表面处理技术。
主要包括铬化、磷化、锌置换和化学腐蚀等处理技术。
1)铬化处理
铬化处理就是工作在以铬酸或重铬酸盐等为主体的处理溶液中进行浸渍,使表面产生氧化镁、氧化铬或铬酸盐保护膜层的表面处理技术。
典型的处理规范如表1所示。
通常含铬离子处理液的成膜性较好,对工件的表面质量要求不高,对厚、薄工件均适用。
铬化处理膜层均匀,厚度通常为0.5-3μm,可使工件的耐腐蚀性可以提高数十倍。
镁合金的铬化处理研究开展得较多,较为成熟,但由于铬离子对人体和环境的副作用较大,所以其应用已在逐渐减少。
2)磷化处理
磷化处理就是工件在以磷酸或磷酸盐为主体的溶液中进行浸渍或采用喷枪进行喷淋,使表面产生完整的磷酸盐保护膜层的表面处理技术。
典型的处理规范如表2所示。
磷化处理液的成膜性不如铬化处理液的好,对工件的表面质量要求较高,通常不太适合于表面质量差的薄壁压铸件(壁厚小于2mm)的表面处理。
磷化处理膜层的厚度较大,作为油漆底层,可使漆膜的粘附力、耐潮湿性和耐蚀能力提高几十倍至几百倍。
镁合金磷化处理的研究较少,目前的应用十分有限。
3)锌置换处理
锌置换处理就是工件在以锌盐为主体的溶液中(通常加入焦磷酸盐)进行浸渍,使表面进行锌置换,从而产生完整的保护膜层的表面处理技术。
典型的处理规范如表3所示。
锌置换膜层不但有良好的耐腐蚀性,而且可以明显提高金属的附着性能,进行锌置换处理后,可进行触击电镀铜、镀镍、镀铬等处理,所以锌置换处理主要用于镀金属前的压铸件的表面处理。
4)化学腐蚀处理
镁合金压铸件的化学腐蚀处理分二步进行,第一步采用铬酸-硝酸系溶液进行腐蚀;第二步在氢氟酸系溶液里进行处理,以除去第一步处理时生成的铬酸膜,同时在工件表面形成氟化镁膜层。
典型的处理液如表4所示。
由于化学腐蚀使工件表面凸凹不平,所以难于得到平滑光亮的膜层,但由于提高了膜层的附着性,所以经化学腐蚀过的表面,可以直接进行镀镍、镀铬等处理。
2.阳极氧化成膜
阳极氧化成膜主要是指镁合金压铸件作为阳极、在外加电压的作用下、通过在一定温度的溶液中进行一段时间的处理、利用工件与处理液之间的电化学反应在工件表面形成保护氧化膜层的一类表面处理技术。
阴极通常为槽体或不锈钢板。
阳极氧化成膜主要包括常规阳极氧化和等离子体微弧阳极氧化处理技术。
1)常规阳极氧化处理
常规阳极氧化处理也就是工件在低电压作用下进行的阳极氧化处理技术。
典型的处理规范如表5所示。
通常经过常规阳极氧化处理后,工件表面形成较为致密的氧化膜层,该膜层主要由氧化镁与六方氢氧化镁构成,与基体结合良好。
与化学成膜处理相比,常规阳极氧化处理膜层的耐蚀性、耐磨性好、机械强度高,工件的尺寸精度几乎不发生影响,在某些使用情况下可省去涂装工艺,直接可作为最终处理,因此常规阳极氧化处理技术得到了较为广泛的应用。
2)等离子体微弧阳极氧化处理
将常规阳极氧化处理的电压升高到一定值,在阳极区将产生等离子体微弧放电,微弧直径一般在几微米至几十微米之间,在工件表面的停留时间约为几十毫秒,相应的温度可高达几千度,可使周围的液体汽化,形成高温高压区,在该区域内,在电场的作用下,可产生大量的电子和正负离子,因此可产生特殊的物理化学作用,使生成的氧化膜成为陶瓷质的有序结构(主要由立方结构的氧化镁构成),这种特殊的镁合金压铸件表面处理技术就是等离子体微弧阳极氧化处理技术。
这是近年来刚刚探索出来的一种崭新的处理方法,典型的处理规范如表6所示。
因为微弧放电会使处理液的温度不断升高,所以为了保证处理液的温度恒定,进行表面处理时还需要采用循环冷却系统。
由于得到了陶瓷膜层为基体原位生长,因此完整、致密、与基体和油漆的附着性能好,具有优良的耐蚀性、耐磨性和电绝缘性。
目前采用等离子体微弧阳极氧化处理技术可根据具体要求,制备出装饰型、保护型、功能型等陶瓷表面,已应用于实际生产,进一步的研究正处在不断的探索中。
3.交流等离子体微弧氧化处理技术
作者近半年来针对镁合金压铸件的表面处理进行了研究,开发出了交流等离子体微弧氧化处理技术及相应的处理溶液。
该技术采用工频交流电对镁合金压铸件进行等离子体微弧氧化处理,与前述的阳极氧化处理相比,该技术不需用直流电源、设备简单,工件的表面处理时间大大缩短,其处理效率较其它方法提高了20倍以上,在处理镁合金压铸手机外壳时,一般在1分钟处理时间之内就可达到表面处理的全部要求。
在实际生产中的初步应用已经证明交流等离子体微弧氧化处理技术是一种非常实用、有前途的镁合金压铸件表面处理技术。
目前,该技术在其它方面的应用正在研究当中,相信不久将会取得可喜的成果。
二.表面处理的关键技术问题
镁合金压铸件表面处理的目的,就是根据具体要求,采用合适的技术,得到满足要求的高质量的膜层。
由于目前现有的各种表面处理技术还分别存在各自的问题,所以要达到此目的,应该对不同处理技术中的关键问题有所了解。
1.化学成膜中的关键技术
由于化学成膜是完全依靠处理液与工件之间的化学反应来进行的,不象阳极氧化成膜那样有外加电压的作用,所以要形成高质量的膜层,除了要严格遵守各个环节的操作规程以外,应对压铸件表面万分的均匀性予以充分的重视。
只有成分均匀的表面才能形成均匀的处理膜层,所以应确保镁合金液的成分均匀、压铸件的成分均匀、压铸件表面充分的清洁,尤其是采用成膜性能较低的无铬处理液对薄壁(小于2mm)压铸件进行处理时,对影响压铸件表面成分均匀性的合金液成分设计、压射速度、型模条件等要进行严格控制,力保压铸件表面成分的均匀、稳定。
2.阳极氧化成膜中的关键技术
由于阳极氧化成膜是在外加电压的作用下进行的,所以该技术对压铸件的表面质量要求不象化学成膜那样苛刻,对于某一表有时甚至不进行预处理面的压铸件,总能够找到合适的处理电压和处理时间来得到高质量的膜层。
对于阳极氧化成膜,最关键的问题就是处理液的有效性问题。
对压铸件表面质量要求的降低,使脱模剂有机会进入处理液,如果脱模剂和处理液的选择不匹配,将导致处理液的迅速失效,另外,在等离子体微弧氧化成膜中,处理液的温度会迅速升高,这种温升将导致某些处理液的失效,影响表面处理效果。
因此合理选择脱模剂和处理液、保持处理液温度的恒定是阳极氧化成膜的关键技术问题。
三.今后的发展方向
目前的镁合金压铸件表面处理技术各有千秋,化学成膜设备简单、操作污染小,与涂装处理相结合极有优势;阳极氧化成膜包括交流等离子体微弧氧化处理技术在内,可根据具体要求实现多种不同的处理目的,但这些技术还存在各自的问题,今后有待逐步完善和发展。
从提高表面处理质量、满足各类产品需求角度来讲,尽快开发短时、多功能而高质量成膜、可实现最终处理的新技术,将是今后的一个发展方向,等离子体微弧氧化成膜技术将会得到迅速的发展。
站在长期发展高度,从保护环境角度来讲,实现"绿色表面处理"将是今后发展的根本原则,开发对环境和操作者的无危害的处理液和相应的处理技术,将是今后的一个主要发展方向,目前处理液向无铬化的发展,已经迈出了可喜的一步。
当前,保护环境和满足各类产品需求之间还存在一定的矛盾,镁合金压铸件表面处理技术的发展有赖于二者的有机结合以及产、学、研的密切合作。
氧化膜阳极的缺陷及处理方法
字体大小:
大|中|小2006-12-1416:
08-阅读:
212-评论:
0
氧化膜阳极的缺陷及处理方法
(1)铝合金制品经硫酸阳极氧化处理后,发生局部无氧化摸,呈现肉眼可见的黑斑或条纹,氧化膜有鼓瘤或孔穴现象。
此类故障虽不多见但也有发生。
上述故障原因,一般与铝和铝合金的成分、组织及相的均匀性等有关,或者与电解液中所溶解的某些金属离子或悬浮杂质等有关。
铝和铝合金的化学成分、组织和金属相的均匀性会影响氧化膜的生成和性能。
纯铝或铝镁合金的氧化膜容易生成,膜的质量也较佳。
而铝硅合金或含铜量较高的铝合金,氧化膜则较难生成,且生成的膜发暗、发灰,光泽性不好。
如果表面产生金属相的不均匀、组织偏析、微杂质偏析或者热处理不当所造成各部分组织不均匀等,则易产生选择性氧化或选择性溶解。
若铝合金中局部硅含量偏析,则往往造成局部无氧化膜或呈黑斑点条纹或局部选择性溶解产生空穴等。
另外,如果电解液中有悬浮杂质、尘埃或铜..铁等金属杂质离子含量过高,往往会使氧化膜出现黑斑点或黑条纹,影响氧化膜的抗蚀防护性能。
(2)同槽处理的阳极氧化零件,有的无氧化膜或膜层轻薄或不完整,有的在夹具和零件接触处有烧损熔蚀现象。
这类故障在硫酸阳极氧化工艺实践中往往较多发生,严重影响铝合金阳极氧化质量。
由于铝氧化膜的绝缘性较好,所以铝合金制件在阳极氧化处理前必须牢固地装挂在通用或专用夹具上,以保证良好的导电性。
导电棒应选用铜或铜合金材料并要保证足够接触面积。
夹具与零件接触处,既要保证电流自由通过,又要尽可能减少夹具和零件间的接触印痕。
接触面积过小,电流密度太大,会产生过热易烧损零件和夹具。
无氧化膜或膜层不完整等现象,主要是由于夹具和制件接触不好,导电不良或者是由于夹具上氧化膜层未彻底清除所致。
(3)铝合金硫酸阳极氧化处理后,氧化膜呈疏松粉化甚至手一摸就掉,特别是填充封闭后,制件表面出现严重粉层,抗蚀性低劣。
这一类故障多发生在夏季,尤其是没有冷却装置的硫酸阳极化槽,往往处理1-2槽零件后,疏松粉化现象就会出现,明显地影响氧化膜的质量。
由于铝合金阳极氧化膜电阻很大,在阳极氧化工艺过程中会产生大量焦耳热,槽电压越高产生热量越大,从而导致电解液温度不断上升。
所以在阳极氧化过程中,必须采用搅拌或冷却装置使电解液温度保持在一定范围。
一般情况下,温度应控制在13~26℃,氧化膜质量较佳。
若电解液温度超过30℃,氧化膜会产生疏松粉化,膜层质量低劣,严重时发生“烧焦”现象。
另外,当电解液温度恒定时,阳极电流密度也必须予以限制,因为阳极电流密度过高,温升剧烈,氧化膜也易疏松呈粉状或砂粒状,对氧化膜质量十分不利。
(4)偶然发生铝合金硫酸阳极氧化后氧化膜暗淡无光,有时产生点状腐蚀,严重时黑色点状腐蚀显著,导致零件报废,引起较大损失。
这类故障往往是偶然发生并有特殊原因造成的。
(1)在铝合金阳极氧化过程中,中途断电又重新给电,往往会使氧化膜暗淡无光,2;而中途停电零件在清洗槽停留过久,清洗水槽酸度过高,水质不净,含悬浮物、泥砂等较多,往往会使铝合金制件发生电化学腐蚀,发生点状腐蚀黑斑等。
有时向电解液中添加自来水,水经漂白粉处理且Cl-含量超标或有时盛装过HCl的容器未经彻底清洗又盛装硫酸,都会使阳极氧化电解液中混人超量的Cl-,从而导致铝合金零件阳极氧化产生点状腐蚀使产品报废等。
(5)工件局部位置电击烧伤或穿孔
1.工作物和阴极接触发生短路,放置工作物於处理槽内时,注意与阴极之距离,避免发生接触。
2.工作物彼此之间接触发生短路。
加大工作物间距离。
3.工作物件和夹具接触不良。
夹具使用前须加以清洗,与工作物间须夹紧。
(6)氧化膜层疏松,用手就可擦掉
1.电解液温度太高设法降低温度,进行搅拌或开动冷却设备,并控制温度差在20±2℃内。
2.氧化处理时间太久。
缩短氧化时间。
3.工作电流密度太高。
降低电流密度。
(7)氧化膜带红色斑点或整个表面或局部表面发红
1.导电棒和夹具之间的接触不好令铜沉积在铝表面。
.改善导电棒与夹具的材质改用纯铝材制作导电杆,。
2.氧化过程中有断电现象,.氧化过程注意观察电流表,电压表的变化。
(8)氧化膜暗淡不够光亮或烧焦现象
1.工作物件在槽中长时间无给电,或断电后又给电形成双层氧化膜。
经常检查纠正与电器维修,严格氧化处理时间控
2.硫酸溶液内溶存的铝离子增加导致氧化膜的透明性变差,及溶液内阻增加最后发生烧焦现象。
检验处理液中的铝量,硫酸液中含铝量以10g/L左右为宜。
新配槽液需添加12~13gm/l的硫酸铝。
(9)氧化膜有黑斑或黑条纹
1.电解液中有悬浮的杂质清理表面悬浮杂质。
2.工作物件表面有油渍,或其它污染物。
彻底纠正除油液成份;确实执行前处理。
3.电解液中含铜和铁杂质太多。
分析后除去或更新部份电解液。
4.电解后工作物未洗乾净就进行封孔。
电解后工作物要立即清洗乾净,避免处理液或杂质残留於氧化膜表面
(10)氧化膜局部表面被腐蚀
1.氧化后氧化膜上的电解液未洗乾净。
加强氧化后的洗涤。
2.深凹处藏有电解没清洗乾净。
对盲孔,细孔工件可用高压气吹出孔内残余的电解液并加强氧化后的洗涤。
3.电解液没清洗乾净就进行封孔处理。
应加强氧化后的洗涤。
(11)无色的工作物件经热水填充处理易沾上手印,水印,膜层发白
1.封孔的温度和时间不够按适宜条件进行。
2.PH值不当调整PH值。
3.溶液氢氧化铝太多。
更换用水。
4氧化温度过高,氧化膜孔呈开口壮
(12)氧化膜粗糙
1氧化电流过大,降低氧化电流及氧化槽温度
2,挤压比过小,速度过快,锭温度高使挤压出口温度高
3,淬火温度不够
4,锭坯原始晶粒粗
(13)黑灰色条带
1,铝锭表面油污或油灰流入型材的表面
2,压佘,
3,锭的温度低,而挤压筒的温度较高,使坯锭表皮物流入工件的表面,表皮物一般含较高的合金元素及不溶性渣
4,挤