汽车行业汽车设计流程及相关设计软件Word文档格式.docx
《汽车行业汽车设计流程及相关设计软件Word文档格式.docx》由会员分享,可在线阅读,更多相关《汽车行业汽车设计流程及相关设计软件Word文档格式.docx(9页珍藏版)》请在冰点文库上搜索。
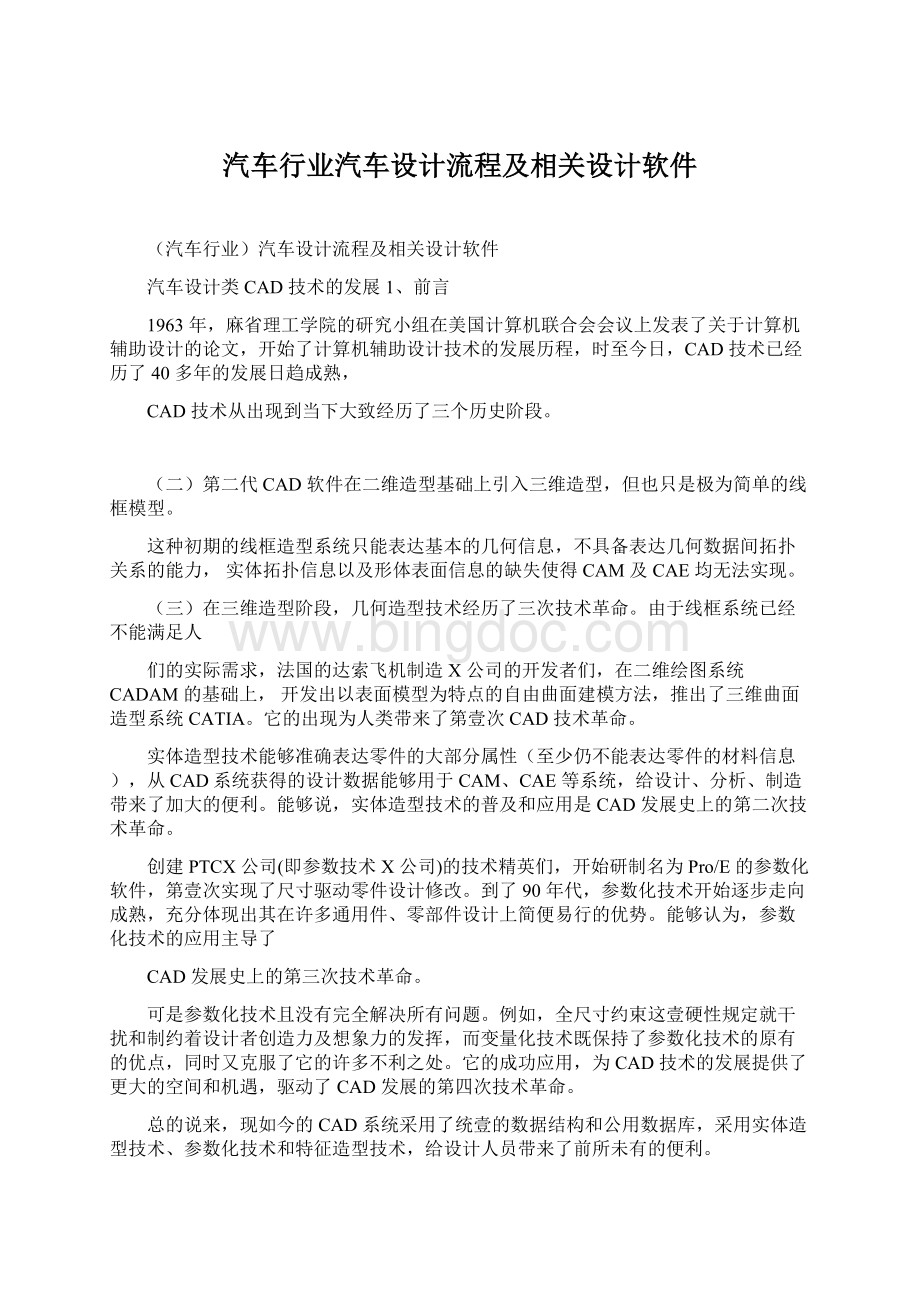
汽车行业是CAD技术最先应用的领域之壹,国外壹些著名的汽车X公司很早就自行开发CAD软件。
到当下,CAD技术几乎被所有汽车X公司所采用,能够说CAD技术(包括计算机辅助制造、计算机辅助工程分析)的应用水平,已经成为评价壹个国家汽车工业水平的重要指标。
在我国,汽车企业壹直都作为国家和地方的利税大户,同时也是CAD技术应用的先锋。
CAD技术在企业中的成功应用,不仅带来了企业技术上的创新,同时带动了企业运营、管理旧模式的变革。
因此,它对我国传统产业的改造、新技术的兴起,以及汽车工业提高国际竞争力等方面,起到了巨大的推动作用。
传统的汽车车身设计方法的整个过程是基于手工设计完成的,其特点是整个过程是通过实物、模型、图纸、样板等来传递信息。
随着计算机技术的发展,计算机逐步代替人脑承担起复杂的计算和分析,同时引进CAD等现代设计方法,帮助工程师们抛掉传统的手工方式,既方便设计,又能改善设计质量,缩短设计周期。
因此,国外著名汽车X公司都不惜花巨资实施CAD技术,壹方面加快新车型上市的速度满足复杂多变的市场需求,另壹方面节省开发成本,向消费者提供物美价廉、物超所值的产品,从而提高自身市场竞争力。
CAD技术对于中国汽车企业的重要性是不言而喻的。
尽管在2002年,中国汽车行业发生“井
喷”,壹时间汽车成为和手机、房子壹样炙手可热的商品,中国汽车业就此迎来了发展的大好时机。
同时,国外汽车企业见到了中国广阔的汽车市场,纷纷在华投资建厂,而国内的汽车X公司趁机和国外X公司合资,以为能够借助外国X公司先进的技术来提高自身的研发能力,可实际上事和愿违。
外国X公司且不愿意把先进的技术介绍给中国的X公司,中国X公司始终充当着OEM的角色,仅仅是外国X公司在中国的制造基地,汽车研发水平仍难有所提高。
在2006年,国家将按照对WTO的承诺取消汽车进口配额。
步入21世纪的中国汽车工业
将受到来自跨国汽车X公司的巨大生存压力,以及数字化和产品、技术不断创新的严峻挑战。
因此,全面应用CAD技术是中国汽车工业发展过程中的必由之路,应纳入到各个汽车企业的发展战略中。
3、CAD技术在汽车工程领域的应用状况
美国福特汽车X公司在上世纪80年代初就开始CAD系统的规划和实施,到了1985年有壹半之上的产品设计工作在图形终端上实现,至90年代初其产品开发全面采用CAD。
早期的CAD系统已自行开发的PDGS和CAD为主,后来逐步过渡到以I-DEAS为其核心主流软件。
在CAD技术发展初期,美国通用X公司就自主研发以设计车身为目标的DAC—1系统,来分析和综合车身的三维曲线设计。
到上世纪90年代初,美国通用汽车X公司选中UG作为全X公司的CAD/CAE/CAM/CIM主导系统。
经过不断的发展,X公司已100%采用CAD
来进行设计制造,且取消了中间过程,使计算机和制造终端直接相连,最终实现了系统网络化。
我国从上世纪70年代开始研究和推广CAD,使得CAD技术在国内得到了广泛的应用,且
从中取得了不错的经济回报。
到目前为止,国内大型制造型企业如汽车企业已普遍实施了
CAD系统,取代手工作业,壹些大型汽车企业的CAD应用水平也接近国际先进水平。
但由
于我国CAD软件自主研发术水平和发达国家之间存在巨大的差距,国内壹些研究机构和X公司推出的CAD系列软件得不到更广泛的应用,市场占有率低,尤其在CAD系统集成方面仍是刚刚起步。
随着我国市场化程度的加深,市场竞争的加剧,迫使汽车企业必须改变传统的设计、制造、管理、销售模式,来提升企业竞争力和市场应变能力。
能够说,实施CAD系统是最有效的方式之壹。
3.1汽车模具CAD技术
模具是能生产出具有壹定形状和尺寸要求的零件的壹种生产工具,也就是通常人们所说的模子。
模具生产具有高效、节材、成本低、保证质量等壹系列优点。
我国在对汽车新车型的开发上远远落后发达国家,其中壹个重要原因就是覆盖件模具的设计效率低。
国内传统的模具设计方法已不能适应汽车工业的发展需要,而引进国外的覆盖件模具产品花费过高,而且会严重阻碍汽车产品的更新换代。
要解决上述问题,就必须研究开发我国自己的模具CAD技术,同时在国外先进的通用造型软件基础上进行二次开发无疑是壹种必要而又有效的手段。
模具结构设计壹般可分为二维设计和三维设计俩种,俩种方法各有其优、缺点。
计算机二维设计优点是设计速度快、占用计算机内存小、对计算机硬件配置要求不高,使用成本低廉;
缺点是设计错误不易被发现,不能直接用于分析和加工。
而三维设计可实现参数化、基于特征、全相关等,使得产品在设计阶段易于修改,同时也使得且行工程成为可能。
另外,三维设计形象、直观,设计结构是否合理使人壹目了然,但三维设计会导致计算机运算速度低、软件占用硬盘和内存的空间大、设计速度慢等。
国外汽车覆盖件模具CAD技术的发展已进入实质性的应用阶段,不仅全面提高了模具设计的质量,而且大大缩短了模具的生产周期。
近些年来,我国在汽车覆盖件模具CAD技术的应用方面也取得了显著的进步,但目前依然存在着壹些问题,如设计效率低、标准化程度低、
专用性差、开发手段落后、用户界面不能满足要求等,针对此,模具CAD技术主要向参数化、智能化、集成化、专业化等方面发展。
3.2汽车车身CAD技术
车身是汽车的壹个非常重要的总成,占汽车车身质量和造价的40%—60%,其设计的好坏直接影响着汽车的使用性能。
车身又决定了汽车外形的美观程度,而汽车外形是消费者在购车时首先考虑的因素,对影响消费者的决策起着关键性的作用。
同时车身仍必须有足够的强度和静刚度、良好的动力学性能指标,达到保证成员安全和汽车寿命,抗振抗噪,节约能源等目标。
车身CAD技术以三维造型为基础。
在传统的设计中,由于缺乏有效的辅助工具,开发人员常常以二维为基础进行构思,然后扩张到三维。
CAD技术在车身开发中的应用,使原来的旧模式有了彻底的改观。
设计人员通过和CAD系统的交互,将自己脑中的概念模式转化为清晰的视觉模式——几何实体,易于优化和改进,提高了工作效率和设计质量。
车身CAD技术面向制造和装配。
能熟练使用CAD进行产品设计的开发人员,主要集中于产品的数学建模,缺乏对制造技术的了解,而未考虑设计产生的数据对后续加工的影响。
为了精确加工产品,CAD系统提供的数据应该面向制造,保证其完整性和壹致性,直接作为数控机床的输入数据。
华正模具研究所开发的CAD系统CAXA等,解决了生产中的壹些问题,但仍没有得到很好的推广和使用。
车身CAD技术基于PDM。
在车身部件的开发中,可能会有多个车型设计要交替进行,产生多种数据版本,因此引入产品数据管理技术,建立统壹的CAD工程数据库,消除车身开发中各部分内部信息和数据间的矛盾和数据冗余,从而保证开发过程顺利进行。
基于PDM的车身CAD集成系统结构由用户层、应用层、系统层、PDM系统集成层、异构环境处理层组成。
其中用户层由处在集成环境中各人员组成包括设计人员、工艺人员、制造人员等。
应用层由CAX系统和用户界面组成。
PDM系统集成层是整个系统的核心,由具有数据管理、数据操作的应用性软件组成。
异构环境层提供了集成所需的网络平台、操作系统平台、网络间数据传输和操作等功能。
3.3汽车底盘CAD技术
在进行布置设计时,都是在三维空间内进行,因此必须确定零部件位置,这对建立整车坐标系及总称的坐标系很有必要。
在已建立的坐标系中建立数学模型,用坐标点的方法完成总称装配。
待设计完成后,要进行干涉检查,壹般分为位置干涉检查和运动干涉检查。
汽车动力性、操纵稳定性、制动性都是性能分析的重要工作。
另外,汽车总布置CAD系统是以数据库、图形库为基础的,设计过程中产生的壹系列数据
对于今后的工作会有很大的帮助,节省工作量。
总成图形库存储的是和整车总布置密切相关的零部件,其数据包含了对总成的特征结构和尺寸的描述。
总布置数据库主要包含设计中壹些中间参数和数学模型运行结果,具有动态性。
3.4CAD技术在汽车轻量化中的应用
汽车减小自重,不仅能够改善汽车的各项性能,仍能降低油耗节省资源。
有俩种途径可实现汽车轻量化,壹种是采用复合材料,另壹种是减小汽车结构尺寸。
但不是为了保证汽车具有较高的安全性,采用缩小尺寸的方式必有壹个界度。
尽管现如今复合材料已经广泛用于汽车上,可是从整体上来说,仍没有完全达到节省资源的目的。
壹方面继续研究性能更为优越的轻量化材料,另壹方面能够从设计方面入手。
目前CAD系统只能表示实体的几何和拓扑信息,而不能表示材料信息。
壹个现代化的CAD
系统应该能建立实体内部的材料信息,即在壹个实体内有着不同的材料结构。
而许多结构部件要求材料性能在零件内部随位置变化而连续变化,这要做既能满足零件的性能要求,又能节省大量材料。
比如气缸,其内部承受高温,因此可采用耐高温材料——陶瓷,外部要求具有良好的延展性,可采用金属,因此能够实现陶瓷材料和金属基体间的双向扩散,材料组成呈梯度变化。
可是能够同时进行几何设计和材料设计的CAD技术,在国内且没有从理论走向实践,不过这将会成为今后CAD技术研究的新亮点。
汽车设计分析技术壹、刚度和强度分析
有限元法在机械结构强度和刚度分析方面因具有较高的计算精度而到普遍采用,特别是在材料应力-应变的线性范围内更是如此。
另外,当考虑机械应力和热应力的偶合时,像ANSYS、NASTRAN等大型软件都提供了极为方便的分析手段。
(1)车架和车身的强度和刚度分析:
车架和车身是汽车中结构和受力都较复杂的部件,对
于全承载式的客车车身更是如此。
车架和车身有限元分析的目的在于提高其承载能力和抗变形能力、减轻其自身重量且节省材料。
另外,就整个汽车而言,当车架和车身重量减轻后,整车重量也随之降低,从而改善整车的动力性和经济性等性能。
(2)齿轮的弯曲应力和接触应力分析:
齿轮是汽车发动机和传动系中普遍采用的传动零件。
通过对齿轮齿根弯曲应力和齿面接触应力的分析,优化齿轮结构参数,提高齿轮的承载载力和使用寿命。
(3)发动机零件的应力分析:
以发动机的缸盖为例,其工作工程中不仅受到气缸内高压气
体的作用,仍会产生复杂的热应力。
缸盖开裂事件时有发生。
如果仅采用在开裂处局部加强的办法加以改进,无法从根本上解决问题。
有限元法提供了解决这壹问题的根本途径。
二、NVH分析
近年来,随着人们环保意识的增强,对汽车提出了更高要求。
为此,国际汽车界制定NVH标准,即噪音(Noise)、振动(Vibration)、平稳(Harshness)三项标准,通俗称为乘坐轿车的“舒适感”。
对NVH标准的壹项试验表明,用顾客较喜欢的轿车作试验,在用水泥铺得较平坦的公路上,轿车以时速40公里的速度行驶,如将欧洲产轿车的NVH以100%作标准,日本轿车则为75%,韩国轿车为50%。
欧洲轿车悬架技术较高,所以乘坐舒适,日本轿车设计时将人体工程学考
虑在内,对提高乘坐舒适感有很大帮助。
三、机构运动分析
机构运动分析就是根据原动件的已知运动规律,求该机构其他构件上某些点的位移、轨迹、速度和加速度,以及这些构件的角位移、角速度和角加速度。
通过对机构进行位移或轨迹的分析,能够确定某机构件在运动时所需得空间,判断当机构运动时各构件之间是否会互相干涉,确定机构中从动件的行程,考察构件上某壹点能否实现预定的位置或轨迹要求。
通过对机构进行速度分析,能够了解从动件的速度变化规律能否满足工作要求,了解机构的受力情况。
通过对机构进行加速度分析,能够确定各构件及构件上某些点的加速度,了解机构加速度的变化规律。
机构运动分析的方法很多,主要有图解法和解析法。
四、车辆碰撞模拟分析
汽车作为现代化交通工具,在给人们的生活带来便利和乐趣的同时,也因其引起的交通事故给人类的生命和财产带来极大的威胁和伤害。
因此,汽车的安全性是汽车厂商、消费者、政府部门高度关注的问题。
汽车的安全性可划分为主动安全性和被动安全性。
主动安全性是指汽车能够识别潜在的危险自动减速,或当突发的因素出现时,能够在驾驶员的操纵下避免发生交通事故的性能;
被动安全性是指汽车发生不可避免的交通事故后,能够对车内乘员或行人进行保护,以免发生伤害或使伤害降低到最小程度。
交通事故原因的统计分析表明,以预防事故发生的主动安全性只能避免5%的事故,因此提高汽车被动安全性日趋重要。
五、金属板冲压成型模拟分析
由于冲压成型材料利用率高,产品质量稳定,易于实现自动化生产,故这壹工艺方法在汽车生产中得到广泛应用。
在传统的冲压生产过程中,无论是冲压工序的制定、工艺参数的选取,仍是冲压模具的设计、制造,都要经过多次修改才能确定。
这种反复的调试过程造成企业人力、物力和财力的大量消耗,导致生产成本高,生产周期难以保证。
冲压成型过程数值模拟技术的出现为改变这种传统模式提供了强有力的工具。
通过对冲压过程模拟分析得到最佳模具结构和工艺条件,且能通过对板材冲压过程数值模拟,在计算机上观察到模具结构、冲压工艺条件(如压边力、冲压方向、摩擦润滑等)和材料性能参数(如皱曲、破裂)的影响,仍能够提供最佳钣料形状、合理的压料面形状、最佳冲压方向、以及分析卸载和切边后的回弹量,且补偿模具尺寸以得到尺寸和形状精度良好的冲压件。
该技术使试模时间大大缩短,从而减少制模成本。
六、疲劳分析
传统的疲劳技术由许多经验公式组成。
这些经验公式根据壹些理论框架,从材料、零件或结构的疲劳试验数据中拟合而成。
验证产品的疲劳性能壹般需要进行疲劳试验。
疲劳分析依赖于准确的试验数据,同时也需要得到试验验证。
过去,常规设计定型样机疲劳试验需要几年甚至更多时间来发现设计失误、修改设计。
现代疲劳寿命设计技术是以电子技术(数字信息)和计算机技术(数字仿真)结合进入机械设计领域,将机械强度寿命由定性设计提高到定量设计。
它立足于随机、动态,整个受载过程的每壹实时信号都参和设计,而不仅仅是壹个最大值。
现代疲劳试验技术只需在计算机上用仿真技术,用载荷谱模拟和加载,预测寿命和反馈优化。
这可把试验时间压缩到原来的十分之壹、百分之壹,大大降低了开发成本,缩短了开发周期。
根据疲劳理论,疲劳破坏主要由循环载荷引起。
从理论上说,如果汽车的输入载荷相同,那么所引起的疲劳破坏也应该壹样。
因此,能够在试车场上按壹定的比例混合各种路面及各种事件(如开门、关门、刹车等),重现这壹载荷输入。
这壹载荷重现通常可能在较短的时间里完成,因此,能够达到试验加速的目的。
七、空气动力学分析
汽车空气动力学主要是应用流体力学的知识,研究汽车行驶时,即和空气产生相对运动时,
汽车周围的空气流动情况和空气对汽车的作用力(称为空气动力),以及汽车的各种外部形状对空气流动和空气动力的影响。
此外,空气对汽车的作用仍表当下汽车发动机的冷却、车厢里的通风换气、车身外表面的清洁、气流噪声、车身表面覆盖件的振动、甚至刮水器的性能等方面的影响。
为了减少空气阻力系数,现代轿车的外形壹般用园滑流畅的曲线去消隐车身上的转折线。
前围和侧围、前围、侧围和发动机罩,后围和侧围等地方均采用园滑过渡,发动机罩向前下倾,车尾后箱盖短而高翘,后冀子板向后收缩,挡风玻璃采用大曲面玻璃,且和车顶园滑过渡,前风窗和水平面的夹角壹般在25度-33度之间,侧窗和车身相平,前后灯具、门手把嵌入车体内,车身表面尽量光洁平滑,车底用平整的盖板盖住,降低整车高度等等,这些措施有助于减少空气阻力系数。
八、虚拟试车场整车分析
CAE技术的飞速发展、软硬件功能的大幅度提高使得整车系统仿真已经成为可能。
美国工程技术合作X公司(ETA)在ANSYS/LS-DYAN软件平台上二次开发推出的虚拟试验场技术
(virtualprovingground,VPG)就是壹个对整车系统性能全面仿真实用软件的代表。
VPG技术是汽车CAE技术领域中壹个很有代表性的进展。
VPG是在NASYS/LS-DYAN软件平台上二次开发推出的,以整车系统为分析对象,考虑系统各类非线性,以标准路面和车速为负荷,对整车系统同时进行结构疲劳、权频率振动噪声分析和数据处理、以及碰撞历程仿真,达到在产品设计前期即可得到样车道路实验结果的“整车性能预测”效果的计算机仿真技术。
九、焊装模拟分析
机器人在车身焊装工位上的大量应用提高了车身的焊接质量,缩短了生产加工时间。
但如何能够快速而准确地完成全部焊点的加工,即如何规划机器人焊接路径问题,是目前汽车制造
企业迫切需要解决的问题。
传统的机器人焊接路径规划方法是根据设计人员提供的工位上的焊点数量和焊接顺序,由工艺人员根据经验或类似工艺离线编制机器人加工程序,设计加工工艺。
所编写的程序输入到相应设备中,在实验室里预操作,记录下每次偏差位置,重新编程、设计直至满足生产要求。
这不仅耗时、费力,同时对于多机器人加工的碰撞问题无法解决。
壹旦涉及多机器人协同加工,则往往在实验室中采用步进式逼近方法配合专家经验加以解决,以免发生碰撞,损坏设备。
为此,现代车身焊装模拟分析结合虚拟制造技术,在仿真环境下,运用相应的优化算法对车身焊装工位的机器人加工路径进行离线规划,且通过仿真加工进行验证,从而达到指导实际生产的目的。
虚拟制造的基础是采用计算机支持的技术,应用数字建模和仿真技术、虚拟现实技术等来模拟生产、加工和装配等过程,在计算机上将产品“制造”出来,实现将工艺过程转为数字化操作,再由数字化操作指导实际生产。
通过建立生产加工的仿真模型研究制造活动,使用户在设计阶段能够了解产品未来制造过程,实现对生产系统性能有效的预测和评价。
在仿真环境下的试运行,有利于进行多工艺方案比较,更有利于多机器人焊接轨迹的选取和优化。
汽车底盘设计流程及相关设计软件
1.二维图纸绘制软件
1.1AUTOCAD及其相关汉化软件
1.2CAXA电子图板
2.三维结构设计及模具设计软件
2.1UGNX
2.2PRO/E
2.3CATIA
2.4SolidWorks3.有限元分析软件
3.1ANSYS
3.2MSC.NASTRAN
3.3ABAQUS
3.4ALGOR
3.5ADINA
3.6COSMOS
4.整车性能分析软件
4.1ADAMS
4.2CARSIM/TRUCKSIM
4.3AMESIM
4.4MATLAB
5.虚拟试验软件
5.1NILABVIEW
5.2LABWINDOW/CVI
6.流场分析软件
6.1FLUENT
6.2STAR-CD
7.造型软件7.1Alias7.2Photoshop7.3Coreldraw8.产品数据管理软件8.1UGSIman8.2SmartTeam8.3Metaphase8.4Optegra9.加工类软件
9.1POWERMILL
9.2MASTERCAM
9.3I-DEASCAMAND
10.NVH分析软件
10.1SYSNOISE
10.2SoundPLAN10.3ViNAS
10.4AUTOSEA
11.疲劳分析软件
11.1MSC.FATIGUE
11.2LMS.FALANCS
11.3nSoft12.其它相关设计分析软件
12.1Romax齿轮分析软件
12.2BETAsoft电路板级、器件级热分析软件12.3RelexStudio可靠性设计分析和工程管理软件12.4PAM-CRASH冲击碰撞分析软件
12.5RADIOSS结构冲击碰撞、流体CFD、噪音等大型分析软件
12.6CFdesign流体流动、传热和电子冷却模拟软件
12.7iSight最优化分析软件
12.8VisualDOC最优化分析软件
12.9MOLDFLOW注塑成型仿真软件
12.10ProCast铸造仿真软件