组合铣床的总体设计和主轴箱设计文档格式.docx
《组合铣床的总体设计和主轴箱设计文档格式.docx》由会员分享,可在线阅读,更多相关《组合铣床的总体设计和主轴箱设计文档格式.docx(21页珍藏版)》请在冰点文库上搜索。
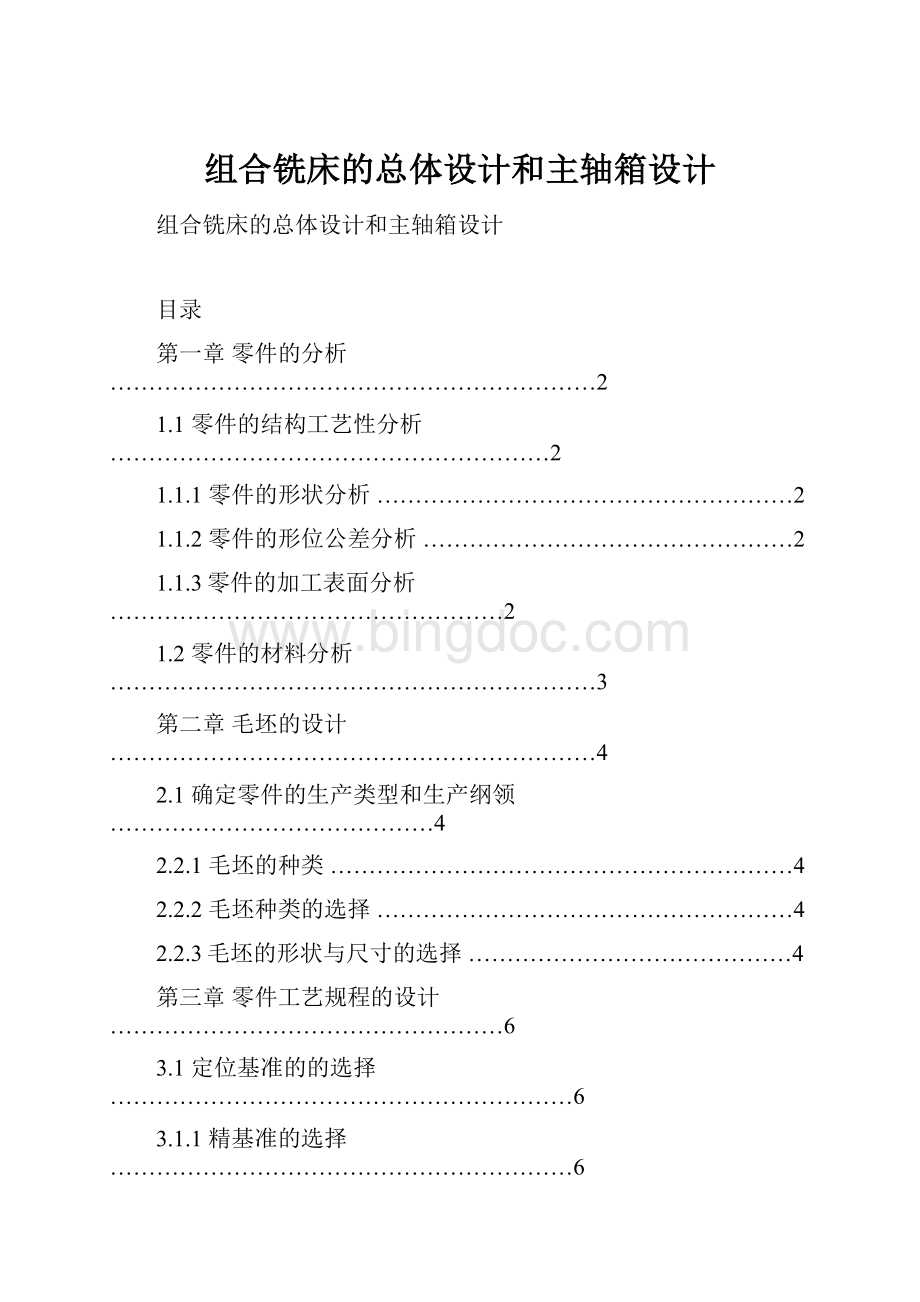
4.4机械手回转轴4上的齿轮齿条设计………………………………………23
4.5自动换刀装置的相关技术要求……………………………………………24
4.5.1主轴准停装置…………………………………………………………24
4.5.2换刀机械手的安装与调试……………………………………………24
4.6自动换刀程序的编制………………………………………………………26
第5章自动换刀装置的控制原理…………………………………………………26
5.1自动换刀装置的液压系统原理图…………………………………………26
5.2自动换刀装置换刀动作的顺序控制过程…………………………………26
致谢词………………………………………………………………………………27
参考文献……………………………………………………………………………28
前言
毕业设计是培养我们实际工作能力的最后一个重要实践性学习环节,它不但是对我们三年来的学习与实践是一个很好的总结和考验,也是为以后从事专业技术工作做个强而有力的铺垫。
本次我的设计题目是组合件,在设计之前对此类零件没有太多了解,经过多次调查研究和指导老师的细心指导下,使我能够很好的完成这次设计。
此次设计不但培养了我们综合运用所学知识分析和解决本专业一般技术问题的能力,而且也进一步巩固扩大和深化了我们所学的基本理论、基本知识和基本操作技能,同时也培养了我们树立正确的设计思想和生产观念、经济观念、全局观念,养成了理论联系实际和严谨的工作作风,培养我们掌握机械加工的一般工艺规程和方法,独立正确的使用技术文献资料和正确的表达自己设计思想的能力。
首先,我积极地查阅相关资料,对零件图进行了仔细的研究,了解了现场工作情况,然后,向老师认真的请教了加工工艺过程及方法等技术性问题,为自己进行毕业设计做好准备。
通过以上学习,使我了解了本组零件的结构,生产纲领和生产条件,并确定其重要加工表面。
老师的辅导与分析,让我能综合运用所学过的理论知识和方法,正确地制定一个零件的机械加工工艺规程,从而保证零件的加工质量、生产率和经济性;
能较熟练地使用有关的手册,图表资料及技术参考书,也能够较熟练应用工艺计算的方法,正确地进行工艺计算,熟练掌握一般零件的数控编程方法,机床的操作以及零件的数控加工。
最后说明书来阐述了关于零件的有关内容及加工工艺过程等几个重要方面,认真地完成了整个设计的过程。
在此,对给予我大力支持和热情帮助的老师们表示忠心的感谢。
由于个人能力有限,经验欠缺,因此,文中错误,不妥之处在所难免,恳请各位领导及老师批评指正。
第一章:
零件的分析
1.1零件的结构工艺性分析
件1件2
零件的结构工艺性是指所设计的零件在能满足使用要求的前提下制造的可行性和经济性,即所设计的零件结构应便于成形,并且成本低,效率高。
它的涉及面广,因此有必要对零件进行结构工艺性分析,找出技术关键,以便在拟定工艺规程时采用适当的工作措施加以保证。
1.1.1零件的形状分析
轴系组合件较为复杂,从外形上看件一左端是不完整的球端面.球端的边面质量Ra1.6.外阶梯形圆柱表面质量Ra1.6,车40度的槽及椭圆左端的槽,内孔螺纹等的加工难度较大内边面质量Ra1.6,右端外部椭圆留双边1mm。
件二是椭圆,阶梯形圆柱质量Ra1.6,外螺纹加工精度都很高。
大体加工过程:
加工件加工件二:
首先在车床上用外圆车刀粗加工,倒角,车外螺纹,用外圆车刀车椭圆,然后用手工切断.加工加工件一:
先在车床用外圆粗车加工球面,车40度槽,倒角,内孔镗刀加工内孔,切内孔φ31的槽,然后车M30X1.5的内螺纹,最后外圆车刀加工椭圆.
1.1.2零件的技术要求分析
零件图纸上标注的技术要求:
1.锐边倒角C0.3
2.未注倒角C1.
3.圆弧过渡光滑
4.未注尺寸公差按GB/T1804-m加工和效验
5.调质硬度HRC30-35
1.1.3零件的加工表面的分析
从零件图可以看出轴系零件的主要加工表面是:
1.φ31的槽:
它的表面粗糙度是Ra1.6,而且其轴心线是设计基准。
2.M30×
1.5-6H的螺纹:
此螺纹是一个标准螺纹,虽然没有特殊要求,但它在配合时起传递扭矩的作用,故其配合精度要求高。
3.椭圆:
表面粗糙度Ra3.2,轴心线是设计基准。
4.球面:
尺寸以确定,表面粗糙度Ra1.6,圆心是设计基准.
通过以上的分析可知,零件的结构较为简单,易于加工,具有一定的可行性。
1.2零件的材料分析
零件材料的选用是非常重要的,选材不当制成的零件不能满足使用要求,过早损伤和破坏产生不良影响或经济效益差等。
机械零件选材的一般原则是:
首先满足使用性能的要求,同时兼顾工艺性、经济性和环保性。
对于轴类零件的选材应具有以下几点要求:
1.优良的综合力学性能,即要求有高的强度和韧性,以防止由于过载和冲击而引起的变形和断裂。
2.高的疲劳极限,防止疲劳断裂。
3.良好的耐磨性。
4.在特殊条件工作时,还应有特殊要求。
本零件的材料是45号钢,它属于低淬透性合金调质钢,其力学性能是:
MPa,
MPa,
J。
其化学成分是:
碳含量0.37%~0.45%,铬含量0.8%~1.1%,锰含量0.17%~0.37%,硫含量0.5%~0.8%,其中碳含量过高、过低均不能满足经调质后获得良好综合力学性能的要求,主加元素为铬,在配以硫、锰等合金元素,其作用是提高淬透性,强化铁素体和细化晶粒,因此,此钢的热处理变形小,废品率低,因而降低了工艺成本。
其热处理特点是:
当原始组织为珠光体时,预先热处理可采用正火或退火处理;
该类钢最终热处理均采用淬火后在500-650℃的高温回火工艺,即调质处理工艺,调质处理可使材料具有良好的综合力学性能。
材料长度的选择:
件一取φ50*100,件二取φ50*80的棒料
第二章:
毛坯的设计
2.1确定零件的生产类型和生产纲领
生产类型是指企业(或车间,工段,班组,工作地)生产专业化程度的分类,一般分为大量生产,成批生产和单件生产三种类型。
它可根据生产纲领和产品及零件的特征或工作地每月担负的工序数来具体划分。
生产纲领是指在计划期内应当生产的产品产量和进度计划。
计划期常定为一年,所以生产纲领也称年产量。
零件的生产纲领要计入备品和废品的数量,其计算式为:
N=Qn(1+α)(1+β)
N—零件的年产量(件/年)
Q—产品的年产量(台/年)
n—每台产品中,该零件的数量(件/台)
α—备品的百分率
β—废品的百分率
其中Q=500n=1α=5%β=2%所以N=500
(1+5%)(1+2%)=535.5即536(件/年)
由上所述,查《机械制造工艺学》中表1-3知该零件为中批生产。
2.2确定零件毛坯的制造形式
毛坯是根据零件所要求的形状,工艺尺寸等方面而制成的供进一步加工使用的生产对象。
毛坯种类的选择不仅影响着毛坯制造的工艺装备及制造费用,对零件的机械加工工艺装备及工具的消耗,工时定额计算有很大影响。
2.2.1毛坯的种类
常用的毛坯种类有:
铸件、锻件、型材、焊接件、冷压件等。
1.铸件:
适用于形状复杂的毛坯。
2.锻件:
适用与零件强度较高,形状较简单的零件。
尺寸大的零件因受设备限制,故一般用自由锻;
中、小型零件可选模锻;
形状复杂的刚质零件不宜用自由锻。
3.型材:
热轧型材的尺寸较大、精度低,多用作一般零件的毛坯;
冷轧型材尺寸较小、精度较高,多用于毛坯精度要求较高的中小零件,适用于自动机床加工。
4.焊接件:
对于大件来说,焊接件简单方便,特别是单件小批生产可大大缩短生产周期,但焊接后变形大,需经时效处理。
5.冷压件:
适用于形状复杂的板料零件,大多用于中小零件的大批量生产。
2.2.2毛坯种类的选择
选择毛坯种类需考虑的因素有以下几点:
1.根据图纸规定的材料及机械性能选择毛坯。
2.根据零件的功能选择毛坯。
3.根据生产类型选择毛坯。
4.根据具体生产条件选择毛坯。
2.2.3毛坯的形状和尺寸的选择
确定毛坯的形状与尺寸的步骤是:
首先选取毛坯加工余量和毛坯公差,其次将毛坯加工余量叠加在零件的相应加工表面上,从而计算出毛坯尺寸,最后标注毛坯尺寸与公差。
其总的要求是:
减少“肥头大耳”,实现少屑或无屑加工。
因此,毛坯形状要力求接近成品形状,以减少机械加工的劳动量。
本零件的大部分加工表面是回转体表面,根据本零件的生产纲领,年生产数量,经济价值及复杂程度,另外本零件为轴类零件,考虑其复杂程度,所以本零件毛坯为棒料。
因为棒料的经济性好,加工余量小,而且成本较低。
根据本零件的结构特征和尺寸要求及考虑到经济性,所以毛坯一件圆棒料的尺寸为φ50mm×
100mm,二件圆棒料的尺寸为φ50mm×
80mm.
第三章:
零件工艺规程的设计
机械加工工艺规程是规定产品或零部件工艺过程和操作方法等的工艺文件,它是指导生产的主要技术文献,是组织和管理生产的基本依据,是新建和扩建工厂或车间的基本资料,是进行技术交流的重要手段。
3.1定位基准的选择
在制订零件的加工工艺规程时,正确地选择工件的基准有着很重要的意义。
基准选择的好坏不仅影响零件的加工位置精度,而且对零件各表面的加工顺序也有很大的影响。
基准有粗基准与精基准之分。
选择定位基准时是从保证工件精度要求出发的,因而分析定位基准选择的顺序就应从精基准到粗基准。
3.1.1精基准的选择
1.基准重合原则:
就是尽可能选用设计基准作为定位基准,这样可以避免定位基准与设计基准不重合而引起定位误差。
2.基准统一原则:
位置精度要求较高的某些表面加工时尽可能选用同一定位基准,这样有利于保证各加工表面的位置精度。
3自为基准原则:
当某些表面精加工要求加工余量小而均匀时,选择加工表面本身作为定位基准,用于提高加工面本身的精度。
4互为基准原则:
为了使加工面间有较高的位置精度,又为了使其加工余量小而均匀采取此原则。
5.保证工件定位准确、夹紧可靠、操作方便的原则。
3.1.2粗基准的选择
粗基准选择的要求应能保证加工面与非加工面之间的位置要求及合理分配加工表面的余量,同时,要为后续工序提供精基准。
1.为了保证加工面与非加工面之间的位置要求,应选非加工面作为粗基准。
2.合理分配各加工面的加工余量。
3.粗基准应避免重复使用,在同一尺寸方向上,通常只允许使用一次。
4.选作粗基准的表面应平整光洁,要避开锻造飞边和铸造浇冒口,分型面,毛刺等缺陷,以保证定位准确、夹紧可靠。
由于本工件毛坯为棒料,所以采用φ50棒料的外圆柱面为粗基准,车削零件一的左端,再以粗车后的圆柱面为粗基准,车削零件的右端,然后再以粗车后零件的回转轴心分别对零件的沟槽、椭圆的左端槽及内孔,内孔槽,螺纹右端外部椭圆进行加工,保证各个部位的尺寸精度及位置精度,然后以φ48的右椭圆的端面为基准,加工零件的螺纹,阶梯圆柱,内孔槽,最后以件一为基准,精加工件一的左端球面,阶梯圆柱,车槽,倒角及右端内孔,车槽.
由以上分析可知本零件采用两种基准原则,一是基准重合原则,它是以零件的轴心线为定位基准也是设计基准,对零件的外圆、内孔、槽以及螺纹等表面进行切削加工;
另一种是基准统一原则,它是多个加工表面都以一个基准作基准面加工定位的。
3.2零件表面加工方法的选择
零件表面的加工应根据这些表面的加工要求和零件的结构特点及材料性质等因素,而选用相应的加工方法。
在选择某一表面的加工方法时,一般总是首先选定它的最终加工方法,然后再逐一选定各有关前道工序的加工方法。
加工方法选择的原则如下:
1.所选加工方法应考虑每种加工方法的经济加工精度范围要与加工表面的精度要求和表面粗糙度要求相适应。
2.所选加工方法能够确保加工面的几何形状精度,表面相互位置精度的要求。
3.所选加工方法要与零件材料的可加工性相适应。
4.加工方法要与生产类型相适应。
5.所选加工方法要与企业现有设备和工人技术水平相适应。
通过以上原则,本零件各主要表面加工方法为:
1.各回转表面,球面,椭圆及槽,倒角:
车削加工
2.M30X1.5-6H的螺纹:
3.3加工顺序的安排
3.3.1加工阶段的划分
工件的加工质量要求较高时,应划分阶段。
一般分为粗加工、半精加工和精加工三个阶段。
粗加工阶段是从坯料上切除较多余量,所能达到的精度和表面质量都比较低的加工过程。
半精加工阶段是在粗加工和精加工之间进行的切削加工过程。
精加工是从工件上切除较少余量,所能达到的精度和表面质量都比较高的加工过程。
划分加工阶段的作用是:
1.避免毛坯内应力重新分布而影响获得的加工精度。
2.避免粗加工时较大的夹紧力和切削力所引起的弹性变形和热变形对精加工的影响。
3.粗精加工阶段分开,可较及时地发现毛坯的缺陷,避免不必要的损失。
4.可以合理使用机床,使精密机床能较长期地保持其精度。
5.适应加工过程中安排热处理的需要。
3.3.2工序的合理组合
确定加工方法后,就要按生产类型、零件的结构特点、技术要求和机床设备等具体生产条件,确定工艺过程的工序数目。
确定工序数目有两种基本原则可供选择:
1.工序集中
所谓工序集中,就是零件的加工集中在少数工序内完成,而每一工序的加工内容却较多。
其特点:
1).采用高效专用设备及工艺装备,生产率高。
2).工件装夹次数减少,易于保证表面间位置精度,还能减少工序间运输量,缩短生产周期。
3).工序数目少,可减少机床数量,操作工人数和生产面积,还可简化生产计划和生产组织工作。
4).因采用。
结构复杂的专用设备及工艺装备,便投资大,调数和维修复杂,生产准备工作量大,转换新产品比较费时。
2.工序分散
所谓工序分散就是将工件的加工分散在较多的工序内进行,每道工序的加工内容很少,最少时即每道工序仅一个简单工步。
1).设备及工艺装备比较简单,调整和维修方便,工人容易掌握,生产准备工作量少,又易于平衡工序时间,易适应产品更换。
2).可采用最合理的切削用量,减少基本时间。
3).设备数量多,操作工人多,占用生产面积大。
从生产批量或设备等方面考虑,本零件属于中批生产,虽然工序越集中,加工周期越短,加工的精度也高,但是,本零件部分加工在普通机床上无法加工,所以粗精加工必须在数控机床上一起完成,这样虽提高了生产率,但同时也提高了成本,也没有合理的使用机床,因此,此零件采用工序集中原则。
3.3.3加工顺序的安排
1.机械加工工序的安排原则
1).对于形状复杂、尺寸较大的毛坯或尺寸偏差较大的毛坯,应首先安排划线工序,为精基准加工提供找正基准。
2).按“先基面后其它”的顺序,先加工精基准面。
3).在重要表面加工前,应对精基准进行修正。
4).按“先主后次,先粗后精”的顺序,对精度要求较高的各主要表面进行粗加工、半精加工和精加工。
5).对于与主要表面后位置精度要求的次要表面,应安排在主要表面加工之后加工。
6).对于易出现废品的工序,精加工和光整加工可适当提前,一般情况主要表面的精加工和光整加工应放在最后阶段进行。
2.热处理工序安排的原则
调质的目的是为了提高工件的综合力学性能,减少工件的变形或为以后的表面热处理做好组织准备。
因此,一般安排在粗加工后、精加工前进行,可以保证淬透性差的钢种表面调质层(回火索氏体)的组织不被切削掉。
3.辅助工序安排的原则
1).中间检验一般安排在粗加工全部之后,精加工之前,送往外车间加工的前后,花费工时较多和重要工序的前后。
2).荧光检验、磁力探伤等特种检验,主要用于表面质量的检验,通常安排在精加工阶段。
荧光检验如用于检验毛坯的裂纹,则安排在加工前。
3).电镀、涂层、发蓝、氧化等表面处理工序,一般安排在工艺过程的最后进行。
通过前面对定位基准的选择,零件表面加工方法的选择及加工顺序的安排的分析说明,再结合本零件的结构特点及制定工艺路线的出发点:
保证加工质量、提高生产率、降低成本,从而获得最好的经济性。
所以,此零件制定的工艺路线是:
00.下料
05.加工件2轮廓
10.加工件1左端轮廓
15.加工件1右端轮廓
20.加工件1右端内轮廓
25.打毛刺
30.清洗
35.最终检验
3.4工艺的制定
3.4.1工序基准的选择:
工序基准是在工艺图上以标定被加工表面位置尺寸和位置精度的基准,所标定的位置尺寸和位置精度分别称为工序尺寸和工序技术要求。
工序尺寸和工序技术要求的内容,在加工后应进行测量,测量所用的基准称为测量基准,通常工序基准与测量基准重合。
对于设计基准尚未最后加工完毕的中间工序,应选各工序的定位基准作为工序基准和测量基准。
在各表面的最后精加工时,当定位基准与设计基准重合时,虽然工序基准和测量基准就应选用这个重合的基准;
当所选定位基准未与设计基准重合时,在这两种基准都能作为测量基准的情况下,工序基准的选择应注意以下几点:
1.选设计基准作为工序基准时,对工序尺寸的检验就是对设计尺寸的检验,有利于减少检验工作量。
2.当本工序中位置精度是由夹具保证而不需进行试切调整的情况,应使工序基准与设计基准重合。
3.对一次安装下的加工出来的各个表面,各加工面之间的工序尺寸应选与设计尺寸一致。
本零件在加工时,其轴向尺寸是以零件的两端作为工序基准,径向尺寸是以零件的轴心线作为工序基准。
它的工序基准与设计基准重合,为加工和检测提供了方便。
3.4.2确定工序尺寸的方法:
1.对外圆和内孔简单加工的情况工序尺寸可由后续加工的工序尺寸加上(对被包容面)或减去(对包容面)公称工序余量而求得,工序公差按所加工方法的经济精度选定。
2.当工件上的位置尺寸精度或技术要求在工艺过程中是由两个甚至更多的工序所间接保证时,需通过尺寸链计算,来确定有关工序尺寸,公差及技术要求。
3.对于同一位置尺寸方向有较多尺寸,加工时定位基准又需多次转换加工的工件,由于工序尺寸相互联系的关系较复杂,就需要从整个工艺过程的角度用工艺尺寸链作综合计算,以求出各工序尺寸、公差及技术要求。
根据本零件的加工工艺路线和技术要求,其工序尺寸确定如下:
工序1:
粗车件2轮廓
工步一:
平端面
此端面经过两次车削,粗车和精车。
查表知,其轧制件端面加工余量为1m,粗车余量为0.5mm,车削后达到的表面粗糙度为Ra1.6。
工步二:
粗车左端外轮廓
本工序采用粗车-半精车-精车的加工方式,经查表知,其切削余量为2mm,故该工序车削后基本尺寸应为48+2=50mm,与该尺寸对应的公差值分别是0.33mm,按入体原则标注,工序尺寸为φ
mm,。
工步三:
粗加工右端椭圆
留双边1mm余量
工序2:
加工件1轮廓
此工步同工序10中工步一,但其加工余量是0.5mm。
粗车加工左端轮廓
此工步同工序10中工步二,其基本尺寸是30+2=32mm,与该尺寸对应的公差值是0.33mm,按入体原则标注,工序尺寸为φ
mm。
车外槽
槽宽5,切削余量为0
工步四:
椭圆左端槽
槽宽2,切削余量为0
工步五:
粗加工右端内孔
每次背吃刀量1mm,退刀量0.5mm
工步六:
精加工右端内孔
切削余量为0.1mm
工步七:
车内槽
此槽是作为加工螺纹时的退刀槽,其工序尺寸应为φ31mm。
工步八:
车削内螺纹
查表知,M30×
1.5-6H的螺纹EI=0,中径公差是0.19mm,小径公差是0.3mm。
3.4.3加工余量的确定:
加工余量是指加工过程中所切去的金属层厚度。
其余量的大小对工艺过程有一定影响,余量不足不能保证零件的加工质量,不但增加了机械加工的劳动量,而且增加了刀具,能源及材料的消耗,从而增加了成本,降低了生产率,所以必需合理的安排加工余量。
确定加工余量的方法有查表法、经验仿计法和分析计算法。
本零件采用查表法,参照《数控加工技术》第二篇第四章加工余量表对本零件的加工余量所查结果如下:
表3.1
加工表面
加工方案
余量(mm)
φ25外圆
粗车
2.0
精车
0.1
切槽
车
外螺纹
椭圆
1.0
SR球端面
钻
3.4.4机床的选择:
零件的加工精度很大程度上取决于所用机床,因此必须合理的选择机床,对于单件小批量生产一般选择通用机床;
对于中批量则广泛采用专用机床、数控机床和组合机床。
在选择机床时应注意以下几点:
1.机床的加工尺寸范围与零件外形尺寸相适应。
2.机床精度与工件精度相适应。
3.与现有加工条件相适应。
4.机床的生产率应与工件的生产类型相适应。
本零件尺寸小、重量轻、属中批生产,其毛坯是棒料,加工余量较大,为了合理的利用机床,故此零件在粗加工时选用普通机床,另外工件的某些部分在普通机床上很难加工出来,又因此次设计着重练习的是对数控机床的熟练程度,故精加工时选择数控机床,根据现有的生产条件,选择的机床型号是:
CA6140普通车床
CJK6032A教学型数控车