现代工业工程(IE)技术PPT.ppt
《现代工业工程(IE)技术PPT.ppt》由会员分享,可在线阅读,更多相关《现代工业工程(IE)技术PPT.ppt(73页珍藏版)》请在冰点文库上搜索。
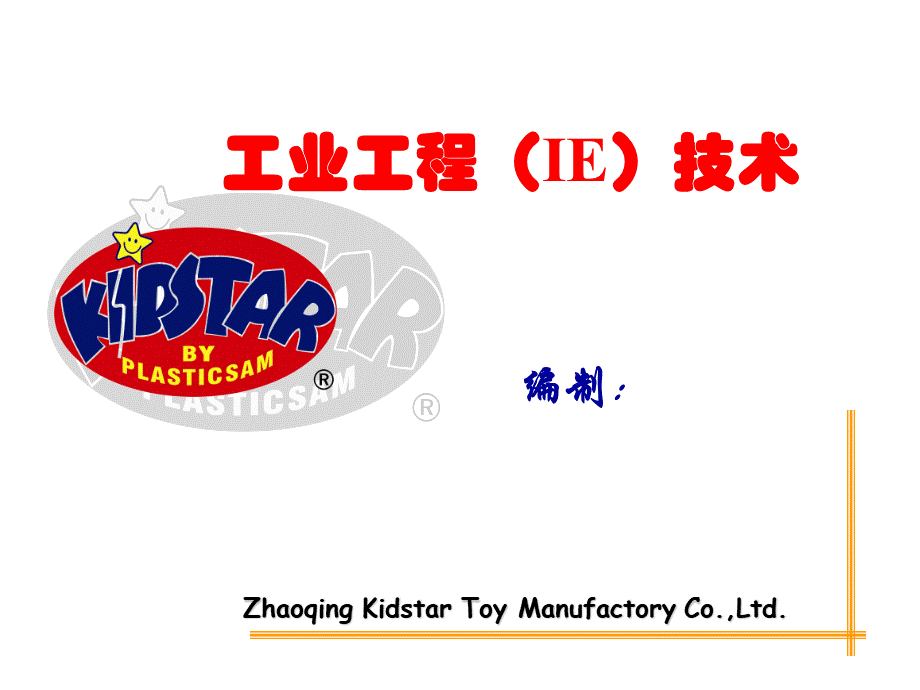
工业工程(IE)技术编制:
概论,随着生产技术与控制方法的不断进步,由品质占主导的市场竞争模式,逐渐被品质与成本并重的市场策略所取代;经验的持续积累,加上不断的改善及创新,无疑会增强公司的实力与信心,人做为生产力变革的主体,其价值观念,逻辑的思考能力,科学的工作方法,势必对改善的效果与投入的成本带来重要的影响,为此,请你秉承积极,认真的心态理解下面的內容,并思考行动的步骤!
课程大纲,工业工程概论,工作研究之方法研究,工作研究之工作测量,生产率改善与生产线平衡,工业工程与精益生产的关系,第一讲:
工业工程(IE)概论工业工程和定义工业工程的发展工业工程的作用工业工程的研究内容,工业工程师的素养,什么是工业工程?
IndustrialEngineeringIE,工业工程是对人员、物料、设备、能源和信息所组成的集成系统,进行设计、改善和设置的一门学科。
综合运用数学、物理学、社会科学的专门知识、技术以及工程分析与设计的原理、方法,对由人、物料、设备、能源、信息组成的集成系统,进行规划、设计、评价、改进(创新)的一门学科。
ImproveEfficiency改善效率。
IE的目标:
使生产系统投入的要素得到有效的利用,降低成本,保证质量和安全,提高生产效率,获得最佳效益。
成本和效率意识问题和改革意识工作简化和标准化意识全局和整体化意识以人为中心的意识。
IE的意识:
工业工程的发展,18561915科学管理之父-泰勒强调科学管理,从而提高生产率;创立了“方法研究、时间研究”;分析工作内容改进方法设计工作方法最大效益;提出了一系列科学管理原理与方法。
旧方法新方法作业员配置400600人140人每人每日平均工作吨数12.5吨48吨每人每日平均工资115188每吨人工成本00720033,泰勒铁锹铲煤实验(1898),泰勒,工作测量方法之父,创立了“动作研究”。
Lillian(1878-1972):
人因工程学的奠基人。
分解动作确定基本动作要素,经科学分析建立省时高效和最满意的操作顺序,吉尔布雷斯砌砖研究,旧方法新方法动作18412每时砌砖数120块350块效率100300,工业工程的作用,综合体系,利用,设计Design,改善Improve,实施Installation,专门的,数学物理学社会科学,知识技术,规划设计评价改进创新,工学的,分析设计,原理方法,通过,人员机器物料能源信息,IE是系统优化技术,期待的成果,PQCDSF,PQCDSF,工作研究(WorkStudy),方法研究(MethodStudy),工作衡量(WorkMeasurement),程序分析(ProcessAnalysis),工艺程序分析(流程型/总装型)流程程序分析(人型/物型)布局与路径程序分析,操作分析(OperationAnalysis),人机配合分析联合操作分析双手作业分析,动作分析(MotionAnalysis),细微动作分析动作经济原则,时间研究(TimeStudy),马表测时法摄像法速度评比宽放时间(Allowances),工作抽样(WorkSampling),预定动作时间标准(PTS),模特排时法(MOD)方法时间衡量(MTM)工作因素(WF),工业工程的研究内容,第二讲:
IE方法研究之程序研究,工作研究的内容和步骤程序分析的定义程序分析的方法1)工艺程序分析(流程)2)流程程序分析(工序)3)布置与路径程序分析程序分析改善方法,工作研究的内容,作业测量:
是分析效率的技术。
包括制定标准时间及改善目标时间,测定作业效率等。
方法研究:
通过程序分析、操作分析、动作分析等研究,进行作业系统的设计、改善及实施。
IE的全过程:
利用程序分析、操作分析、动作分析获得-标准化作业利用作业测定-制定标准工时,工作研究的步骤,程序分析:
以整个生产过程为研究对象,研究分析一个完整的工艺过程(注塑、装配、糖果、包装、存储等),消除其中包含的多余作业、搬运、等待、不合理的程序等,从而提高工作效率(D029垃圾桶)。
程序分析的特点:
生产过程的宏观分析。
程序分析包含:
工艺程序分析、流程程序分析、布置和路径程序分析。
程序分析,程序分析符号,工艺程序分析,工艺程序图:
表明生产过程中所有的操作、检验和物料加工的先后顺序,使整个制造过程一目了然。
用于分析操作之间的关系,生产过程中的操作、检查、布局设计。
流程程序分析,流程程序图:
进一步对整个制造过程作详细记录:
由操作、检验、搬运、等待、贮存五种符号构成,根据研究对象的不同可分为:
物型:
记录生产过程中材料、零部件被加工处理的过程。
人型:
记录操作人员在生产过程中的各种活动。
用于分析间接或隐藏的成本,如等待、存储、搬运等。
人型程序分析表,程序改善方法-ECRS,消除不必要的流程、工序、作业、动作等(E)尽可能结合项目明细(C)将项目明细以好的顺序重编排组合(R)将重编排组合明细简单化(S),布置与路径程序分析,路径分析:
对现场布局、物料(零件、产品)、设备、作业者的实际流通线路进行分析,改进现场布置、缩短移动路径。
布置与路径分析图由操作、检验、搬运、暂存、贮存五种符号和布置示意图构成。
重点是“搬运”和“移动”的线路。
作用:
流程程序图的补充,指明移动距离及时间和交通的拥挤,是改进现场布局与路径的工具。
程序分析技巧-5W2H,做什么?
(what)何处做?
(where)何时做?
(when)由谁做?
(who)如何做?
(how),为什么Why?
做什么?
要在此处做?
有无其他更合适之处?
要此时做?
有无更合适的时间?
由他做?
有无更合适的人去做?
要这样做?
有无更好的方法去做?
有没有成本更低的方法?
成本如何?
(howmuch),要做这,是否必要?
程序分析五方面,程序的改善五大步骤,选择-所需的研究工作,记录-研究图表及关键数据,分析-5W2H、五个分析方面,改善-科学合理的新方法(如:
ECRS),维持-经常进行检查/改善,人机操作分析联合操作分析双手操作分析,第三讲:
IE方法研究之操作研究,人机操作分析,人机操作分析:
分析操作周期内,人与机器的作业内容及关系,以协同机器与人的操作,充分利用人、机的闲余能量,提高人机协作效率。
人机操作图,清晰展现了生产过程中人与机器的交互过程及操作的时间。
单独工作,空闲,共同工作,人机协作图标,线段的长度代表时间比例。
如1cm代表10min等。
当人或机器操作时用表示,人或机器空闲用表示。
人机共同工作时用表示。
0.2,0.4,0.6,0.8,1.0,1.2,1.4,1.6,1.8,2.0,(取)放装好的吸盆,放卡纸,转动转盘,空闲,机器工作,空闲,人,时间(min),人机操作分析图的构成,吸塑热压机,联合操作分析,多人同时对一台机器(一项工作)进行操作,称为联合操作。
对该作业过程中各个对象的不同操作间的相互关系所进行的分析,称为联合操作分析。
基于人机协作的基础上更复杂的人机协作分析。
联合作业分析研究目的:
发掘空闲与等待时间,提高机器利用率。
平衡各操作者的工作,减少周期时间。
压定糖棒视频,插定糖棒视频,双手操作分析:
双手操作分析:
对生产现场作业者双手的操作进行分析研究,以平衡双手作业动作及负荷,减少动作数量。
双手操作分析的符号,入产品视频,入糖视频,包糖视频,第四讲:
IE方法研究之动作研究,动作分析的含义和目的动作经济性十大原则,动作分析:
以动作为对象进行的分析,去掉多余动作,降低动作等级,把必要的动作组合成标准动作系列,以开发合理、高效的工作方法。
动作分析的工具沙布利克分析(Therblig),世界上最大的浪费,莫过于动作的浪费.-吉尔布雷斯(Gilbreth),动作分析,沙布利克分析符号,伸手(TE)()握取(G)移物(TL)()装配(A)()使用(U)(U)拆卸(DA)()放手(RL)()检查(I)()寻找(SH)(),(U),选择(ST)()计划(PN)()定位(P)()预定位(PP)()持住(H)()休息(R)()迟延(UD)()故延(AD)()发现(F)(),U,沙布利克分析,核心动素常用动素改善的对象辅助性动素减少的对象消耗性动素取消的对象,U,U,U,动作经济原则,动作经济原则:
使作业(动作的组成)能以最少的“工”的投入,产生最有效的成果。
动作经济性的基本准则减少动作数量追求动作平衡缩短动作移动距离使动作保持轻松自然的节奏,质优工简,折盒子视频,打吊咭视频,打吊咭改善后视频,动作经济性十条原则,与人体动作有关的原则:
原则一:
双手并用、对称原则。
原则二:
降低等级原则手指手腕肘部肩部腰部走动原则三:
尽可能利用物体的动能采用流畅和连续的动作。
曲线运动优于方向突变的直线运动弹道式运动优于受控制的运动(高尔夫)动作尽可能有轻松的节奏与工作地布置有关的原则:
原则四:
工具、物料置于工作者前面,依工作顺序排列。
原则五:
零件、物料利用重量堕送至工作者前面“下坠式”传送。
原则六:
照明设备,工作台及坐椅符合人因工学。
与工具设备有关的原则:
原则七:
以夹具或足踏工具代替手的工作。
(脚踏拖把)原则八:
将两种或以上工具合并为一;原则九:
各指负荷应按其本能给予分配原则十:
工具及物料尽可能预放在工作位置。
符合中国人身体的人因工程学,物料(或工具)放置点、产品组装点、操作者手的位置形成的三角形的边长越小越好。
模特排时法(MOD)方法时间衡量(MTM)工作因素(WF),第五讲:
IE工作测量之时间研究,工作研究(WorkStudy),方法研究(MethodStudy),工作衡量(WorkMeasurement),程序分析(ProcessAnalysis),工艺程序分析(流程型/总装型)流程程序分析(人型/物型)布局与路径程序分析,操作分析(OperationAnalysis),人机配合分析联合操作分析双手作业分析,动作分析(MotionAnalysis),细微动作分析动作经济原则,时间研究(TimeStudy),马表测时法摄像法速度评比宽放时间(Allowances),工作抽样(WorkSampling),预定动作时间标准(PTS),作业测量:
运用各种技术测量合格工人按规定的作业标准在常的工作条件和环境下,以正常的速度下完成某项工作所需的时间-必要时间+宽放-标准工时。
目的:
制定标准作业方法制定标准工时制定最佳作业系统常用方法:
秒表时间研究/视频分析研究工作抽样预定时间标准法,标准时间(StandardTime=ST),1、方法;按照明确的作业方法与使用固定设备2、条件:
在明确作业条件(例如环境)3、熟练度:
进行操作的人具备中等偏上的熟练度与必要的技能4、劳动强度与速度:
没有在肉体上、精神上不利的影响5、品质要求:
达到规定的品质要求在上述条件下完成单位作业量所需要的时间。
在正常的操作条件下,用规定的作业方法和设备,普通熟练作业者以标准的作业方法及合理的劳动强度和速度下完成符合质量要求的工作所需的时间,称标准时间。
标准时间5个必要条件:
标准时间,正常时间,宽放时间,主体作业时间,副作业时间,私事宽放时间,疲劳宽放时间,作业宽放时间,集体宽放时间,标准工时的构成,1.秒表测时法:
用秒表直接进行作业时间测定的方法。
明确时间分析调查的目的,并向车间人员说明。
选择观测对象,观测时间选择。
(什么时间测量合适?
)用具准备。
分解作业要素,确定观测次数。
观测及记录,统计整理观测结果(测量多次)。
讨论观测结果,制定改善方案。
预定时间标准,2.工作抽样法:
在一段较长时间内,以随机方式对调查对象进行工作与否的间断观测,得出结果。
工作改善:
调查人机的工作与空闲比率,对空闲部分进行研究、分析、改善。
制定标准工时:
高阶次工作的标准时间。
(作业/工序)标准工时=+宽放,预定时间标准法(PTS):
对分析对象的作业进行细分,分别决定时间标准,求出作业所需的总和。
PTS标准法的代表:
工作因素法-WF/方法时间测量法-MTM/模特排时法-MODAPTS,模特法分析代码对应示意图,MOD法的时间值:
1MOD=0.1=0.1秒(熟练者动作)=0.129秒(正常速度)=0.143秒(含恢复疲劳的10.74%),移动动作,反射性动作,放的动作,移动动作,终结动作,胳膊的基本动作,腿的动作,结合动作,现场的动作,边看边抓的动作,模特法基本体系和记号,M1手指M2手M3下臂M4上臂M5肩膀(M1/2,M1,M2,M3)G0接触后抓G1抓在手里G3难抓的动作P0容易放的动作P2边看放1次P5边看放2次F3踩PedalW5步行L1重量要素E2眼R2改抓D3判断A4压力(按)C4回转B17弯曲起来S30坐起来,模特法分析代码,模特法分析代码,第六讲:
生产率改善与产线平衡,生产率的改善方法生产率的改善步骤生产线平衡的方法生产线平衡的步骤生产线平衡实例,5W2H,ECRS,改善的方法,未达到预计的结果,计划Plan,试行o,实施Action,达到预期结果,找到浪费收集数据确定预计结果找到方案,实施方案,评估结果,标准化防止再发生,核查heck,IE工作研究改善的步骤,工作研究,方法研究,作业测定,选择研究对象,记录现行工作方法,程序分析,进行方法改进,拟定新的工作方法,培训操作者,实施新的工作方法和标准时间,提高工作效率,操作分析,动作分析,选择研究对象,确定时间研究方法,直接时间研究,预定动作时间标准法,标准资料法,确定宽放时间,制定标准时间,持续改进,生产线平衡,生产线平衡:
对生产各工序进行作业内容均衡化,使各工序的作业时间基本相近。
其核心是消除工序不平衡从而消除工时浪费,最终实现“单件流”。
流水生产线是在“分工”和“作业标准化”的基础上发展起来的。
分析作业内容及时间分解工序,将作业内容初步分配到各工序对各工序进行作业内容调整及改善,使各工序时间基本相等按加工顺序布置工位。
研究生产现平衡时几个重要概念,TAKT(节拍时间):
客户需求节拍,目标:
按需生产(按月变化)。
CT(周期时间):
生产制程时间,制造一件产品所需时间(基本恒定)。
瓶颈时间(Bottleneck):
整个流程中最长的工序时间,通过,前端到达所需时间,生产线平衡步骤,确定流水线作业内容及作业标准计算节拍时间(TAKTTIME)画优先图-AOV确定理论工位数生产线平衡排程(将作业要素按一定准则分配到各工位)计算流水线负荷(效率),如何有效的设拉,D,F,J,C,1.绘制生产线优先图(又称网络活动图)(PrecedenceDiagram),A,B,G,H,E,K,I,玩具小车生产线平衡案例,任务,时间(S),作业描述,紧前任务,A,45,安装后轴支局,拧4个螺母,无,B,11,插入后轴,A,C,9,拧紧后轴支架螺栓,B,D,50,安装前轴,用手拧紧4个螺母,E,15,拧紧前轴螺栓,D,F,12,安装1#后车轮,拧紧轮轴盖,C,G,12,C,H,12,E,I,J,K,12,8,9,无,E,F,G,H,I,安装2#后车轮,拧紧轮轴盖,安装1#前车轮,拧紧轮轴盖,安装2#前车轮,拧紧轮轴盖,安装前轴上的车把手,拧紧螺栓螺钉,拧紧全部螺栓螺钉,2.计算节拍:
玩具小车的生产在一个传送带上进行组装,客户每天的需求是500辆,每天的生产时间为420Min.,3.计算工作站最小数量(理论上):
Smin,W/TT,195/50.4,3.87,4,W:
流水线中所有工作站工作内容的时间总和,4.选择作业分配规则:
规则一:
按后续作业数量最多规则优先安排作业。
规则二:
按作业时间最长规则优先安排作业。
规则三:
按该项作业元素时间与后续作业元素时间的总和最大规则优先安排作业。
5.平衡装配生产线,将作业分配到各工作站:
平衡方案A,选用规则一,当规则一遇到问题时,采用规则二,直至所有作业均安排完毕.,流水线负荷率:
E=W/(S*TT)=195/(5*50.4)=77.38%,平衡方案B,选用规则三:
即该项作业元素时间与后续作业元素时间的总和最大规则优先安排作业(下图为小车作业元素阶位表),按阶位法分配小车作业元素过程,通过上面的阶位式作业元素分配过程得到作业地仍为5个,负荷率仍为77.38%,平衡效果依然不好。
平衡方案C,选用规则二:
即按作业元素时间最长规则安排作业,并用规则一作为辅助规则,以达到生产线平衡的目的。
流水线负荷率:
E=W/(S*TT)=195/(4*50.4)=96.73%(只有6.6S空闲)计算各工序作业负荷:
平衡方案C,各工作站的负荷率均有大幅提升,故选用平衡方案C更好.,精益生产的定义:
“精益”一词取自“精”字中的完美,周密,高品质和“益”字中的利和增加的意思,更有精益求精的意思,精益生产起源于丰田生产模式。
第八讲:
工业工程与精益生产,5S-精益生产的基础识别并消除七种浪费(7Wastes)标准化作业(SOP)准时化生产(JIT)精益布局与物料流动路径(LeanLayout)价值流分析(VSM)-现在一般先用VSM来分析VA/NVA快速换型(SMED)均衡生产(LevelingProduction)设备效率(OEE)全员生产自主维护(TPM),精益生产的主要内容,精益生产,5S-精益生产的基础,整理-区分有用及无用物品,并分开整顿-将有用物品放置于规定位置(定位)清扫-按谁使用谁清洁的原则作好物品的日常清洁清洁-对上述三方面的强化管理素养-形成员工的5S素养,严守标准,团队精神“定品”,“定量”,“定置”化管理的三定原则。
与工业工程中路径与布局的技术及动作经济性原则,这其中含有了工业工程中关于布局(与搬运有关),动作分析的技术(多余动作),程序分析(与等待,检验,存储有关),方法研究中的防错技术(不良缺陷)。
常见的七大浪费,不良、修理的浪费加工的浪费动作的浪费搬运的浪费库存的浪费制造过多/过早的浪费等待的浪费(不平衡)产业废弃物浪费,浪费,是指那些导致成本增加的因素虽然增加价值,但耗用资源过高,A.不良品浪费,人为操作失误设备/工具不稳定不按照标准作业来料不稳定设计没考虑装配需求环境温度/湿度/静电存放周期长,B.过分加工浪费,质量成本概念,C.动作浪費,动作太大单手空闲转身动作过大操作动作不流畅重复/不必要的动作不必要的弯腰动作,超出/低于产品特定需求的精度多余的作业项目,D.搬运浪费,也就是说“每个工位都从手工操作开始”.-找到、拿起、移动,用手放,然后-从手推车移到货板-从货仓到工厂-从工厂到生产线-从生产线到机械化车间-从机械化车间到操作工位,E.库存浪費,存货过多-过多的原材料交货周期过长?
错误的订货量?
-过多的成品是因为生产过剩?
是因为生产排期错误?
F.过量生产浪费,超出下一操作的需求量提前生产下一操作的需求设备速度过快,生产过剩是最大的浪费,G.不平衡浪费,人员工作分配不合理计划对人员需求不均匀设备产能搭配不合理设备故障物料短缺信息流与物流不同步,标准化作业(SOP),以人的动作为中心,用没有MUDA(浪费),效率最高的生产方式。
标准化作业由标准动作,标准作业顺序,标准中间库存(WIP)三部分构成。
SOP与工业工程中程序分析,操作分析,动作分析的技术相关。
准时化生产(JIT),JIT与工业工程中工艺程序,流程程序分析相关。
精益布局与物料流动路径,与工业工程中设施与布局技术相关。
SOP,JIT,价值流分析(VSM),从客户角度出发对产品价值形成的全过程进行分析,去除或减少非价值增值的部分。
价值流图包括物流、信息流、过程流三部分,VSM与工业工程中程序分析技术相关。
快速换型(SMED),为快速响应客户需求,需经常更换产品的生产,如何缩短产品换型时间从而减少生产停顿的浪费称为SMED。
其核心思想是把线内时间转换为线外时间,并尽量减少线内、线外时间。
SMED与工业工程中程序分析,操作分析,动作分析技术相关。
工业工程与精益生产,通过前面的描述,可以看到工业工程与精益生产是紧密关联的,工业工程是工程技术,而精益生产是一门生产管理技术。
工业工程是精益生产的基础,精益生产离不开工业工程的支撑。
也就是说工业工程做到极致就是精益生产。
谢谢参与!
下回我们再继续.,