降低镀锡线锡的消耗研发研究报告.docx
《降低镀锡线锡的消耗研发研究报告.docx》由会员分享,可在线阅读,更多相关《降低镀锡线锡的消耗研发研究报告.docx(28页珍藏版)》请在冰点文库上搜索。
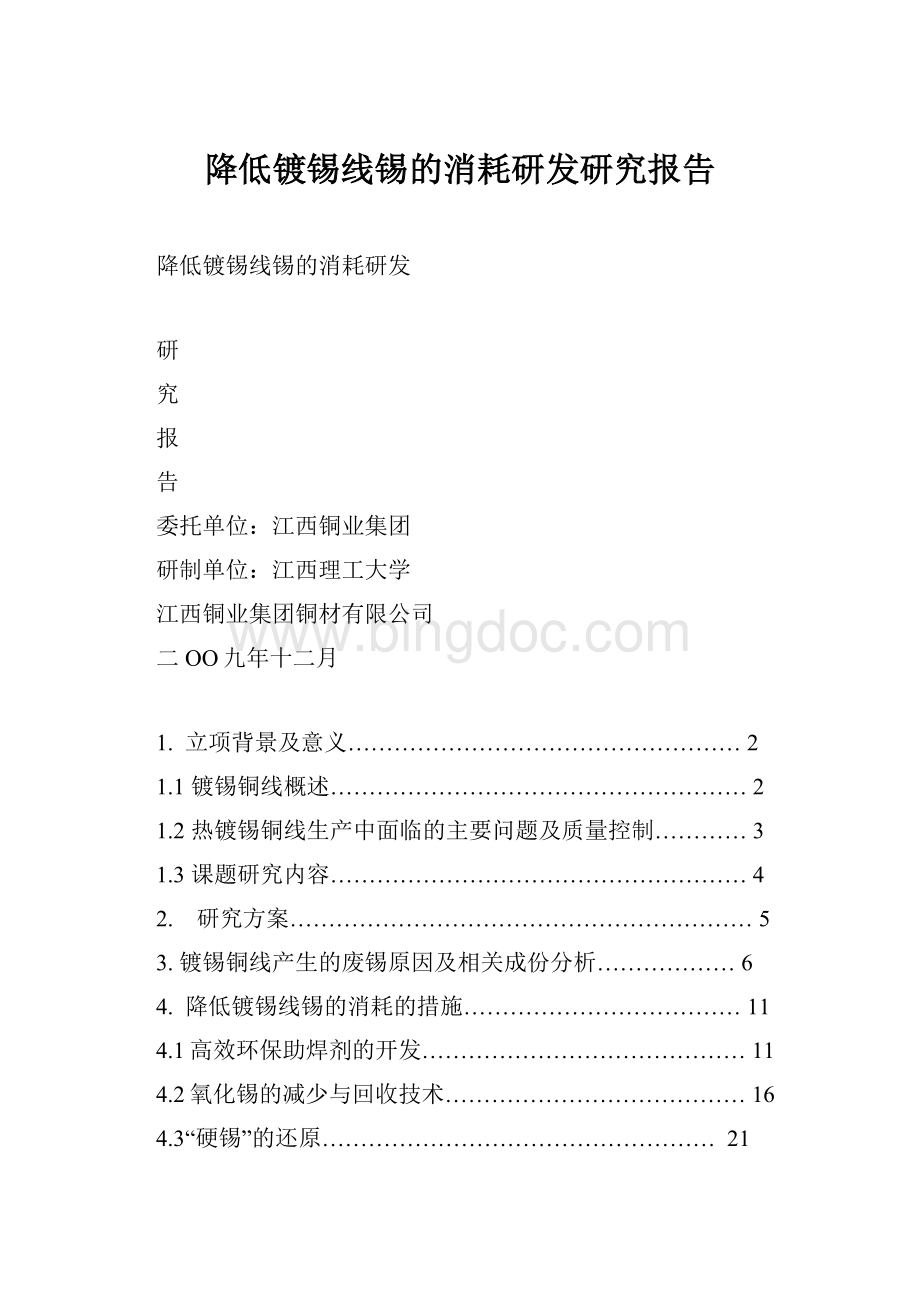
降低镀锡线锡的消耗研发研究报告
降低镀锡线锡的消耗研发
研
究
报
告
委托单位:
江西铜业集团
研制单位:
江西理工大学
江西铜业集团铜材有限公司
二OO九年十二月
1.立项背景及意义……………………………………………2
1.1镀锡铜线概述………………………………………………2
1.2热镀锡铜线生产中面临的主要问题及质量控制…………3
1.3课题研究内容………………………………………………4
2. 研究方案……………………………………………………5
3.镀锡铜线产生的废锡原因及相关成份分析………………6
4.降低镀锡线锡的消耗的措施………………………………11
4.1高效环保助焊剂的开发……………………………………11
4.2氧化锡的减少与回收技术…………………………………16
4.3“硬锡”的还原……………………………………………21
5.工业化生产试验…………………………………………28
6.经济和社会效益分析……………………………………28
6.1助焊剂效益分析…………………………………………28
6.2锡渣利用效益分析………………………………………30
6.3降低锡消耗效益分析……………………………………30
7.知识产权分析及后续研究………………………………30
8.研制结论……………………………………………………30
1立项背景及意义
1.1镀锡铜线概述
以镀锡铜线作为线芯的电线电缆,其产量约占世界线缆产量的10%,随着高新技术产业的蓬勃发展以及各类电器设计技术性能的不断提高,镀锡铜线的需求量日益增长,其技术指标要求也日益趋高,其技术指标要求也日益趋高。
镀锡铜线的主要优点在于它能较好地防止橡胶护套中折出的游离态硫与铜发生化学反应而产生硫化铜,从而有效地避免橡胶护套发粘、发黑和硬化破裂。
另外,它大大提高了导线的可焊性及表面的抗氧化性。
因此广泛应用于橡皮绝缘的矿用电缆、软电线、软电缆和船用电缆等作为导电线芯,以及用作电缆的外屏蔽编织层和电刷线等。
镀锡工艺主要方法有热镀锡法、电解镀锡法、真空镀锡法等,其中热镀锡法为传统方法,以其工艺简单、投资少、上马快而被广泛采用。
热镀法生产镀锡铜线于近10年内在国内迅速推广,其生产效率高、操作简便,其工作原理也很简单。
热镀锡铜线的生产工艺原理是利用固态金属铜与液态金属锡的较强润湿性,使铜线以一定的速度经过具有一定温度的液态锡槽,从而完成锡的镀覆。
热镀锡的工艺流程为放线→表面处理→热浸锡→冷却→收线。
图1热镀锡铜线生产原理示意图
图1为热镀锡铜线生产的示意图,经过助焊剂的去氧化处理的裸铜线浸入到锡液槽中,在迅速通过锡液的时候,完成锡的镀覆,随后被牵出完成收线。
其中镀锡模用以控制镀锡线的尺寸和表面质量。
在热镀前,铜线一般经过退火处理,与退火炉在一起,形成一条整体生产线,在整个生产过程中,主要的工艺过程即包括退火、冷却、烘干、裸铜线表面处理、镀锡、收卷几个主要步骤。
关键在于保证裸铜线与锡液的润湿能力,并保证工艺流程的稳定性。
1.2热镀锡铜线生产中面临的主要问题及质量控制
热镀锡线虽然原理简单,但工艺控制却十分严格,需要助焊剂、走线速度、锡液温度的可靠结合。
此外,铜线质量以及锡的质量也非常重要。
镀锡铜线的原材料是铜和锡。
我厂铜线材质好,这样可以有效提高铜线在镀锡过程中的单线长度,减少镀锡铜线的断线率。
有人认为,铜线在镀锡之前要经过去氧化处理,因而对铜线的质量要求不严。
须知表面氧化严重或沾污的铜线在去氧化过程中无法在短时间内达到清洁目的,这样生产出的镀锡铜线锡层和铜体结合不牢,易脱落,且针孔较多。
正因为铜线质量直接影响到镀锡铜线的质量,因此,必须纠正对镀锡铜线用铜线质量要求不高的偏见。
我们认为镀锡铜线用铜线的质量应达到制造漆包线所用铜线的技术要求。
锡的质量也直接影响到镀锡铜线的质量。
如果使用纯度低的锡锭或市场中的杂锡,在生产过程中锡炉的温度不易控制,容易导致成品线的锡层合金化,影响锡层的连续性和附着性。
而且由于杂质过多,很容易堵塞模孔,造成频繁断线,影响成品单线长度。
因此,为了保证镀锡铜线的质量,所用的锡锭应不低于GB/T728—1984中二号锡的技术要求。
相对来说,我厂设备运行稳定,基础原材料质量可靠,在几年的生产过程中不断完善工艺制度,镀锡线生产逐渐稳定。
然而尽管如此,根据实际生产情况,值得重点的关注的主要有:
(1)助焊剂的研究,助焊剂的好坏关系到锡的损耗、环境污染以及成本的问题;
(2)提高锡的利用率,镀锡铜线产品中通常平均每吨含有金属锡约9kg(各种规格镀锡线的综合平均值),而实际生产中我厂平均每吨产品需要消耗锡原料约16kg,在热镀过程中,锡液的有效利用率通常不足60%,从多方面入手,着手提高锡的利用率,具有十分重要的现实意义。
(3)镀锡线的抗氧化研究,目前,越来越多的客户要求热镀线的表面能抗氧化,表面不发黄、不发灰,我厂尚未完全掌握此项技术,需要进行进一步研究。
热镀锡工艺简单,且设备投入低,因而被许多厂家采用。
由于各厂热镀锡的工艺不尽相同,用料和工厂水平不同,生产的镀锡铜线的质量也各不相同。
据统计,2006年我国对镀锡铜线的市场需求量为15万吨。
镀锡铜线的附加值较高,是铜材公司年利润确保的产品之一。
铜材公司于2006年建成5000吨热镀锡生产线,并于当年5月投产,2008年5月扩产8000吨,形成13000吨年生产能力。
产品主要规格φ0.08mm~0.8mm。
采用热镀锡工艺生产镀锡铜线,具有投资少、工艺简单易行、生产效率高的优点,是目前国内大多数铜线生产企业普遍采用的一种生产工艺。
铜材公司从2002年开始试生产,至今已有6年生产经验,工艺技术也很成熟。
然而,热镀法生产镀锡铜线也有其不足之处,问题之一就是耗锡量高。
在热镀锡过程中,锡的有效利用率只有50~60%,部分金属锡成为废锡。
废锡不能重复使用,目前只能降价销售,增加了生产成本。
1.3课题研究内容
本课题旨在充分研究分析铜材公司现有热镀锡铜线生产中锡消耗原因的基础上,通过研制新型助焊剂和锡合金等工艺调整措施,从多方面减少锡渣产生和烟尘排放量。
课题研究对于企业的环境改善,降低生产成本,提高经济效益,改善产品表面质量,争取更大的市场,具有重要的社会意义和经济价值。
2. 研究方案
本项目旨在降低镀锡线锡的消耗。
为此必须先分析浪费锡的原因,确定“废锡”成分,研究其成因、机理和规律,再对症下药,解决相关问题,达到保证镀锡线质量的同时,减少镀锡线锡的用量。
拟采取的方案如图2所示:
图2研究方案流程
其主要研究内容有:
1、确定锡渣、锡灰等“废锡”的成分,并充分研究其产生的各种原因、机理和规律;
2、开发新型助焊剂,研制出具有自主知识产权的助焊剂配方;
3、在锡液里添加特殊合金元素,并将其配制成抗氧化添加剂,达到减缓“硬锡”产生的效果;
4、对于无法避免产生的“锡渣”、“锡珠”、“硬锡”等集中处理,精炼成可重新回炉利用的锡料。
重点在于对锡渣精炼工艺的研究与开发。
3 镀锡铜线产生的废锡原因及相关成份分析
生产镀锡线产生的废锡来源为①锡炉表面的浮渣②锡炉底部的沉渣③溅出锡④废锡线。
要了解废锡产生的原因,需要先了解锡渣的成分。
从生产现场看,工艺废锡主要由三部分组成,一种是锡液表面的灰黑色锡皮和锡灰,一种是铜线入锡液时,锡液溅出形成的小锡珠,一种是浮于锡液表面和沉于锡锅底的“硬锡”这种“硬锡”熔点高,不能直接使用。
将这三种废锡分别作成分分析,得到结果如表1所示:
表1 废锡成分分析
废锡种类
成分构成
灰黑色锡皮和锡灰
SnO、SnO2、SnCl2、SnCl4
锡 珠
纯锡(含有少量铜)
“硬 锡”
含铜量为4%~7%wt的铜锡合金
从三种废锡的成分可分析废锡的来源。
灰黑色锡皮和锡灰主要由锡的氧化物和锡的氯化物组成。
显然,SnO、SnO2是锡液受高温氧化而生成的,另一方面,整个系统中只有助焊剂含有氯离子,因此SnCl2、SnCl4是锡液与助镀(焊)剂发生反应生成的。
助焊剂具有一定的还原性,可破坏锡的氧化膜,但其本身也会与纯锡液发生化学反应而耗费一部分锡。
第二种废锡是“锡珠”,其产生原因在于,快速行进的铜线进入锡液时,其表面沾着的液态助焊剂遇到高温时迅速气化膨胀而将锡液带起。
从成分上讲,锡珠是纯锡,可直接利用,但是由于“锡珠”是到处“溅”出来的,因此难以回收完全,但收集到的锡珠通过熔融即可回收。
第三种废锡在工业上俗称“硬锡”,在工业实践中,随着生产过程的进行,锡槽的液面会变得粘稠起来,并逐渐变硬。
从成分上分析,这种硬锡是含铜量为4%~7%wt的铜锡合金。
其产生原因在于金属铜与锡较强的亲和力,随着生产的进行,铜元素不断向锡液扩散形成铜锡合金,当达到一定铜含量时,这种铜锡合金的固相线高于锡液温度将形成固相,并浮于液面,停留在静止的液面处,因此这部分锡液将变得很粘稠或者坚硬。
由于浓度起伏的作用,加上液面温度较低,因此这个过程可以连续进行,使得“硬锡”越来越多,最终覆盖锡槽的大部分液面。
锡炉表面的浮渣是由于锡的高温氧化,锡和助焊剂的化学反应,助焊剂与铜的反应产物铜离子和锡反应,锡和铜的相互溶解等因素产生的。
底部的沉渣是铜线在锡中的溶解,以及助焊剂腐蚀铜线产生的铜离子,被锡还原成铜,又溶解在锡中,形成Cu6Sn5以及Cu-Sn互溶产生的比重大于锡的合金“硬锡”。
溅出锡为助焊剂入锡时产生的飞溅“锡珠”和操作不小心溅出的锡。
废锡线为日常生产和镀锡断线时的废品。
从损失量上看,“硬锡”是废锡的主要部分,大约在2/3左右,其次是氧化锡和锡盐约占1/3,“锡珠”的含量较少,而且可以融熔回收,锡线必须挑出另外回收。
将回收的锡渣熔融捞去浮渣,加温至剩下的锡全熔融,浇样模,得余锡的成份如表2所示。
同时将锡灰和锡渣做X射线衍射分析如图4、5所示。
表2废锡渣的存在成份
Cu/Sn之相圖
图3Sn-Cu相圖
依Sn-Cu相圖:
99.3Sn/0.7Cum.p.(約)227℃,98Sn/2Cum.p.(約)227–270℃97Sn/3Cum.p.(約)227–310℃,96Sn/4Cum.p.(約)227–335℃,95Sn/5Cum.p.(約)227–350℃,94Sn/6Cum.p.(約)227–375℃,90Sn/10Cum.p.(約)227–450℃
图4“硬锡”X衍射图
图5表面锡灰衍射图
通过精确分析,进一步印证了前面的分析:
锡的熔点随铜的含量在升高,结晶相为Cu6Sn5,表面锡灰的锡组成为SnO2、粘结的锡及其合金、助焊剂残渣和灰尘。
4降低镀锡线锡的消耗的措施
4.1高效环保助焊剂的开发
助焊剂通过去除材料表面氧化膜及污染物等,保证锡和铜线之间很好的润湿,形成良好镀锡层。
没有助焊剂是不可能获得质量好的镀锡线。
对助焊剂的研究,不仅对于锡消耗有帮助,同时也为铜材公司节约生产成本,铜材公司将自主形成助焊剂生产能力,拥有自主知识产权,意义重大。
镀锡线生产产生的锡消耗,是由于铜线上的镀锡层和镀锡过程产生的废锡。
为保证镀锡线的质量,必须保证一定镀锡层的厚度,因此该部分锡的消耗是必须的。
此处的锡厚度由锡线模的孔直径决定,但如果助焊剂对铜线的腐蚀重的话,将减少铜线的直径,从而增加锡的消耗。
减少锡的消耗,主要在减少废锡的量。
生产镀锡线产生的废锡来源为①锡炉表面的浮渣②锡炉底部的沉渣③溅出锡④废锡线。
锡炉表面的浮渣是由于锡的高温氧化,锡和助焊剂的化学反应,助焊剂与铜的反应产物铜离子和锡反应,锡和铜的相互溶解等因素产生的。
底部的沉渣是铜线在锡中的溶解,以及助焊剂腐蚀铜线产生的铜离子,被锡还原成铜,又溶解在锡中,形成Cu6Sn5以及Cu-Sn互溶产生的比重大于锡的合金“硬锡”。
溅出锡为助焊剂入锡时产生的飞溅“锡珠”和操作不小心溅出的锡。
废锡线为日常生产和镀锡断线时的废品。
从损失量上看,“硬锡”是废锡的主要部分,大约在2/3左右,其次是氧化锡和锡盐约占1/3,“锡珠”的含量较少,而且可以融熔回收,锡线必须挑出另外回收。
助焊剂是产生废锡的主要因素。
为了把锡有效的镀上铜线,必须将铜线表面的氧化膜破坏,露出光亮清洁铜表面,由于铜的化学性质比锡惰性,因此助焊剂在清洁铜线表面的同时,将不可避免会与锡发生反应。
助焊剂按其成分来分,可能分为无机助焊剂和有机助焊剂。
无机助焊剂所使用的化学成分在助焊过程中以及焊后呈残渣状时,均有很强的化学活性。
其中典型的酸有盐酸、氢氟酸和正磷酸,典型的盐有氯化亚锡、氯化锌、氯化铵和氟化物,典型的气态有氢气和氯化氢。
有机水溶性助焊剂主要有有机酸类;胺;酰胺及其衍生物;上述组分组合类。
典型的有机酸有丁二酸、己二酸、戊二酸、乳酸、谷氨酸、油酸、硬脂酸和苯二甲酸。
典型的有机卤化物有盐酸肼,氢溴酸肼和盐酸苯胺。
典型的胺和酰胺及其衍生物有乙二胺及磷酸苯胺。
主要依靠羧基或者是胺基的作用,通过化学反应除去氧化膜,具有中等去除氧化膜的能力,且作用比较缓慢,一般其助焊效果比无机助焊剂要弱,但残渣腐蚀性小。
镀锡涉及的反应如下:
CuO+2H+=Cu2++H2OCu2++Sn=Cu+Sn2+
Cu+Sn=CunSnx
CuO+2RCOOH=Cu(RCOO)2+H2O
Cu(RCOO)2+H2+Sn=RCOOH+CunSnx
Sn+H+=H2↑+Sn2+Sn+O2=SnO2
在镀锡炉的温度时,水也会与锡反应,
,因此可以说,对采用水作为溶剂的助焊剂锡渣的产生是不可避免的。
如果采用有机溶剂,可以使其不与锡发生反应,但将增加昂贵的成本,并且还具有着火的危险。
综合考虑,采用水作为配制镀锡线的助焊剂的溶剂。
助焊剂一般包括成膜剂、活化剂、添加剂和溶剂等。
1成膜剂
常用成膜物质有天然树脂、合成树脂剂和部分有机化合物。
加入成膜物质后助焊剂能形成一层致密的有机膜,防止焊接过程中熔融合金进一步氧化。
成膜物质还会形成机械、化学性质稳定的有机膜,对镀层表面和基体等部位起到一定保护作用,具有防腐蚀性和优良的电气绝缘性。
2活性剂
是为了提高助焊剂性能而加入的活性物质,主要起到去除氧化物的作用,同时还可降低合金表面张力。
活性剂的活性是指与表面氧化物等起化学反应的能力,它反映了清洁金属表面和增强润湿性的能力。
③添加剂
是为适应工艺和环境而加入的具有特殊物理和化学性能的物质。
常用添加剂有pH调节剂、消光剂、缓蚀剂、光亮剂、阻燃剂、润湿剂和发泡剂等。
3溶剂
将助焊剂各成份溶解均匀,并将其成份稀释到适当浓度的物质。
热镀锡细铜线的生产流程为:
放线→退火→浸助焊剂→镀锡→冷却→牵引→收排线等七个流程。
从该生产流程特点来看,锡线是先沾助焊剂,再入锡炉,在锡炉中穿行再过锡线模,得到镀锡线。
因为上锡后的锡线会在锡炉中穿行一段路程,这样会导致,除了已与铜线结合形成合金的锡外,表层的锡和其他物质将会流动,直至在线模处锡冷却形成镀锡铜线。
水是天然的溶剂,采用水作为镀锡助焊剂的溶剂是最合适的。
镀锡助焊剂的关键组分在活性剂。
活性剂将铜线表面的氧化层去除,裸露出新鲜的活性铜面,铜再与锡形成合金层,将锡牢固的和铜结合在一起,从而得到镀锡铜线。
这里要考虑到活性剂的活性强度、用量和残余量。
只要线不是太细,助焊剂的活性过强、过量都不致于造成断线,问题都不大,只是可能增加了锡的用量,产生的锡渣过多。
锡渣不仅是表面的浮渣,还包括形成重的铜锡沉淀渣。
有机助焊剂的活性和助焊效果弱于无机助焊剂,但它最好的特性是残渣少和腐蚀性小,一般将其用在电子线路板的器件焊接上。
镀锡线的生产特点,锡线会在锡炉中穿行一段路程,这样会导致,除了已与铜线结合形成合金的锡外,表层的锡和其他物质将会流动,不用着重考虑残渣的腐蚀问题,而且有机物价格高,一般又存在潜在的慢性中毒和致癌性,所以我们不采用有机助焊剂。
无机助焊剂一般是无机酸和它们的盐,无机助焊剂的活性一般强于有机助焊剂。
其中典型的酸有盐酸、氢氟酸和正磷酸,典型的盐有氯化亚锡、氯化锌、氯化铵和氟化物。
酸在常温下有除去氧化膜的功能,而无机盐类助焊剂不具备,但单独的无机酸的高温活化能力是有限的,而且它还会与锡发生置换反应。
活性剂的作用机理是:
在加热时释放出HC1,微量的HC1将钎料及被焊金属表面的氧化物转化为可溶于水的氯化物,使其与清洁的金属表面分离开来。
镀锡时铜线和锡接触面涉及的反应如下:
CuO+2H+=Cu2++H2O2Cu2++Sn=2Cu+Sn4+
Cu2++Sn=Cu+Sn2+Sn+H+=H2↑+Sn2+
nCu+xSn=CunSnx
加入表面活性剂增加铜线的润湿和液面起泡,减少水遇高温造成的锡飞溅。
我们通过扩展率考察了多种物质的助焊活性效果。
从GB/T2040规定的二号铜板(牌号为T2)上切取50mm×50mm×O.3mm平整试片,去油后用砂纸打磨铜板表面去除氧化膜,并用抛光膏抛光后,再用无水乙醇清洗干净并充分干燥。
将试片放在温度为(150_+2)℃的烘箱中氧化1h,所有试片放在烘箱的同一高度上。
试片从烘箱中取出后,放在密封的干燥器中备用。
取5块铜板,在每块铜板中部放一个钎料球,将助焊剂均匀涂于钎料球表面,再将这些铜板水平放置在(260±5)℃的锡炉上保持60s;取出试样水平放置,冷却至室温,如图6所示。
每种助焊剂测试5块铜板,测量焊点高度h,以5块铜板上焊点高度的算术平均值作为焊点高度。
图6扩展率试验示意图
在扩展率的计算中,将测试前的焊料看成球状,计算出小球的等效体积,然后再计算小球的标称直径D,测出铜片上的焊点高度h,根据以下公式即可求出扩展率S。
式中,D为将试验所用钎料看作球体时的直径(mm);S为扩展率(%);h为扩展润湿完成后焊点高度(mm)。
我们通过扩展率考察了多种物质的助焊活性效果,但这还仅仅是参考,还必须在生产线考察该助焊剂对镀锡产生的残渣。
经过工业试验,总结挑选出两个配方。
对助焊剂的研究已获成功,获得了合格的产品,锡炉面飞溅减少,断线率降低,从节约锡的角度看,锡盐产生量明显减轻,且环境友好。
同时,助焊剂成本大大降低。
4.2氧化锡的减少与回收技术
氧化锡也是废锡产生一个原因,同时氧化锡也给镀锡生产带来一些不良影响,当氧化锡裹入眼模时,将造成镀锡线废品,严重影响产品质量和生产效率。
课题组计划从两个方面解决这个问题,一是制备抗氧化添加剂,从本质上增强锡液的抗氧化性能,另一方面是对氧化锡进行回收。
4.2.1锡液抗氧化合金添加剂的制备
项目实施的技术路线如图7所示:
添加剂成分制定 →合金的实验室制备 →性能检测和评价 →合金成分优化 →热镀锡等应用场合试用 →继续优化成分 →工业制备添加剂 →制定添加剂的工业使用工艺。
图7 锡液抗氧化合金添加剂研究技术路线
1) 成分确定,合理制定添加元素的种类,充分考虑一些具有抗氧化性、耐腐蚀性、强还原性的元素;合理确定各种元素的添加量和配对。
2) 添加剂合金制备,一些抗氧化和耐腐蚀性高的元素往往熔点很高,而一些强还原性的元素往往在熔入时很容易烧损。
因此这类锡基中间合金的制备工艺是关键。
在制备时,充分研究各种元素的加入顺序、熔炼温度、浇铸温度、铸模设计等,综合考虑合金元素熔损率,并最终确定最佳的熔炼和铸造工艺。
并且需要利用微观手段检查中间合金的成分均匀性、合金化程度等。
3) 工业使用工艺,这主要包括不同的使用场合时使用何种添加剂,使用量以及使用方法等。
本项目研究热镀锡铜线以及锡焊料制备两种场合的抗氧化添加剂使用工艺。
A锡液抗氧化添加剂成分确定与合金配制
锡液抗氧化添加剂的成分选取原则必然是考虑合金元素的抗氧化能力、合金元素的金属相容性以及经济环保性等因素。
综合这些因素,能满足条件元素主要有Al、Mg、Ni、P四种元素。
由于锡液的工业存在温度通常很低(300℃以内),因此这四种添加元素都不能直接添加使用,需要配制成锡基合金。
好的固态锡液抗氧化添加剂应是:
1)抗氧化(或还原)效果好;2)易熔解于250~320℃的锡液中;3)易破碎,以方便配料。
因此在优化合金成分时应以此为判断依据。
为了检验几种添加元素对锡液抗氧化效果的影响,课题组专门设计了试验方案:
分别配制一定成分比例的Sn-Al、Sn-Mg、Sn-Ni和Sn-P中间合金,按一定比例往恒温锡炉中添加以上四种中间合金。
以恒速在规定时间和温度内搅拌,之后观察并称量氧化膜的产生量。
(该试验的装置示意见图8所示)
图8 抗氧化效果试验原理图
在试验装置中,每炉锡液总重量为1kg,锡炉为直径为100mm的圆形试验锡锅,锡液的加热温度为300℃,给锡液的机械搅拌速度为1r/min,试验时间为30min,到达时间后,刮取锡液氧化膜并称重,试验结果如表3所示。
表3 四种添加剂的使用性能
添加剂名称及重量百分比
氧化膜产生量/g
其它情况
锡-铝
0.5%Al
35.9
塑性极好,不易破碎;熔化较快。
0.1%Al
40.7
0.05%Al
43.6
锡-镁
0.5%Mg
18.6
极易破碎;
很难熔化。
0.1%Mg
22.2
0.05%Mg
25.5
0.02%Mg
30.7
锡-镍
0.1%Ni
18.3
塑性好,不易破碎;
熔化速度一般;
液面明亮。
0.05%Ni
20.0
0.02%Ni
22.7
0.01%Ni
23.2
锡-磷
0.1%P
10.3
极易破碎;
熔化较快;
液面明亮。
0.05%P
10.9
0.02%P
12.1
0.01%P
12.8
无添加剂
59.5
氧化皮迅速产生,液面上很多灰色锡皮。
试验表明,所选的四种添加元素对锡液均有一定的抗氧化效果,其中金属铝能适当降低锡的消耗,且随着铝含量的不同而抗氧化效果差别较大,但效果不是很明显,且锡-铝中间合金有易破碎,使用起来不是很方便;金属镁能有效减少锡液氧化膜的产生,即使镁含量<0.05wt%仍然较好的效果,但镁含量小于0.02wt%时,效果就明显更差,锡-镁中间合金易破碎,方便配料,但是熔解速度较慢,且锡-镁中间合金中镁含量越高,熔解速度越慢;金属镍也能有效降低锡的消耗,效果与镁相近,而且即使含量很低也能有效降低锡的消耗,添加时熔化速度随添加的中间合金中镍含量成反比,但在相同效果的情况下,比锡-镁中间合金的熔解速度更快;锡-磷合金的抗氧化效果十分明显,且熔化较快,也方便配料,抗氧化时间也较长。
铝、镁、镍、磷四种添加元素均能在不同程度上有效减少锡液的氧化消耗,尤其是磷元素,因此说,锡液抗氧化添加剂的最佳添加元素应为磷元素,但也可镁镍这两种元素,通过合理配比,让三种元素各自发挥自身的抗氧化效果,同时不致于影响锡液的固有性能(即单种元素的添加量不能太多)。
BSn-P合金的配制
磷是一种广泛使用的金属熔体脱氧剂,这是由于其脱氧速度快,氧化渣不留于金属熔体中,并且磷是一种经济的普遍存在的工业原料。
磷在较低温时就有很好的还原效果,十分适合用于200℃以上的金属熔体脱氧。
然而Sn-P合金的配制难度较大,图9所示为Sn-P二元合金相图。
从图中可以看出,随着磷含量的增加,合金的液相温度快速上升,这表明熔炼温度要高;相对金属锡而言,磷的密度很低,这使得熔炼时磷极易浮在锡的表面;磷极易燃烧,且蒸汽压很高,燃烧火焰大;液固两相区的温度区间高达三百多摄氏度,凝固时间长,铸造有难度。
为此,课题组高度重视,