某加热炉温度控制过程控制.docx
《某加热炉温度控制过程控制.docx》由会员分享,可在线阅读,更多相关《某加热炉温度控制过程控制.docx(19页珍藏版)》请在冰点文库上搜索。
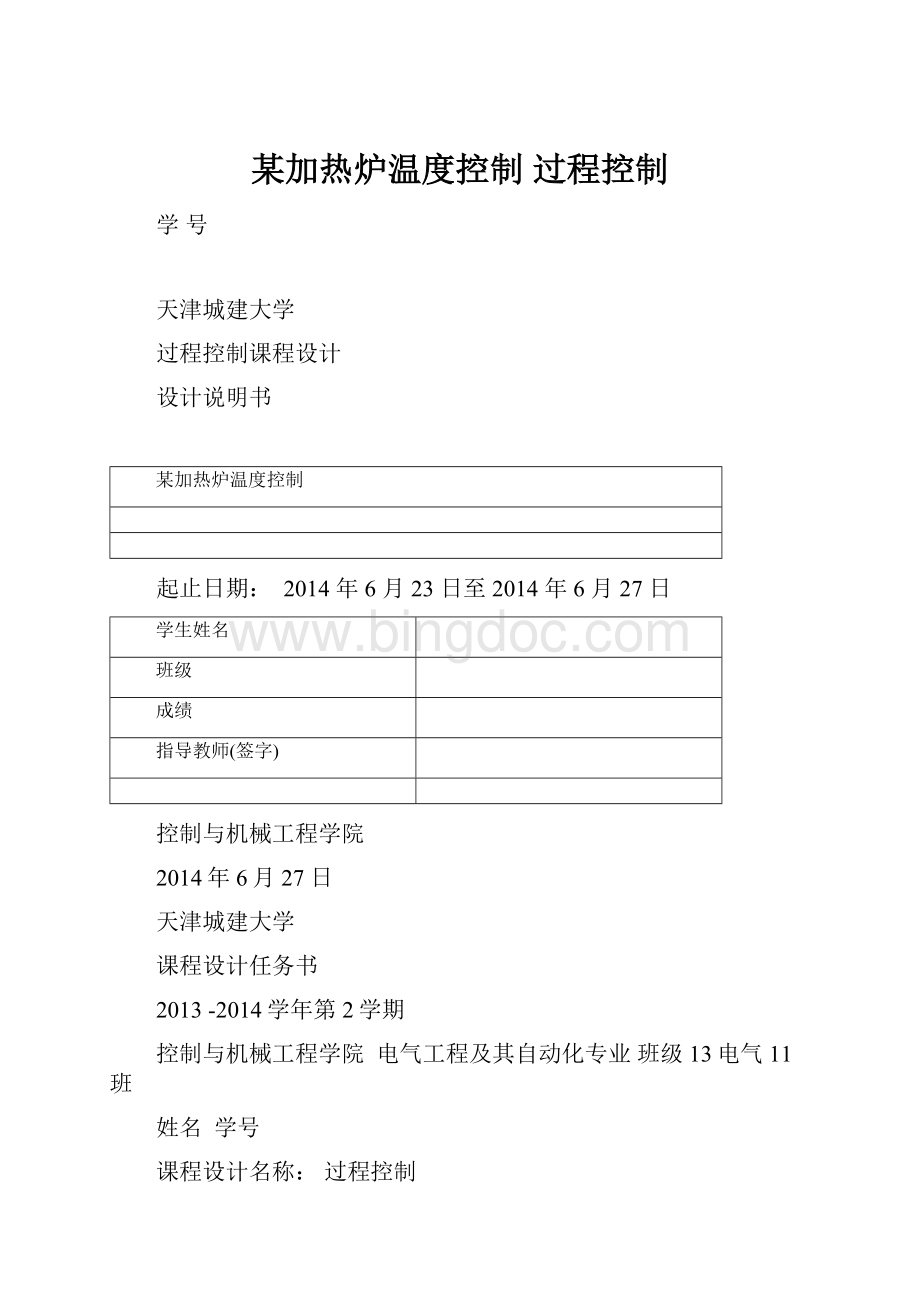
某加热炉温度控制过程控制
学号
天津城建大学
过程控制课程设计
设计说明书
某加热炉温度控制
起止日期:
2014年6月23日至2014年6月27日
学生姓名
班级
成绩
指导教师(签字)
控制与机械工程学院
2014年6月27日
天津城建大学
课程设计任务书
2013-2014学年第2学期
控制与机械工程学院电气工程及其自动化专业班级13电气11班
姓名学号
课程设计名称:
过程控制
设计题目:
某加热炉温度控制
完成期限:
自2014年6月23日至2014年6月27日共1周
设计依据、要求及主要内容:
一、设计任务
某温度过程在阶跃扰动
作用下,其温度变化的数据如下:
t/s
0
10
20
30
40
50
60
70
80
90
100
150
200
0
0.16
0.65
11.5
1.6
1.8
1.9
1.95
1.98
1.99
2.0
2.0
2.0
试根据实验数据设计一个超调量
的无差控制系统。
具体要求如下:
(1)根据实验数据选择一定的辨识方法建立对象的数学模型;
(2)根据辨识结果设计符合要求的控制系统(控制系统原理图、控制规律选择等);
(3)根据设计方案选择相应的控制仪表;
(4)对设计的控制系统进行仿真,整定运行参数。
二、设计要求
采用MATLAB仿真;需要做出以下结果:
(1)超调量
(2)峰值时间
(3)过渡过程时间
(4)余差
(5)第一个波峰值
(6)第二个波峰值
(7)衰减比
(8)衰减率
(9)振荡频率
(10)全部P、I、D的参数
(11)PID的模型
(12)设计思路
三、设计报告
课程设计报告要做到层次清晰,论述清楚,图表正确,书写工整;详见“课程设计报告写作要求”。
四、参考资料
[1]何衍庆.工业生产过程控制(1版).北京:
化学工业出版社,2004
[2]邵裕森.过程控制工程.北京:
机械工业出版社2000
[3]过程控制教材
指导教师(签字):
教研室主任(签字):
批准日期:
年月日
摘要
在工业生产中必然地要求对加热炉内的温度进行有效的控制,使之保持在某一特定的范围内。
而温度的维持又要求燃料在炉内稳定地燃烧。
加热炉燃烧过程是受随机因素干扰的,具有大惯性、纯滞后的非线性过程。
本设计针对加热炉燃烧控制系统,主要介绍的控制方案有单回路控制系统、串级比值控制系统、单交叉限幅控制系统、双交叉限幅控制系统,并对每一种控制方案进行了理论分析。
运用MATLAB软件对温度控制系统进行了较为全面的仿真和性能分析。
通过分析比较可以得出结论,双交叉限幅对加热炉温度的控制优于其它的控制方案。
双交叉限幅的炉温控制系统使煤气流量和空气流量相互限制,既防止了燃烧中冒黑烟,也防止了空气过剩,达到控制加热炉温度,提高煤气燃烧率,避免环境污染等目的。
关键词:
加热炉;单交叉限幅控制;双交叉限幅控制;MATLAB仿真
绪论1
一对象模型的建立2
1.1数学模型概念2
1.2系统各装置数学模型的建立3
二仪表选型4
2.1单回路系统选择原则4
2.2调节器5
2.3执行器7
2.4变送器8
2.5检测元件9
三控制系统仪表配接图及说明9
3.1控制系统仪表配接说明9
四加热炉炉温控制系统仿真结果分析10
4.1根据已知数据画出单位阶跃曲线10
4.2炉温单回路控制仿真10
五参考文献13
绪论
温度控制系统在国内各行各业的应用虽然已经十分广泛,但从国内生产的温度控制器来讲,总体发展水平仍然不高,同日本、美国、德国等先进国家相比,仍然有着较大的差距。
成熟的温控产品主要以“点位”控制及常规的PID控制器为主,它们只能适应一般温度系统控制,而用于较高控制场合的智能化、自适应控制仪表,国内技术还不十分成熟,形成商品化并广泛应用的控制仪表较少。
随着我国经济的发展及加入WTO,我国政府及企业对此都非常重视,对相关企业资源进行了重组,相继建立了一些国家、企业的研发中心,开展创新性研究,使我国仪表工业得到了迅速的发展。
随着新技术的不断开发与应用,近年来单片机发展十分迅速,一个以微机应用为主的新技术革命浪潮正在蓬勃兴起,单片机的应用已经渗透到电力、冶金、化工、建材、机械、食品、石油等各个行业。
传统的温度采集方法不仅费时费力,而且精度差,单片机的出现使得温度的采集和数据处理问题能够得到很好的解决。
温度是工业对象中的一个重要的被控参数。
然而所采用的测温元件和测量方法也不相同;产品的工艺不同,控制温度的精度也不相同。
因此对数据采集的精度和采用的控制方法也不相同。
传统的控制方式已不能满足高精度,高速度的控制要求,如温度控制表温度接触器,其主要缺点是温度波动范围大,由于它主要通过控制接触器的通断时间比例来达到改变加热功率的目的,受仪表本身误差和交流接触器的寿命限制,通断频率很低。
近几年来快速发展了多种先进的温度控制方式,如:
PID控制,模糊控制,神经网络及遗传算法控制等。
这些控制技术大大的提高了控制精度,不但使控制变得简便,而且使产品的质量更好,降低了产品的成本,提高了生产效率。
本系统要求有数据处理,显示功能等,被控对象为一阶惯性环节和一阶积分环节的组合,惯性时间常数为2s,开环增益k=10,温度控制范围为50~150℃。
一对象模型的建立
1.1数学模型概念
控制系统的数学模型在控制系统的研究中有着相当重要的地位,要对系统进行仿真处理,首先需要知道系统的数学模型,而后才有可能对系统进行仿真。
同样,只有知道系统模型,才有可能在此基础上设计一个合适的控制器,使系统响应达到预期效果,满足实际的工程需要。
在线性系统理论中,常用的数学模型形式有:
传递函数模型(系统的外部模型)、状态方程模型(系统的内部模型)、零极点增益模型和部分分式模型等。
这些模型之间都有着内在的联系,可以相互进行转换。
微分方程是控制系统模型的基础,一般来讲,利用机械学、电学、力学等物理规律便可以得到控制系统的动态方程,这些方程对于线性定常连续系统而言是一种常系数的微分方程。
控制系统动态微分方程的建立基于以下两个条件:
(1)在给定量产生变化或扰动出现之前,被控量的各阶导数都为零,即系统是处于平衡状态的,因此,在任一瞬间,由各种不同环节组成的自动控制系统用几个独立变量就可以完全确定系统的状态。
(2)建立的动态微分方程式是以微小增量为基础的增量方程,而不是其绝对值的方程,因此,当出现扰动和给定量产生变化时,被控量和各独立变量在其平衡点附近将产生微小的增量,微分方程式描述的是微小偏差下系统运动状态的增量方程,不是运动状态变量的绝对值方程,也不是大偏差范围内的增量方程。
动态微分方程描述的是被控制量与给定量或扰动量之间的函数关系,给定量和扰动量可以看成系统的输入量,被控制量看成输出量。
建立微分方程时,一般从系统的环节着手,先确定各环节的输入量和输出量,以确定其工作状态,并建立各环节的微分方程,而后消去中间变量,最后得到系统的动态微分方程。
动态系统数学模型有多种表达形式,可以是微分方程、差分方程,也可以是传递函数、状态方程。
微分方程描述的系统模型,通过求解微分方程,可以得到系统随时间变化的规律,比较直观。
但是,当微分方程阶次较高时,微分方程的求解变得十分困难,不易实现,而采用拉氏变换就能把问题的求解从原来的时域变换到复频域,把微分方程变为代数方程,而代数方程的求解通常是比较简单的,求解代数方程后,再通过拉式反变换得到微分方程的解。
传递函数是在拉式变换的基础上,以系统本身的参数所描述的线性定常系统输入量和输出量的关系式,它表达了系统内在的固有特性,而与输入量或驱动函数无关。
它可以是有量纲的,也可以是无量纲的,视系统的输入量、输出量而定,它包含着联系输入量与输出量所需要的量纲。
它通常不能表明系统的物理特性和物理结构,许多物理性质不同的系统却有着相同的传递函数,正如一些不同的物理现象可以用相同的微分方程描述一样。
加热炉具有大滞后、大惯性的特点,将加热炉简化为一个带有纯滞后的一阶惯性环节,则温度对象传递函数为:
(1-1)
此外,燃料流量对象和空气流量对象本设计将把它们近似看成一阶惯性环节,相应的传递函数如下:
燃料流量对象传递函数:
(1-2)
空气流量对象传递函数:
(1-3)
1.2系统各装置数学模型的建立
1.PID调节器数学模型的建立
在温度PID调节器中,有比例、积分、微分三个环节,比例、积分、微分在PID调节器中的作用如下:
P调节器的输出与输入成比例关系,只要有偏差存在,调节器的输出立刻与偏差成比例的变化,因此比例调节作用及时迅速,这是它的一个显著特点。
但是这种调节器用在控制系统中,将会使系统出现余差。
也就是说,当被控变量受干扰影响而偏离给定值后,不可能再回到原先数值上,因为如果被控变量值和给定值之间的偏差为零,调节器的输出不会发生变化,系统也就无法保持平衡。
为了减小余差,可增大Kp。
Kp越大,余差也越小。
但是Kp增大将使系统的稳定性变差,容易产生振荡。
P调节器一般用于干扰较小,允许有余差的系统中。
具有比例积分运算规律的调节器为PI调节器。
对PID调节器而言,当微分时间TD=0时,调节器呈PI调节特性。
只要偏差存在,积分作用的输出就会随时间不断变化,直到偏差消除,调节器的输出才稳定下来。
这就是积分作用能消除余差的原因。
TI越短,积分速度越快,积分作用就越强。
由于积分输出是随时间积累而逐渐增大的,故积分动作缓慢,这样会造成调节不及时,使系统稳定裕度下降。
因此积分作用一般不单独使用,而是与比例作用组合起来构成PI调节器,用于控制系统中。
微分作用是根据偏差变化速度进行调节。
即使偏差很小,只要出现变化趋势,就有调节作用输出,故有超前调节之称。
在温度、成分等控制系统中,往往引入微分作用,以改善控制过程的动态特性,不过在偏差恒定不变时,微分作用输出为零,故微分作用也不能单独使用。
比例调节作用及时迅速,积分的作用是为了消除静态误差和稳定控制对象的作用,微分的作用是为了克服加热炉的大惯性。
则温度PID调节器的传递函数表示如下:
(1-4)
空气和燃料流量PID调节器设为纯比例,即(Kp)。
如果系统接受一个阶跃信号,此时执行器由一个开度变化成另一开度,那么中间就有一个过渡过程,但过渡过程时间通常比较短。
所以,可以将其传递函数近似为一阶惯性环节,如下:
(1-5)
因为时间常数比较小,在要求不是很精确的场合也可以近似为比例。
检测和变送装置把输入信号和输出信号看成线性化,在此作为一个比例环节来对待。
由于加热炉一般都属于一阶对象和带纯滞后的一阶对象,被控对象传递函数可表示为:
(1-6)
式中Kf—被控对象的放大系数;
Tf—被控对象的时间常数;
τ—纯滞后时间。
考虑被控对象为加热炉炉温,因此取Kf=1:
Tf=3,τ=3所以加热炉的传递函数为:
二仪表选型
2.1单回路系统选择原则
单回路控制系统选择被控参数时要遵循以下原则:
在条件许可的情况下,首先应尽量选择能直接反应控制目的的参数为被控参数;其次要选择与控制目的有某种单值对应关系的间接单数作为被控参数;所选的被控参数必须有足够的变化灵敏度。
故在本系统中选择物料的出口温度θ作为被控参数。
工业过程的输入变量有两类:
控制变量和扰动变量。
其中,干扰时客观存在的,它是影响系统平稳操作的因素,而操纵变量是克服干扰的影响,使控制系统重新稳定运行的因素。
而控制参数选择的基本原则为:
①选择对所选定的被控变量影响较大的输入变量作为控制参数;
②在以上前提下,选择变化范围较大的输入变量作为控制参数,以便易于控制;
③在①的基础上选择对被控变量作用效应较快的输入变量作为控制参数,使控制系统响应较快;
故本系统选择燃料的流量Qg量作为控制参数。
对温度的控制算法,采用技术成熟的PID算法,对于时间常数比较大的系统来说,其近似于连续变化,因此用数字PID完全可以得到比较好的控制效果。
简单的比例调节器能够反应很快,但不能完全消除静差,控制不精确,为了消除比例调节器中残存的静差,在比例调节器的基础上加入积分调节器,积分器的输出值大小取决于对误差的累积结果,在差不变的情况下,积分器还在输出直到误差为零,因此加入积分调节器相当于能自动调节控制常量,消除静差,使系统趋于稳定。
积分器虽然能消除静差,但使系统响应速度变慢。
进一步改进调节器的方法是通过检测信号的变化率来预报误差,并对误差的变化作出响应,于是在PI调节器的基础上再加上微分调节器,组成比例、积分、微分(PID)调节器,微分调节器的加入将有助于减小超调,克服振荡,使系统趋于稳定,同时加快了系统的稳定速度,缩短调整时间,从而改善了系统的动态性能,其控制规律的微分方程为:
(1-7)
传递函数为:
(1-8)
用PID控制算法实现加热炉温度控制是这样一个反馈过程:
比较实际物料出口温度和设定温度得到偏差,通过对偏差的处理获得控制信号,再去调节加热炉的燃料流量,从而实现对炉温的控制。
图2-1电动III型调节器构成方框图
2.2调节器
实现PID算法的控制仪表的主要类型大致分为电动或气动,电动I型、II型、III型,单元组合仪表或是基地是仪表等。
常用的控制仪表有电动II型、III型。
在串级控制系统中,选用的仪表不同,具体的实施方案也不同。
电动III型和电动II型仪表就其功能来说基本相同,但是其控制信号不相同,控制II型典型信号为
,而电动III型仪表的典型信号为
,此外。
III型仪表较II型仪表操作、维护更为方便、简捷,同时III型仪表还具有完善的跟踪、保持电路,使得手动切换非常方便,随时都可以进行切换,且保证无扰动。
作用方式选择:
对于单回路控制系统,调节器正、反作用的选择要根据控制系统所包括的各个环节的情况来确定,这样只要根据被控参数与变送器放大倍数的符号及整个控制回路开环放大倍数的符号为“负”的要求,就可以确定调节器的正、反作用。
在本系统中,被控参数的放大倍数为的符号为“正”,所以调节器应选“负”作用即反作用。
本系统采用的DDZ-III型PID调节器TDM-400。
其主要技术参数见下表:
表2-1DDZ-III型PID调节器性能指标
名称
性能
输入信号
1-5V直流电压
外给定信号
4-20mA直流电流(输入电阻250Ω)
输出信号
4-20mA直流电流
负载电阻
250Ω-750Ω
输入与给定指示
0-100%,指示误差为
1.0%
输出信号指示
0-100%,指示误差为
2.5%
整定参数
(F=1情况下)
比例带Xp=2-500%连续可调,最大值刻度误差
2.5%;
积分时间Ti有两档0.01-2.5分与0.1-25分。
分别连续可调,最大值与最小值刻度误差为
%;
微分时间Td=0.04-10分,连续可调,最大刻度误差为
%
干扰系数F
积分增益Kd
Kd
10
闭环跟踪误差
DDZ-III型调节器接线端子如下图所示:
图2-2DDZ-III型调节器TDM-400接线端子图
2.3执行器
执行器在控制系统中的作用是接受来自控制器的控制信号,通过其本身开度的变化,从而达到控制流量的目的。
执行器在结构上分为执行机构和调节机构。
其中执行机构包括气动、电动和液动三大类,而液动执行机构使用甚少,同时气动执行机构中使用最广泛的是气动薄膜执行机构,因此执行机构的选择主要是指对气动薄膜执行机构和电动执行机构的选择,由于气动执行机构的工作温度范围较大,防爆性能较好,故本系统选择气动薄膜执行机构并配上电/气阀门定位器。
调节阀的开、关形式需要考虑到以下几种因素:
①生产安全角度:
当气源供气中断,或调节阀出故障而无输出等情况下,应该确保生产工艺设备的安全,不至发生事故;
②保证产品质量:
当发生控制阀处于无源状态而恢复到初始位置时,产品的质量不应降低;
③尽可能的降低原料、产品、动力损耗;
④从介质的特点考虑。
综合以上各种因素,在加热炉温度控制系统中,执行器的调节阀选择气开阀:
执行机构采用正作用方式,调节机构正装以实现气开的气动薄膜调节蝶阀。
图2-3电/气阀门定位器和气动调节阀组成的系统框图
调节阀的流量特性:
调节阀的流量特性的选择,在实际生产中常用的调节阀有线性特性、对数特性、抛物线特性和快开特性四种,在本系统中执行器的调节阀的流量特性选择等百分比特性。
调节阀的口径:
调节阀的口径的大小,直接决定着控制介质流过它的能力。
为了保证系统有较好的流通能力,需要使控制阀两端的压降在整个管线的总压降中占有较大的比例。
1.本系统选用电/气阀门定位器ZPD-01和薄膜气动调节阀ZMBS-16K。
其主要技术参数见下表:
表2-3ZPD-01参数表
名称
性能
输入信号
4-20mA·DC
输出信号
0-0.14MPa
2.4变送器
变送器在自动检测和控制系统中的作用,是对各种工艺参数,如温度、压力、流量、液位、成分等物理量进行检测,以供显示、记录或控制之用。
无论是由模拟仪表构成的系统,还是由计算机控制装置构成的系统,变送器都是不可缺少的环节,获取精确和可靠的过程参数值是进行控制的基础。
本系统中的变送器用于温度信号变送,故选择温度变送器。
其中较为常用的有模拟式温度变送器、一体化温度变送器和智能式温度变送器三种,本系统采用典型模拟式温度变送器中的DDZ-III型热电偶温度变送器,属安全火花型防暴仪表,还可以与作为检测元件的热电偶相配合,将温度信号线性的转换成统一标准信号。
DDZ-Ⅲ类仪表相对于DDZ-Ⅱ类仪表的一个优点是电流范围不是从零开始,这样就避免了把仪表不能正常工作误认为是输出为零,所以应选择DDZ-Ⅲ型K型热电偶温度变送器。
本系统选择型号为HR-WP-20-1TC20K-W的单输入单输出热电偶温度变送器。
主要特点有:
全智能、数字化、可编程;环境温度、零点、满幅自动补偿;符合国际电工委员会IEC61000相关抗电磁干扰标准。
其主要技术参数见下表:
表2-4热电偶温度变送器参数表
名称
性能
系统传输准确度
±0.5%×F.S(可订制±0.2%)
冷端温度补偿准确度
±1℃(预热时间30分钟)
输入阻抗
电流—100Ω;电压—500KΩ
电流输出允许外接的负载阻抗
4~20mA≤350Ω;0~10mA≤700Ω
温度漂移
<0.005%F.S/℃
工作环境温度
-10—+55℃
供电电源
直流,DC24V±10%;交流,AC95~265V
2.5检测元件
温度的测量方式有接触式测温和非接触式测温两大类。
本系统选择接触式测温元件。
其中较为常用的有热电偶、热电阻和集成温度传感器三种,由于系统对温度的要求不是很高,一般的测温元件即可满足要求,故选择K型热电偶作为测温元件,其电路原理图如下图所示:
、
图2-5热电偶电路原理图
三控制系统仪表配接图及说明
3.1控制系统仪表配接说明
接线图主要由接线板W、温度变送器K(HR-WP-20-1TC20K-W)、电动III型调节器T(TDM-400)、电/气阀门定位器Z(ZPD-01)和气动薄膜调节阀S(ZMBS-16K)五个部分组成。
K型热电偶的输出接入温度变送器HR-WP-20-1TC20K-W的输入信号端K1(-),K2(+);变送器输出信号由K9(+),K10(-)端子接至电动III型调节器TDM-400的输入信号端T1(+),T2(-);调节器的输出信号由T13(+),T14(-)端子接至电/气阀门定位器ZPD-01的输入信号端子Z1(+),Z2(-);阀门定位器的输出信号由Z3(+),Z4(-)端子接至气动薄膜调节阀ZMBS-16K的输入信号端子S1(+),S2(-)。
表3-1接线图元器件
编号
名称
个数
型号
1
电/气阀门定位器
1
ZPD-01
2
气动薄膜角型调节阀
1
ZMBS-16K
3
热电偶温度变送器
1
HR-WP-20-1TC20K-W
4
电动III型调节器
1
TDM-400
四加热炉炉温控制系统仿真结果分析
基于各种控制方案的讨论,在仿真环节对各种控制方案进行了仿真。
4.1根据已知数据画出单位阶跃曲线
图4-1数据画出单位阶跃曲线
4.2炉温单回路控制仿真
(3-1)
图4-2PID控制仿真原理图
当KP=1.2TI=0.24TD=1.5时,阶跃响应结果如图4-3所示:
由传递函数画出系统的阶跃响应曲线
图4-3调节前的阶跃响应曲线
当KP=0.9TI=0.2TD=1.2时,阶跃响应结果如图4-4所示
图4-4调节后的阶跃响应曲线
(13)超调量=(1.65-1.5)/1.5*100%=10%
(14)峰值时间=25s
(15)过渡过程时间=125s
(16)余差=0
(17)第一个波峰值=25s
(18)第二个波峰值=76s
(19)衰减比=1.06
(20)衰减率=0.06
(21)振荡频率=0.0314
五参考文献
[1]金以慧主编.过程控制.北京:
清华大学出版社2010年
[2]乐嘉谦主编.仪表工手册.北京:
化学工业出版社,2004年;
[3]张毅、张宝芬、曹丽、彭黎辉编著.自动检测技术及仪表控制系统[M].北京化学工业出版社,2009年
[4]周泽魁主编.控制仪表与计算机控制装置.北京:
化学工业出版社,2009年;
[5]工业自动化仪表手册编辑委员会编.工业自动化仪表手册.第三册产品部分
(二),北京:
机械工业出版社,1986年
[6]高金生责任编辑.仪器仪表产品目录(第二册).北京:
机械工业出版社,1991年