从化工企业生产事故原因看实现本质安全的重要性.docx
《从化工企业生产事故原因看实现本质安全的重要性.docx》由会员分享,可在线阅读,更多相关《从化工企业生产事故原因看实现本质安全的重要性.docx(8页珍藏版)》请在冰点文库上搜索。
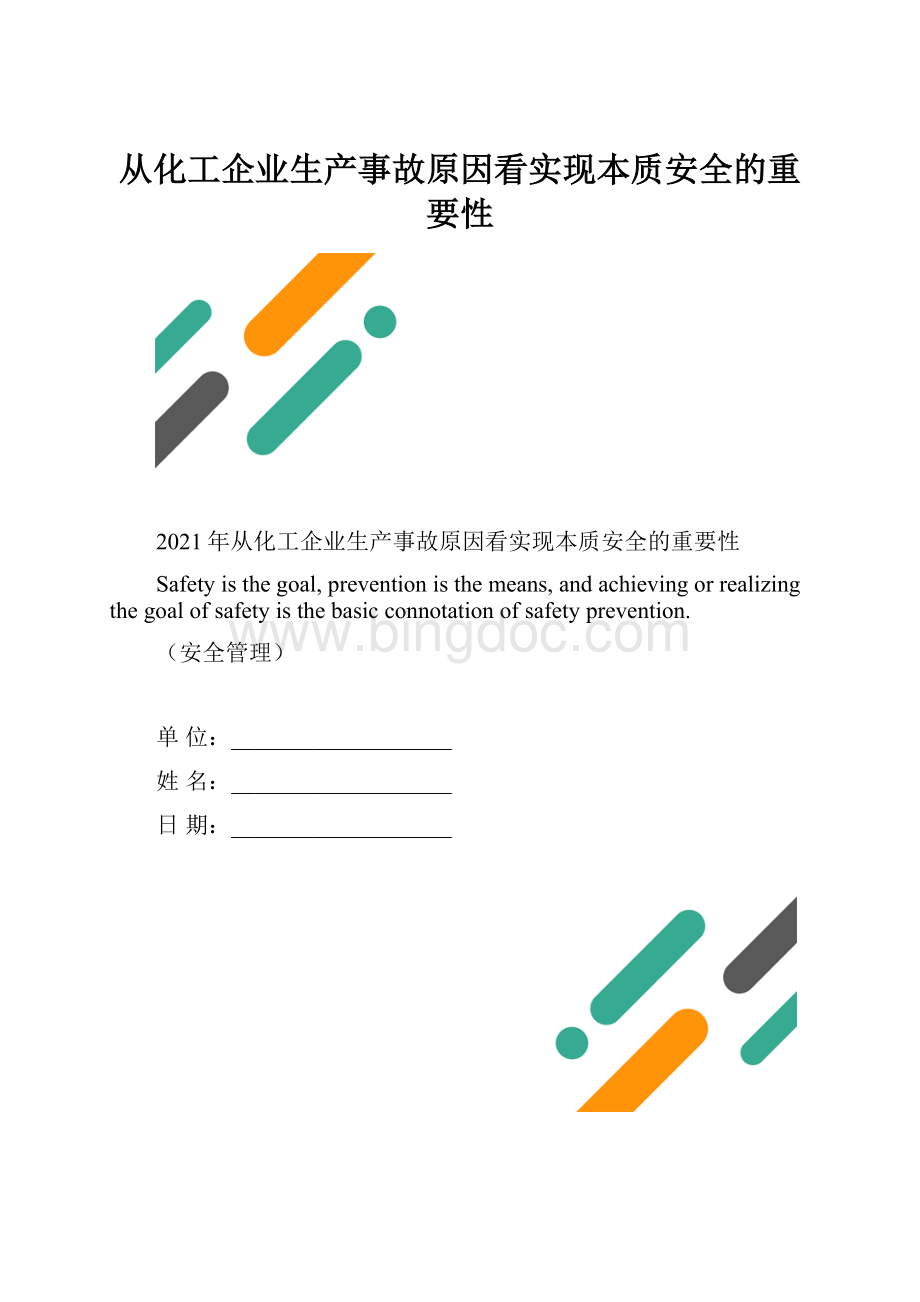
从化工企业生产事故原因看实现本质安全的重要性
2021年从化工企业生产事故原因看实现本质安全的重要性
Safetyisthegoal,preventionisthemeans,andachievingorrealizingthegoalofsafetyisthebasicconnotationofsafetyprevention.
(安全管理)
单位:
___________________
姓名:
___________________
日期:
___________________
2021年从化工企业生产事故原因看实现本质安全的重要性
导语:
做好准备和保护,以应付攻击或者避免受害,从而使被保护对象处于没有危险、不受侵害、不出现事故的安全状态。
显而易见,安全是目的,防范是手段,通过防范的手段达到或实现安全的目的,就是安全防范的基本内涵。
一、引言
化学工业的迅猛发展正在给人类生活带来巨大的变化,并已成为国民经济的支柱产业,但化工过程具有生产流程长、工序多、工艺复杂的特点,既有高温、高压,也有低温、低压,同时生产过程中具有危险特性,原料、中间产品、产品及废弃物大多具有易燃、易爆或有毒、有害、易腐蚀的特性,生产工艺过程的这些因素决定了化工生产事故具有发生突然、扩散迅速、持续时间长、涉及面广和危害后果严重等特点。
据统计,全球每年因化工事故和化学危害所造成的损失已超过4000亿元人民币。
因此,分析化工企业生产事故的原因、特点和规律,提出有效的事故防范措施,遏制事故的发生,减少事故造成的损失,具有很重要的意义。
二、化工事故致因分析
海因里希首先提出了事故因果连锁论,用以阐明导致伤亡事故的各种原因及与事故之间的关系。
海因里希认为,人的不安全行为、物的不安全状态是事故发生的直接原因,亦即事故的发生是由人的不安全行为和物的不安全状态共同作用的结果,其物理本质是一种意外释放的能量。
全方位考量我国化工行业企业发生事故的原因主要有三个方面:
⑴化学工业是危险的行业,对从业职工的要求比较高。
目前我国许多化工企业(尤其是中小型化工企业)的职工素质差,常常因为误操作而造成事故;
⑵化工行业生产的工艺过程存在很多的危险因素,生产中使用的原料、中间体和产品绝大多数具有易燃易爆、有毒有害、腐蚀等危险性,加之生产工艺过程复杂、工艺条件苛刻,从原料到产品,需要经过许多工序和复杂的加工单元,并且生产过程连续性强,存在腐蚀、高温、高压等易造成事故的诸多因素;
⑶安全管理不到位,安全生产法规、规章制度不健全,监察力度不够,安全投入不足,不能摆正安全与经济效益的关系等,这些往往为事故的发生埋下了深层次的隐患。
虽然从业人员素质不高、化工行业高危险特点以及安全管理存在问题等三方面因素是造成我国化工企业事故多发的原因,但从引发事故的直接原因“物的不安全状态”因素盾,通过对大量化工事故分析表时,引发事故的根源有这样几个方面:
工厂选址不合适、工厂布局不合理、设施设备不健全、安全距离不足、工艺存在问题、物料输送存在危险因素、设备缺陷等,其中,因为设备缺陷造成事故所占比例很大。
特别是目前我国建于上世纪六七十年代的化工企业还很多,并且在化工企业中,90%以上是生产规模较小的中小企业,工艺落后、技术水平低、设备简陋、自动化控制水平差,因此,从总体上看可以说,化工行业整体技术水平不高、本质安全程度差,是造成化工行业企业事故多发、事故危害严重的重要原因。
化工事故模式也反映了绝大多数化工事故的发生是由于化工工艺和设备出现了事故隐患,而作业人员未发现、未及时地采取措施或处理不当导致的。
因此,改善化工工艺、提高生产装置设备水平,亦即提高化工行业整体过程控制技术水平的本质安全程度是保障化工行业企业安全生产和发展成长的根本条件。
三、化工企业因本质安全问题引发的事故案例
由本质安全问题相关原因引发的化工企业事故,特别是引起中央各级领导、有关安全监管部门高度重视以及业界广泛关注的典型事故案例很多,不管是往年发生的还是今年发生的,事故都非常令人震惊,教训都非常惨痛,让我们记忆深刻。
1、近年典型事故案例
案例一沧州大化TDI公司“5.11”硝化装置爆炸事故
2007年5月11日,化工集团沧州大化TDI公司TDI(甲苯二异氰酸酯)车间硝化装置发生爆炸事故,造成5人死亡,80人受伤,其中14人重伤,厂区内供电系统严重损坏,附近村庄几千名群众疏散转移。
对事故原因进行调查分析后,得出此次爆炸事故的直接原因是一硝化系统在处理系统异常时,酸置换操作使系统硝酸过量,甲苯投料后,导致一硝化系统发生过硝化反应,生成本应在二硝化系统生成的二硝基甲苯和不应产生的三硝基甲苯(TNT)。
因一硝化静态分离器内无降温功能,过硝化反应放出大量的热无法移出,静态分离器温度升高后,失去正常的分离作用,有机相和无机相发生混料。
混料流入一硝基甲苯储槽和废酸储槽,并在此继续反应,致使一硝化静态分离器和一硝基甲苯储槽温度快速上升,硝化物在高温下发生爆炸。
调查还发现该工厂布局不合理、消防水泵设计不合理等问题。
从这起重大爆炸事故的原因看,TDI(甲苯二异氰酸酯)生产车间生产过程中从工艺技术、设备工况异常处置能力、硝化反应系统自动化控制等等存在一连串的问题,实质问题是化工过程控制技术水平不高,是化工过程本质安全度不高。
案例二吉化双苯厂硝基苯精馏塔爆炸事故
2005年11月13日,中国石油天然气股份有限公司吉林石化分公司双苯厂硝基苯精馏塔发生爆炸,造成8人死亡,60人受伤,直接经济损失6908万元,并引发松花江特别重大水污染事件。
此特大安全生产责任事故由国务院事故及事件调查组进行调查和分析,认定爆炸事故的直接原因是:
硝基苯精制岗位外操人员违反操作规程,在停止粗硝基苯进料后,未关闭预热器蒸汽阀门,导致预热器内物料气化;恢复硝基苯精制单元生产时,再次违反操作规程,先打开了预热器蒸汽阀门加热,后启动粗硝基苯进料泵进料,引起进入预热器的物料突沸并发生剧烈振动,使预热器及管线的法兰松动、密封失效,空气被吸入系统,由于摩擦、静电等原因,导致硝基苯精馏塔发生爆炸,并引发其他装置、设施连续爆炸。
国家安监总局在安监总危化字(2005182号)文件中也公布了该双苯厂苯胺装置爆炸事故的原因。
文件说,经调查分析,这起事故的直接原因是由于当班操作工停车时,疏忽大意,未将应关闭的阀门及时关闭,误操作导致进料系统(预热器E102及附属管线)温度超高,长时间后引起爆裂,随之空气被抽入负压操作的T101塔,引起T101塔、T102塔发生爆炸,随后致使与T101塔、T102塔相连的2台硝基苯储罐及附属设备相继爆炸,随着爆炸现场火势增强,引发了装置区内的2台硝酸储罐爆炸,并导致与该车间相邻的55号罐区内的1台硝基苯储罐、2台苯储罐发生爆炸。
此事故不但造成重大人员伤亡,还引发了引起国际争端的特别重大水污染事件。
此次特大事故直接原因虽然是由于操作人员违反操作规程引起的,但从操作的具体过程看,在这样高温高压、有毒有害、反应过程复杂、操作过程繁复的岗位,都要求操作工一步一步手工操作,且温度超出工艺要求时无报警及联锁控制,足以说明实质问题仍然是过程控制本质安全化不高的问题。
由于此事件影响巨大,并且国内共有19家企业拥有20套此类苯胺装置,因此不断有人对苯胺装置本质在设计上、技术工艺上是否存在先天性的安全问题表示关心。
对此,对生产工艺研究较深的清华大学化工系学位委员会主任魏飞教授和专门研究苯胺装置的骞伟中博士认为,从国内外苯胺装置设计与工艺上看,国内苯胺装置所配套的等温硝化装置与国外绝热硝化装置相比,技术上较为落后,实有提升技术水平的必要。
案例三重庆天原化工总厂氯气泄漏爆炸事故
2004年4月15日下午,重庆天原化工总厂氯氢分厂2号氯冷凝器出现穿孔,有氯气泄漏,厂方随即进行处置。
16日1时左右,列管发生爆炸;4时左右,再次发生局部爆炸,大量氯气向周围弥漫。
由于附近民居和单位较多,重庆市连夜组织人员疏解居民。
16日17时57分,5个装有液氯的氯罐在抢险处置过程中突然发生爆炸,当场造成9人死亡。
此次氯气泄漏爆炸事故,导致重庆市江北区、渝中区、沙坪坝区近15万人疏散,引起了中共中央、国务院和重庆市委、市政府的高度重视,在社会上造成了恶劣影响。
这次事故是我国氯碱工业生产史上从未有过的重大生产安全事故,事故原因很复杂,有设备腐蚀问题、压力容器管理问题,有搬迁问题,有设备更新投入不足、对NCl3爆炸机理不明等问题。
但事故的直接原因是设备腐蚀穿孔导致盐水泄漏,是造成NCl3形成和聚集并导致爆炸的重要原因。
根据技术鉴定和专家的分析,造成氯冷凝器列管腐蚀穿孔的原因主要有5个方面,这里不再赘述。
总之,直接原因是设备问题,是本质安全化不高的问题。
案例四“9.2”TDI生产线光气室爆炸事故
1999年9月2日,甘肃省白银市某厂TDI生产线光气室发生爆炸事故,造成3人死亡,5人重伤,8人轻伤,直接经济损失达4821.8万元,属特别重大事故。
事故调查组结论:
“9.2”光气室爆炸事故的直接原因是光气室内K520甲苯解吸塔发生甲苯蒸气泄漏,使光气室内充满了甲苯蒸汽与空气的混合气体,达到爆炸极限,由于光气室内电器线路短路或者甲苯蒸汽喷射产生静电火花,将该爆炸性混合气体点燃,使光气室内发生了整体爆炸。
调查组认定此起事故的性质是一起因设计存在严重缺陷,而造成的责任事故,调查认为,由于光气室设计上的严重缺陷,造成了严重的腐蚀性和可燃性气体聚集,为爆炸事故发生创造了物质条件。
2、今年发生的事故
案例一辽宁省辽阳市金航公司爆炸事故
2008年9月14日,辽宁省辽阳市灯塔市的金航石油化工有限公司发生爆炸事故,造成2人死亡,1人下落不明、2人轻伤。
初步分析,该起事故的主要原因是,在滴加异辛醇进行硝化反应的过程中,当班操作工违章脱岗,反应失控时,没能及时发现和处置,导致反应釜内温度、压力急剧上升,釜内物料从反应釜顶部的排放口喷出,喷到成品库房内的可燃物上,导致着火,引发成品库内堆积的桶装硝酸异辛酯爆炸,并引起厂内其他物料爆炸、燃烧。
经查,该企业的硝化反应釜没有装备高温报警和高温联锁停车及超温时自动排料装置;冷冻盐水系统也没有自动调节装置,仅靠操作工人现场监控、操作。
案例二广维化工“8.26”爆炸事故
2008年8月26日,广西河池宜州市维尼纶集团有限责任公司发生爆炸事故,爆炸引发的火灾导致车间内装有甲醇、乙炔、酸酸乙烯等易燃易爆危化品的储罐发生爆炸。
事故造成20人死亡,60人受伤住院治疗(其中6人伤势严重)。
事故还造成周围3km范围内18个村屯和广维集团生活区的11500名群众紧急疏散。
事故的具体原因至今仍在调查中。
在“8.26”爆炸事故发生后,国家安监总局副局长孙华山率危化司及有关专家组成的工作前往事故现场,指导事故抢险和调查处理等工作。
在指导事故现场抢险后孙华山表示:
“8.26”爆炸事故是近10年来全国伤亡最严重的化工事故。
他指出,要制定化工行业安全发展规划,严格生产和储存建设项目安全设施设计审查,从源头上消除工艺技术落后、安全没有保障的新建项目。
案例三云南齐天化“6.12”硫化氢中毒事故
2008年6月12日发生在云南省安宁市齐天化肥有限公司的硫化氢中毒事故造成了6人死亡,28人受伤。
根据事故调查组的调查,这起事故的主要原因是工艺设计存在严重缺陷,管理和从业人员未充分认识到硫化氢气体中毒的隐患,未佩戴应急救援防护器材,进行盲目施救,导致事故扩大。
调查还发现,齐天化公司未按规定办理危险化学品建设项目安全生产“三同时”行政许可手续,项目实施未经审批,无安全生产设施和装置。
案例四浙江武义博阳实业公司火灾和燃爆事故
2008年1月15日,浙江省武义县博阳实业有限公司重排车间在生产过程中发生燃爆事故,造成4名工人死亡。
该化工公司主要产品是二甲基硅油。
从调查情况看,该公司未经安全条件论证,擅自改变生产工艺,还存在工厂布局不合理、危险场所电气设备不防爆等问题。
上面列举的几起事故安全,是发生在我国近年和今年化工行业企业的影响较大、死亡人员较多、损失较惨重的事故。
从这些让人“耳熟能详”的惨痛事故中可以看出,每一起事故发生的致命原因,都与生产过程的本质安全有着千丝万缕的剪不断的联系。
应该说本质安全是保障化工行业这种高危险行业生产安全顺利进行的根本,现在是应该得到无比重视的时候了。
四、提高化工企业本质安全的策略
本质安全是指设备、设施或技术工艺包含在内的能够从根本上防止事故发生的功能。
通俗地讲,就是机器、设备、设施和工艺自身带来的安全。
从外形、功能等方面来讲,即使由于操作者的操作失误或不安全行为的发生,也仍能保证对操作者、设备或系统的安全而不发生事故。
要做到这一点,本质安全必须从设计抓起。
由于技术、资金和人们对客观世界认识的程度等原因,从宏观上讲,要真正做到本质安全是比较困难的,但从微观上讲,在某一点、某一台设备、某一个环节上要做到本质安全还是完全可以的,同时本质安全也应该是一个逐步提高完善的过程。
要努力提高本质安全,应从以下几方面考虑:
1、设计开始抓本质安全
化工生产过程开发是由可行性分析、工艺研究、概念设计、基础设计、工程设计等多个阶段组成的,各阶段实现本质安全的机会是不相同的。
设计、开发早期阶段过程变化的自由度大、实现本质安全的机会也就多,投资也较少。
在设计、开发阶段实现本质安全要重点考虑的方面包括:
地理位置、生产工艺、设备水平、防火防爆设施、操作环境、应急救援等。
2、工程施工抓本质安全
工程设计阶段是设计开始的实施和目的达成过程,因此设备型号、规格、零部件及材质要明细,要有设备加工制造的图纸和装配图,以及指导装置安装的详细工艺流程图,保证工程施工质量真正完成设计理念,并达到本质安全的要求。
3、加强工艺过程的安全管理
随着生产技术的进步,生产设备的质量和安全防护装置水平将不断提高和改进,系统的自动化程度和本质安全度也将随之提高,但归根结底还要由人来控制操作,要由人来设计制造、组织管理、维修维护,企业的安全生产才能够进行。
要真正维护好本质安全的成果,就必须加强制度建设,制定和完善工艺操作规程,同时提高作业人员工艺、安全技术素质,通过对工艺过程的安全管理,达到过程控制本质安全目标的实现。
五、实现化工企业本质安全化的建议措施
以上多起重特大事故充分暴露出部分化工企业工艺装置技术水平低,设备设施落后,自动化程度不高,安全设施不齐全,本质安全水平低。
这些因素仍然是引发我国化工行业事故多发、事故重大、人员伤亡惨重的重要因素,因此必须加快推进我国化工行业企业本质安全化进程。
国家安全生产监督管理总局前不久曾就化工企业安全当前的形势发文提出要求,要推动化工企业尽快提升改造,提高本质安全水平。
对采用危险工艺、没有实现自动控制的化工装置,要加快技术改造,2010年底前必须实现工艺过程的自动化控制和自动化报警。
涉及硝化、氧化、磺化、氯化、氟化等重氮化等危险工艺的化工装置,要在实现自动化控制的基础上装备紧急停车系统(ESD)。
液氯、液氨、液化石油气、液化天然气充装装置要进行压力自动控制改造,完善防泄漏措施和应急措施,提高化工装置和重要单元的本质安全水平。
要切实推动、促进化工企业本质安全化工作,还需要多方面的努力,需要多部门的共同参与与协作,还要从以下多方面采取措施:
1、完善法制法规建设,抓紧制定修订石油化工行业相关法规、标准及规程。
2、加快化工行业本质安全基础性研究,注重研究成果的转化。
3、加强危险化学品建设项目安全生产“三同时”行政许可管理,加强项目审批。
4、提高化学品生产企业准入门槛,加强安全评价和安全预评价工作。
5、建立安全生产长效机制,加大安全投入。
6、加大本质安全化宣传力度,加强化工行业企业从业人员技术教育培训,提高人员工艺技术、安全管理综合素质。
XX设计有限公司
YourNameDesignCo.,Ltd.