电镀铜薄膜的疲劳断裂研究.docx
《电镀铜薄膜的疲劳断裂研究.docx》由会员分享,可在线阅读,更多相关《电镀铜薄膜的疲劳断裂研究.docx(19页珍藏版)》请在冰点文库上搜索。
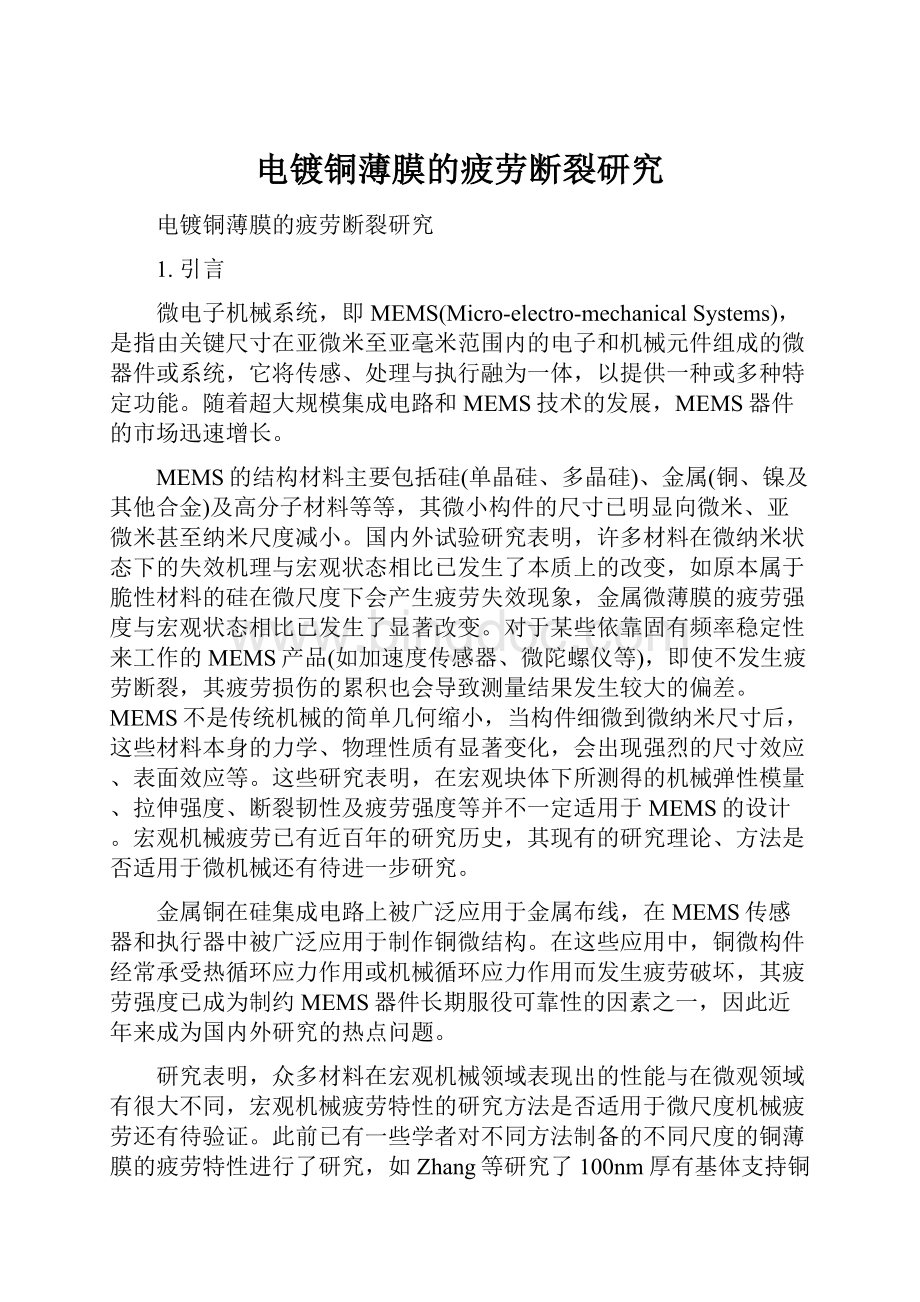
电镀铜薄膜的疲劳断裂研究
电镀铜薄膜的疲劳断裂研究
1.引言
微电子机械系统,即MEMS(Micro-electro-mechanicalSystems),是指由关键尺寸在亚微米至亚毫米范围内的电子和机械元件组成的微器件或系统,它将传感、处理与执行融为一体,以提供一种或多种特定功能。
随着超大规模集成电路和MEMS技术的发展,MEMS器件的市场迅速增长。
MEMS的结构材料主要包括硅(单晶硅、多晶硅)、金属(铜、镍及其他合金)及高分子材料等等,其微小构件的尺寸已明显向微米、亚微米甚至纳米尺度减小。
国内外试验研究表明,许多材料在微纳米状态下的失效机理与宏观状态相比已发生了本质上的改变,如原本属于脆性材料的硅在微尺度下会产生疲劳失效现象,金属微薄膜的疲劳强度与宏观状态相比已发生了显著改变。
对于某些依靠固有频率稳定性来工作的MEMS产品(如加速度传感器、微陀螺仪等),即使不发生疲劳断裂,其疲劳损伤的累积也会导致测量结果发生较大的偏差。
MEMS不是传统机械的简单几何缩小,当构件细微到微纳米尺寸后,这些材料本身的力学、物理性质有显著变化,会出现强烈的尺寸效应、表面效应等。
这些研究表明,在宏观块体下所测得的机械弹性模量、拉伸强度、断裂韧性及疲劳强度等并不一定适用于MEMS的设计。
宏观机械疲劳已有近百年的研究历史,其现有的研究理论、方法是否适用于微机械还有待进一步研究。
金属铜在硅集成电路上被广泛应用于金属布线,在MEMS传感器和执行器中被广泛应用于制作铜微结构。
在这些应用中,铜微构件经常承受热循环应力作用或机械循环应力作用而发生疲劳破坏,其疲劳强度已成为制约MEMS器件长期服役可靠性的因素之一,因此近年来成为国内外研究的热点问题。
研究表明,众多材料在宏观机械领域表现出的性能与在微观领域有很大不同,宏观机械疲劳特性的研究方法是否适用于微尺度机械疲劳还有待验证。
此前已有一些学者对不同方法制备的不同尺度的铜薄膜的疲劳特性进行了研究,如Zhang等研究了100nm厚有基体支持铜薄膜的疲劳断裂行为;Maire等测定了用等通道转角挤压法制作的铜薄膜的循环应力一应变响应;Read等开展了用电子束蒸发工艺制作的铜薄膜拉伸疲劳试验;Merchant等研究了电镀和轧制铜薄膜的弯曲疲劳特性。
但测试无基体支持的电镀铜薄膜疲劳特性参数并进行寿命预测,还需进一步研究。
2.基本原理(铜材料微构件的疲劳特性)
2.1循环形变行为及疲劳强度
Judelewicz等研究了经轧制的晶粒尺寸为100
、厚度为20~150
的铜薄膜的疲劳行为。
对于不同应力水平来说,在低应力与高应力时都呈现硬化现象;用扫描电镜和透射电镜发现,在高周疲劳时,可以观察到位错、孪晶、驻留滑移带等变形结构,在低周疲劳时,可观察到准梯形裂纹结构。
另外,其还发现晶粒的大小并不影响位错的形态,薄膜的循环形变与单晶体相似。
其又发现厚度为100
的铜薄膜的疲劳寿命比20
的疲劳寿命低10~30倍,显示出明显的疲劳尺寸效应。
Hong和Weil研究了25
厚饿电镀铜薄膜和33
厚的轧制铜薄膜的拉-拉疲劳行为,他们发现铜薄膜的疲劳强度系数高于块体材料的疲劳强度系数;此外,铜薄膜表现出循环应变硬化行为,原因在于疲劳形变在材料中引入了高的位错密度和孪晶密度。
最近,Schwaiger和Kraft等对厚度具有微米和亚微米的银薄膜和铜薄膜的疲劳行为进行了较为系统的研究,其发现随着薄膜厚度的减小,引起疲劳损伤的临界应力幅值将显著升高,薄膜表现出明显的疲劳尺寸效应。
2.2疲劳裂纹的萌生与扩展
2.2.1疲劳裂纹的萌生
Judelewicz发现厚度为100
的铜薄膜中仍然出现疲劳挤出,而厚度为20
的薄膜中的疲劳挤出只在疲劳寿命末期才出现,表明较薄薄膜中疲劳挤出损伤的出现有被推迟的趋势。
Hong和Weil发现厚度为25
铜薄膜中疲劳开裂起源于位错的胞墙或孪晶界处。
Schwaiger等人通过对银薄膜和铜薄膜疲劳损伤行为的研究表明,3.0
厚的薄膜表面仍然出现类似于块体材料的“挤出”损伤,疲劳裂纹萌生于挤出处,如图2-1所示。
图2-1不同厚度铜薄膜的微结构损伤图
随后,Zhang等利用聚焦离子束显微镜(FIB)对不同厚度铜薄膜表面的疲劳挤出进行了观察,并对疲劳挤出面积与晶体面积比进行了定量的测量,他们发现铜薄膜疲劳挤出的尺寸(即挤出宽度与高度)随薄膜厚度的减小而减小。
分析认为,疲劳挤出尺寸的减小是由于较薄薄膜中的循环应变局部化的倾向减小所致。
因此需要更高的外加应力引起疲劳破坏,从而解释了疲劳强度随薄膜厚度减小而升高的尺寸效应。
2.2.2疲劳裂纹的扩展
Shimizu等用电子散射衍射电镜观察了厚度为100
轧制回火后铜薄膜疲劳裂纹扩展情况,其发现:
如果预制裂纹与轧制方向相同,那么裂纹沿直线式扩展;如果预制裂纹垂直于轧制方向,那么裂纹扩展呈现锯齿形状。
他们还发现疲劳裂纹易在回火孪晶处产生,因为回火孪晶与立方体金属滑移带在同一平面内;薄膜轧制后的各项异性在回火后仍然存在,且回火孪晶边界大多数与轧制方向一致。
Hadrboletz等在研究厚度为20~200
的铜薄膜的疲劳裂纹扩展行为时发现,厚度小于100
的铜薄膜疲劳裂纹扩展速率随循环数的增加而减小,而厚度大于100
的铜薄膜疲劳裂纹扩展速率随循环数的增加而增加,如图2-2。
通过建立不同厚度薄膜的裂纹张开柔度与裂纹长度的关系,可以看出,随薄膜厚度减小,裂纹张开的柔度随裂纹长度的增加而减小。
经分析认为,两者的差别是由于较薄薄膜和较厚薄膜分别收到了平面应力和平面应变的作用。
图2-2铜薄膜疲劳裂纹扩展行为
2.2.3疲劳损伤的微观机制及尺寸效应
在块体金属材料中,循环形变行为及疲劳损伤机制与材料中的位错结构有着密切的关系,疲劳引起的挤出/侵入对应着驻留滑移带(PSB)的位错墙结构,而疲劳裂纹往往萌生于PSB或者是PSB撞击的晶界处。
由于薄膜材料的厚度均在微米至亚微米范围,材料中的位错行为将仍然对疲劳行为起重要作用。
Hofbeck等认为,所观察到的细铜丝中缺少疲劳挤出特征是由于滑移的位错受到表面像力的作用和相互湮灭的影响。
Judelewicz等发现,较薄薄膜不容易萌生裂纹是由于其几乎没有疲劳“挤出”损伤和因较短位错滑移距离及像力的作用导致位错数量的减少。
在上述这些研究中,晶粒尺寸均在几十个微米。
Hong和Weil认为,在晶粒尺寸大于2
的铜薄膜中,循环应变硬化来源于位错缠结和位错胞墙结构的形成。
Read研究了电子束蒸发的晶粒尺寸为0.98
,厚度为1.1
铜薄膜的疲劳行为,发现薄膜表面没有疲劳台阶和位错胞结构。
这些前期工作初步表明,材料疲劳行为的尺寸效应不仅与材料外部几何尺寸有关,也与内部组织结构尺寸,如晶粒大小有关,但没有系统地针对不同厚度的薄膜及各种尺寸的晶粒进行位错结构研究。
最近,Zhang等对经疲劳变形的厚度为3.0~0.4
的铜薄膜进行了较为系统的电镜观察。
他们发现,只有薄膜厚度或晶粒尺寸都大于3.0
时,才会出现像块体材料中的典型位错胞、墙。
而随着薄膜厚度或晶粒尺寸的减小,位错结构变成松散的缠结组态;当薄膜厚度或晶粒尺寸小于1.0
时,只有单根位错存在。
他们还观察到,在厚度为3.0
的薄膜中疲劳挤出处有位错墙结构,而较薄薄膜中的疲劳挤出处只有单根位错存在,说明疲劳损伤和材料内部的位错行为有关。
这些位错结构的观察结果清楚地表明了无论是材料的几何尺度或是微观结构尺度都控制了疲劳位错结构的形成。
由于薄膜中的位错可动性降低,同时较薄薄膜内的位错源相对较少,从而导致了位错不能够像块体材料那样进行充分的交互作用,如位错偶极子的相互捕获,湮灭等,故位错结构的形成受到了抑制。
可见,“材料尺度越小,疲劳强度越高”的疲劳尺寸效应,是由于材料尺度对位错结构形成的强烈约束,导致材料只有靠少量单根位错的运动来累积循环塑性应变,从而导致疲劳形变局部化的损伤行为受到抑制。
3.铜薄膜缺口件疲劳的研究现状
目前关于缺口件电镀铜薄膜疲劳研究的文献仍很少,此前学者主要对光滑件铜薄膜作出了一些研究,一部分为关于铜薄膜的常规机械性能,例如屈服强度、抗拉强度、塑性指数的研究;一部分为光滑件电镀铜薄膜的疲劳性能及影响因素,例如轧制铜薄膜与电镀铜薄膜的疲劳性能,不同晶粒尺寸铜薄膜疲劳性能,铜薄膜低周疲劳性能与高周疲劳性能等。
但对于缺口件电镀铜薄膜的疲劳性能及其影响因素方面鲜有研究。
因此,研究铜薄膜缺口件的疲劳断裂特性及其影响因素对提高MEMS器件的可靠性具有重要的理论和实际意义。
4.电镀铜薄膜疲劳的研究内容及科学问题
(1)查阅文献,结合国内外相关研究成果和经验,在现有的条件下设计出合理的电镀铜薄膜疲劳试样。
(2)设计、绘制以及加工制造出电镀铜薄膜光刻掩膜板,并利用准LIGA技术制作电镀铜薄膜。
(3)利用微机械疲劳试验机对电镀铜薄膜进行疲劳加载试验,并在试验过程中进行疲劳试验现象观察,且用扫描电镜对断裂面进行观察和分析。
(4)建立有限元模型,对缺口件电镀铜薄膜进行塑性有限元分析。
(5)利用试验结果以及有限元计算数据对电镀铜薄膜的寿命进行预测。
5.电镀铜薄膜疲劳研究的试验方法
5.1基于准LIGA技术的电镀铜薄膜试件制作
LIGA工艺(光刻、电铸、注塑)是微机械加工中最重要的工艺之一,在微机械特别是高深宽比微构造的制作上占有很重要的地位。
LIGA技术具有许多优点,如加工精细(最小横向尺寸可达1
),精密度高(误差小于0.2
),可获得很大的深度比(深度/宽度>50),结构高度最大可达500
可制作任意形状的二维平面结构等等。
但其掩模版制作困难,需要用高能量X射线源—同步回旋加速器,这一昂贵的设施和复杂的掩膜制造工艺限制了它的广泛应用。
准LIGA工艺过程除了所用光刻光源和掩膜外,与LIGA工艺基本相同。
准LIGA技术可满足微系统对加工精度、集成度以及成本的要求,丰富并充实了MEMS技术,当对微结构侧壁的垂直度要求不是很高时,它可取代LIGA技术。
以前采用表面微机械加工技术制作的微结构,也大多可用准LIGA技术制作而成。
5.1.1准LIGA技术介绍
准LIGA技术是利用常规光刻机上的深紫外光对厚胶或光敏聚酰亚胺光刻,形成电铸模,结合电镀、化学镀或牺牲层技术,由此获得固定的或可转动的金属微结构。
准LIGA技术典型的光刻工艺流程为:
涂胶和前烘→曝光→显影和坚膜→服饰→去胶。
涂胶是在光刻硅片表面敷上一层光刻胶膜,其要求是粘附良好、均匀、厚薄适当。
前烘的目的是使胶膜体内溶剂充分地挥发,使胶膜干燥,以增加胶膜与结构层的粘附性和胶膜的耐磨性;同时,只有光刻胶干燥,曝光时才能充分进行光化学反应。
曝光是指采用尽量平行的光束垂直照射到硅片上,使胶膜没被掩膜版挡住的部分在光线的照射下发生光化学反应。
显影是把曝光后的基片放在显影液里,将应除去的光刻胶膜溶剂干净,以获得所需要的抗蚀剂的图形。
坚膜就是在一定的温度下,将显影后的片子进行烘烤,除去显影时胶膜所吸收的显影液和残留水分,改善胶膜与基片间的粘附性,增加胶膜的抗蚀能力,以及消除显影时所引起的图形变形。
腐蚀就是用适当的腐蚀剂,对未被胶膜覆盖的结构层进行腐蚀,按照光刻胶上已显出来的图形,完整、清晰、准确地腐蚀,供选择性扩散或达到金属布线的目的。
去胶就是在结构层的图形做出来后,把起保护作用的胶除净。
在硅片上刻出所需试件图形后,将硅片置入电镀液中,并与纯铜板连接成电流回路,此时通入适当的电流,并搅拌电镀液,硅片上刻蚀出的图形部分将逐渐淀积纯铜。
5.1.2铜薄膜试件制作工艺流程
试验用铜薄膜试件制作的工艺流程为:
1.采用标准RCA工艺清洗硅片,去除硅片表面杂质及损伤;
2.在单管氧化炉中将硅片表面进行氧化,生成约0.5nm厚的氧化层,生成SiO2绝缘层;
3.在氧化层上旋涂聚酰亚胺,在150℃下烘烤五分钟,形成牺牲层;
4.在聚酰亚胺层上分别溅射Cu种子层,为电镀做准备,使Cu生长在种子层;然后继续在Cu种子层上溅射Cr层,是为了防止显影液溶解Cu种子层;
5.进行甩光刻胶,110℃烘烤1分钟,为光刻做准备;随后曝光、显影、110℃固胶5分钟,将掩膜板上的图形转移到光刻胶上,形成一个凹槽;
6.用刻铬盐酸甘油去掉铬层,露出种子层;然后进行电镀,设置电流大小,控制电镀试件,并不停搅拌,使Cu在种子层上按照图形均匀生长;最后溶解牺牲层聚酰亚胺释放出铜薄膜试件,得到无基本支持的铜薄膜试件。
需要注意的是,制作出试件后,应尽快开展疲劳试验,否则铜薄膜表面将会很容易被空气氧化,影响实验结果。
5.2MEMS疲劳试验方法
微机械疲劳试验由于其试件尺度很小,因此在试件制作、试验夹持及测量精度等方面增加了试验难度。
综合国内外的研究成果,可以将MEMS疲劳试验方法总结如表5-1:
表5-1MEMS疲劳试验方法
分类
片上测试
片外测试
原理
静电谐振
电磁驱动
压电激励
超声激励
适用材料
硅
硅、金属、高分子
特点
利用MEMS工艺制造集驱动、检测为一体的性能测试系统,直接在芯片上进行测试,能实现对MEMS器件机械性能的在线检测,无需装卡、对中,加载频率高,但试件制作工艺复杂、成本高
利用MEMS工艺制造试件,制造工艺相对简单,加载方式稳定可靠,试验中的各种参量易于记录,但需要复杂的驱动、检测试验系统,且试件装卡、对中难度较大。
5.2.1静电谐振法
谐振疲劳试验装置是利用对试样施加与其固有频率相当的周期性驱动力,使结构发生共振而产生周期性的应力与应变,以达到疲劳试验的效果。
试验加载方式与MEMS构件的实际受力环境较为接近,因此试验结果更接近真实情况。
基于梳状驱动器的谐振疲劳试验装置采用静电驱动原理,其中最主要的部件就是如梳齿一样相互交错的静电力驱动器,在梳齿的两边施加一固定频率的交流电压,从而产生交变静电力,驱动结构发生振动,造成对试样的循环加载。
图5-1基于梳状驱动器的谐振疲劳试验装置
基于梳状驱动器静电力驱动的硅微薄膜谐振疲劳试验装置如5-1左图所示,其中A、C为两组相互交错的梳齿,A为驱动器,C为电容式位移传感器,B为共振块,D为试样,右图为试样的放大图。
试样中的缺口是为了引入应力集中系数,增大试验的应力水平。
驱动器A靠近外沿的梳齿接正弦电压,与振动块B相连的梳齿接地,这样便会使两者之间产生周期性的静电力,从而导致悬置的振动块B发生共振而带动试样D作往复运动,试样除了受循环变化的弯曲力和剪切力外还受到循环变化的离心力,该离心力是由于振动块在振动过程中角速度的变化而导致的。
位移传感器C靠近外沿的梳齿接恒定电压,共振块的振动将会造成梳齿间电容的变化,根据电容的变化便能够测得共振块的振动幅度。
试样所受的应力可以根据振动块的振动幅度由有限元分析算出。
5.2.2
电磁驱动法
电磁驱动是一种较为理想的驱动方式,它具有很好的线性、低滞后性、无摩擦,能直接进行精确控制等特点;运动的磁铁或线圈相对于结构具有很小的惯性,在磁力作用下能实现沿轴向自动对中,从而消除横向力,同时也能降低振动。
在得到电磁力与电流的线性关系后,可通过施加交变电流以控制载荷的大小,从而克服微拉伸装置中微小力的测量困难,其原理图如图5-2。
Ando等人采用的装置如图5-3(a)所示,主要由载荷传感器、真空台、试样芯片、顶针及位移传感器组成。
试样芯片如图5-3(b)所示,包含外框架、加载梁、扭转块和试样四个部分,其中试样的放大图如图5-3(c)所示。
图5-3Ando采用的疲劳拉伸装置
试验过程中对顶针加载点进行位移和力的跟踪测量,再利用平衡原理可求得试样所受的应力和应变。
采用控制应变方式,加载频率为10Hz,载荷比为0.1,在不同的应变水平下对不同晶向的单晶硅进行了疲劳试验。
5.2.3压电激励法
目前,适用压电式激励器作为驱动方式的较多,主要用计算机编程控制压电单元释放位移,从而带动夹头提供驱动力,但压电单元中存在蠕变、滞后和非线性等问题,至今未能很好解决。
Allameh采用的拉伸疲劳试验装置见图5-4,主要由压电驱动器、载荷传感器、试样、旋转/平移台和摄像机组成。
试验中通过对压电驱动器施加固定频率的交流电压,由于压电效应,便可对试样产生循环变化的拉伸力以达到疲劳试验的效果。
试验所采用的载荷比为R=0.1,加载频率为10Hz。
图5-4Allamaeh采用的拉伸疲劳试验装置图
5.2.4超声激励法
超声激励是利用超声波振动,使滑块产生往复位移,从而对试件产生循环拉压作用。
Cho采用的拉伸疲劳试验装置由超声波驱动,主要由扬声器、直线滑块、试样、夹具和力传感器组成。
试验通过扬声器发出一定频率的声波,导致滑动块的振动从而形成对试样的循环加载,加载频率为200Hz,载荷比为0.1。
与压电驱动器相比,这种方法能够获得更高的振动频率。
图5-5Cho采用的拉伸疲劳试验装置
5.2.5纳米压痕法
目前对材料在纳米尺度下疲劳特性的研究相对较少,采用的方法主要是纳米压痕法,该方法的基本原理如图5-6所示。
纳米压头对固定梁的中点施加循环载荷
(其中
为平均压力,
为压力幅),因为疲劳损伤的累积会导致试样刚度的下降,因此在试验过程中通过对接触刚度的连续观测可以得知试件的疲劳损伤情况,从而能够间接对纳米梁的疲劳特性进行研究。
图5-6纳米压痕法原理图
5.3疲劳寿命预测方法
目前对于宏观疲劳寿命研究已经有较为成熟的研究方法,如名义应力法,局部应力应变法等,但对于微机械疲劳寿命研究,其研究并不多见。
5.3.1名义应力法
前人已对名义应立法进行了大量的研究,积累了许多宝贵的资料和经验。
在应力水平较低,载荷比较稳定的情况下,名义应力法仍是目前工程中广为应用的一种寿命估算方法。
其根据S-N曲线,应用线性疲劳累积损伤理论(Miner定律)进行寿命估算。
此方法以外部名义应力作为损伤控制参量。
其寿命预测步骤为:
(1)求名义应力谱;
(2)计算结构缺口的应力集中系数和其他影响因素的系数;
(3)利用S-N曲线应用插值方法确定所求的应力集中系数和应力水平下破坏寿命值。
该方法优点是:
构件的名义应力很容易根据外载计算或者实际测量得到。
但这种方法也有很大的不足之处:
疲劳破坏总是从结构上具有应力集中的部位开始,但是名义应力不能够代表应力集中部位的真实的应力-应变状况,也不能正确的考虑应力次序和各级载荷之间的相互作用,因此它不能反映出疲劳破坏的本质。
5.3.2局部应力应变法
局部应力应变法是目前预测疲劳寿命的一种主要方法,这种方法综合了五十年代以来疲劳强度研究中各方面成果,特别是材料循环特性的研究,采用了现代的试验方法和分析技术,建立了一套估算裂纹形成寿命的方法,得到了广泛的应用。
其基本思想是,认为零件和构件的整体疲劳性能取决于最危险区域的局部应力-应变状态。
局部应力-应变法认为循环塑性变形是造成疲劳损伤的根本原因。
其与名义应力法相比,在描述材料的疲劳性能时,用
关系代替了
曲线,用循环的
代替了单调的
曲线;采用弹塑性有限元分析或试验力学分析方法求解局部屈服状态下的应力-应变。
其估算疲劳形成裂纹形成寿命的具体步骤如下:
(1)首先确定材料的疲劳性能参数(
)和缺口几何参数(
或
);
(2)根据名义应力、应变和局部应力、应变转换关系求解缺口根部的局部应力、应变;
(3)根据选定的损伤寿命公式进行损伤计算及寿命预测。
上述局部应力应变法中的每一个主要步骤,在具体应用时都有多种处理方法,由于采用的方法不同,寿命计算结果可能也会不一样。
5.3.2.1缺口处局部应力和应变的确定
目前,在局部应力应变法中,一般采用以下几种方法来确定局部应力-应变关系:
(1)采用试验方法确定缺口根部的局部应力-应变值。
确定缺口局部应力-应变的试验分析方法有很多,如电测法、云纹法、光弹法、散斑法等。
工程上使用较多的是电测法和云纹法。
试验方法直观准确,但试验繁琐,往往由于实际条件的限制,不便于采用此种方法。
(2)用近似计算法确定局部应力-应变值。
工程上可采用简单实用的近似计算方法,如Molski等效能量法、诺伯法和修正诺伯法等。
该方法的缺点是计算出的应力应变数据不够精确。
(3)采用弹塑性有限元法计算局部应力-应变值。
目前计算机运算功能十分强大,在处理实际问题时极大地方便了研究工作者开展研究。
目前较为通用的有限元软件有ANSYS等,有限元法模拟的精度很高。
5.3.2.2损伤计算及寿命预测
目前,在局部应力应变法寿命估算中许多损伤公式都是以Manson-Coffin公式为理论演化的,其中应用较广的损伤公式有:
(1)Dowling损伤公式
Dowling等人认为以转换寿命(
曲线中弹性线与塑性线的交点)
为界。
当
时塑性应变分量占优势,平均应力影响可以忽略不计。
塑性应变幅值
循环一周造成的损伤为:
(5-1)
当
时弹性应变量占优势,弹性应变幅值
循环一周造成的损伤为:
(5-2)
考虑平均应力影响时,
(5-3)
(2)Landgraf损伤公式
Landgraf选择塑性应变幅值与弹性应变幅值之比作为计算损伤的参数:
(5-4)
(3)Smith-Watson(SWT)损伤公式
Smith等人选择
作为损伤计算的参数,由于最大应力
在对称循环中等于应力幅
,所以,
。
结合Manson-Coffin公式,得到:
(5-5)
5.4铜薄膜缺口件有限元分析
传统的设计分析方法已经不能满足设计的需求,因而工程设计中出现了有限单元分析法。
有限元的核心思想是结构的离散化,就是将实际结构离散为有限个单元通过有限个节点按一定次序连接在一起并在一定边界条件下求解的集合体。
有限元不仅计算精度高,而且能适应各种复杂形状。
通过有限元分析,可发现设计阶段潜在的问题,增加可靠性;可模拟试验方案,减少试验次数,从而减少试验经费;降低原材料成本;缩短产品投向市场的时间。
随着计算机技术的普及和计算速度的不断提高,有限元分析在工程设计和分析中得到了越来越广泛的重视,已经成为解决复杂工程分析问题的有效途径。
5.4.1有限元数值分析基本假设
材料非线性分析与线形分析相比,最明显的不同体现在材料属性的定义上。
在材料非线性问题的建模过程中,定义材料属性时必须将非线性这一特性恰当地表示出来。
在ANSYS程序里面,提供了多种塑性材料选项,在此主要介绍四种最常用的材料选项,可以通过激活一个数据表来选择这些选项。
经典双线性随动强化(BKIN):
使用一个双线性来表示应力应变曲线,有两个斜率,分别是弹性斜率和塑性斜率,由于随动强化的VonMises屈服准则被使用,所以包含有包辛格效应,此选项适用于初始为各向同性材料的小应变问题(如大多数金属)。
双线性等向强化(BISO):
使用双线性来表示应力-应变曲线,适用于初始各向同性材料的大变形问题。
多线性随动强化(MKIN):
使用多线性来表示应力-应变曲线,模拟随动强化效应,此选项使用VonMises屈服准则。
多线性等向强化(MISO):
使用多线性来表示应力-应变曲线,它适用于比例加载的情况和大应变分析。
在实际分析中,应根据试验的实际情况,选择最适合的模型,选择适当的参数和条件,根据公式计算以及相关理论和知识得到结果。
5.4.2有限元网格划分
有限元分析过程中,模型的建立与网格的划分是非常重要的。
它直接影响计算结果的正确与否和精确程度。
有限元模型,边界条件及加载过程都尽量逼近实际的试验情况,这样计算结果将更为准确。
由于试件厚度方向尺寸很小,试样受力情况为平面应力状态,建模时选取平面