卡车和客车内外饰工艺简述Word文档下载推荐.docx
《卡车和客车内外饰工艺简述Word文档下载推荐.docx》由会员分享,可在线阅读,更多相关《卡车和客车内外饰工艺简述Word文档下载推荐.docx(32页珍藏版)》请在冰点文库上搜索。
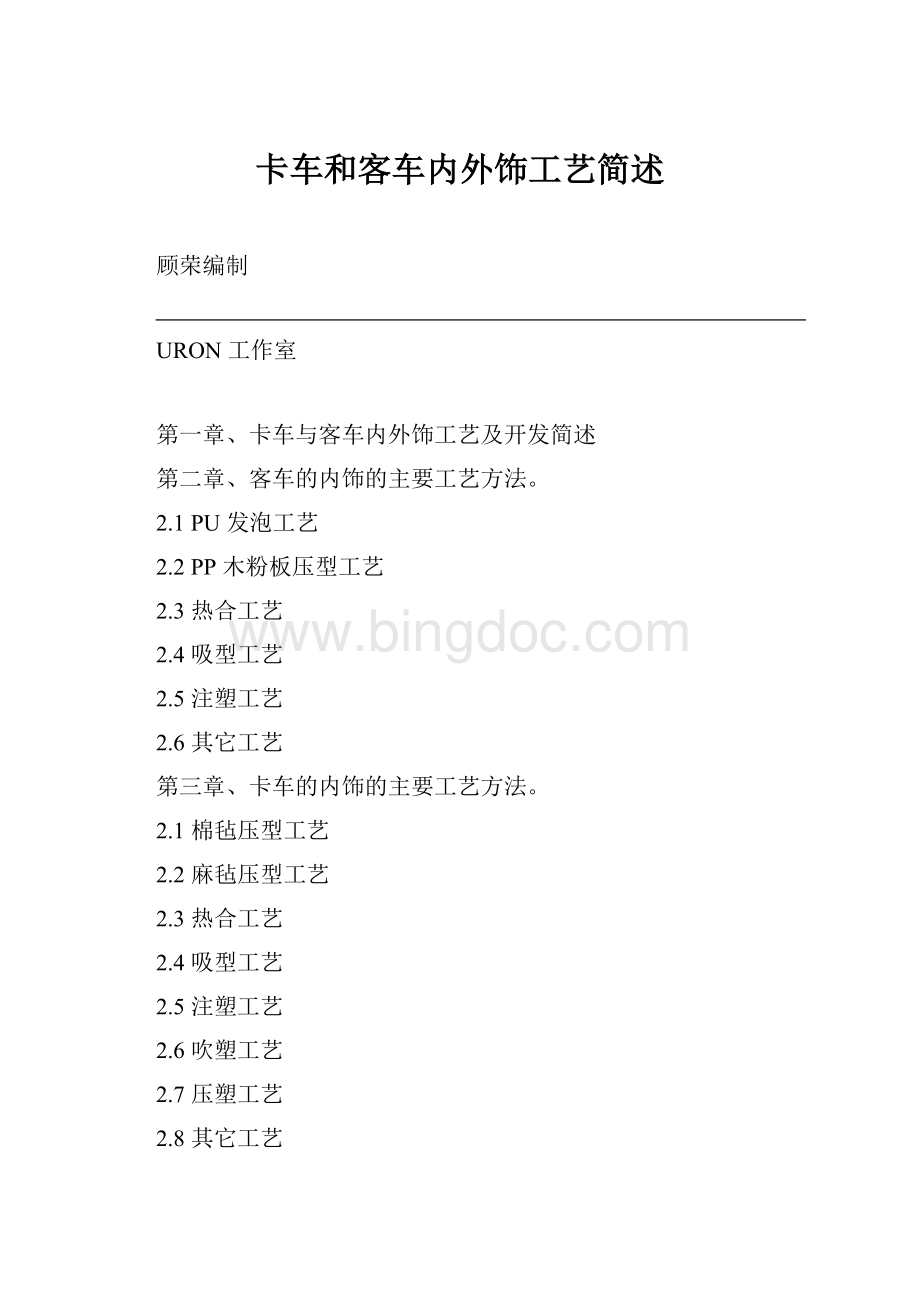
在目前的汽车内饰中已明确要求
阻燃的要求,这也是汽车安全性能的一个组成部分。
2、结构功能。
汽车的外饰
已成为汽车的一个结构组成部分。
同时内外饰件也是多种汽车功能件的载体。
3、装饰功能。
汽车内外饰件不仅要求有实用功能,还要具有极强的观赏性。
汽
车的外饰体现了汽车的风格,是硬朗的,还是秀气的,是雍容的,还雅致的。
外饰能够给人一个鲜明的印象。
无论内饰外饰,都比较重视色彩、纹理、线条、
质感。
汽车内外饰是汽车被人能够目视的能达到装饰件的所有部件的统称,本文
涉及的内饰部件主要包括:
仪表台、顶棚内衬、侧围内衬、车门内衬、地垫、
外饰包括保险杠、车顶盖、车厢仓门。
工艺特点,客车内饰在
90
年代以前还是
以普通材料直接装饰的形式制作,包括纤维板加压条,钣金件糊革,塑料板。
以后逐步形成以模具制造为主的多工艺生产特点,包括仪表台的聚氨酯硬泡、
半硬泡工艺,热固性或热塑性材料热压成型工艺,吸塑工艺,注塑工艺,玻璃
钢糊制工艺等,外饰一般以钢板钣金制作,以后又有玻璃钢糊制工艺。
卡车的
内饰由于批量原因,平台较客车高,即使较大的客车制造厂家,其生产批量也
达不到卡车一般车型的批量。
因而卡车的内外饰生产工艺更多倾向于向轿车的
工艺靠拢,卡车内外饰更有机会使用先进的生产工艺,比如注塑、冲压、
SMC、GMT
等,并要求更高要求的工艺装备和生产设备,以达到足够的生产能
力。
-2-
第三章、客车内饰主要工艺方法
聚氨酯发泡仪表台工艺
聚氨酯(polyurethane
简称
PU)发泡,一般是由多异氰酸酯与多元醇化合
物相互作用而成,具有可发泡性、弹性、耐磨性、粘结性、耐高低温性、耐溶
剂性、耐生物老化性等优良性能,聚氨酯工艺近年来发展迅速,有多种改良或
添加辅剂的科研成果。
对制品性能、环保等方面作了改进。
聚氨酯发泡仪表台是将仪表台在结构上分为三层,即骨架层,表面层和聚
氨酯层。
最里层是骨架层,可使用玻璃钢(FRP),成形钢板或其它成形材料,
它的主要是起结构功能,需要具用一定的强度,并能够装配。
最外层是表面层,
一般是
ABS/PVC
表皮。
表皮在发泡前也要热成空成形。
最后形成中间的
发
泡层,PU
发泡可能过人工搅料或机械混合注料方式将两种组分的材料混合发泡。
并在发泡模具(阴阳)内成型。
一、主要工艺流程(以玻璃钢骨架为例)
骨架制作
表皮成型
发泡
修皮
锯切
装配
二、工序说明(以玻璃钢骨架为例)
一)骨架糊制
1、清理模具,使模具表面洁净,
2、检查模具有无变形、破损,模具编号是否与作业指导书相符。
3、在检查合格的模具上涂脱模剂(用量为
40g/㎡),然后在
25℃室温下固化
10
分钟。
4、树脂配料:
1)取树脂倒入配料桶
2)取固化剂倒入配料桶,
3)取促进剂倒入配料桶,边倒边搅拌,搅拌须充分、均匀
5、用漆刷在骨架模上涂第一层树脂后糊上一层厚度为
0.2mm
的玻璃纤维布
6、刷第二层树脂,糊上一层厚度为
0.4mm
的玻璃纤维布。
7、刷第三层树脂,糊上一层厚度为
8、在仪表板所需要部位放上相应的嵌体,用厚度为
的玻璃纤维布加树脂
加强。
9、在加强部位用厚度为
玻纤布及树脂加厚二层
10、糊第四层厚度为
的玻璃纤维布,最后用树脂刷平外表面。
11、90
分钟固化后,骨架出模,放置于工件架上,室温为
25℃时后熟时间为
24hr
上述操作的技术规范
1、骨架厚度控制在
3~4mm
2、要求模具表面不允许有灰尘、杂物等
3、树脂配比:
A
当室温
20~30℃时:
树脂:
固化剂:
促进剂=100:
4:
2
B
当室温为
0~20℃时:
4
C
当室温≤0℃时促进剂配比加大,当室温≥20℃时促进剂配比
减小,先进行小样调配
-3-
4、先倒树脂再倒固化剂,最后倒促进剂并且边倒边搅拌,搅拌均匀充分
5、骨架表面要光滑
6、预埋嵌件无毛刺、锈蚀、油污,定位准确,部分件需镀锌打孔处理,孔径
φ8
以上
7、骨架不起泡,玻纤布糊透不起翘
二)
骨架锯切
1、前弧及周边锯切:
沿前弧及周轮廓线进行锯切
2、其它修边锯切:
按模具所带修边线锯切
3、仪表面罩检修门等开孔锯切:
1)划线:
将样板放置在开孔位置,用铅笔沿划线样板或修切线
2)用手枪钻在划线一角钻孔
3)将曲线锯锯头伸进孔内
4)启动曲线锯开关沿线锯切
4、打磨:
用磨光机将骨架表面磨光
5、送检
1、边线锯切准确,嵌件无滑落
2、周边光滑、圆顺、无切痕及破损等弊病
3、外表面无树脂瘤块,无毛刺
三)
1、成型第一个件时检查凸模真空眼及模具表面质量
2、点按成型机“平台上升”按钮使工作台上升到上止点
3、将成型模具固定于工作台上清洁模具表面
4、点按“平台下降”按钮,使工作台下降至下死点
5、检查表皮质量、型号及规格
6、将表皮用钳子夹紧在表皮压框之间(花纹面朝上)
7、将加热板拉至表皮上部开始对表皮进行加热(加热箱内部
240±
10℃)注意
表皮在加热过程中,如出现裂纹、分层、起泡等现象,应立即停止加热并换
表皮重新加热。
8、1.5
分钟后拉开加热板
9、点按“平台上升”按钮
10、点按“真空泵启动”按钮,抽真空成型
11、在加强部位用厚度为
玻璃纤维
12、用外包海绵的条状物抵住主体
,部分拐角处辅助成型,防止出现皱折
13、点按“吹气”按钮降温(30
秒左右)
14、2
分钟后点按“真空泵停止”
按钮
15、用美工刀划离成型表皮,从真空成型模上取下
16、将表皮套在表皮定形骨架上
1、表皮应保持清洁,不允许有任何水滴杂物、油污等弊病
2、实用区域表皮无拉破和起皱现象
3、表面拉伸处无明显拉薄和可视发白现象。
4、成型表皮表面不能有针孔眼,凸凹点
5、真空泵真空度≥0.08MPa
-4-
6、空压机压力≥0.5MPa
四)
发
泡
1、打开发泡成型模具
2、清理凹模:
用干净抹布将模腔擦拭干净
3、检查滑块是否是有缺损现象,并将滑块放入模腔相应位置
4、检查表皮是否达到质量要求
5、发泡第一个件时用通针穿透凹模排气孔
6、将成型表皮放置于凹模内
7、真空吸气定型表皮
8、用漆刷沿骨架模模具表面来回刷脱模剂,保证表面涂刷均匀,脱模剂不得堆
积、流挂(60g/㎡)
9、将薄膜覆盖在凸模表面
10、将玻璃钢骨架放入凸模上,不能有起翘或不贴合等现象
11、配料:
1)、用大药勺取组合聚醚
2)、用另一药勺取异氰酸酯
3)、将量取好的组合聚醚和异氰酸酯倒入搅拌桶中,开动搅拌机
进行搅拌(10~15
秒)
12、浇注:
将搅拌好的混合料沿凹模表皮内边匀速浇注
13、将凸模与凹模合模并锁紧
14、计时:
室温
25℃时
15~25
分钟,室温低于
15℃时时间加长,室温高于
25℃时时间缩短
15、出模并检查发泡件外观
16、将合格发泡件置于台架上熟化
24
小时
1、发泡前凸模、凹模需保证清洁
2、工艺跑料部位发泡前一定要涂脱模剂
3、填充料的配比需符合
10:
6
室温>
30℃或<
18℃应降温或加温,如需加强增硬,
需加
2%增硬剂
4、在温度在
8℃以下,为保证质量模具,加温表皮成型后不超过
12
小时发泡
5、真空要求不少于
0.080MPa
6、发泡台架制作的产品在制作前应检台架机构是否灵活
7、配料时搅拌要均匀
8、发泡件表面光滑、无凹坑、缩瘪、皱折、漏料等影响外观的现象。
9、成型仪表台表面层无明显空料、气泡,发泡不完全等缺陷
五)
小件发泡
用干净抹布、漆刷将模腔擦拭干净
4、检查表皮及骨架是否达到质量要求,必要时须用铁锤整理铁骨架,使它与骨
架模贴合
5、将成型表皮放置于凹模内
6、配料(可进行多模配制):
1)、用料罐称取组合聚醚
2)、用另一料罐称取异氰酸酯
-5-
3)、将量取好的组合聚醚和异氰酸酯倒入搅拌桶中,搅拌
20~25
秒。
7、浇注:
8、将骨架(镀锌板等)放入凹模内不能有起翘或不贴合等现象
9、将薄膜覆盖在玻璃钢骨架内表面
10、将凸模放入凹模内,及时拧紧两侧锁紧螺丝(或压上压脚)
11、计时:
15℃时,时间加长,室温高于
30℃时,时间缩短
12、出模并检查发泡件外观。
13、将合格发泡件置于台架上熟化
16
小时以上。
10:
(5.8—6.0)
4、配料时搅拌要均匀
5、发泡件表面光滑、无凹坑、缩瘪、皱折、漏料等影响外观的现象。
六)修皮
1、清理工作台,不允许工作台有任何坚硬、锐利工具或杂物,以防拉毛或刮伤
仪表台表皮
2、从料架上取下仪表板发泡件放置在修皮工作台上,检查表面质量
3、修整前弧及周边,用美工刀沿前弧及周边将表皮修理掉
4、用铲刀铲去因发泡产生的多余溢料(发泡料)
5、对仪表罩及开关孔处按靠模进行划线
6、根据划线及表皮上所带刻线修检修门孔,仪表罩开孔,开关孔,碟盒孔及其
它开孔。
7、美工刀修齐边沿,对骨架内用铲刀去除泡沫料
8、送
检
9、将合格品放置在货架上
1、切口必须光滑、平整、无刀痕、折角及有损表皮美观的弊病
2、为保证下道开孔工序的尺寸,需严格按照样板尺寸进行修皮处理
七)
开
孔
1、将仪表台放置在工作台上
2、检查仪表台有无损坏
3、沿修皮线用电锯进行锯切处理,如需要开风球装配孔:
将扩孔器钻头垂直对
准仪表台上预留孔位后开启扩孔器开关,直至钻空
4、用锉刀对所有锯切孔进行修理直至切口光滑、平整。
并用样板塞规等检查开
孔尺寸
5、清洁处理:
用干净抹布将锯切时残留在仪表台表面的灰尘擦拭干净
6、送检
7、将合格品送总装车间
1、开孔时沿修皮尺寸进行开孔,不可超出修皮尺寸
2、切口光滑、无切痕及破损等弊病
八)
装
配
-6-
1、塑料拉手检修门装配:
1)将拉手定位靠板放在拉手沉坑内,按靠板预留孔在检修门上打孔,然后取出
靠板,将拉手放入沉坑并用螺母将其与检修门固定
2)划线:
按检修门装配要求在检修门背面划线,确定插销及碰珠装配位置(注
塑门按预留孔)
3)按划线打眼攻丝,将插销和碰珠固定于检修门背面
2、金龙锁扣检修门装配
1)将锁扣放入门件预留沉坑内,然后在背面用螺丝固定。
按检修门装配要求在检修门背面划线确定插销装配位置
3)按划线打眼攻丝,将插销固定于检修门背面
1、装配过程中保持工作台面的清洁、无任何与装配无关的尖锐杂物
2、钻孔时手枪钻须与表面垂直
3、无靠模(靠板)的定位须严格按照图纸尺寸要求进行划线后再行钻孔
4、用螺钉紧固时不可出现螺钉歪斜现象,螺钉需与丝锥孔松紧自如
5、操作过程中不可有划伤表皮的现象
九)
总
装
1、将仪表台主体放置在总装工作台上
2、碰珠型检修门与主体装配:
1)将检修门插销插入主体
2)翻转仪表板,使其倒置于工作台
3)根据碰珠位置划线确定碰珠固定座位置
4)将碰珠固定座用螺钉固定于主体背面
5)将检修门碰珠与固定座锁紧
3、锁扣型检修门与主体装配:
2)翻转仪表台,使其倒置于工作台上。
3)将锁扣螺丝调整至上极限,关闭锁扣,根据锁扣螺丝与主体间隙予以调整。
4)将仪表台重新正放在工作台上,打开锁扣旋紧罗母,再用
502
胶水粘死固定
螺丝。
4、在加强部位用厚度为
5、固定脚与主体装配:
1)将仪表台倒置于主体固定架上
2)取固定脚靠模置于仪表台底部并与其贴合,用大力钳夹紧
3)根据靠模上预留孔划线确定固定脚安装中心位置(划线标记)
4)根据划线位置将固定脚分别与主体连接,注意为保证固定脚的上下位置,在
连接时应用直角定位件保证固定脚下平面与仪表
5)对孔进行攻丝处理
6)将仪表面罩放入主体沉坑内
7)用螺钉将面罩连接在主体上
8)如加子母扣,应内加垫圈,在螺钉头部加盖帽。
(或从反面上螺母装接于主
体上)
6、仪表及碟机等支架装配
1)仪表台倒置于总装工作台上
-7-
2)把支架放置于仪表台的准确位置上,用铅笔按支架的装配孔在主体上做好标
识,标识位置应在嵌件
3)取下支架,用手枪钻在标识处打孔,不能打穿使外部表皮破坏
4)对打好的孔进行攻丝
5)用螺栓把支架装配在主体上。
注:
仪表和碟机支架的位置可通过工装等确定。
7、装饰条粘接:
1)将仪表台放置于总装工作台上
2)把装饰条放置于主体沉坑内确认间隙均匀表面平整
3)用
胶涂在装饰条反面边沿
4)将装饰条粘在主体上
5)用
AB
胶在装饰条边沿加固
2、装配件的焊接严禁少焊、漏焊、焊接不牢等现象。
表面无毛刺、锈斑、渍点、
尖角。
各钻孔孔距符合装配要求,各工件具体参照自制图纸或实物样件。
并
进行镀锌,喷涂等防腐处理
3、用到靠模(靠板)的须保证靠模与主体吻合
4、无靠模(靠板)的定位须严格按照图纸尺寸要求进行划线后再行钻孔
5、用螺钉紧固时不可出现螺钉歪斜现象,螺钉需与丝锥孔松紧自如
6、操作过程中不可有划伤、拉毛、刺破表皮、周边翘皮、卷边等现象。
7、仪表台的门件、塑料件等的装配,要求牢靠,无明显扭曲,缝隙匀称,门件
开启自如。
8、仪表台的内部各零件严格按工艺要求进行装配,不得有漏装、错装、少装、
装接不牢靠等现象。
9、仪表台的标准件必须拧紧到位,严禁有假装、斜螺钉等现象存在。
10、主体与下挂连接固定角,固定角应低主体装接边
1-2㎜
11、主体装接边玻璃钢骨架与发泡体不能有分层现象
十)清
洗
1、将清洗工作台清理干净,要求无任何杂物
2、将总装好的仪表台放置在工作台上
3、用水桶取水
4、向水桶内加入少许清洁剂
5、取干净抹布一块放入水桶搅拌
6、用带有清洁剂的抹布在仪表台表面来回擦拭,去除油污、斑点等影响外观的
污点
7、翻转仪表台
8、对仪表台背面进行清理
9、换水和清洁剂重新擦拭一遍
10、送检
1、清洗要全面,不可出现局部漏洗
2、不可用酸、碱等腐饰性洗液清洗
3、清洗后表面有光泽无任何影响外观的污点及斑痕
-8-
十一)包
1、将瓦楞纸箱平放在地上
2、将仪表台放置在工作台面上
3、用气泡袋套住仪表台
4、将外包薄膜的辅件放置在包装袋内
5、用黄色胶带纸将辅件与仪表台捆扎牢固
6、将仪表台放入纸箱内
7、将纸箱盖合上
8、用包装带和包装夹分别在纸箱左、中、右三处将纸箱捆扎紧,检查松紧程度
9、在包装纸箱外表面标注产品名称、厂名、厂址、产品标准号、出厂日期等
(贴牢装箱清单)
10、如不能稳定放于包装箱内,则应制作支撑木架、聚丙烯成型泡沫并固定好
11、送进成品仓库
1、
包装时工作台面保持清洁,不可有任何尖锐物体及其他杂质
2、
包装前将手洗净
3、
打包机打包时必须将纸箱打包牢固,不可太紧以致纸箱破裂但不脱落
三、工装及模具制作(一般树脂模具的制作的过程)
1、模型制作
仪表台的首先来源于模型,它既是产品的外表面,也可在模型的基础上进
一步进行结构设计。
模型一般可采用石膏制作,也可制作木模模型,对于仪表
台的模型是表面要求比较高,也可以使用油泥制作。
模型的依据可以是主机厂提供的图纸或实物,也可以是边界尺寸与效果图。
涉及装配的尺寸一般是来源于主机厂的,但是制作模型也应当分析,比如装配
的尺寸(仪表台的总长、方向机的中心距,前弧线,前弧到地板的高度),所放
的间隙,装配件(仪表开关、空调系统、音响影相系统)的装配,是否放便检
修,可以会发生的功能件更改。
这些最终是被认定为关键的尺寸和公差。
这些
都应当在做模型的初期考虑。
换句话说,这些方面不确定,模型是不好做的,
至少是有风险的。
模型的制作的一个很重要的责任是仪表台的造型,造型一般会有一些思路
与概念,比如是豪放大气的,精巧的,婉约柔和,硬朗而挺括等。
国内的设计,
经常是借鉴的较多,这需要一个融合,盲目的模仿,会有不伦不类的感觉。
值
得提醒的是在造型的设计中应当考虑仪表台功能的要求,即仪表台既要美观,
但首先能装配好。
还要工艺完成能力,不能制造,再好的造型也是没有用的。
模型的基本要求:
相关尺寸符合顾客装配要求,模型表面曲线和曲线面应
光顺、流畅,无凹凸不平现象,筋线应清晰、明确,圆弧过渡自然、光顺。
模
型还应当考虑它的强度,不能在下道工序使用过程中产生变形。
模型的支撑也
很重要,一般使用木材和胶合板作为支撑结构,考虑到以后的模型会分成不同
零件或分总成,应提前设计好分型线,并能方便折分。
2、翻制石膏备模
石膏备模上是制作真空模(表皮成型使用)和骨架模的基础。
石膏备模翻制前,如果需要分型,先对前期模型进行分型,制作辅助面。
-9-
辅助面的设计在工艺上是很关键的一环,就象分型一样,也应得到应有的重视,
辅助制作应当至少考虑以下几个方面,1)设备因素,最大模具的外形尺寸应当
确定,2)材料因素,不仅是材料的规格是否受到限制,表皮的拉伸,发泡料的
挂壁,均应当考虑
3)模具因素,分型以及脱模角度,应尽量避免倒扣的现象
出现。
因此,制作辅助面应先确定基准面,以后放置模具角度,再设计辅助面
的角度及延伸距离。
如果设备允许,可以低于基准面作辅助面,辅助面之间连
接尽量使用圆弧面或连续的曲面过度。
并在石膏备模翻制前后制作工艺圆角。
由于在基准面的垂直方向上存有倒扣,所以需要制作滑块(活块),方便
模具的出模。
活块的要求与正式模具的活块可能不同,并且要求也没有浇铸模
具的活块那样高,但是还是应当保证能够顺利出模为最低条件。
具体的方法是
在模型上刷泡力水,涂脱模蜡,将用水调好的石膏涂在缺口处,在干硬后用铲
刀进行表面修理,这样,活动滑块就制好了。
下一步翻制石膏备模,将做好滑块的模型平放在地面上,均匀涂上脱模蜡,
周边用胶合板钉好护框,调好石膏,倒石膏模。
除了表面,其余的地方均可用
其它废料。
并且高度以最高点为参照。
倒得太高费料,且太重,不易翻转,太
矮可能缺料,并在翻转时易碎。
木模型/石膏模型脱模后修整石膏备模内腔,用清水或稀石膏补涂,并在石
膏模上钉相应沉坑垫块,可形成真空模具的沉坑,这里需要补充说明的是,一
般在翻制模具是尽量使用加高方式而不是削出沉坑的方式形成模具的形状,如
果真空模需要沉坑,就在石膏备模上加,如果是突台,就在主模型上加。
当然
也可以面模具上直接加铁板,但这一方式在
表皮真空模上很少用。
3、真空模制作。
糊制真空模:
在石膏模内均匀涂上脱模蜡后,调制环氧树脂、固化剂、增
强剂等混合物(环氧树脂
100
份+T31
固化剂
15~25
份+铁粉
20
份+滑石粉
份,
树脂需加热至
35℃),注意必须搅拌均匀,然后均涂于模具表面(第一层),不
可漏涂,第一层稍干后重新调制混合物,均匀涂于模具表面(第二层),待第二
层稍干后铺一层
0.2
玻纤布,调制环氧合成树脂涂刷于模具表面,铺一层
0.4
玻
纤布,如此逐层糊制至
层后,上木框及加强筋,再糊
3
层左右结束。
钉制真
空木模时,应在胶合板背面用
20mm
的杉木板加强。
修整真空模表面光顺流畅,无凹陷、塌角等缺陷,筋线应清晰、明确、无
波浪现象,R
角处应均等,圆弧过渡应自然、光顺。
打真空眼应控制在
Φ0.8~Φ1.0
之间,间距
15~20mm。
制作树脂滑块,根据产品脱模需要,制作环氧树脂滑块。
一般方法是先用
石膏填好倒扣位置,并作修理,然后再用石膏围好,并要可靠,调制环氧树脂,
配方与环氧模具基本一致,对大型滑块摆放钢丝玻纤布等加强物。
滑块的制作
是非常重要的一环,制作时可以考虑以下几个方面:
1)质轻,防止脱落时砸坏
浇铸模,因此可将大滑块内部做空。
2)有强度,因为是活动部分,防止自身的
损坏。
3)易滑落,在出模一定距离后能自动滑到底,(如果是跟上模的,就应
当防止滑落,但还是应当好出滑块,而不能损伤产品)4)吻合性好,要与真空
模与浇铸模放置的缝隙细且整体平整,不然会使产品在分形处形成梗状凸台。
正是其于以上考虑,滑块不能角太尖锐,不能太薄,与浇铸模有自然下行重力
可滑行,重心在浇铸模的靠外一侧,能回归原位而不是落于浇铸模内,要合理
分形,滑块的分形面尽量与产品的筋线吻合,如下沿翻边处,不能吻合的应保
-
-
持等距,为避免过得分形线与滑块分离,滑块表面可用玻璃薄板(塑料)粘盖,
有较好的较多,常用有主仪表弦的下沿。
批量大的滑块尽量翻制铝制。
铝滑块
的内部做空。
4、制作浇铸模
浇铸模糊制前应贴一层产品表皮的厚度,同时也要虑表皮在加热成形
后会产生的收缩,不同厂家的表皮的收缩率有一点的区别,我们希望较少的与
较一致的收缩。
一般收缩
5-8‰,如果收缩达达到
1%。
表皮性能就有问题了