氯化钾镀锌.docx
《氯化钾镀锌.docx》由会员分享,可在线阅读,更多相关《氯化钾镀锌.docx(9页珍藏版)》请在冰点文库上搜索。
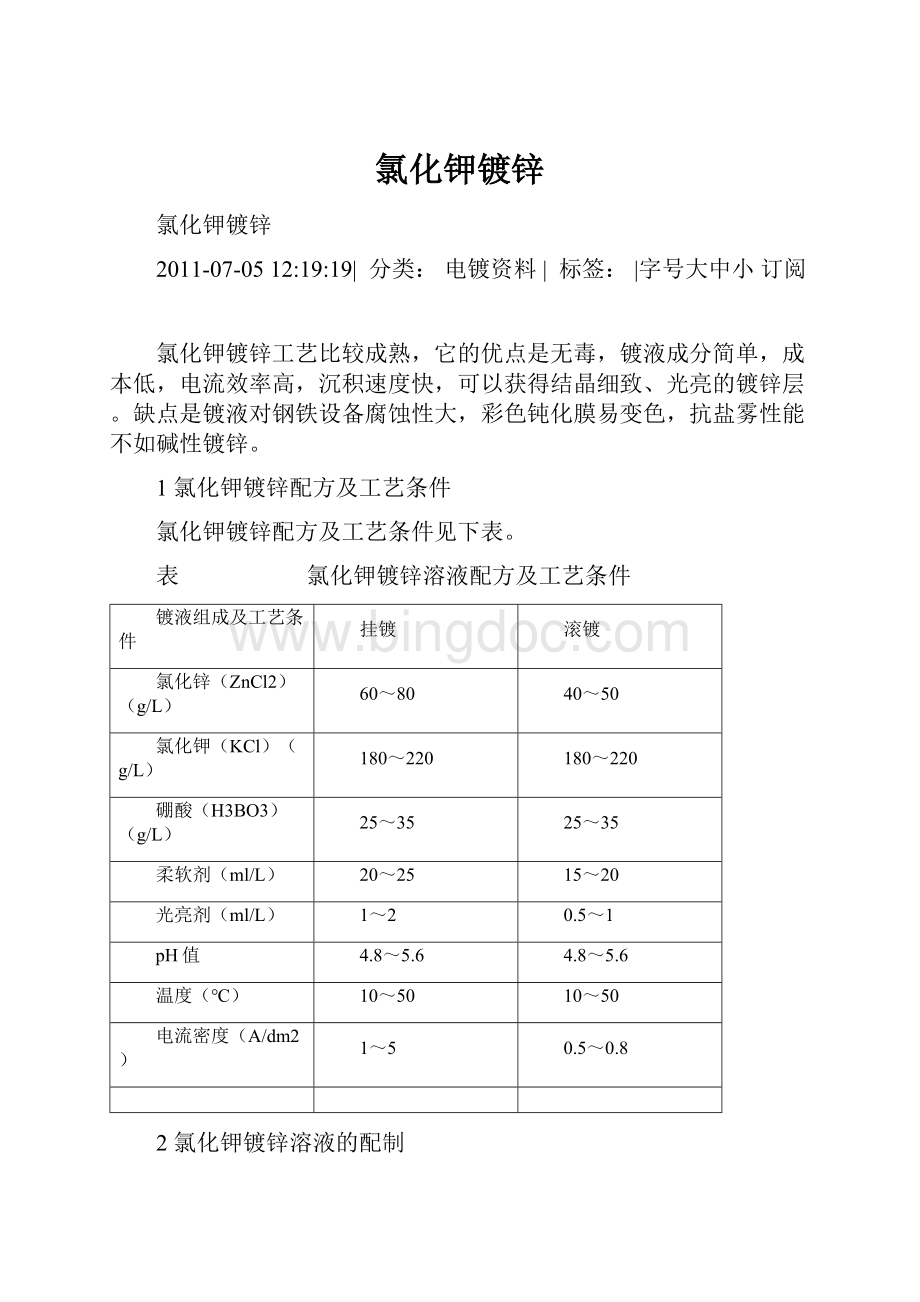
氯化钾镀锌
氯化钾镀锌
2011-07-0512:
19:
19| 分类:
电镀资料| 标签:
|字号大中小 订阅
氯化钾镀锌工艺比较成熟,它的优点是无毒,镀液成分简单,成本低,电流效率高,沉积速度快,可以获得结晶细致、光亮的镀锌层。
缺点是镀液对钢铁设备腐蚀性大,彩色钝化膜易变色,抗盐雾性能不如碱性镀锌。
1氯化钾镀锌配方及工艺条件
氯化钾镀锌配方及工艺条件见下表。
表 氯化钾镀锌溶液配方及工艺条件
镀液组成及工艺条件
挂镀
滚镀
氯化锌(ZnCl2)(g/L)
60~80
40~50
氯化钾(KCl)(g/L)
180~220
180~220
硼酸(H3BO3)(g/L)
25~35
25~35
柔软剂(ml/L)
20~25
15~20
光亮剂(ml/L)
1~2
0.5~1
pH值
4.8~5.6
4.8~5.6
温度(℃)
10~50
10~50
电流密度(A/dm2)
1~5
0.5~0.8
2氯化钾镀锌溶液的配制
2.1先在镀槽加入总体积二分之一容积的50~60℃热水,然后将计算量的氯化锌及氯化钾分别加入并搅拌溶解。
2.2在另一容器用沸水溶解计算量的硼酸,然后加入槽中。
2.3加水至规定体积,在搅拌下加入1~2ml/L双氧水,继续搅拌约30min,加入锌粉1~2g/L,并剧烈搅拌,静止沉淀2h后过滤。
2.4测定镀液pH值,如不在工艺范围,可用稀盐酸或稀氢氧化钠溶液调节镀液pH值至5.5左右,加入计算量的添加剂,添加剂需要用水稀释5~10倍后加入。
2.5用0.1~0.3A/dm2的阴极电流密度通电处理1~2h。
2.6取镀液用赫尔槽做小样试验,根据试验结果调整镀液后即可生产。
氯化钾应选用精制的电镀级,不要用农用氯化钾,因农用氯化钾杂质太多(配槽时溶液带有赭红色的沉渣沉淀就是农用氯化钾)。
3各成分及工艺条件的影响
3.1氯化锌
氯化锌是主盐,也是一种导电盐,能增加镀液的导电性。
其浓度允许在较大范围内变化,当锌离子含量取上限时,能提高阴极电流密度及提高镀层沉积速度,但分散能力和覆盖能力变差;当锌离子的含量取下限时,能提高镀液的分散能力,减少镀液的带出量。
若锌离子浓度过低,浓差极化较大,导致电流开不大,使光亮区变窄,阴极电流密度也相应降低,沉积速度减慢,高电流密度区易出现烧焦现象。
在实际生产中,只要添加剂选择合适,就可以适当提高氯化锌的含量,即使提高电流密度镀层也不容易烧焦,这样即能保证镀层质量,又提高了产量。
3.2氯化钾
氯化钾是镀液中的导电盐,它除了起导电作用外还有一个活化阳极的作用,即促使阳极正常溶解。
镀液中氯化钾的含量高,镀液的导电性就好,但含量过高会影响镀液对添加剂的溶解,使镀层光亮度下降。
当氯化钾含量过低时,镀液的分散能力和覆盖能力下降,光亮电流密度范围变窄。
3.3硼酸
硼酸是一种缓冲剂,能抑制镀液pH值的升高,使镀液的pH值保持相对的稳定。
如果镀液中硼酸含量不足,镀液的阴极电流密度上限就会缩小,镀层容易粗糙、烧焦,影响镀层的光亮度。
若含量过高,镀层会发花,因此,镀液中硼酸的含量以25~30g/L为佳,平时补充可按氯化钾添加量的1/7添加。
3.4添加剂
添加剂在镀液中能起到提高阴极极化、细化结晶、提高光亮度和整平作用,在镀液中起决定性作用,如果不加添加剂只能得到灰黑色、粗糙及疏松的海绵状锌层。
加入添加剂后,就能使镀层发亮,结晶细致。
因此添加剂的质量好坏是决定镀层质量最重要的因素。
好的添加剂能显著提高镀液的分散能力和覆盖能力及整平性能。
3.5pH值
当镀液的pH值遍低时,镀层光亮但氢大量析出,电流效率降低,覆盖能力下降;pH值高,镀层粗糙发暗,局部灰黑。
通常在电镀过程中pH值会缓慢上升,这时要注意及时用稀盐酸调整pH值。
调pH值时要不断搅拌,防止局部酸度过高而造成添加剂析出。
一般镀液的pH值应控制在4.5~6范围内,以5为佳。
3.6温度
镀液温度高可加大电流密度,但温度高了镀液的分散能力和覆盖能力下降。
镀液温度低可以减少光亮剂的消耗。
3.7电流密度
电流密度一般控制在1.5~2.5A/dm2范围。
阴极电流密度大,镀层细致光亮,沉积速度快,覆盖能力好,因此只要镀层不烧焦,电流密度越大越好。
4镀液维护及杂质的处理
槽液中的氯化锌、氯化钾及硼酸可根据分析结果调整,pH值可用盐酸调整,前处理的除油、酸腐蚀等工序不能疏忽,不然会影响镀层结合力,在日常工作中对掉入零件要及时捞出来。
4.1铁杂质的影响
镀液中的铁杂质有两种:
一种是二价铁,另一种是三价铁。
镀液中三价铁的含量达到10g/L时仍能正常生产,这可能与三价铁不能在阴极上与锌产生电化学共沉积有关。
而镀液中的二价铁则比较敏感,使电流密度范围明显缩小,尤其是影响高端电流密度处镀层的质量。
在进行赫尔槽试验时发现,在二价铁加到0.2g/L时,高电流端有近20mm出现烧焦和粗糙区;当加到0.3g/L时,几乎有半块样板出现烧焦粗糙区,同时低电流区镀层发灰。
这种镀液用于滚镀,则会出现贴近滚桶壁处镀层出现严重烧焦,这就是氯化钾滚镀锌常见的黑点,即滚桶眼子印。
一般在生产中,当铁离子含量大于5g/L时,低电流密度区镀层就会出现发黄。
这种故障的处理方法是在镀液中加入30%的双氧水0.5~1ml/L,然后充分搅拌,将镀液的pH值调至6,然后过滤除去铁。
4.2铜杂质的影响
镀液中的铜离子主要来源于铜棒、铜挂具、铜挂钩等落入镀槽而自溶解的。
铜杂质会造成低电流区发暗、镀层钝化不亮、发花及发黑。
处理的方法一般用置换法较好,即在镀槽加入1~2g/L锌粉,充分搅拌,静置1h后过滤。
也可采用0.5A/dm2电流密度电解除去。
铜杂质主要在于平时的预防,镀锌的阳极最好采用0号锌锭,其次要防止铜棒、铜勾及挂具掉入镀槽,同时更要防止铜绿掉入镀槽。
4.3铅杂质的影响
镀液中的铅杂质主要来源于锌阳极,铅杂质可使高电流区出现雾状,低电流区发黑色或淡黑。
镀液中的铅杂质可采用除铜杂质的方法处理,即采用锌粉置换或小电流密度电解。
4.4六价铬的影响
六价铬是氧化剂,对氯化钾镀锌溶液有较大的影响,尤其是在低电流密度区危害更大。
而三价铬对氯化钾镀锌溶液影响较小,但过多的三价铬也会导致镀锌层出现麻点。
一般三价铬离子应低于0.1g/L,而六价铬离子的含量一般不要超过3ppm。
氯化钾镀锌溶液一旦被六价铬污染,首先要找出污染的根源,先把源头堵住。
处理六价铬的方法是用保险粉,先将六价铬还原成三价铬,然后将溶液的pH值调整到6.0左右,沉淀后过滤。
4.5硝酸根的影响
硝酸根也是一种强氧化剂,对光亮剂有一定的破坏性作用,一般硝酸根离子应低于0.5g/L。
少量的硝酸根离子可用小电流密度长时间电解处理,如果含量过高就只更换溶液。
4.6有机杂质的影响
添加剂分解及油脂带入积累会产生有机杂质,有机杂质含量过高会使镀层钝化后发雾不光亮,覆盖能力降低,镀层粗糙。
有机杂质的去除可加入1~5g/L的活性炭来吸附有机杂质,搅拌并静置一夜,过滤去除。
5常见故障及处理方法
氯化钾镀锌常见故障及处理方法见下表。
表 氯化钾镀锌常见故障及处理方法
故障现象
原因及处理方法
镀层起泡或结合力差
1、镀前处理不良;
2、镀液光亮剂含量过高,加入双氧水或电解处理;
3、阴极电流密度过高。
底电流密度区域镀层发暗
1、镀液中光亮剂含量偏低;
2、镀液被重金属杂质污染,加入锌粉处理,过滤;
3、镀液温度偏高;
4、镀液中氯化钾含量偏低。
镀层有条纹或斑点
1、前处理不良或镀后处理不及时;
2、镀液有机杂质含量过多;
3、镀液氯化钾含量偏低;
4、镀液pH值偏低。
镀层光亮度差
1、镀液光亮剂含量偏低;
2、镀液温度偏高;
3、镀液pH值偏高或偏低。
镀层粗糙发灰,分散能力差
1、前液中有悬浮物,可过滤处理;
2、镀液中锌含量偏高或氯化钾含量偏低;
3、镀液温度偏高;
4、镀液有重金属杂质污染;
5、镀液光亮剂含量偏低。
电流密度无法提高,镀层容易烧焦
1、镀液锌离子含量偏低;
2、镀液光亮剂含量偏低;
3、镀液pH值偏高。
镀层发黑
1、硼酸不钝,造成镀液中杂质含量过高;
2、氯化钾不钝,造成镀液中杂质含量过高。
6氯化钾镀锌一些经验
6.1滚镀零件出现孔眼的处理
在滚镀时一些零件(特别是片状零件)出现孔眼,即片状零件在滚镀时出现部份零件上与塑料滚桶孔眼相仿的孔点。
出现这种情况主要有两种原因,一是电流密度过大导致镀层被烧焦而形成黑色斑点;另一种原因就是镀液中金属杂质含量过高所引起的,一般电力线是穿过孔眼至零件放电,所以孔眼处的电流密度最大,这样电位正的金属如铜、铅等杂质沉积较少,而相反电位较负的金属沉积较多,所以孔眼中锌镀层夹有较多的铁,在硝酸出光时零件表面出现明显的灰点或黑点。
溶液中的铁主要来源于镀件在镀槽中未通电时溶解,解决镀件出现孔眼的方法如下:
(1)增加滚桶转速;
(2)增加孔眼密度和孔径;
(3)降低电流密度,并适当延长电镀时间以保证镀层厚度;
(4)操作时镀件要带电下槽;
(5)镀液要定期用双氧水处理,处理方法是将溶液的pH提高至工艺要求的上限或是把溶液的pH值提高至≥5.8后,加入稀释的双氧水,使溶液中铁离子生成氢氧化铁沉淀。
6.2镀液的综合处理
氯化钾镀锌溶液在生产中不可避免要受到外来油污、化学药品及阳极材料不纯等污染,造成镀液中杂质逐渐增多而影响镀锌质量。
因此,对镀液要定期采取综合处理,其方法如下:
(1)先用稀盐酸调节溶液pH值至4,然后计算量的高锰酸钾(0.5~1g/L)用热水溶解,在搅拌条件下均匀加入镀槽,再继续搅拌约30min后静置1h。
(2)用5%的氢氧化钠溶液调节pH值至6.0~6.2,使铁形成氢氧化铁析出,然后加入3~5g/L活性碳,边加入边搅拌,以充分吸附有机杂质,然后静置1h。
(3)为除掉铜、铅等杂质,此时可按2g/L加入锌粉,并充分搅拌,静置1~2h后过滤。
(4)用稀盐酸调节溶液pH值至5~6,再用低电流密度电解处理1~2h,最后取样分析,根据分析调整镀液成分及适当补充添加剂即可投产。
6.3氯化钾镀锌添加剂
氯化钾镀锌添加剂通常也叫光亮剂,就其作用来讲一般可分为三种类型,即第一类是载体光亮剂,第二类是主光亮剂,第三类是辅助添加剂。
6.3.1第一类载体光亮剂
载体光亮剂的作用一是增溶主光亮剂;二起辅助光亮作用;三是降低镀液的表面张力,提高镀液的阴极极化作用,对阴极表面起润湿作用。
在镀液中的含量一般为6~8g/L,含量过高时会引起镀层脆性增加,同时还影响钝化膜的质量;含量过低时,镀层的光亮效果不佳。
载体光亮剂多是一些非离子型表面活性剂的磺化反应物。
常用的有平平加O与氨基磺酸磺化反应产物、或平平加O与顺丁烯二酸酐,焦亚硫酸钠的反应产物、或平平加O与硫酸,氢氧化钠的反应产物、以及OP乳化剂、TX乳化剂等。
6.3.2第二类主光亮剂
主光亮剂的作用是能吸附在阴极表面,提高阴极极化,使镀层结晶细致、平整和光亮,有的还能改善镀液的分散能力和覆盖能力。
通常使用的主光亮剂大多是由芳香醛、芳香酮以及杂环醛和杂环酮等组成。
如香草醛、苄叉丙酮、亚苄基丙酮、邻氯苯甲醛、对氯苄叉丙酮、聚乙烯吡咯烷酮等,可以使用一种,也可以内种一起使用。
一般几种同时使用效果会更好。
对氯苄叉丙酮的用量为0.2~0.5g/L,在三种材料中效果最好,但价格最高。
在氯化钾镀锌溶液中苄叉丙酮的光亮作用和整平能力最好。
如与载体光亮剂和辅助光亮剂配合好一些,镀层的应力也不大,也就是对镀层脆性较小。
通常在氯化钾镀锌溶液中苄叉丙酮的用量为0.2~0.4g/L。
邻氯苯甲醛可代替苄叉丙酮,其用量为0.2~0.4g/L。
邻氯苯甲醛的优点是出光快,镀层光亮度高,但缺点是易氧化成邻氯苯甲酸,使镀液变的不稳定。
另外邻氯苯甲醛属低毒、易燃物,使用也受到限制。
一般将邻氯苯甲醛和苄叉丙酮配合使用效果会更好。
6.3.3第三类辅助光亮剂
通常在氯化钾镀锌溶液中有了载体光亮剂和主光亮剂就能获得结晶细致和质量良好的锌镀层,但这种光亮剂是不够完美的,这是因为它的电流密度范围不够宽和深镀能力差。
当加入辅助光亮剂就能提高镀液的分散能力,扩大光亮电流密度范围,特别是低电流密度区,同时还能减少主光亮剂的消耗量。
常用的辅助光亮剂有苯甲酸钠(PTSA)、扩散剂NNO(亚甲基二萘磺酸钠)、肉桂酸、水扬酸钠、烟酸、糖精、苯骈三氮唑、巯基苯骈咪唑、甘氨酸、3-吡啶甲酰胺等。
大致用从0.001~10g/L不等。
另外,烟酸对改善镀层质量有明显的效果,但价格较高。
6.3.4添加剂的组成
主光亮剂可采用亚苄基丙酮和邻氯苯甲醛两种。
亚苄基丙酮价格便宜,对镀层有明显的光亮和整平作用,如果和载体光亮剂及辅助光亮剂配合得好,镀层的应力小,脆性也不大。
采用亚苄基丙酮作主光亮剂的氯化钾镀锌添加剂参考配方如下:
亚苄基丙酮 20g/L
载体光亮剂 220~300g/L
苯甲酸钠 60~80/L
扩散剂NNO 30~40g/L
邻磺酰苯甲酰胺钠盐 10~15g/L
吡啶-3-甲酸 5~8g/L
对氨基磺酰胺 2~3g/L
后三种物质可酌情加入,且不一定全加。
混合搅拌后,每升加入量为20ml/L。
由于添加剂是由多种成分复配的,各成分的消耗速度不会同步,一般要根据实践经验或通过赫尔槽试验进行补加。
载体的主要组成是:
150~250g/L萘酚与环氧乙烷加成的非离子型表面活性剂,15~25g/L月桂酸聚氧乙烯醚,10~20g/L的HS-1000表面活性剂。