偏心盘另工工艺与工装设计Word文档格式.docx
《偏心盘另工工艺与工装设计Word文档格式.docx》由会员分享,可在线阅读,更多相关《偏心盘另工工艺与工装设计Word文档格式.docx(28页珍藏版)》请在冰点文库上搜索。
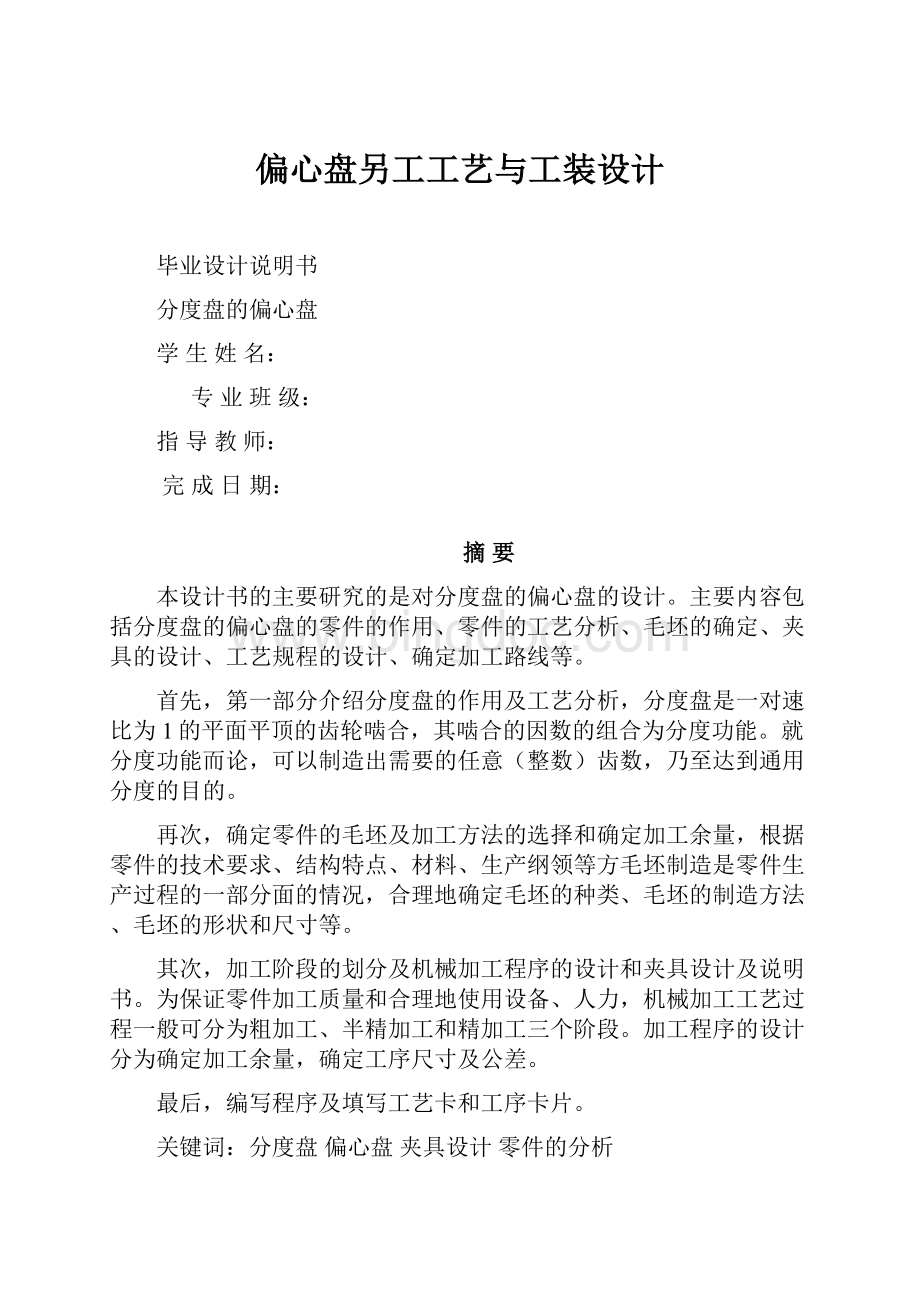
4.加工方法的选择………………………………………………………………………………..6
5.加工余量的概念………………………………………………………………………………..9
6.加工阶段的划分……………………………………………………………………………….12
7.机械加工程序的设计………………………………………………………………………….14
8.夹具的设计及说明…………………………………………………………………………….15
9.分度盘的偏心盘的零件图及程序的编制………………………………………………….....16
结论...................................................................................................................................................23
参考文献............................................................................................................................................24
致谢…………………………………………………………………………………………………25
1、零件的分析
1.1零件的作用
分度盘,是一对速比为1的平面平顶的齿轮啮合,其啮合的因数的组合为分度功能。
1.1.1、转动操纵手柄台面将上升到开启位置,转动台面实现分度;
反向转动操纵手柄台面下降与底座结合成为一个整体,无任何间隙方可开始工作。
1.1.2、在台面转动时,禁止将操纵手柄转至工作(锁紧)位置,以防碰击毁坏分度齿面。
1.1.3、台面可任意(方向)转动分度,不影响精密分度效果,也无机械故障。
1.1.4、在磁台上安装使用时应及时退磁,以防细小铁屑进入活动部位,造成意外故障。
1.1.5、使用中,如必须用冷却液时,应选用清洁的20号机油,不要使用皂油,避免腐蚀
2.零件的工艺分析
由附图1得知,其材料为HT300。
该材料具有较高的强度、硬度、耐磨性、耐热性及减振性,适用于承受较大应力、要求耐磨的零件。
2.1定位基准的选择
机械加工的第一道工序中,只能用毛坯上未经加工的表面作定位基准,这种定位基准称粗基准。
在随后的工序中,用加工过的表面作定位基准的称为精基准。
有时,为便于安装和保证所需的加工精度,在工件上制出专门供定位用的表面,这种定位基准称为辅助基准。
2.1.1粗基准选择的原则
粗基准的选择要保证用粗基准定位所加工出的精基准有较高的精度,通过精基准定位,使后续各被加工表面具有较均匀的加工余量,并与非加工表面保持应有的相对位置精度。
一般按下列原则选择:
保证相互位置要求的原则选取与加工表面相互位置精度要求较高的不加工表面作为粗基准。
这样可使加工表面与不加工表面有正确的相对位置。
在采用多轴联动的加工中心加工时,还可以在一次安装中将大部分加工表面加工出来。
如图1—4所示的毛坯,在铸造时内孔2与外圆1有偏心,因此在加工时,应选用不需加工的外圆1作为粗基准,三爪卡盘定心夹紧,加工内孔2,保证加工后的壁厚均匀。
又如图1—5所示零件,由于要求要~22内孔与中40外圆同轴,因此在钻#22内孔时,应选择#40外圆为粗基准。
图1-4粗基准的选择
图1-5拨杆加工粗基准的选择
2.2保证加工表面余量合理分配的原则
以余量最小的表面作为粗基准,以保证各表面都有足够的余量。
如图1—6所示的锻轴毛坯大小端外圆的偏心达5mm,若以大端外圆为粗基准,则小端外圆周可能无法加工出来,所以应选择加工余量较小的小端外圆作粗基准。
3.毛坯的确定
根据零件的技术要求、结构特点、材料、生产纲领等方毛坯制造是零件生产过程的一部分面的情况,合理地确定毛坯的种类、毛坯的制造方法、毛坯的形状和尺寸等,不仅影响到毛坯制造的经济性,而且影响到机械加工的经济性。
所以在确定毛坯的时候,既要考虑热加工方面的因素,也要兼顾冷加工方面的要求,以便从确定毛坯这一环节中,降低零件的制造成本。
3.1.毛坯的种类确定
毛坯的种类有铸件、锻件、压制件、冲压件、焊接件、型材和板材等。
表1—2给出了各种制坯方法的主要技术特征。
具体确定时可结合有关资料进行,同时还要全面考虑下列因素的影响:
3.1.1零件的材料及力学性能当零件的材料确定后,毛坯的类型也就大至上确定了。
例如:
材料是铸铁,毛坯就是铸造;
材料是钢材,且力学性能要求高时,可选锻件;
当力学性能要求较低时,可选型材或铸钢。
3.1.2生产类型大批大量生产时,可选精度和生产率都比较高的毛坯制造方法,用于毛坯制造的费用可由材料消耗和机械加工成本的降低来补偿。
如锻件应采用模锻、冷轧和冷拉型材;
铸件采用金属模机器造型或精铸等。
单件小批生产时,可选成本比较低的毛坯制造方法,如本棋手工造型和自由锻等。
各种毛坯制造方法的工艺特点
3.1.3零件的形状和尺寸形状复杂的毛坯,常用铸造方法。
尺寸大的零件可采用砂型铸造或自由锻造;
中、小型零件可用较先进的铸造方法或模锻、精锻等。
常见的一般用途的钢质阶梯轴零件,若各台阶的直径相差不大,可选用棒料;
着各台阶的直径相差较大,宜用锻件。
3.1.4现有生产条件确定毛坯时,必须结合具体的生产条件,如现场毛坯制造的实际水平和外协的可能性等。
尤其应注意发挥行业协作网络的功能,实行专业化协作是实现优质低耗的重要途径。
3.1.5充分考虑利用新工艺、新技术和新材料的可能性如考虑精铸、精锻、冷轧、冷挤压、粉末冶金和工程塑料等在机械中的应用。
这样可大大减少机械加工量,甚至有时可不用机械加工,其经济效益非常显著。
3.2.毛坯形状和尺寸的确定
受毛坯制造技术所限,加之对零件精度和表面质量的要求越来越高,故毛坯某些表面仍留有一定的加工余量,以便通过机械加工来达到质量要求。
称为毛坯加工余量,毛坯制造尺寸的公差称为毛坯公差。
毛坯加工余量及公差同毛坯制造方法有关,生产中可参照有关工艺手册和部门或企业的标准来确定。
毛坯加工余量确定以后,还要考虑毛坯制造、机械加工和热处理等多方面工艺因素的影响。
如为了加工时安装工件的方便,有些铸件毛坯需铸出工艺搭子,如图1—2所示,工艺搭子在零件加工好后一般均应切除。
又如图1—3所示发动机连杆等零件,为了保证加工质量,同时也为了加工方便,常将这些零件先做成一个整体毛坯加工到一定阶段后再切割分离。
对于形状比较规则的小型零件,应将多件合成一个毛坯,当加工到一定阶段后,再分离成单件。
材料为HT300
分度盘的偏心盘的毛坯图
4.加工方法的选择
4.1各种加工方法所能达到的经济精度和表面粗糙度
零件上的各种典型表面都有许多加工方法,一种加工方法能获得的加工精度和表面粗糙度都有一个范围。
在正常加工条件下(采用符合质量标准的设备和工艺装备,以及标准技术等级的工人不延长加工时间)所能保证的加工精度,称为经济加工精度,简称经济精度。
通常它的范围是较窄的。
例如,公差为IT7级和表面粗糙度为Ra0.4μm的外圆表面。
精车能够达到,但采用磨削则更为经济。
随着科学技术的发展和工艺水平的提高,同一加工方法所能达到的加工精度和表面粗糙度是在不断进步的。
例如,过去在外圆磨床上精磨外圆仅能达到IT6级精度,但在采取有效措施提高磨床精度并改进了磨削工艺后,现在普通外圆磨床上可以进行镜面磨削,已达到IT5级以上精度,表面粗糙度凡值为0.04~0.02μm。
各种加工方法所能达到的经济加工精度和表面粗糙度。
常用加工方法的经济加工精度和表面粗糙度
4.2工件材料的性质
加工方法的选择,常受工件材料性质的限制,例如淬火钢淬火后应采用磨削加工;
而有色金属磨削困难,常采用金刚健或高速精密车削来进行精加工。
4.3工件的结构形状和尺寸
以内圆表面加工为例,回转体零件上较大直径的孔可采用车削或磨削,箱体上IT7级的孔常用镇削或铰削,孔径较小时宜用铰削,孔径较大或长度较短的孔宜选镇削。
4.4生产率和经济性的要求
大批大量生产时,应采用高效率的先进工艺,如拉削内孔及平面等。
或从根本上改变毛坯的制造方法,如粉末冶金,精密铸造等可大大减少机械加工的工作量。
但在生产纲领不大的情况下,应采用一般的加工方法,如螳孔或钻孔,扩孔,铰孔及铣削、刨削平面等。
综上所述,加工方法的选择应考虑的主要因素有:
零件的精度要求、零件材料及其结构的可加工性能、生产率的要求、企业自身或企业协作网络的工艺能力和设备的经济加工精度。
5.加工余量的概念
在机械加工工艺中,每一工序加工质量的标准是各个加工表面的工序加工尺寸及其公差。
确定工序尺寸,首先要确定加工余量。
所谓加工余量是指加工过程中,所切去的多余金属层的厚度。
工序余量是同一被加工表面相邻两工序尺寸之差;
加工总余量是某一表面毛坯尺寸与零件图样的设计尺寸之差。
由于工序尺寸有公差,故实际切除的余量会在一定的范围内变动。
图12—15表示工序余量与工序尺寸的关系。
由图可知,工序余量的基本尺寸(简称基本余量或公称余量)可按以下式表示:
对于被包容面Z=a—b
对于包容面Z=b—a
对于回转体表面,余量的计算公式为:
轴Z=(da一db)/2
孔Z=(db一da)/2
式中:
Z——工序余量的基本尺寸;
=
a、da——上道工序基本尺寸;
b、db——本工序基本尺寸。
平面等非回转表面的加工余量则指单边余量,它等于实际切削的金属层厚度。
对于孔和外圆等回转表面,加工余量指双边余量即以直径方向计算,实际切削的金属层厚度为加工余量的一半。
a)补包容面(轴)b)包容面(孔)
图1-15工序余量与工序尺寸的关系
图1-16表示加工总余量与工序余量的关系,由图可得(适用于被包容面和包容面):
Z0=
Zi
Z0——加工总余量(毛坯余量);
Zi——各工序余量;
n——工序数。
为了便于加工,工序尺寸都按“入体原则”标注极限偏差,即按被包容面取上偏差为零;
包容面的工序尺寸取下偏差为零。
毛坯尺寸则按双向布置上、下偏差。
工序余量和工序尺寸之公差的计算公式如下:
Zmin=Z-Ta
Zmax=Z+Tb
Tz=Zmax-Zmin=Ta+Tb
Zmin——最小工序余量;
Zmax——最大工序余量;
Ta——上工序尺寸的公差;
Tb——本工序尺寸公差;
Tz——工序余量公差。
工序余量的公差为上工序与本工序公差之和。
此毛坯的加工余量2mm
粗加工的工序余量为1.5mm
半精加工的工序余量为0.06mm
5.1加工余量的确定
加工余量的大小对工件的加工质量和生产率有较大的影响。
余量过大,会造成浪费工时,增加成本;
余量过小,会造成废品。
确定加工余量的基本原则是在保证加工质量的前提下,尽可能减小余量。
在确定时应考虑以下因素:
5.1.1上工序的各种表面缺陷和误差因素本工序的加工余量应能修正上工序的表面粗糙度Ra,凡和缺陷层Da、上工序的尺寸公差Ta和上工序的形位误差ρa。
5.1.2本工序加工时的装夹误差它包括定位误差、夹紧误差(夹紧变形)和夹具本身的误差,安装误差应为上述三项误差的向量和。
本工序的工序余量应大于Ra、Da、Ta、ρa。
和装夹误差之和。
如图1-17所示工件螳孔时的加工余量必须大于上工序Ra、Da、Ta、ρa。
和本工序装夹偏心误差εb。
之代数和。
在实际生产中,确定加工余量的方法有以下几种:
a)被加工零件b)前工序误差与表面质量c)本工序安装误差
图1-17影响加工余量的因素
1)经验估计法此法是根据工艺人员的实际经验确定加工余量的。
为了防止因余量不够而产生废品,所估计的加工余量一般偏大。
此法常用于单件小批量生产。
2)查表法此法是以工厂生产实践和试验研究积累的有关加工余量的资料数据为基础,先制成表格,再汇集成手册。
确定加工余量时,查阅这些手册,再结合工厂的实际情况进行适当的修改后确定。
目前,这种方法用的比较广泛。
3)分析计算法此法是根据一定的试验资料和计算公式,对影响加工余量的各项因素进行综合分析和计算来确定加工余量的方法,这种方法确定的加工余量最经济合理,但必须有比较全面和可靠的试验资料。
目前,只在材料十分贵重,以及军工生产或少数大量生产的工厂中采用。
在确定加工余量时,要分别确定加工总余量(毛坯余量)和工序余量。
加工总余量的大小与毛坯制造精度有关。
用查表法确定工序余量时,粗加工工序余量不能用查表法得到,而是由总余量减去其他各工序余量之和而得。
6.加工阶段的划分
为保证零件加工质量和合理地使用设备、人力,机械加工工艺过程一般可分为粗加工、半精加工和精加工三个阶段。
(1).粗加工阶段主要任务是切除毛坯的大部分加工余量,使毛坯在形状和尺寸上尽可能接近成品。
因此,此阶段应采取措施尽可能提高生产率。
(2.)半精加工阶段减小粗加工后留下的误差和表面缺陷层,使被加工表面达到一定的精度,为主要表面的精加工做好准备,同时完成一些次要表面的加工。
(3).精加工阶段保证各主要表面达到图样的全部技术要求,此阶段的主要目标是保证加工质量。
(4).光整加工阶段对于零件上精度和表面粗糙度要求很高(IT6级以上,表面粗糙度为0.2um以下)的表面,应安排光整加工阶段。
减小表面粗糙度或进一步提高尺寸精度,一般不用以纠正形状误差和位置误差。
通过划分加工阶段,首先可以逐步消除粗加工中由于切削热和内应力引起的变形,消除或减少已产生的误差,减小表面粗糙度。
其次,可以合理使用机床设备。
粗加工时余量大,切削用量大,可在功率大、刚性好、效率高而精度一般的机床上进行,充分发挥机床的潜力。
精加工时在较为精密的机床上进行,既可以保证加工精度,也可延长其使用寿命。
此外,通过划分加工阶段,便于安排热处理工序,充分发挥每一次热处理的作用。
消除粗加工时产生的内应力、改变材料的力学、物理性能。
还可以及时发现毛坯的缺陷,及时报废或修补,以免因继续盲目加工而造成工时浪费。
工艺过程划分阶段随加工对象和加工方法的不同而变。
对于刚性好的重型零件,可在同一工作地点,一次安装完成表面的粗、精加工。
为减少夹紧变形对加工精度的影响,可在粗加工后松开夹紧机构,然后用较小的力重新夹紧工件,继续进行精加工。
对批量较小、形状简单及毛坯精度高而加工要求低的零件,也可不必划分加工阶段。
加工顺序的安排
机械加工工艺规程是由一系列有序安排的加工方法所组成的。
在加工方法选定后,工艺规程设计的主要内容就是合理地安排这些加工方法的顺序,及其与热处理、表面处理(如镀铬、镀铜、磷化等)工序间以及与辅助工序(如清洗、检验等)的相互顺序。
6.1机械加工顺序的安排
主要取决于基准的选择与转换。
在设计时遵循以下原则:
基面先行精基准选定后,机械加工首先要选定粗基准把精基准面加工出来。
在加工轴类零件时,一般是以外圆为粗基准来加工中心孔,再以中心孔为精基准来加工外圆、端面等。
(1)先主后次零件的主要工作表面、装配基面应先加工,从而能及早发现毛坯中主要表面可能出现的缺陷。
次要表面可穿插进行,放在主要表面加工到一定的精度之后,最终精加工之前进行。
(2)先粗后精通过划分加工阶段,各个表面先进行粗加工,再进行半精加工,最后进行精加工和光整加工。
从而逐步提高表面的加工精度与表面质量。
(3)先面后孔对于箱体、支架等类零件,平面的轮廓尺寸较大,一般先加工平面以作精基准,再加工孔和其它表面。
有些表面的最后精加工安排在部装或总装过程中进行,以保证较高的配合精度。
6.2热处理工序的安排
热处理工序在工艺路线的安排主要取决于零件的材料及热处理的目的。
预备热处理的主要目的是改善切削加工性能,消除毛坯制造时的残余应力。
其工序位置多在机械加工之前。
消除残余应力处理最好安排在粗加工之后精加工之前。
对精度要求不太高的零件,一般将消除残余应力的人工时效和退火安排在毛坯进人机械加工车间之前进行。
对精度要求较高的复杂铸件,在加工过程中通常安排两次时效处理:
铸造一粗加工~时效一半精加工一时效一精加工。
对于高精度的零件,如精密丝杠、精密主轴等,应安排多次消除残余应力的热处理。
甚至采用冰冷处理稳定尺寸。
最终热处理的目的是提高零件的强度、表面硬度和耐磨性。
常用淬火、回火以及各种化学处理(渗碳淬火、渗氮、液体碳氮共渗等)。
最终热处理后会产生内应力或其他缺陷,因而还应增加回火等处理,并把它安排在精加工工序(磨削加工)之前进行。
6.3辅助工序的安排
辅助工序主要包括:
检验、清洗、去毛刺,去磁、倒棱边、涂防锈油及平衡等。
其中检验工序是主要的辅助工序,是保证产品质量的主要措施。
它一般安排在:
粗加工全部结束以后精加工开始以前、零件在不同车间之间转移前后、重要工序之后和零件全部加工结束之后。
有些重要零件,不仅要进行几何精度和表面粗糙度的检验,还要进行如X射线、超声波探伤等材料内部质量的检验以及荧光检验、磁力探伤等材料表面质量的检验。
此外,清洗、去毛刺等辅助工序,也必须引起高度重视,否则将会给最终的产品质量产生不良的甚至严重的后果。
6.4.工序的集中与分散
在选定了零件上各个表面的加工方法及其加工顺序以后,制定工艺路线可以采用两种不同的原则:
一种是工序集中的原则,即使每个工序中包括尽可能多的加工内容,从而使工序的总数减少:
另一种是工序分散的原则,其含义与之相反。
工序集中的主要特点是:
6.4.1有利于采用高效的专用设备和工艺装备,大大提高生产效率。
6.4.2可减少工序数目,缩短工艺路线,简化生产计划工作和全产组织工作。
6.4.3可减少工件的装夹次数。
这不仅保证了各个加工表面间的相互位置精度,还减少了辅助时间及夹具的数量。
6.4.4可减少机床设备数量,减少工人人数及生产所需的面积。
6.4.5较多采用专用设备和工艺装备,生产准备周期较长.调整和维修也较麻烦,产品变换困难。
工序分散的特点是:
(1)每台机床完成较少的加工内容,机床、工具、夹具结构简单,调整方便,对工人的技术水平要求低。
生产适应性强,转换产品较容易。
(2)便于选择更合理的切削用量,减少机动时间。
(3)所需设备及工人人数多,生产周期长,生产所需面积大,运输量也较大。
7.机械加工工序设计
分度盘的偏心盘的工序设计
(1)确定加工余量。
毛坯余量(总余量)已在画毛坯图时确定,这里主要是确定工序余量。
工序余量一般可用计算法、查表法或经验估计法三种方式来确定。
本次设计可参阅有关机械加工工艺手册用查表法按工艺路线的安排,逐工序、逐表面地加以确定。
(2)确定工序尺寸及公差。
计算工序尺寸和标注公差是制订工艺规程的主要工作之一。
工序尺寸公差一般按经济加工精度确定(可查阅有关的机械加工工艺手册)。
当定位基准(或工序基准)与设计基准重合时(如单纯孔与外圆表面的加工;
单一平面加工等),可采取“层剥皮”的方法,即将余量层一层层叠加在被加工表面上,可以清楚地看出每道工序的工序尺寸,再按每种加工方法的经济加工精度公差按尺寸上,如前述似
孔,可画出如图1-2所示的简图。
“入体方式”标注在对应的工序当定位基准(或工序基准)与设计基准不重合
时,即加工中基准多次变换时,此时应按尺寸链原理来计算确定工序尺寸与公差,并校核余量层是否够切。
例如,活塞销孔加工有关的设计尺寸与工艺过程如图1-3所示,试确定工序尺寸A、B及其偏差。
设计尺寸56mm为最后形成的被间接保证的尺寸,为尺寸链的封闭环。
(3)确定各工序切削用量。
选择切削用量的一般原则是保证加工质量,在规定的刀具耐用度条件下,使机动时间少、生产率高。
为此,应合理选择刀具(材料、几何角度、耐用度等)。
在选择切削用量时,首先确定切削深度(现标准称为背吃刀量。
粗加工时尽可能等于工序余
削速度(精加工则主要依据表面质量的要求)。
量);
然后根据表面粗糙度要求选择较大的进给量;
最后,根据切削速度与耐用度或机床功率之间的关系,用计算或查表方法求出相应的切本次设计可参阅有关的机械加工工艺手册采用查表法。
组合机床的切削用量选择,主要参照现场情况,根据多年积累的经验数据进行,具体数据可查阅参考文献〔1〕。
一般多轴加工组合机
图1-2基准重合下工序尺寸与公差的确定
1
下料
用车床下φ92×
65
2
粗车
车φ40端面、外圆、φ78凹槽
3
车φ80端面、外圆
4
半精车
车φ40端面、外圆、倒角
5
车φ80端面、外圆、倒角
6
检验
检验尺寸、余量、表面质量与工件缺陷
7
热处理
调质
8
精车
9